DV = VdОТЛ [aVЖ(ТЖ.С – ТКР) + eV,З].
Объем твердого металла при переходе от этапа б к этапу в изменяется от нуля до Vвм. Усредненно определим усадку в твердом состоянии по формуле 0,5Vботл × aV,T (Tкр - Тт. с). Таким образом, объем плотного металла в отливке равен
VВМ = VВОТЛ [1 - aV,Ж(ТЖ.С – ТКР) - eV,З – 0.5aV,T × (TЗ – ТТ.С)].
Абсолютный объем усадочной раковины найдем по формуле
VВР = VВМ - VdОТЛ[1 - aV,Ж(ТКР – ТТ.С) – 1 + aV,Ж(ТЖ.С – ТКР) + eV,З + 0.5aV,T (TЗ – ТТ.С)] =
= VdОТЛ[aV,Ж(ТЖ.С – ТКР) + eV,З - 0.5aV,T(TЗ – ТТ.С)].
Относительный объем усадочной раковины будет равен
так как aV,T (Tкр - Тт. с) << 1. Относительный объем усадочной раковины равен сумме усадки в жидком состоянии, при затвердевании и в твердом состоянии. Эта сумма должна быть уменьшена на величину объемной усадки всей отливки в целом за период от начала до конца ее затвердевания:
VОТНР = aV, Ж(ТЖ.С – ТКР) + eV,З + 0.5aV,T(ТКР – ТТ.С) - aV,Т(ТКР – ТТ.С) = aV, Ж(ТЖ.С – ТКР) + eV,З - - 0.5aV,T(ТКР – ТТ.С).
Так как aV,т = 3aт, то
VОТНР = aV, Ж(ТЖ.С – ТКР) + eV,З – 1.5aT(ТКР – ТТ.С).
После полного охлаждения отливки до Т = Tк (этап г) объем отливки по наружным габаритам равен Vготл = Vвотл [1 - aV,T (Tт.с – Тк)], а объем плотного металла в отливке равен Vгм = Vвм [1 - aV,T (Tт.с – Тк)].
Объем усадочной раковины равен
VГР = VГОТЛ – VГМ = (VВОТЛ - VВМ)[1 - aV, T(ТТ. С – ТК)] = VВР[1 - aV, T(ТТ. С – ТК)].
Относительный объем раковины найдем по формуле
![]() |
т. е. относительный объем раковины при охлаждении затвердевшей отливки не изменяется. Абсолютный же объем раковины Vгр при этом уменьшается, так как вследствие усадки в твердом состоянии все размеры отливки, а следовательно, и размеры раковины уменьшаются.
Таким образом, для расчета относительного объема усадочной раковины применяют формулу, впервые полученную Ю. А. Нехендзи и Н. Г. Гиршовичем:
VОТНР = VР/VОТЛ = aV, Ж(ТЖ.С – ТКР) + eV,З - 1.5aT(ТКР – ТТ.С).
Рассмотрим влияние технологических факторов на величину Vротн
Как видно из полученной выше формулы, относительный объем усадочной раковины при прочих равных условиях тем больше, чем больше коэффициент объемной усадки в жидком состоянии и относительная объемная усадка при затвердевании сплава. В связи с этим при увеличении содержания углерода объем усадочной раковины в стальных отливках увеличивается, так как при этом увеличивается как aV,ж, так и eV,з. При одинаковых значениях aV,ж и eV,з объем усадочной раковины зависит от перегрева сплава в момент начала затвердевания отливки (Tж.с - Ткр). Очевидно, что (Tж.с - Ткр) будет тем больше, чем выше температура заливки (при Тзал = Ткр Тж.с - Ткр = 0), меньше теплопроводность сплава и выше теплоаккумулирующая способность материала формы. Поэтому с увеличением температуры заливки объем усадочной раковины при прочих равных условиях увеличивается. Так как легирующие компоненты понижают теплопроводность стали, отливки из легированной стали имеют больший объем усадочных раковин, чем из углеродистых. Особенно большой объем усадочных раковин (до 6 %) в отливках из высокомарганцовистой стали 110Г13Л. В отливках из углеродистой стали объем усадочных раковин составляет 3—3,5%. Так как с увеличением теплоаккумулирующей способности формы возрастает перепад температуры по сечению отливки, т. е. при заданной температуре заливки увеличивается разность (Tж.с - Ткр) величина aV,ж (Tж.с - Ткр) + eV,з при кокильном литье больше, чем при литье в песчаные формы. Однако объем усадочной раковины при этом может не изменяться, так как одновременно с увеличением (Tж.с - Ткр) повышается и (Tт.с - Ткр), т. е. усадка отливки по наружным габаритам. С увеличением приведенной толщины стенки отливки возрастает перепад температур (Tж.с - Ткр) и увеличивается не только абсолютный, но и относительный объем усадочной раковины.
Для уменьшения объема усадочных раковин в чугунных отливках необходимо в максимальной степени использовать возможность увеличения объема чугуна за счет графитизации в период его затвердевания. При этом процесс графитизации преимущественно должен протекать в жидком состоянии при жесткой литейной форме.
При затвердевании серого чугуна с пластинчатым графитом графитизация почти компенсирует усадку в жидком состоянии и при затвердевании, что практически исключает образование концентрированных усадочных раковин в относительно тонкостенных отливках.
Объем усадочных раковин при литье белого (ковкого) чугуна может быть определен по выведенной выше формуле.
Усадка в твердом состоянии будет уменьшать усадочную раковину тем в большей степени, чем больше коэффициент усадки eV,т и чем ниже средняя температура твердого металла к концу затвердевания отливки Tт.с. Именно это является одной из причин большей склонности к образованию усадочных раковин чугуна с шаровидным графитом по сравнению с чугуном с пластинчатым графитом. Графитизация в твердом состоянии чугуна с шаровидным графитом приводит не к усадке, а к расширению отливки в доперлитной области, что при достаточной податливости песчаной формы ведет к увеличению объема усадочной раковины.
В заключение рассмотрим влияние на объем усадочных дефектов продолжительности заливки формы сплавом. Приведенный выше вывод расчетной формулы справедлив при мгновенной заливке. При увеличении продолжительности заливки увеличивается доля сплава, затвердевшего в процессе заливки. Усадка этого сплава автоматически компенсируется поступающим из ковша в форму жидким сплавом. Поэтому с увеличением продолжительности заливки объем усадочной раковины уменьшается. Если форму заливать достаточно медленно, то усадочная раковина не образуется, так как усадка будет полностью компенсирована сплавом, поступающим из ковша. Это имеет место, если продолжительность заливки равна продолжительности затвердевания отливки.
