Петренко Н.Н.
Филиал «Газопромысловое управление»
газовый промысел №5
Повышение конденсатоотдачи при отборе газа. Изотермическое снижение пластового давления в газоконденсатной залежи одновременно сопровождается конденсацией высококипящих углеводородов (С.Н. Закиров, 1998; Р.М. Тер-Саркисов, 1999; А.Х. Мирзаджанзаде и др., 2003) и испарением остаточной воды. Парообразная влага пластовой парогазовой системы способна в значительных количествах растворять углеводороды, что подтверждено экспериментально. На примере крупного газоконденсатного месторождения GE была выполнена оценка количества ретроградного конденсата, испарившегося во вновь образованную парообразную влагу от испарения остаточной воды, вызванного возрастанием влагоёмкости пластового газа. Принималось, что в 1 м3 водяного пара растворяется такое же количество конденсата, какое содержится в пластовом газе при текущем пластовом давлении. За весь период разработки количество испарившегося ретроградного конденсата составило 471,4 тыс. т.
|
|
Повышение конденсатоотдачи при сайклинг-процессе. На повышение кондесатоотдачи при сайклинг-процессе оказывают влияние два фактора: нагнетаемый в пласт сухой газ насыщается ретроградным конденсатом до равновесного состояния; одновременно газ насыщается парообразной влагой за счёт испарения остаточной воды, и образующийся при этом водяной пар также насыщается ретроградным конденсатом.
Рисунок – Динамика испарения ретроградного конденсата в месторождении GE
На рисунке приведено сопоставление количеств ретроградного конденсата, испарившегося в месторождении GE при отборе газа, при сайклинг-процессе и при испарении его в дополнительно сформированную парообразную влагу.
Оценка объёмов испарения ретроградного конденсата от парциального давления водяного пара. Пластовое давление газовой залежи состоит из парциального давления паров углеводородов и паров воды. Чем выше пластовая температура, тем выше парциальное давление парообразной влаги. Оценка парциального давления водяного пара для газоконденсатного месторождения GE выполнена через мольную долю водяного пара, рассчитанную по программе, разработанной автором. Расчеты показали, что даже при малом значении парциального давления водяного пара дополнительная добыча конденсата составила 632,73 тыс. т.
Осушение пласта–коллектора при сайклинг–процессе. Оценка размеров осушения порового пространства в пределах призабойных зон и репрессионных воронок нагнетательных скважин имеет большое научное и практическое значение. Важно установить, происходит ли повышение приёмистости скважин в результате возрастания газонасыщенности порового пространства, или, наоборот, приёмистость понижается в результате выпадения солей в сужениях поровых каналов из-за полного испарения остаточной воды.
|
|
Сайклинг-процесс в месторождении GE осуществлялся нагнетанием сухого газа в 52 нагнетательные скважины, расположенные в виде двух нагнетательных рядов со средним расстоянием между скважинами 1,53 км.
Оценка выполнена для средней нагнетательной скважины за 18-летний период нагнетания газа. За указанный период вокруг каждой нагнетательной скважины испарилось 17,612 тыс. м3 остаточной воды, а радиус полного осушения порового пространства составил 90 м.
«ПОДБОР ОПТИМАЛЬНОЙ МЕТОДИКИ ПОСТРОЕНИЯ КАРТЫ ИЗОБАР В ПО ПЕТРЕЛЬ НА ПРИМЕРЕ НЕОКОМСКОЙ ЗАЛЕЖИ ЗНГКМ»
Степанов М.М.
Управление геологии разработки и лицензирования месторождения
Отдел программно-математического обеспечения.
Важной задачей при разработке месторождений севера Западной Сибири является контроль энергетической характеристики продуктивных отложений. Пластовое давление - один из важнейших факторов, описывающих энергетические возможности продуктивного пласта, производительность скважин и залежи в целом. Контроль за изменением пластового давления в продуктивном пласте в процессе разработки залежи проводят с помощью карт изобар.
Построение карт изобар производится ежеквартально. При построении карты на установленную дату используются замеры пластового давления в скважинах, приведенные к дате картопостроения, а также данные гидродинамического моделирования. На рисунке 1 показан тренд снижения пластового давления с использованием замеров пластового давления, а также на основе снижения пластового давления по гидродинамической модели.
