ЗАЛЕЖНО ВІД ТЕХНОЛОГІЇ ТА ВИДУ МАТЕРІАЛУ
Структура й властивості тонких плівок визначаються наступними параметрами:
1) температурно-часовими режимами нагрівання та випару;
2) об’ємом робочої камери й інтенсивністю розпилювання (щільність пари);
3) температурою стінок робочої камери;
4) температурою підкладки, на якій здійснюється напилювання;
5) тиском пари в робочому об’ємі.
6.1. Вибір температурно–часових режимів
Вибір температурно–часових режимів залежить від характеру плавлення вихідного матеріалу. Всі матеріали можна розділити умовно на 2 групи:
I група - матеріали, що плавляться при постійній температурі плавлення;
II група – матеріали, що плавляться при змінній температурі плавлення.
До I групи матеріалів, що розплавлюються при постійній температурі, відносяться однокомпонентні матеріали й евтектичні сполуки на основі металевих і керамічних компонентів. У цьому випадку термограма випару речовини буде мати такий вигляд (рис. 6.1).
Як видно із графіка на рис. 6.1, процес нагрівання матеріалу складається із трьох етапів.
I – ізотермічна витримка при температурі 0,6 ÷ 0,8 Тпл. На цій стадії відбувається гомогенізація й зняття пружних напружень у шихті евтектичного складу. Для однокомпонентних матеріалів цей режим може бути опущений.
II – відповідає плавленню шихти. При плавленні матеріал нагрівається до температур на 10 ÷ 20°С вище ліквідусу з метою запобігання нерівномірності напиляного шару за рахунок передчасного випару легких компонентів.
III – відповідає випару речовини. Випар здійснюється при нагріванні на 100 ÷ 150°С вище температури випару для підвищення інтенсивності паротворення з метою одержання однорідної за хімічним складом пари.
Термограмма випару речовин зі змінною температурою плавлення Тпл.( рис. 6.2):
На даній термограмі також можна виділити три основних етапи:
I – загальний етап, тобто як у випадку речовин з постійною температурою плавлення.
II – відмінність від попередньої термограми полягає в тому, що нагрівання області плавлення відбудеться поступово зі швидкістю 20 ÷ 50 °С/хв. Це забезпечує розчинення надлишкових фаз і одержання гомогенного за складом твердого розчину.
III – випар відбудеться при температурах на 100÷150°С вище в порівнянні з рівноважними значеннями.
|
|
|
|
|
|



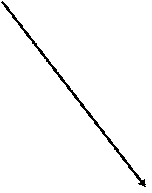
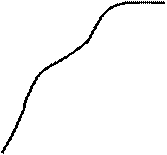




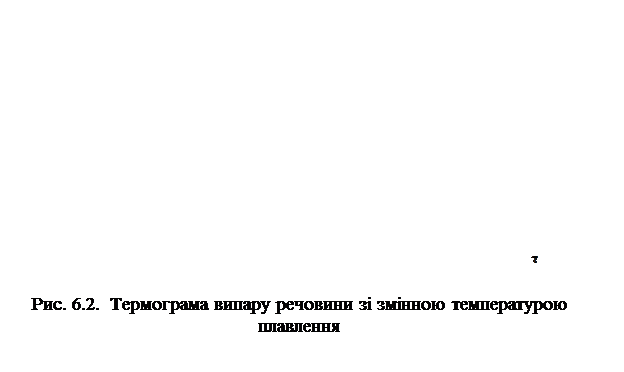
Вплив швидкості нагрівання/охолодження на процеси структуроутворення демонструє рисунок 6.3.
Із рисунка 6.3 видно, що при тривалому нагріві завдяки тому, що в матеріалі встигають пройти всі дифузійні процеси, ми отримаємо однорідний твердий розчин, тобто, однорідну структуру. В той час, як при швидкому нагріві ми отримаємо двофазний сплав, основною складовою якого буде евтектика.
Осадження матеріалу на підкладці може відбуватися по двох механізмах (рис. 6.4):
-Конденсація – це перехід матеріалів з газоподібного в рідкий стан.
-Сублімація– перехід з газоподібного у твердий стан.
![]() |
Рис. 6.4. Використання діаграми стану для вибору режиму |
Основним фактором, що впливає на перевагу процесу конденсації або сублімації є тиск. Це пов’язане з тим, що одержання тонких плівок вимагає значних переохолоджень, які збільшують за допомогою зниження тиску. Тому реальне значення тиску Р, що відрізняє переходи з газоподібного стану у рідкий або твердий стан, вибираються вище потрійної точки діаграми стану однокомпонентної системи.
