2.6 Наладка станков с ЧПУ на обработку детали
Станок 16А20Ф3 оснащен оперативным устройством ЧПУ "NC-210". Для данного УЧПУ размерную настройку не выполняют, ее заменяют привязкой инструмента.
Режим размерной привязки инструмента применяют в тех случаях, когда необходимо привязать режущий инструмент к измерительной системе устройства ЧПУ. Перед привязкой инструмента необходимо вызвать инструмент в рабочую позицию, т. е. набрать «Номер инструмента» Т даже в тех случаях, когда на станке нет автоматической смены инструмента. Режим размерной привязки инструмента производят в такой последовательности:
1. Включают шпиндель и в ручном режиме подводят инструмент к заготовке.
2. В режиме работы «Штурвал» протачивают заготовку вдоль ее образующей.
3. Останавливают шпиндель и замеряют диаметр обработки (например, 152,45 мм).
4. Устройство переводят в режим размерной привязки инструмента нажатием клавиши, и замеренный диаметр вводят в память устройства (например, X152.45), при этом индикатор адреса и числа гаснет.
5. Включают шпиндель и в ручном режиме подводят инструмент к торцу заготовки, а затем обтачивают ее торец.
6. Отводят режущий инструмент по оси Х и останавливают шпиндель; замеряют расстояние от торца заготовки до зажимных кулачков патрона. Из замеренной величины вычитают припуск по усмотрению оператора (3-7 мм). Например, из замеренного размера 98,37 мм вычитают 3,37 мм и получают 95 мм.
7. Устройство переводят в режим размерной привязки инструмента нажатием клавиши, после чего замеренную величину вводят в память устройства (например, 295). Относительно этой точки программируется начало обработки. Точку начала обработки выбирают с учетом погрешности установки заготовки.
Пульт устройства ЧПУ «NC-210» (рис.3.1) включает пульт оператора и станочный пульт/консоль, которые объединяют в себе все функции типа ввода/вывода в системе Оператор – УЧПУ – Станок.
Пульт включает алфавитно-цифровую клавиатуру, жидкокристаллический дисплей TFT 10.4”, замок с ключом для включения/выключения питания УЧПУ.
Станочный пульт/консоль включает корректоры для изменения скорости подачи, вращения шпинделя, для выбора направления и скорости ручных перемещений, а также клавиши/переключатель для выбора режима работы, кнопки «СТОП» и «ПУСК». В станочный пульт дополнительно могут быть установлены свободно программируемые клавиши и штурвал ручных перемещений.
Рис.3.1 Пульт устройства ЧПУ «NC-210»
Элементы ПОна лицевой панели УЧПУ разделены пластмассовой накладкой на 4 секции:
- секция дисплея;
- секция алфавитно-цифровой клавиатуры (АЦК);
- секция функциональной клавиатуры (ФК);
- секция станочной консоли (СК), на которой расположены элементы индикации, переключатели, сетевой выключатель и аварийный выключатель.
Вывод алфавитно-цифровой информации на экран дисплея осуществляется в режимах «КОМАНДА» и «УПРАВЛЕНИЕ СТАНКОМ».
Режим «КОМАНДА» используется при процедурах редактирования, визуализации списка программ, таблиц корректоров, исходных точек и срока службы инструмента.
Алфавитно-цифровая информация в режиме «УПРАВЛЕНИЕ СТАНКОМ» выводится на видеостраницы #1-#5 и #7, которые визуализируют:
• название программы;
• текущее время;
• сообщения оператору;
• реальные размеры осей;
• запрограммированные размеры осей;
• функции G, T, S, M;
• исходные точки;
• корректора;
• номер кадра;
• повтор циклов и подпрограмм.
Графическая информация выводится в режиме «УПРАВЛЕНИЕ СТАНКОМ» на видеостраницу #6. Первые четыре строки видеокадра используются для воспроизведения краткой информации, что и на видеокадре #1. В стадии обработки свободная часть видеоэкрана используется для воспроизведения декартовых осей, запрограммированных размеров, профилей и точек, на которых реализуются запрограммированные циклы и движения оси, перпендикулярной к плоскости обработки.
Управляющие программы обработки детали должны быть занесены в память УЧПУ с клавиатуры или с периферийных устройств. Введенные символы в память программы могут быть воспроизведены на видеоэкране и модифицированы посредством удаления, модификации или вставления кадров. Эти операции могут осуществляться во время обработки детали на станке.
Режимы работы выбираются клавишами со станочной панели. Они могут быть:
• выполнение кадров введенных с клавиатуры («MDI»);
• выполнение выбранной программы в автоматическом режиме («AUTO»);
• выполнение выбранной программы по кадрам («STEP»);
• выполнение безразмерных ручных перемещений («MANU»);
• выполнение фиксированных ручных перемещений («MANJ»);
• автоматический выход на профиль и продолжение работы после прерывания цикла обработки, за которым следовали ручные перемещения («PROF»);
• выход в «0» станка («HOME»).
