
























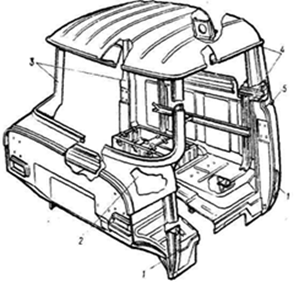
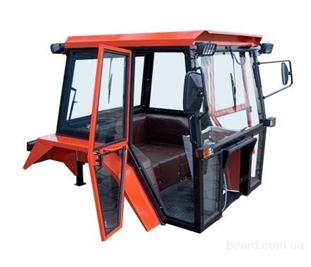
а) б)
Рис. 7.1. Дефекты кабины грузового автомобиля и трактора
Восстановление металлического сварного кузова или кабины целесообразно выполнять в следующей последовательности:
– предварительная правка панелей кузовов или кабин, имеющих аварийные повреждения;
– удаление поврежденных участков панелей, которые затем восстанавливаются постановкой ДРД;
– устранение имеющихся трещин и разрывов;
– приварка предварительно изготовленных и собранных деталей и узлов вместо удаленных;
– проковка и зачистка сварочных швов;
– окончательная правка и тонкая рихтовка поверхностей.
Предварительная правка кузовов и кабин, имеющих аварийные повреждения, производится на специальных стендах или с использованием набора растяжек (рис. 7.2, 7.3).
Рис. 7.2. Набор оборудования и приспособление для правки кузовов и кабин:
1 – оправка для вытягивания вогнутых деталей; 2, 3 – самозакрепляющиеся гидравлические зажимы; 4 – специальная оправка; 5 –гидравлическая струбцина; 6 – пневмогидравлический насос; 7 – правильное устройство; 8– двойной захват; 9 – натяжной цилиндр с вытягивающим устройством; 10– натяжной цилиндр с захватами.
|
|
Набор для правки кузова с тележкой GYSLINER W 3502 (рис. 7.3) (GYSLINER + GYSPOT 3502).
Рис. 7.3. Набор оборудования и тележка GYSLINER W 3502 для правки
Отличительными особенностями GYSLINER + GYSPOT 3502 то, что не требует демонтажа и замены ремонтируемых деталей, уменьшает время восстановления и увеличивает рентабельность.
В комплекте GYSLINER + GYSPOT 3502 имеются:
– GYSPOT 3502 – аппарат для точечной сварки;
– Manuspot;
– рычаг с одной опорой для правки без крюков;
– рычаг с двумя опорами для правки без крюков;
– рычаг с двумя опорами для правки без крюков;
– сдвоенная опора с для правки 2 шт.;
– рычаг для вытягивания 1.20м без опор;
– крюк с 4-мя зацепами;
– крюк с 6-тью зацепами;
– крюк с 8-тью зацепами;
– набор из 3-х стержней;
– набор расходников для стали: змейки 25шт., серьги 50шт., серьги крученые 25шт.;
– земляная масса с магнитным держателем;
– поддержка на присосках;
– тележка.
При больших деформациях панелей правку производят с нагревом поврежденных мест, а при малых геометрических искажениях — в холодном состоянии. Предварительной правкой устраняются глубокие вмятины, изгибы и перекосы корпусов кабин и кузовов. Эту операцию следует производить перед сварочными работами, так как в процессе ее выполнения могут образоваться трещины или разрывы, которые в дальнейшем завариваются.
Удаление поврежденных участков панелей производится газовым резаком, электрифицированным фрезерным инструментом или резцом с пневматическим приводом. Наибольшее распространение при ремонте панелей нашли пневматический резец и процесс газовой резки. Удаление поврежденных частей панелей пневматическим резцом обеспечивает лучшее качество кромок в местах вырезки. Однако несложность оборудования и возможность совмещения операций удаления поврежденных панелей и приварки новых обеспечили газовой сварке широкое применение при ремонте кузовов и кабин. Перед вырезкой дефектные участки размечают с помощью специальных шаблонов. Разметочные шаблоны по форме соответствуют дополнительным ремонтным деталям. При удалении дефектных деталей с корпуса кабины или кузова необходимо принять меры по предохранению корпуса от геометрических искажений вследствие ослабления его жесткости и под действием собственной массы.
|
|
Трещины и разрывы в панелях кузовов, кабин и оперения устраняют с помощью электродуговой сварки в среде углекислого газа и газовой сварки. При ремонте используются в равной степени оба способа, однако производительность процесса и качество выполняемых сварочных работ при электродуговой сварке в среде углекислого газа выше.
