2.3.1. Расчет и выбор основных параметров буровой лебедки
К основным параметрам буровых лебедок относятся мощность, скорости подъема, тяговое усилие, длина и диаметр барабана лебедки. От правильного выбора указанных параметров зависят производительность, экономичность, габариты и масса лебедки, которые существенно влияют на эффективность бурения, транспортабельность и монтажеспособность всей буровой установки.
Мощность лебедки определяется полезной мощностью на ее барабане, которая должна быть достаточной для выполнения спуско-подъемных операций и аварийных работ при бурении и креплении скважин заданной конструкции. Оптимальная мощность буровой лебедки определяется из условий подъема наиболее тяжелой бурильной колонны для заданной глубины бурения с расчетной скоростью 0,4—0,5 м/с [6]:
(2.48)
где - мощность на барабане лебедки, кВт;
—вес бурильной колонны, кН;
— вес подвижных частей талевого механизма, кН;
— расчетная скорость подъема крюка, м/с;
— к.п.д. талевого механизма.
|
|
Мощность лебедки уточняется после выбора двигателей и силовых передач ее привода:
где — мощность, получаемая от вала двигателя, кВт;
— к.п.д. трансмиссии (от вала двигателя до барабана лебедки).
Максимальная скорость подъема ограничивается безопасностью управления процессом подъема и предельной скоростью ходовой струны, при которой обеспечивается нормальная навивка каната на барабан лебедки. Скорость подъема крюка, согласно требованиям безопасности, не должна превышать 2 м/с. Нормальная навивка каната на барабан лебедки, как показывает опыт, обеспечивается при скорости ходовой струны каната не более 20 м/с.
Учитывая известную зависимость скорости ходовой струны от скорости подъема крюка
согласно рассмотренным требованиям, максимальную скорость подъема выбирают из следующих условий:
для талевых механизмов с кратностью оснастки
м/с
для талевых механизмов с кратностью оснастки
м/с
Минимальная скорость подъема — резервная и используется для технологических целей: при расхаживании колонн бурильных и обсадных труб; при ликвидации осложнений и аварий, связанных с затяжкой и прихватом бурильных труб; при подъеме колонны труб через закрытые превенторы; при подъеме колонны труб в случае отказа одного из двигателей привода лебедки. Величина минимальной скорости подъема принимается в установленных практикой бурения пределах:
Отношение предельных скоростей определяет диапазон регулирования скоростей подъема лебедки
Число ступеней передач (скоростей) зависит от типа привода буровой лебедки. При использовании электродвигателей постоянного тока имеем бесступенчатое изменение скоростей подъема в заданном диапазоне регулирования. В зависимости от нагрузки по условию полного использования выходной мощности
, двигателя промежуточные скорости подъема
|
|
где — к.п.д. подъемного механизма от двигателя до крюка;
— вес талевого механизма.
В приводе буровых лебедок от дизеля и электродвигателя переменного тока, обладающие жесткой естественной характеристикой. Число ступеней механических передач буровой лебедки назначается из условия достаточно полного использования мощности двигателей. В связи со ступенчатым изменением веса поднимаемой колонны труб степень использования мощности зависит от числа ступеней передач лебедки и с достаточной точностью определяется выражением
где k — число ступеней передач буровой лебедки.
Целесообразно ограничивать число ступеней передач для лебедок, используемых в бурении скважин глубиной до 3 000 м, к=4, а более 3000 м к=6.
При дизель-гидравлическом приводе число ступеней передач
где — диапазон регулирования частоты вращения гидротрансформатора.
Диапазон регулирования частоты вращения гидротрансформатора ограничивается сравнительно высокими значениями к.п.д. (0,75—0,85) гидротрансформатора, при которых . Расчеты показывают, что благодаря гидротрансформатору число ступеней передач буровой лебедки может быть уменьшено до 2—3.
На рис. 2.10 приведена номограмма для определения числа рабочих слоев навивки каната на барабан. Полученное по номограмме значение х округляют до ближайшего целого числа и затем с учетом первого нерабочего слоя определяют конечное число слоев навивки:
.
Пример. Дано: = 1350 мм,
=2 мм, оснастка талевой системы 5
6,
=750 мм,
=35 мм;
=21,4. Ответ: х =2,35. Принимаем m =3.
Диаметр конечного слоя навивки каната на барабан
(2.49)
где =0,93 — коэффициент, учитывающий уменьшение диаметра навивки вследствие смещения каната в промежутки между витками нижнего слоя.
Средний диаметр навивки
где — диаметр 1-го слоя навивки каната на барабан.