3.3.2. ВЛИЯНИЕ ТЕХНОЛОГИЧЕСКИХ ФАКТОРОВ НА КОНФИГУРАЦИЮ И ПОЛОЖЕНИЕ УСАДОЧНОЙ РАКОВИНЫ В ОТЛИВКЕ
Рассмотрим факторы, определяющие конфигурацию и положение усадочной раковины в отливке. Для иллюстрации найдем
уравнение контура усадочной раковины цилиндрической высокой отливки (H0 >> R) при условии, что кинетика затвердевания описывается законом квадратного корня x = m , а суммарная относительная усадка равна eV (рис. 3.4).
Пусть в момент времени t толщина затвердевшей корки равна x, а сплав в отливке находится на высоте у. За время dt затвердевает слой dx = mdt/(2 ), объем которого равен
dV = 2pg(R - x)dx = 2pg(R - m )m/2
×dt.
![]() |
Объем жидкого сплава внутри цилиндра уменьшится на величину 2pg (R -


![]() |
При t = 0 y = H0 и z = 0
![]() |
ln y = 2eV× ln z + ln C; l n C = ln H0 - 2eV × l n R;
![]() |
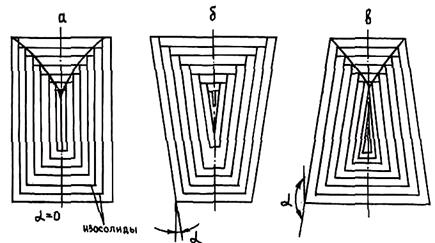
Рис. 3.5. Влияние угла наклона поверхности охлаждения отливки а на положение усадочной раковины
![]() |
В конце затвердевания при t = R2/m2 y = 0, т. е. усадочная раковина доходит до нижнего основания отливки. Текущая координата x = R - m

Для тонкостенных отливок в осевой зоне усадочная раковина имеет вид узкого осевого канала, через который фильтрация жидкого сплава затруднена. Поэтому под усадочной раковиной вдоль оси отливки всегда имеет место усадочная пористость. Для уменьшения глубины проникновения раковины необходимо, чтобы угол a между вертикалью и поверхностью охлаждения был как можно больше. Для определения положения усадочной раковины применяют метод построения изосолид, т. е. линий, отвечающих положению фронта затвердевания в данный момент времени. Из рис. 3.5 видно, что увеличение угла a приводит к перемещению усадочной раковины вверх. В случае обратной конусности отливки (a > p/2) в ее нижнем сечении образуется усадочная раковина (рис. 3.5, в). В общем случае усадочные раковины будут образовываться во всех изолированных узлах отливки, затвердевающих в последнюю очередь, которые обычно называют «теплыми» или «горячими» узлами. Их можно установить, строя изосолиды (рис.3.6).
Подавляющее большинство отливок отличается наличием закруглений, переходов и сочленений различного сечения. В этих местах может создаваться скопление металла, образующее термический узел, затвердевающий медленнее, чем соседние элементы отливки. В подобных узлах возникают усадочные раковины. Для выявления возможности образования усадочных раковин можно рекомендовать метод «вписанных окружностей». Если окружность, вписанную в термический узел, можно «выкатить» вверх через стенку отливки, то в нем усадочная раковина не образуется (рис. 3.7, а). В противоположном случае в узле образуется усадочная раковина (рис. 3.7, б).
Можно сформулировать общий принцип, которому должны удовлетворять конфигурация отливки и условия ее затвердевания, чтобы при установке сверху питающих прибылей в отливке отсутствовали усадочные раковины. Этот принцип был сформулирован В. Е. Грум-Гржимайло и носит название принципа направленного затвердевания. Он состоит в выполнении двух требований:
1) каждое вышележащее сечение отливки должно затвердевать позднее нижележащего;
2) сплав в прибыли должен затвердевать в последнюю очередь.
Если с нижнего сечения отливки направить вверх вертикальную ось х, то продолжительность затвердевания элементов отливки вдоль этой оси должна увеличиваться, т. е. dtзатв/dx > 0. Чем больше эта производная, тем больше направленность затвердевания и тем выше и более компактно располагается усадочная раковина. Для обеспечения направленного затвердевания необходимо уже на стадии конструирования отливки обеспечить непрерывное увеличение приведенной толщины стенки отливки в направлении снизу вверх к месту установки прибыли. Если это требование выполнить невозможно из конструкторских соображений, то необходимо ускорить затвердевание всех изолированных термических узлов отливки, отделенных от места установки прибыли более тонкостенными элементами, с помощью установки наружных и внутренних холодильников. Наружные холодильники представляют собой металлические вставки, оформляющие поверхности соответствующих элементов отливки (рис. 3.8). Чаще всего наружные холодильники выполняют из чугуна.
Внутренние холодильники представляют собой вставки (чаще всего в виде пружин) из отливаемого сплава, устанавливаемые в полость формы, оформляющей термические узлы отливки (рис. 3.9).
Можно строго рассчитать массу устанавливаемых холодильников и толщину наружных холодильников, выполнив на ЭВМ численный расчет продолжительности затвердевания термического узла и соседнего, более близкого к прибыли, узла отливки. Задача сводится к уменьшению продолжительности затвердевания термического узла в сравнении с продолжительностью затвердевания соседнего верхнего элемента отливки. Обычно толщин; наружных холодильников выбирают по соответствующим таблицам в зависимости от типа схемы (рис. 3.10) и параметров соседних с данным термическим узлом элементов отливки. Подробно технологические методы подбора и установки наружных и внутренних холодильников будут рассмотрены в курсе «Технология стального литья».