6.2. Вплив температури стінок робочої камери на швидкість осадження матеріалу
Основною вимогою ефективної роботи випарника є підтримка потрібного температурного режиму стінок робочої камери. Температура робочої камери вибирається таким чином, щоб при заданому залишковому тиску пари речовини запобігти його конденсації або сублімації на оснащенні усередині робочого простору. На рисунку 6.5 показаний спосіб вибору температури робочої камери по діаграмі стану речовини (а) і схема напилювання вакуумтермічним методом (б).
Використання окремих нагрівальних елементів для підтримки заданого температурного режиму стінок робочої камери допускається в напилювальних установках великої продуктивності, у яких відносини об’єму робочої камери й випарника більше або дорівнює 5:
![]() |
а б
Рис. 6.5. Метод вибору температури (а) для вакуум-термічного методу напилювання (б)
На рисунку 6.6. показана конструктивна схема випарника (а) і графік залежності довжини вільного пробігу атомів від температури.
Коли об’єми робочої камери й випарника не підкоряються такій нерівності, тоді використовують випарник спеціальної конструкції, яка сполучає у собі область випару речовини й стінки робочої камери. Необхідний градієнт температур робочої камери створюється за допомогою нагрівального елемента, що має більшу щільність витків у нижній частині випарника й меншу у верхній частині.
У сучасних пристроях для напилювання часто використовуються монолітні нагрівачі змінного перетину, які виконують ту ж функцію, що й градієнтні печі, однак мають більший коефіцієнт корисної дії.
![]() |
Рис. 6.6. Конструкція випарника (а) і залежність довжини вільного пробігу від температури (б)
У сучасних пристроях для випаровування використовуються спеціальні системи фільтрації пари (рис. 6.7), які усувають наслідок краплинного кипіння в початковий момент плавлення речовини.
| |||
Рис. 6.7. Схема фільтрації пари |
Ця система являє собою електро–ізольовані фільтри, що мають різні розміри комірок, які за допомогою спеціальних нагрівачів нагріваються до температур, що задовольняють нерівності:
|
Для усунення турбулентності газових потоків при випарі складних матеріалів, що включають компоненти з різним парціальним тиском пари використовується прогресуючий режим нагрівання стінок робочої камери (у заключній стадії розпилення температура стінок робочої камери підвищується).
6.3. Вплив температури підкладки
У більшості випадків підкладку, на яку передбачається нанесення тонких плівок, нагрівають до температур вище 100°С для забезпечення задовільної адгезії речовини, що напилюють. Підігрів підкладки здійснюється як для адгезійних, так і для неадгезійних методів напилювання плівок. Схема, що демонструє вплив температури підкладки на формування тонкої плівки, показана на рисунку 6.8.
Рис. 6.8. Схема формування тонкої плівки залежно від температури підкладки і її адгезійності
Основною причиною підігріву підкладок при неадгезивному методі одержання плівок є підвищення коефіцієнта змочування матеріалу з ростом температури.
Охолодження підкладок використовується в рідких випадках при необхідності одержання плівок з аморфною й нанокристалічною структурою з матеріалів, схильних до аморфізації.
Вибір температури підкладки виконується на підставі діаграми стану даної системи з урахуванням механізму осадження речовини (рис. 6.9). При конденсації речовини температура підкладки вибирається більш високою, ніж при сублімації.
Рис. 6.9. Вибір температури підкладки за допомогою діаграми стану речовини
Під час вибору температури підкладки варто також ураховувати нерівноважність процесу осадження, наприклад: при швидкості осадження речовини 50мкм/сек. Фактичні температури та тиск процесів сублімації й конденсації можуть відрізнятися від рівноважних на 250 ÷ 300 %.
Як сказано вище, найбільш важливими параметрами формування структури тонких плівок при їхньому одержанні методами вакуумного напилювання являється щільність пари, температура підкладки, відстань від випарника до підкладки та ступінь перегріву речовини, що випаровується. Атомна структура твердої фази і її об'ємна структура визначаються рівнем переохолодження підкладки відповідно до температури стабільної сублімації й концентраційного профілю на межі неконденсованого й конденсованого станів (рис. 6.10).
