1
2
3
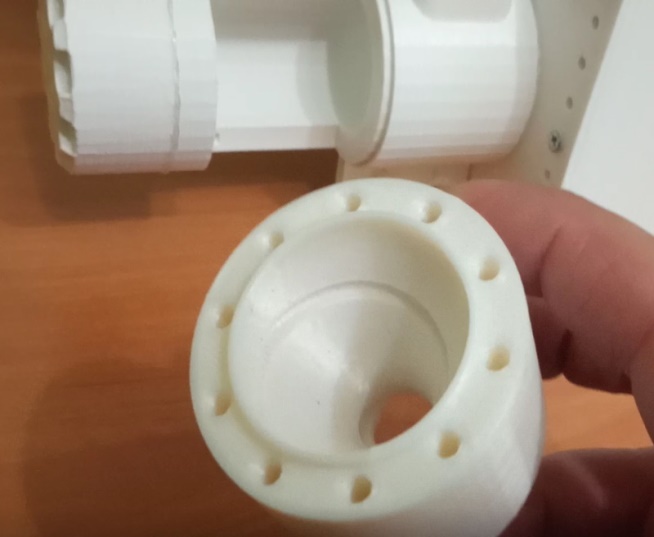
Технічна схема ударного преса
Технічна схема циліндра
Технічна схема плунжера
Технічна схема одноканальної головки з кутом атаки 45°
Технічна схема фільєри одноканальній головки
Готові деталі циліндра плунжера і змінних головок
|
|
Целиндр з головками в сборі
1) плунжер ударний 2) циліндр стиснення деревних відходів в сборі 3) укорочений циліндр зі змінних головок
Чому ми пропонуємо стрічкових камер.
У стандартних пресах стійкість до прес-інезу відбувається через бічні сили «суперечливих» і сили тертя матеріалу проти стінки циліндра.
Ми пропонуємо стрічкових камер. Ми маємо наступні цілі:
1) зменшити розмір прес-камери і стиснути матеріал (50-70%);
2) зменшити розмір преса і збільшити його ефективність.
Ми збільшуєте ефективність роботи преси, створюючи спіраль, на поверхні конуса, пресування.
1
2
1. спіраль дозволяє поліпшити підштовхування до стінки брикетольного циліндра. 2. прилипання і формування зі зрізаних гілок плодових дерев, допомагає спіралі на брикеті на камері, зменшуючи тертя від стіни.
Ефект від винної пробки-знизити силу тертя через обертання.
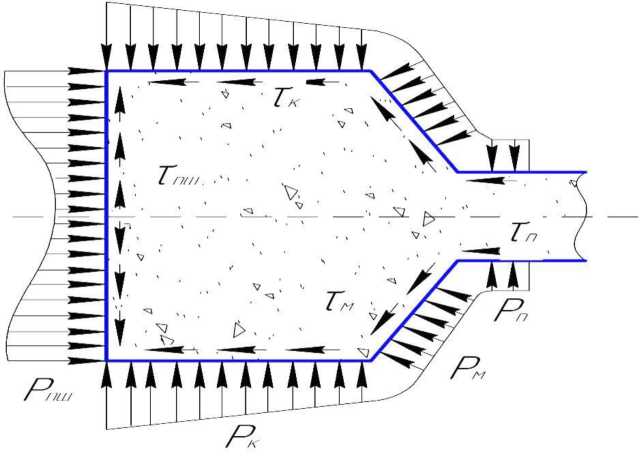
Малюнок 1.2.
Визначаємо зусилля на пресувальному плунжеру за формулою:
де P max = 6,0 МПа=6,0·106 Па=6,0·106
Тоді Fпл=6,0·106·0,002=12·103 Н.
Демонстрація роботи плунжера в циліндрі
1) плунжер ударний 2) циліндр стиснення деревних відходів в сборі
3) відео огляд роботи плунжера в циліндрі
|
|
Теоретичні дослідження процесу формування брикету з подрібненої тріскі в закрьітой матриці під дією ударної навантаження Визначення пружних характеристик конгломерати древесньїх частинок
Спрессованнмй брикет, що складається з связанньїх між собою частинок, що не являетея сплошньїм однородньїм тілом. Тим не Менс, поскольку зв'язку між частинками в брикеті досить прочньї, до процесу брикетірованія можна застосувати, положення механіки деформованого твердого Таке припущення дозволяє в описах пружних властивостей подрібненої тріскі керуватися зкеперіментальнммі данньї- ми, полученньїмі для цільної тріскі Однак прессуемьій матеріал являетея конгломератом древесньїх частинок, що істотно впливає на його властивості Для опису пружних властивостей ущільнюється матеріалу целесо- образно скористатися методами, тобто використовувати техніч ське наближене рішення. Зто виправдано главньїм чином тим, що рассматріваемьій матеріал не володіє великою стабільністю механи- чеських властивостей, і використання точних методів рішення, значно усложпяющіх вьічісленія, не дає істотного збільшення точності. Данньїй підхід, стосовно древесньїм матеріалам, описаний в робо тах А.І. Вігдоровіча, А.А. Позднякова, Г.В. Сагалаєва і ін. Учених. У його основу покладено припущення про рівність компонентів тензора напряженій або тензора деформацій окремої частіцьі і конгломерати частіц - брикету. Вважаючи розподіл древесньїх частинок в межах некоторьіх кутів равномерньїм, оередненньїе значення модулів пружності Аук конгломерати древесньїх частинок можна визначити по ізвестньїм формулами як матема- тичні очікування величин (переменньїмі <ро, 6о, у / о позначення угльї раз- викиду частинок, рис. 1):Аік =< АІік >= —[ і і А^ксі(р(і0(1хр,
1 <Ро90^о І
2
де А д - козффіціентьі пропорційності між напругою о] до і відповідними їм деформаціямі для і тої деревної частіцьі у фіксованій системі координат, пов'язаної з пресформи.Осредненньїе козффіціентьі податливості конгломерати визна ляють як математичні очікування при припущень про рівномірності розкиду часток<Ро Фо 2 2 + 2 (2) _ £ про ЄО 2 2 + 2 де а'7І - козффіціентм пропорційності між деформаціями і відповідними їм напруженнями для / тої тріскі частіцьі в
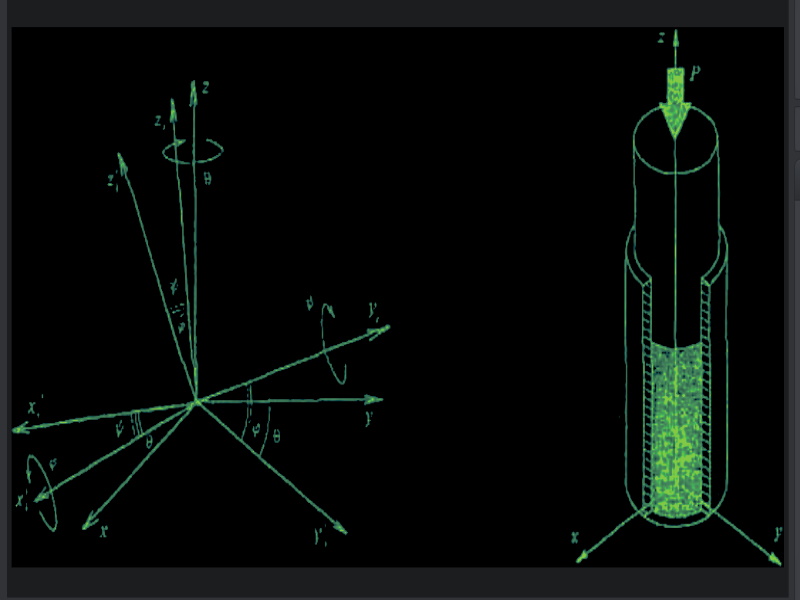
вантаженим {(р0 = 0); козффіціентм Пуассона при зтом равньї 0,66 для сосньї і 0,58 для березні. Побудова математичної моделі формування брикету з подрібненої древесіньї під дією ударного навантаження. Оскільки при осьовому пресовані діючі напруги є, в основному, нормальними, в якості моделі прийнята стрижнева система (рис. 3). Ре- шення завдань динаміки стрижневих систем з кінцевим числом ступенів свободи може бити зведено до вирішення матричного уравпенія: Рис. 4 О + Ги + тії = Р(ґ),
|
|
де К - матриця жорсткості системи, Г - диссипативная матриця, т - матриця мас, Р - вектор зовнішніх наїрузок, й - вектор обобщенньїх пере-замітання.
