3.1. Основные элементы локомотивной откатки
К рельсовой локомотивной откатке относятся следующие основные элементы:
· рельсовые пути с комплексом вспомогательных устройств;
· рудничные вагонетки;
· тяговая сеть;
· преобразовательные и зарядные подстанции.
Тяговая сеть необходима при откатке контактными и индукционно-высокочастотными электровозами. Преобразовательные подстанции используются при откатке контактными электровозами, а зарядные подстанции – при откатке аккумуляторными электровозами (зарядка батарей), гировозами (раскрутка маховика) и пневмовозами (смена баллонов со сжатым воздухом).
3.2. Рудничные рельсовые пути
3.2.1. Характеристика рельсовых путей
Расположение рельсового пути в пространстве определяется трассой, планом и профилем.
Трасса – ось пути, нанесенная на карту (на план выработки) или разбитая на местности с помощью реперов.
План пути – проекция трассы на горизонтальную плоскость.
Профиль пути – проекция развернутой (не искаженной по длине) трассы на вертикальную плоскость.
Рельсовый путь состоит из двух основных частей: нижнего (основания) и верхнего строений.
К нижнему строению относится земляное полотно с искусственными сооружениями (мостами, путепроводами, акведуками), а для подземных путей – почва выработки с соответствующими продольными и поперечными уклонами и водоотливными канавками.
Верхнее строение составляет балластный слой, шпалы, рельсы, рельсовые скрепления и различное путевое оборудование.
Рельсовые пути, представляющие собой две нити скрепленных между собой рельсов (рис.6), характеризуются шириной рельсовой колеи S p, которая измеряется расстоянием между внутренними поверхностями головок рельсов.
Колесная колея S к – расстояние между наружными (рабочими) кромками реборд колес подвижного состава (локомотивов и вагонеток). Связь между рельсовой и колесной колеей следующая:
где x – игра колеи, обеспечивающая центрирование колесных пар (или полускатов) в движении и предотвращающая возможность расклинивания реборд колес между головками рельсов, для подземных рельсовых путей x = 10 мм.
![]()
|
Что касается ширины рельсовой колеи, то она для угольных шахт может быть 600 и 900 мм, для рудников – 750 мм. На поверхности, в карьерах, чаще используется нормальная колея S p = 1524 мм. Колея меньше 1524 мм называется узкой колеей. Допуски на колею для подземных рельсовых путей – 2 + 4 мм.
Для рудничного рельсового транспорта применяют рельсы с различными линейными массами: 18, 24, 33 кг/м и более. Выбор типа рельса определяется величиной нагрузки на колесную пару от подвижного состава и степенью ответственности рельсового пути. В последнее время применяют, как правило, тяжелые рельсы.
Балластный слой предназначен для распределения давления от шпал на возможно бόльшую площадь нижнего строения, образования под шпалой упругой подушки, предупреждения относительного смещения шпал, дренажа воды и создания постоянного уклона на участках рельсового пути.
Для формирования балластного слоя используют щебень из изверженных пород фракции 20-40 мм и дробленый гравий фракции 3-20 мм.
Шпалы предназначены для укрепления на них рельсов и передачи давления от рельсов на балластный слой. Применяют шпалы деревянные (предварительно пропитанные антисептиком), металлические и из предварительно напряженного бетона.
|
Рельсовые скрепления служат для соединения смежных рельсов в стыках и для прикрепления рельсов к шпалам, стык располагают между сближенными шпалами.
Для перевода отдельных вагонеток с одного пути на другой применяют плиты и поворотные круги, а для перевода составов используют стрелочные переводы или съезды (рис.7), которые характеризуются маркой крестовины
где a – угол между осями сходящихся путей.
В зависимости от направления ответвления боковых путей различают правые, левые и симметричные стрелочные переводы (рис.7 а, б, в). Для соединения параллельных путей применяют съезды (рис.7, г).
![]()
|
Для стрелок используют следующие переводные механизмы (рис.8):
· ручные индивидуальные;
· ручные групповые;
· с дистанционным управлением.
