Разработка технологического процесса обработки детали заканчивается оформлением комплекта документов, определяемого стандартами ЕСТД.
Состав и форма карт, входящих в комплект документов, зависят от вида технологического производства (единичное, типовое или групповое), типа производства (единичное, серийное, массовое) и степени использования средств вычислительной техники. По степени детализации различают следующие виды описания технологических процессов: маршрутное, операционное, маршрутно-операционное.
При маршрутном описании технологического процесса весь ТП излагается в маршрутной карте (МК). В МК указывается содержание операций и переходов, а также выдерживаемые размеры. Маршрутное описание применяется в единичном и мелкосерийном производстве.
При операционном описании маршрутная карта выполняет роль сводного документа, в котором указывается адресная информация (номер цеха, участка, рабочего места, операции); наименование операции; перечень документов, применяемых при выполнении операций; технологическое оборудование; трудозатраты.
|
|
Сами операции разрабатываются на операционных картах и картах эскизов (КЭ).
Операционное описание применяется в крупносерийном и массовом типах производства. В большинстве своем курсовые проекты выполняются на уровне операционного описания.
Маршрутно-операционное описание предусматривает разработку сложных операций на операционных картах и картах-эскизах, а остальная часть – только в маршрутной карте. Применяется в единичном и мелкосерийном производстве сложных деталей.
Маршрутная карта является обязательным документом любого технологического процесса. Форма и правила оформления МК определены ГОСТ 3.1118–82. В целом в курсовом проекте оформляются следующие документы: титульный лист (ТЛ), карта эскизов (КЭ), маршрутная карта (МК), карта технологического процесса (КТП), карта типового (группового) технологического процесса (КТТП), операционная карта (ОК), карта типовой (групповой) операции (КТО), карта кодирования информации (ККИ), карта наладки (КН).
Важной частью разработки технологического процесса является создание графических документов, общие требования к которым регламентированы ГОСТ 3.1104–81 ЕСТД:
1. Графические изображения следует выполнять с целью наглядной и дополнительной информации к документам.
2. Эскизы следует разрабатывать на технологические процессы, операции, переходы.
3. Эскизы следует исполнять с соблюдением масштаба или без соблюдения масштаба, но с примерным соблюдением пропорций.
4. Графические изображения следует выполнять с применением чертежного инструмента. Допускается выполнять изображения от руки.
|
|
5. Изображать изделия на эскизах необходимо в рабочем положении изделия на операции. Если эскиз изделия разработан для нескольких операций, допускается изображать изделия на эскизе в нерабочем положении.
6. Изображение изделия на эскизе должно содержать размеры, предельные отклонения, обозначение шероховатости, баз, опор, зажимов и установочно-зажимных устройств, необходимых для выполнения операций, для которых разработан эскиз.
Кроме того, при выполнении операционных эскизов необходимо соблюдать следующие требования:
1. Поверхность, обрабатываемую на данной операции, обводят линией толщиной 2 S.
2. Проставляют только те размеры, которые выполняют на данной операции.
3. Проставлять размеры надо с учетом способа получения этого размера.
4. Все размеры или конструктивные элементы обрабатываемых поверхностей нумеруются арабскими цифрами. Номер размера или конструктивного элемента обрабатываемой поверхности проставляют в окружности диаметром 6–8мм и соединяют размерной или выносной линией. При этом размеры, предельные отклонения обрабатываемой поверхности в тексте содержания операций или перехода не указывают (П.3). Допускается в тексте содержания операций или перехода номер размера или конструктивного элемента не обводить окружностью, например: «Развернуть отверстие 1», «Точить канавку 2». Нумерацию следует производить в направлении часовой стрелки.
5. Технические требования следует помещать на свободной части документа справа от изображения изделия или под ним и излагать по ГОСТ 2.316–68.
6. Таблицы и графики, поясняющие изображения изделий, следует помещать на свободной части документа справа от изображения изделия и выполнять по ГОСТ 2.105–79.
7. Если изображение изделия на эскизе относится к нескольким операциям технологического процесса, то номера этих операций следует указывать над изображением изделия и подчеркивать. Допускается не записывать все номера операций, если изображение относится к нескольким последовательным операциям. Например, изображение изделия на эскизе относится к операциям 005, 010, 015, 020, в этом случае можно записать 005 - 020.