Газовой сваркой устраняются трещины и разрывы на панелях, изготовленных из листовой стали толщиной 0,5… 2,5 мм. Для ограничения распространения трещины по длине в процессе сварки ее концы засверливают. Затем выполняют сварку горелками ГСМ-53 или ГС-53 с наконечниками № 1 для листов толщиной 0,5…1,5 мм и № 2 для листов толщиной 1…2,5 мм при предельном давлении кислорода 0,1…0,4 Мпа. Для сварки применяется проволока марки Св. 08 или Св. 15 диаметром 0,5 мм (h — толщина свариваемого листового материала). Для предотвращения коробления при нагреве сварку производят вначале в отдельных точках, расстояние между которыми должно быть 10…30 мм. Затем по мере необходимости отдельные участки проваривают сплошным швом в направлении от концов трещины к середине.
Приварку ремонтных деталей и панелей целесообразно производить полуавтоматической сваркой в среде углекислого газа. Этот вид сварки применяется также и для устранения трещин и разрывов на стойках корпуса кузова или кабины и в элементах основания. Сварка в среде углекислого газа осуществляется полуавтоматами постоянным током обратной полярности электродной проволокой Св. 08ГС или Св. 082ГС. Заварку трещин выполняют сварочной проволокой диаметром 0,7 мм при силе тока 40 А и напряжении 30 В.
При сварке ремонтных деталей и панелей вначале производится операция их прихватывания к корпусу отдельными точками, расстояние между которыми 80…120 мм. «Прихватка» выполняется проволокой диаметром 0,8 мм той же марки, что и для сварки основных швов при силе сварочного тока 90…110 А и напряжении на дуге 18… 28 В. Окончательно панели приваривают сплошным швом внахлестку с перекрытием краев около 25 мм. Рекомендуется следующий режим сварки: сила тока до 100 А, напряжение 19…20 В, расстояние от сопла до поверхности детали 8…10 мм, вылет электрода 10…12 мм, наклон электрода от вертикали 18…20°.
Контактно-точечная сварка применяется при ремонте кузовов и кабин для сборки панелей в сборочные единицы, которые затем целиком присоединяются к корпусу. При точечной сварке соединение панелей выполняется внахлестку с помощью машины МТПП-75. Ширина отбортовки кромок устанавливается исходя из минимального расстояния от центра сварочной точки до края. При сварке двух деталей расстояние до края должно быть равно двум диаметрам точки, а при сварке трех деталей – четырем диаметрам. В случаях, когда невозможен двусторонний подход электродов к месту соединения, могут быть использованы однополюсные распорные пистолеты, присоединенные к трансформатору передвижных сварочных устройств. Повышение производительности процесса контактно-точечной сварки панелей кузовов, кабин и оперения осуществляется путем использования роботизированных комплексов. Однако применение роботов связано с большими затратами, поэтому они могут быть использованы только для сварки панелей или сборочных единиц кузовов, которые при восстановлении и КР заменяются в обязательном порядке.
|
|
При выполнении сварочных работ требуется большое внимание уделять созданию для сварщиков необходимых санитарно-гигиенических условий. При нагревании защитных противокоррозионных средств на битумной основе, которые иногда остаются на панелях кузова, возникают густой дым и испарения, вредные для здоровья работающего. Ядовитые испарения и дым должны удаляться системой вентиляции. Для защиты глаз и лица сварщик должен пользоваться шлемом-маской или щитком с защитными стеклами. Руки сварщика должны быть защищены брезентовыми рукавицами, а сам он одет в брезентовый костюм. При использовании углекислого газа следует помнить, что при утечке он скапливается в ямах, канавах и других низких местах.