Для иллюстрации приведем упрощенный метод расчета массы внутренних холодильников для схемы, изображенной на рис. 3.11. Исходя из закона квадратного корня, определим продолжительность затвердевания вышерасположенного элемента: tэ = R2э /m2э где Rэ — приведенная толщина стенки элемента; тэ — коэффициент затвердевания элемента, равный
![]() |
В термическом узле с холодильником теплота при затвердевании отливки отводится в форму и частично расходуется на нагрев холодильника. Массу холодильника нужно определить так, чтобы не происходило его расплавления, т. е. максимальная температура его нагрева Т должна быть равна Тсол. Уравнение теплового баланса для термического узла с некоторым приближением можно записать следующим образом:
![]() |
где Сх и mx — удельная теплоемкость и масса холодильника; Vтв — масса затвердевшего сплава; Тх и Tж — температура холодильника и жидкого сплава. После интегрирования имеем
![]() |
Приняв mт.у = rVт.у = rжVж, после преобразований имеем
Примем t = R2э/m2э, т. е. с учетом значения mэ имеем
![]() |
С учетом этого
![]() |
Приняв r» rж, имеем
![]() |
Выполним расчет для углеродистой стали при dэ = 4 см, dт.у = 12 см, hт.у= 12 см, L = 258 Дж/г, Сж = 0,92 Дж/(г×К), Сх = 0,75 Дж/(г×К), Тзал = 1 597 °С, Тсол = 1 447 °С, Ткр = 1 472 °С:
RЭ = dЭ/2 = 2 см; RТ.У = dТ.У× hТ.У/[2(dТ.У + hТ.У)]=12×12/(2×24) = 3 см; mX/mТ.У = 0,37(1-2/3)» 0.12
Обычно масса холодильника не превышает 10—15 % от массы захолаживаемого узла отливки. В случае применения спиральных холодильников при стальном литье рекомендуют выбирать их массу в пределах 3—4 % от массы питаемого узла. При большей массе холодильники начинают резко ухудшать механические свойства стали в захолаживаемом узле. Поэтому если необходимая с точки зрения тепловых условий масса холодильников больше 3—4 %, то их применение следует комбинировать с использованием наружных холодильников.
На направленность затвердевания существенное влияние оказывают место подвода сплава в форму, температура заливки сплава и скорость заливки. В конечном счете они определяют знак и величину температурного градиента dT/dx по высоте отливки. Для усиления направленности затвердевания необходимо, чтобы имел место положительный температурный градиент по высоте отливки (dT/dx > 0). Этому способствует подвод сплава сверху, чаще всего под прибыль. Увеличение продолжительности заливки при подводе сверху увеличивает градиент температур, так как при этом температура в верхних частях отливки и в прибыли возрастает. Однако подвод сверху для высоких отливок (Hотл > 300 мм) и отливок, изготовляемых из склонных к окислению и вспениванию сплавов (алюминиевые и магниевые сплавы, высоколегированные стали), применять нельзя из-за возможного разрушения формы, окисления сплава, образования газовой пористости и окисных плен в отливках.
При подводе снизу формируется отрицательный температурный градиент по высоте отливки, что не способствует направленности затвердевания. При увеличении продолжительности заливки в этом случае охлаждение сплава в форме увеличивается номере его подъема, что приводит к ухудшению условий питания отливки из прибыли. Следует отметить, что при подводе снизу происходит разогрев нижних сечений отливки в процессе заливки формы, особенно в зоне действия питателей. В результате этого около питателей образуются локализованные термические узлы, объемная усадка которых не может быть компенсирована перетоком металла из соседних областей отливки, затвердевающих раньше.
Поэтому в зонах около питателей может возникать пористость или концентрированные усадочные раковины. Для их устранения следует применять рассредоточенный подвод сплава через несколько питателей, размещенных по периметру отливки. В этом случае количество металла, проходящего через каждый питатель, уменьшается, что снижает перегрев прилегающих к нему областей отливки.
Если отливка толстостенная, то вследствие свободной конвекции после заливки формы происходит выравнивание температур по высоте отливки, что уменьшает отрицательное влияние подвода снизу на направленность затвердевания. Действительно, находящийся после заливки в нижней части полости формы жидкий сплав имеет меньшую плотность, чем сплав в верхней части формы. В результате возникает конвективный поток, стремящийся выровнять температуры в объеме отливки. Однако в относительно тонких отливках для большинства машиностроительных деталей вследствие быстрого увеличения вязкости охлаждающегося сплава действие конвекции не проявляется и его можно не учитывать.
Для высоких отливок и отливок из сплавов, склонных к окислению, применяют подвод сплава на нескольких уровнях и через вертикально-щелевые литниковые системы (рис. 3.12). В этих случаях металл подается из стояка через соответствующий питатель или щель непосредственно на зеркало поднимающегося в форме сплава, что обеспечивает положительный температурный градиент в отливке. Методы расчета и конструирование таких литниковых систем рассматриваются в курсе «Технология литейного производства».
Очень часто в отливках образуются открытые усадочные дефекты, называемые утяжинами. Они возникают не только на верхних, но и на боковых поверхностях отливки. Рассмотрим механизм образования этих дефектов. Они появляются в тех местах отливки, где по тем или иным причинам скорость нарастания затвердевшей корки замедленна по сравнению с другими участками отливки. Рассмотрим отливку, содержащую внутренний угол (рис. 3.13).
Участок формы, оформляющий внутренний угол отливки, прогревается более интенсивно (тепло поступает в него через 2 поверхности), чем остальные поверхности. Поэтому рост твердой корки около него замедлен.
Пусть объем полости формы равен исходному объему жидкого сплава V0, плотность жидкого и твердого сплава соответственно rж и rтв, исходная масса жидкого сплава M = Vo×rmo. К моменту времени t в отливке выделится доля твердой фазы y = mтв/M. Объем твердой фазы равен Vтв = mтв/rтв = My/rтв. Фактический объем жидкого сплава в этот момент равен Vж = V0 – Vтв = M/ржо - My/rтв. Плотность жидкого сплава в этот момент будет равна
rЖ = MЖ/VЖ = (M - mТВ)/VЖ = M(1-y)/[1/rЖ0 - y/rТВ] = (1 - y) rТВrЖ0/(rТВ - rЖ0×y = (1 –
- y)rЖ0/[(rТВ - rЖ0)/rТВ + rЖ0(1 - y)/rТВ] = (1 - y)rЖ0/[eV + rЖ0(1 - y)/rТВ] = rЖ0/[eV(1 - y) +
+ rЖ0/rТВ] (3.3)
Из этой формулы видно, что с ростом доли затвердевшего сплава y плотность жидкого сплава внутри отливки уменьшается. Известно, что жидкость малосжимаема. Поэтому, в отличие от газов, малейшие изменения плотности приводят к резким изменениям давления жидкости. В процессе затвердевания жидкость испытывает деформацию всестороннего растяжения, так как вследствие усадки ее удельный объем увеличивается. Снижение плотности жидкости (даже очень малое) приводит к резкому падению давления жидкости внутри отливки Рж. В результате на затвердевшую корку сплава действует направленный внутрь перепад давлений ΔР = Ра - Рж.
