Процесс получения капролактама из циклогексанона включает в себя следующие стадии:
- получение аммиачной воды;
- оксимирование циклогексанона гидроксиламинсульфатом и отгонка органики из раствора сульфата аммония с последующей доупаркой раствора сульфата аммония;
- перегруппировка циклогексаноноксима и нейтрализация продуктов перегруппировки;
- экстракция капролактама трихлорэтиленом из лактамного масла и раствора сульфата аммония, реэкстракция капролактама из трихлорэтилена водой;
- регенерация трихлорэтилена;
- отгонка трихлорэтилена из водного раствора капролактама;
- ионообменная очистка водного раствора капролактама;
- выпарка капролактама из водного раствора;
- очистка сырого капролактама методом дистилляции;
- кристаллизация жидкого капролактама, расфасовка и упаковка его в мешки, погрузка жидкого капролактама в железнодорожные цистерны, выдача жидкого капролактама на производство полиамида.
4.1 Описание технологического процесса
4.1.1 Получение аммиачной воды
В процессе производства капролактама применяется аммиачная вода с концентрацией 11-17%.
11-17% аммиачная вода получается путем абсорбции газообразного аммиака конденсатом сокового пара (далее КСП).
Образование аммиачной воды сопровождается выделением тепла по реакции:
NН3 + Н2О NН4ОН + 30,3 кДж/моль
Тепло реакции снимается в холодильниках, охлаждаемых оборотной водой и в аммиачных испарителях.
К качеству аммиачной воды и, соответственно, конденсату, применяемому для ее приготовления, предъявляются жесткие требования, т.к. наличие ионов хлора в аммиачной воде ведет к усилению коррозии оборудования и коммуникаций, а следовательно к загрязнению лактамного масла продуктами коррозии.
4.1.2 Оксимирование циклогексанона гидроксиламинсульфатом.
Циклогексаноноксим (далее по тексту оксим) получают по открытой Мейером в 1882 г. реакции между гидроксиламинсульфатом (далее по тексту ГАС) и циклогексаноном (далее по тексту анон).
Процесс оксимирования проводится в реакторах с турбинными мешалками по двухступенчатой противоточной схеме при атмосферном давлении и температурах: до 570С на первой ступени и 72-850С на второй ступени.
Реакция оксимирования протекает по следующему уравнению:
![]() | ![]() | ||
+ NH2OH • 0,5 H2SO4 == + H2O + 118 кДж/моль
В кислой среде циклогексаноноксим находится в форме соединения с серной кислотой или же в протонированной форме С6Н10 = N+ОН.
Для сдвига равновесия реакции вправо в реакционную смесь вводят газообразный аммиак, что приводит к образованию оксима и побочного продукта сульфата аммония:
| |||
| |||
+
+ 2 NH3 + 0,5(NH4)2SO4
Газообразный аммиак вводится в процесс оксимирования для поддерживания заданного рН среды.
Химизм процесса можно представить в следующем виде:
![]() | ![]() |
1) С = О + Н+ С+ - ОН
Взаимодействие анона с ГАС протекает по механизму электрофильного замещения. Электрофильный характер атома углерода карбонильной группы в молекуле анона усиливается протонированием кислородного атома карбонильной группы кислотой. При этом атом углерода приобретает положительный электрический заряд.
2) Присоединение атома азота ГАС за счет неподеленной электронной пары к положительно заряженному атому углерода:
+
С+ - ОН + NH2OH C
3) Миграция атома водорода к кислородному атому карбонильной группы:
|
| ||||
+ +
С С
|
|
4) Отщепление молекулы воды:
|

С С= NHOH + H2O
|
5) Образование свободного оксима с выделением иона водорода (под воздействием газообразного аммиака):
+
C = NHOH С = NOH + H+
Лимитирующей стадией процесса оксимирования является стадия два, присоединение атома азота ГАС за счет неподеленной электронной пары к положительно заряженному атому углерода. Наивысшая скорость достигается при максимальном произведении концентраций:
![]() | |||||||||
![]() | ![]() | ||||||||
![]() | |||||||||
![]() | |||||||||
C+ – OH * NH2OH
Имеется следующая зависимость концентрации от рН:
![]() |
NH2OH
![]() |
C+ – OH
|

3 4 5 7
Оптимальной величиной для проведения реакции оксимирования является значение рН от 3,0 до 4,5. В реальных условиях процесс осуществляется при рН от 4,5 до 5,8.
Сдвиг реакции оксимирования в сторону образования оксима существенно зависит от рН среды. Установлено, что остаточное содержание циклогексанона менее 0,1% достигается при рН 4 ÷ 5,8. Кроме того, при рН больше 5,8 гидроксиламинсульфат интенсивно разлагается с выделением газообразных продуктов. Помимо потерь гидроксиламинсульфата, выделяющийся газ перемешивает реакционную массу в разделителях, что приводит к нарушению раздела фаз.
Так как реакция оксимирования протекает на границе раздела фаз, то на ее скорость весьма значительно влияет интенсивность перемешивания.
При проведении процесса оксимирования необходимо добиться полного превращения циклогексанона в оксим. Циклогексанон в оксиме в условиях последующей изомеризации в среде олеума подвергается автоконденсации с образованием непредельных соединений. Эти соединения, попадая в капролактам, ухудшают его качественные показатели, поэтому процесс оксимирования проводится в две ступени по противоточной схеме. На первой ступени создается избыток циклогексанона, на второй – избыток гидроксиламинсульфата.
На второй ступени, во избежание проскока анона в оксиме, создают избыток ГАС. На первой ступени избыточный ГАС извлекается из раствора сульфата аммония при взаимодействии с аноном.
