1.Загальні відомості про зварювання металів.
2. Дугове зварювання.
3. Електрошлакове зварювання.
4. Газове зварювання.
5. Контактне зварювання.
6. Особливі способи зварювання.
1 Зварювання – технологічний процес отримання нероз'ємних з'єднань за допомогою встановлення міжатомних зв'язків між зварюваними частинами виробу при їх місцевому або загальному нагріванні, пластичній деформації, а також при сумісній дії того й іншого факторів.
Залежно від стану металу в зварювальній зоні всі способи зварювання поділяються на дві групи: плавленням і тиском. Зварне з'єднання, отримане зварюванням плавленням (рис. 2.14, а) складається з:
- зварюваного металу 1, що не змінив своїх властивостей при зварюванні;
- зони термічного впливу 2, структура і властивості металу цієї частини зварного з'єднання змінилися в результаті фазових перетворень або рекристалізації під впливом нагріву від 500оС до Тпл;
- зони сплаву 3 з частково оплавленими зернами зварюваного металу;
- зварного шва 4, що утворився в результаті кристалізації зварної ванни (розплавленого зварюваного і присадного металу) і має дентридну будову.
|
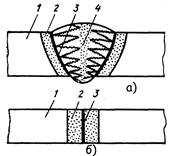
З'єднання, виконане зварюванням тиском (рис.2.14,б), складається із зварюваного металу 1, зони термомеханічного впливу 3 і зони з'єднання 2, де утворилися міжатомні зв'язки між зварюваними металами.
До зварювання плавленням відносяться такі способи: дугове, електрошлакове, електронно-променеве, лазерне, газове, термітне, а до зварювання тиском — контактне, дифузійне, холодне, ультразвукове, вибухом і ін.
Зварні з'єднання можуть бути (рис. 2.15): стиковими— а (виконуються за допомогою стикових швів), кутовими — б, тавровими— в, внакладку— г (виконуються за допомогою кутових швів).
|
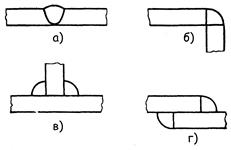
2. Загальні відомості про дугове зварювання (ДЗ). Вперше дугу для зварювання застосував Н.Н. Бенардос в 1881 р. (для зварювання він використовував дугу між вугільним електродом і металом), а Н. Г. Славянов в 1888 р. запропонував дугове зварювання металевим плавким електродом, яке знайшло найбільше застосування серед інших способів зварки. При ручному дуговому зварюванні (РДЗ) плавким електродом (рис. 2.18) дуга виникає між стержнем електроду 7 і зварюваним металом 1 сприяє їх плавленню, краплі 8 електроду, що розплавляються, переносяться в зварювальну ванну 4 через дуговий проміжок. Разом із стержнем плавиться електродне покриття 6, створюючи газовий захист навколо дуги 5 і рідку шлакову ванну, яка разом ізрозплавленим металом утворює зварювальну ванну. При пересуванні дуги метал зварювальної ванни твердне і перетворюється на зварний шов 2, на поверхні якого утворюється шлакова корка 3, що видаляється після охолодження зварного шва.
|
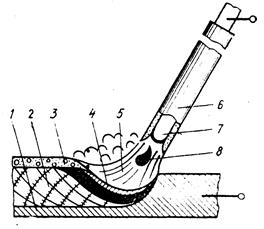
Зварювальна дуга є стійким електричним розрядом в іонізованій суміші газів і парів матеріалів, вживаних при зварюванні. Дуга може горіти при використовуванні джерел живлення (ДЖ) постійного струму прямої (електрод підключений до негативного полюса ДЖ і називається катодом, а виріб — до позитивного і називається анодом) і зворотної полярності (виріб – катод, а електрод – анод), а також змінного струму промислової частоти
Ручне дугове зварювання (РДЗ) використовується для виготовлення зварних з'єднань практично всіх типів з металів товщиною від 2 до 60 мм При РДЗ використовують зварювальні електроди, які подаються в дугу і переміщуються уздовж виробу зварником вручну. Плавкі електроди виготовляються у відповідності з ГОСТ 2246—70 із зварювального дроту: вуглецевого (Св-08; Св-08А; Св-10ГА і ін.) і легованого (Св-10Г2СА; Св-10Х18Н10Т; Св-12Х11НМФ і ін.), де в написанні маркування дроту позначають: Св — зварювальний; цифри, що йдуть далі, вміст вуглецю в сотих частках відсотка; подальша розшифровка маркування проводиться аналогічно відповідним маркуванням сталей.