Если затвердевшая корка достаточно толстая, то ее деформация незначительна. В этом случае падение давления жидкости рано или поздно приведет к разрыву сплошности жидкого сплава (при достижении предела прочности жидкости на разрыв) и образованию усадочной раковины. Разрыв сплошности жидкого сплава облегчается наличием в нем растворенных газов. Можно принять, что образование усадочной раковины произойдет в момент, когда давление в жидкости будет ниже значения, при котором количество растворенных в сплаве газов превысит их растворимость, т. е. при Рж < [Г]/К2, где [Г] — содержание газа, например водорода, в жидком сплаве, см3/100 г сплава; К — коэффициент в законе Сивертса.
В тех местах, где корка тонкая, например в области внутреннего угла (см. рис. 3.13), перепад давлений вдавливает корку внутрь и образуется утяжина. Очень часто при этом корка прорывается и в отливке возникает усадочная раковина.
3.3.3. УСАДОЧНАЯ ПОРИСТОСТЬ В ОТЛИВКАХ
Суммарная объемная усадка проявляет себя не только в виде усадочных раковин, но и в виде усадочной пористости. Выше было показано, что даже при чисто последовательном затвердевании в осевых зонах отливки возникает усадочная пористость. В отливках всегда имеет место пористость, более или менее неравномерно распределенная по объему отливки. Общий объем усадочных дефектов складывается из объема концентрированных раковин и суммарного объема рассредоточенной по отливке пористости, т. е. Vy.д = Vy.p + Vпop. В отливках, затвердевших преимущественно последовательно, превалируют усадочные раковины. При преимущественно объемном затвердевании основным видом усадочных дефектов является усадочная пористость. Известна связь характера усадочных дефектов с диаграммой состояния сплава (рис. 3.14).
Видно, что минимальный суммарный объем усадочных дефектов, как правило, имеют сплавы эвтектического состава. С увеличением ширины интервала затвердевания, т. е. ширины жидкотвердой зоны в отливке и доли объемного затвердевания, увеличивается доля усадочных дефектов в виде усадочных пор и уменьшается доля дефектов в виде усадочных раковин. В сплавах эвтектического состава, углеродистых сталях и чистых металлах усадочные дефекты проявляются главным образом в виде усадочных раковин. При литье объемно затвердевающих алюминиевых и магниевых сплавов объем концентрированных раковин очень мал и основным видом дефектов является усадочная пористость.
Рассмотрим механизм образования усадочной пористости, предложенный М. Флемингсом. В условиях объемной кристаллизации в изолированных объемах жидкого сплава между кристаллитами или в междендритных областях происходит уменьшение плотности сплава, и снижение его давления аналогично рассмотренному выше случаю для сплава внутри затвердевающей отливки. Если эти объемы изолированы, т. е. не связаны с соседними, то процессы компенсации усадки за счет переноса жидкого сплава отсутствуют. В этом случае образуются поры за счет разрыва сплошности жидкого сплава.
Если же в жидкотвердой зоне имеются междендритные или межзеренные капилляры, то под действием перепада давлений происходит фильтрационный перенос жидкости через капилляры из прибыли или из областей отливки, имеющих запас жидкого сплава. Процесс компенсации усадки за счет направленного массопереноса жидкого сплава называется питанием отливки, а объем жидкого сплава, необходимый для компенсации усадки, называется дефицитом питания. Питание отливки за счет фильтрации жидкости через междендритные и межзеренные капилляры называется фильтрационным питанием. Перепад давлений при фильтрационном питании создается за счет действия внешнего, гидростатического и отрицательного (меньше атмосферного) давления в объемах жидкости при ее кристаллизации. Процесс уменьшения давления жидкости при ее кристаллизации описан выше (п.3.3.2). Капиллярные силы, если не произошло разрыва сплошности жидкости, при наличии запаса жидкого сплава в прибыли отсутствуют.
![]() |
Для описания гидродинамики фильтрации обычно используют закон Дарси
где v — вектор скорости фильтрации, отнесенной ко всему поперечному сечению пористой среды; m — динамический коэффициент вязкости сплава; k— коэффициент проницаемости среды, м2; P — градиент давления.
Для одномерной фильтрации уравнение Дарси имеет вид
![]() |
Выведем уравнение неразрывности потока при фильтрационном питании отливки. Для того чтобы плотность жидкости при кристаллизации не изменялась, необходимо за время t за счет фильтрации подать в заданный объем Vo некоторое количество жидкого сплава m ф, который бы компенсировал объемную усадку. Для плотности жидкости rж в этом случае можно написать выражение
Величину mф следует выбрать такой, чтобы в ходе всего процесса соблюдалось условие rж = rжo Сократив rж и rжo получаем
; rТВ - rЖ0 × y = rТВ - rТВ × y + mФrТВ/M
;
; eVy = mФ/M
Массовый поток жидкости в объем V = M/rжо через ограничивающую его поверхность S в единицу времени равен, как известно из теории поля,
где v — вектор скорости как функция координат точек поверхности. Продифференцируем полученное выше уравнение по времени:
Как известно из теории поля, — дивергенция вектора скорости. В итоге получаем уравнение неразрывности
(3.6)
Так как , где vx, vy, vz — проекции скорости на соответствующие оси, то
(3.7)
Если это условие не выполняется, т. е. фильтрация недостаточна для полной компенсации усадки, то плотность жидкости будет уменьшаться.
Однако в силу резкого уменьшения давления жидкости при малейшем уменьшении ее плотности изменением плотности можно пренебречь вплоть до разрыва сплошности жидкости и образования поры. Поэтому полученное выше уравнение неразрывности, выведенное впервые Г. Ф. Баландиным, можно применять для описания любого режима фильтрации.
Математическая модель фильтрационного питания отливки должна включать в себя краевую задачу затвердевания отливки, позволяющую определить долю твердой фазы y как функцию времени и координат, уравнение Дарси и уравнение непрерывности. Кроме того, должна быть задана функция, связывающая долю твердой фазы y с температурой в интервале ликвидус — солидус. Эксперименты показывают, что эту зависимость можно аппроксимировать формулой
y = A(TЛИКВ - T)/(TСОЛ - В)
где А и В — эмпирические коэффициенты.