Учитывая то, что циклогексанон в кислой среде при умеренно высоких температурах частично димеризуется в 2-циклогексилиденциклогексанон:
= О =О
2 = + H2O
реакцию на первой ступени, где имеется избыток анона, проводят при температуре от 50 °С до 57 °С. При этой температуре ограничиваются побочные реакции. При температуре менее 40 °С на 1-ой ступени возникает опасность кристаллизации смеси анон-оксима в трубопроводах и оборудовании.
Температура процесса оксимирования на второй ступени поддерживается в пределах от 72 °С до 85 °С. Нижний предел определяется температурой кристаллизации оксима; при повышении температуры выше 90 °С интенсивно протекают побочные реакции. Протекание побочных реакций на 2-ой ступени сдерживается за счет избытка ГАС, так как скорость реакции анона с ГАС значительно выше скорости реакции димеризации анона.
Примеси, содержащиеся в исходных продуктах, могут повлиять на процесс оксимирования и, как следствие, на качество готового продукта следующим образом:
- повышенное содержание циклогексанола в аноне приводит к увеличению оптической плотности чистого капролактама;
- повышенное содержание гептанона-2 в аноне приводит к увеличению содержания летучих оснований в капролактаме.
4.1.3 Отгонка анона из раствора сульфата аммония
Раствор сульфата аммония со стадии оксимирования с концентрацией 25-32% направляется в колонну поз. 1/108 для отгонки содержащегося в нем циклогексанона. Пары анона и воды после отгонки конденсируются и возвращаются на стадию оксимирования. Раствор сульфата аммония из колонны отгонки анона направляется на стадию доупарки.
4.1.4 Стадия доупарки раствора сульфата аммония
Для увеличения концентрации сульфатов до 38-42% часть раствора сульфата аммония из колонны отгонки анона направляется в колонну доупарки поз. 10362, оставшаяся часть в корпус 713 и далее в корпус 714 цеха № 25. Упаренный раствор сульфата аммония с концентрацией 38-42% подается на стадию оксимирования в узел осушки и в цех №25. Конденсат сокового пара поступает на НДФ цеха №39.
4.1.5 Перегруппировка циклогексаноноксима и нейтрализация перегруппированного продукта.
|
![]() |
Реакция идет с выделением тепла в количестве 235 кДж - в пересчете на 1 моль оксима.
Реакция перегруппировки протекает при катализе сильными минеральными кислотами (олеумом). Механизм является ионным и включает образование катиона с положительным зарядом на атоме азота и миграцию к нему алкильной группы. На заключительной стадии лактимная форма ε - капролактама переходит в лактамную.
Механизм Бекмановской перегруппировки оксима в лактам можно представить в следующем виде:
1 стадия
Образование протонированной формы оксима (ионной пары):
=NOH =NOH + _
+ H2SO4 H • HSO4
2 стадия
Дегидратация оксима в ионной паре:
=NOH + _ =N + _
|
При этом происходит образование катиона с положительным зарядом на атоме азота.
3 стадия
Миграция к атому азота близлежащего атома углерода с расширением цикла
![]() |
=N + _
• HSO4
4 стадия
Гидролиз сульфоэфира лактимной формы ε - капролактама с образованием ε- капролактама в лактимной форме и серной кислоты:
![]() |
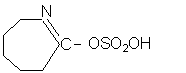
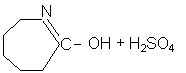
![]() |

![]() |
или
![]() |
Стадия гидролиза сульфоэфира в крепком олеуме протекает незначительно, этим и обусловлена необходимость стадии нейтрализации, где в основном проходит гидролиз сульфоэфира.
5 стадия
Переход e - капролактама из лактимной формы в лактамную (лактим-лактамная таутомерия)
![]() |
![]() |
![]() |
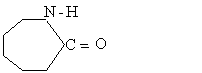
Лимитирующей стадией Бекмановской перегруппировки является разрыв связи С–С с образованием связи С–N. Ввиду незначительного гидролиза сульфоэфира в 19-24% олеуме, перегруппированный продукт состоит из следующих соединений:
В связи с этим процесс получения лактамного "масла" заканчивается обработкой перегруппированного продукта аммиачной водой на стадии нейтрализации:
|
![]() | |||
![]() |
Процесс Бекмановской перегруппировки оксима в лактам проводится в реакторах перегруппировки по двухступенчатой схеме. Перегруппировка оксима осуществляется при температуре в реакторах от 90 °С до 110 °С. Данные температуры обеспечивают наивысшую скорость целевой реакции при относительно низких скоростях побочных реакций. При более низкой температуре происходит накопление оксима вследствие понижения скорости реакции и увеличения вязкости циркулирующего перегруппированного продукта. Оксим и олеум подаются в молярном соотношении, так чтобы кислотность перегруппированного продукта составила от 59 % до 64 % на первой ступени и от 55 % до 58 % на второй ступени. При кислотности менее 55 % происходит увеличение вязкости перегруппированного продукта и как следствие этого, ухудшение теплосъема и накопление оксима в продукте, что может привести к выбросу. Кроме того, при снижении кислотности происходит неполное связывание воды в оксиме, что приводит к гидролизу оксима на анон и гидроксиламин. Выделившийся анон в свою очередь вступает в реакции поликонденсации с образованием продуктов конденсации и воды. Реакция идет как цепная и приводит к выбросу токсичных продуктов. Увеличение кислотности перегруппированного продукта более 65 % ведет к неоправданному перерасходу олеума, а также снижает эффективность процесса перегруппировки, так как SO3 в олеуме оказывает окисляющее действие на лактам.
Для стадии изомеризации циклогексаноноксима основными параметрами, влияющими на скорость реакции, выход и качество продуктов являются: соотношение оксим: олеум, температура реакции, эффективность перемешивания.
Количество подаваемого олеума зависит от содержания влаги в оксиме, а также от концентрации серного ангидрида в олеуме.
Критерием отсутствия воды в перегруппированном продукте является массовая доля свободного SО3 в перегруппированном продукте.