Подготовка всей необходимой геометрической и технологической информации для осуществления предусмотренного цикла обработки требует от программиста проведения подготовительной работы, которая состоит из следующих операций:
1) определить на чертеже начальную точку осей (ноль детали), относительно которой должны быть измерены все перемещения. Этот выбор должен быть осуществлен в соответствии с фактическими размерами чертежа. Надо иметь в виду, что, если чертеж был выполнен с учетом одной точки, будет возможно выбрать ноль детали, совпадающий с этой точкой. В обратном случае, выбирается точка, которая позволяет осуществить наиболее легкий переход от данного измерения к новому;
2) определить на чертеже детали точки отсчета и точки зажима самой детали;
3) убедиться в том, что все операции, которые необходимо выполнить, находятся в пределах рабочего поля станка;
4) составить список требуемых инструментов в строгой последовательности, необходимой для выполнения программы;
5) определить технологические условия резания (скорость вращения шпинделя и скорость подачи) для каждого инструмента. Вышеуказанные данные заносятся программистом в карточку инструмента.
Программа состоит из последовательности кадров, которые позволяют описать цикл обработки. Каждый кадр - это последовательность слов, определяющих операции, которые необходимо выполнить. Каждый кадр должен заканчиваться символом LF (ISO). Максимальная длина кадра - 128 символов. Символы, используемые для составления кадра, приведены в таблице 2.1. Все кадры, кроме комментирующего, могут иметь в начале три дополнительных поля независимо от класса, к которому принадлежит кадр. А именно:
1) поле подтверждения кадра и выведения его из рабочего состояния (символ 1);
2) поле метки;
3) поле номера кадра.
Они могут присутствовать в кадре по одиночке или одновременно. В случае если они присутствуют одновременно, последовательность расположения одиночных полей должна быть следующей в обязательном порядке: 1), 2), 3). Поле подтверждения кадра и выведения его из рабочего состояния позволяет включить в программу кадры, выполнение которых зависит от параметра системы, названного USB. Если параметр является активным (USB=1), кадр выполняется, в обратном случае (USB=0) кадр рассматривается как комментирующий. Формат устанавливается знаком «/» в первой позиции кадра.
Поле метки позволяет дать символическое название кадру, которому оно принадлежит. Метка служит для возможности вызова кадра из различных точек программы при помощи инструкций перехода. Метка - это алфавитно-цифровая последовательность символов, максимальная длина которой 6 символов, заключенная в знак «» (кавычки). Должна быть запрограммирована сразу же после поля «/», если оно присутствует.
Поле номера кадра служит для нумерации одиночных кадров программы. Номер кадра устанавливается символом «N», за которым следует число. Номер кадра должен быть запрограммирован в начале каждого кадра, но после символа «/» и метки.
Если программа введена с клавиатуры, то символы начала и конца программы не обязательны. Если программа перфорирована на ленте, то первым и последним символами должны быть «%» (ISO). В первом кадре обычно программируется информация о замене инструмента (Т...М06). В конце обработки необходимо установить оси в позиции, удобной для демонтажа детали. Затем следует остановить вращение шпинделя и охлаждающий поток и осуществить управление автоматической установкой (СБРОС) программы при помощи функции М30.
Возможно, вставить во внутрь программы сообщение, заключённое в кавычки и предназначенное для оператора станка. Это сообщение программируется трёхбуквенным кодом, следующим образом: (DIS, «текст сообщения»).
Текст сообщения не должен превышать 32 символа.
2.7 Регулирование узла станка с ЧПУ
Регулирование натяжения ремня главного привода.
Регулирование производится перемещением плиты 1 посредством вращения гаек 2 на тяге 3. Перекос плиты устраняется упорным винтом 4.
Рисунок 3.3 – Регулирование натяжения ремня главного привода
Регулирование положения путевых кулачков на продольной и поперечной линейках.
На каждой линейке (рис.3.4; рис.3.5) предусмотрены два паза для установки кулачков аварийного отключения подачи и аварийного отключения станка. Кулачки воздействуют на блоки путевыхэлектропереключателей, смонтированных на суппортной группе станка.
Кулачки аварийного отключения подачи воздействуют на штоки блока конечных выключателей за 5-8 мм до кулачков 2 аварийного отключения станка, а эти кулачки - за 5-8 мм до крайних положений поперечного суппорта и упора каретки в корпус задней бабки и резцов в кулачки патрона. По команде кулачков отключения подачи при ошибке программиста или наладчика отключается подача в соответствующем направлении без удара о смежные узлы. При этом система программного управления и станок не отключаются, и информация от датчиков обратной связи сохраняется в памяти системы. По команде кулачков аварийного выключения станка электросхема полностью выключается.
