Разъёмы предназначены для печатных плат и имеют выводы, к которым припаяны провода. Студенты отпаивают провода, очищают выводы разъёмов от лишнего припоя. Затем они приготавливают провода к пайке, скручивая их жилы под жалом паяльника. При необходимости заменить провод его зачищают от изоляции и лудят. Затем студент припаивает один провод и показывает пайку преподавателю. Если пайка хорошая, преподаватель разрешает припаять остальные провода.
Для пайки применяют паяльники мощностью 25 Вт (рисунок 5).
Рисунок 5 – Паяльник мощностью 25 Вт (https://drim.by)
Пайка – соединение однородных или разнородных металлов, а также металлов с неметаллами, с помощью расплавленного припоя. Как правило, процессу пайки предшествует лужение. Лужение (полудка) – операция, при которой металл покрывается слоем расплавленного припоя. Пайка медных жил и проводов малого сечения осуществляется с помощью паяльника (электропаяльника), для пайки медных жил большого сечения используют пламя пропанокислородной или ацетиленокислородной горелки, паяльной лампы либо способ заливки предварительно расплавленным припоем.
|
|
При пайке меди и сплавов применяют мягкие припои марки ПОС (оловянно-свинцовые), а также твердые припои ПМЦ (медно-цинковые) и ПСр (серебряные).
Оловянно-свинцовые припои марки ПОС (цифра от 18 до 90 показывает содержание олова) применяют:
– ПОС-61 (температура плавления – 183 ºС) – при пайке РЭА;
– ПОС-40 (235 ºС) – для пайки соединения проводов;
– ПОС-30 (250 ºС) – для пайки свинцовых оболочек кабелей.
Трубчатые припои изготавливают в виде трубочки диаметром 1–5 мм, заполненной канифолью, служащей в качестве флюса.
Добавки в оловянно-свинцовые припои сурьмы, кадмия, а особенно висмута позволяют снизить температуру их плавления (до 60,5 ºС у сплава Вуда). Однако легкоплавкие припои отличаются малой механической прочностью и хрупкостью.
Твёрдые припои обладают высокой механической прочностью и применяются для выполнения соединений, работающих при повышенной температуре. Температура плавления латуней ПМЦ с содержанием меди 36–54 % (остальное – цинк) составляет 825–860 ºС. Серебряные припои содержат 25–70 % серебра, 26–40 % меди, 4–35 % цинка, имеют температуру плавления 720–765 ºС и отличаются высокой электропроводностью.
Для разрушения оксидной плёнки, а также для защиты поверхности соединяемых металлов от окисления при нагреве применяют различные флюсы. При пайке меди и сплавов мягкими припоями используют активные (кислотные), пассивные (бескислотные), активированные и антикоррозийные флюсы.
Активные флюсы используют при пайке железа, стали и сплавов на основе железа, а также меди, латуни и бронзы. После пайки место спая требует тщательной промывки в воде. Если на металле остался активный флюс, то он через некоторое время покрывается ржавчиной и зеленеет, происходит разрушение как спая, так и основного металла. Широко применяемая паяльная кислота представляет собой 30%-ный раствор хлористого цинка в воде.
|
|
Бескислотные флюсы (канифоль в чистом виде, а также с добавками спирта и глицерина) используют для пайки меди и сплавов на основе меди мягкими припоями при монтаже РЭА. В промышленном производстве для пайки печатных плат используют флюс ЛТИ-120 (этиловый спирт 65–70 %, канифоль 20–25 %, диэтиламин 5 %, триэтаноламин 1–2 %).
Активированные флюсы приготавливают на основе канифоли с добавками небольшого количества солянокислого или фосфорнокислого анилина, салициловой кислоты и т. п. Они позволяют производить пайку без предварительной зачистки поверхности соединяемых металлов (достаточно обезжиривания). Активированным флюсом является также паяльный жир, содержащий 10 % хлористого цинка и широко используемый при пайке оцинкованного железа. Промывка спая в воде от остатков таких флюсов не требуется.