Все технологическое оборудование стадии изомеризации изготавливается из кислотно-упорной стали во избежании попадания в капролактам соединений железа или других металлов.
Примеси, содержащиеся в исходных продуктах, могут влиять на процесс следующим образом:
- повышенное содержание анола в аноне ведет к увеличению оптической плотности готового капролактама.
При перегруппировке анол реагирует с олеумом с образованием продуктов разложения, повышенное содержание анона в оксиме ведет к возможности сульфирования анона и вспенивания при перегруппировке.
В процессе перегруппировки могут иметь место следующие побочные реакции:
- две молекулы оксима могут давать декагидрофеназин-I и октагидрофеназин-II.
Этим побочным реакциям способствует повышенное содержание оксима в перегруппированном продукте, что является следствием снижения скорости реакции перегруппировки, происходящей при снижении температуры процесса.
Более высокая температура приводит к образованию эфира оксима:
|
|
![]() | |||
![]() | |||
+ H2SO4 + H2O
При слишком высокой температуре может образоваться нитрилгексен:
![]() | |||
![]() | |||
+ HSO4─
![]() | |||||||
![]() | |||||||
![]() | |||||||
![]() | |||||||
+ H2O + H+
| |||||
![]() | ![]() | ||||
+ OH-
Температура более 140 °С может привести к неконтролируемой реакции с выбросом продукта. Свободная вода в перегруппированном продукте приводит к гидролизу оксима на анон и гидроксиламин:
|

|

+ H2O + NH2OH
Выделившийся анон вступает в реакцию поликонденсации с образованием воды:
![]() |
|

Реакция идет как цепная.
Процесс нейтрализации перегруппированного продукта проводится при температуре в реакторах нейтрализации от 40 °С до 50 °С. При более высокой температуре происходит гидролиз лактама в ε - аминокапроновую кислоту, что снижает выход полезного продукта, а также нарушается технологический режим стадии экстрагирования:
![]() | |||
![]() | |||
+ Н2О Н2N – (СН2)5 С ε – аминокапроновая
|
кислота
При более низкой температуре возникает опасность кристаллизации сульфата аммония в циркуляционных холодильниках нейтрализации. рН процесса нейтрализации поддерживается в пределах от 5,5 до 6,5. Отклонение может привести к неудовлетворительному разделению фаз в разделительных емкостях поз. 1/331-4, в результате чего в лактамном «масле» окажется значительное количество сульфата аммония, который, пройдя через стадию экстрагирования, попадет на стадию дистилляции, где явится инициатором полимеризации капролактама. По этой же причине необходимо строго выдерживать массовую долю раствора сульфата аммония после разделительных емкостей поз. 1/331-4, от 38 до 42%. При более высокой массовой доле сульфата аммония возможна его кристаллизация.
4.1.6 Экстракция капролактама трихлорэтиленом
Проектом предусмотрена раздельная экстракция капролактама из лактамного масла и капролактама из раствора сульфата аммония. Стадия экстракции выполнена в две ступени: первая ступень – экстракция капролактама трихлорэтиленом; вторая ступень – реэкстракция капролактама водой.
В качестве экстрагента применяется трихлорэтилен, т.к. он по сравнению с бензолом и толуолом менее взрывопожароопасен, кроме того трихлорэтилен имеет большую плотность, что обеспечивает применение меньшей по объему экстракционной аппаратуры и улучшает разделяемость водного и органического слоя, особенно при реэкстракции водой.
Раздельная экстракция капролактама из лактамного масла и капролактама из раствора сульфата аммония применена с целью сведения к минимуму вероятности попадания в экстракт сульфата аммония и водо-растворимых смол.
4.1.7 Отгонка трихлорэтилена из водного раствора капролактама
Водный раствор капролактама после стадии экстракции содержит остатки трихлорэтилена.
На стадии ионообменной очистки трихлорэтилен не выводится, попадание его на следующую стадию очистки лактама отрицательно сказывается на качестве конечного продукта.
Вследствие этого, для удаления трихлорэтилена из водного раствора капролактама, предусмотрена стадия отгонки трихлорэтилена из водного раствора капролактама.
Отгонка производится в колонне насадочного типа, заполненной кольцами Рашига при температуре куба не более 110 0С и давления верха не более 0,015 МПа.
Азеотропная отгонка трихлорэтилена с водой проводится под атмосферным давлением.
4.1.8 Регенерация трихлорэтилена
Качество капролактама в большой степени зависит от чистоты трихлорэтилена, применяемого для экстракции, поэтому загрязненный примесями (продукты осмоления, сульфат аммония, циклогексанон и др.) циркулирующий трихлорэтилен постоянно выводится из системы и подвергается регенерации по двухступенчатой схеме. На первой ступени регенерацию трихлорэтилена проводят его отгонкой в колонне поз. 1026. Дистиллят колонны направляется в сборник чистого трихлорэтилена поз. 2/71, куб – на следующую ступень регенерации. На второй ступени в колоннах поз. 2/521,2 и 2/46 отгонку трихлорэтилена проводят с водой с целью исключения забивки трубного пучка выносного подогревателя продуктами осмоления. В связи с наличием большого количества примесей дистиллят 2-й ступени стадии регенерации направляется в сборник циркулирующего трихлорэтилена поз. 2/611,2 для его повторной регенерации. Кубовый продукт направляется на сжигание в сборник поз. 2/07 и далее в 2/70.
4.1.9 Ионообменная очистка водного раствора капролактама
После очистки методом экстракции, водный раствор лактама проходит очистку с использованием ионообменных смол. Сначала раствор лактам-воды очищают катионообменной смолой для удаления катионов (например NH4+, NR+). Процесс в общем виде можно представить уравнением:
Ро1-SO3-H + NH4+ → Ро1-SO3-NH4 + H+
Затем раствор очищают на анионите, где удаляют анионы (например, НSО3-, НСОО-, SO32-, SO42-) и происходит адсорбция органических примесей. Процесс в общем виде можно представить уравнением:
2 Ро1-NR-OH + SO42- → (Ро1-NR)2 SO4 + 2 OH-
Ионы ОН- поступают в раствор.
