1 Загальні відомості про електрофізико-хімічні методи обробки.
2 Загальна характеристика основних методів.
3 Види електроерозійних методів обробки.
А) Електроіскрова обробка.
Б) Електроімпульсна обробка.
В) Електроконтактно – дугова обробка.
Г) Анодно-механічна обробка.
1 Електрофізичні і електрохімічні методи розмірної обробки, основані на різних процесах безпосередньої енергетичної дії на оброблювану заготовку, знаходять в промисловості все більш широке розповсюдження.
Характерними особливостями цих методів є можливість обробки заготовок незалежно від твердості матеріалу. При цьому оброблювальний інструмент може мати твердість значно меншу. У процесі обробки інструмент не надає силової дії на заготовку, що виключає утворення поверхневого шару наклепу.
Верстати для електричної обробки надзвичайно прості, що дозволяє легко автоматизувати їх роботу. На верстатах даної групи виготовляють складні штампи не тільки з жароміцних сталей, але і з твердих сплавів, прес форми і інші деталі, отвори дуже малих розмірів, у тому числі некруглі.
|
|
2. Залежно від виду фізико-хімічних процесів ці методи підрозділяються на такі групи:
1. Електроерозійні методи – основані на руйнуванні матеріалу оброблюваної заготовки за допомогою електричних розрядів, що виникають між інструментом і заготовкою. Залежно від тривалості розряду і прийнятої схеми обробки розрізняють електроіскровий, електроімпульсний, електроконтактний і анодно-механічний методи.
2. Хімічні і електрохімічні методи основані на видаленні металу із заданих ділянок заготовки за рахунок протікання або хімічних, або електрохімічних процесів, при яких метал заготовки перетворюється на хімічні з'єднання, що легко видаляються із заготовки.
3. Ультразвукові методи основані на знятті із заготовки припуска за рахунок імпульсних дій абразивних частинок, які вони скоюють під дією ультразвукових коливань інструменту.
4 Променеві методи обробки основано на дії на заготовку висококонцентрованою енергією світлового або електронного променя, яка в місці падіння перетвориться в теплову енергію.
На даний час найбільш поширені установки для електроерозійної або хімічної обробки (75%), значно менше – ультразвукові (18%), електрохімічні (7%) і променеві (1%).
Широкому застосуванню електрохімічних методів перешкоджають істотні недоліки. Їх точність і продуктивність значно нижче, ніж у традиційних методів, а енергоємність значно вище. Тому вони знаходять застосування лише в тих випадках, коли іншими методами не забезпечити виконання поставлених задач.
3. Розглянемо принципи обробки металів електроерозійними методами.
|
|
Електроіскрова обробка металів зоснована на використанні короткочасних іскрових розрядів. Схема обробки металів показана на рисунку 2.21.
Заготовку (анод) 1 й інструмент (катод) 2 підключають до джерела струму з напругою, достатньою для збудження іскрового розряду. Для отримання цих розрядів використовують спеціальні генератори імпульсів. При роботі цих генераторів за схемою опір – конденсатор електрична енергія поступає до джерела енергії (наприклад, від мережі) через опір 3 і постійно заряджає конденсатор 4. Після закінчення зарядки напруга на обмотках конденсатора підвищується.
|
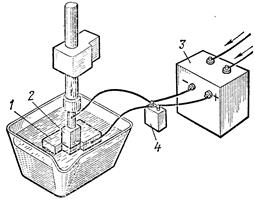
При зближенні заготовок й інструмента відбувається іонізація простору між ними і його пробій, тобто виникає електричний розряд у вигляді вузького стовба (провідного каналу) з температурою від 6000 до 50 000оС. Канал розряду звичайно утворюється між двома виступами на електродах, що лежать на коротшій відстані. У підвалини цього каналу відбувається руйнування і часткове випаровування металу – електрична ерозія.