Условие образования поры можно записать так: пора образуется, если давление в фильтрационном потоке в данной точке будет меньше величины Pt;p=^[ti]2/kp, где [Н]—содержание водорода в сплаве, т. е. Р а^ Рцр. Величина пористости в жидко-твердой зоне равна
П = VПОР/VЗ × 100% = eV(1 - yКР) × 100%
где yкр — доля твердой фазы, при которой выполнено указанное условие. Данное значение пористости отнесено к жидкотвердой зоне. Если пористость отнести ко всей отливке, то она равна
где Vз/Vотл — отношение объема жидкотвердой зоны в момент образования пористости к объему отливки.
В первом приближении коэффициент проницаемости двухфазной зоны отливки можно выразить формулой
k = d2(1 - y)3(150y2)
где d — эффективный диаметр кристаллита. Так как с увеличением доли твердой фазы y k убывает, то в процессе затвердевания фильтрационный поток, естественно, уменьшается. В ходе затвердевания эффективный диаметр кристаллита увеличивается. С некоторым приближением, считая кристаллиты сферическими, при заданном их числе в единице объема NV можно получить формулу для вычисления d. Число кристаллитов в двухфазной зоне (ее ширина определяется в момент снятия перегрева в центре отливки) равно N k = NV×Nз. Считая, что все они зародились в один момент времени, можно записать уравнение
rТВpd3/6 = yVЗrЖ-Т/Nk
![]() |
Приняв rтв» rж-т, получаем
С учетом этого получаем
![]() |
Методика численной реализации описанных физической и математической моделей образования усадочной пористости рассматривается на практических занятиях.
Не приводя промежуточных преобразований, выполним анализ формулы (3.9), связывающей пористость с технологическими факторами. Она получена для следующих условий. Отливка представляет собой плиту, высота которой значительно больше толщины (H0 >> 2R). Положение фронта солидуса определялось уравнением xc = R - . Распределение температур по сечению двухфазной зоны принято линейным. Расчетная схема приведена на рис. 3.15.
Предлагаем студентам вывести формулу (3.9) на индивидуальных занятиях под руководством преподавателя.
где П0 — пористость, отнесенная ко всему объему отливки; Y = xc (t = tл)/R — относительная толщина затвердевшей корки в момент снятия перегрева в центре отливки.
Очевидно, что с увеличением Y, т. е. при более последовательном затвердевании и меньшей ширине жидкотвердой зоны, пористость уменьшается. Поэтому все мероприятия, приводящие к уменьшению ширины жидкотвердой зоны, снижают уровень пористости отливок. Возрастание скорости затвердевания (увеличение коэффициента m) приводит к росту пористости отливки. Однако увеличение m приводит к росту Y. Поэтому влияние m может быть неоднозначным. Измельчение кристаллической структуры, если это не сопряжено с принятием соответствующих мер, приводит к росту пористости (увеличение Nз).
Важным технологическим фактором является повышение давления на расплав Р0, приводящее к снижению в нем содержания водорода. С уменьшением толщины стенки отливки R усложняются условия фильтрационного питания и увеличивается пористость отливок. Очевидно, что по мере удаления от прибыли (увеличение у) пористость увеличивается.
В реальных условиях картина фильтрационного питания значительно сложнее. Фильтрационный поток сплава развивается раньше, чем в осевой части отливки будет снят перегрев. До этого момента в центральной зоне отливки имеется жидкий сплав, который через междендритные каналы может фильтроваться в направлении фронта солидуса под действием перепада давлений, природа которого описана выше. При этом процесс кристаллизации сплава сопровождается движением в сторону фронта кристаллизации междендритной жидкости. Условия питания на этой стадии облегчены наличием в центре отливки жидкого сплава. Они существенно затрудняются при смыкании фронтов ликвидуса в центре отливки. При этом питающий расплав может поступать только из прибыли, т. е. длина фильтрационного пути значительно увеличивается.
Наиболее благоприятные условия создаются при заполнении формы и питании отливки из тигля через металлопровод, как это осуществляется при литье вакуумным всасыванием, под низким давлением и с противодавлением. При этих методах в верхней части металлопровода имеется достаточное количество жидкого расплава и, кроме того, есть возможность значительно повысить перепад давлений на расплав. Как показали исследования, проведенные при литье с противодавлением на алюминиевых сплавах, при обычных условиях в отливках практически отсутствовала усадочная раковина, но наблюдалась значительная пористость. При увеличении перепада давлений до 0,3 МПа начинает выявляться концентрированная усадочная раковина и уменьшается пористость. При перепаде давлений 0,5 МПа пористость исчезает практически полностью. Дальнейшее повышение давления до 2,5 МПа не изменило характера усадочных дефектов, но несколько сместило усадочную раковину вверх. Следует отметить, что при значительном (до 2,5 МПа) повышении всесторонне действующего газового давления получаются практически бездефектные отливки, но боковые и верхние поверхности вдавливаются внутрь, что искажает конфигурацию отливки.
Фильтрационному режиму питания предшествует режим так называемого суспензионного питания. Известно, что перегретые жидкие сплавы подчиняются реологическому закону ньютоновской жидкости и обладают неограниченной способностью к течению. Именно поэтому не возникает проблем с компенсацией объемной усадки в жидком состоянии. Как было показано в разд. 1, это относится к сплавам при температурах ниже температуры ликвидуса, доля твердой фазы в которых не превышает 8—10%. При большем количестве твердой фазы изменяется реологическая природа сплавов и для их течения требуется выполнение условия t > ts, где t — касательные напряжения, создаваемые внешними силами; tS — предельное касательное напряжение сдвига для сплава. Так как с увеличением доли твердой фазы в расплаве с понижением его температуры ts увеличивается, рано или поздно компенсация усадки за счет перемещения металлической суспензии как единого целого прекратится. При этом произойдет образование жесткой структуры суспензии, которая при дальнейшем охлаждении отливки ведет себя как капиллярно-пористое тело, и компенсация усадки осуществляется рассмотренным выше фильтрационным путем.
Нарушение условия t > ts происходит при некотором критическом содержании твердой фазы yкр, которое зависит от природы сплава и давления, прилагаемого к отливке в процессе ее формирования. Температура сплава, соответствующая доле твердой фазы yкр, называется температурой нулевой жидкотекучести.