Па тех же линейках установлены (рис.3.3, 3.4) кулачки 3 подачи команды на предварительное замедление скорости перемещения при выходе суппорта в фиксированное положение и кулачки 4 фиксированного положения.
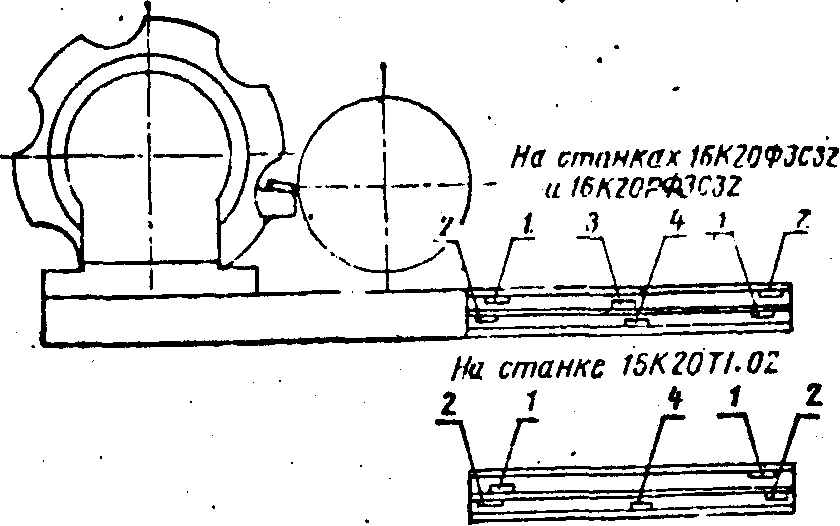
Рисунок 3.4 – Схема расположения кулачков в пазах линейки, поперечного перемещения
Рисунок 3.5 – Схема расположения кулачков в пазах линейки продольного перемещения
Регулирование положения задней бабки в перечном направлении.
Для совпадения оси пиноли с осью шпинделя в поперечном направлении предусмотрены два регулировочных винта 1 и 2 (рис.3.6).
Рисунок 3.6 – Регулирование положения задней бабки
Регулирование натяга в винтовой шаровой паре.
На станке установлены шариковые пары продольного и поперечного перемещений, представленные на рис.3.7.
Регулирование натяга (рис.3.7) производится поворотом полугаек 2, 3 (число впадин на полугайке 2 - 57, на полугайке 3 - 58). Поворот полугаек на одну впадину приводит к осевому смещению на 1-1,2мкм.
В случае необходимости регулирование натяга следует производить в следующем порядке:
- отвернуть винты 8 и снять крышки 4;
- отжать фиксирующие штифты 6 в корпусе 1, сжав пружины 7;
- повернуть полу гайки 2 и 3 на необходимое количество впадин в нужную сторону до входа штифтов 6 в соответствующие впадины на полугайках;
- закрепить крышки 4 винтами 8.
Рисунок 3.7 – Регулирование натяга в винтовой паре
2.8 Техника безопасности при выполнении операции на станках с ЧПУ
Территория предприятия, производственные помещения и размещение оборудования должны удовлетворять требованиям безопасности. Каждый человек, находящийся на территории предприятия, обязан выполнять общепринятые правила безопасности труда. Территория промышленного предприятия должна быть ровной. Различные углубления, канавы, траншеи, необходимые для проведения строительных или ремонтных работ, должны быть плотно закрыты, а в случае необходимости надежно ограждены. Дороги и проходы на территории предприятия должны быть, как правило, прямолинейными, а их ширина должна отвечать интенсивности движения. На переходах, переездах должны быть установлены шлагбаумы, светофоры, звуковая сигнализация и предупредительные надписи. В местах особо интенсивного железнодорожного движения и на основных потоках движения людей нужно сооружать мосты-переходы над рельсовыми путями или тоннели. Места движения людей, транспорта и работ должны быть хорошо освещены. Транспортные средства на территории предприятия должны двигаться с невысокой скоростью. На территории предприятия нужно строго соблюдать следующие правила: ходить только по пешеходным и переходным дорожкам, не переходить железнодорожные пути и дороги вблизи приближающегося транспорта, не пролезать под вагонами, стоящими на путях, а также не прыгать на ходу в вагоны или на платформы. Если на территории предприятия работает экскаватор или подъемные краны, запрещается стоять или ходить под ковшом или поднятым грузом.
Общие требования безопасности распространяются на все группы металлорежущих станков и содержат общие требования к станкам, электрооборудованию и местному освещению и дополнительные требования к станкам различных групп.