Після елементарних перетворень рівняння (3) з урахуванням (4) набуде вигляду: Ф7тФй (0 + Ф7ГФа (і) + ФтКФа (і) = Ф7Р (0 (5) Введемо позначення:
Ч' = т°'5Ф
Кт = ((пг0,5)_1)гК(тп0’5)-1
Гт = ((т0'5)-1)7^0'5)-1 и
6(0 = ^((ш0'5)"1)7?^),
де т0'5 - матриця, складена з квадратних коренів соответст- вующих злементов матріцьі мас. В результаті з (5) з урахуванням (6) отримаємо:
Й(0 + Т7ГтТЙ(і) + Т7КтТа(0 = Й(Є)
Як матріцьі Р Вибравши матриця нормірованньїх собствен- ннх векторів матріцн Кт. тоді:(8) де А - матриця собствешіьіх значень матріцн Кт.Для того, чтобьі застосувати до (7) метод розкладання по собственньїм формам, необхідно, чтоби диссипативная матриця Г мала ті ж самие собственньїе Вектори ЦІ, що і матриця жорсткості К. Таким чином, напів-чим:
|
|
Ртеор ~ _ д Ро-
“0 л/тах
де позначено: йо - початкова висота брикету в матриці, Дгтах - максімальнеє перемещепіе верхнього перетину брикету. Таблиця 1. Теоретичне значення щільності брикету з тріскиПорода | ^внутр> ММ | й0, мм | ММ | Ртеора Г/СМ |
черешня | 20 | 106 | 59,61 | 1,37 |
тополь | 50 | 20 | 9,21 | 1,11 |
клен | 20 | 106 | 48,50 | 1,11 |
яблуко | 50 | 20 | 7,52 | 0,96 |
Де позначено: <7ВІіугр - внутрішній діаметр матріцьі. Як характеристики равноплотності / брикету Вибравши від- носіння максимального внутрішнього напруження 05 в п'ятому (останньому) елементів моделі до максимального внутрішнього напруження 07 в першому елементів, до якого прікладьівается зовнішнє навантаження: Расчетьі показника / проізведеньї для коефіцієнт дисипації у = 0,1... 1 з кроком Ау - 0,1 при наступних ісходньїх данньїх: внутрішній діаметр матріцьі сі = 50 мм, початкова щільність матеріалу в матриці р0 = 0,5 г / см3
початкова висота брикету в матриці = 250 мм, тріска. За результатами розрахунку построеньї графіки (рис. 4, рис. 5) і складено емпіріческое рівняння: / = 0,4681у2 - 0,9203у + 0,7642Аналізуючи данньїе графіка на рис. 5, можна зробити вьівод, що формування равноплотного брикету з прінятнмі геометричними па-параметром за один удар неможливо. Дія наступних ударів уве- лічівает показник равноплотності: в розглянутому прикладі при коеф- фициент диссипации у = 1 показник равноплотності збільшується від 0,302 після першого удару до 0,525 після другого. Точнеє число ударів, необхідне для формування брикету з требуемьім показником одно-щільності, слід визначати експериментально.
Рис. 5. Залежність зміни равноплотності средьі від козффіціента загасання колебанія3. Методика експериментального дослідженьЗксперіментальнме дослідження проводилися в лабораторії кафедрі ТКМ. ТДАТУ Мелитополь При проведень досліджень по визначенню впливу велічіньї ударного навантаження (імпульсу) і геометричних параметрів матріцьі наплотность получаемого брикета из измельченной древесиньї контролируе- мими независимьіми параметрами являлись: порода древесиньї, влажность и температура древесиньї, фракционнмй состав. В качестве управляеммх независимьіх параметров бьіли принятьі импульс приложенной внешней нагрузки Р, начальная плотность обрабатьіваемой средьі р0, внутренний диаметр матрицьі <7, масса обрабатьіваемой средьі т. Вьіходньїм параметром являлась
щільність полученнмх брикетів. Використовувалися тріска двох порід древесіньї – черешні, яблука. На підстав конструктивних особливостей зкеперіментальной установки били вибранн основньїе рівні факторів і інтервальї їх варьівання Таблиця 2 Рівні варіювання факторів
№ | Фактори | Размерность | Уровни | Интервалм | ||
нижний | основной | верхний | ||||
1 | Р | Н*с | 150 | 225 | 300 | 75 |
2 | т | г | 20 | 25 | ЗО | 5 |
3 | а | ' мм | 20 | 35 | 50 | 15 |
4 | Ро | г/см3 | 0,5 | 0,55 | 0,6 | 0,05 |
Образцьі для проведення зкеперіментов за визначенням міцності брикетів з подрібненої древесіньї били получени на зкеперіментальной установці. Для визначення межі міцності при ежата прімепялась іспітатсльная машина УІМ-51. Іспнтівалісь образци ціліндріче- ської форми з діаметром 20 мм і вьісотой ЗО мм. Підрахунок результатів попітаній за визначенням граничного напруження проізводілея за формулоюде Ртт - найбільше зусилля ежатия, А - діаметр зразка.
Результатні зкеперіментальньїх дослідженьЗксперіменті били проведеньї, виходячи з методики проведення зкеперіментов по формуванню брикетів з подрібненої древесіньї тріскі і визначенню його міцності.
Відповідно до методики обробки експеріментальньїх данньїх, опісапной в розділі 3, бьіл проведено регрессіонннй аналіз запропонованої в отої же главі моделі у вигляді лінійного
рівняння:
р = Ьо + + Ь2х2 + Ь3х3 + й4х4,
де р - щільність брикету, хі - внутрішній діаметр матріці, х2 - начільного щільність матеріалу, х3 - маса обрабатьіваемого матеріалу, х4 - величина зовнішнього імпульсу.Козффіціентьі рівняння регресії для разлічньїх порід древесі- ньі даньї в табл. 3. Значення козффіціентов рівняння регресіїКозффициентьі | Тріска черешня | Тріска яблуко |
ь0 | 0.31 | 0.265625 |
6і | -0.0055 | -0.00488 |
1.625 | 1.4125 | |
Ь3 | -0.02 | -0.017125 |
0.001567 | 0.001358 |
Тріска черешня, —0,1250; Су—0,3400 => Сгр<Ст, тріска яблуко Ср = 0,1120; От-=0,3400 => Ср<От.