Для електродів використовуються металеві стержні (дріт) діаметром 1,6—12 мм і завдовжки 200—450 мм, на які наноситься шар покриття товщиною від 0,5 до 2—3 мм. До складу покриття для якісних електродів вводять компоненти, які відповідно до їх призначення можна розбити на групи:
- стабілізуючі; що містять метали з малим потенціалом іонізації (крейда, поташ, діоксид титану);
- газоподібні, призначені для захисту розплавленого металу від кисню і азоту повітря середовищем відновних газів, що утворюються при згоранні органічних речовин (крохмаль, декстрин, целюлоза);
- шлакоподібні (польовий і плавиковий шпат, крейда, марганцева руда); легуючі і розкислюючі, що вводяться у вигляді феросплавів Мn, Si, Тi;
- зв'язуючі (рідке скло).
Стандарти на електроди (для вуглецевих і легованих сталей ГОСТ 9467—75) визначають типи електродів: Э42; Э42А; Э55 та ін. Цифри в позначеннях типів електродів означають гарантовану межу міцності металу зварного шва (відповідно sв — 420; 550 МПа); для електродів типу Э42 використаний дріт Св-08, а типу Э42А — Св-08А.
Автоматичне дугове зварювання під флюсом (АДЗФ) — спосіб зварювання, при якому дуга горить під шаром зварювального флюсу (неметалевого сипкого матеріалу), що забезпечує добрий захист металу зварювальної ванни від газів повітря (рис. 2.17). Дуга 10 горить між електродним дротом 2 і зварюваним металом 11 під шаром флюсу 4, що подається з бункера. Частина оточуючого дугу флюсу розплавляється, утворюючи на поверхні зварювальної ванни 8 шар рідкого шлаку 5, під яким створюється порожнина 9, заповнена парами металу, флюсу і газами. По мірі переміщення дуги відбувається затвердіння металу і шлаку — утворюється зварний шов 7, покритий шлаковою коркою 6. Подача дроту в дугу і переміщення автомата вздовж виробу здійснюються за допомогою механізмів подачі електродного дроту 1 і переміщенням автомата. Струм підводиться до дроту через струмопровід 3 від зварювального ДЖ (виліт електроду, що знаходиться під струмом, рівний 40—50 мм, що дозволяє використовувати великі зварювальні струми).
|
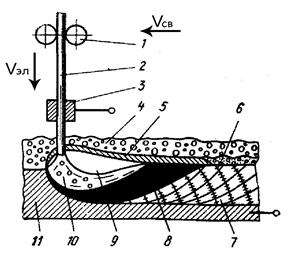
АДЗФ застосовують у заводських і монтажних умовах для зварювання швів великої протяжності в нижньому положенні і кільцевих поворотних швів. Зварюють сталі, алюміній, титан, мідь і їх сплави товщиною від 2 до 300 мм.
Перевагами АДЗФ є: висока продуктивність (у 5—10 разів вище, ніж при РДЗ) завдяки застосуванню великих струмів, більшої глибини проплавлення, відсутності втрат металу на чад і розбризкування, а також механізації процесу; висока якість зварних швів за рахунок доброго захисту металу в процесі зварювання і рівномірного їх формування; поліпшення умов праці зварників і ін. Недоліки АДЗФ полягають у важкості зварювання коротких швів, а також швів, розташованих в складних просторових положеннях і важкодоступних місцях.
3. Електрошлакове зварювання (ЕШЗ) — спосіб зварювання плавленням, при якому для плавлення металу використовується теплота, що виділяється при проходженні електричного струму через електропровідний шлак (розплавлений флюс).