Общие требования безопасности к станкам относятся к защитным устройствам, органам управления, устройствам для установки и закрепления заготовок на станках и др. Эксплуатируемое оборудование должно быть в исправном состоянии. Работать на неисправном оборудовании запрещается. Оборудование должно располагаться на фундаментах или основаниях.
Проходы между станками должны быть свободными. Все передачи (зубчатые, ременные, цепные и др.) должны иметь специальные ограждения на высоте 2 м от уровня пола. Оборудование, работающее с выделением пыли (сухое шлифование), необходимо размещать в отдельном помещении, в котором должна быть приточная вентиляция и пылеотсасывающие устройства Подвесные транспортные устройства (монорельсы, конвейеры и др.) не должны располагаться под рабочим местом. Защитные устройства (экраны), ограждающие зону обработки, должны защищать рабочего от стружки и СОЖ. Защитные устройства, которые снимают при смене инструмента и заготовки, припод наладке станка и т. д., должны иметь массу не более 6 кг; они должны быть достаточно жесткими и при необходимости иметь смотровые окна нужных размеров.
Безопасность работы станочника во многом зависит от правильной организации его рабочего места и поддержания последнего в нормальном состоянии. Станочник должен строго выполнять все требования инструкций по охране труда. Основные правила безопасной эксплуатации металлообрабатывающих станков для рабочих всех профессий следующие:
Перед началом работы необходимо:
— проверить, хорошо ли убрано рабочее место, и при наличии неполадок в работе станка в течение предыдущей смены ознакомиться с ними и с принятыми мерами по их устранению;
— привести в порядок рабочую одежду. Застегнуть обшлаги рукавов, убрать волосы под головной убор;
— проверить состояние решетки под ноги, ее устойчивость на полу;
— проверить состояние ручного инструмента. Ручки напильников и шабера должны иметь металлические кольца, предохраняющие их от раскалывания. Гаечные ключи должны быть исправными; при закреплении болтов (гаек) размер их зева должен соответствовать размеру головки болта (гайки); не допускается применение прокладок и их удлинение с помощью труб, 5. Привести в порядок рабочее место: убрать все лишнее; подготовить и аккуратно разложить необходимые инструменты и приспособления в удобном и безопасном порядке (то, что берется левой рукой, должно находиться слева, а то, что правой, – справа). Уложить заготовки в предназначенную для них тару, а саму тару разместить так, чтобы взятие заготовок и укладка обработанных деталей не вызывала излишних движений рук и корпуса тела;
— при наличии местных грузоподъемных устройств проверить их состояние. Приспособления массой более 16 кг устанавливать на станок только с помощью этих устройств;
— проверить состояние станка: убедиться в надежности крепления стационарных ограждений, в исправности электропроводки, заземляющих (зануляющих) проводов, рукояток и маховичков управления станком. Разместить шланги, проводящие СОЖ, электрические провода и другие коммуникации, так, чтобы была исключена возможность их соприкосновения с движущимися частями станка или вращающимся инструментом;
— подключить станок к электросети, включить местное освещение и отрегулировать положение светильника так, чтобы рабочая зона была хорошо освещена и свет не слепил глаза;
— на холостом ходу проверить исправность кнопок «Пуск» и «Стоп», действие и фиксацию рычагов и ручек включения и переключения режимов работы станка, системы принудительного смазывания, а также системы охлаждения. Далее произвести или проверить настройку станка в соответствии с технологической документацией;
— подготовить средства индивидуальной защиты и проверить их исправность. Для предупреждения кожных заболеваний при необходимости воспользоваться средствами дерматологической защиты;
— обо всех обнаруженных недостатках, не приступая к работе, сообщить мастеру.