3.2.2. Особенности укладки рельсовых путей на закруглениях
На закруглениях рельсовые пути укладывают с превышением наружного рельса над внутренним и с уширением колеи.
Укладка наружной нитки с превышением (рис.9) обеспечивает прохождение равнодействующей силы тяжести и центробежной силы через ось симметрии пути и вагонетки. Благодаря этому исключается сход подвижного состава с рельсов на закруглениях пути.
Из расчетной схемы (рис.9) находим превышение (в миллиметрах) наружного рельса над внутренним:
|
где v – скорость движения подвижного состава (вагонетки), м/с; R – радиус криволинейного участка, м; S p – рельсовая колея, м.
Уширение рельсовой колеи на закруглении (рис.10) производится за счет сдвижки внутрь кривой внутреннего рельса из условия вписывания реборд колес подвижного состава при заданной жесткой базе B в рельсовую колею на участке закругления пути.
|
Величина уширения (в миллиметрах):
Разгон уширения и превышение наружного рельса над внутренним осуществляют постепенно на примыкающих к кривой с обеих сторон участках, длина которых (в метрах) L p = (1/3¸1/10)D h.
Радиус закругления для подземных рельсовых путей R = (7¸10) B.
3.3. Рудничные вагонетки
3.3.1. Классификация, основные элементы
и требования к вагонеткам
Рудничные (шахтные) вагонетки различаются по следующим признакам:
· по назначению – грузовые, людские (пассажирские), специальные (вспомогательные);
· по грузоподъемности (или вместимости кузова) – малой (до 1 т или 1,25 м3), средней (1-2 т или 1,25-2,8 м3); большой (больше 2 т или 2,8 м3);
· по типу кузова и способу его разгрузки – с глухим неопрокидным, с саморазгружающимся (опрокидным, с откидными бортом, торцевой стенкой, днищами или донной разгрузкой);
· по форме поперечного сечения кузова – с прямоугольным (рис.11, а), трапецеидальным (рис.11, б), анзеновским (рис.11, в), полукруглым (рис.11, г), прямоугольным с утопленными колесами (рис.11, д);
· по ширине колеи;
![]()
|
· по типу сцепок – с крюковыми вращающимися, штыревыми вращающимися, автоматическими (замыкание автоматическое, размыкание вручную с помощью тяги);
· по устройству ходовой части – с колесными парами и полускатами.
Наибольшее распространение получили в горной промышленности вагонетки с глухим кузовом и полукруглым днищем (61 % в рудной и 96 % в угольной промышленности), благодаря высокой надежности при эксплуатации в тяжелых условиях горного производства.
Вагонетка состоит (рис.12, 13) из следующих основных элементов: кузова; рамы (имеются безрамные вагонетки с самонесущим кузовом); полускатов (ось с двумя свободно вращающимися на ней колесами) или колесных пар (ось с жестко закрепленными на ней колесами); подвагонного упора (для взаимодействия с кулаками толкателя, подвагонной цепи или компенсатора высоты); двух буферов; двух сцепных приборов.
Комплект из двух полускатов называется скатом.
![]()
|
К рудничным вагонеткам предъявляются следующие требования:
· безопасность сцепки и расцепки вагонеток на конечных станциях;
· минимальные размеры и масса при заданной вместимости кузова;
![]()
|
· прочность и жесткость конструкции, достаточная для восприятия всех нагрузок (постоянная нагрузка – собственный вес и вес перемещаемого груза, сила тяги при установившемся движении; кратковременные нагрузки – центробежная сила на закруглении рельсового пути, сила инерции при неустановившемся движении – разгоне и торможении, удары кулака толкателя в подвагонный упор, удары на стыках рельсов);
· устойчивость вагонетки при любом расположении груза в кузове, плане и профиле рельсового пути;
· малые сопротивления движению;
· легкое и полное опорожнение кузова при разгрузке вагонетки;
· низкие эксплуатационные расходы.
