![]() | ЗВ |
![]() | зв |
Однородность | 2В |
Двулучепроломление | |
Ослабление | |
Бессвильность | 2А |
Пузырность | 4Г |
Требования к обработке | |
N | |
![]() | 0,4 |
Р | IV |
Требования к изготовлению | |
![]() | |
![]() | |
![]() | |
l |
Рис. 1.16. Фрагмент чертежа призмы
Допуск на пирамидальность - это отклонение от параллельности ребра прямого угла гипотенузной грани (рис. 1.17).
Рис. 1.17. К определению допуска на пирамидальность пи призмы
Выражается в угловой мере. Отклонение от параллельности ребра прямого угла гипотенузной грани приводит к тому, что призма становится пирамидой с весьма малым углом при вершине. Пирамидальность вызывает отклонение луча от расчетного направления и вносит хроматизм.
Общую пирамидальность призмы при обработке измеряют от гипотенузной плоскости по разности размеров А1, А2 на длине ребра прямого угла к гипотенузной грани.
Обычно значение пи лежит в диапазоне 30'-1".
Допуск на разность углов призмы 45 выражается в угловой мере (
) (разность острых углов), обычно устанавливают
45 =>30'-10".
|
|
Допустимое значение предела разрешения E выражают в угловой мере.
Величина E определяет влияние оптической неоднородности, двойного лучепреломления, бессвильности стекла, а также влияние N, Р, ,
45 на разрешающую способность призмы.
Величина l - длина хода лучей в призме.
1.4. Заготовки оптических деталей
Заготовка - предмет производства, из которого изменением формы, размеров, шероховатости и свойства материала изготавливают деталь.
Виды заготовок: прессовки (призма, линза, пластина) - наиболее рациональные заготовки, так как приближены по форме и размерам к готовой детали (рис. 1.18).
Абвг
Рис. 1.18. Виды прессовок: а - призма; б, в, г - пластина
Для изготовления прессовок необходимы пресс-форма и шаблоны, стоимость которых окупается при прессовании определенного числа заготовок.
По ГОСТ 13240-78 «Заготовка оптического стекла» установлен минимальный объем партии заготовок-прессовок, в зависимости от массы заготовки (табл. 1.2).
Таблица 1.2
Масса, г, | Количество (не менее), шт. |
1,5-10 | |
250-500 |
Размеры прессовок 8-150 мм; толщина прессовок для линз не менее 3 мм, плоских деталей не менее 4 мм. Отношение диаметра или диагонали заготовки к ее толщине
/t>1/15. Прессовки используются в массовом и крупносерийном производствах.
Если необходимо меньшее число заготовок (прессовок), чем предписано ГОСТ, то их получают из плиток, кратных заготовок, штабиков (рис. 1.19).
Кратная заготовка имеет размеры, кратные размерам единичной заготовки. Стеклянный пруток называют штабиком. Заготовки из него получают в виде таблеток. Штабики - основной вид заготовок для микрооптики 3-12 мм.
|
|
1.5. Общие сведения о припуске на оптические детали
Деталь отличается по размерам от заготовки на величину полного припуска. Припуском на обработку называется толщина слоя стекла, снимаемого в процессе обработки деталей для обеспечения требуемых размеров и точности.
Полный припуск (рис. 1.20): =
1+
2+
3+
4+...
n=
i(для iот 1 до п).
![]() |
Операционный припуск i - это слой стекла, удаляемый с поверхности заготовки при выполнении каждой отдельной операции.
Обычно припуски распределены следующим образом:
1 - припуск на распиливание кратной заготовки (как правило, устанавливается в диапазоне от 1 до 1,5 мм);
2 - припуск на грубое шлифование (значение от 0,5 до 0,8 мм);
3 - припуск на тонкое шлифование (значение от 0,1 до 0,3 мм);
4 - припуск на полирование (значение от 0,05 до 0,1 мм).
Может быть предусмотрен припуск на центрировку.
На производстве грубое шлифование иначе называют заготовительной операцией, среднее шлифование - шлифованием, мелкое (тонкое) шлифование и полирование - полированием.