8. Если на поле для графической информации содержится несколько отдельных эскизов для различных операций (переходов) технологического процесса, то над каждым эскизом следует указать номер операции (перехода) и подчеркнуть.
9. Эскизы обработки на наиболее сложных и оригинальных операциях могут быть показаны в графической части проекта (формат А1).
При выполнении эскизов наладок необходимо придерживаться следующих требований:
1. Выполнять эскизы наладок в графической части проекта (формат А1). На одном листе формата А1 размещают 3-4 эскиза наладок разнообразных операций (токарных, фрезерных и т.д.).
2. Заготовка показывается закрепленной в приспособлении, второстепенные подробности которого могут быть опущены (полуконструктивный вид). Необходимо изображать элементы приспособления, обеспечивающие базирование и закрепление заготовки, ориентацию и закрепление приспособления на станке. Изображение должно быть в плане.
На заготовке указывают размеры и шероховатость обрабатываемых поверхностей, обрабатываемые поверхности обводят толстой линией (толщиной 2 S). Допускается изображать только часть заготовки с обрабатываемой поверхностью, указывая ее размеры и шероховатость.
3. Указывают схему размещения инструментов и приспособлений. Приспособление для крепления инструментов указывают в полуконструктивном виде.
Режущий инструмент изображают в конце рабочего хода. Если необходимо, то штриховой линией показывают и исходное положение инструмента. Если инструмент затемняет чертеж, то его можно изображать отведенным от заготовки. При применении (последовательно) нескольких различных инструментов, например сверла, зенкера, развертки, один из них показывают в конечном положении, а остальные вычерчивают рядом в порядке выполнения переходов. Сложный инструмент не следует вычерчивать полностью, достаточно, например, показать габариты и форму фрезы, два-три зуба и способ их крепления. Винтовые канавки, например у сверл, можно показать наклонными линиями. Во всех случаях из эскиза должен быть ясен способ крепления инструмента на шпинделе, суппорте и т.п. Стрелками показывают направление движения режущего инструмента или заготовки.
|
|
При проектировании наладок для станков с ручным управлением на листе вычерчивают таблицу, на которой указывают режим резания.
Для станков с ЧПУ в графической части карт наладки кроме отмеченного выше указывают взаимное расположение нулевых точек станка и заготовки и основные размеры заготовок. На схеме размещения инструментов отмечают координаты положения вершин инструментов по осям и порядок расположения инструментов в резцовой головке.
Для станков с ЧПУ существует специальная табличная форма карт наладки инструмента по ГОСТ 3.1418–82. В эти карты вносят данные по исходной заготовке, режущему инструменту, технологической оснастке, указывают материал, род и основные размеры исходной заготовки; шифр и материал режущей части инструмента; номер корректора, закрепленного за инструментом; наименование и шифр технологической оснастки; указывают материал, род и основные размеры исходной заготовки; номер корректора, закрепленного за инструментом; наименование и шифр технологической оснастки. Для каждого установа заготовки приводят численные значения координат вершин инструментов по осям и наладочные размеры. Данные о применяемом режущем инструменте записывают в строгой последовательности вступления инструментов в работу. Кроме указанных сведений включают наименование и номер чертежа детали, модель и номер станка, номер программы.
|
|
Запись технологической и геометрической информации,
необходимой для разработки управляющей программой, а также данных, используемых для настройки станка ЧПУ, производится в специальных формах документации. Основной формой является расчетная технологическая карта (РТК), предназначенная для ручного способа подготовки программ механической обработки изделий на станках с ЧПУ.
Для наладки станка с ЧПУ в производственных условиях используют карту наладки произвольной формы, а при составлении РТК для обработки заготовок повышенной сложности, как правило, вычерчивают схему движения режущего инструмента. В карте
наладки должны содержаться все сведения, необходимые для наладки станка на конкретную операцию. По карте производится установка заготовки на станке и режущих инструментов в резцовой головке или в магазине закрепления блоков коррекции положения инструментов, устанавливается порядок смены инструментов и изменения положения заготовок. Карта наладки состоит из графической части и таблицы.