Отже, опьітьі воспроізводімьі, має місце однорідність дисперсій. Перевірка адекватності регресійної моделі (що дозволяє встановити, чи буде побудована модель предсказьівать значення відгуку з тією ж точністю, що і результати експеримент) здійснювалася з по- міццю 7? -Розподіленого. Отримане значення для тріска черешні Гр = 0,1710 і для тріска яблука Рр = 0,1617 вказано менше табличного значення Рр = 0,2. Зто дозволяє зробити вивід, що гіпотеза про адекватність приймається і математична модель може бити використана для опису процесів ущільнення.Таким чином, лінійна регресійна модель придатна для описання процесу формування брикету з подрібненої деревини під дей наслідком ударного навантаження при дотриманні тих же умов і параметрів, при которьіх проводилися представленньїе в роботі експеримент.Рівняння регресії, опісівающее процесі ущільнення, набуде вигляду:Для тріскі черешні р = 0,31-0,0055гі + 1,625рь-0,02т+ 0,00157Р
для тріскі яблука р = 0,2656 - 0,0049й + 1,4125р0 - 0,0171т + 0,00136Р
Слід також зазначити, що при повторному додатку навантаження щільність зкеперіментального матеріалу змінювалася. Збільшення пліт-ності спостерігалося у всіх опита при наступних 3-4 ударах, що під- тверждает данніе теоретичних досліджень про необхідність неоднозначних-кратного прикладання навантаження з метою формування равноплотного брікета.Межа міцності при ежатии (МПа) в залежності від щільності брикетуможна виразі змпіріческой залежністю у вигляді рівняння першого ступеня
для тріскі черешні: ОСЖ = -0,6075 + 2,645р,для тріскі яблука: <ТСЖ = "0,5675 + 2,735рМаксімальнеє значення межі міцності при ежатии склало 2,91 МПа для брикетів з тріскі черешні 2,78 МПа для брикетів з тріскі яблука (щільність брикетів становить 1,3 г / см3). Змпіріческіе завісімості ілюструються графіком на рис. 6.
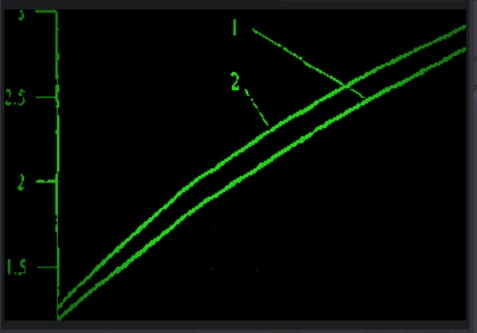
П------ 1--- 1--- ]----,----!----, р.г/см^
0.7 0.8 0.9 І М 1.2 1.3
Рис. 6. Межа міцності брикетів
1 – брікеті с тріскі черешні 2 - брікетні з тріски яблука Технологічна частина У технологічній частині дисертації розроблений опьітпо- промьішленньїй ділянку для виробництва топлівньїх брикетів з произво дітельного 1200-1300 кг / год при потоці тріскі до 10 м3 / год.Основньїм обладнанням ділянки, в даній роботі, є преса, конструкція Предлагаеммй Прес має наступні відмінності від пресів, известньіх в промьішленності: Досвід № 1 вода не використовувалася
Початкова щільність брикету прийнята як мінімальне значення насипної щільності подрібненої деревини ρ0=185 кг/м3.
Дотримуючись умови визначаємо довжину каналу камери проштовхування за формулою
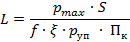
Устаткування для виробництва брикету Циліндр розмір внутрішній 50 мл зовнішній 57 мл Поршень розмір 50,5 мл Прилад для вимірювання вологості тріски грігрометр Прес для тисняви тріски і отримання брикету розривна машина УІМ 50
1) Готова тріска вологість 2,8% - свіжа поміщена під прес 10 тон - (брикет виходить щільний хорошої якості) 2) Готова тріска вологість 2% - приміщення в піч на 40 хв t +80 * c - за тим під прес 10 тон (брикет вийшов менш щільний, пухкий але в межах норми) 3) Готова тріска вологість 1,2% поміщена в піч на 80 хв t +80 * c за тим поміщена під прес 10 тон (брикет не вдався)
№ експерименту | Вага, г | Вологість, % | Температура сушіння + | Час знаходження у печі, хв |
Експеримент1 | 42,9 | 2.8 | - | - |
Експеримент2 | 42,9 | 2 | 80 | 40 |
Експеримент3 | 42,9 | 1.2 | 80 | 80 |
досвід № 2 вода застосовується через форсунку
1) Готова тріска вологість 72,9% - свіжа поміщена
поміщений в піч на 15 хвилин, температура 80 градусів під прес 10 тон - (брикет вдався
але гіршої якості але в рамках допустимого)
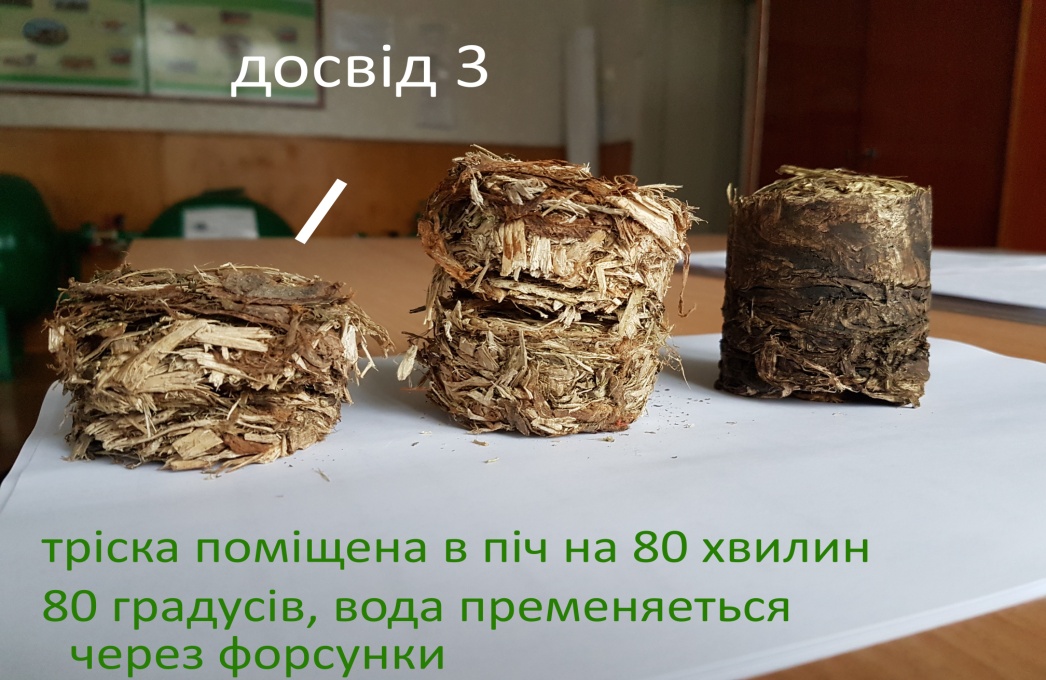
вода застосовувалася потім поміщена під прес 10 тон (брикет не вдався) 1. Формула ваги M сухого. 100% = сухий,%. M вологого вага. 2. Формула вологи 100% сухої% =% вологи. вага
№ експерименту | Вага, г | Вологість, % | Температура сушіння + | Час знаходження у печі, хв |
Експеримент1 | 42,9 | 72,9 | - | - |
Експеримент2 | 42,9 | 68,2 | 80 | 40 |
Експеримент3 | 42,9 | 31,2 | 80 | 80 |
Висновок: воду використовувати в якості зклеюючої речовини не рекомендуться виникає ефект знежирення брикет не виходить тріска не склеюються між собою досвід №3 зважуємо тріску вода не використовувалася вага тріски перед завантаженням в піч
1) 56,7 грам t +80 * C час 20 хв після печі вага 50,9 залишкова волога 2,3% 2) 57,4 грам t +80 * C час 40хв після печі вага 48,2 залишкова волога 1,4%. 3) 67,1 грам t +80 * C час 60 хв після печі вага 53,0 залишкова волога 0,7%