Изготовление металлических ремонтных деталей панелей кузовов, кабин и оперения выполняется авторемонтными предприятиями ввиду отсутствия их в номенклатуре запасных частей. Типовой технологический процесс изготовления ремонтных деталей из листового металла складывается из следующих операций:
– правки листа стали;
– раскроя материала;
– резки заготовок по разметке;
– загиба детали или формообразования на специальном оборудовании;
– обрезки готовых деталей;
– сверления, правки и зачистки.
Особую сложность в выполнении представляет операция формообразования деталей. При наличии больших производственных программ ремонтные детали изготовляют холодной штамповкой на прессах с использованием роботизированных комплексов (рис. 7.4).
Рис. 7.4. Роботизированный технологический комплекс на базе однокривошипного пресса простого действия:
|
|
1 – система управления роботом; 2 – устройство поштучной выдачи заготовок; 3 – электрошкаф пресса: 4 – пресс; 5 – тара для отштампованных деталей; 6 – датчики внешней информации; 7 – промышленный робот; 8 – ограждение комплекса
На однокривошипных прессах простого действия выполняются листоштамповочные операции вырубки, пробивки, неглубокой вытяжки. Операции, выполняемые промышленным роботом, зависят от его конструкции и наличия вспомогательных устройств. При изготовлении ремонтных деталей штамповкой на прессах роботизированные технологические комплексы обеспечивают:
– захватывание заготовки с исходной позиции питателя;
– перенос ее в рабочую зону пресса;
– укладку в штамп;
– захватывание отштампованной детали;
– укладку ее в тару или на транспортное средство.
Кроме того, робот может захватывать и выносить из рабочей зоны пресса отходы в рядом расположенную тару.
Проковка и зачистка сварочных швов производятся для упрочнения места сварки и придания ему необходимого профиля панели, а также для создания лучшей герметичности кузова или кабины. Проковку выполняют пневматическим рихтовочным молотком при помощи комплекта поддержек. Места сварки зачищают шлифовальными кругами, установленными в пневматических или электрических переносных машинах.
Окончательная правка и тонкая рихтовка кузовов, кабин и оперения выполняются с целью обеспечения их правильной геометрической формы, а также для удаления мелких вмятин и выпучин, оставшихся на поверхностях.
Тонкую рихтовку выполняют механизированным способом с помощью пневматических рихтовальных молотков. Все восстановительные работы с корпусом кузова или кабины, как правило, выполняются на конвейерной линии.
Ремонтные работы на постах выполняют на стендах-тележках (рис. 7.5 (а)), позволяющих устанавливать и закреплять кабины, поворачивать их, а также передвигать по рельсовым путям конвейера. Стенд-тележка состоит из рамы 1, в нижней части которой установлены четыре колеса 2, и механизма фиксации 3 с тяговой цепью конвейера, педали 4, стойки 5, в верхней части которой на плите закреплен самотормозящий редуктор 7, и опорного диска 9 в сборе с опорой 10. Кабину устанавливают на опору 10 стенда и крепят в двух точках. При ремонте кабину вращают вокруг оси А—А при помощи рукояти 6 редуктора и фиксируют ее положение стопором 8. Восстановленные корпуса кузовов, кабин и оперение поступают затем на линию сборки до окраски.
а) б)
Рис. 7.5. Стенд-тележка для ремонта кабин а), векторная анкерная система для правки кабин и рам грузовиков б)
7.6.2. Восстановление неметаллических деталей кузовов и кабин.
Как в тракторостроении так и в автомобилестроении широко распространены неметаллические материалы. К таким материалам относятся: пластмассы, синтетические кожи, дерево, стекло, резина. В последнее время значительно возросло применение различных пластмасс. Большинство деталей из этих материалов дешево в изготовлении и при ремонте тракторов автомобилей восстановлению не подлежит, а заменяется новыми.
Полимеры в ремонтном производстве используются для изготовления небольших деталей декоративного назначения, арматуры, для устранения дефектов деталей. Детали из реактопластов изготовляются обычно прямым прессованием или литьевым прессованием. Детали из термопластов изготовляют литьем под давлением в термопластавтоматах, в экструдерах или с помощью вакуумного формования.