Ионы Н+ поступают в раствор, взаимодействуют с ионами ОН- с получением воды:
ОН- +Н+ → Н2О
После этого водный раствор снова проходит через катионит для удаления оставшихся катионов и органических примесей и далее через анионит для удаления оставшихся анионов.
Для вытеснения примесей, адсорбированных на смолах, проводят процесс их регенерации. Смолы переводят в солевую форму обработкой 5% раствором азотной кислоты или 4 % раствор едкого натра.
В фильтры, заполненные анионитом, подают 5 % раствор азотной кислоты:
Ро1-NR-OH + HNO3 → Ро1-NR-NO3 + H2O
В фильтры, заполненные катионитом, подают 4 % раствор едкого натра:
Ро1-SO3-H + NaOH → Ро1-SO3-Na + H2O
Избыток кислоты и щелочи удаляют обессоленной водой и проводят активацию смол.
В фильтры, заполненные анионитом, подают раствор едкого натра:
Ро1-NR-NO3 + NaOH → Ро1-NR-OH + NaNO3
В фильтры, заполненные катионитом, подают раствор азотной кислоты:
Ро1-SO3-Na + HNO3 → Ро1-SO3-H + NaNO3
Затем проводят отмывку фильтров обессоленной водой.
Лактам вода поступает в фильтры стадии ионообменной очистки при температуре не более 40 °C, т.к.температура более 50 °С вызывает разрушение термолабильных ионообменных смол.
При контакте с азотной кислотой с концентрацией выше 7% или при повышении температуры азотной кислоты выше 50 °С анионит способен бурно разлагаться.
4.1.10 Выпарка водного раствора
После экстракции капролактама водой, получается водный раствор с концентрацией от 22 до 32% капролактама. Выпаривание воды осуществляется в выпарных аппаратах в три ступени: на первой ступени раствор упаривается до концентрации капролактама 50÷60%; на второй – до 70%; на третьей – до 95%.
Во избежание образования побочных продуктов температуру выпаривания на 2 и 3 ступени понижают за счет создания вакуума.
При работе стадии выпаривания необходимо поддерживать заданный температурный режим. Неудовлетворительная работа стадии выпаривания приводит к образованию олигомерных соединений и снижает технико-экономические показатели процесса, затрудняет проведение очистки лактама на последующей стадии дистилляции.
4.1.11 Очистка сырого капролактама методом дистилляции
Капролактам относится к числу термически нестойких продуктов. При повышенных температурах капролактам взаимодействует с кислородом воздуха, образуя гидроперекисные соединения, которые под влиянием ионов железа или кобальта превращаются в адипанид, который при взаимодействии со щелочью превращается в адипат натрия с выделением аммиака. В связи с тем, что капролактам является термически нестойким продуктом, в процессе его перегонки необходимо обеспечить минимально возможное термическое воздействие.
Возможность протекания таких реакций диктует жесткие условия для хранения и переработки капролактама. Соприкосновение его расплава с воздухом недопустимо.
С целью снижения температуры и времени пребывания капролактама при высоких температурах дистилляцию и ректификацию проводят под глубоким вакуумом в роторно-пленочных, тепло- и массообменных аппаратах. Эти аппараты обладают низким гидравлическим сопротивлением, время пребывания в них перерабатываемого продукта составляет несколько секунд.
В связи с тем, что при нагревании капролактама образуется ε -аминокапроновая кислота, перед дистилляцией капролактама в него добавляется натриевая щелочь для связывания кислоты в нелетучую соль:
4.1.12 Кристаллизация жидкого капролактама
Сущность процесса заключается в кристаллизации расплавленного капролактама на поверхности вращающегося, охлаждаемого водой, барабана. Кристаллизующийся на поверхности барабана капролактам срезается ножами и фасуется в мешки.
Поскольку идет застывание расплава лактама (отсутствует маточный расплав), то все примеси из расплава капролактама переходят в кристаллический продукт. В процессе кристаллизации может происходить окисление капролактама, а также десорбция легколетучих примесей с поверхности кристаллического продукта. Все это приводит к различию в качества расплава капролактама и качества получаемого из него кристаллического продукта.
4.2 Описание технологической схемы
4.2.1 Получение 11-17 % аммиачной воды (схема № 1)
Стадия расположена в корпусе 709 блок «В».
11¸17 % аммиачная вода получается путем абсорбции газообразного аммиака конденсатом сокового пара.
Газообразный аммиак с температурой не более 40 оС и давлением 0,125-0,2 МПа (1,25-2,0 кгс/см2) поступает на приготовление 11¸17 % аммиачной воды из коллектора общезаводской сети в струйные смесители поз.1/501,2,3. Технологическая обвязка смесителей поз.1/501,2,3 позволяет эксплуатацию каждого аппарата отдельно или в паре.
Газообразный аммиак подается в цех от общезаводской сети через диафрагму FIR-101. Возможна подача газообразного аммиака из испарителя поз. 1/51, через диафрагму FIR-103.
Поступающий газообразный аммиак в смесителях поз.1/501,2,3 смешивается с циркулирующей по замкнутому циклу слабо концентрированной аммиачной водой, подаваемой насосом поз.1/551,2 из емкости поз.1/54. В результате экзотермической реакции абсорбции в смесителях поз.1/501,2,3 образуется 11¸17 % аммиачная вода с выделением большого количества тепла.
11¸17 % аммиачная вода, поступает в холодильник поз.1/85, где охлаждается оборотной водой и далее, с температурой не более 60ºC в трубное пространство испарителя жидкого аммиака поз.1/51.