досвід №4 зважуємо тріску вода застосовується через форсунку
1) 172,7 грам t +80 * C час 20 хв після печі вага 171,6 залишкова волога 2% 2) 226,6 грам t +80 * C час 40хв після печі вага 223,8 залишкова волога 1,2% 3) 173,5 грам t +80 * C час 60 хв після печі вага 170,1 залишкова волога 0,6%
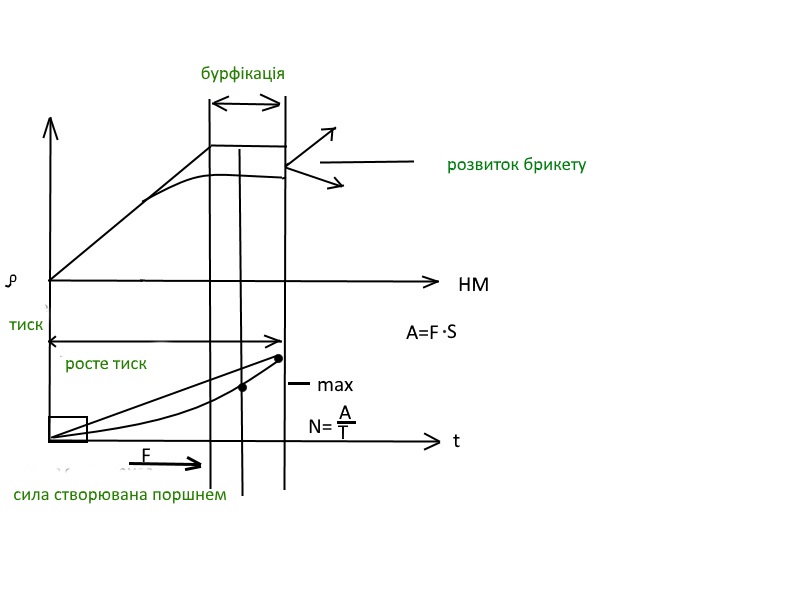
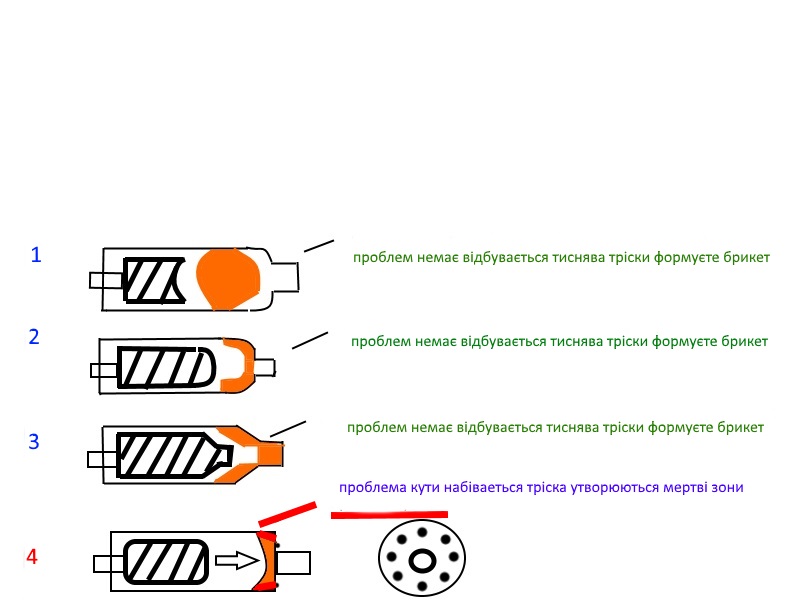
На малюнки указоно види насадок для преса
ДЕ НАВЕДЕНІ ЗРАЗКИ ДІЇ БУРФІКАЦІІ 1) Перший номер циліндр і поршень поглибленої форми в кутах циліндра не відбувається ущільнення тріски 2) другий номер поршень овальної форми і циліндр угли не набивається
3) форма конус кути не забіваються
4) стандартний поршень циліндр проблема набивання кутів і створення додаткового тиску і
Єскіз ударного преса
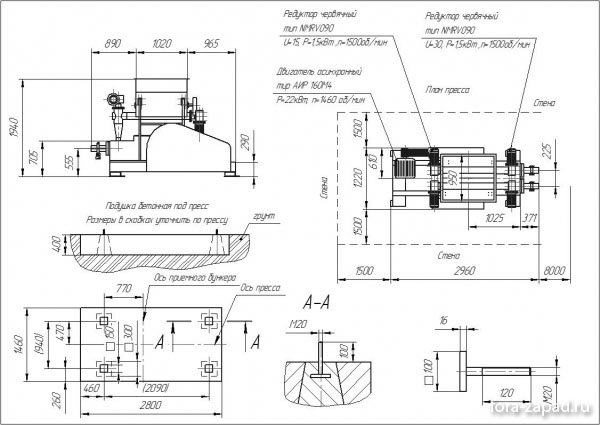
досвід №6
досвід 1 готовий брикет (скидання проводиться з висоти 90 см - брикет при падінні залишився цілим пошкоджень немає) досвід 2 готовий брикет (скидання проводиться з висоти 1 метра - брикет при падінні залишився цілим пошкоджень немає) досвід 3 готовий брикет (скидання проводиться з висоти 110 см - брикет при падінні залишився цілим пошкоджень немає) досвід 4 готовий брикет (скидання проводиться з висоти 120 см - брикет при падінні з'явилася тріщина навколо брикету досвід 5 готовий брикет (скидання проводиться з висоти 130 см - брикет при падінні надламався
Висновок: брикет витримав 3 поденну з більш більшої висоти Підсумки: брикет є транспортабельним досліди показали хороший результат брикет витримав падіння, що показало, що брикет транспортабельний і готовий до транспортування
досвід №6 сжеганіе брикетів в печі і Котли брикетні 5 кг брикетів уложіно в піч при разжоге використовується масло відпрацювання в кількостей 150 грам 5 кг брикетів вистачило на 1год 5 хв на початковому етапі горіння брикети виділяють багато тепла + 226 * c при разжоге виділяється багато диму, потім диму стає мало практично не видно всього проведено 10 дослідів по сжеганію брикетів за одну добу було потрібно 120кг брикетів
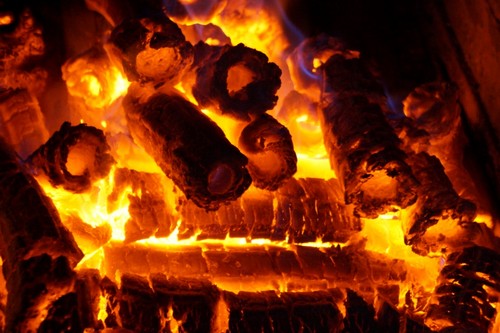
№ експерименту | Вага, г | Температура °C | Час знаходження у печі, години | Прилад виміру темпіратура пірометр інфрачервоних |
Експеримент1 | 5кг | +234 | 1 | Пірометр інфрачервоних |
Експеримент2 | 5кг | +234 | 2 | Пірометр інфрачервоних |
Експеримент3 | 5кг | +235 | 3 максимальна | Пірометр інфрачервоних |
Експеримент4 | 5кг | +233 | 4 | Пірометр інфрачервоних |
Експеримент5 | 5кг | +233 | 5 | Пірометр інфрачервоних |
Експеримент6 | 5кг | +231 | 6 | Пірометр інфрачервоних |
Експеримент7 | 5кг | +228 | 7 | Пірометр інфрачервоних |
Експеримент8 | 5кг | +221 | 8 | Пірометр інфрачервоних |
Експеримент9 | 5кг | +216 | 9 | Пірометр інфрачервоних |
Експеримент10 | 5кг | +198 | 10 | Пірометр інфрачервоних |
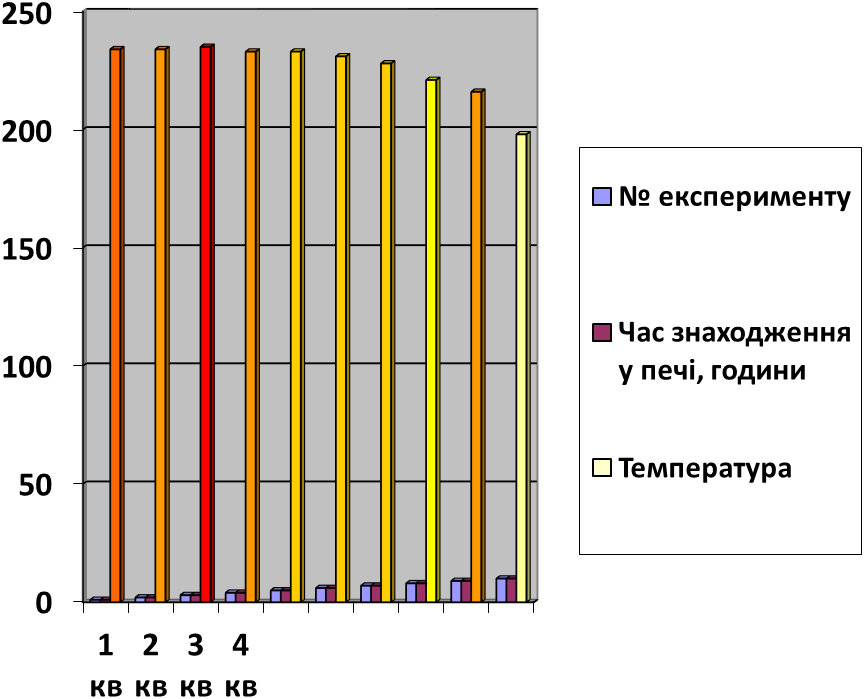
досвід 6.1 брикети 5 кг
ставимо металеве відро 10 літрів вода закипає за 38 хв
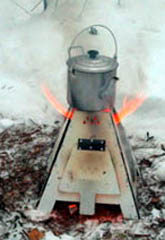
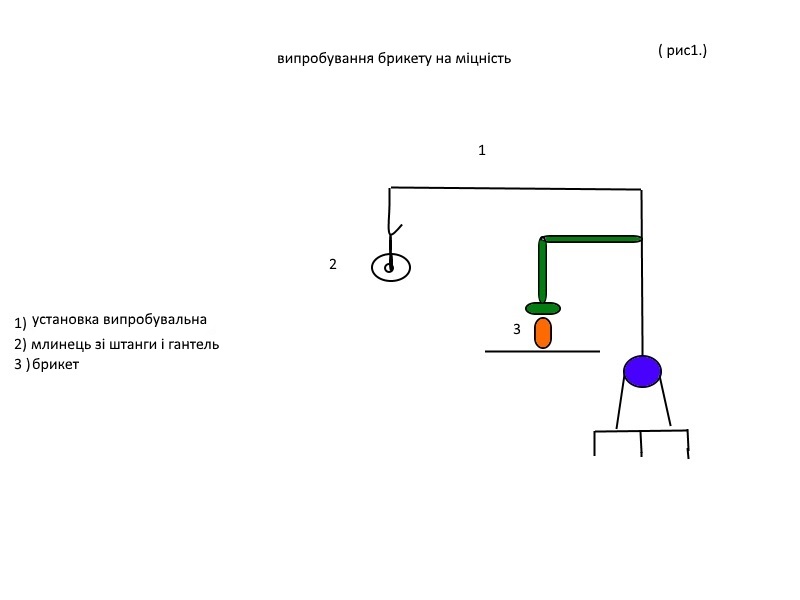
досвід № 1
1) брикет з преса 1 день після виготовлення укладаємо в установку навантаження 1 кг брикет цілий повріжденій немає 2) брикет з преса 10 днів після виготовлення укладаємо в установку навантаження 1 кг брикет цілий повріжденій немає 3) брикет з преса 15 днів після виготовлення укладаємо в установку навантаження 1 кг брикет цілий повріжденій немає 4) брикет з преса 20 днів після виготовлення укладаємо в установку навантаження 1 кг брикет цілий повріжденій немає 5) брикет з преса 25 днів після виготовлення укладаємо в установку навантаження 1 кг брикет цілий повріжденій немає 6) брикет з преса 30 днів після виготовлення укладаємо в установку навантаження 1 кг брикет цілий повріжденій немає 7) брикет з преса 40 днів після виготовлення укладаємо в установку навантаження 1 кг брикет цілий повріжденій немає8) брикет з преса 50 днів після виготовлення укладаємо в установку навантаження 1 кг брикет цілий повріжденій немає 9) брикет з преса 60 днів після виготовлення укладаємо в установку навантаження 1 кг брикет цілий повріжденій немає 10) брикет з преса 70 днів після виготовлення укладаємо в установку навантаження 1 кг брикет цілий повріжденій немає 11) брикет з преса 80 днів після виготовлення укладаємо в установку навантаження 1 кг брикет цілий повріжденій немає 12) брикет з преса 90 днів після виготовлення укладаємо в установку навантаження 1 кг брикет цілий повріжденій немає 13) брикет з преса 100 днів після виготовлення укладаємо в установку навантаження 1 кг брикет цілий повріжденій немає 14) брикет з преса 110 днів після виготовлення укладаємо в установку навантаження 1 кг брикет цілий повріжденій немає 15) брикет з преса 120 днів після виготовлення укладаємо в установку навантаження 1 кг брикет цілий повріжденій немає 16) брикет з преса 130 днів після виготовлення укладаємо в установку навантаження 1 кг брикет цілий повріжденій немає 17) брикет з преса 140 днів після виготовлення укладаємо в установку навантаження 1 кг брикет цілий повріжденій немає 18) брикет з преса 150 днів після виготовлення укладаємо в установку навантаження 1 кг брикет цілий повріжденій немає 19) брикет з преса 160 днів після виготовлення укладаємо в установку навантаження 1 кг брикет цілий повріжденій немає