Таблица 2.7
Технические характеристики буровых лебедок ВЗБТ
Лебедка | Б1.02.30.000 | Б7.02.00.000 | Б48.02.00.000 |
Расчетная мощность на входном валу, кВт | |||
Максимальное натяжение ходовой ветви талевого каната, кН | 141,6 | ||
Диаметр барабана, мм | |||
Длина барабана, мм | (нарезка) | ||
Диаметр талевого каната, мм | |||
Масса, кг |
Таблица 2.8
Краткие характеристики буровых лебедок (традиционных) Уралмашзавода
Наименование параметров | ЛБУ-1200 | ЛБУ-1200К | ЛБУ22-720 | ЛБУ-37-1100Д-1 | ЛБУ-1200Д-1 | ЛБУ-1200Д-II | ||
Максимальная грузоподъемность, кН | ||||||||
Расчетная мощность на входе в лебедку, кВт | ||||||||
Диаметр талевого каната, мм | ||||||||
Оснастка | 5х6 | 5х6 | 5х6 | 5х6 | 5х6 | 5х6 | ||
6х7 | 6х7 | 6х7 | ||||||
Число скоростей вращения подъемного вала | ||||||||
Размеры подъемного барабана, мм диаметр длина | ||||||||
Тормозная система | Ленточный тормоз с управляющим балансиром | |||||||
Тормоз вспомогательный | Гидродина- мический УТГ-1450 | Электромагнитный тормоз | УТГ-1450 | УТГ-1450 или ЭМТ-4500 | ||||
ТЭП-4500 | ТЭИ-710 | ТЭИ-800 | ||||||
Размеры тормозного шкива, мм диаметр ширина | ||||||||
Привод дополнительный | - | Привод дополнительный** | РПД*** | РПД*** | - | Привод дополнительный** | ||
Цепи | 2Н-50,8 | 3Н-50,8 | 3Н-50,8 | 4Н-50,8 | 2Н-50,8 | 3Н-50,8 | ||
2Н-50,8 | 2Н-50,8 | 2Н-50,8 | 2Н-50,8 | |||||
ПР-12,7-1820-1 | ПР-12,7-1820-1 | 6Н-38,1 | ||||||
ГОСТ13568-75 | ГОСТ13568-75 | ПР-12.7-1820-1 | ||||||
ГОСТ13568-75 | ||||||||
Муфты | 2МШУ-1070 | МШУ-1070 | МШУ-1070 | 2МШУ-1070 | 2МШУ-1070 | 2МШУ-1070 | ||
МШ-700 | 2МШ-700 | 2МШУ-500 | МШУ-1070 | МШ-700 | МШ-700 | |||
2МШ-500 | 2МШ-500 | зубчатые | 2МШУ-500 | 2МШ-500 | 2МШ-500 | |||
кулачковые | зубчатые | зубчатые | ||||||
Габаритные размеры, мм длина ширина высота | 2420* | |||||||
Масса, кг | 40450 с системой охлаждения тормоза ТЭИ-800-60 | (с УТГ-1450) | ||||||
* Высота без бака гидродинамического тормоза.
|
|
** Привод дополнительный предназначен для подъема и опускания вышки, для подъема бурильных труб и аварийных работ.
*** Функции РПД, кроме указанных в дополнительном приводе регулирование подачи долота на забой.
2.3.2. Кинематика подъемного механизма
Задача кинематики — определение скоростей и ускорений подъемного механизма. При этом заданными являются высота подъема, кинематическая схема и размеры звеньев подъемного механизма, частота вращения и характеристика используемого двигателя.
При спуско-подъемных операциях высота подъема h несколько превышает длину бурильной свечи l, т. е. 1,02 l. Это обусловлено возможностью установки бурильной колонны на клинья либо элеватор. При спуске бурильная колонна приподнимается для освобождения клиньев либо элеватора, поэтому перемещения при спусках и подъемах бурильных свечей примерно одинаковые.
Изменения скорости за время подъема и спуска одной свечи изображаются тахограммой. Для подъемных механизмов характерна трехпериодная тахограмма подъема, имеющая трапецеидальную форму (Рис. 2.11.). В первый период происходит разгон барабана лебедки, чему соответствует ускоренное движение крюка со скоростью, возрастающей от нуля до начальной установившейся Характер изменения скорости крюка в период разгона зависит от привода лебедки и навыков управляющего ею бурильщика. Режим разгона буровой лебедки существенно не влияет на продолжительность подъема. Однако для снижения динамических нагрузок ускорение при разгоне должно быть минимальным. При линейном нарастании скорости, как рис. 2.11., имеем
;
,
где — ускорение крюка при разгоне, м/с2;
— начальная установившаяся скорость крюка, м/с;
— продолжительность разгона, с;
— путь крюка в период разгона, м;
— угол наклона кривой скорости.
|
|
Второй период соответствует установившемуся движению крюка, при котором двигатель и барабан лебедки вращаются с постоянной частотой. Скорость подъема в период установившегося движения
(2.50)
где — диаметр навивки каната на барабан лебедки, м;
— передаточное число трансмиссии лебедки;
— кратность оснастки подъемного механизма.