Рис. 3. 16 Зависимость t, tS (a) и v (б) от расстояния r до центра отливки
На рис. 3.16 показано распределение величины предельного касательного напряжения сдвига ts и касательного напряжения t, создаваемого активными силами, внутри жидкотвердой зоны в центре отливки (0 £ r < rс, где r с — радиальная координата фронта солидуса). Так как с увеличением r уменьшается температура сплава и увеличивается доля твердой фазы y, то величина ts по мере удаления от оси отливки резко возрастает. Видно, что при rкр1 > r > rкр t > ts. Поэтому в этой зоне dv/dx ¹ 0. В области rкр1 < r <rс может осуществляться только фильтрационное питание. На рис. 3.16, б показано распределение скорости суспензионного питания. В зоне rкр1 < r < R имеет место стержневое течение (dv/dx = 0).
При затвердевании фронт солидуса перемещается к центру отливки, а кривая ts смещается вверх и влево. В некоторый момент кривая ts займет положение tS2 (рис. 3.16, a), a фронт солидуса — rс2. При этом t < ts для всей жидкотвердой зоны (0 < r <rс2). Поэтому с данного момента времени прекратится суспензионное питание.
Очевидно, что за счет этапа суспензионного питания уменьшается ширина зоны фильтрационного питания, так как rс2 < rс(t = tл}, где t л — время снятия перегрева в центре отливки. Подставив в формулу (3.10) вместо 1 – У = 1 - xc(t = tл}/ R величину rс2/R, получим выражение для определения пористости отливки
Так как rс2 < rс(t = tл}, то очевидно, что за счет суспензионного питания пористость уменьшается.
Влияние суспензионного питания на процесс компенсации объемных усадочных дефектов для разных сплавов и условий различно. Например, структурирование алюминиевых сплавов происходит при температурах, очень близких к температуре ликвидуса. Поэтому роль суспензионного питания при формировании отливок из этих сплавов очень незначительна. Учет суспензионного питания связан с математическим описанием движения жидкотвердой фазы как B-тела, закономерности которого рассмотрены в курсе «Основы литейной гидравлики и теплофизики».
Следует отметить, что с ростом прилагаемого к отливке перепада давлений Р0 влияние суспензионного питания на уменьшение пористости отливок увеличивается.
Анализу математической модели совместного действия суспензионного и фильтрационного питания должно быть посвящено несколько практических занятий.
3.3.4. МЕТОДЫ БОРЬБЫ С ОБЪЕМНЫМИ УСАДОЧНЫМИ ДЕФЕКТАМИ. РАСЧЕТ И КОНСТРУИРОВАНИЕ ПРИБЫЛЕЙ
Практические меры борьбы с усадочными дефектами в отливках основываются на изложенных выше теоретических положениях. Основными направлениями в устранении
усадочных дефектов являются: установка над каждым термическим узлом прибыли и оптимизация тепловых и гидродинамических условий питания отливки из прибыли. При этом конфигурация отливки и тепловые условия ее затвердевания должны отвечать условиям принципа направленного к прибыли затвердевания. Прибыль — дополнительный объем сплава, имеющий соответствующие размеры и конфигурацию, в который в процессе питания отливки выводятся усадочные дефекты. Расположена прибыль на термическом узле отливки. После охлаждения отливки прибыль удаляется (отрезается или отламывается) и передается на переплавку. Так как установка прибылей увеличивает расход сплава на изготовление отливки, нужно применять меры, направленные на повышение эффективности ее работы и снижение объема. Эффективность использования жидкого сплава характеризуется выходом
годного (ВГ). Он равен отношению черновой массы отливки Мотлк массе жидкого сплава, залитого в форму, Мж:
ВГ = MОТЛ × 100%/MЖ
При этом Мж = Мотл + Мл.с + Мпр, где Мл.с — масса литниковой системы; Мпр — масса прибылей.
Эффективность работы прибылей зависит от их расположения, размеров и конфигурации, тепловых и гидродинамических условий.
По направлению питания прибыли разделяются на прямые, местные и боковые. Прямые прибыли располагаются непосредственно над всем питаемым узлом (рис. 3.17). Так как сплав, компенсирующий усадку, подается при этом в отливку из прибыли по кратчайшему пути, то условия питания наиболее благоприятны. Недостатком прямых прибылей, если они устанавливаются, например, по всему периметру кольцевой отливки, является большой расход металла на прибыли. С целью экономии металла можно устанавливать вместо одной сплошной прибыли несколько местных прибылей. Как видно из построенных изосолид (рис. 3.18), местные прибыли, если их установить друг от друга на некотором максимально допустимом расстоянии, обеспечивают хорошее питание отливки.
При применении местных прибылей прямое питание получают только части отливки, находящиеся непосредственно под прибылями (рис. 3.18). Части, находящиеся между прибылями, получают уже не прямое питание, а боковое. При этом различного рода включения не могут всплыть в прибыль. Поэтому на верхней поверхности необходимо предусматривать повышенные припуски на механическую обработку. Обычно суммарная длина местных секторных прибылей на отливках типа колес (рис. 3.19) составляет не менее 1/3и не более 2/3 от периметра отливки.
Местные прибыли обеспечивают питание примыкающих к ним участков отливки на определенную длину, называемую зоной действия прибыли. Зоны действия прибылей определяют на основании эмпирических данных в зависимости от толщины питаемого узла (рис. 3.20). Например, для прибылей, установленных по схеме рис. 3.20, а, зона действия прибыли для сплава латуни равна А = 4Т, для силуминов А = 3Т. Вследствие влияния концевого эффекта (нарастание твердой корки на торцевой поверхности отливки) зона действия прибыли, установленной у края отливки (рис. 3.20, б), увеличивается и равна для латуни А = 5Т, а для силумина А = 6,5Т. Таким образом, расстояние между местными прибылями l не должно превышать удвоенную величину зоны действия прибыли, т. е. l £ 2А. Если l > 2A, то в зависимости от характера затвердевания сплава за пределами зоны влияния прибылей в отливках будут образовываться усадочные дефекты в виде раковин или усадочной пористости.
Для протяженных отливок с большим отношением длины к толщине или ширине целесообразно применять боковые прибыли (рис. 3.21). Боковые прибыли применяют также при изготовлении отливок из сплавов, плохо обрабатывающихся резанием (сталь 110Г13Л, ковкий чугун и т. п.).