Рисунок 1 - Прогноз падения пластового давления по скважине №11301 ЗНГКМ
Далее в ПО Петрель по рассчитанной на определённую дату гидродинамической модели из 3Д куба давления строится двумерная карта изобар. Для построения итоговой карты изобар необходимо учитывать точки с замерами давления.
Для построения поверхности могут использоваться следующие четыре опции:
1) Convergent (Конвергентный): Используется конвергентное построение грида, которое, в общем, является наиболее подходящим для привязки к скважинам, так как глобально экстраполируются глобальные тренды и в то же время сохраняются детали.
2) Moving average (Скользящее среднее): Рассчитывает среднее взвешенное значение по расстоянию точек около узла грида. Метод больше всего подходит для низкой плотности точек или при плохом качестве данных. Доступны следующие настройки для работы с данными маркеров:
· Equal (Равное): Все точки имеют равное взвешивание.
· Inverse distance (Обратное расстоянию): Точки, расположенные в непосредственной близости от узла грида, имеют более тяжёлое взвешенное значение.
· Inverse distance squared (Обратное расстоянию в квадрате): Обратное расстоянию, но с более тяжёлым взвешенным значением.
· Inverse distance quadrupled (Обратное расстоянию в четвертой степени): Обратное расстоянию, но с более тяжёлым взвешенным значением.
3) Cos expansion (Распространение по косинусу): Функция минимальной кривизны, результатом которой является сглаживание. Этот вариант работает хорошо при наличии нескольких точек, но при большом количестве точек данных (более 100 точек) работает медленно.
4) Minimum curvature (Минимальной кривизны): Использует сглаживающий оператор, который сохраняет поверхность гладкой.
Как видно из рисунка 2, некоторые алгоритмы при одинаковых входных данных показывают разные результаты – локальные экстремумы в межскважинном пространстве, по-разному происходит и экстраполяция за пределы области наличия (неразбуренные участки). На периферии и в межскважинном пространстве большее
|
|
Рисунок 2 – Алгоритмы моделирования
падение давления показывает алгоритм Minimum curvature и Convergent, меньшее – алгоритм Moving average. При сравнении с величиной p/z, рассчитанной по уравнению материального баланса на геологические запасы, ближе всех лежит карта, построенная с помощью алгоритма Convergent.
Таким образом, из данных методик в соответствии с исходными данными наилучшие результаты показывает метод Convergent, достаточно хорошо отработав интерполяцию и экстраполяцию. Разность карт изобар текущей и построенной в прошлом квартале показана на рисунке 3.
Рисунок 3 – Карта, построенная вычитанием текущей и предыдущей карт изобар пласта БТ6-8 ЗНКГМ
«ПРОБЛЕМЫ И ПУТИ ПОВЫШЕНИЯ ЭФФЕКТИВНОСТИ РАБОТЫ УСТАНОВКИ СТАБИЛИЗАЦИИ КОНДЕНСАТА (УСК) ГП-2 БОВАНЕНОВСКОГО НГКМ»
Тимергалеев Р.Р.
ООО «Газпром добыча Надым»
Филиал «Ямальское Газопромысловое управление»
Производственно-технический отдел
23 октября 2012 года введено в эксплуатацию уникальное по запасам Бованенковское НГКМ – первое месторождение ОАО «Газпром», введенное в результате реализации Мегапроекта «Ямал» по освоению месторождений полуострова Ямал.
На сегодняшний день введены в эксплуатацию 2 модуля ГП-2, суммарной годовой мощностью по газу 60 млрд. м3, в составе которого так же – первый пусковой комплекс установки стабилизации конденсата (УСК) и регенерации метанола (УРМ).
УСК обеспечивает стабилизацию газового конденсата способом колонной ректификации с получением товарного стабильного конденсата соответствующий ОСТ 51.65-80 “Конденсат газовый стабильный. Технические условия”, а также газов стабилизации и выветривания, подготавливаемых в качестве газа собственных нужд. Установка содержит три технологические нитки (2 рабочие + 1 резервная) с проектной производительностью 5,5 тонн/час каждая из расчета максимального поступления нестабильного конденсата.