Вследствие изменения диаметра навивки при переходе каната на каждый последующий слой на тахограмме скорость подъема в период установившегося движения изображается ступенчатой прямой линией. В кинематических расчетах пользуются средней установившейся скоростью подъема
где — конечная установившаяся скорость подъема крюка, определяемая по диаметру последнего (конечного) слоя навивки каната.
Средняя установившаяся скорость подъема рассчитывается также по среднему диаметру навивки каната на барабан лебедки
(2.51)
В практических расчетах, согласно рекомендациям Уралмашзавода, максимальная скорость спуска принимается в зависимости от длины свечи l:
l, м......... 18 24 27 36
м/с..... 2,5 2,9 3,1 3,6
2.3.3. Подъемная характеристика
Подъемная характеристика рассчитывается в результате совместного рассмотрения конструктивно-кинематических параметров лебедки и механической характеристики используемых двигателей.
Буровые лебедки с приводом от дизелей и электродвигателей переменного тока имеют ступенчатую подъемную характеристику (рис. 2.12, а),расчет которой проводится по номинальным мощности и частоте вращения используемых двигателей:
скорость подъема крюка на i -й передаче:
(2.52)
предельная нагрузка (кН) на крюке на i -й передаче:
(2.53)
где — номинальная мощность двигателя, кВт;
— к.п.д. трансмиссии от двигателя до подъемного вала на i -й передаче;
— к.п.д. талевого механизма;
— вес подвижных частей талевого механизма.
Лебедки с дизель-гидравлическим приводом имеют непрерывно-ступенчатую тяговую характеристику (рис.2.12, б).В этом случае скорости подъема и предельные нагрузки на крюке рассчитываются по мощности и соответствующей ей частоте вращения выходного вала гидротрансформатора, значения которых определяются из совместной характеристики дизеля и гидротрансформатора.
Лебедки с приводом от двигателей постоянного тока имеют бесступенчатую подъемную характеристику. Скорости подъема и нагрузки на крюке в этом случае рассчитываются из условия постоянства используемой мощности двигателя:
(2.54)
Пример 2.8. Найти частоты вращения подъемного вала лебедки ЛБУ-1100. Коробка перемены передач (рис. 2.13) получает мощность от силового привода установки на ведущий вал с помощью четырехрядной цепной передачи. На этом валу на шпонках закреплены две цепные звездочки z=27, передающие две частоты вращения ведомому валу коробки через цепные колеса z = 52 и z=34, находящиеся на валу на подшипниках качения отключаемые с помощью двусторонней зубчатой муфты.
Третье цепное колесо z=34 закреплено на ведущем валу на подшипниках и включается зубчатой муфтой, а затем передает вращение на ведомый вал через цепное колесо z=27, установленное на валу на шпонке. Таким образом, ведомый вал получает от ведущего три частоты вращения. При помощи двух цепных передач 21x81 и 39x40 число частот вращения подъемного вала увеличивается до шести. Барабан от цепных колес z = 81 и z= 40 включается с помощью шинно-пневматических муфт 7 и 12.
Вращение на ротор 8 от КПП 5 передается включением цепных передач 39х40 и 40x33. Ротор включается шинно-пневматической муфтой МШ500 9.
Если принять частоту вращения ведущего вала КПП равной 340 б/мин, то для определения частоты вращения подъемного вала лебедки надо сделать следующие вычисления:
Пример 2.9. Определить скорости подъема крюка, зная частоту вращения подъемного вала ni (из примера 2.8) и расчетный диаметр барабана D p.
Примем D р= D p2=0,84 м.
Скорость подъема крюка
(2.55)
где u тc = 8 — число рабочих струн при оснастке 4х5; 60 —для перевода частоты вращения вала в 1 мин в частоту вращения в 1 с.
В табл. 2.8. приведена техническая характеристика буровых лебедок, серийно выпускаемых отечественной промышленностью.
Скорости крюка (в м/с):
«Тихие» «Быстрые»
Скорость навивки каната на барабан при оснастке 4х5 в 8 раз выше скорости подъема крюка и составит соответственно: 2; 3,04; 4,88; 7,36; 11,28; 17,92 м/с. При оснастке 5x6 скорости навивки каната на барабан будут в 0,8 раза меньше, т.е. 1,6; 2,43; 3,9; 5,88; 9,02 и 14,34 м/с.
Пример 2.10. Определить нагрузки на крюке при различных скоростях подъема (υ к i берутся из примера 2.9). Вес подвижной части талевой системы G тс = 100 кН, оснастка 4х5.
Мощность на подъемном валу лебедки ЛБУ-1100
где N max = 1000 кВт — максимальная мощность привода лебедки из технической характеристики лебедки.
Подъемная сила (в кН) на крюке при различных скоростях его подъема
(2.56)
где ηтс — к.п.д. талевой системы; ηл = 0,9 — к.п.д. лебедки.