Охлаждение аммиачной воды в испарителе поз. 1/51 происходит за счет испарения жидкого аммиака в межтрубном пространстве. Уровень жидкого аммиака не более 60% поддерживается автоматически клапаном LIRCAh-502, через который аммиак поступает в испаритель. Концентрация аммиачной воды на выходе из испарителя поз.1/51 замеряется плотномером QIRC-402 и регулируется путем изменения количества газообразного аммиака, подаваемого в струйные смесители поз.1/501,2,3 клапаном поз. 6031,2.
После испарителя аммиачная вода с температурой не более 55 оС сливается в сборник поз.1/53. Откуда часть аммиачной воды самотеком поступает в сборники поз.1/561 или 1/562, а другая часть – по переливу - в сборник поз.1/54. Уровень в сборнике поз.1/54 LIRCAhl-501 поддерживается автоматически регулирующим клапаном, путем изменения выдачи аммиачной воды в сборник поз.1/561. В сборник 1/54 предусмотрена подача КСП от насоса поз. 1/031,2, расход регулируется клапаном через диафрагму FIRC-102.
Так же в емкость поз.1/54 предусмотрена подача конденсата сокового пара с небольшим содержанием лактама из сборника поз. 2/43 и обессоленная вода после промывки ионообменных фильтров из сборника поз.1118.
Содержащие аммиак сдувки из сборников поз.1/53, 1/54, 1/561,2 поступают в смесительную трубу скруббера поз.1/861. Скруббер поз.1/861 представляет собой вертикальный цилиндрический аппарат, внутри которого имеется центральная труба со смесителем. Сюда же подается охлажденный до 35оС конденсат сокового пара после аммиачного испарителя поз.1/52. Уровень жидкого аммиака в межтрубном пространстве испарителя не более 60% поддерживается автоматически регулирующим клапаном LIRCAhl-503, через который аммиак поступает в испаритель. Количество конденсата сокового пара, поступающего на орошение, регулируется узлом автоматического регулирования FIRC-130, состоящего из ротаметра и клапана. Предусмотрена подача конденсата сокового пара на орошение скруббера поз.1/861 от насосов поз.1/031,3.
Из смесителя конденсат и сдувки по центральной трубе поступают в нижнюю часть скруббера поз.1/861, проходят через уровень слабо концентрированной аммиачной воды, где завершается абсорбция аммиака и сливаются в сборник 1/54. Сдувки из скруббера поз. 1/861 отводятся в скруббер поз. 1/862 и далее в атмосферу.
Газообразный аммиак после аммиачных испарителей 1/51, 1/52 возвращается в корпус 711 цеха № 25, также возможна подача в смеситель поз. 1/501 через диафрагму поз. FIR-103.
Из сборника поз.1/561,2 аммиачная вода с концентрацией 11-17% подается насосом поз.1/591,2,3 на нейтрализацию перегруппированного продукта в напорный бак поз. 1/81, в корп. 911 цеха № 35 для приготовления 25%-ной аммиачной воды, на всас насосов поз.1035 стадии регенерации трихлорэтилена. Подачу аммиачной воды на стадию нейтрализации можно осуществлять насосами поз.1/581,2, используя перемычки на всасе и нагнетании между насосами.
4.2.2 Оксимирование циклогексанона гидроксиламинсульфатом(схема № 2)
Стадия расположена в корпусе 709 «В».
Стадия оксимирования работает в две ступени. На первой ступени реакция протекает при избытке циклогексанона в реакторе поз.1/112, объемом 10 м3 при температуре не более 57 оС. На второй ступени процесс протекает при избытке гидроксиламинсульфата в реакторе поз.1/122 объемом 16 м3 при температуре 72÷85 оС.
Циклогексанон из корп.708 цеха № 22 с температурой не более 45 оС через вихревой расходомер поз. FIR-1061 поступает в экстрактор поз.1/1032, где он экстрагирует циклогексанон и циклогексаноноксим, поступающий от поз. 1/412 и 1/110, либо на всас насоса поз.1/1211,2 стадии оксимирования через клапан FIRC-1151. После экстрактора поз. 1/1032, циклогексанон самотеком поступает в разделительную емкость поз. 1/1041, где отделяется от сульфата аммония и затем подается в сборник поз. 1/1042.
Из сборника поз. 1/1042 насосом поз.1/021,2, через узел автоматического регулирования FIRC-1152, циклогексанон подается на первую ступень оксимирования в смесительное сопло 1/382. Сюда же из сборника поз.1/362 насосом поз.1/372,4 поступает раствор сульфата аммония, содержащий непрореагированный на 2-ой ступени оксимирования гидроксиламинсульфат (ГАС). Уровень в сборнике поз.1/362 LIRCAhl-5092 регулируется автоматически, изменением подачи раствора слабого ГАС в смесительное сопло поз.1/382. В смесительном сопле гидроксиламинсульфат реагирует с циклогексаноном, после чего реакционная смесь поступает на всас насосов поз. 1/1211,2 и далее через смеситель поступает в сопло 1/452.
В сопле поз.1/452 производится нейтрализация серной кислоты, выделяющейся в результате реакции в смесительном сопле поз.1/382, газообразным аммиаком, поступающим по трубопроводу от коллектора аммиака цеха № 35, через вихревой расходомер FIR-009, либо с заводского коллектора со склада аммиака №2.
Газообразный аммиак подается в зависимости от рН реакционной смеси, поддерживаемого в пределах 4,5÷5,8, на 1-ой ступени регулируется с помощью узла автоматического регулирования рНRC-4132. И контролируется при помощи рНIR-4142, расположенным на линии выхода реакционной смеси из реактора поз. 1/112 в разделительную емкость поз. 1/412. Расход газообразного аммиака замеряется вихревым расходомером поз. FIRС-1442.