Общие требования во время работы:
— масса и габарит обрабатываемых деталей должны соответствовать паспортным данным станка;
— при обработке деталей массой более 16 кг производить установку и снятие с помощью грузоподъемных устройств, не допуская превышения нагрузки, установленной для них. Для перемещения применять специальные строповочные и захватные приспособления. Освобождать обработанную деталь от них только после надежной укладки, а при установке — только после надежного закрепления на станке;
— при необходимости воспользоваться средствами индивидуальной защиты. Запрещается работать в рукавицах и перчатках, а также с забинтованными пальцами без резиновых напальчников на станках с вращающимися обрабатываемыми деталями или инструментами;
— перед включением станка убедиться, что его пуск ни для кого не опасен; постоянно следить за надежностью крепления станочного приспособления, обрабатываемой заготовки в нем, а также режущего инструмента;
— при работе станка не производить переключения рукояток режимов работы, измерений, регулировки и чистки. Не отвлекаться от наблюдения за ходом обработки самому и не отвлекать других;
— если в процессе обработки образуется отлетающая стружка, установить переносные экраны для защиты окружающих и при отсутствии специальных защитных устройств на станке надеть защитные очки или предохранительный щиток из непрозрачного материала. Следить за своевременным удалением стружки, как со станка, так и с рабочего места, остерегаться наматывания стружки на обрабатываемую деталь или инструмент, не удалять стружку непосредственно руками, а пользоваться для этого специальными устройствами; запрещается с этой целью обдувать сжатым воздухом обрабатываемую деталь и узлы станка;
— правильно укладывать обработанные детали, не загромождать подходы к станку, периодически убирать стружку и следить, чтобы пол не заливался охлаждающей жидкостью и маслом; особое внимание обратить на недопустимость попадания стружки, СОЖ и масла на решетку под ноги;
— при использовании для привода станочных приспособлений сжатого воздуха следить за тем, чтобы отработанный воздух отводился в сторону от станочника;
— постоянно осуществлять контроль за устойчивостью деталей или штабелей из них на местах складирования, а при размещении деталей в таре обеспечить устойчивое положение их в ней, а также самой тары. Высота штабелей не должна превышать 0,5 м для мелких деталей, 1 м для средних деталей и 1,5 м для крупных деталей;
— обязательно выключать станок при уходе даже на короткое время, при перерывах в подаче электроэнергии или сжатого воздуха, при измерении обрабатываемой детали, а также при регулировке, уборке и смазывании станка;
— при появлении запаха горящейэлектроизоляции или ощущения действия электрического тока при соприкосновении с металлическими частями станка немедленно остановить станок и вызвать мастера. Не открывать дверцы электрошкафов и не производить какую-либо регулировку электроаппаратуры.
Общие требования по окончании работы:
— выключить станок и привести в порядок рабочее место. Разложить режущий, вспомогательный и измерительный инструмент по местам хранения, предварительно протерев его;
— стружку смести в поддон или на совок щеткой; чистку труднодоступных мест производить кистью или деревянной заостренной палочкой, обернутой ветошью. Во избежание несчастного случая и попадания стружки в механизмы запрещается для чистки станка использовать сжатый воздух;
— проверить качество уборки станка, выключить местное освещение и отключить станок от электросети;
— обо всех неполадках в работе станка, если они имели место на протяжении смены, сообщить сменщику или мастеру;
— осуществить санитарно-гигиенические мероприятия. Кроме указанного станочник обязан: работать только на том станке, к эксплуатации которого он допущен, и выполнять ту работу, которая поручена ему администрацией цеха; без разрешения мастера не допускать к эксплуатации станка других лиц; заметив нарушения правил по охране труда со стороны других станочников, предупредить их и потребовать соблюдения требований безопасности; в обязательном порядке требовать от администрации цеха проведения внепланового инструктажа при переводе на эксплуатацию станка другой модели или при привлечении к разовым работам, не входящим в круг обязанностей станочника; о всяком несчастном случае немедленно сообщить мастеру и обратиться в медицинский пункт; уметь оказывать первую помощь пострадавшему, применять первичные средства пожаротушения и проводить работы по устранению последствий аварийных ситуаций или пожара.
В производственных условиях не всегда еще удается устранить все опасные и вредные факторы, действующие на станочников, путем применения общетехнических мероприятий и средств коллективной защиты. В этих условиях обеспечения нормальных условий труда достигают применением средств индивидуальной защиты (СИЗ). В общем случае средствами индивидуальной защиты называют устройства, предназначенные для индивидуального применения во время работы в целях защиты определенных органов или частей тела человека от вредных и опасных факторов внешней среды.
В основу классификации СИЗ положены их целевое назначение, конструктивные и эксплуатационные свойства. В соответствии с государственным стандартом все СИЗ в зависимости от целевого назначения объединены в 11 классов, которые по конструктивным особенностям подразделяют на виды, а последние, в зависимости от эксплуатационных свойств, на группы.
За соблюдением безопасных условий работы в цехе осуществляется трехступенчатый или административно-общественный контроль. Первая ступень контроля: мастер (начальник цеха) вместе с общественным инспектором или дежурным по охране труда ежедневно за 15-20 мин до начала смены проверяют рабочие места, исправность оборудования, инструмента, технологической оснастки, работу вентиляционных установок, состояние ограждений, сигнализации и местного освещения, наличие знаков безопасности, средств индивидуальной защиты и их соответствие характеру выполняемой работы. Выявленные недостатки устраняют немедленно или разрабатывают мероприятия по их ликвидации. В течение смены мастер контролирует соблюдение технологической дисциплины, исправность оборудования и оснастки, чистоту рабочих мест, проходов и проездов, осуществляет надзор за выполнением станочниками безопасных приемов труда, использованием средств индивидуальной защиты. Все зафиксированные мастером в специальном журнале нарушения правил по охране труда и фамилии нарушителей подлежат обсуждению на производственных планерках или собраниях.