При u тc = 8 из выражения ηтс =1—0,02 u тc
Вес колонны (в кН), который может быть поднят на различных скоростях:
Пример 2.11. Для установки БУ5000 с лебедкой ЛБУ-1100 при оснастке талевой системы 4х5 определить число свечей длиной l =25 м из труб диаметром 114 мм, которые могут быть подняты на третьей скорости.
Исходные данные: мощность на подъемном валу лебедки 800 кВт; частота вращения вала лебедки 111 об/мин (см. пример 2.8); диаметр барабана лебедки 0,75 м; вес подвижной части талевой системы G тс =100 кН; вес 200 м утяжеленных бурильных труб G убт=380 кН.
Скорость подъема крюка на третьей скорости
где D p=0,84м —средний диаметр барабана при двух рядах навивки каната; u тc —8 —кратность полиспаста талевой системы.
Тогда
Максимальный вес труб, поднимаемых из скважины на третьей скорости, P к3=892 кН (из примера 2.10).
Число свечей из 114-мм труб, которое можно поднять на третьей скорости:
![]() | |||
![]() |
=
где qбт=300 Н/м—вес 1 м труб; ρр=1,5 и ρс=7,8 —плотности соответственно бурового раствора и стали.
Следовательно, на третьей скорости можно поднимать 84 свечи и УБТ, находящиеся над долотом.
2.3.4. Расчет дисково-колодочного тормоза
Тормоз предназначен для выполнения следующих функций:
- фиксация остановленной системы в заданном положении талевого блока при СПО с целью разгрузки основного электродвигателя;
- торможение спускаемой колонны при отказе электродвигателя (основного тормоза) и срабатывании блокировок (разовый эпизодический режим).
![]() | ![]() |
Рис. 2.14. Расчетная схема дискового тормоза 1 – тормозной диск; 2 – тормозные колодки | Рис. 2.15. Тарельчатая пружина |
Расчетная схема тормоза представлена на рис. 2.14. На рис. 2.15 представлена тарельчатая пружина, применяемая в тормозе. Основными элементами тормоза являются тормозной диск 1 и две тормозные колодки 2. В нормальном замкнутом положении колодки 2 прижимаются к диску с помощью пружин, а в расторможенном – колодки отводятся гидроцилиндрами, сжимающими пружины.
Устройство тормоза представлено на рис. 2.16, где на стойке 1 с помощью проставки 2 крепятся два корпуса 3. Тормозные колодки 4 соединяются с накладками 5 с помощью хомута 6. В корпусе 3 находится стакан для размещения комплекта тарельчатых пружин 7. Внутри корпуса 3 находится также гидроцилиндр 8 с поршнем. С торцов устанавливаются крышки 10, которые закрывают корпус с помощью болтов 11. В центре корпуса установлен палец 12, на котором с помощью гайки жестко посажен поршень 9. С левой стороны палец, с помощью гайки, жестко соединен с накладкой 5, а справой – с помощью гайки 13 осуществляется выбор зазоров и необходимый натяг сборки пружин для обеспечения необходимого рабочего хода и силы прижатия тормозных колодок к диску. Герметизация гидроцилиндра и поршня осуществляется резиновыми кольцами 14, 15, 16. Соединение стойки с проставкой осуществляется болтовыми соединениями 17. Принцип действия тормоза – нормально замкнут, то есть комплект пружин под действием усилия предварительного сжатия перемещает тормозную колодку 4 (совместно с пальцем 12, стаканом и накладкой 5) и прижимает ее к тормозному диску.
Для выключения тормоза (то есть для растормаживания) в гидроцилиндр подается рабочая жидкость под давлением, поршень 9 вместе с пальцем 12, накладкой 5 и тормозной колодкой 4 перемещается вправо, при этом комплект пружин сжимается. Рабочий ход до 7 мм.
Максимальный тормозной момент будет при торможении спускаемой колонны при отказе электродвигателя.
При этом момент на барабане равен
,
где М1 – статический момент на барабане от натяжения тяговых концов талевого каната при установившемся движении спускаемой в скважину колонны труб; М2 – динамический момент от дополнительного усилия в тяговых струнах, вызванного замедлением масс системы при торможении поступательно движущихся масс; М3 – динамический момент от замедления вращающихся масс системы, принимается равным 5% от суммы (М1 + М2); К = 1,2 – коэффициент запаса тормозного момента.
,
,
где Vторм = 0,2 м/с – расчетная скорость спуска обсадной колонны; g = 9,81 м/с2 – ускорение свободного падения; tторм = 3 с – расчетное время торможения.
.
Таким образом, момент на барабане
.
Момент на тормозном диске
.
Расчетная схема дискового тормоза представлена на рис. 14.83.
Требуемая тормозная сила, необходимая для создания МТ
.
Принимаем диаметр тормозного диска DT =730 мм, толщина диска ; размеры накладки для тормозной колодки, b=h= 200 мм, площадь накладки,
; радиус расположения центра колодки RT =25 см. Принимаем 2 поверхности трения (n=2 колодки) в одном тормозе.