Вакуумное формование деталей внутренней отделки салона как трактора так и автомобиля основано на деформировании пленочного термопластического материала в эластичном состоянии за счет разности между атмосферным давлением и разрежением, создаваемым внутри формы. На рис. 7.6 представлено вакуумное формование детали с механической вытяжкой.
Рис. 7.6. Вакуумное формирование детали с механической вытяжкой пленки
Пуансон 2, имеющий каналы 3 для отсоса воздуха, устанавливают на рабочем столе-толкателе 5 и соединяют с приводом 6. Пленку закрепляют на прокладке 4 на зажимном устройстве над пуансоном и нагревают до температуры формования. Затем пуансон 2 поднимают вверх и растягивают пленку. После окончания подъема пуансона и вытяжки пленки воздух из полости пуансона отсасывают. При этом создается разрежение между пуансоном и пленкой. Размягченная пленка плотно прижимается к пуансону, точно воспроизводя контуры его поверхности. Этим методом можно получить детали с малыми радиусами закругления и стенками, близкими к вертикальным, а также детали, глубина которых равна их ширине.
Обивку кузовов икабин при КР снимают полностью. Подушки и спинки сидений разбирают, изношенные детали ремонтируют или заменяют новыми. Наиболее распространенными повреждениями в обивке являются: потёртости и разрывы верхней части обивки, в подушках сидений и подлокотниках; поломка оснований сидений; вырывы и разрывы в прокладках сидений из губчатой резины; загрязнение обивки. Ремонт обивки включает: разборку обивки в зависимости от её состояния, восстановление элементов подушек и спинок сидений, устранение дефектов обивки, раскрой и пошивку новых деталей, сборку обивки после ремонта.
При ремонте обивки выполняют все виды работ, присущие процессу изготовления новой обивки, и дополнительные работы, связанные с разборкой обивки и очисткой её деталей от концов ниток, пыли и загрязнений, а также подготовку поверхностей, подлежащих восстановлению. При разборке сшивные швы распарывают. Края обивки, которые приклеены к картону, необходимо смочить бензином.
Устранение дефектов обивки включает постановку ее новых частей, приклейку или пришивание оторванных частей, порезов и разрывов. Для пошива новых деталей обивки материал предварительно раскраивают по шаблонам на заготовки. Соединяемые детали прошивают с нелицевой стороны на заданном расстоянии от кромок одинарным или двойным швом с определенным шагом строчки. Сшитая обивка не должна иметь слабой затяжки, перекосов, морщин, складок и повреждений на лицевой стороне. Подушки и спинки сидений собирают на стендах с пневматическим устройством, позволяющим сжимать матрац подушек сидений для обеспечения натяжения материала и предотвращения образования морщин и складок на лицевой стороне.
Приклеивание края обивки двери к древесноволокнистой панели производится по нелицевой стороне с последующей выдержкой под прессом в течение 30 мин. Верх обивки сидений, изготовленной из поливинилхлоридной пленки, армированной сеткой из синтетических волокон, при необходимости склеивается клеем 88НП при последующей выдержке отремонтированного места под прессом в течение 1…1,5 ч. Такой же режим склеивания рекомендуется при ремонте обивки дверей и подлокотников, изготовленных из неармированной поливинилхлоридной пленки.
Ремонт деревянных деталей платформы кузова выполняют наращиванием их по длине склеиванием или заменой негодных деталей новыми. При ремонте следует учитывать место расположения восстановленной детали в собранном изделии, условия ее работы, породу древесины. Деревянные детали изготовляют из пиломатериалов хвойных пород (сосна, ель), имеющих влажность не выше 18 %. Для склеивания деревянных деталей применяют клей казеиновый и из синтетических смол. Качество клеевого соединения зависит от силы сжатия склеиваемых поверхностей деталей, вязкости клея, температуры и времени выдержки под давлением. Восстановленные деревянные детали должны быть без трещин, задиров и ступенчатости; торцы – чистыми, без отщипов и сколов.