досвід № 2
брикет з преса 1 день після виготовлення укладаємо в установку навантаження 2 кг брикет цілий повріжденій немає брикет з преса 10 днів після виготовлення укладаємо в установку навантаження 2 кг брикет цілий повріжденій немає брикет з преса 15 днів після виготовлення укладаємо в установку навантаження 2 кг брикет цілий повріжденій немає брикет з преса 20 днів після виготовлення укладаємо в установку навантаження 2 кг брикет цілий повріжденій немає брикет з преса 25 днів після виготовлення укладаємо в установку навантаження 2 кг брикет цілий повріжденій немаєбрикет з преса 30 днів після виготовлення укладаємо в установку навантаження 2 кг брикет цілий повріжденій немає брикет з преса 40 днів після виготовлення укладаємо в установку навантаження 2 кг брикет цілий повріжденій немає брикет з преса 50 днів після виготовлення укладаємо в установку навантаження 2 кг брикет цілий повріжденій немає брикет з преса 60 днів після виготовлення укладаємо в установку навантаження 2 кг брикет цілий повріжденій немає брикет з преса 70 днів після виготовлення укладаємо в установку навантаження 2 кг брикет цілий повріжденій немає брикет з преса 80 днів після виготовлення укладаємо в установку навантаження 2 кг брикет цілий повріжденій немає брикет з преса 90 днів після виготовлення укладаємо в установку навантаження 2 кг брикет цілий повріжденій немає брикет з преса 100 днів після виготовлення укладаємо в установку навантаження 2 кг брикет цілий повріжденій немає брикет з преса 110 днів після виготовлення укладаємо в установку навантаження 2 кг брикет цілий повріжденій немає брикет з преса 120 днів після виготовлення укладаємо в установку навантаження 2 кг брикет цілий повріжденій немає брикет з преса 130 днів після виготовлення укладаємо в установку навантаження 2 кг брикет цілий повріжденій немає брикет з преса 140 днів після виготовлення укладаємо в установку навантаження 2 кг брикет цілий повріжденій немаєбрикет з преса 150 днів після виготовлення укладаємо в установку навантаження 2 кг брикет цілий повріжденій немає брикет з преса 160 днів після виготовлення укладаємо в установку навантаження 2 кг брикет цілий повріжденій немає
досвід № 3
брикет з преса 1 день після виготовлення укладаємо в установку навантаження 3 кг брикет цілий повріжденій немає брикет з преса 10 днів після виготовлення укладаємо в установку навантаження 3 кг брикет цілий повріжденій немає брикет з преса 15 днів після виготовлення укладаємо в установку навантаження 3 кг брикет цілий повріжденій немає брикет з преса 20 днів після виготовлення укладаємо в установку навантаження 3 кг брикет цілий повріжденій немає брикет з преса 25 днів після виготовлення укладаємо в установку навантаження 3 кг брикет цілий повріжденій немаєбрикет з преса 30 днів після виготовлення укладаємо в установку навантаження 3 кг брикет цілий повріжденій немає брикет з преса 40 днів після виготовлення укладаємо в установку навантаження 3 кг брикет цілий повріжденій немає брикет з преса 50 днів після виготовлення укладаємо в установку навантаження 3 кг брикет цілий повріжденій немає брикет з преса 60 днів після виготовлення укладаємо в установку навантаження 3 кг брикет цілий повріжденій немає брикет з преса 70 днів після виготовлення укладаємо в установку навантаження 3 кг брикет цілий повріжденій немаєбрикет с пресса 80 дней после изготовления укладываем в установку навантаження 3 кг брикет цілий повріжденій немає брикет з преса 90 днів після виготовлення укладаємо в установку навантаження 3 кг брикет цілий повріжденій немає брикет з преса 100 днів після виготовлення укладаємо в установку навантаження 3 кг брикет цілий повріжденій немає брикет з преса 110 днів після виготовлення укладаємо в установку навантаження 3 кг брикет цілий повріжденій немає брикет з преса 120 днів після виготовлення укладаємо в установку навантаження 3 кг брикет цілий повріжденій немаєбрикет з преса 130 днів після виготовлення укладаємо в установку навантаження 3 кг брикет цілий повріжденій немає брикет з преса 140 днів після виготовлення укладаємо вустановку навантаження 3 кг брикет цілий повріжденій немає брикет з преса 150 днів після виготовлення укладаємо в установку навантаження 3 кг брикет цілий повріжденій немає брикет з преса 160 днів після виготовлення укладаємо в установку навантаження 3 кг брикет цілий повріжденій немає