Определяем требуемую силу зажима тормозных колодок
.
Принимаем фрикционный материал в тормозе – лента асбестовая тормозная ЛАТ-2 ГОСТ 1198-78, допускаемое удельное давление , коэффициент трения по стали не менее
.
Силу трения прижатия обеспечиваем тарельчатыми пружинами по ГОСТ 3057-79 (см. рис. 2.14). Выбираем пружины 1-1-2-125-63-6,3х3 с максимальным рабочим усилием одной пружины (при максимальной деформации ) Q1max =64 кН. Минимальное рабочее усилие одной пружины (при минимальной деформации
) Q1min =59,2 кН. Принимаем максимально допускаемой износ колодок
, тогда необходимое количество пружин будет равно
.
Принимаем количество пружин в комплекте z = 9.
Определяем давление в цилиндре (см. рис. 14.85) для уравновешивания усилия пружин
;
,
где s – площадь поршня; DH, dB – наружный и внутренний диаметры поршня, DH = 180 мм, dB = 80 мм.
.
Определяем действующее удельное давление в тормозных колодках
.
Определяем необходимое количество дисковых тормозов
,
где n = 2 – количество поверхностей трения одного тормоза.
Принимаем количество тормозов m = 2.
Если принять диаметр тормозного диска DТ =1200 мм, а RT =475 мм, то требуемая тормозная сила на диске будет
,
и требуемая прижимная сила, зажимающая колодки
.
Тогда требуемое количество дисковых тормозов будет равно
.
То есть, одного тормоза будет достаточно для торможения системы. Второй тормоз может быть рекомендован в качестве резервного для повышения надежности тормозной системы.
2.3.5. Расчет ленточного тормоза
Тормозной момент, создаваемый ленточным тормозом в результате трения между фрикционными колодками и тормозными шкивами, должен удовлетворять условию
(2.57)
где — вращающий момент, Нм;
— коэффициент запаса торможения.
Вращающий момент зависит от нагрузки на крюке и возрастает по мере углубления скважины. Расчетная величина вращающего момента определяется весом наиболее тяжелой колонны труб, принимаемым с некоторым запасом, равным допускаемой нагрузке на крюке:
(2.58)
где — допускаемая нагрузка на крюке талевого механизма буровой установки, Н;
— вес подвесных частей талевого механизма, Н;
— средний диаметр навивки каната на барабан, м;
— к.п.д. подъемного вала лебедки;
— к.п.д. талевого механизма;
— кратность оснастки талевого механизма.
Запас торможения принимается в зависимости от режима работы лебедки. Учитывая крайне редкое использование лебедки при нагрузках, равных допускаемой нагрузке на крюке, в расчетах ленточного тормоза достаточен коэффициент запаса торможения [ ]= 1,5.
Тормозной момент, создаваемый ленточным тормозом:
(2.59)
где Т — натяжение набегающего конца ленты, Н; t — натяжение сбегающего конца ленты, Н; — диаметр тормозного шкива, м; z — число тормозных шкивов.
Натяжение t сбегающего конца ленты зависит от усилия на рукоятке тормоза, соотношения плечей рычагов и к.п.д. привода тормоза. Натяжение Т набегающего конца ленты с достаточной для практических расчетов точностью определяется по известной формуле Эйлера, устанавливающей соотношение между усилиями на концах гибкой нити:
(2.60)
где - коэффициент трения между шкивом и тормозной колодкой;
- угол обхвата тормозного шкива лентой, рад.
После подстановки значений Т и t формула (2.59) принимает вид
(2.61)
Контактное давление (в Па) возникает в результате натяжения ленты между шкивом и тормозными колодками:
(2.62)
где S — текущее натяжение ленты, Н; В — ширина тормозной колодки, м.
Максимальное контактное давление возникает от натяжения набегающего конца ленты (S = T):
По дуге обхвата тормозного шкива контактное давление изменяется и на сбегающем конце ленты имеет минимальную величину:
Для обеспечения достаточной долговечности фрикционной пары контактное давление не должно превышать допускаемого значения:
По допускаемому контактному давлению предельное натяжение набегающего конца ленты составляет:
Подставляя значение предельного натяжения ленты в формулу (2.61), можно определить величину тормозного момента ленточного тормоза по допускаемому контактному давлению:
(2.63)
Из полученной формулы следует, что при заданном допускаемом контактном давлении, зависящем от материалов фрикционной пары, тормозной момент ленточного тормоза возрастает пропорционально ширине и квадрату диаметра тормозного шкива. Согласно этому, при проектировании тормозной момент лебедок выгоднее повышать за счет диаметра тормозных шкивов, чем путем увеличения их ширины.
Диаметр тормозного шкива, согласно формуле (2.63), с учетом необходимого тормозного момента ( и допускаемого контактного давления
(2.64)
В табл. 2.9 приведены значения в зависимости от коэффициента трения и угла обхвата шкивов.