Остекление кузовов и кабин при ремонте должно быть надежно восстановлено. Установка лобовых и боковых стекол, через которые осуществляется обзор дороги с какими-либо дефектами, запрещена. Недопустимы желтизна, радужность, нечеткость обзора, износ от щеток стеклоочистителей. Указанные дефекты могут быть устранены шлифовкой и последующей полировкой поврежденных участков.
Перед шлифовкой стекло, подлежащее обработке, очищают от грязи, пыли и жировых загрязнений. Места, требующие шлифования, выделяют мелом. Затем на войлочную обивку круга шлифовального станка с вертикальной осью вращения наносится разномерный слой пасты, представляющий собой водный раствор порошка пемзы, и отмеченные места шлифуют с частотой вращения круга 300…400 мин-1 до полного выведения рисок, царапин и следов изнашивания.
По окончании шлифования со стекла смывают остатки пасты, на круг наносят водный раствор крокуса или полирита и полируют стекло до получения необходимой прозрачности. Частота вращения круга при полировании принимается 700…800 мин-1. По окончании полирования стекло обезжиривают, протирают насухо и упаковывают в бумагу.
7.6.2. Ремонт и восстановление основных механизмов, и оборудования кузовов, и кабин.
К основным механизмам и оборудованию кузовов и кабин относятся: замки и петли дверей и капотов, стеклоподъемники и механизм крепления стекол, оборудование системы вентиляции и отопления салона, пневматические дверные механизмы, подъемный механизм платформы автомобиля-самосвала.
Все детали кузовных механизмов просты по своей конструкции, и ремонт их заключается в выполнении несложных слесарно-сварочных операций. Имеющиеся трещины в корпусах заваривают, а износы рабочих поверхностей устраняют наплавкой или постановкой дополнительной ремонтной детали. Корпусные детали с обломами выбраковывают. Пружины, потерявшие свою упругость, и сломанные заменяют новыми. Обломанные детали резьбовых соединений вывертывают или высверливают, если не удается удалить болт вывертыванием. Поврежденные резьбы в отверстиях прогоняют метчиком либо заваривают и после сверления отверстия под резьбу нужного размера нарезают новую резьбу. Разрушенные манжеты, сальники, уплотнительные кольца и прокладки заменяют новыми. Ремонт замков дверей (рис. 7.7) и капотов заключается в устранении дефектов механического характера, обеспечении необходимых зазоров и натягов в сопрягаемых деталях.
Рис. 7.7. Замок двери
При наличии люфта между кожухом ротора 8 и корпусом замка 5 или при ослаблении клепки в месте соединения ротора замка 9 с храповиком 10 выбивают заклепку 3 щеколды 6 и отводят щеколду в сторону: места расклепки кожуха и храповика окажутся доступными для замены заклепок или сварки. Затем расклепывают или приваривают к корпусу лапки кожуха 8 ротора замка и хвостовик ротора 9 в месте соединения с храповиком 10. Вращение ротора должно быть легким, без заеданий. После этого устанавливают заклепку щеколды, щеколду, втулку, шайбы и расклепывают конец оси, обеспечив свободное вращение щеколды на оси. Если головка заклепки выступает над поверхностью фиксатора 2, ее следует запилить заподлицо с поверхностью. При наличии обломов рычага 1, пружины 4 и защелки храповика 7 они заменяются новыми. При износе зубьев защелки 11 замка ее заменяют новой. Для замены сухаря 13 защелки необходимо вынуть ось 12, сухарь и пружину 14. Ось сухаря заменяется новой.
Ремонт петель дверей, крышек багажника и капота (рис. 7.8) заключается в правке погнутости петель 3, замене изношенных осей 1 и втулок 2 новыми, устранении трещин и восстановлении отверстий 4 заваркой с последующей механической обработкой. Восстановленные петли должны исключать провисание дверей, перекосы капота и крышки багажника.
Рис. 7.8. Петли дверей (а) и крышки багажника (б) в сборе
Наиболее характерные дефекты стеклоподъемников и механизма крепления стекол: трещины и обломы деталей, перекос и деформация обойм, рамок и направляющих, нарушение крепежных соединений (резьбовых, клепаных) деталей к панели двери, повреждение резиновых уплотнителей, коррозия деталей.