Принципиальная технологическая схема УСК представлена на Рисунке 1.
|
|
Отсепарированная на установке НТС ГП-2 газожидкостная смесь ВМР и НК поступает в буферную емкость 100Е-5 предназначенную для накопления сырья и частичной его дегазации. Далее смесь проходит теплообменник 100Т‑1 в котором он подогревается за счет рекуперации тепла стабильного конденсата, который в свою очередь охлаждается. Из теплообменника 100Т‑1 поток поступает в блок трехфазного делителя 100Р-1, где происходит дегазация и разделение газожидкостной смеси на НК и ВМР. ВМР подается на установку регенерации метанола, часть конденсата – на орошение в колонну стабилизации, а другая часть в рекуперативный теплообменник. Количество НК, поступающего в колонну на орошение, определяется температурным режимом в верхней части колонны. Из теплообменника 100Т‑3 нестабильный конденсат подается на тарелку питания в блок колонны стабилизации 100К-1.
Колонна представляет собой вертикальный аппарат переменного сечения диаметрами 219/377/530/1000 мм с узлами ввода питания и орошения, полуглухой тарелкой, распределительными тарелками и контактными устройствами в виде пакетов сетчатой насадки с провальными тарелками.
Рис.1. Принципиальная технологическая схема УСК.
Кубовая часть колонны разделена на две камеры: приемную и отбора продукта. В колонне в результате тепло- и массообмена при нагревании компоненты конденсата газа нестабильного с более низкой температурой кипения переходят в пары, а компоненты с высокой температурой кипения остаются в жидкости.
Для поддержания необходимого температурного режима колонны производится циркуляция постоянного количества кубовой жидкости насосами 100Н‑2 через блок печи стабилизации 100П‑1 и возврат парожидкостной смеси в нижнюю часть стабилизатора. Стабильный конденсат из кубовой части колонны, проходя теплообменники 100Т‑3 и 100Т‑1, охлаждается и направляется в резервуарный парк стабильного конденсата (РПК).
Учитывая тот факт, что после вывода месторождения на полное развитие с объемом добычи газа около 100 млрд. м3/год, загрузка колонны стабилизации составит 6,8…7,2 т/ч. Вместе с тем, если учесть подключение в разработку пластов ХМ с пока неизвестным конденсатным фактором, но, предположительно – 3…6 г/м3, то загрузка одной колонны может возрасти до 10 т/ч. Тогда как проектная загрузка колонны 100К-1 составляет всего 5,5 т/ч.
В связи с данным обстоятельством в марте-апреле 2014 года совместно со специалистами ООО «Газпром ВНИИГАЗ» были проведены специальные испытания. Задачей испытания являлось – определение возможности работы технологической линии УСК с повышенной загрузкой по сырью: 9–10 т/ч против 5,5 т/ч по проекту.
На первом этапе исследовалась проектная схема УСК с «полной» колонной. Данный цикл исследований проводился при относительно высоком давлении в дегазаторе 20Д-1 и в аппаратах УСК.
На основании анализа многочисленных режимов были сделаны следующие выводы:
1. При работе по проектной схеме максимально достижимая загрузка колонны стабилизации 100К-1, составила около 7 т/ч. При объёмном расходе газа стабилизации более 20 м3/ч наблюдался активный вынос жидкости с газом стабилизации, который регистрировался стремительным повышением уровня жидкости в сепараторе подготовки топливного газа для собственных нужд 100С-1, что недопустимо.
2. Увеличение производительности УСК может быть достигнуто только в результате значительного снижения газонасыщенности сырья УСК, как результат понижения давления в дегазаторе 20Д-1 и аппаратах УСК.
На втором этапе исследовалась проектная схема УСК с «усеченной» колонной, при пониженных давлениях в системе 20Д-1 – 100Е-5 – 100Р-1 – 100К-1. Согласно этому решению отключается подача орошения, и весь поток направляется в середину, т.е. в этом случае тарелки верхней секции колонны исключаются из работы, число рабочих тарелок составляет шесть единиц (три теоретические тарелки), в результате работает только нижняя часть колонны, которая имеет значительно больший диаметр (377 мм против 200 мм в верхней части). При этом колонна работает устойчиво, технически удалось загрузить 100К-1 сырьём в количестве 9 т/ч, без уноса конденсата с газом стабилизации, а ДНП стабильного конденсата полностью удовлетворяет требованиям ГОСТ Р 54389-2011, которое должно быть не выше 66,7 кПа (500 мм.рт.ст.). Важно также отметить, что при этом оказалось возможным резко снизить давление в 100К-1: с фактических 0,85 МПа до 0,35 МПа, что позволило работать на повышенных расходах с тем же огневым подогревателем 100П‑1.