В тексте содержания технологических операций для записи технологических переходов применяют следующие ключевые слова: вальцевать, врезаться, галтовать, гравировать, довести, долбить, закруглить, заточить, затыловать, зенкеровать, навить, нарезать, обкатать, отрезать, подрезать, полировать, притирать, протянуть, развернуть, развальцевать, раскатать, рассверлить, расточить, сверлить, строгать, суперфинишировать, точить, хонинговать, шевинговать, шлифовать, цековать, центровать, фрезеровать, выверить, закрепить, настроить, переустановить; переустановить и закрепить; переустановить, выверить и закрепить; переместить,
подогнать, проверить, смазать, установить; установить и выверить; установить и закрепить; установить, выверить и закрепить.
Важным вопросом является простановка предельных отклонений на операционные размеры. По этому признаку конструктивные элементы классифицируются на три группы: валы, отверстия, элементы, не относящиеся к валам и отверстиям (рис. 9).
Для операционных размеров валов и отверстий предельные отклонения принято назначать по квалитетам односторонними – «в тело» материала (для валов – от нуля в минус, для отверстий – от нуля в плюс). Для размеров элементов, не относящихся к валам и отверстиям, назначаются симметричные предельные отклонения по классам точности как более простые для использования и измерения универсальными средствами. К этим конструктивным элементам относятся уступы, глубины отверстий, высоты выступов, расстояние между осями отверстий или плоскостями симметрии, размеры, определяющие расположение осей или плоскостей симметрии элементов (отверстий, пазов, выступов). Однако в зависимости от требований конструкции или рациональной технологии возможно и иное расположение поля допуска. Так же, как для операционных размеров, назначают неуказанные предельные отклонения конструкторских размеров. Неуказанные предельные отклонения не ставятся непосредственно после номинальных размеров, а оговариваются общей записью в технических требованиях, и правила их назначения установлены ГОСТ 25670–83,
ГОСТ 25346–89, ГОСТ 25348–82 [4,8, 11].
|
|
|
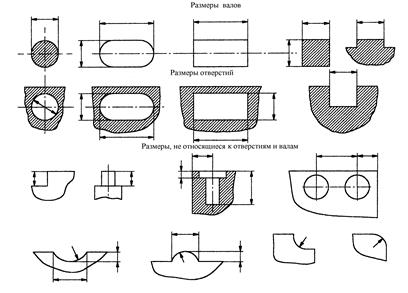
Рис. 9. Классификация конструктивных элементов деталей
Для дальнейшего изучения вопроса о простановке размеров рассмотрим отклонения и допуски расположения поверхностей (ГОСТ 24642–81). Отклонением расположения называется отклонение реального (действительного) расположения элемента (поверхности, оси или плоскости симметрии) от номинального расположения. Для оценки точности расположения поверхностей, как правило, назначают базы. База определяет привязку детали к плоскости или оси координат, относительно которой задаются допуски расположения или определяется расположение нормируемого элемента. Базой может быть поверхность (например, плоскость), ее образующая, или точка (например, вершина конуса, центр сферы). Для поверхности вращения базой является ее ось.
Допуском расположения называется предел, ограничивающий допускаемое значение отклонения расположенных поверхностей. Для плоскости, симметричности, пересечения осей и позиционного допуска допуск расположения может быть задан в радиусном и диаметральном выражениях.
Отклонения расположения поверхностей и отклонения размеров (диаметров, ширины и т.п.) элементов деталей в зависимости от условий сборки и работы изделий могут проявляться как совместно, так и независимо друг от друга. Установлены понятия о зависимых и независимых допусках расположения. Независимым
называется допуск расположения, числовое значение которого постоянно для всей совокупности деталей, изготовляемых по данному чертежу, и не зависит от действительного размера нормируемого или базового элемента. Зависимым называется допуск расположения, числовое значение которого переменно для различных деталей, изготовляемых по данному чертежу, и зависит от действительных размеров нормируемого или базового элементов.
В чертежах зависимый допуск задается своим минимальным значением, которое допускается превышать на величину, соответствующую отклонению действительного размера детали от проходного предела (наибольшего предельного размера вала или наименьшего предельного размера отверстия):
Т зав = Т min + Т доп ,
где Т min – минимальная часть допуска, указываемая в чертежах (постоянная для всех деталей); Т доп – дополнительное значение допуска, зависящее от действительных размеров рассматриваемых элементов (переменная часть допуска).