Реакционная смесь после сопла поз.1/452 охлаждается в холодильниках поз.1/391,2 оборотной водой до температуры не более 57 оС. Далее по двум вводам поступает в верхнюю (с 1/391) и нижнюю (с 1/392) часть реактора оксимирования поз.1/112, где при интенсивном перемешивании остаточный гидроксиламинсульфат реагирует с циклогексаноном. Температура в реакторе поз.1/112 контролируется прибором TIR-14-7.
Для снятия тепла и дополнительного перемешивания предусмотрен и включен в схему циркуляционный контур: реактор поз.1/112® насос поз. 1/1211,2® холодильник поз. 1/391,2® реактор поз.1/112.
Продукты реакции по переливному трубопроводу с реактора поз.1/112 поступают в разделительную емкость поз.1/412, где за счет разности удельных весов смесь разделяется на два слоя: верхний слой (органический), состоящий из циклогексанона и растворенного в нем циклогексаноноксима, и нижний слой (неорганический) – раствор сульфата аммония, содержащий до 0,2 % циклогексанона. Уровень раздела фаз в разделителе поз.1/412 регулируется с помощью воронки, установленной на линии отбора нижнего слоя.
Процесс оксимирования 2-ой ступени в реакторе поз.1/122 протекает при температуре 72÷85 оС, интенсивном перемешивании, атмосферном давлении и рН в пределах 4,5¸5,8.
Для более полного, равномерного протекания реакции и достаточного охлаждения реакционной массы используется циркуляционный контур:
реактор поз. 1/122® насос поз. 1/1181-3® холодильник поз.1/1201,2® реактор поз.1/12 2.
Верхний слой (циклогексаноксим, содержащий до 50÷85 % масс. циклогексанона) из разделительной емкости поз. 1/412 самотеком через смотровой фонарь и ротаметр поз. FIR-1082, поступает на всас насоса поз. 1/1181-3 циркуляционного контура 2-ой ступени оксимирования. В эту же линию подается гидроксиламинсульфат с концентрацией не менее 275 г/л, который поступает из цеха № 38 корп. 912. Расход гидроксиламинсульфата регулируется автоматически с помощью клапана FIRCAl-1172.
Необходимая температура реакционной смеси поддерживается узлом автоматического регулирования TIRC-131,2 подачей оборотной воды в теплообменники поз.1/1201,2.
Образующаяся в результате реакции серная кислота нейтрализуется газообразным аммиаком, подаваемым в смесительное сопло поз. 1/40 на линии циркуляции перед теплообменниками поз. 1/1201,2, расход которого (FIR-62) регулируется автоматически pHRC-4102 в зависимости от рН среды на выходе из теплообменника поз. 1/1201,2 в реактор поз.1/122.
Для разогрева реакционной массы при пуске или охлаждения во время работы, реактор поз.1/122 снабжен змеевиком, в который подается пар 5 кгс/см2 или оборотная вода.
Реакционная смесь с реактора поз.1/122 самотеком поступает в нижнюю часть реактора поз.1/132, где при температуре 72÷85 оС, атмосферном давлении и интенсивном перемешивании оставшийся циклогексанон взаимодействует с гидроксиламинсульфатом. Продукты реакции из реактора поз.1/132 по переливу самотеком поступают в разделительную емкость поз.1/142, в которой циклогексаноноксим отделяется от раствора сульфата аммония за счет разности удельных весов.
Нижний слой с разделителя поз.1/142 - раствор сульфата аммония и непрореагировавший гидроксиламинсульфат направляется в сборник поз.1/362.
Верхний слой с разделителя поз.1/142 - циклогексаноноксим, содержащий до 0,2 % циклогексанона и не более 5 % воды, самотеком поступает в разделитель поз. 1/1142.
В разделитель поз. 1/1142 подается СА со стадии доупарки, для предварительной осушки циклогексаноноксима. Нижний слой с разделителя поз.1/142 - раствор сульфата аммония направляется в сборник поз.1/362.
Верхний слой с разделителя поз.1/1142 - циклогексаноноксим, поступает в сборник поз.1/172, откуда насосом поз.1/182,4 подается в смеситель вихревого типа поз. 1/20. Сюда же подается раствор сульфата аммония с концентрацией 38-42% с установки доупарки цеха № 24, охлажденный оборотной водой до температуры 72÷85ºC в теплообменнике поз. 1/06. Расход раствора СА регулируется автоматически прибором FIRC-51, клапан которого установлен на этой линии.
Для поддержания рН реакции, в трубопровод раствора сульфата аммония со стадии доупарки подают газообразный аммиак через узел автоматического регулирования рНRIC 420. Также предусмотрена подача ГАС, через вихревой расходомер FIR-13-3, для взаимодействия непрореагированного циклогексанона в циклогексаноноксиме. ГАС и газообразный аммиак, подаются в линию сульфата аммония до теплообменника поз. 1/06.
Смесь циклогексаноноксима и раствора сульфата аммония из смесителя поз. 1/20 поступает в разделительный сосуд поз.1/141. Нижний слой с разделителя поз.1/141 – раствор сульфата аммония с концентрацией не более 40,5 % - направляется в сборник поз.1/361 и насосами поз.1/371,3 в реактор поз. 1/122 или по перемычке в сборник поз.1/362.
Верхний слой –циклогексаноноксим с массовой долей влаги не более 4,5 % - через переливную воронку, самотеком, поступает в емкость поз.1/171, а затем насосами поз.1/181,3 подается через фильтры механической очистки поз. 1/191,2(один в работе, второй резервный), расположенные в корп.709 блок «В» на отметке 6.00м, на стадию двухступенчатой перегруппировки, в реакторы поз.1/212,4
Фильтры предназначены для очистки циклогексаноноксима от механических примесей. Внутри фильтров установлена сетка специального назначения типа ССН 38,5-01 из стали марки 10Х17Н13М2Т которая и является фильтрующим элементом. При снижении расхода циклогексаноноксима на стадию перегруппировки необходимо перейти на резервный фильтр и произвести промывку ранее работающего фильтра.