На початку процесу збуджують дугу, за допомогою якої розплавляють флюс, що засипається в порожнину, утворену кромками зварюваних деталей 2, формувачів 5 і початковою технологічною планкою 8 (рис. 2.18, а, б). Після утворення шлакової ванни 3 дуга гасне і процес дуговий переходить в електрошлаковий. У нагрітому до 2000°С шлаку плавиться електрод 1 і оплавляються кромки зварюваних деталей, встановлених із зазором 20—50 мм. Для формування зварного шва 7 і утримання шлакової і металевої 4 ванн від витікання використовують формувачі — мідні повзуни, охолоджувані водою 6 і що переміщаються разом із зварювальним апаратом по бічних поверхнях деталей. Метал, що кристалізується в нижній частині металевої ванни, утворює зварний шов.
|
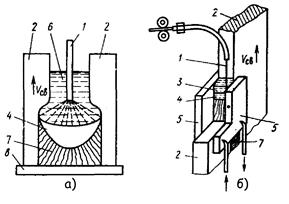
Головна перевага ЕШЗ — можливість зварювання за один прохід металу (сталей, алюмінієвих і титанових сплавів) практично будь-якої товщини (від 20 до 2000—3000 мм), тому продуктивність ЕШЗ у 5—15 разів вище, ніж у АДЗФ. ЕШЗ дозволяє виконувати вертикальні шви, а також кільцеві (при цьому зварювані деталі — обичайки – обертаються на спеціальному роликовому стенді щодо нерухомих зварювального апарата і формувачів).
4. Газова зварка (ГЗ) — спосіб зварювання плавленням, при якому метал в зварювальній зоні нагрівається полум'ям газу (ацетилену, метану), спалюваного для цієї мети в суміші з киснем у зварювальних пальниках. Перевага ГЗ — це його універсальність. За допомогою ГЗ можна зварювати метали різної товщини з різними властивостями (сталі, чавуни, кольорові метали). Недоліками ГЗ є трудність автоматизації процесу і тривала теплова дія на метал, що приводить до зміни структури і форми зварного з'єднання.
5. Контактне зварювання (КЗ) — основний спосіб зварки тиском. При КЗ для нагрівання металу в зварювальній зоні використовується теплота, що виділяється при проходженні струму в місці контакту зварюваних деталей. Особливістю КЗ є використовування короткочасних (t = 0,003÷10 с) імпульсів струму великого значення (I = 1 ÷ 100 кА) при напрузі U= 2 ÷ 12 В і тиску Р = 10 ÷ 150 МПа. Живлення зварювальним струмом здійснюється від знижувального трансформатора. Максимальна кількість теплоти виділяється в зоні контакту деталей, де метал нагрівається до пластичного стану або до плавлення. Під дією стискаючих зусиль нерівності знімають, а оксидні плівки видавлюються із стику — відбувається зближення нагрітих деталей до міжатомних відстаней, тобто зварювання. Основними видами КЗ є точкове, шовне (роликове) і стикове.
Точкове зварювання (рис. 2.19, а) здійснюється для з'єднання металів (різних сталей, сплавів А1, Ti, Сu) завтовшки 0,6—2,5 мм. Зварювані деталі 2 і 3 з`єднують внакладку і затискають між рухомим 1 і нерухомим 4 електродами машини і пропускають через них струм, нагріваючий метал у місці стику до плавлення, а прилеглу до ядра зварювальної точки 5 зону — до пластичного стану. Після кристалізації зварювальної точки тиск знімається. Цей спосіб відрізняється великою продуктивністю і забезпечує необхідну міцність зварних з'єднань (корпуси автомашин, вагонів, холодильників, деталей радіоелектроніки та ін).
|
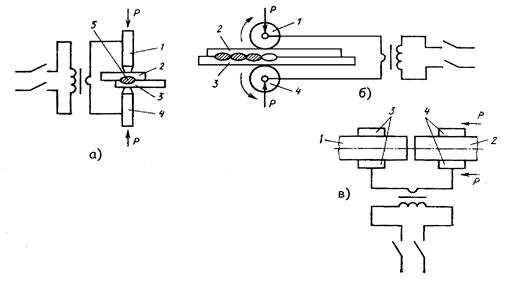
Шовне (роликове) зварювання (рис. 2.19, б) здійснюється для з'єднання внакладку металів (сталей, сплавів А1, Ti, Сu) завтовшки 0,6—3 мм При зварюванні деталі 2 і 3 затискають між електродами (роликами) 1 і 4, що обертаються, за допомогою яких відбуваються передача зусилля до деталей, підведення струму і переміщення деталей. При шовному зварюванні утворення безперервного (герметичного) і міцного шва відбувається перекриттям подальшої точки попередньої, що робить можливим застосування цього способу для виготовлення різних ємностей.