Припуски установлены:
• для линз, пластин - на диаметры, толщину по оси и шамотную сторону;
• для призмы - на чистую и шамотную стороны. Припуски устанавливаются в зависимости от номинального размера диаметра или наибольшей стороны готовой детали.
1.6. Абразивные материалы
Абразивными материалами называют хрупкие, твердые материалы, которые при раскалывании образуют частицы с острыми кромками (острые режущие грани), способные самозатачиваться при износе в процессе обработки детали. Абразивные материалы делятся на природные и синтетические. Природные абразивные материалы
1. Корунд - состоит из 80 - 90% кристаллического окисла алюминия А1203 и примесей (железо, хром, титан и др.), которые определяют его цвет (от белого до светло-коричневого). Твердость корунда - 9 единиц. Применяется для шлифования большинства оптических материалов.
Твердость - основная характеристика абразивных материалов, определяется по шкале Мооса царапанья материалов образцами-эталонами. Твердость показывается в условных единицах от 1 до 10.
2. Наждак - содержание А12О3 в отличие от корунда не превышает 60%. Наждак - это корунд в сочетании с минералами (слюда, гематит, пирит, магнетит), снижающими его твердость до 8 единиц. Окраска - темно-коричневая.
3. Кварц (кварцевый песок) - зерна окиси кремнезема SiO2, твердость - 7 единиц. Применяется для обработки технического стекла.
4. Алмаз - кристаллическая модификация углерода, твердость -10 единиц. Показатель преломления пe - 2,42. Материал - дорогой: для получения одного карата, т.е. 0,2 г, обрабатывают от 3 до 15 тонн руды.
Синтетические абразивные материалы
1. Электрокорунд - окись алюминия (А1203), получаемая электроплавкой руд, содержащих глинозем (бокситы). Твердость -9 единиц (изготавливают шлифпорошки, микропорошки). Цвет -белый, серый.
Карборунд - Si2C - карбид кремния. Получают оплавлением кварцевого песка с коксом. Цвет - зеленый, черный. Твердость - 9,6 единиц. Применяется для грубого шлифования.
2. Карбид бора В4С - получают оплавлением борного ангидрида с коксом. Цвет - черный. Применяется для обработки твердых материалов. Твердость - 8 единиц.
4. Алмазы синтетические. Их получают при t - 2500 °С и давлении 102 Па, исходный материал - графит. Твердость -10 единиц. Не уступают по свойствам природным алмазам.
Алмазы применяются в оптическом производстве (до 20 %), в основном, в связанном состоянии, а на завершающих стадиях обработки некоторых кристаллов - в свободном состоянии.
Маркировка и обозначение абразивных материалов В зависимости от размеров зерна порошки из абразивных материалов, кроме алмазов, различают:
|
|
1) абразивные, их параметры нормируются по ГОСТ 3647-80 (табл. 1.3); микрошлифпорошки обозначают буквой М и последующей цифрой, указывающей размер зерна основной фракции в мкм;
Таблица 1.3
№ п/п | Наименование | Зернистость по ГОСТ | Размер зерен основной фракции, мкм |
Шлифзерно | 20................. 16 | 200.................. 160 | |
Шлифпорошки | 12, 10,8,6,5,4 | 120....40 | |
Микрошлифпорошки | М63, М50, М40, М28, М20.М14 | 63....14 | |
Тонкие микрошлифпорошки | М10.М7, М5, МЗ | 10....3 |
2) алмазные, их параметры определяются ГОСТ 9206-80 (табл. 1.4).
Таблица 1.4
|
Главной характеристикой абразивного порошка является процент содержания и крупность его основной фракции. Например, микропорошок Ml4, кроме основной фракции - зерен размером 14 мкм, может содержать и другие фракции: предельную М28 не более 3 %, М20 - не более 20%, М7 - не более 31%.
При маркировке шлифзерна шлифпорошков за единицу измерения зернистости принята величина 0,01 мм, т.е. шлифзерно М20 имеет размер зерна основной фракции 0,01 х 20 = 0,2 мм = =200 мкм; шлифпорошок М8 - 0,01 х 8=80 мкм.