![]() ![]() |
Рис. 6.10. Вплив швидкості охолодження підкладки на формування структури тонкої плівки
При низькій щільності пари й достатньо холодній підкладці формування першого шару твердої фази відбувається в умовах значного переохолодження, що сприяє формуванню в основному аморфної структури. Низька концентрація пари речовини сприяє цьому й перешкоджає швидкому формуванню плівки, а також не дає знижуватися переохолодженню. Збільшення щільності пари приводить до прискорення процесу формування твердої фази в напрямку від підкладки й зниженню ступеня переохолодження на фронті росту плівки. Створюються умови для утворення кристалічної фази з вихідних атомних блоків, що мають переважну орієнтацію в напрямку відводу тепла.
Однак, зі збільшенням щільності пари до деякого критичного значення, перехід до конденсованого стану відбувається настільки швидко, що можливість формування кристалічної фази різко знижується. Також важливо те, що в умовах високих значень щільності пари, кристалічна фаза має більшу область однорідності в порівнянні з фазами, отриманими у звичайних умовах.
6.4. Вплив тиску пари в робочому об’ємі
Як було показано вище, процес одержання плівок і покриттів методом випару і конденсації у вакуумі складається із двох етапів: випару речовини у вакуумі й наступній конденсації пари на підкладці.
Конденсація відбувається при тисках пари речовини більших тиску насиченої пари, коли на одиниці поверхні в одиницю часу конденсується більше число молекул, чим випаровується.
При одержанні плівки з нерівномірністю товщини 10% необхідно розташовувати підкладку на відстані l = 4,5Р від джерела, а для зниження нерівномірності до 5% ця відстань повинна бути збільшена до 6,3Р, де Р – це тиск пари речовини. Пласке джерело дає більшу, ніж крапкове, швидкість нанесення покриття, але нерівномірність покриття при цьому зростає.
Якщо над поверхнею речовини тиск його пари менше, ніж тиск насиченої пари при даній температурі, то буде відбуватися процес випару речовини. Випар припиняється при рівності тиску пари тиску насиченої пари. При цьому швидкості випару й конденсації молекул на поверхні рівні, що відповідає умовам динамічної рівноваги.
Імовірність вильоту молекул із плаского джерела дорівнює подвоєному добутку відносного тілесного кута на косинус кута між нормаллю до поверхні й напрямком вильоту.
Випар різних матеріалів у вакуумі, у тому числі й металів, відбувається при нагріванні до температури плавлення й випару (сублімації) або при розпиленні (методи катодного й магнетронного розпилення). Метали можна нагрівати резистивним методом (випарники прямонакальні й непрямого нагрівання), електронним променем, електричною дугою, струмами високої частоти. Способи нагрівання, що визначають конструкції відповідних унутрікамерних пристроїв промислових вакуумних установок, детально описані в інструкціях для експлуатації установок. Більша частина металів при нагріванні переходить у парову фазу через рідкий стан, тобто спочатку вони плавляться, а потім випаровуються. Деякі метали переходять із твердого стану в парову фазу, минаючи рідку (сублімують).
Узагальнена схема конденсації пари представлена на рисунку 6.11.
![]() ![]() |
Рис. 6.11. Загальна схема конденсації пари: φ- кут розповсюдження потоку пари; α- кут падіння пари на поверхню основи; l- відстань від матеріалу, що випаровується, до підкладки; d – діаметр плями напилювання речовини |
Випар із плаского джерела підкоряється закону косинуса, по якому ймовірність вильоту молекул пропорційна косинусу кута між нормаллю до поверхні й напрямком вильоту (рис. 6.12).
![]() |
Рис. 6.12. Загальна схема поширення пари у вакуумі, що підкоряється закону косинуса: φ- кут розповсюдження потоку пари; θ- кут падіння пари на поверхню основи; l - відстань від точки падіння пари до нормалі; h – відстань від матеріалу, що випаровується, до підкладки |
Якщо над поверхнею речовини тиск його пари менше, ніж тиск насиченої пари при даній температурі, то буде відбуватися процес випару речовини. Випар припиняється при рівності тиску пари тиску насиченої пари. При цьому швидкості випару й конденсації молекул на поверхні рівні, що відповідає умовам динамічної рівноваги.
7. СТРУКТУРОУТВОРЕННЯ В ТОНКИХ ПЛІВКАХ
Фактори, що впливають на формування структури у тонких плівках, наступні:
1. Щільність пари на фронті росту тонкої плівки.
2. Температурний градієнт у напрямку, перпендикулярному до підкладки.