Вторая ступень контроля: начальник цеха, председатель комиссии по охране труда цехового профсоюзного комитета, инженер по охране труда, а также работники технических служб цеха еженедельно обходят участки цеха и проверяют выполнение мероприятий по устранению недостатков, выявленных при предыдущих проверках, а также недостатков, зафиксированных мастерами в журналах в течение недели, в целях разработки мероприятий по их устранению.
Третья ступень контроля: утверждается комиссия под председательством главного инженера предприятия, которая работает по специальному графику и контролирует качество проверок на первой и старей ступенях, а также общее состояние охраны труда и культуры производства в подразделениях и цехах предприятия. Результаты проверки отражаются в приказе по предприятию.
2.9 Мероприятия по охране окружающей среды при обработке детали
Защита об оздоровлении экологической обстановки, создание более благоприятных, с экономической точки зрения, условий жизни и деятельности людей, становиться одной из важнейших задач, как мирового общества, так и каждой отдельно взятой страны.
Основными загрязнителями воздушного бассейна являются оксиды углерода и серы, углеводород, оксиды азота, а также высокотоксичные соединения свинца.
Не менее острой является проблема загрязнения подземных и наземных вод. Оценка состояния водного бассейна свидетельствует о тенденции роста концентраций минерального азота, фосфора, калия, сульфатов и др. элементов, поступающих с сельскохозяйственных угодий, в результате сброса загрязненных сточных вод городов и других населенных пунктов.
Одной из серьезнейших проблем Беларуси является проблема утилизации, обезвреживания и захоронения промышленных отходов.
Сложившаяся экологическая обстановка в республике значительно снижает качественны уровень жизни населения, ограничивает возможность развития таких природоохранительных мероприятий, которые бы обеспечивали снижение либо исключение загрязнения окружающей среды.
Важное место в этом направлении должна занимать подготовка экологически грамотных специалистов в высшей школе. С учетом существующих проблем законами Республики Беларусь «Об образовании» и «Об охране окружающей среды» закреплена приоритетность экологического образования во всех учебных заведениях.
В связи с описанными проблемами с 1.07.1997 на промышленных предприятиях изготавливается экологический паспорт, который составляется согласно ГОСТ 17.0.04-90.
Экологический паспорт промышленного предприятия – это нормативно-технический документ, включающий данные предприятия об использовании ресурсов и определения его влияния на окружающую среду.
Экологический паспорт предприятия представляет комплекс данных, выраженных через систему показателей, отражающих уровень использования предприятием природных ресурсов и степенью его воздействия на окружающую среду.
Экологический паспорт разрабатывается за счет его средств и утверждается руководителем предприятия по согласованию с территориальными органами по охране труда и природе, где он регистрируется.
Основой для разработки экологического паспорта являются согласованные и утвержденные показатели производства, разрешенные на предприятии, разрешение на природопользование, паспорта газо- и водосточных сооружений и установок по утилизации отходов.
Экологический паспорт не заменяет и не отменяет действующие формы и виды государственной отчетности.
2.10 Решение проблем энерго- и ресурсосбережения при производстве данной детали
Машиностроение представляет собой энергоемкую сферу промышленного производства, где, в результате морального и физического старения основных фондов происходит постоянное и непрерывное увеличение потребления энергии. Рост расходов на энергетические ресурсы и вызываемое им повышение себестоимости машиностроительной продукции обозначает необходимость сокращения энергетической составляющей в издержках производства. Для получения максимального эффекта от реализации программы энергосбережения на предприятиях машиностроения она должна представлять собой оптимальную для него совокупность энергосберегающих мероприятий. Для этого необходимо, с одной стороны, классифицировать объекты энергосбережения и их социально-экономические результаты, и, с другой, сформировать и обосновать систему показателей эффективности энергосбережения. При этом наибольшее значение имеет оценка экономической эффективности совокупности энергосберегающих мероприятий, которую в каждом конкретном случае определяет специфика технологического процесса на различных стадиях производства конечного продукта. Исходя из этого необходимо учитывать особенности оценки экономической эффективности мероприятий в соответствии с результатами энергосбережения на машиностроительном предприятии: при подготовке основного производства, в процессе основного производства, на вспомогательных производствах, при складировании продукции, модернизации основного и обслуживающих производств.
Указанные особенности должны быть учтены в соответствующих расчетах за счет внесения изменений при определении прибылей и убытков предприятия, которые, в свою очередь, вызываются различными социально-экономическими результатами энергосберегающих мероприятий, входящих в программу энергосбережения. На сегодняшний день программы энергосбережения разрабатывают обычно эксперты технологического сектора, не знакомые с экономическим механизмом энергосбережения. В связи с этим большинство имеющихся программ не содержат оценок экономического эффекта и не создают стимулов к энергосбережению.