Как правило, зависимые допуски рекомендуется назначать для тех элементов деталей, к которым предъявляются только требования собираемости в соединениях с гарантированным зазором. В этих случаях допуски расположения рассчитывают исходя из гарантированного (наименьшего) зазора. Если этот зазор фактически будет увеличен (что и происходит при отклонениях действительных размеров сопрягаемых элементов от проходного предела), то становится допустимым и соответственно увеличенное отклонение расположения, разрешаемое зависимым допуском. Примеры назначения зависимых допусков расположения: допуски расположения сквозных отверстий под крепежные детали; допуски соосности ступенчатых валов и втулок, собираемых с зазором; допуски перпендикулярности осей отверстий под заглушки, стаканы,
крышки.
Зависимые допуски расположения более экономичны, ибо позволяют увеличивать действительные допуски расположения, дают возможность контролировать детали с помощью комплектных калибров расположения (при этом калибры расширяют допуск на величину Т доп.)
|
|
|
Одним из видов отклонений и допусков расположения является позиционное отклонение и позиционный допуск. В ГОСТ 10356–63, ГОСТ 2308–68 понятию позиционного отклонения соответствовал термин «смещение оси от номинального расположения».
Позиционное отклонение (смещение от номинального расположения) – наибольшее расстояние между реальным расположением элемента (его оси, центра или плоскости симметрии) и его номинальным расположением в пределах нормируемого участка. Различают позиционные допуски оси, прямой, точки, плоскости симметрии в радиусном и диаметральном выражениях. Поэтому, например, позиционный допуск оси (прямой) в пространстве – это область в пространстве, ограниченная цилиндром.
Точность расположения элементов, заданного проставленными на чертежах линейными и угловыми координирующими размерами, нормируется двумя способами:
1. Указанием предельных отклонений координирующих размеров.
2. Указанием позиционного допуска элемента (его оси, плоскости симметрии).
Нормирование позиционных отклонений предполагает, что чертежом определено, к каким элементам относится позиционный допуск и какими размерами определяется номинальное расположение, от которого отсчитывается позиционное отклонение. Такие размеры указываются на конструкторских чертежах номинальными значениями без предельных отклонений и заключаются в прямоугольные рамки.
Между обоими способами нормирования существует взаимосвязь. Позиционные допуски обеспечивают комплексное нормирование расположения элементов, так как позволяют ограничить отклонения расположения каждого из элементов, как от общей базы – номинального расположения, так и в любом из направлений. По отношению к позиционным допускам предельные отклонения координирующих размеров являются поэлементными отклонениями, ограничивающими отклонения в координатных направлениях и отдельно для каждой пары элементов, связанных соответствующим координирующим размером.
Позиционные допуски упрощают анализ взаимозаменяемости, расчет допусков и простановку их в чертежах. Они обеспечивают более широкие поля допусков расположения, чем эквивалентные им предельные отклонения координирующих размеров. Метод позиционных допусков может быть использован при любых методах изготовления и контроля, при назначении как зависимых, так и независимых допусков расположения. Но, в первую очередь, его преимущества проявляются при назначении зависимых допусков для деталей, в которых необходимо обеспечить точность взаимного расположения более чем двух элементов, объединенных общими точностными требованиями, например требованием собираемости с парной деталью одновременно по нескольким сопрягаемым элементам. Чаще всего метод позиционных допусков применяется для нормирования расположения осей отверстий под крепежные детали. Он может быть применен также для нормирования точности деления шкал, расположения рабочих элементов штампов, кондукторов и другой технологической оснастки, расположения измерительных элементов комплектных калибров и т.д.
Примеры указания зависимых допусков
Способы указания зависимых допусков проиллюстрированы следующими примерами:
Ф0,02 МА Ф0,02 А М Ф0,02 М
а б в
![]() |


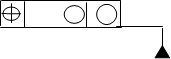
Ф0,02 М А МФ0,02 М М
г д
М означает зависимый допуск расположения и формы;
– знак позиционного отклонения;
а – зависимый допуск связан с действительными размерами рассматриваемого элемента; М стоит после числового значения допуска;
б, в – зависимый допуск связан с действительными размерами базового элемента; б – М после буквенного обозначения базы, в – М при отсутствии буквенного обозначения базы;
г, д – зависимый допуск связан с действительными размерами рассматриваемого и базового элементов.