Антикоррозийные флюсы изготавливают на основе фосфорной кислоты (с добавлением различных органических соединений и растворителей), а также на основе органических кислот. Остатки этих флюсов не вызывают коррозии.
При пайке твёрдыми припоями меди и её сплавов используют буру (тетраборно-кислый натрий) и другие флюсы, содержащие соединения фтора, хлора и бора с калием, натрием, литием, цинком, кадмием, аммонием, а также триэтаноламин.
Пайка печатных плат
Печатные платы предназначены для электронных устройств. В них впаяны различные элементы: резисторы, конденсаторы, транзисторы, интегральные микросхемы. Студенты учатся ремонтировать электронные устройства, выпаивая из печатных плат как будто неисправные элементы и впаивая в них как будто исправные.
Печатные платы. В основе печатного монтажа лежит печатная плата, представляющая собой диэлектрическую пластину, на которую с одной или двух сторон нанесены печатные проводники в виде тонких электропроводящих полосок. При печатном монтаже обычно толщина проводников – 20–50 мкм, их ширина – 0,5–0,8 мм и минимальное расстояние между ними – 0,3–0,5 мм. Вследствие благоприятных условий теплоотвода в печатных проводниках допускается высокая (до 30–50 А/мм2) плотность электрического тока. Контактные переходы с одной стороны платы на другую осуществляют путём металлизации стенок отверстий или установкой металлических трубок с последующей их развальцовкой и опайкой. При микроминиатюризации аппаратуры на основе многовыводных интегральных схем применяют многослойные печатные платы (склеенные между собой) и тем самым достигают существенного повышения плотности монтажа.
В практике конструирования электронной аппаратуры на печатной плате особо важное место занимает компоновка. При рациональной компоновке деталей следует добиваться минимальной длины соединительных проводников. Следует также учитывать, что любой элемент схемы (резистор, транзистор, конденсатор, катушка индуктивности и т. д.) требует для нормальной работы площади и объёма пространства гораздо больше своих геометрических размеров, поскольку электрическое, магнитное и тепловое поля работающего элемента выходят за пределы его конструкции. Непродуманная компоновка деталей на плате является главной причиной неудовлетворительной работы прибора, собранного по многократно проверенной схеме.
Технологический процесс сборки печатной платы состоит из следующих типовых этапов:
– подготовка выводов электронных компонентов (формовка, обрезка);
|
|
– установка компонентов (ручная, автоматическая);
– пайка (волной припоя, ручная, селективная);
– отмывка (ультразвуковая, струйная).
На некоторых предприятиях сохранилась технология, при которой из-за проблем с покрытиями выводов и хранением компонентов подготовка выводов включала в себя предварительное лужение, однако современная технология этого не предусматривает благодаря качественной упаковке и покрытию выводов современных компонентов.
Подготовка выводов электронных компонентов производится с целью:
– выравнивания (рихтовки) выводов (если требуется);
– обеспечение необходимого монтажного расстояния между выводами;
– получения определённого зазора между платой и компонентом (если требуется);
– фиксации компонентов на плате при ручном монтаже, либо до поступления платы в установку пайки.
Рисунок 6 – Обеспечение с помощью формовки выводов: а – зазора между платой и компонентом; б – самофиксации компонента |
а) |
б) |
Тяжёлые элементы (например трансформаторы) или элементы, подверженные механическим воздействиям (тумблеры, потенциометры, подстроечные конденсаторы), устанавливаются с помощью особых держателей. Такие держатели обеспечивают надёжное механическое крепление соответствующих элементов к печатной плате и предотвращают обрыв и поломку выводов под воздействием механических нагрузок.
Ручная пайка предварительно установленных компонентов на печатную плату проводится с применением аналоговых и цифровых паяльных станций (рисунок 7).