Перед разборкой выведенного в резерв фильтра необходимо промыть его чистым паровым конденсатом, со сливом из него промывных вод содержащих циклогексаноноксим в сборник поз. 1/151. Фильтры поз.1/191,2 и трубопроводы обогреваются горячей 90оС водой, подаваемой в рубашки обогрева от действующих гребенок корп.709 блока «В» отм 6.00м.
Через нижний дренажный вентиль емкости поз. 1/171 предусмотрена возможность выводить накопившуюся в течение 8-10 часов воду. Обогрев всаса и нагнетания насосов осуществляется 90оС водой, поступающей из корпуса 709 блока «А» для исключения осмоления циклогексаноноксима в трубопроводах и арматуре.
Раствор сульфата аммония (нижний слой), с концентрацией 25-32 %, из разделителя поз.1/412 через буферные емкости самотеком поступает в экстрактор поз.1/1032. Экстракция циклогексаноноксима из раствора сульфата аммония осуществляется в экстракторе поз. 1/1032 путем подачи в него чистого циклогексанона. Далее смесь направляется в разделитель поз.1/1041.
Из разделителя поз.1/1041 раствор сульфата аммония (нижний слой) через регулирующий клапан по уровню LIRCAl-6.1 поступает в сборник поз.1/105, откуда насосом поз. 1/1061,3 по двум вводам подается в колонну отгонки циклогексанона поз.1/108. Уровень в сборнике поз.1/105 LIRCAhl-7 регулируется клапаном, установленным на этой линии.
Отгонка циклогексанона осуществляется в колонне поз.1/108 с 30-ю клапанными тарелками. Раствор сульфата аммония предварительно подогревается до 90 оС в трубном пространстве теплообменника поз.1/1071,2 за счет тепла охлаждаемого сульфата аммония, выводимого из куба колонны, и подается на питание в колонну поз.1/108. Температура в кубе колонны поз.1/108 (не более 120 оС) регулируется клапаном TIRC-7, установленном на линии пара 0,5 МПа (5 кгс/см2) в испаритель поз.1/109. Температура верха колонны не более 107 оС. Давление верха колонны 0,01-0,06 МПа (0,1-0,6 кгс/см2) контролируется прибором РIR-5. Конденсат поступает в сборник поз. 1/124, откуда направляется в сборник поз.1/65 и далее в корпус 722 цеха № 25.
25÷32 % раствор сульфата аммония из куба колонны поз.1/108 проходит через межтрубное пространство теплообменника поз.1/1071,2 и насосом поз.1/1062,3 подается в колонну 10362 на стадию доупарки сульфата аммония. Уровень в кубе колонны поз.1/108 LIRСAhl-4 регулируется клапаном, установленным на линии нагнетания насосов поз.1/1062,3.
Пары циклогексанона и воды с верха колонны поз.1/108 в азеотропном состоянии конденсируются в теплообменнике поз.1/110 за счет охлаждения оборотной водой и самотеком поступают в экстрактор 1/1032, где смешиваются со свежим циклогексаноном и раствором сульфата аммония из разделительной емкости поз. 1/412, и далее в разделитель поз. 1/1041. Верхний слой – органический - отводится в сборник поз. 1/1042 и насосом поз. 1/021,2 подается в смесительное сопло поз. 1/382. Несконденсированные пары циклогексанона из теплообменника поз.1/110 поступают в теплообменник поз.1/111, где охлаждаются оборотной водой, проходят через гидрозатвор поз.1/125, в котором абсорбируются раствором сульфата аммония, подаваемого насосом поз.1/1061,3, и далее направляются в экстрактор поз.1/1032.
Опорожнение реакторов поз.1/112, 1/122, 1/132 и разделительных емкостей поз.1/141,2, 1/1142,1/412 осуществляется в дренажные емкости поз.1/151,2, уровень в которых контролируется при помощи прибора LIRAh-507. Откачка скопившихся продуктов производится насосами поз.1/161,2 через смотровой фонарь в реактор 1/122 стадии оксимирования.
Дренажи с экстрактора поз.1/1032, с емкостей поз.1/1041,2, насосов поз.1/021,2 направляются в дренажную емкость поз.1/93, откуда насосом поз.1/833 откачиваются в сборник сульфата аммония поз.1/105.
Сбор стоков с полов стадии оксимирования, содержащих сульфат аммония и ГАС, циклогексанон, осуществляется в сборник поз. 1/921 и насосом поз.1/833 откачивается в экстрактор 1/1032 или сборник 2/70.
На стадии оксимирования смонтирована система воздушек которая разделена на две лини «анонную» (с поз. 1/112, 1/412 и буферных емкостей) и «оксимную» (с поз. 1/151,2, 1/122, 1/132, 1/141,2, 1/171,2, 1/361,2).
4.2.3 Перегруппировка и нейтрализация(схема № 3)
Стадия перегруппировки-нейтрализации расположена в корпусе 709 «В».
Стадия перегруппировки работает в две ступени. На первой ступени реакция протекает в реакторе поз.1/214, объемом 5 м3 при температуре 80-110 оС. На второй ступени процесс протекает в реакторе поз.1/212 объемом 6,3 м3 при температуре 90-110 оС.
На первую ступень подается 85 % циклогексаноноксима от общего количества подаваемого на стадию перегруппировки. Циклогексаноноксим подается насосами поз. 1/181,3 в смесительные сопла поз. 1/981,2, установленные на линии циркуляции перегруппированного продукта. Имеющаяся перемычка на оксимной гребенке от насосов поз.1/181,3 и 1/182,4 позволяет использовать, при необходимости, подачу циклогексаноноксима на стадию перегруппировки насосами поз. 1/182,4. Расход циклогексаноноксима в смесительные сопла поз.1/981,2 регулируется автоматически FIRCShAh-2/1,2 по заданию.