3. Швидкість тепловідводу від підкладки й з боку покриття.
4. Ступінь дисоціації компонентів у пароподібному стані.
5. Температурна залежність енергії взаємодії компонентів у пароподібному й рідкому станах.
6. Енергія взаємодії компонентів з матеріалом підкладки, коефіцієнт змочування.
7.1. Механізми зародження конденсованих фаз на твердій підкладці
Зародження конденсованих фаз на твердій підкладці та їх подальший ріст залежать у першу чергу від температури підкладки та напрямку тепловідводу від цієї підкладки (рис. 7.1).
![]() |
Рис. 7.1. Напрямок тепловідводу в підкладці |
Зародження конденсованих фаз може відбуватися по гомофазному й гетерофазному механізмах. Наявність підкладки робить переважним гетерофазний механізм зародження фаз. Будучи гетерофазним при макроскопічному спостереженні, на мікроскопічному рівні можливі різні механізми утворення конденсованих фаз залежно від напрямку тепловідводу від підкладки.
Пошарова атомна сублімація. У цьому випадку неодмінною умовою є високий ступінь змочування підкладки речовиною, що наноситься, у твердому стані.
Пошарове осадження атомів звичайно порушується після формування декількох атомних шарів. Це пов’язане з тим, що на атомному рівні підкладка має значні нерівності (рис. 7.2).
Осадження атомів на виступаючу сторону підкладки значно полегшено, тому що відбувається в умовах більше високої його концентрації (рис. 7.3).
Схильність до пошарової сублімації може бути посилена за рахунок уповільнення процесу осадження (зниження температури переохолодження підкладки, зменшення щільності пари). Це уможливлює одержання плівок різної товщини 100 ÷ 200 Å (1Å = 10–10м).
Схема утворення твердої фази за рахунок формування гвинтової дислокації показана на рисунку 7.4.
На цей момент визначено кілька моделей росту вакуумних покриттів.
Першою моделлю росту є острівний ріст (рис 7.5). Він має місце при великій роботі утворення тривимірного зародка. Ріст плівки покриття протікає в результаті росту ізольованих зародків. У процесі зіткнення один з одним зародки поєднуються поки не буде вся поверхня заповнена.
Подібний ріст здійснюється при великому розходженні кристалічних ґрат матеріалу основи й матеріалу покриття.
Другою моделлю росту є шаруватий ріст (рис.7.6).
![]() |
Рис. 7.5. Схема острівного росту вакуумних покриттів |
![]() |
Рис. 7.6. Схема шаруватого росту вакуумних покриттів |
Він характерний при малій роботі зародкоутворення. У цьому випадку енергетично вигідно утворювати нові зародки чим добудовувати старі. Ріст іде шарами, зокрема нижній шар може бути аморфним. Такий ріст має місце, коли кристалічні ґратки матеріалу покриття й матеріалу основи однакові.
Третьою моделлю росту є змішана модель росту Сперанського-Крастанова, коли спочатку відбувається шаруватий ріст, а потім острівний. Такий ріст характерний при субкритичних температурах.
Четвертою моделлю є модель стовпчастого росту. Модель характерна для тих випадків, коли кожний атом, що попадає на поверхню, залишається в тім же положенні, у якому він зштовхнувся з поверхнею. Такий ріст можливий при низькій температурі поверхні підкладки.
Критичний розмір зародка конденсованої фази.
Зародження твердої фази завжди пов’язане з появою зародка критичного розміру, тобто, що складається з певної кількості атомів, число яких залежить від переохолодження вихідної рідини або пари й типу атомних зв’язків усередині кристала, що зароджується. Утворення твердої фази з меншим числом атомів не призводить до початку процесу кристалізації, й зародок розміром менше критичного розчиняється (переходить у стадію ближнього порядку розташування атомів).
При утворенні рідкої фази з пароподібної (конденсація) поняття критичного зародка не існує. Таке ж явище спостерігається при плавленні зародків фази критичного розміру.
З теорії зародкоутворення й даних, отриманих за допомогою електронної мікроскопії, випливає наступна послідовність етапів росту вакуумних покриттів (рис. 7.7):
1. Утворення адсорбційних атомів (адатомів).
2. Адсорбційні атоми утворюють ембріони субкритичних розмірів.
3. Утворення зародків критичних розмірів.
4. Зародки ростуть до надкритичних розмірів, при цьому відбувається об'єднання адсорбційними атомами зон захвата, а починаючи з певних розмірів зародки приймають кристалографічну орієнтацію.