Если допуск расположения или формы не указан как зависимый, то его считают независимым.
Рассмотрим допуски расположения осей отверстий под крепежные детали.
Соединение двух деталей с помощью крепежных элементов подразделяются на два типа: тип А и тип В. При соединении типа А (рис. 11) в соединяемых деталях (1, 2) предусмотрены сквозные отверстия под проход крепежной детали с гарантированным зазором S (болтовые, заклепочные соединения).
При соединении типа В (рис. 12) сквозные отверстия под проход крепежной детали предусмотрены только в одной из соединяемых деталей, а в другой детали имеются или резьбовые отверстия, или отверстия, обеспечивающие натяг.
Для соединения типа А определим условия собираемости, в данном случае условие прохождения болтов в отверстия. При этом к деталям предъявляют требования, полные взаимозаменяемости.
В тех случаях, когда к деталям не предъявляются требования взаимозаменяемости, их собираемость допускается обеспечивать различными способами совместной обработки в парных соединяемых деталях, например, когда сверление отверстий производится сначала в одной детали, используемой затем в качестве кондуктора для сверления отверстий в парной детали.
В этих случаях назначают предельные отклонения на размеры, координирующие оси отверстий в одной из сопрягаемых деталей, более удобной для разметки, например в детали, имеющей меньшую массу. При этом исходят из экономической точности обработки и назначают симметричные предельные отклонения по квалитетам или по классам точности.
На рис. 11, а показано номинальное расположение верхней, нижней деталей и болтов. L – координирующий размер. Анализ
необходимо вести по минимальному (гарантированному) зазору S min, ибо расчеты по S min обеспечивают взаимозаменяемость. Зазор S min имеет место при D о = D , d болта =
. Далее выбираем зазоры между каждым болтом и отверстием до тех пор, пока проходит болт (рис. 11, б). Осуществляем это за счет смещения осей отверстий верхней и нижней деталей в разные стороны. В крайнем положении оси отверстий D
смещены в радиусном выражении на D = S min / 2. Тогда для соединения типа А позиционный допуск оси отверстия в диаметральном выражении равен Т = 2D = S min.
Кроме смещения оси отверстия от номинального положения существуют и другие погрешности, влияющие на прохождение болта в отверстия:
а) отклонение от перпендикулярности оси отверстий к опорной плоскости в обеих соединяемых деталях (учитывается в тех случаях, когда при соединении деталей необходимо обеспечить плотное соприкосновение по опорным плоскостям, а отклонение от перпендикулярности не включено в позиционный допуск);
б) отклонение от соосности ступеней крепежной детали учитывается в тех случаях, когда крепежная деталь ступенчатая, например несоосность резьбовой и гладкой части стержня винтов и шпилек. Кроме того, может быть оставлена часть минимального зазора для последующей регулировки взаимного расположения деталей или для облегчения сборки, тогда Т = kS min = S p, где S p – расчетный зазор; k – коэффициент использования зазора.
|
|
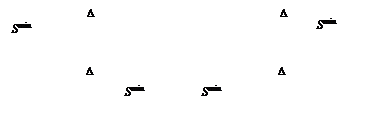
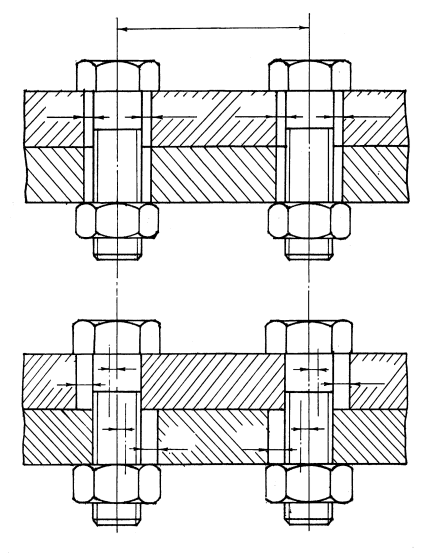
а – номинальное положение; б – предельное (крайнее) положение
|
|
|
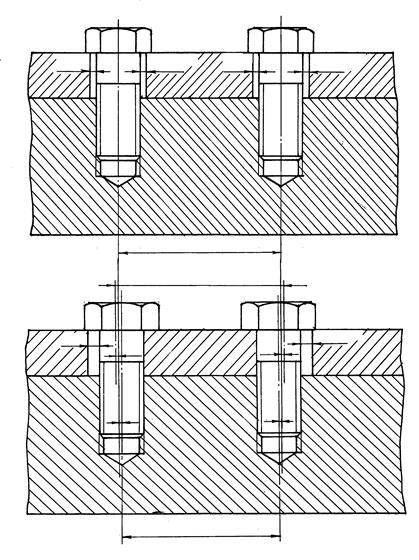
Рис. 12. Соединение типа В:
а – номинальное положение; б – предельное (крайнее) положение
Для компенсации отклонения расположения осей принимают k = 0,8 – 1,0 для соединений, не требующих регулировки взаимного расположения деталей; k = 0,6 – для соединений, в которых требуется регулировка взаимного расположения деталей при сборке.