Зернистость алмазных шлифпорошков обозначают дробью, числитель которой соответствует размеру (в мкм) ячеек верхнего сита, ограничивающего максимальный размер зерен основной фракции, а знаменатель соответствует размеру ячеек нижнего сита, ограничивающего минимальный размер зерен основной фракции.
В зависимости от сырья алмазные шлифпорошки обозначаются индексами: А - из природных алмазов, АС - из синтетических.
Алмазные микропорошки и субмикропорошки обозначаются индексами: AM - из природных алмазов, АСМ - из синтетических.
К буквенному обозначению добавляют долю зерен крупной фракции в процентах.
Сито 1 (сетка крупная) Сито 2 (сетка средняя) Сито 3 (сетка мелкая) |
![]() |
Разделение абразивных материалов на группы (фракции)
1. Ситовый метод - просев порошков через ряд сит с контрольными сетками, расположенными по убывающим номерам (рис. 1.21).
Рис. 1.21.Схема разделения абразивных материалов ситовым методом |
Набор сит устанавливают на просеивающую машину. Зерна, задерживающиеся в любом сите, обозначаются дробью, у которой числитель - размер верхнего сита, а знаменатель - размер нижнего сита (размеры в мкм).
|
|
2. Разделение в восходящем потоке жидкости.
На производстве данный метод реализуется следующим образом: берут несколько емкостей различных диаметров и устанавливаются последовательно (рис. 1.22).
Рис. 1. 22. Схема разделения абразивных материалов в восходящем потоке жидкости
3. Метод отмучивания.
![]() |
Водный раствор абразива взбалтывается, потом одну минуту отстаивается, за это время на дне сосуда оседает слой абразива определенной фракции (тяжелые фракции оседают быстрее). Мутную воду переливают в другой сосуд и опять взбалтывают и в течение двух минут ждут оседания абразива уже более мелкой фракции, чем в первом сосуде и т. д. (рис. 1.23).
Скорость падения частиц в жидкой среде зависит от их размеров.
В основу маркировки положена одна минута.
1.7. Алмазные инструменты
Алмазные инструменты обладают сравнительно высокой износостойкостью, которая зависит от формы и размеров алмазостойкого слоя, зернистости и концентрации алмазного порошка в алмазоносном слое.
Концентрация алмазного слоя определяет содержание алмаза в алмазоносном слое объемом в 1 см3. За 100%-ную концентрацию условно принята масса 4,4 карата (примерно 0,88 г). При плотности алмаза р = 3,52 г/см объем, занимаемый алмазом, при 100%-ной концентрации составит 0,25 см3.
В оптическом производстве применяется 25- и 50%-ные концентрации.
Наряду с зернистостью и концентрацией алмаза на производительность и износостойкость влияет связка, которая должна прочно удерживать алмазные зерна, обладать хорошей адгезией по отношению к зернам и корпусу, быть достаточно термостойкой, не препятствовать самозатачиванию.
Существуют многокомпонентные связки на основе порошков С и Al, Fe, Со, Ni, Pb, Sn, но в основном применяются связки наоснове меди Ml, Ml0 и железа МЖ (50% Сu +Fe).
Различные виды алмазного инструмента (круги) представлены на рис. 1.24.
![]() |
Круги чашечные алмазные (АЧК) - для обработки плоских и сферических поверхностей (рис. 1.24, а). Параметры Д = 50 - 200 мм; H = 2 - 3 мм.
Круги плоские алмазные прямого профиля (АПП) - для обработки цилиндрических поверхностей, центрирования (рис. 1.24, б). Параметры: Д = 12 - 300 мм; H = 2 - 3 мм; t = 5 - 20 мм.
Круги отрезные алмазные (АОК) 300x1,5x1,5 (рис. 1.24, в). Параметры: Д = 50 - 320 мм; H = 2 - 3 мм; t = 0,15 - 2,0 мм.
Круги кольцевой формы алмазные (алмазные коронки) (АК) - для обработки плоских сферических поверхностей, сверления (рис. 1.24, г). Например, параметры сверла: Д = 10 мм, t = 1 мм; Д = 100 мм, t = 2 мм; Н=2-3 мм.