Таблица 2.9.
Значения
Угол обхвата ![]() | Коэффициент трения ![]() | |||||
градус | рад | 0,2 | 0,25 | 0,3 | 0,35 | 0,4 |
4,71 | 2,57 | 3,25 | 4,10 | 5,20 | 6,60 | |
5,23 | 2,85 | 3,72 | 4,81 | 6,24 | 8,12 | |
5,75 | 3,16 | 4,25 | 5,63 | 7,48 | 10,01 | |
6,02 | 3,33 | 4,50 | 8,09 | 8,32 | 11,10 |
В табл. 2.10 приведен пример расчета тормозного момента и размеров ленточного тормоза буровой лебедки.
Таблица 2.10.
Расчет тормозного момента и выбор размеров
ленточного тормоза буровой лебедки
Исходные и расчетные величины | Единицы измерения | Обозначения | Способ определения | Численное значение |
Максимальная нагрузка | Н | ![]() | Задано | 12 ![]() |
Вес подвижных частей талевой системы | Н | ![]() | » | 6 ![]() |
Кратность оснастки | ![]() | » | ||
Диаметр барабана | м | ![]() | » | 0,7 |
Коэффициент запаса торможения | ![]() | Принимаем | 1,5 | |
к п. д. подъемного вала | ![]() | По табл. | 0,97 | |
Материал колодок | ФК-24А | |||
Коэффициент трения | ![]() | По табл. | 0,3 | |
Угол обхвата | рад | ![]() | Принимаем | 4,71 |
Число тормозных лент | ![]() | » | ||
Средний диаметр навивки | м | ![]() | ![]() | 0,78 |
Допускаемое контактное давление | Па | ![]() | Принимаем | 12 ![]() |
Тормозной момент | Нм | ![]() | По формуле (2.61) | 0,9 ![]() |
Ширина тормозной колодки | м | ![]() | Принимаем | 0,22 |
Натяжение концов тормозной ленты: | ||||
сбегающего | Н | ![]() | По формуле (2.61) | 0,52 ![]() |
набегающего | Н | ![]() | По формуле (2.60) | 1,64 ![]() |
Пример 2.12. Определить усилия натяжения набегающего и сбегающего концов тормозной ленты и проверить давление колодок на барабан.
Исходные данные: максимальная нагрузка на крюке G к = 1,7 МН; диаметр барабана лебедки ЛБУ-1100 D б=0,75 м; оснастка талевой системы 4х5; диаметр тормозного шкива 1,45 м; ширина тормозной ленты 0,23 м; материал колодок — ретинакс; допустимая удельная нагрузка σmax=0,8, а σmin =0,5 МПа.
Натяжение набегающего на барабан ведущей струны каната при торможении
(2.65)
где G тс= 0,1 МН — вес подвижной части талевой системы; u тc = 8 - кратность талевой системы; ηтc = 0,83 — к.п.д. талевой системы; k д=1,1—коэффициент динамичности.
Момент на барабане
(2.66)
D бр =. D р3= 0,98 м — расчетный диаметр барабана с навитым канатом по третьему слою, при котором момент на барабане будет наибольшим).
Натяжение (в кН) набегающих концов лент (рис 2.17)
(2.67)
где k = 1,2 —коэффициент запаса; F т— окружное тормозное усилие, кН
(2.68)
где μ — коэффициент трения колодок, примем μ = 0,35; α — угол обхвата тормозного шкива лентой, рад, α =270:360×2π = 4,71; D т=1,45 м — диаметр тормозного шкива.
Натяжение сбегающих концов лент
(2.69)
Максимальное давление колодок на тормозной шкив
(2.70)
(В —ширина тормозной ленты, м).
Полученное давление допустимо, так как σmin < p max < σmax.
Минимальное давление колодок на тормозной шкив
Среднее давление колодок на шкив
(2.71)
Средняя удельная нагрузка
Следовательно, р ср < σср, что допустимо.
Пример 2.13. Определить усилие на тормозном рычаге лебедки.
Момент на коленчатом валу тормоза
(2.72)
(r =0,03 м — радиус рычажка коленчатого вала тормоза).
Необходимое для торможения усилие на тормозной рукоятке рычага
(2.73)
Здесь G р=500 Н—вес тормозного рычага; L =0,35 м - расстояние от центра тяжести тормозного рычага до оси вала (см. рис.2.17); а = l· соsψ; l =1,6 м - длина рукоятки тормоза; η = 0,8 — к.п.д., учитывающий трение в опорах, амортизаторе и др.
При ψ = 60º и а =1,4 м
при ψ =30 ° и а =0,8 м
Так как усилие рабочего не должно быть более 0,25 кН, то для создания необходимой силы торможения используется пневматический цилиндр.
Пример 2.14. Проверочный расчет тормозной ленты. Тормозные ленты изготовляют из стали 50.