Олеум из цеха № 23 корпус 926, через фильтры поз. 1/2011,2, поступает в сборник поз. 1/251,2, откуда насосом поз. 1/261,2 направляется в напорный бак поз. 1/08.
Фильтры поз. 1/2011,2 представляют собой вертикальный цилиндрический аппарат объемом 0,058м3, внутри в несколько слоев обмотан сеткой с просечкой 2,0 х 1,2 мм из нержавеющей стали.
Расход олеума поз. FIRC-122 регистрируется, регулируется на ЦПУ. Уровень в сборнике поз. 1/251,2 регулируется клапаном поз. LIRCShAhl-5152, установленным на линии подачи олеума в сборник. Из напорного бака поз. 1/08 олеум самотеком поступает в смесительные сопла поз.1/881,2, установленные на линии всаса насосов поз.1/226,8,9. Расход олеума регулируется автоматически прибором FIRCS1A1–4/1,2 по соотношению к качественному показателю кислотности, которая должна составлять в зависимости от нагрузки: на 1-ой ступени 59÷64 %; на 2-ой ступени – 55÷58 %.
Для снятия тепла реакции и обеспечения интенсивного перемешивания, реакционная смесь циркулирует при помощи насосов поз.1/226,8,9 по двум циркуляционным контурам через реактор поз.1/214, смесительные сопла поз.1/882,4 и холодильники поз.1/234,5. Расход циркулирующего перегруппированного продукта на 1-ой ступени перегруппировки измеряется прибором FIR-5/1;5/2.
В холодильниках поз.1/234,5 реакционная смесь охлаждается оборотной водой. Температура реакционной смеси на выходе из теплообменников поз.1/234,5 регулируется автоматически регуляторами температуры TIRCShlAhl–3/1 и TIRCShlAhl–3/2, за счет изменения количества подаваемой воды в холодильники поз.1/234,5.
При повышении (понижении) температуры перегруппированного продукта после теплообменников поз.1/234,5 до 120 оС (75 оС) предусмотрена блокировка по прекращению подачи оксима.
Перегруппированный продукт самотеком поступает из реактора 1-ой ступени поз. 1/214 в линию циркуляции реактора 2-ой ступени поз.1/212. На вторую ступень подаются в смесительное сопло поз. 1/983 остальные 15 % от общего количества оксима, поступающего на стадию. Расход регулируется с помощью клапана FIRCShAh-2/3.
Для снятия тепла на второй ступени перегруппировки и интенсивного перемешивания, реакционная смесь циркулирует с помощью насоса поз. 1/222,4 через холодильник поз.1/232. В холодильнике поз.1/232 реакционная смесь охлаждается оборотной водой. Температура реакционной смеси регулируется автоматически регулятором температуры TIRCShlAhl – 4 за счет изменения подачи охлаждающей воды в теплообменник поз.1/232.
Кислотность на второй ступени в зависимости от нагрузки поддерживается в пределах 55÷58 %. Перегруппированный продукт после реактора второй ступени самотеком сливается в сборник поз. 1/28, откуда насосом поз.1/292,4 направляется на стадию нейтрализации.
Схемой предусмотрено:
- для опорожнения реакторов поз.1/212,4 (в период подготовки реакторов к ремонту ) слив осуществляется в сборник поз. 1/27, откуда насосами поз.1/291,3 перегруппированный продукт откачивается в реакторы нейтрализации поз.1/301÷3;
- подача перегруппированного продукта из сборника поз.1/28 насосом поз.1/292,4 в реактор поз.1/212,4 для заполнения (в период пуска);
- по перемычке имеется возможность включения насоса поз. 1/226 на циркуляцию второй ступени, вместо насосов поз. 1/222,4.
Для исключения полной остановки 2-х ступенчатой перегруппировки и сохранения выработки при возникших неполадках на 2-й ступени предусмотрен трубопровод подачи реакционной смеси с реактора I ступени поз.1/214 в сборник поз.1/28, минуя реактор II ступени поз.1/212.
Азот, использующийся для сухого уплотнения насосов поз.1/226,8,9, поступает в корпус 709 из цеха №10 с давлением до 3,4 МПа (34 кгс/см2). Далее азот редуцируется до 0,8 МПа (8 кгс/см2), с помощью двух редукторов высокого давления типа РДФ-7 (с 30 кгс/см2 до 15 кгс/см2) и двух средних типа РДФ-6 (с 15 кгс/см2 до 8 кгс/см2) и подается на распределительное устройство сухих торцевых уплотнений, снабженное расходным устройством и узлом регулирования. Давление азота на торцах должно быть выше рабочего на 2 кгс/см2, автоматическая остановка насосов поз.1/226,8,9 происходит при снижении давления азота на торцы до 2,4 кгс/см2 (PISlАl-223).
Для предотвращения возникновения различных опасностей в процессе перегруппировки, предусмотрены блокировки, вызывающие остановку насосов подачи циклогексаноноксима поз.1/182,4 при:
1 повышении температуры после теплообменников поз.1/234,5,2 до 120 оС и понижение до 75 оС;
2 снижении расхода олеума на каждый контур 1-ой ступени до 0,98 м3/ч;
3 повышении расхода циклогексаноноксима на установку стадии до 17,5 м3/ч;
4 повышении расхода циклогексаноноксима в реактор 1-ой ступени на каждый контур поз.1/214 до 7,5 м3/ч;
5 повышении расхода циклогексаноноксима в реактор 2-ой ступени поз.1/212 до 2,5 м3/ч;
6 понижении давления в линиях нагнетания циркуляционных насосов поз.1/226,8,9 до 2,2 кгс/см2;
7 остановке циркуляционных насосов поз.1/226,8,9.
При пусковых операциях все блокировки снимаются на время пуска.
Нейтрализация перегруппированного продукта производится аммиачной водой в реакторах нейтрализации поз.1/301&divid