Круги плоской формы алмазные (АП) для нанесения (снятия) фасок на призмах, пластинах (рис. 1.24, д). Д = 100, 160, 200, 320, 400 мм; H = 2 - 3 мм; t = 10 - 40 мм.
Клеймение кругов производится условными обозначениями: тип круга, основные размеры круга, марка и зернистость алмаза, тип связки, концентрация алмаза, масса алмаза в каратах. Например: АПП 150x5x3x32 (ДхtхHхМ); АСК 125/100 Ml-100-30,0; АСК 125/100 - шлифпорошок К из синтетического алмаза; Ml -связка на медной основе; 100%-ная концентрация; 30,0 - масса алмаза.
1.8. Методы изготрвления алмазных инструментов
1. Метод порошковой металлургии
Суть метода заключается в прессовании металлических порошков связки, смешанных с алмазным порошком с последующим спеканием, т.е. состав материала: шихта + алмазный порошок + связка (рис. 1.25).
На съемник со стержнем укладывается основание инструмента, на который устанавливается внутренняя обойма. В кольцевой зазор между внутренней и наружной обоймами засыпается алмазоносная шихта, на которую сверху устанавливается кольцевой пуансон. Предварительно части, соприкасающиеся с шихтой, смазываются графитовой смазкой.
Режим прессования: Руд = 1700 кг/см2 (1,7х102 Па).
Полученный брикет спекают в печи при температуре Т =(0,7-0,8)Tпл ооновного компонента связки
После спекания пресс-форму вторично устанавливают под пресс и производят допрессовку под давлением Руд=(0,6-1,5)102 Па что уплотняет алмазоносный слой, надежнее закрепляет зерна алмазов. Затем производят разборку пресс-формы и извлекают инструмент.
Рис. 1.25. Схема изготовления алмазного инструмента методом порошковой металлургии
Преимущества метода:
1) можно получить большую толщину режущей части инст
румента, что позволяет повысить срок его службы;
2) высокая износостойкость инструмента.
Недостаток: нельзя изготовить инструмент сложной формы.
2. Метод гальваностегии В основу метода положено явление электролиза (рис. 1.26).
Рис. 1.26. Схема изготовления алмазного инструмента методом гальваностегии.
В ванну заливается электролит никелевый NiCl2-6H20+HCl.
Корпус инструмента - катод (К). Анод (А) - пластина из материала связки - никеля. В электролит добавляется алмазный порошок 10 - 15 карат на 1 литр. Между К и А подают напряжение от источника постоянного тока.
Электролит перемешивается вращением корпуса инструмента. В процессе электролиза положительные ионы металла связки устремляются к катоду, и, увлекая частицы алмаза, оседают на поверхности инструмента, образуя алмазоносный слой.
Достоинство: можно получить инструмент сложной формы.
Недостатки: а) невозможно нарастить толщину алмазоносного слоя более 0,7 мм; б) следовательно, мала стойкость инструмента и его долговечность.
3. Таблеточный инструмент для тонкого шлифования Методом порошковой металлургии формуют алмазоносные цилиндрические таблетки: 0 = 6 -14 мм; t = 3 - 5 мм. Связка медная М21 с алмазом АСМ7/5 - АСМ 40/28. Концентрация алмаза до 25%.
Алмазные таблетки крепятся на корпус двумя способами (рис. 1.27)
Рис. 1.27. Примеры таблеточного инструмента для тонкого шлифования.
Первый способ - жесткий: таблетки наклеиваются на поверхность корпуса инструмента эпоксидной смолой.
Второй способ - эластичный: таблетки выставляются по шаблону в требуемом положении на поверхности инструмента, крепятся слоем пластилина, затем заливаются эпоксидной смолой. Преимущества второго способа перед первым:
а) можно использовать таблетки различной толщины t;
б) меньше времени на доводку инструмента (например,
сферы).
На производстве в основном применяют плоские круги прямого профиля (ПП) D= 100 300 мм, диски (D) D =100 - 400 мм.
1.9. Абразивный инструмент
Форма и структура абразивного инструмента представлены на рис. 1.28.