В соединении типа В при смещении осей отверстий верхней и нижней деталей в разные стороны смещаются и винты, поэтому D = S min / 4. Тогда позиционный допуск оси отверстия в диаметральном выражении равен Т = 2D = 0,5× S min. Если учесть другие погрешности, то Т = 0,5× kS min = 0,5× S p.
Предельные отклонения координирующих размеров определяют исходя из соответствующего позиционного допуска осей отверстий. Для этого производится геометрическое разложение позиционного допуска на координатные составляющие: Тх, Тy в прямоугольных координатах (рис. 13, а) и Tr, T a в полярных координатах (рис. 13, б).
а б
Рис. 13. Геометрическое разложение геометрического допуска:
а – прямоугольные координаты; б – полярные координаты
Соотношения между координатными составляющими и позиционным допуском следующие:
;
,
здесь R, Tr, T – в мм; Т a – в мин.
За основу берется разложение, когда приняты одинаковые отклонения оси в обоих координатных направлениях, в этом случае круговое поле допуска заменяется вписанным в него квадратным полем в прямоугольной системе координат, а в системе полярных координат – приближенно квадратным полем. Тогда обе координатные составляющие позиционного допуска будут одинаковы и будет справедливо:
;
.
На этот случай в справочной литературе [4, 11] приводятся данные по переходу с позиционных допусков на предельные отклонения координирующих размеров для различного характера расположения отверстий. Рассмотрим пример. Определить допуски расположения осей четырех отверстий под болты М12-6g´60,58 ГОСТ 7798–70 (рис. 14, а).
У данного болта номинальные размеры гладкой и резьбовой частей равны, отклонения «в тело». Согласно ГОСТ 11284–75 «Диаметры сквозных отверстий под крепежные детали и соответствующие им наименьшие гарантированные зазоры» диаметр
отверстий D = 13 Н 12+0,18, тогда S min = 1 мм. Имеем соединение типа А, значит, позиционный допуск Т = S р = kS min. Берем k = 0,6 для соединений, в которых требуется регулировка взаимного
расположения деталей при сборке. Тогда Т = S p = kS min = 0,6×1 =
= 0,6 мм есть минимальное значение зависимого допуска, указываемого на чертеже. Расчетное значение Т сопоставляем с табличным [4,11]. В данном примере они равны. Позиционные допуски указываются на конструкторских документах, на которых также указываются координирующие размеры номинальными значениями в прямоугольных рамках без предельных отклонений (рис. 14, а).
М означает зависимый допуск,
– позиционное отклонение.
![]() | |||||||
![]() | |||||||
| |||||||
|

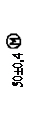

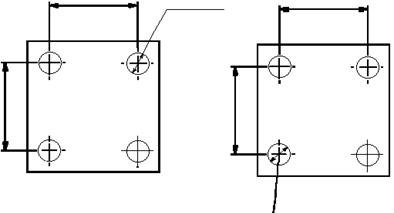
а б
Рис. 14. Расположение осей четырех отверстий под болты:
а – конструкторский документ; б – технологический документ
Предельные отклонения координирующих размеров проставляют в технической документации, т.е. на операционных эскизах. Определим эти отклонения:
.
Так как предельные отклонения координирующих размеров определяются позиционными отклонениями двух отверстий, то отклонения координирующих размеров
0,42.Табличные
0,40. Тогда координирующие размеры равны
М.