На основании проведенного анализа режимов работы УСК можно сделать следующие выводы:
1. Значительное увеличение производительности УСК может быть достигнуто только при работе по схеме с «усечённой» колонной.
2. Максимальный расход газа стабилизации, который не приводит к «выносу» жидкости из верхней части колонны, составляет 50 м3/ч при фактических термобарических параметрах.
3. Имеются все основания полагать, что УСК обеспечит работу при загрузке 10 т/ч.
Во время проведения второго этапа исследований и по настоящее время УСК успешно работает по схеме с «усеченной» колонной.
«АНАЛИЗ ИННОВАЦИЙ В ОБЛАСТИ ПОДГОТОВКИ ГАЗА ПРИ РЕШЕНИИ ПРОБЛЕМ СЕПАРАЦИИ НА ЗНГКМ»
Хасанов Д.Ю.
Филиал «Инженерно-технический центр»
Заполярная лаборатория техники и технологии добычи газа
Большая роль в технологии подготовки природного газа к транспорту на УКПГ отводится сепараторам, которые предназначены для очистки газа от жидкости, механических примесей и для отмывки солей, поступающих с пластовой водой из скважин, и абсорберам – для извлечения паров воды из газа. Критерием эффективности работы сепарационного оборудования является унос капельной жидкости с газом из сепаратора, в то время как наиболее важной характеристикой абсорбера является возможность достижения требуемой глубины осушки газа, которая должна соответствовать СТО Газпром 089-2010.
По проекту сепараторы сеноманских УКПГ ЗНГКМ оборудованы двумя сепарационными тарелками с вихревыми элементами по входу и выходу, а так же промывочной секцией с двумя массообменными тарелками. Абсорберы по проекту были оборудованы массообменной секцией из 5 контактных тарелок с инжектирующими вихревыми контактно-сепарационными элементами и сепарационной тарелкой с центробежными сепарационными элементами, в фильтрующей секции - тарелка фильтр-патронов и тарелка с центробежными сепарационными элементами.
Разработка сеноманской залежи ЗНГКМ началась в 2001 году после пуска УКПГ-1С. В первый год эксплуатации УКПГ, обнаружен ряд проблем снижающих эффективность подготовки газа: повышенные уносы из сепараторов; образование стойких эмульсий в аппаратах при перемешивании BMР и ДЭГа с конденсатом, не разлагающихся в течение длительного времени и способствующих более интенсивному выносу конденсата в абсорбер; снижение абсорбционной способности ДЭГа по влаге из-за присутствия конденсата уносимого из сепараторов; наличие критического режима абсорберов по производительности, причем этот режим наступает при меньших расходах, чем номинальная (проектная) производительность и как следствие ограниченный по времени ресурс непрерывной, эффективной работы; повышенный унос или прорывы газа в дегазатор при накоплении конденсата в верхней части абсорбера. Многие из перечисленных проблем были решены в первый год эксплуатации УКПГ-1С и учтены при строительстве УКПГ-1С, 2С.
Валанжинские УКПГ ЗНГКМ имеют три ступени сепарации. Сепаратор первичный 10С-1 оснащён одной тарелкой с прямоточно-центробежными элементами ГПР 353 (узлом входа в виде отклоняющей пластины, сетчатым коагулятором). Основным узлом промежуточного сепаратора 20С-2 является тарелка с сепарационными элементами ГПР 515. Низкотемпературный сепаратор 20С-3 оснащён тарелкой сепарационных элементов ГПР 515 и тарелкой фильтрующих элементов ГПР 2331.