Рис. 1.28. Абразивный инструмент и его состав
Состав абразивного инструмента: абразивный порошок (20 - 60%) + связка (20 - 30 %) + поры (30 - 40 %).
Шихта для инструмента на керамической основе (глина огнеупорная, полевой шпат, песок). Ее помещают в форму, подвергают прессованию, сушке и последующему отжигу. Связка - бакелитовая, керамическая.
По твердости (т.е. по способности связки сопротивляться выкрашиванию абразивных зерен) абразивные круги различают:
• мягкие Ml, М2, МЗ;
• среднемягкие; СМ 1, СМ2 (применяются в оптическом производстве);
• средние CI, С2 (применяются в оптическом производстве);
• среднетвердыеСТЛ, СТ2 (применяются в оптическом производстве);
• твердые Tl, Т2 (применяются в оптическом производстве);
• весьма твердые ВТ (применяются в машиностроении);
• чрезвычайно-твердые Т(применяются в машиностроении). Твердость круга зависит от количества связки и пор: чем
больше пор, тем мягче круг, чем тверже оптическое стекло, тем мягче должен быть круг.
При правильном выборе инструмента по твердости и режиму шлифования абразивный инструмент работает с самозатачиванием (рис. 1.29).
Рис. 1.29. Схема сил, возникающих в связке инструмента и при обработке поверхности оптической детали
Процесс самозатачивания протекает непрерывно: как только абразивные зерна затупляются, перестают работать (возрастая, F превышает силы F) и вырывают их из связки, обнажая другие зерна, расположенные ниже. Выход новых зерен у мягких кругов осуществляется быстрее, что и необходимо для обработки твердых оптических стекол.
Контрольные вопросы.
1. Что такое производственный и технологический процессы? Дайте характеристику этим понятиям.
2. Какие требования к материалу и качеству изготовления указывают на чертежах оптических деталей - пластины, линзы, призмы?
3. Методы разделения абразивных материалов на группы (фракции).
4. Абразивные материалы - природные и синтетические маркировка и обозначение, методы разделения фракции.
5. Какие виды алмазного инструмента используются в технологий изготовления оптических деталей?
6. Методы изготовления алмазных инструментов.
7. Абразивный инструмент и принцип самозатачивания в процессе работы.
8. Какие виды инструмента применяют для шлифования оптических деталей свободным абразивом?
9. Методы разделительных операций стекла и используемые для этого режущие инструменты.
Вопросы для самостоятельной подготовки
1. Какие клеи применяют для склеивания оптических деталей? Какими свойствами должны обладать оптические клеи?
Дайте определение понятию «размерная цепь». Какие параметры включает размерная цепь линзы и призмы?
2. Какие типы покрытий имеются в оптическом производстве и каково их назначение?
3. В чем суть химических и физических способов нанесения покрытий? Поясните работу схем установок для нанесения покрытий.
4. Охарактеризуйте способы соединения оптических деталей: склеивание, глубокий оптический контакт, спекание, сварка.
Глава 2
ТЕХНОЛОГИЯ ФОРМООБРАЗОВАНИЯ ОПТИЧЕСКИХ ДЕТАЛЕЙ, ОСНАСТКА И ОБОРУДОВАНИЕ
2.1. Инструменты для шлифования оптических деталей свободным абразивом
Наиболее распространенные формы инструмента для шлифования оптических деталей свободным абразивом представлены на рис. 2.1.
Рис. 2.1. Формы инструментов шлифовальников: а - планшайба; б - гриб, в- чаша.
Материалы, используемые при изготовлении шлифовальников: чугун СЧ 18-36, ОЧ 28-48; сталь 10, сталь 20; латунь ЛС59-1
Диаметр планшайбы Дпл (рис. 2.1, а) зависит от диаметра обрабатываемой детали Ддет следующим образом:
1) Дпл =(1,1 - 1,25)Ддет, если инструмент находится снизу;
2) Дпл = (0,8 - 0,9)Ддег, если инструмент находится сверху На планшайбу подается абразивная суспензия (одна часть
абразива и пять частей воды), частицы абразива которой режут стекло. Наблюдается явление шаржирования, т.е. временное за крепление абразива на поверхностит планшайбы (рис. 2.2).