Стикове зварювання (рис. 2.19, в) здійснюється за двома схемами (зварювання опором і оплавленням) з використанням однотипного устаткування. Зварювані деталі 1 і 2 (стержні, труби, рейки) закріплюють у нерухомому 3 і рухомому 4 затискачах — електродах зварювальної машини, до яких підводиться струм. При зварювані опором ретельно зачищені торці деталей з`єднують під невеликим тиском, а після включення струму і розігрівання металу в стику тиск підвищують. Так зварюють маловуглецеві сталі і кольорові метали невеликого перетину (до 200—250 мм2). При стиковому зварюванні плавленням стик зварюваних деталей розігрівається до оплавлення, а наступне за цим осідання сприяє видавлюванню із стику рідкого металу, що забезпечує отримання високої якості зварних з'єднань. Зварювання оплавленням дозволяє зварювати вироби з вуглецевих і легованих сталей, чавуну, сплавів А1 і Ti перетином до 100 000 мм.
6. Особливі способи зварювання. Термітне зварювання (ТЗ) здійснюється за допомогою теплоти, одержуваної при згорянні порошкоподібних оксиду (Fе2О3) і елементів з великою активністю по відношенню до кисню (А1, Мg). Якщо в тигель з вогнетривкого матеріалу помістити суміш, що складається з А1 і Fе2О3 (алюмінієвий терміт), і запалити за допомогою термосірників, то відбувається екзотермічна реакція Fе2О3 + 2А12О3 + 2Fе. Температура отриманого розплаву складає 2200—2600°С, а складові цього розплаву Fе і А12О3 розділяються відповідно до їх густини (залізо внизу). Акумульований цим розплавом запас теплоти може бути використаний для зварювання плавленням і тиском. При ТЗ плавленням нагрівання встановлених у формі зварюваних деталей і плавлення їх кромок у місці утворюваного стику здійснюються рідким розплавом заліза, що служить одночасно і присадним металом. При ТЗ тиском на підготовлене для зварювання з'єднання з щільно стиснутими торцями одягають форму. У форму заливається спочатку розплав А12О3, який змочує зварюваний метал і створює на його поверхні плівку, перешкоджаючу його зварюванню з термітним металом, а потім розплав Fе, який розігріває зварюваний метал. Після цього застосовують здавлення деталей (осідання) за допомогою стяжних пресів. В основному використовується ТЗ плавленням для зварювання рейок, ремонту сталевих і чавунних деталей за допомогою алюмінієвого терміту і сталевих дротів за допомогою магнієвого терміту.
Дифузійне зварювання — зварювання тиском, при якій зварювані деталі піддаються загальному електронагріву у вакуумних камерах до температури (0,4 - 0,8) Тпл, тривалій витримці при цій температурі і стисненню з тиском до 25 МПа. Такі умови зварювання сприяють протіканню процесів дифузії атомів у поверхневих шарах зварюваних металів. Дифузійне зварювання застосовують для з'єднання важкозварюваних металів і сплавів (сталь з Аl, Тi, W і Мо; Сu з А1, Тi), а також металокерамічних виробів.
Зварювання тертям — спосіб зварювання тиском, при якому місцевий нагрів металу в стику до температури, близької до Тпл, здійснюється завдяки роботі сил тертя, що виникають при переміщенні один щодо одного зварюваних деталей, стиснутих осьовою силою. Крім нагрівання металу тертя сприяє руйнуванню оксидних плівок в зварюваному стику. При зварюванні тертям одержують зварні з'єднання круглого і суцільного або трубчастого перетинів.
Холодне зварювання (ХЗ) – зварювання тиском, здійснюване без нагрівання за рахунок пластичної деформації металу в зварювальній зоні. Для проведення ХЗ необхідно видалити оксиди із зварюваної поверхні і зближувати їх на відстань параметра кристалічних граток для утворення міжатомних зв'язків між ними. Холодним зварюванням можна одержувати з'єднання з пластичних металів (Al, Cu, Ag, Au і їх сплавів) внапусток завтовшки 0,2 – 15 мм і встик перетином до 700 мм2.