Детали, имеющие трещины, завариваются с последующей зачисткой сварочного шва. Погнутые рычаги правят в холодном состоянии на плите. Обломанные детали восстанавливают постановкой дополнительной ремонтной части или выбраковывают. Ремонт механизма крепления стекол состоит из демонтажа их из рамок, замены уплотнительных прокладок в рамках и установки стекол в рамки. Перед установкой стекол в рамки проверяют прямолинейность рамок, обойм и при необходимости их правят. При запрессовке стекол необходимо следить, чтобы обойма встала на свое прежнее место по ширине стекла, так как иначе стекло будет плохо подниматься и опускаться в направляющих желобках.
Калориферная система вентиляции и отопления кузова или кабины состоит из следующих узлов: радиатора, крана управления, вентилятора, кожухов, крышек люков притока и распределения воздуха.
Технология ремонта радиатора отопителя аналогична процессу восстановления радиаторов системы охлаждения двигателя. Вентиляторы отопителей, требующие ремонта, отправляют в отделение ремонта электрооборудования тракторов либо автомобилей.
Вмятины, трещины и изломы металлических деталей воздуховодов устраняются жестяницкими и сварочными операциями. При ремонте жалюзи воздуховодов правкой необходимо обеспечить нормальное передвижение установленных на них задвижек. После ремонта трубы отопления и вентиляции испытывают на герметичность сжатым воздухом в ванне с водой. Поврежденные соединительные резиновые шланги заменяют новыми.
В пневматическом дверном механизме кузовов (рис. 7.9) встречаются следующие неисправности: срыв резьбы в деталях механизма; износ манжет, сальников, уплотнительных колец, втулок наконечников штоков и тяг вмятины на поверхности цилиндров, изгиб штоков, срез шлицев рычагов управления; потеря упругости пружин.
Рис. 7.9. Механизм управления дверями:
1 – крышка дверного цилиндра; 2 – большой поршень; 3, 11 – уплотнительные кольца; 4, 9 – сальники; 5 – манжета большого поршня; 6 – цилиндр дверного механизма; 7, 12 – штоки; 8 – манжета малого поршня; 10 – малый поршень; 13 – малый цилиндр; 14 – хомут; 15 – защитный кожух; 16 – шайба; 17 – шейка; 18 – откидной болт.
Восстановление деталей механизма открывания дверей сводится к выполнению следующих работ. В деталях, имеющих сорванную резьбу, нарезают ремонтную резьбу. Изношенные втулки наконечников или других деталей заменяют новыми. После запрессовки отверстия новой втулкой её развертывают до номинального размера. Погнутые штоки поршней выправляют на призмах. При небольшом износе отверстий в вилках тяг их рассверливают под ремонтный размер. Изношенные манжеты, сальники и уплотнительные кольца заменяют новыми. Трещины в местах пайки цилиндра разделывают и запаивают. Вмятины на цилиндрах устраняют протяжкой, имеющей калиброванную и хорошо отполированную сферическую поверхность, на гидравлическом прессе. Диаметр сферической поверхности должен соответствовать внутреннему диаметру цилиндра. Пружины, потерявшие упругость, заменяют новыми. Рычаги управления с поврежденными шлицами, а также тяги и вилки с поврежденной резьбой заменяют новыми. Испытывают дверной механизм на стендах, предназначенных для контроля и регулировки пневматического оборудования.
Восстановление подъемного механизма платформы грузового автомобиля-самосвала производят только при значительных изменениях работоспособности его узлов, когда резко увеличивается время подъема платформы с грузом и снижается надежность работы механизма. Значительную долю трудозатрат по восстановлению занимает гидравлический подъемник (рис. 7.10). Трещины на головке цилиндров устраняют сваркой при условии, если она не проходит через крепежные отверстия.
Рис. 7.10. Гидравлический подъемник автомобиля-самосвала:
1 – грязесъемник гильзы; 2 – грязесъемник корпуса; 3 – сектор втулки плунжера; 4 – сектор втулки гильзы; 5 – уплотнительное кольцо гильзы; 6 – уплотнительное кольцо корпуса; 7 – плунжер; 8 – гильза; 9 – корпус; 10 – сектор кольца плунжера; 11 – уплотнительное кольцо; 12 – сектор кольца гильзы; 13 – стопорное кольцо; 14 – днище корпуса; 15 – пробка.