Преимущества боковых прибылей по сравнению с верхними сводятся к возможности питания меньшими по объему прибылями протяженных отливок, снижения трудоемкости удаления прибылей от отливок (их можно отламывать или отрезать при значительно меньшей площади резки), уменьшения трудоемкости механической обработки подприбыльных участков отливки и т. д. Место соединения боковой прибыли с отливкой называется шейкой прибыли. Следует отметить, что шейка прибыли может иметь приведенную толщину стенки, существенно меньшую, чем у отливки. Это объясняется влиянием прогрева формы около шейки прибыли протекающим через нее металлом, так как заливка в данных случаях осуществляется через прибыль (см. рис. 3.21). К моменту окончания заливки температура формы около шейки прибыли наибольшая и убывает по мере удаления от прибыли, что способствует направленности затвердевания.
Иногда боковые прибыли устанавливают на термических узлах отливки, расположенных на разной высоте. Такие прибыли называют потайными (рис. 3.22).
Для того чтобы прибыль работала так, как показано на рис. 3.22, необходимо обеспечить в ней некоторый баланс давления жидкого металла. Потайные прибыли являются закрытыми. Поэтому с момента образования на их поверхностях достаточно прочной корки затвердевшего металла жидкий расплав отсекается от внешнего атмосферного давления. Вследствие действия атмосферного давления со стороны открытой прибыли и увеличивающегося к низу отливки гидростатического давления, равного, например, для нижней прибыли rgHн, перепад давлении будет направлен вверх, т. е. он будет обеспечивать перенос металла в прибыль, а не из прибыли в отливку. В этом случае установка потайных прибылей приведет к увеличению объема верхней прибыли, так как она должна компенсировать дополнительно усадку сплава в этой прибыли. Прибыли начнут действовать только после затвердевания сечений В — В и А — А.
Для улучшения действия прибылей в них устанавливают газопроницаемые стерженьки, передающие внутрь прибыли атмосферное давление (см. рис. 3.22). Однако гидростатическое давление rgHн и rgHс. в этом случае все равно оказывается некомпенсированным. Для обеспечения нужного баланса давлений целесообразно создать в прибылях повышенное газовое давление, равное для нижней и средней прибыли соответственно Ра + rgHн и Pa. + rgHс. В этом случае все прибыли с самого начала будут действовать независимо: каждая будет питать свой узел.
По конфигурации различают шаровые или полушаровые, цилиндрические, конусные, овальные, прямоугольные прибыли (рис. 3.23).
С точки зрения тепловых условий работы конфигурация прибыли должна обеспечить при данном ее объеме минимальную поверхность охлаждения. Известно, что этому условию удовлетворяет шар. Однако такие прибыли сложно выполнить в форме, поэтому наиболее широко применяют полушаровые закрытые прибыли или конические открытые прибыли. Часто используют прибыли, имеющие овальное горизонтальное сечение. Следует заметить, что при конструировании прибылей их конфигурация всегда увязывается с конфигурацией питаемого узла. Более детально вопросы конструирования прибылей изучаются в технологических курсах.
Рассмотрим основные принципы расчета прибылей. Прежде всего, прибыль должна иметь запас сплава, обеспечивающий компенсацию объемной усадки отливки и самой прибыли. Так как в процессе формирования отливки на стенках прибыли происходит образование затвердевшей корки, то объем прибыли равен
VПР = VУС.Р + VЗ.К
VУС.Р = eV(VОТЛ + VПР)
где Vyc.p — объем усадочной раковины; Vз.к — объем затвердевшего сплава в прибыли. Объем затвердевшего металла зависит от тепловых условий работы прибыли и гидродинамических условий, определяющих скорость опускания сплава в прибыли. Чем больше интенсивность теплоотвода от прибыли и чем меньше скорость опускания уровня сплава в ней, тем больше Vз.к. Как следует из полученного в предыдущем разделе уравнения неразрывности потока питающего жидкого сплава, скорость опускания сплава в прибыли непосредственно связана со скоростью выделения в расплаве отливки твердой фазы dy/dt. Чем больше dy/dt, тем с большей скоростью может опускаться сплав в прибыли.
Однако эта потенциальная возможность в зависимости от характера затвердевания используется в разной степени. При последовательном затвердевании, за исключением питания осевых участков отливки, жидкий расплав полностью и практически мгновенно компенсирует появившийся в отливке дефицит питания. При объемном затвердевании в условиях фильтрационного и суспензионного питания скорость питающего потока существенно зависит от прилагаемого к расплаву давления. Если давление недостаточно велико, то, несмотря на наличие дефицита питания, расплав из прибыли не будет израсходован. При этом в отливке образуется большая усадочная пористость.
Коэффициент полезного использования металла в прибыли — b = Vyc.p/Vпp. Здесь, строго говоря, в величину Vyc.p следует включать весь дефицит питания, а не только собственно объем усадочной раковины. Величина b зависит от конфигурации прибыли, прилагаемого к расплаву давления и тепловых условий работы прибыли. Для обычных открытых прибылей b = 0,1, для закрытых прибылей b = 0,11 — 0,15, для прибылей с газовым давлением b = 0,13 ¸ 0,2. Применение подогрева сплава в прибылях позволяет значительно повысить b и снизить расход металла на прибыли. Если принять, что коэффициент b известен, то можно рассчитать объем прибыли по простой формуле, впервые полученной И. Пржибылом:
VУС.Р = eV(VОТЛ + VПР)
VУС.Р = bVПР
bVПР = eVVОТЛ + eVVПР
Отсюда VПР(b - eV) = eVVОТЛ или
VПР=eVVОТЛ/(b-eV)
Здесь Vотл — объем узла отливки, питаемого данной прибылью. Высота прибыли принимается равной ее диаметру или несколько больше.
Классический метод расчета прибылей сводится к определению глубины проникновения усадочной раковины в системе отливка — прибыль. Высоту прибыли устанавливают, исходя из обеспечения полного расположения усадочной раковины в прибыли с некоторым запасом.
В основе математического расчета прибылей на ЭВМ лежит балансный принцип расхода сплава из прибыли на питание и затвердевание на ее стенках (см. гл. 6.3 и 6.4) при определении контура усадочной раковины. Кроме балансного уравнения модель включает дифференциальные уравнения, описывающие кинетику затвердевания сплава в отливке и прибыли. Навыки машинного расчета прибылей студент должен получить на практических занятиях.
Приведенная формула (3.12) получена для плоской отливки толщиной 2Ro при следующих допущениях:
1) фронт солидуса в отливке продвигается по закону, а В Прибыли
2) толщина прибыли равна 2Rп > 2R0;
3) вся усадка приведена к температуре солидуса и включает усадку в жидком состоянии и при затвердевании.