3.3.2. Основные характеристики рудничных вагонеток
Основные конструктивные и эксплуатационные характеристики, определяющие уровень показателя качества рудничной вагонетки как массового средства рудничного транспорта, следующие:
1. Вместимость кузова V (в кубических метрах). Принимается из ряда (предпочтительных чисел) 1; 1,4; 2; 2,8; 4; 5; 6; 10 м3.
2. Грузоподъемность G (в тоннах). Этот показатель является производным от вместимости кузова:
G = V g,
где g – насыпная плотность транспортируемого груза, т/м3.
3. Коэффициент сопротивления движению вагонетки (рис.14). Определяется как отношение суммарного сопротивления движению W (в ньютонах), возникающего при движении с равномерной скоростью по прямолинейному горизонтальному пути, к полному весу вагонетки, т.е.
(3)
где g – ускорение свободного падения, м/с2; G в – масса вагонетки, т; для порожней вагонетки G в = G 0, а для груженой G в = G 0 + G; G 0 – масса порожней вагонетки, т.
Расчетное значение коэффициента сопротивления движению вагонетки может быть найдено следующим образом. Крутящий момент, необходимый для качения приведенного колеса по рельсам (в килоньютонах на метр),
![]()
|
где r – коэффициент (плечо) трения качения, м; f – коэффициент трения в подшипниках (буксах) колесных пар; d – диаметр цапфы оси колесной пары, м; K р – коэффициент трения реборд колес о головки рельсов, K р > 1.
Суммарное сопротивление движению
где D к – диаметр колеса, м.
Отсюда в соответствии с формулой (3)
.
Значения очень важного эксплуатационного показателя определяющего энергоемкость транспортирования грузов, в зависимости от типа подшипников, состояния их смазки, условий эксплуатации, загруженности вагонетки транспортируемым грузом, изменяется в достаточно широких пределах:
= 0,005¸0,012.
При расчете и выводе параметров локомотивной откатки часто удобнее пользоваться не коэффициентом сопротивления движению, а удельным сопротивлением движению. Его физический смысл – усилие (в ньютонах), которое необходимо приложить для перемещения по горизонтали с постоянной скоростью один килоньютон состава.
Удельное сопротивление движению (в ньютонах на килоньютон)
Таким образом, если – величина относительная (безразмерная), то
– размерный показатель, численное значение которого в 1000 раз превышает показатель
.
Использование показателя вместо
связано с тем, что сила тяги, необходимая для передвижения состава, на несколько порядков меньше его веса, поэтому вычисления существенно упрощаются.
Различают следующие показатели (или
): для груженой вагонетки при установившемся движении
(
), порожней вагонетки при установившемся движении
(
), груженой вагонетки при ее трогании с места
порожней вагонетки при ее трогании с места
Ясно, что
а
Для этого, ходовая часть вагонетки должна быть спроектирована так, чтобы минимальные сопротивления были при перемещении груженого состава. Чем меньше коэффициент сопротивления движению
или удельное сопротивление движению
тем более совершенной является вагонетка.
4. Коэффициент тары. Показывает эффективность конструкции транспортного средства, используемого для перевозки груза,
Обычно для угольных вагонеток K т = 0,45¸0,7, а для рудничных K т = 0,4¸0,6.
Чем меньше значения коэффициента тары, тем более совершенна вагонетка (конечно, при условии выполнения всех остальных предъявляемых к ней требований).
5. Коэффициент использования габаритных размеров
где V 0 – габаритный объем (прямоугольная призма, в которую вписана вся вагонетка), м3.
6. Удельная вместимость (в кубических метрах на тонну)
7. Линейная вместимость (в кубических метрах на метр)
где l в – длина вагонетки по сцепкам, м.
8. Коэффициент поперечной (боковой) устойчивости (рис.15)
где М в, М о – моменты восстанавливающий и опрокидывающий вагонетку в поперечном направлении относительно ее продольной оси, кН×м,
![]()
![]() |
;
v – скорость движения вагонетки, м/с; R – радиус закругления рельсового пути, м; h 0 – превышение центра массы вагонетки над головками рельсов, м.
Поперечная устойчивость рудничных вагонеток обычно обеспечивается при угле устойчивости (рис.15) a ³ 22°.