После ввода в эксплуатацию в 2011-2012 гг. двух валанжинских промыслов УКПГ-1В, 2В по технологии НТС с дросселем в первый период работы установки был выявлен ряд проблем эффективной работы сепарационных узлов технологических аппаратов. В связи с переходом с дроссельной технологии на турбодетандерную, так как НТС с дросселем летом характеризуется низким выходом товарного нестабильного конденсата, возникает вопрос о качестве газа подаваемого на турбины. Существует требование, согласно которому содержание капельной жидкости на входе в турбодетандер не должно превышать 50 г/тыс. м3. Наряду с этим фактическая эффективность промежуточных сепараторов 20С-2 значительно ниже регламентных требований, уносы жидкости из сепараторов в 50-100 раз и более превышают допустимое количество. Для обеспечения перехода работы установки на низкотемпературную сепарацию с ТДА было принято решение на одной из технологических линий провести пробную модернизацию промежуточного сепаратора с целью снижения капельного уноса жидкости. Модернизацию проводила ДОАО «ЦКБН ОАО «Газпром»» на 2 технологической нитке УКПГ-1В ЗНГКМ.
В данной работе приведен анализ выполненных модернизаций в аппаратах, позволивших повысить эффективность сепарации и абсорбции. Перечислены проблемы возникшие на начальных этапах подготовки газа и пути их решения, дана оценка эффективности выполненных мероприятий.
«ТЕХНИЧЕСКИЕ РЕШЕНИЯ, НАПРАВЛЕННЫЕ НА ПОВЫШЕНИЕ ЭФФЕКТИВНОСТИ ТЕХНОЛОГИЧЕСКИХ ПРОЦЕССОВ ПОДГОТОВКИ ГАЗА»
Черенков Ф.А.
ОАО «Севернефтегазпром»
В ОАО «Севернефтегазпром» ведется работа по реконструкции и техническому перевооружению объектов, направленная на повышение эффективности технологических процессов подготовки газа.
В процессе эксплуатации блоков огневой регенерации ГП 2054.03 поз. 30БР–1-1;2 производства ОАО «Курганхиммаш» были выявлены недостатки по бесперебойному обеспечению горелок газом с существенным превышением расхода газа от установленных норм, а также при сбое розжига одной из горелок образование взрывоопасной смеси.
Работы производились в пять этапов:
Мероприятия первого этапа были направлены на разделение общего трубопровода на две линии подачи топливного газа.
На втором этапе была произведена замена горелок фирмы ОАО «Промгаз» ПГ-М/70 (0,7 МВт) на более мощные автоматизированные производства компании «Weishaupt» (0,95 МВт).
Реализован единый алгоритм автоматического управления интеллектуальными модулями БОР с режимом «Холодный старт», который позволяет производить плавный прогрев блока огневой регенерации до 1500С, также реализована задача «Стабилизации процесса регенерации гликоля» с обеспечением температуры ТЭГа в испарителе (2600х16 мм) достаточной для достижения заданной концентрации регенерированного гликоля при управлении мощностью горелок.
На третьем этапе были разделены топочно-дымовые тракты испарителя БОР с монтажом центральных перегородок, и произвели замену поворотных и дымовых камер.
Для обеспечения дополнительной продувки топочных камер испарителя перед розжигом горелок и при плановом или аварийном останове БОР произвели установку автономных вентиляторов для каждой камеры.
Для исключения разрушения БОР при возможном образовании и возгорании взрывоопасной смеси в топочно-дымовых камерах смонтировали взрывные клапаны Ду 450 на боковых стенках передней дымовой поворотной камеры.
Реконструкция блоков огневой регенерации позволила достичь максимально безопасных условий производства и повышение надежности работы установки регенерации триэтиленгликоля.
«ПРОВЕДЕНИЕ ОПЫТНО-ПРОМЫШЛЕННОЙ ЭКСПЛУАТАЦИИ (ОПЭ) МЕХАНИЧЕСКОГО ОБОРУДОВАНИЯ НА ПРОИЗВОДСТВЕННЫХ ОБЪЕКТАХ ООО «ГАЗПРОМ ДОБЫЧА ЯМБУРГ».
Саньков А.З., Ганеев А.М., Карамышев С.Г.
ООО «Газпром добыча Ямбург»
Одной из важнейших функций ОГМ является разработка и внедрение мероприятий по замене малоэффективного устаревшего оборудования на более высокопроизводительное и эффективное. При этом необходимо учитывать и экономические аспекты данного вопроса.
Зачастую не всегда представляется возможным сделать выбор в пользу того или иного производителя оборудования, предлагаемого проектировщиком или централизованным поставщиком, ввиду отсутствия опыта эксплуатации и работы заявленного оборудования конкретно в наших условиях эксплуатации.