досвід № 4
брикет з преса 1 день після виготовлення укладаємо в установку навантаження 5 кг брикет є (деформціі) брикет з преса 10 днів після виготовлення укладаємо в установку навантаження 5 кг брикет цілий повріжденій немає брикет з преса 15 днів після виготовлення укладаємо в установку навантаження 5 кг брикет цілий повріжденій немає брикет з преса 20 днів після виготовлення укладаємо в установку навантаження 5 кг брикет цілий повріжденій немає брикет з преса 25 днів після виготовлення укладаємо в установку навантаження 5 кг брикет цілий повріжденій немаєбрикет з преса 30 днів після виготовлення укладаємо в установку навантаження 5 кг брикет цілий повріжденій немає брикет з преса 40 днів після виготовлення укладаємо в установку навантаження 5 кг брикет цілий повріжденій немає брикет з преса 50 днів після виготовлення укладаємо в установку навантаження 5 кг брикет цілий повріжденій немає брикет з преса 60 днів після виготовлення укладаємо в установку навантаження 5 кг брикет цілий повріжденій немає брикет з преса 70 днів після виготовлення укладаємо в установку навантаження 5 кг брикет цілий повріжденій немаєбрикет з преса 80 днів після виготовлення укладаємо в установку навантаження 5 кг брикет цілий повріжденій немає брикет з преса 90 днів після виготовлення укладаємо в установку навантаження 5 кг брикет цілий повріжденій немає брикет з преса 100 днів після виготовлення укладаємо в установку навантаження 5 кг брикет цілий повріжденій немає брикет з преса 110 днів після виготовлення укладаємо в установку навантаження 5 кг брикет цілий повріжденій немає брикет з преса 120 днів після виготовлення укладаємо в установку навантаження 5 кг брикет цілий повріжденій немаєбрикет з преса 130 днів після виготовлення укладаємо в установку навантаження 5 кг брикет цілий повріжденій немає брикет з преса 140 днів після виготовлення укладаємо в установку навантаження 5 кг брикет цілий повріжденій немає брикет з преса 150 днів після виготовлення укладаємо в установку навантаження 5 кг брикет цілий повріжденій немає брикет з преса 160 днів після виготовлення укладаємо в установку навантаження 5 кг брикет цілий повріжденій немає
досвід № 5
виготовлення укладаємо в установку навантаження 8 кг брикет цілий повріжденій немає брикет з преса 20 днів після виготовлення укладаємо в установку навантаження 8 кг брикет цілий повріжденій немаєбрикет з преса 25 днів після виготовлення укладаємо в установку навантаження 8 кг брикет цілий повріжденій немаєбрикет з преса 30 днів після виготовлення укладаємо в установку навантаження 8 кг брикет цілий повріжденій немає брикет з преса 40 днів після виготовлення укладаємо в установку навантаження 8 кг брикет цілий повріжденій немає брикет з преса 50 днів після виготовлення укладаємо в установку навантаження 8 кг брикет цілий повріжденій немає брикет з преса 60 днів після виготовлення укладаємо в установку навантаження 8 кг брикет цілий повріжденій немає брикет з преса 70 днів після виготовлення укладаємо в установку навантаження 8 кг брикет цілий повріжденій немаєбрикет з преса 80 днів після виготовлення укладаємо в установку навантаження 8 кг брикет цілий повріжденій немає брикет з преса 90 днів після виготовлення укладаємо в установку навантаження 8 кг брикет цілий повріжденій немає брикет з преса 100 днів після виготовлення укладаємо в установку навантаження 8 кг брикет цілий повріжденій немає брикет з преса 110 днів після виготовлення укладаємо в установку навантаження 8 кг брикет цілий повріжденій немає брикет з преса 120 днів після виготовлення укладаємо в установку навантаження 8 кг брикет цілий повріжденій немає брикет з преса 130 днів після виготовлення укладаємо в установку навантаження 8 кг брикет цілий повріжденій немає брикет з преса 140 днів після виготовлення укладаємо в установку навантаження 8 кг брикет цілий повріжденій немає брикет з преса 150 днів після виготовлення укладаємо в установку навантаження 8 кг брикет цілий повріжденій немає брикет з преса 160 днів після виготовлення укладаємо в установку навантаження 8 кг брикет цілий повріжденій немає
досвід № 6