Напряжение растяжения в сечении ленты определяем по формуле
Площадь сечения ленты (в м2)
где δ=0,006 м—толщина ленты; b =0,22 м — ширина ленты; z = 3 — число отверстий; d =0,014 м — диаметр отверстия.
При обрыве одной ленты тормозной момент передается на другую ленту, которая должна обеспечить торможение опускаемой колонны. В этом случае σmax =2 δл =170 МПа, что для стали 50 вполне допустимо.
Конец ленты закреплен 12-ю заклепками, работающими на двойной срез. Напряжение среза в заклепках
= 61 МПа;
σз=61 МПа, что значительно ниже допустимого.
Здесь Sн1= Sн/2 — натяжение набегающего конца одной ленты; n =12- число заклепок; d з = 0,014 м — диаметр заклепок.
2.3.6. Динамика торможения. Безопасные скорости спуска
Динамические нагрузки, испытываемые тормозом буровой лебедки, обусловлены снижением скорости поступательно движущихся и вращающихся масс. На рис. 2.18 показаны моменты сил, действующие на тормоз в период торможения. Статический момент направлен в сторону вращения барабана лебедки, тормозной момент
— против вращения и в рассматриваемой схеме лебедки действует при спуске по часовой стрелке, а при подъеме — против часовой стрелки. Если за условное положительное направление принять действие моментов, направленных против часовой стрелки, то уравнения вращательного движения можно написать в следующем виде:
для торможения при спуске
(2.74)
где I — приведенный к валу барабана лебедки момент инерции вращающихся и поступательно движущихся масс; — угловое замедление вала барабана лебедки;
— статический момент;
и
—тормозные моменты соответственно при спуске и подъеме.
Приведенный момент инерции определяется из равенства кинетической энергии приведенной массы и фактически распределенных масс с учетом потерь на трение. Для упрощения расчетов можно пренебречь кинетической энергией канатных шкивов, не имеющей существенного влияния. В этом случае справедливо равенство
(2.75)
где — угловая скорость вала барабана;
— масса подвижных частей талевого механизма и подвешенной колонны труб; v — скорость поступательно движущихся масс;
— к.п.д. талевого механизма.
Из рассматриваемого равенства приведенный к валу барабана момент инерции вращающихся и поступательно движущихся масс
Так как зависимость между скоростями барабана лебедки и крюка
полученную формулу можно представить в следующем виде:
(2.76)
где
— средний диаметр навивки каната на барабан; — кратность оснастки талевого механизма.
Формулы для определения моментов инерции некоторых типовых деталей приведены в таблицах справочной литературы. Для деталей и узлов сложной конструкций момент инерции определяется экспериментальным путем и по маховому моменту
где — маховый момент относительно оси вращения, равный произведению приведенного веса вращающихся деталей подъемного вала на квадрат диаметра приведения,
(например, маховый момент барабана буровой лебедки ЛБУ-1200 К вместе с подъемным валом и другими вращающимися деталями
).
При равномерном торможении угловое замедление вала барабана лебедки
где и
— начальная и конечная угловая скорость вала барабана лебедки,
;
— время торможения, с.
В результате торможения конечная скорость становится равной нулю, тогда имеем
где n — начальная частота вращения вала барабана, об/мин.
Статический момент с учетом к.п.д. талевого механизма при спуске
при подъеме
Тормозной момент при спуске из формулы (2.74)
После подстановки значений I, и
имеем
Учитывая, что , полученную формулу можно представить в более удобном для практических расчетов виде
(2.77)
Для безопасного торможения следует ограничить величину тормозного момента, необходимого для остановки спускаемого груза:
где — тормозной момент ленточного тормоза буровой лебедки;
— запас торможения.
Предельную частоту вращения подъемного вала лебедки при спуске в зависимости от нагрузки на крюке и продолжительности торможения можно определить, пользуясь рассматриваемым условием из уравнения (2.78):
(2.78)
В табл. 2.11 приведен пример расчета предельных скоростей спуска, ограниченных постоянным запасом торможения.