![]() ![]() |
9. Коэффициент продольной устойчивости (рис.16)
;
,
где Р и.в, Р и.г – силы инерции порожней вагонетки и находящегося в конце кузова груза массой G г; l – удаление центра массы груза от ближайшей оси колесной пары, м; h г – превышение центра массы груза над головками рельсов, м.
3.3.3. Мероприятия по повышению
долговечности вагонеток
Вагонетки являются массовым транспортным оборудованием на горном предприятии, поэтому весьма актуальны способы повышения долговечности вагонеток, что позволяет существенно снизить эксплуатационные расходы на рудничном транспорте и снизить себестоимость добычи полезного ископаемого.
К мероприятиям по повышению долговечности рудничных вагонеток, реализуемым при их проектировании, изготовлении и эксплуатации, можно отнести:
· прогнозирование и учет всех возможных нормальных эксплуатационных нагрузок на конструктивные элементы вагонетки;
· изготовление кузова из низколегированных сталей (лигатура: медь, хром, марганец, никель);
· горячее оцинкование кузовов;
· окрашивание, лаковое покрытие;
· изготовление кузова из стеклопластика;
· изготовление кузова из алюминиевых сплавов (удается снизить коэффициент тары до 0,17).
На предприятиях долговечность вагонеток и их эксплуатация при нормативных значениях коэффициентов сопротивления движению обеспечивается при регулярной ревизии состояния ходовой части (на испытательных горках), смазке подшипников колесных пар и полускатов, очистке внутренней поверхности кузовов от налипшего груза, неуклонном соблюдении правил эксплуатации.
3.4. Рудничные локомотивы
3.4.1. Виды локомотивов и их основной показатель
Применяемые на горных предприятиях локомотивы в зависимости от способа питания двигателей энергией делятся на две группы:
1) с источником энергии на самом локомотиве (дизелевозы, воздуховозы, аккумуляторные электровозы, инерционные локомотивы – гировозы);
2) с источником энергии вне локомотива (контактные, контактно-кабельные, высокочастотные, конденсаторные).
В ряде случаев применяются локомотивы смешанного типа (например, контактно-аккумуляторные).
Локомотивы первой группы работают с уменьшающимся запасом энергии, поэтому периодически на специальных станциях необходимо производить пополнение энергии.
Локомотивы второй группы не связаны со станцией, но требуют специального оборудования пути для непрерывного питания энергией во время движения. Для электровозов различных типов – это тяговая питающая сеть.
Наибольшее распространение получили контактные и аккумуляторные электровозы, работающие на постоянном токе с применением в качестве тяговых двигателей с последовательным возбуждением.
Основной характеристикой локомотива любого типа является его сцепной вес Р, т.е. вес, приходящийся на его ведущие оси. Для рудничных локомотивов сцепной вес равен полному весу, так как все оси – ведущие.
3.4.2. Классификация электровозов
Используемые на горных предприятиях электровозы можно классифицировать по следующим признакам.
1. По способу питания – контактные, индукционно-высокочастотные, аккумуляторные, аккумуляторно-контактные, контактно-кабельные.
2. По роду тока – постоянного и переменного тока.
3. По сцепному весу – легкие (до 5 g кН), средние (от 5 до 10 g кН), тяжелые (больше 10 g кН).
4. По назначению – магистральные, маневровосборочные.
5. По ширине колеи.
6. По конструктивному исполнению кузова – рамные (колесные пары установлены на раме) и тележечные.
7. По конструктивному исполнению ходовой части – с индивидуальным приводом на каждую колесную пару (основной тип локомотивов) и с групповым приводом (от одного тягового двигателя через коробку передач).
8. По способу управления – с непосредственной (контроллерной) и косвенной (контакторной) системами управления тяговыми двигателями.
9. По способу торможения – с механическим; с механическим и электрическим реостатным; механическим, электрическим реостатным и электромагнитным торможением.
10. По типу привода механических тормозов – с ручным, пневматическим и гидравлическим приводами.