Рис. 2.2. Схема шлифования плоской детали свободным абразивом: а - общий вид; б - увеличенный фрагмент
Рабочая поверхность шлифовальников может быть сплошной, кольцевой, каблучной.
Гриб (рис. 2.1, б) применяется для шлифования вогнутых поверхностей, чаша (рис. 2.1, в) - для шлифования выпуклых поверхностей оптических деталей.
Материал для инструментов: ЛС59-1; ЛС63.
По сравнению с чугуном латунь имеет на 80 - 85% хуже показатели по износу и на 20% по сошлифоваемости.
Недостатком чугуна является его структурная неоднородность, неодинаковая твердость, что сказывается на качестве шлифования.
Для шлифования одной детали нужно несколько чаш и грибов с различным Rинстр. Обработка осуществляется в несколько
переходов, для которых характерно изменение Rинсгр и зернистости абразива.
Значение Rинстр определяется по величине Rдет, зернистости образива Мi, глубине слоя детали Fi (нарушаемого), снимаемого этим абразивом, толщине слоя абразива Аi, между рабочей поверхностью шлифовальника и обрабатываемой деталью (рис. 2.3).
Рис. 2.3. Схема шлифования детали
Значения величин Мi Fi, Аi, изменяются для каждого перехода.
2.2. Разделительные операции
Разделительные (заготовительные) операции - это операции отделения одной части куска стекла от другой.
Разделка стекла производится распиливанием, раскалыванием или разрезанием.
Распиливание стекла осуществляется алмазным инструментом, в виде отрезного круга (рис. 2.4).
Рис. 2.4. Распиливание стекла и формы инструмента: а - схема; б – сплошной отрезной круг; в - сегментный отрезной круг.
Инструмент АОК - алмазный отрезной круг - бывает:
а) сплошной, диаметром D от 200 - 400 мм, Н = 0,3 - 2 мм
б) сегментный, диаметром D от 200 - 600 мм, Н = 3 - 5мм
При использовании сегментных кругов улучшается подача
СОЖ в зону резания, вымываются отходы стекла из зоны резания Скорость резания V=20-80 м/мин, обороты инструмента
n = 1400 об/мин, подача Sинстр = 0,05 - 0,2 мм/об. Станки алмазные отрезные типа К - 8618.
Для распиливания более крупных кусков (А > 700 мм) применяется гибкий алмазный инструмент (рис. 2.5).
Рис. 2.5. Схема распиливания гибким алмазным инструментом.
Трос охватывает заготовку и поджимается к ней натяжными роликами. Все погружено в ванну с жидкостью. Режимы обработки по паспорту станка. Станок типа С-29.
Также применяется инструмент с алмазосодержащими кольцами (рис. 2.6).
Рис. 2.6. Схема инструмента с алмазосодержащими кольцами
Раскалывание стекол большой толщины осуществляется следующим образом.
Стекло кладут на резиновую прокладку, сверху давят на стекло пуансоном, в результате чего стекло, коснувшись острия призмы, раскалывается (рис. 2.7). Резиновая прокладка необходима, чтобы не было сколов на ребрах заготовки. Тонкие стекла, предварительно сделав надрез алмазным резцом, раскалывают вручную короткими, месильными ударами с обратной стороны листа. Раскалывание толстых стекол (свыше 8 мм) производят на гидравлических прессах. Процесс производительный, не требуется сложного оборудования и инструмента, но неточный (припуск 20 мм на сторону).
Разрезание стекол выполняют (рис. 2.8) алмазным стеклорезом, роликом-стеклорезом и нагретой электроспиралью.
|
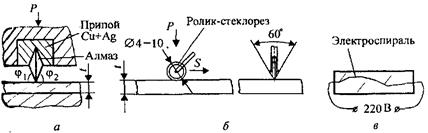
Также применяется инструмент с алмазосодержащими кол цами (рис. 2.6).
Алмазным стеклорезом (рис. 2.8, а), который имеет зерно натурального алмаза (0,02-0,2 карата) с углами ф, и ф2 режут только полированные стекла. Линию реза проводят один раз, держа резец перпендикулярно поверхности стекла с легким нажатием.