Для решения этой проблемы в нашем Обществе сложилась хорошая практика - при выборе оборудования, проводить опытно промышленную эксплуатацию (ОПЭ) до принятия решения о его применении.
В случае положительного заключения по результатам ОПЭ Обществом направляются рекомендации в ОАО «Газпром», проектным организациям и централизованному поставщику ООО «Газпром комплектация» о применении испытанного оборудования при проектировании, модернизации, реконструкции и комплектации объектов нашего Общества. Наши рекомендации мы также направляем для сведения коллегам в дочерние общества ОАО «Газпром».
В ходе проведения ОПЭ мы проверяем не только работоспособность оборудования (в первую очередь при воздействии низких температур и агрессивной среды - метанола) но и такие характеристики как удобство обслуживания, наличие сервисных структур у производителей/ поставщиков, их «адекватность» и быстрота реагирования на наши замечания, предложения, возникающие в ходе ОПЭ.
Необходимо отметить, что перечень оборудования и материалов, прошедших ОПЭ составляют как отечественные, так и зарубежные образцы.
По результатам ОПЭ были как положительные, так и отрицательные заключения. Были случаи окончания ОПЭ без рекомендаций к применению на наших объектах из-за отсутствия, каких-либо существенных преимуществ (в т. ч. экономических) перед применяемым аналогичным оборудованием.
Система ОПЭ в нашем Обществе позволяет решать сразу несколько задач:
- производственная необходимость в замене вышедшего из строя и неэффективного оборудования (т.к. в большинстве случаев мы проводим ОПЭ именно такого оборудования);
- поиск и внедрение нового альтернативного оборудования, с целью улучшения производительности и эффективности при эксплуатации;
- систематизация полученных результатов ОПЭ оборудования различных производителей, с целью понимания отдельных преимуществ/недостатков, а также их учет при принятии решений о необходимости применения того или иного оборудования и анализе экономической целесообразности такого решения.
«ПРИМЕНЕНИЕ ГДИ ДЛЯ ОПРЕДЕЛЕНИЯ ЗОН ФИЛЬТРАЦИИ В ПЛАСТЕ К ГОРИЗОНТАЛЬНОМУ СТВОЛУ СКВАЖИНЫ»
Д. И. Шустов
Филиал НГДУ, газовый промысел № 2
В последние десятилетия стали массово применять горизонтальные скважины (ГС) при разработке месторождений нефти и газа, при этом возникло много новых задач, которые по необычному механизму течения флюидов в пласте к ГС не могли возникнуть при работе вертикальных скважин. Для горизонтальных скважин главной задачей является определение характера движения жидкости в пласте к горизонтальному стволу.
Для определения характера притока жидкости в ствол скважины очевидно можно было бы с успехом применить известные методы термометрии и расходометрии. И на практике есть уже немало примеров спуска приборов с помощью колтюбинговых установок для замера расходометрией или термометрией зон поступления жидкости в ствол. Однако при этом возникает не только технические проблемы доставки приборов в горизонтальный ствол с последующим замером притока во времени и по длине ствола. Принятые технологии заканчивания скважин с перфорированными хвостовиками приводят к тому, что жидкость часто попадает в хвостовик, сначала двигаясь по затрубному пространству, так как хвостовики не цементируются. При этом сложно выявлять зоны притока термометрией и расходометрией.
В данной работе приводятся примеры оценки механизма движения жидкости к ГС на основе гидродинамических исследований. С помощью кривых восстановления (КВД) давления, записываемых после отработки скважины, или кривых падения давления – после остановки закачки (КПД), определяется в целом средняя проницаемость пласта в зоне дренирования скважины, средний скин-эффект и эффективная длина ствола.
Ниже приведем конкретный практический пример, показывающий, как вести обработку данных исследования нагнетательных ГС. На рис.1 показан график давления, записанный при испытании горизонтального ствола нагнетательной скважины. Выполнено 6 режимов работы, первый - режим закачки с расходом q2 = - 157 м3/сут, далее выполняется режим падения давления.