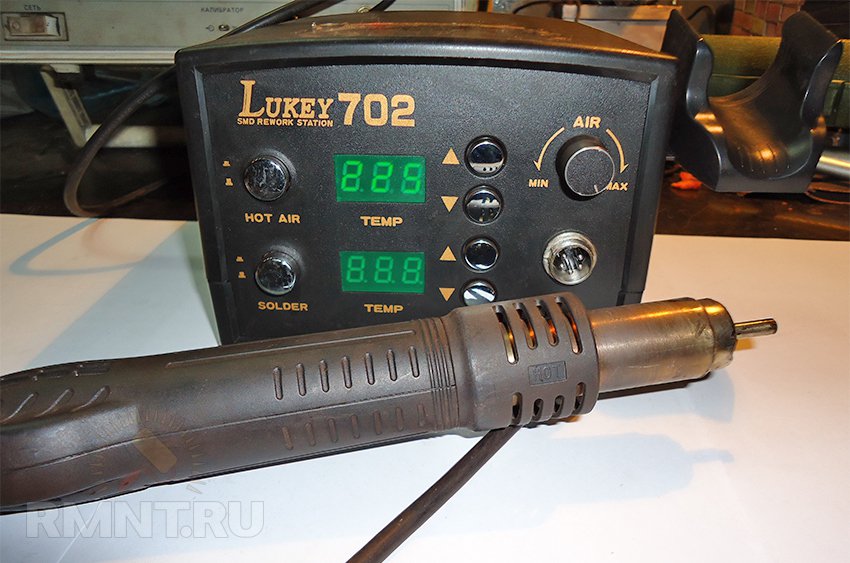
Рисунок 7 – Цифровая паяльная станция (https://rmnt.ru)
Подготовленные поверхности покрывают флюсом непосредственно перед пайкой. Механизм действия флюса заключается в том, что оксидные плёнки металла и припоя под действием флюса растворяются, разрыхляются и всплывают на его поверхности. Вокруг очищенного металла образуется защитный слой флюса, препятствующий возникновению оксидных плёнок.
|
|
Жидкий припой замещает флюс и взаимодействует с основным металлом. Слой припоя постепенно увеличивается и при прекращении нагрева затвердевает. При проведении процесса пайки крайне важно выдерживать необходимую температуру. Подбор температуры осуществляется в зависимости от применяемого припоя, типа и размера корпуса компонента, материала и топологии платы.
Пониженная температура приводит к недостаточной жидкотекучести припоя и плохому смачиванию соединяемых поверхностей. Значительное увеличение температуры вызывает обугливание флюса до активации им поверхностей спая.
Важными характеристиками паяльной станции являются:
– быстрый нагрев жала до рабочей температуры;
– точный контроль температуры жала с максимальной частотой;
– автоматическая калибровка станции при смене жала либо паяльника;
– быстрая смена жал.
Такими возможностями обладают преимущественно цифровые паяльные станции, которые обеспечивают более точное задание, поддержание и управление температурой паяльника по сравнению с аналоговыми, а также позволяют подключать к станции несколько инструментов.
Для пайки обычно используются жидкий флюс и проволочный припой. Флюс наносится кистью в места пайки. Для пайки в труднодоступных местах, а также для ремонта применяют трубчатые припои с несколькими каналами флюса внутри. Преимущественно применяются припои со слабоактивированными низкоканифольными флюсами, не требующими отмывки, либо со среднеактивированными канифольными, для которых отмывка возможна, но не является обязательной при нормальных условиях эксплуатации изделия. Для пайки сильно окисленных поверхностей, а также поверхностей с плохой паяемостью применяются активированные канифольные флюсы, требующие последующей отмывки в деионизованной воде или органическими растворителями на спиртовой основе. Припои используются как оловянно-свинцовые (Sn-Pb, Sn-Pb-Ag), так и бессвинцовые (Sn-Cu, Sn-Ag-Cu); поставка осуществляется в катушках.