Можно сделать вывод о том, что рациональное использование энергетических ресурсов на предприятии является важной составляющей снижения производственных издержек, и, следовательно, получения дополнительной прибыли, завоевания большей доли рынка и решения социальных проблем на основе:
— реализации процесса подготовки производства в соответствии с оптимальными режимами ввода основных средств в эксплуатацию;
— использования наиболее рентабельных производственных технологий;
— разработки, освоения и внедрения новой техники и технологий, в которых энергетические ресурсы используются более эффективно;
— улучшения социально-бытовой сферы для персонала машиностроительного предприятия и социального климата населения, проживающего на территории, закрепленной за соответствующим предприятием.
Вследствие этого, энергосбережение рассматривается не как бесцельная экономия энергетических ресурсов, проводимая зачастую за счет сокращения объема производства, а как фактор экономического роста, улучшения благосостояния населения, обеспечения соответствующей экологической и социально-бытовой обстановки. Таким образом, энергосбережение должно быть одним из приоритетных направлений экономической политики промышленного предприятия. В то же время сегодня пристального внимания заслуживает оценка эффективности энергосбережения и ее составляющих, которую необходимо учитывать при последующей разработке целевых программ энергосбережения и сценариев их реализации.
Основные этапы разработки программы энергосбережения:
Энергоаудит. Энергетическое обследование (энергоаудит) проводится в целях определения путей быстрого и эффективного снижения издержек на энергоресурсы, сокращения и исключения непроизводительных расходов (потерь), оптимизации или замены технологии производства. Он может стать основательной базой, трамплином для качественного рывка в конкурентной борьбе на рынке товаров и услуг.
Существуют три способа снижения потребления энергии:
— исключение нерационального использования энергоресурсов;
— устранение потерь энергоресурсов;
— повышение эффективности использования энергоресурсов.
Энергоаудит условно можно разделить на четыре основных этапа:
— ознакомление с предприятием, сбор и анализ необходимой информации, составление программы обследования. На этом этапе производится уточнение объемов и сроков проведения работы;
— обследование предприятия. В том числе: разработка подробных балансов по всем энергоресурсам, выявление основных потребителей и "очагов" нерациональных потерь энергоресурсов; проведение необходимых испытаний и инструментальных замеров;
— разработка энергосберегающих проектов и мероприятий. Определение технического и экономического эффекта от их внедрения. Формирование программы энергосбережения предприятия;
— оформление отчета по энергетическому обследованию и энергетического паспорта предприятия. Презентация результатов работы.
Структурно программа энергосбережения состоит из следующих разделов: общей части, нормативно-правовой базы, перечня основных направлений энергосбережения, программного блока, информационно - образовательного блока и приложений.
В первом разделе сформулированы цели и задачи программы, ожидаемые результаты, основные принципы построения и управления, а также приведена схема управления энергосбережением предприятия.
Особое внимание уделено принципу возвратности средств финансирования мероприятий по энергосбережению, стимулированию производителей, потребителей и поставщиков энергии, а также компаний, занимающихся решением практических вопросов энергосбережения.
Нормативно-правовая база содержит перечень первоочередных нормативно-правовых актов, которые должны быть учтены при разработке программы.
Основная часть программы энергосбережения – программный блок, включающий организационно-технические мероприятия, перечень проектно-конструкторских и научно-исследовательских работ в области энергосбережения, а также перечисление первоочередных объектов создания демонстрационных зон высокой энергетической эффективности.
Главной особенностью построения программного блока является возможность разработки на его основе детальных годовых программ энергосбережения и оптимизации направлений энергосбережения предприятия.
Информационно-образовательный блок содержит два основных вида этой деятельности: подготовку и переподготовку специалистов всех уровней по энергосбережению, пропаганду идей энергосбережения.
Основными принципами программы энергосбережения являются:
— приоритет повышения эффективности использования топлива и энергии над увеличением объемов добычи и производства;
— сочетание интересов потребителей, поставщиков и производителей топлива и энергии;
— первоочередность обеспечения выполнения экологических требований к добыче, производству, переработке, транспортировке и использованию топлива и энергии;
— обязательность учета юридическими лицами производимых или расходуемых ими энергетических ресурсов, а также учета физическими лицами получаемых энергетических ресурсов;
— сертификация топливно-, энергопотребляющего, энергосберегающего и диагностического оборудования, материалов, конструкций, транспортных средств, а также энергетических ресурсов;
— аинтересованность производителей и поставщиков энергетических ресурсов в применении эффективных технологий;
— осуществление мероприятий программы за счет собственных средств либо на возвратной основе.