где A—коэффициент запаса (обычно k = 1,5 ¸ 3). Как правило, отношение приведенных размеров прибыли и отливки принимают в пределах Rп/R0 = 1,15 ¸ 1,5.
Выполним расчет высоты прибыли для стальной отливки: Rп/R0 = 1,25; R0 = 15 см; Rп = 18,75 см; eV = 0,06; высота отливки H0 = 40 см; m0 = 0,085 cм/с1/2; mп = 0,060 cм/с1/2.
Для того чтобы уменьшить mп по сравнению с m 0, необходимо применить подвод сплава в прибыль, использовать смесь с меньшим коэффициентом аккумуляции тепла, а для крупных отливок осуществить доливку металла в прибыль из ковша. В условиях рассмотренного примера при mп = m0 = 0,085 высота прибыли равна Hпр = 2×0,11×95 = 21 см. Видно, что уменьшение интенсивности затвердевания сплава в прибыли приводит к уменьшению объема прибыли.
Существенного уменьшения затвердевшего в прибыли сплава, а следовательно, и необходимого ее объема можно добиться, применяя обогрев прибылей экзотермическими смесями. Из этих смесей изготовляют стаканы или втулки, которые устанавливают в прибыльные части полости формы (рис. 3.24).
Существуют различные по составу экзотермические смеси. Экзотермическая реакция, сопровождающаяся большим выделением тепла, представляет собой реакцию восстановления окиси железа алюминием (алюмотермия) или кремнием (силикотермия):
Fе2О3 + 2Аl = Аl2O3 + 2Fe + Q1,
2Fе2О3 + 3Si = 3SiO2 + 4Fe + Q2.
Кроме алюминиевого порошка, ферросилиция и окалины смесь содержит связующее для придания ей прочности во влажном состоянии и после сушки, а также древесные опилки, гипс, молотый шамот, глину для обеспечения газопроницаемости смеси и регулирования интенсивности экзотермической реакции.
Расчет экзотермических прибылей сводится к определению номера нормализованной экзотермической оболочки для оформления прибыли. Подбор оболочек осуществляют по массе прибыли mпр. Массу прибыли находят по специально разработанным номограммам. Принципиально ее можно определить по приведенной выше формуле И. Пржибыла, приняв b = 0,2 ¸ 0,25, или а использованием полученной выше формулы для расчета высоты прибыли, приняв константу затвердевания в 1,5—2 раза меньшей по сравнению с обычной песчаной формой. По массе прибыли находят размеры экзотермических оболочек по нормализованным таблицам (см., например, рис. 3.24).
Выше было сказано о большой роли в повышении эффективности работы прибылей и их экономичности перепада давлений, действующего на кристаллизующийся расплав. Так, П. И. Ямшановьш были предложены прибыли с повышенным газовым давлением, создаваемым диссоциацией при высоких температурах мела, карбоната магния или цинка:
СаСО3 = СаО + СO2 при Т ³ 825°С;
MgCO3 = MgO + CO2 при Т ³ 350°С;
ZnCO3 = ZnO + CO2 при Т ³ 300°С.
Определенная масса данных веществ помещается в специальный патрон, устанавливаемый внутрь закрытой прибыли (рис. 3.25). Оболочки и крышки патронов изготавливают уплотнением в металлических ящиках смесей, состоящих из глины, молотого шамота и древесных опилок, добавляемых для повышения газопроницаемости оболочки. Оболочки сушат при 100 - 110 0C и обжигают при 350 °С. Главное требование к оболочке сводится к тому, что ее толщина должна обеспечивать прогрев помещенного в нее наполнителя до температуры диссоциации не раньше, чем на стенках прибыли вырастет достаточно прочная корка затвердевшего сплава, способная выдержать повышенное давление.
Параметры прибыли, патрона и массу заряда определяют по эмпирически разработанным номограммам. Массу прибыли можно определить, например, по формуле И. Пржибыла, приняв в ней b = 0,13 ¸ 0,20.
В зависимости от массы прибыли и создаваемого давления по номограмме, приведенной на рис. 3.26, определяют массу мела, помещенного в патрон.
Толщину стенки патрона и его размеры определяют по специальным номограммам. Применение прибылей газового давления позволяет не только повысить выход годного, но и существенно снизить пористость отливок.
Детальное изучение методов расчета и конструирование прибылей для отливок из различных сплавов предусмотрено в соответствующих технологических курсах. Приближенные аналитические и эмпирические формулы для расчета прибылей получены А. А. Рыжиковым, Б. Б. Гуляевым, Ф. Ф. Василевским, Н. Бишопом и В. Джонсоном, Р. Намюром и др. Главной особенностью этих методов является их ориентация на последовательно затвердевающие сплавы и усадочные дефекты, проявляющиеся главным образом в виде усадочной раковины. Их применение к объемно затвердевающим сплавам неправомерно, так как усадочная раковина в этих случаях очень мала по объему по сравнению с объемом пор.
Методику расчета прибылей при объемном затвердевании сплава можно построить, исходя из следующих принципов:
1) прибыль должна быть достаточно теплоизолирована (например, при кокильном литье стенки прибыльных частей оклеиваются листовым асбестом или покрываются специальной краской). При этом должно выполняться условие: продолжительность снятия перегрева в центре прибыли должна быть не меньше продолжительности затвердевания отливки;
2) объем прибыли должен быть достаточным для компенсации объемной усадки отливки и прибыли. Его можно найти по формуле и. Пржибыла, приняв, в ней b = 0,2 ¸ 0,25;
3) высота прибыли и прилагаемое к сплаву в прибыли давление Р0должны обеспечить фильтрационное питание отливки, гарантирующее заданный уровень пористости в ней. Давление (Р0 + rgHп), обеспечивающее заданное значение пористости, в первом приближении можно найти с использованием формул, полученных в разд. 3.
В заключение рассмотрим прибыли с облегченным отделением от отливок (рис. 3.27).
Между прибылью и питаемым узлом устанавливают перегородку в виде керамической пластины. Важнейшим требованием является совпадение оси отверстия в перегородке с термическими центрами прибыли и отливки. При нарушении этого требования в отливке образуется усадочная раковина. Параметры перегородки и размеры отверстия выбирают таким образом, чтобы она быстро прогревалась до температур, исключающих образование на ее поверхностях затвердевшего металла. Обычно диаметр прибыли определяют по формуле
где dвп — диаметр окружности, вписанной в термический узел питаемой отливки, дм; Дпр — диам