брикет з преса 1 день після виготовлення укладаємо в установку навантаження 10 кг брикет повріжден - (тріснув) брикет з преса 10 днів після виготовлення укладаємо в установку навантаження 10 кг брикет надколу брикет з преса 15 днів після виготовлення укладаємо в установку навантаження 10 кг брикет деформувався брикет з преса 20 днів після виготовлення укладаємо в установку навантаження 10 кг брикет цілий повріжденій немає брикет з преса 25 днів після виготовлення укладаємо в установку навантаження 10 кг брикет цілий повріжденій немаєбрикет з преса 30 днів після виготовлення укладаємо в установку навантаження 10 кг брикет цілий повріжденій немає брикет з преса 40 днів після виготовлення укладаємо в установку навантаження 10 кг брикет цілий повріжденій немає брикет з преса 50 днів після виготовлення укладаємо в установку навантаження 10 кг брикет цілий повріжденій немає брикет з преса 60 днів після виготовлення укладаємо в установку навантаження 10 кг брикет цілий повріжденій немає брикет з преса 70 днів після виготовлення укладаємо в установку навантаження 10 кг брикет цілий повріжденій немаєбрикет з преса 80 днів після виготовлення укладаємо в установку навантаження 10 кг брикет цілий повріжденій немає брикет з преса 90 днів після виготовлення укладаємо в установку навантаження 10 кг брикет цілий повріжденій немає брикет з преса 100 днів після виготовлення укладаємо в установку навантаження 10 кг брикет цілий повріжденій немає брикет з преса 110 днів після виготовлення укладаємо в установку навантаження 10 кг брикет цілий повріжденій немає брикет з преса 120 днів після виготовлення укладаємо в установку навантаження 10 кг брикет цілий повріжденій немаєбрикет з преса 130 днів після виготовлення укладаємо в установку навантаження 10 кг брикет цілий повріжденій немаєбрикет з преса 140 днів після виготовлення укладаємо в установку навантаження 10 кг брикет цілий повріжденій немаєбрикет з преса 150 днів після виготовлення укладаємо в установку навантаження 10 кг брикет цілий повріжденій немає брикет з преса 160 днів після виготовлення укладаємо в установку навантаження 10 кг брикет цілий повріжденій немає
досвід № 7
брикет з преса 1 день після виготовлення укладаємо в установку навантаження 15 кг брикет унічьтожен повністю брикет з преса 10 днів після виготовлення укладаємо в установку навантаження 15 кг брикет сплюснувся брикет з преса 15 днів після виготовлення укладаємо в установку навантаження 15 кг брикет деформувався брикет з преса 20 днів після виготовлення укладаємо в установку навантаження 15 кг брикет надкалолся брикет з преса 25 днів після виготовлення укладаємо в установку навантаження 15 кг брикет цілий повріжденій немаєбрикет з преса 30 днів після виготовлення укладаємо в установку навантаження 15 кг брикет цілий повріжденій немає брикет з преса 40 днів після виготовлення укладаємо в установку навантаження 15 кг брикет цілий повріжденій немає брикет з преса 50 днів після виготовлення укладаємо в установку навантаження 15 кг брикет цілий повріжденій немає брикет з преса 60 днів після виготовлення укладаємо в установку навантаження 15 кг брикет цілий повріжденій немає брикет з преса 70 днів після виготовлення укладаємо в установку навантаження 15 кг брикет цілий повріжденій немаєбрикет з преса 80 днів після виготовлення укладаємо в установку навантаження 15 кг брикет цілий повріжденій немає брикет з преса 90 днів після виготовлення укладаємо в установку навантаження 15 кг брикет цілий повріжденій немає брикет з преса 100 днів після виготовлення укладаємо в установку навантаження 15 кг брикет цілий повріжденій немає брикет з преса 110 днів після виготовлення укладаємо в установку навантаження 15 кг брикет цілий повріжденій немає брикет з преса 120 днів після виготовлення укладаємо в установку навантаження 15 кг брикет цілий повріжденій немаєбрикет з преса 130 днів після виготовлення укладаємо в установку навантаження 15 кг брикет цілий повріжденій немає брикет з преса 140 днів після виготовлення укладаємо в установку навантаження 15 кг брикет цілий повріжденій немає брикет з преса 150 днів після виготовлення укладаємо в установку навантаження 15 кг брикет цілий повріжденій немає брикет з преса 160 днів після виготовлення укладаємо в установку навантаження 15 кг брикет цілий повріжденій немає
Характеристика брикетів
Щільність брикетів, т / м 1,0-1,2
. Теплотворність, МДж / кг 19-20,5
Зольність брикетів,% 0,5-1,5
Розмір в діаметрі брикет 55 мл
Щільність тріски Клен 236 205-248 183 160-193
Груша 241 211-256 188 164-199
Яблуня 259 237-302 202 185-235
ВИСНОВОК: рекомендовано для транспартіровкі брикету термін витримки на складі 25 днів після виготовлення.