Основными целями программы энергосбережения предлприятия являются:
— повышение эффективности использования энергетических ресурсов на единицу продукта предприятия;
— снижение финансовой нагрузки за счет сокращения платежей за топливо, тепловую и электрическую энергию;
— улучшение финансового состояния предприятия за счет снижения платежей за энергоресурсы и, соответственно, дополнительное пополнение бюджета области за счет налоговых поступлений.
Цели программы достигаются путем внедрения эффективных технологий и разработки эффективных финансово-экономических механизмов производства, транспортирования и потребления энергетических ресурсов, проведения мероприятий по энергосбережению, внедрения систем учета.
Основные направления энергосбережения:
— энергоаудит – проведение энергетических обследований организаций;
— энергоучет – внедрение централизованных систем учета энергоресурсов на промышленных предприятиях.
— регулирование энергопотребления – внедрение систем регулирования потребления энергоресурсов от источника их производства до конечного потребления;
— реконструкция промышленных вентиляционных установок;
— модернизация топливных и электрических печей;
— модернизация энергетического оборудования.
Для успешного выполнения и дальнейшего развития программы наиболее подходящим инструментом является система управления проектами, широко применяемая в мировой практике.
Программа должна создавать условия, позволяющие сочетать интересы ее участников в направлении намеченных приоритетов. Она является многопроектной средой с различным статусом проблем и проектов: важнейшие проблемы, требующие срочных действий; проблемы, нуждающиеся в дополнительной проработке; проблемы, решаемые в ходе регулярного планирования; региональные, районные, городские, отраслевые проекты, проекты отдельных предприятий и т.д. Поэтому, для достижения поставленных целей, необходима система управления, структура которой будет разрабатываться и оптимизироваться при формировании нормативно-правовой базы энергосбережения предприятия.
4.2.2 Большая часть разработанных в последние годы технологий машиностроения обеспечивает ресурсосбережение. Здесь наиболее высокие показатели достигнуты в снижении металлоемкости продукции. Металлосбережение осуществляется, главным образом, на основе широкого внедрения в производство новых конструкционных материалов и использования новых технологий в производстве заготовок. Значительный экономический эффект достигается при использовании новых технологий изготовления режущего инструмента за счет существенного повышения его износостойкости и соответственно увеличения сроков эксплуатации. Применение технологий напыления металлокерамическими порошками позволяет снижать потребление высокоуглеродистых сталей и некоторых других дорогостоящих металлов. Разработанные методы газотермического напыления экономически выгоднее дорогостоящих вакуумных технологий. Внедрение прогрессивных технологий позволяет наряду с выпуском инновационной продукции, отличающейся высокими эксплуатационными характеристиками, существенно снижать затраты на производство. Существующие темпы освоения новых технологий обеспечили снижение материалоемкости машиностроительной продукции за пять лет на 17%. Этот показатель 20 лет назад можно было бы считать удовлетворительным. В настоящее время современные технологии позволяют существенно снизить потребление металла в машиностроении.
2.11 Данные необходимые для выполнения экономического раздела
Тип производства согласно ГОСТ 3.1108-74 устанавливается на основе определения коэффициента закрепления операций (КЗ.О).
Согласно ГОСТ 1.4003-83 имеются следующие коэффициенты закрепления операций:
для массового производства 1 < КЗ.О < 10;
для крупносерийного производства 1 < КЗ.О < 10;
для среднесерийного производства 10 < КЗ.О < 20;
для мелкосерийного производства 20 < КЗ.О < 40
Коэффициент закрепления операций определяется по формуле:
Σ Поi – суммарное число операций за месяц по участку;
Σ Pi – явочное число рабочих, выполняющих различные операции
– нормативный коэффициент загрузки станка([5]стр.119);
– месячная программа выпуска
Станок 16Б16Т1
Станок 2А135Ф2
Станок 7Б55
Станок 53А20
Станок 3У142
Станок 3М151Ф2
Станок 5А841
ΣПОi =14,935+56,49+34,44+2,551+2,78+34,268+1,677=147,141
Рi= 1,9 ∙ ηм
P1 = P2 = P3 = P4 = P5 = P6 = P7 =1,9∙ 0,75=1,425
ΣPi = P1 ×7=1,425×7=9,975
КЗ.О=ΣПОi/ΣPi =147,141/9,975=14,75
Производство – среднесерийное
Количество станков определяется по формуле
Fд – действительный фонд времени работы станка:
Fд =4015 – универсальные станки;
Fд =4015 – станки с ЧПУ
Станок 16Б16Т1
Станок 2А135Ф2
Станок 7Б55
Станок 53А20
Станок 3У142
Станок 3М151Ф2
Станок 5А841
Принятое число станков
Sпр1= Sпр2= Sпр3= Sпр4= Sпр5= Sпр6= Sпр7 =1
Определяем коэффициент загрузки станоков по штучно-калькуляционному времени по формуле
ηзi=Si/Sпрi
и строим график.