Роликом-стеклорезом (рис. 2.8, б) можно резать шлифованые и полированные стекла. Максимальная толщина стекла tmаx = 20 мм.
При разрезании стекла нагретой электроспиралью (рис. 2.8, в)
проволоку укладывают по линии реза, подается напряжение, спираль нагревается, затем ее убирают, а стекло охлаждают (холодным воздухом) и оно раскалывается.!
Если стекло плохо отожжено, то рез не получится по требуемой линии.
2.3. Формообразующие операции
К формообразующим операциям относятся:
а) получение отверстий;
б) округливание;
в) обработка поверхностей призм, линз.
В этих случаях изменяются не только размеры, но и форма заготовок.
Получение отверстий
Возможные способы исполнения отверстий в стекле представлены на рис. 2.9 - 2.11.
Сверление (рис. 2.9).
Данная операция может быть выполнена на сверлильном, токарном и вертикально-фрезерном станках. Для ее осуществления используются алмазный трубчатый инструмент, сверло с твердосплавной вставкой и трубчатый металлический инструмент.
Схематически алмазный трубчатый инструмент показан на (рис. 2.9, а).
При сверлении на сверлильных и вертикально-фрезерных станках используются алмазно-трубчатые сверла и кольца типа АК (диаметр 2 - 320 мм; точность 9-11-й квалитеты; шероховатость Ra = 1,25 мкм).
Режимы: S = 0,1 м/мин; n = 10000 об/мин; V> 15-20 м/с.
Смазывающая охлаждающая жидкость (СОЖ) - вода, содовый раствор, веретенное или машинное масло.
Дополнительная стеклянная деталь приклеивается к заготовке для исключения выколок на выходе сверла из заготовки.
Трубчатый металлический инструмент со свободным абразивом (рис. 2.9, б) применяют для сверления и высверливания заготовок диаметром от 3 до 150 мм.
Инструмент - из мягкой стали (ст. 20), латуни.
Подача ручная.
Зерна абразива, попав под инструмент, режут стекло, но они быстро истираются, необходимо неоднократно инструмент поднимать и подсыпать абразивный порошок.
Недостатки: производительность ниже в 5 -10 раз по сравнению алмазным трубчатым сверлом и точность хуже на 1 - 2 квалитета.
Достоинства: можно высверлить отверстия любого диаметра, в том числе размерами, на которые не выпускают алмазные инструменты.
Ультразвуковая прошивка (рис. 2.10).
Магнитострикционный генератор создает ультразвуковые колебания с частотой f=20 кГц. Эти колебания концентрируются концентратором и усиливаются. В результате этого рабочая головка колеблется с амплитудой Н=0,01-0,06 мм вдоль своей оси. Профиль рабочей головки различный.
Под инструмент подается абразивная суспензия, зерна углубляются в стекло из-за УЗ-колебаний. Периодически инструмент поднимается и подсыпается новая порция абразивной суспензии.
Резание и удаление частиц стекла из-за явления кавитации.
|
При перемещении инструмента происходит захлопывание пузырьков воздуха - образуется микрогидравлический удар и частицы абразива выкрашивают материал.
Преимущества:
- получение отверстий малых размеров, любой формы, как правило, отличной от круглой;
- получение глухих отверстий.
Округливание
Округливание - это обработка вспомогательных цилиндрических поверхностей. Выполняют на кругло-шлифовальных и бесцентрово-шлифовальных станках.
Схематически круглое шлифование показано на рис. 2.12.
Рис. 2.12. Схема круглого шлифования
Заготовка вращается равномерно (пз) и совершается возвратно-поступательное движение (Sпр). Скорость вращения круга (nинстр) обеспечивает скорость резания. В конце хода заготовки круг перемещается на Sn. Инструмент - абразив или алмазы. Круги типа АПП. Округляют заготовки =8-200 мм. Точность обработки9-10-й квалитеты, шероховатость 0,32. Оборудование ЗБ - 151.
Бесцентровочное шлифование.
Заготовку устанавливают на нож между двумя кругами: абразивным и вспомогательным резиновым (рис. 2.13).