5. Конкуруючим процесом для 4-го етапу росту є ріст зародків критичного розміру на площах, які не об'єднані адсорбційними атомами.
6. У процесі росту зародки стикаються один з одним, протікає процес коалесценції, у результаті якого утвориться острівець, що займає поверхню меншу, ніж сума площ вихідних зародків.
7. На поверхні, що звільнилася, адсорбуються атоми, вони можуть утворювати зародки критичного розміру. Іде процес «вторинного» зародкоутворення.
8. Більші острівці в процесі росту торкаються один одного при цьому на поверхні основи утворюються великі канали й порожнечі.
9. Канали й пори заростають у ході «вторинного» процесу.
10. Утворення суцільного покриття.
7.2. Закономірності утворення епітаксіальних тонких плівок
Загальне поняття епітаксії. Термін " епітаксія " походить від грецьких слів "епі" і "таксі", що має значення "над" і "упорядкування". Технологічний процес епітаксії полягає у вирощуванні на монокристалічній підкладці шарів атомів, упорядкованих у монокристалічну структуру, що повністю повторює орієнтацію підкладки.
Існує три види епітаксії: газова, рідинна й молекулярно-променева.
Причина появи технології виготовлення епітаксіальних плівок і їх переваги. Системи матеріалів, до складу яких входять тонкі плівки, відіграють важливу роль в електротехніці. Плівки товщиною менш 1 мкм можуть бути нанесені на матеріал підкладки шляхом випару, електроосадження з розчинів і розпиленням (плазмовим або катодним). Найбільш важливою характеристикою цих тонких плівок є якість їхнього зчеплення з підкладкою. Тому епітаксіальні плівки завжди будуть адгезійними. Для забезпечення якісного зчеплення структура плівки повинна бути «погоджена» зі структурою матеріалу підкладки, тобто повинна мати місце структурна відповідність між орієнтуваннями площин кристалічних ґрат плівки й підкладки; інакше кажучи, нанесені плівки повинні бути епітаксіальними, тобто «успадковувати» структуру підкладки. Одним із прикладів може служити шар кадмію, осаджений з парової фази на підкладку з дисульфіду молібдену (рис. 7.8).
![]() |
Рис. 7.8. Епітаксіальний ріст шару кадмію на підкладці з MoS2 (схема) |
Це означає, що на відповідним чином підібраних підкладках можуть бути вирощені відносно великі «двомірні» кристали.
Орієнтування площини (0001) у графітоподібної структури підкладки з дисульфіду молібдену визначають орієнтування площини (001) у структури металу, осадженого з парової фази. Надалі ці дрібні кристали кадмію (розміром ~ 500Å) зливаються, утворюючи плівку металевого кадмію (відстань r1120 для кадмію й MoS2 становлять 2,98 і 3,16 Å відповідно).
Атоми матеріалу плівки й матеріалу підкладки, зв'язані один з одним через площину розділу, належать одночасно двом погодженим структурам, у результаті чого утворилася границя розділу, що характеризується низькою енергією й, отже, високою міцністю. Це дозволяє розглядати підкладку, як великий зародок, що визначає структуру металу, який осаджується. З рисунку 7.9 виходить, що відстань між атомами алюмінію в металі приблизно на 6 % менше, ніж в окислі; незважаючи на це, подібна картина розташування атомів уможливлює узгодження орієнтувань кристалічних ґрат.
![]() |
Рис. 7.9. Когерентність ґрат Al2O3 і Al |
Як видно з рисунку 7.9, відносна непогодженість між розташуванням атомів у площині (111) ґрати металу (а) і в площині (0001) ґрати окислу (б) становить усього 6%. Тому шар іонів алюмінію може розташовуватися над атомами алюмінію в ГЦК ґратах металу (в).
Епітаксія з газової фази. Термін "епітаксія" застосовують до процесів вирощування тонких монокристалічних шарів на монокристалічних підкладках. Матеріал підкладки в цьому процесі виконує роль затравочного (зародкового) кристала.
Якщо матеріали шару, що одержали, й підкладки ідентичні, наприклад, кремній вирощують на кремнії, то процес називають автоепітаксіальним або гомоепітаксіальним. Якщо ж матеріали шару й підкладки розрізняються (хоча їхня кристалічна структура повинна бути подібною для забезпечення росту монокристалічного шару), то процес називають гетероепітаксіальним.