Таблица 2.11
Расчет предельной скорости спуска колонн труб
|
|
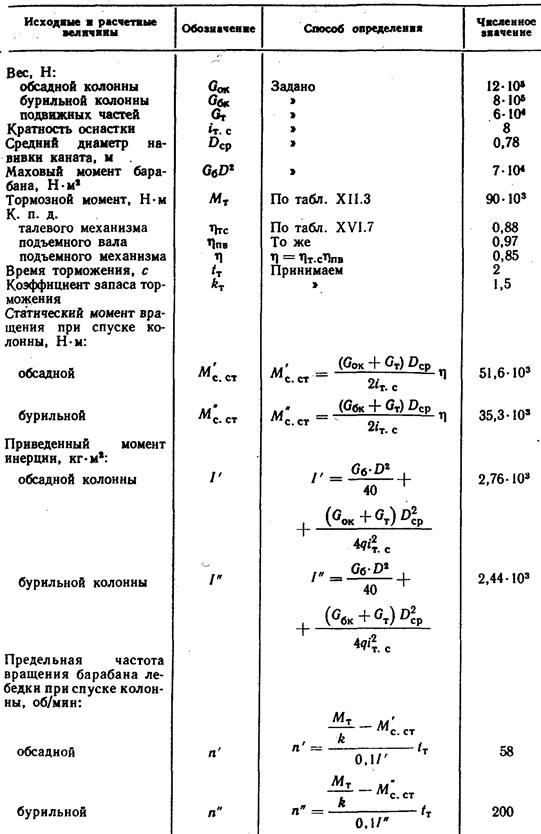
Продолжение табл. 2.11
Исходные расчетные величины | Обозначение | Способ определения | Численное значение |
Предельная скорость спуска колонны, м/с: обсадной | ![]() | ![]() | 0,30 |
бурильной | ![]() | ![]() | 1,02 |
2.3.7. Согласование работы гидродинамического и ленточного тормозов
Для ускорения спуска и безопасной остановки колонн бурильных и обсадных труб необходимо обеспечить согласованную работу гидродинамического и ленточного тормозов буровой лебедки. Угловые ускорение и скорость подъемного вала лебедки при спуске с использованием гидродинамического тормоза определяются из уравнения вращательного движения
(2.79)
где I — момент инерции вращающихся масс лебедки и гидродинамического тормоза; — угловое ускорение барабана лебедки и ротора тормоза; М
— вращающий момент, создаваемыйпод действием спускаемых масс; М
— тормозной момент, создаваемый гидродинамическим тормозом. Из рассматриваемой формулы
(2.80)
Как видно, угловое ускорение пропорционально разности вращающего момента, создаваемого собственным весом спускаемых масс, и тормозного момента гидродинамического тормоза.
Вращающий момент, действующий на барабан лебедки, изменяется в зависимости от веса G спускаемой колонны труб:
(2.81)
Для практических расчетов и изучения внешней характеристики гидродинамических тормозов пользуются формулами тормозного момента, известными из теории лопастных гидромашин:
(2.82)
(2.83)
где — коэффициент гидравлического момента; D — наружный диаметр образующегося при вращении ротора кольца жидкости, принимаемый равным диаметру ротора, d — внутренний диаметр кольца жидкости, зависящий от уровня наполнения тормоза, м; п — частота вращения ротора, об/мин.
Коэффициент гидравлического момента определяется экспериментально и является безразмерной величиной, зависящей от формы рабочей полости, геометрических параметров и числа лопаток гидродинамического тормоза. С увеличением
, возрастает тормозной момент гидродинамического тормоза при одинаковых диаметре и частоте вращения его ротора.
Коэффициенты гидравлического момента рассматриваемых тормозов при полном наполнении приведены ниже:
УТГ-1000 | 0,32 | ТГ-1200 | 0,29 |
УТГ-1450 | 0,27 | ШТГ-1-1200 | 0,29 |
Тормозной момент гидродинамического тормоза в процессе разгона нарастает пропорционально квадрату частоты вращения ротора, как видно из выражения (2.83). Если в процессе спуска тормозной момент, создаваемый гидродинамическим тормозом, достигает величины действующего вращающего момента, то ускорение становится равным нулю [см. формулу (2.80)] в дальнейший спуск происходит при равномерном вращении барабана лебедки.
Частота вращения барабана лебедки на участке равномерного спуска определяется из равенства вращающего и тормозного моментов. Пользуясь формулами (2.81) и (2.83), из указанного равенства имеем
(2.84)
Для согласования работы гидродинамического и ленточного тормозов лебедки необходимо обеспечить условие: , где
— предельная частота вращения барабана лебедки, допускаемая по запасу торможения ленточного тормоза.
На рис. 2.18 кривая 5 выражает предельную частоту вращения барабана лебедки в зависимости от веса спускаемой колонны труб при одинаковой продолжительности и постоянном запасе торможения ленточного тормоза. Кривая 5 построена по ранее приведенной формуле (2.85), которая после преобразования имеет вид
(2.85)
где — тормозной момент ленточного тормоза,
м;
— вращающий момент, Н • м; k — коэффициент запаса торможения; I — момент инерции вращающихся масс буровой лебедки и гидродинамического тормоза,
м2;
— время торможения, с.
Кривые 1—4, построенные по формуле (2.83), выражают зависимость частоты вращения гидродинамического тормоза при различных уровнях наполнения от вращающего момента, действующего на барабан лебедки при спуске.
При весе колонны труб достигается максимально допустимая скорость спуска
,соответствующая ординате точки пересечения кривых 1 и 5. Дальнейший рост скорости в результате увеличения веса спускаемой колонны труб становится опасным для ленточного тормоза буровой лебедки из-за чрезмерных инерционных нагрузок, возникающих при торможении. Поэтому при наращивании последующей свечи скорость спуска колонны труб необходимо снизить. Для этого