Рис. 2.13. Схема бесцентровочного шлифования
Оба круга вращаются в одном направлении, но с разным скоростями, так как трение между абразивным кругом и заготовкой больше, вследствие этого заготовка вовлекается во вращение со скоростью Vз, близкой к V Р инстр.
Ось ведущего круга наклонена к оси рабочего круга под углом .
Скорость резания - Vp = 25 - 30 м/с; скорость ведущего круга - Ув = 0,2 - 0,3 м/с.
Сила сцепления заготовки с ведущим кругом больше, чем с абразивным, так как ведущий круг соединен с заготовкой вулканитовой связкой (каучуковой), а рабочий - керамической.
Продольная подача Sпр регулируется выбором и VB:
Sпр=КVBsin ,
где К - коэффициент проскальзывания, равный 0,97 - 0,99.
Скорость вращения заготовки определяется соотношение
Vз = KVBcos .
При О, близком к нулю, скорость V3 близка к VB.
Обработка поверхностей пластин и призм
Заготовки склеиваются в столбик, который зажимается усилием Р. Инструмент - фреза для обработки оптических деталей состоит из многих абразивных кругов, собранных под наклоном к оси инструмента. Фреза по программе обходит контур детали из начальной точки и возвращается в эту же точку (рис. 2.14).
![]() |
Рис. 2.14. Схема обработки поверхностей пластин
Обработка поверхностей призмы на агрегатном станке схематично представлена на рис. 2.15.
Заготовки крепятся в специальных гнездах с механическим зажимом (рис. 2.15).
Ротор-магазин совершает медленное вращение, по обеим сторонам ротора располагаются две пары инструмента в виде алмазного чашечного круга (АЧК). Первая пара (верхняя) снимает основную величину припуска, вторая - оставшуюся часть до получения требуемого размера по чертежу.
Инструмент для 1-го перехода - АЧК 125/100, инструмент для 2-го перехода - АЧК 63/50. Обработка ведется в СОЖ.
Обработка рабочих поверхностей призм происходит в следующей последовательности.
Призмы 1 собираются в столбик и зажимаются с помощью приспособления 5, как показано на рис. 2.16. Производится обработка одной рабочей поверхности инструментом 2 (АЧК 80/63 с применением СОЖ. Когда инструмент обработает одну грань призмы всего столбика, то столбик поворачивается и устанавливается другой гранью для обработки. Поворот осуществляется по эталонному многогранному зеркалу 4, с использованием коллиматора 3.
Инструмент для обработки рабочих граней призм может быть комбинированным (рис. 2.17).
Рис. 2.17. Схема комбинированного инструмента
Сначала обработка осуществляется кругом с большей зернистостью АЧК 100/80, а затем с более легким зерном АЧК 80/63.
Обработка поверхностей призмы на станке UFMS фирмы LOH схематично представлена на рис. 2.18.
![]() |
Рис. 2.18. Схема обработки поверхностей призм
На стол 3 приспособления устанавливается столбик призм с крышей 1, а над ним расположены несколько алмазных кругов 2, которые вращаются от своих приводов. Подача обеспечивается рабочим столом, за один проход обрабатываются три грани призмы. Оборудование универсальное, углы и
могут изменяться.
Шлифование плоских поверхностей заготовок пластин и призм зависит от формы детали и ее размеров. Заготовки до 100 мм наклеиваются на планшайбу и затем обрабатываются, более 100 мм - закрепляются в приспособлении (рис. 2.19).
![]() | |||
|
Наиболее распространенным является плоскошлифовальный станок типа ЗБ756 с магнитным столом.
Цикл обработки состоит из следующих переходов:
- установка на столе приспособлений с деталями или деталей;
- включение магнитного стола;
- отключение СОЖ, вращение алмазного круга (nинстр), вращение стола (nзаг);
- подведение инструмента до соприкосновения с заготовками;
- установка подачи S, длительности обработки;
- отведение инструмента после окончания обработки. Режимы: nинстр =350 об/мин.; V = 35 м/с; nзаг = 28 об/мин.;
,V = 0,2- 1,2 мм/мин.