Нецелесообразно ремонтировать головки цилиндров, если у них выломаны стенки гнезда под шип кронштейна надрамника или даже при наличии трещины в стенке гнезда длиной более половины длины шипа кронштейна. Корпус телескопического подъемника при наличии трещин любого характера и расположения не восстанавливают, производят лишь расточку цилиндра под ремонтный размер при больших износах или после правки вмятин на корпусе цилиндра.
Поврежденную более двух ниток резьбу под пробку восстанавливают нарезанием ее на набольшую глубину или постановкой ввертыша. Нарушенную сварку восстанавливают. Сваркой с последующей механической обработкой восстанавливают и разрушенный буртик под стопорное кольцо гильзы. Износ гильзы по внутренней рабочей поверхности устраняют растачиванием под ремонтные размеры.
Изношенную поверхность гильзы под направляющую втулку протачивают, а при сборке ставят втулку ремонтного размера. Таким же образом поступают при износе паза под стопорное кольцо. Рабочую поверхность трубы плунжера протягивают под ремонтный размер, а пазы под стопорные кольца протачивают под кольца увеличенного размера. После выполнения необходимых сварочных работ производятся уплотнение швов и гидравлические испытания в отдельности корпуса, гильзы и плунжера под давлением 3,5 МПа в течение 1 мин. Платформу и надрамник восстанавливают в основном правкой вмятин и сваркой при наличии трещин, пробоин и нарушения сварных швов. Балки со сквозной по всему профилю сечения трещиной заменяют. Если же трещина прошла только через верхнюю или нижнюю полку балки, то ее заваривают с постановкой усилительной накладки. Вмятины на бортах и листах пола платформы правят с применением нагрева до первоначальной формы. Для удобства выполнения восстановительных работ на кузовах самосвалов применяется специальный стенд (рис. 7.11).
Стенд состоит из рамы 2, изготовленной из швеллеров. На трубе 4, вращающейся в подшипниках скольжения на кронштейнах 3 вокруг своей оси, приварены два зажима. Каждый зажим состоит из кронштейна 12 и коромысла 8, соединенных между собой трубой 4 при помощи сварки. На коромысло 8 устанавливаются два прихвата 13, соединенные стяжной пружиной 5. Снятый с автомобиля кузов 14 устанавливают на зажимы стенда.
Рис. 7.11. Стенд для восстановления кузова автомобилей-самосвалов
Для этого необходимо посредством крана подать воздух через механизм подвода 6 и 7 к камерам 11. Под действием сжатого воздуха давлением 0,5…0,6 МПа через шток 10 и кронштейн 9 прихваты 13 расходятся. Это позволяет установить платформу на продольные балки основания. Переключив рукоятку крана управления, удаляют воздух из камер, и пружины 5 плотно стягивают прихваты 13, надежно удерживая платформу. В окончательно отремонтированной платформе подвеска заднего борта должна обеспечивать безотказную работу запорного устройства борта. Задний борт в закрытом состоянии должен плотно прилегать к кромкам бортов и полу платформы.
7.6.3. Порядок выполнения работы. Составить отчёт, в котором должны быть приведены способы, оборудование и материалы для восстановления:
– кабин грузового автомобиля и трактора;
– неметаллических деталей кузовов и кабин;
– замков дверей;
– петель дверейи крышки багажника;
– механизма управления дверями;
– гидравлического подъемника автомобиля-самосвала;
–кузова автомобиля самосвала.
7.7. Вопросы для самоконтроля:
1. Какие основные дефекты у кабин грузового автомобиля и трактора?
2. Какими способами восстанавливаются вмятины на цилиндрах механизма управления дверями?
3. Какие основные дефекты у замков дверей?
4. Какие основные дефекты у гидравлического подъемника автомобиля-самосвала?
5. Из каких элементов состоит стенд для восстановления кузова автомобилей-самосвалов?