Последовательность пайки установленных в отверстия компонентов:
– очистка жала паяльника (если необходимо), его облуживание;
– установка температуры жала паяльника на станции;
– выдержка, в процессе которой происходит нагрев жала паяльника до требуемой температуры;
– приведение жала в контакт (одновременный) с контактной площадкой и выводом компонента для обеспечения их прогрева, небольшая выдержка (0,5–1 с);
– подача прутка припоя к паяному соединению с образованием связи между выводом и КП (не следует подавать припой непосредственно на жало паяльника во избежание преждевременного выгорания флюса);
– охват припоем вывода по кругу на 360°;
– одновременный отвод прутка припоя и жала паяльника (по направлению вверх вдоль вывода ЭК для образования галтели правильной формы).
Процесс пайки одного соединения должен быть по возможности кратковременным. Во избежание перегрева компонента и отслаивания контактной площадки его общее время составляет от 0,5 до 2 секунд. При пайке необходимо следить за тем, чтобы паяльник даже на короткое время не прикасался к корпусу компонента и чтобы на него не попадали капли припоя и флюса. После работы жало паяльника необходимо облудить для увеличения срока его службы.
Существуют паяльники с одновременной подачей прутка припоя (пайка одной рукой, вторая может использоваться для удержания компонента и/или платы), а также станции автоматической непрерывной либо дискретной подачи припоя в точку пайки.
Конец вывода должен быть различим в образованном паяном соединении (не должно присутствовать избыточного количества припоя). Поверхность галтелей припоя – вогнутая, непрерывная, гладкая, глянцевая, без тёмных пятен и посторонних включений. Припой не должен касаться корпуса компонента. Не допускается растекание припоя за пределы контактной площадки по проводнику.
Изготовление печатной платы вручную. Когда схема соединений вычерчена, координаты центров контактных площадок, отверстий для крепления, а также контуры платы переносят на плату из фольгированного материала. Поверхность фольги перед этим тщательно зачищают микронной шкуркой, чтобы удалить плёнку оксида, а затем обезжиривают ацетоном. В дальнейшем следует избегать касания фольги руками.
После этого рисунок печатной платы наносят на фольгу кислотоупорной краской (нитроэмаль НЦ-25, асфальтово-битумный лак, цапонлак). Контуры контактных площадок удобно наносить стеклянным рейсфедером с надетой на него ПВХ трубкой или другим способом.
Рисунок печатных проводников можно выполнять самодельным рейсфедером, изготовленным из использованного пластмассового стержня шариковой авторучки. Конец стержня длиной 130 мм осторожно нагревают над пламенем спиртовки. Как только трубка размягчится, оттягивают её конец и обрезают лезвием. Пластмассовый стержень пишет мягче металлического или стеклянного. В процессе работы рейсфедер необходимо периодически промывать в ацетоне.
Заготовки печатных плат обычно травят в растворе хлорного железа с удельным весом 1,36, налитом в фотокювету подходящих размеров. Процесс травления длится 0,5–1,5 ч. Его можно ускорить покачиванием кюветы. После окончания процесса травления заготовку ополаскивают, тщательно промывают тёплой проточной водой. Лак снимают наждачной бумагой № 60, 80 или тампоном, смоченным в ацетоне. Далее в плате сверлят отверстия под выводы деталей и для элементов крепления крупных деталей, а также обрабатывают плату по контуру. После сверления со стороны, противоположной печатным проводникам, со всех отверстий аккуратно удаляют заусеницы, пользуясь сверлом, заточенным под углом 90°, и диаметром, примерно вдвое большим, чем сверло, которым сверлили отверстие.
Готовую печатную плату следует для консервации покрыть тонким слоем канифольного лака или сразу же залудить хотя бы контактные площадки. Лудить проводники платы удобно следующим образом. Тщательно зачищенные проводники покрывают тонким слоем спиртоканифольного флюса. На конец тонкого деревянного стержня надевают отрезок оплётки экранированного кабеля длиной около 20 мм и закрепляют его проволочным бандажом. Свободный конец оплётки, пропитанный припоем, прижимают жалом паяльника к проводнику платы и двигают вдоль него. Слой получается тонким и ровным. Если излишки припоя замкнули соседние проводники, ещё раз проводят нагретой оплёткой, чтобы она впитала лишний припой.