Расположение отверстий под крепежные детали по ГОСТ 2.308–79 и ГОСТ 2.397–68 разделено на одиннадцать видов. Рассмотрим и проанализируем некоторые из них.
Характеристика расположения: три и более отверстия расположены в один ряд, сборочная база отсутствует (рис. 15).
При нормировании позиционных отклонений имеем следующий эскиз (конструкторский документ):
![]() |
Рис. 15. Расположение отверстий под крепежные детали
(конструкторский документ)
Здесь координирующие размеры проставлены координатным методом (лесенкой), ибо в этом случае погрешность размера, получающегося автоматически, складывается из суммы погрешностей двух размеров. При простановке же координирующих размеров цепным методом эта сумма складывается из погрешностей всех
(n –1) размеров, где n – число отверстий. Поэтому при числе отверстий n > 3 не рекомендуется координирующие размеры задавать цепным методом (цепочкой).
При нормировании предельных отклонений координирующих размеров имеем следующий эскиз (технологический документ) (рис. 16).
|
|
|
|
|
|
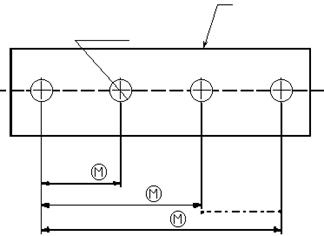
Рис. 16. Расположение отверстий под крепежные детали
(технологический документ)
Отклонение между осями двух любых отверстий не более (допуск зависимый).
Отклонение осей отверстий от плоскости А не более δ y (допуск зависимый).
При однорядном расположении отверстий и отсутствии сборочной базы наиболее эффективным способом нормирования координирующих размеров является нормирование отклонений между осями любых (смежных и несмежных) отверстий в ряду (
– максимальное отклонение). Этим обеспечиваются наибольшие технические возможности, и уменьшается доля брака. Выявим связь между расчетным позиционным отклонением Т р и отклонениями на координирующие размеры
,
. Так как нормирование идет по
, то
, тогда
Так как есть сумма отклонений двух размеров, то
, тогда
.
Характеристика расположения: три и более отверстий расположены по окружности, сборочная база отсутствует (рис. 17, 18). При нормировании позиционных отклонений имеем следующий
эскиз:
Рис. 17. Расположение отверстий под крепежные детали
(конструкторский документ)
Для данного вида расположения рассмотрим задачу следующего содержания. Определить допуски расположения четырех отверстий Ф9 Н 7 под винты М8. Для компенсации смещения осей может быть использован весь гарантированный зазор.
Гарантированный зазор S min = 1 мм. Для соединений типа В расчетный позиционный допуск в диаметральном выражении:
Т р = 0,5× k S min = 0,5×1×1 = 0,5 мм.
Т р = 0,5 мм и проставлено на конструкторском эскизе.
В полярных координатах , тогда
= 0,7× Т р= 0,7×0,5 = 0,35 мм.
Для диаметрального размера имеем Ф50 =
0,35 М отклонения от центрального угла, соответствующее T p.
.
Тогда операционный эскиз имеет следующий вид:
|
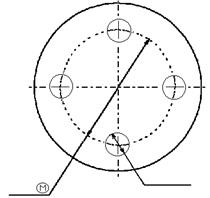
Рис. 18. Расположение отверстий под крепежные детали
(технологический документ)
В тех случаях, когда в одну группу с отверстиями под крепежные детали входит центрирующий элемент (отверстия, выступы и т.п.), для него назначают отдельный позиционный допуск Т о, который для каждой из соединяемых деталей рассчитывается по формуле
Т о = 0,5 ×К о ,
где Т о– позиционный допуск центрирующего элемента в диаметральном выражении (удвоенное предельное отклонение его оси от центра окружности центров или оси симметрии группы отверстий под крепежные детали; – наименьший предельный зазор между центрирующими элементами соединяемых деталей; К о – коэффициент использования зазора
. Допуски расположения центрирующих элементов, соединяющихся по посадке с зазором, рекомендуется назначать зависимыми. Если
= 0 (например, центрирование по скользящей посадке) или К о = 0 (гарантированный зазор является функциональным параметром и не может быть использован для компенсации позиционного отклонения центрирующего элемента), то центрирующий элемент должен быть принят в качестве базы при назначении допусков расположения осей отверстий под крепежные детали.