Електроімпульсна обробка металів зоснована на використанні явищ електричної ерозії металів у рідкому діелектричному середовищі (частіше у мінеральному маслі). Застосовують її найбільше для прошивки, об´ємного копіювання і при обробці різців, фрез і штампів із жароміцних і твердих сплавів.
При електроімпульсній обробці заготовка є катодом, а інструмент – анодом. Це означає, що основний вплив на оброблювану поверхню здійснюють не електрони, а іони. Процес обробки полягає у послідовному збудженні переривистих розрядів між інструментом і заготовкою, що розташовані один від одного на відстані не більш 0,1 – 0,12 мм. Цей процес зоснований на плавленні малих частинок металу у зоні електричних розрядів, що виникають між електродами. Кожний розряд супроводжується виділенням великої кількості теплоти, яка викликає плавлення металу у зоні розряду і викид розплавлених частинок металу у міжелектродний простір. Розплавлений метал “розчиняється” у рідкому діелектрику і затвердіє у вигляді дрібних кульок. Плавлення відбувається переважно на заготовці.
При електроімпульсній обробці застосовується низька напруга (від 10-12 до 24-26 В) і відносно великий струм (50 – 200 А)
Оброблюваність металу визначається температурою його плавлення та теплопровідністю і не залежить від механічних властивостей.
Електроконтактно-дугова обробка зоснована на електромеханічному руйнуванні оброблюваного металу переважно на повітрі без застосування електроліту. Метал руйнується під дією електричних дугових розрядів при швидкому переміщенні інструмента відносно заготовки, що обробляється.
Рисунок 2.22 – Схема різних видів електроконтактно-дугової обробки металів
Обробку застосовують для різання заготовок (рис 2.22,а), обдирки відливок чи зливків (рис. 2.22,б), заточки інструмента (рис. 2.22,в) чи очищення від окалини, обробки круглих заготовок (рис. 2.22,д), а також для згладжування шорсткості поверхні металічних виробів, прошивки отворів та іншої чорнової обробки плоских і криволінійних поверхонь, наприклад кулі (рис. 2.22,е).
Заготовку 1, що обробляють, та інструмент 2 (частіше диск) підключають до джерела постійного чи змінного струму. Опір під невеликим тиском двох металевих електродів (заготовки й інструмента) приводить до утворення у місці контакту підвищеного опору, що утворює розігрів, розм´якшення і плавлення матеріалу заготовки. Для запобігання плавлення диска йому надають велику швидкість переміщення відносно заготовки (50-80 м/с), що скорочує тривалість контакту диска з заготовкою, чи застосовують охолодження. При підвищеній напрузі до 30-40 В виникає іскровий розряд без помітного механічного контакту між інструментом і заготовкою.
|
|
Анодно-механічна обробка зоснована на електрохімічному й електротермічному руйнуванні металу, що оброблюється. При цьому способі обробки (рис. 2.23,а) інструмент 2 є катодом, а заготовка 1 – анодом.
Рисунок 2.23 – Схема анодно-механічної обробки
У процесі роботи установки заготовка, що оброблюється, поливається електролітом через шланг 3 так, щоб зазор між диском і заготовкою завжди був заповнений робочою рідиною. Іноді заготовку занурюють у ванну з електролітом (рис. 2.23,б). Як електроліт звичайно застосовують водний розчин рідкого скла. При проходженні постійного струму через електроди і електроліт поверхня заготовки підлягає анодному розчиненню і на ній утворюється струмопровідна плівка, що забезпечує безперервний потік процесу. Крім того, інструмент і заготовка здатні при визначених умовах збуджувати іскродугові розряди. При подачі до заготовки диска, що обертається, відбувається контакт їх у місці виступів на невеликих ділянках, на яких видалена плівка. При достатньо високій напрузі на малих ділянках поверхні відбувається короткочасний дуговий розряд. Ці розряди, розвиваючи високу температуру, виплавляють метал на заготовці і на місці виступів виникають впадини. У результаті сусідні ділянки опиняються виступами, які при подальшому зближенні інструмента і заготовки будуть виплавлятися, і т.д.