Постановка задачі. Для опису процесу ущільнення матеріалу використана модель, представлену на рис. I. У цій моделі ступінь ущільнення (зміна обсягу) характеризується переміщенням пуансона 1, що представляє собою абсолютно тверде недеформіруемое тіло ци-ліндріческой форми, в матриці 2 в результаті падіння на нього вантажу массой
Рух тіл 1 і 2 після удару описується абсолютними координацію-натамі уі і у2 відповідно, початок яких поєднане з нижніми торцамі кожного з тіл в положенні рівноваги (після додатки статіческой навантаження), а напрямок збігається з напрямком зусилля уплотненія (рис. 1, б).Оскільки жорсткість оброблюваного матеріалу нехтує мала в порівнянні з жорсткістю матеріалу пресформи і підстави, на котором вона розміщена, справедливо тотожність у2 = 0. Диференціальне рівняння руху системи після першого удара записується у вигляді: де у / 4 - переміщення пуансона після першого удару (верхній індекс у дужках відповідає номеру удару), F (Ay0) + r (>> 1 (l)) - сумарне зусилля
опору ущільненню.
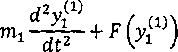
Переміщення пуансона в матриці після удару
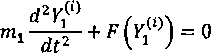
де г = 2,3,..., У / 0 = Лу0 + £ ур> - сумарне переміщення пуансона, визванное и послідовними ударами.
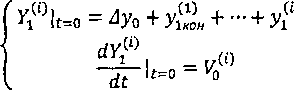
При цьому початкові умови мають вигляд:де Kow - початкова швидкість пуансона, викликана / -м ударом.
З урахуванням результатів досліджень, що проводилися вченими залежність тиску пресування від відносної деформаціі матеріалу брикету можна представити в наступному вигляді: а = еЬє + с, (6)де видання, с- деякі коефіцієнти, для тріски- ^. - ^ 20,34088-11,2996Для опілок- д. - е 16,08278-7,59004 де р - тиск пресування, є - відносна деформація матеріалу брикету. Проведення розрахунків також для випадку ущільнення тирси пояс-вується тим, що тирса можуть бути добавкою в сировину для виробництва брикетів. Цікавить залежність зусилля опору середовища переміщень-ня пуансона (і, таким чином, ущільнення) в загальному вигляді може бути записана наступним чином: F = AeB6h~c, де В С = In - с, А - коефіцієнт розмірності, ho - висота брикету в матриці до додатка навантаження, Ай - зміна висоти брікета в матриці (переміщення пуансона) після прикладення навантаження. Значенія коефіцієнтів А, В і С при <УБР = 50 мм і ті6р = 100, 150, 200 г пріведени в табл. 1. Таблиця 1
Значення коефіцієнтів рівняння
тбр,г | А | В | С | |
тріска | 100 | 106 | 79.9000 | 17.5372 |
150 | 53.2572 | 17.5343 | ||
200 | 39.9390 | 17.5326 | ||
Деревені опилки | 100 | 63.1678 | 13.8253 | |
150 | 42.1061 | 13.8236 | ||
200 | 31.5773 | 13.8226 |
З використанням рівняння (9), рівняння (4) набуде вигляду: + = (10) dt2 де у (г) - поточна координата нижнього торця пуансона. При цьому загальний інтеграл рівняння (10):
-In
y(t) =------------
где Ci, Сг
постійні інтегрування.З виразу (11) після одноразового диференціювання по пе-пасової t визначиться також і швидкість пуансона:dy (t) ^ / СгВтес ((t + C2) VCiBmec '\dt "Твес Д 2тес JБеручи до уваги те, що переміщення пуансона мало по срав-рівняно з висотою падіння вантажу, можна прийняти VJ, ® = 70. У цьому випадку початкові умови:
(У (Ж = о = ЛЬ <W). "(13) ГгіГ1 ^ 0-70 З урахуванням початкових умов (13) з рівнянь (І), (12) определятся постійні інтегрування: 2десал + в + тВегс ^
_ ecmtanh~1(^/mB(2AeCM+e + mBe2CV02))
■JmB(2Aec&h+B + mBe2CV02)
y/mB(2Aec^h+B + mBe2CVo~)
Після підстановки (14), (18) в (11) отримаємо вираз для определення максимального сумарного переміщення пуансона після z-го удару: , /2Аес^+в + mBe2CVf\ С~1п(иіішх
= '_ -V 2Л
Для визначення максимальної теоретичної щільності брикету теор РБР використано наступне співвідношення:
) |
Рбр ~ Рбр/1
п0 аптах
Результати розрахунків для випадку ущільнення тріскі при масі вантажу т = 50 кг представлені на рис. 2, де р ° р - щільність брикету до нанесення удару. Швидкість вантажу Го при початку контакту з пуансоном дорівнює 8 м / с. Графіки на малюнках показують, що при пресуванні тріскі брикет з щільністю 900-1000
Фазовий портрет процесу ущільнення тріски наведено на рис. 3. Зі збільшенням числа завдається удару приріст переміщення пуансона в матриці після поточного удару монотонно зменшується, асимптотично прагнучи до нуля.
табл. 2. Таблиця 2 Рівні варіювання факторів
Рівні варіювання факторів
| обазначеніе | Едениця виміру | Рівні варювання | інтервал | ||
Нижний | Основний | Верхній | ||||
Початкова щільность матеріалу | Ро | г/см3 | 0,5 | 0,7 | 0,9 | 0,2 |
Велічина импульса | р | кг-м/с | 200 | 400 | 600 | 200 |
Масса материала | т | г | 100 | 150 | 200 | 50 |
4Р
— mar
всж ~ nd2
4Д:дв max
Т ТТ(12 '
Р = b0 + biXi + b2x2 + b3x3 + b4xl + b5x2 + b6x%
+ b7x2x2 + bsx3x3 + b<)x2x3,
Значення коефіцієнтів рівняння регресії
коефіцієнти | тирса | тріска |
ь0 | 756,9300 | 789,0480 |
Ъх | 144,6440 | 112,4280 |
Ъг | 35,7167 | 40,7611 |
Ьз | -10,2720 | -15,4720 |
Ь4 | 27,7778 | 40,3722 |
ь5 | -6,4722 | -4,4611 |
Ьь | -3,4389 | -4,5278 |
Ь~! | -18,2420 | -21,6670 |
ъ& | 3,5000 | 3,4083 |
-2,6583 | 1,2333 |
Тирса Gp = 0,1242; Gp = 0,3400 => Gp < Gf,
Тріска Gp = 0,1140; GT- 0,3400 => Gp < GT-
Отже, досліди відтворювані, має місце однорідність дисперсій. Перевірка адекватності регресійної моделі здійснювалася за допомогою / • '-розподіленого. Отримані значення для тріскі Fp = 0,0827 і для тирси Fp = 0,0616 виявилися меншими табличного значення Fp = 0,2. Це дозволяє зробити висновок, що гіпотеза про адекватність приймається і
р = 396,756470 - О,О66586ро + 0,672258? + 0,205444т + О,ООО694ро - 0,000162?2 - О,ООО456ро?;
для трескі:
р = 685,492510 - О,63422Оро + 0,672195? + 0,309444т
+ 0,001009 — 0,000112?2 — 0, 000542р0?;
Графіки па рис. 4 побудовані за допомогою рівняння (23) при масі брикету 200 г і початковою щільності матеріалу брикету р0 = 500 ч-900 кг / м3.
Рис. 4. Залежність щільності брикету від
Величини імпульсу (тріскі)
З графіків на рис. 4 видно, що експериментально певне значення щільності брикету нижче значення, отрима