Рис.1 – График давлений при исследовании горизонтальных скважин (до интенсификации)
Представления о работе горизонтальных стволов можно получить на основе КВД (или КПД) по данным логарифмических графиков производных давления. На рис. 2 приведены три производные КВД для различных режимов течения жидкости к стволам скважин. Все три КВД в начальной своей части имеют кривую в форме полусинусоиды, что является результатом влияния емкости ствола скважины. В нашем анализе рассматривается форма кривых по истечению одного часа замера:
1. Кривая под номером 1 – имеет участок с наклоном i = 0,5 (a - b), который характеризует плоскопараллельное течение к стволу скважины (кривая под номером 1), в конце процесса формируется радиальное течение - i = 0 (участок f - h), оно отражается в виде горизонтальной прямой на диаграмме. Такая форма КВД (или КПД) свидетельствует о том, что течение жидкости к стволу скважины охватывает существенную его часть (или весь ствол) – тогда длина участка a – b должна быть максимальной.
2. Кривая под номером 2 соответствует сферическому течению i = - 0,5 (участок с - d), в конце замера КВД отражает радиальное течение (участок р - s). Такой вид КВД свидетельствует о том, что вскрыта только малая часть ствола, в результате чего и сформировался сферический режим течения, а конце процесса – радиальный.
3. Кривая под номером 3 – соответствует классическому случаю вертикальной скважины с радиальным течением. Здесь нет отклонений конечного участка производной КВД от горизонтальной линии на всем интервале замера.
Рис. 2 – Вид производной давления (КВД) записанной в горизонтальной скважине
Наиболее информативная в нашем практическом примере на рис. 1 – КПД 1. На рис. 3 изображена КПД-1 и ее производная в лог-лог координатах.
|
|
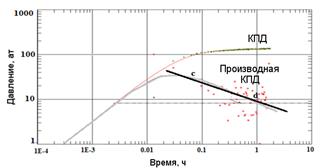
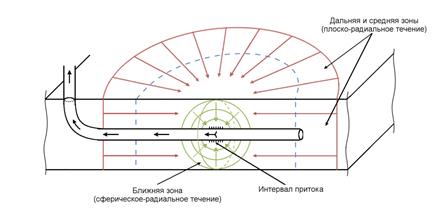
Рис. 3 – а) КПД и производная КПД в билогарифмических координатах; б) схема сферического потока к участку ГС
На графике на рис. 3 а) выделяется прямолинейный наклонный участок с наклоном i = - 0,5, который свидетельствует о появлении тенденции сферического течения (участок с - d). На рис. 3 б) показана схема возможного течения, то есть видим,что работает только очень узкий интервал скважины..
С целью подключения в работу всего ствола скважины была проведена кислотная обработка. Способ обработки нефтяного пласта, вскрытого скважиной с горизонтальным стволом, осуществляется спуском колтюбинговой колонны. Закачку кислоты в пласт осуществляют при равномерном перемещении колонны труб по оси ствола в обрабатываемом интервале продуктивного пласта, а потоку кислоты при выходе из трубы придают вращательное движение. Расходы жидкости при закачке кислоты и давление в скважине при обработке и испытании изображены на рис. 4.
Рис.4. График закачки кислоты и записи КПД
На рис. 5 а представлены КПД и ее производная в билогарифмических координатах, записанная после интесификации скважины. Из графика видно, что после 0,1 ч закрытия скважины на КПД фиксируется прямолинейный участок с наклоном, близким к i = 0,5, что свидетельствует о плоскопараллельном притоке к стволу горизонтальной скважины. То есть, теперь жидкость стала поступать в скважину по большей части ее горизонтального ствола, как это показано на рис. 5 б). Это свидетельство того, что кислотная обработка позволила более равномерно распределить течение жидкости по стволу скважины при нагнетании.
|
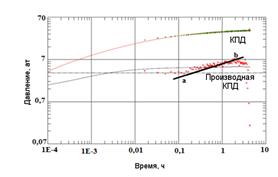
|
Рис.5. а) КПД в лог-лог координатах, записанная после кислотной обработки; б) схема притока жидкости ко всему участку ГС.
Таким образом, выявление тенденций в изменении кривых роста или снижения давления позволяет определить эффективность выравнивания профиля закачки, а также результативность применяемых способов интенсификации. А именно определяется рабочая длина ствола скважины по профилю притока жидкости к нему. Поэтому гидродинамические исследования горизонтальных скважин позволяют так же как и ПГИ и расходометрия определять доминирующие потоки из ствола скважины в пласт при работе нагнетательных скважин.
Секция 3: IT-технологии, автоматизация технологических процессов, метрология, связь