3.4.3. Конструкция электровоза, его основное
оборудование и параметры
Простейший электровоз рамной конструкции (рис.17) состоит из следующих элементов: рамы с кабиной; двух колесных пар с их рессорным подвешиванием к раме; тяговых передач; колодочных тормозов с системой привода из кабины машиниста (может быть две кабины с разных сторон электровоза); буферов со сцепными устройствами; песочниц для подсыпки песка на рельсы при трогании локомотива с места (под каждое колесо); токосъемника (пантографа) для контактного электровоза и съемной аккумуляторной батареи для аккумуляторного электровоза; устанавливаемой на роликах рамы электровоза; пускорегулирующей аппаратуры и осветительной арматуры во взрывобезопасном исполнении.
Рама электровоза изготавливается в двух исполнениях, в зависимости от этого может быть наружной и внутренней (по отношению к колесам). Толщина боковых и торцевых стенок рамы выбирается из условия обеспечения заданного сцепного веса – для контактных электровозов и из условия обеспечения прочности – для аккумуляторных.
![]() |
Буфера могут быть жесткие, полужесткие и эластичные.
Каждая колесная пара состоит из оси, двух колесных центров и надетых на них (при горячей посадке) стальных бандажей наружным диаметром 680 или 760 мм.
Подшипники колесных пар размещены в буксах, которые упруго связаны с рамой через систему рессорного подвешивания (рис.18).
Рессорная подвеска рамы (рис.19) может быть индивидуальная, балансирная – с продольными и поперечными балансирами. Рессоры выполняют из спиральных или листовых пружин.
Наиболее распространенный тип тяговой передачи с индивидуальным приводом выполняется по схеме так называемой трамвайной подвески двигателя. В этом случае двигатель, жестко соединенный с редуктором, со стороны двигателя с помощью спиральных пружин, опирается на кронштейны рамы, а тихоходный вал редуктора является одновременно осью колесной пары. При этом в качестве тяговых используют тихоходные (рис.20) или быстроходные (рис.21) двигатели.
![]()
![]()
![]()
![]()
|
Расположение тяговых двигателей относительно осей колесных пар (расстояние между ними – жесткая база В электровоза) может быть наружное, последовательное и внутреннее (рис.22).
![]() ![]()
|
Минимальная жесткая база В 1 соответствует наружному расположению тяговых двигателей, максимальная В 3 – внутреннему. В этом случае маневренность электровоза с увеличением жесткой базы уменьшается, а устойчивость – увеличивается. Поэтому расположение тяговых двигателей определяет важные эксплуатационные возможности и недостатки электровозов, что должно учитываться при выборе конструкции локомотива в соответствии с условиями его эксплуатации (состоянием путевого хозяйства, радиусами рельсовых путей, горно-техническими и другими условиями).
![]()
|
В настоящее время магистральные контактные электровозы выпускаются со сцепными весами 7, 10, 14, 28 g кН, а аккумуляторные – 10, 14, 20 g кН. Скорость движения обычно не более 20 км/ч. Напряжение контактной сети 250 и 500 В, а на выходе аккумуляторной батареи от 40 до 160 В. Аккумуляторные батареи щелочные, железоникелевые типа ТЖН, реже – свинцовые.
Частота вращения якоря тяговых быстроходных электродвигателей от 900 до 1100 об/мин.
3.4.4. Пневмовозы, гировозы
и специальные типы электровозов
Пневмовозы (воздуховозы) и гировозы относятся к локомотивам с убывающим запасом энергии. В первом случае необходимо периодически менять баллоны со сжатым воздухом, а во втором – на специальной станции производить раскрутку маховика для сообщения ему дополнительной кинетической энергии.
Колесные пары пневмовоза (рис.23) приводятся во вращение с помощью кривошипно-шатунных механизмов с взаимным угловым смещением кривошипов с правой и левой стороны локомотива. Привод каждого кривошипно-шатунного механизма осуществляется от силовых цилиндров высокого и низкого давления. Площади поршней цилиндров обратно пропорциональны давлению воздуха в них: диаметр цилиндра высокого давления меньше диаметра цилиндра низкого давления.
![]() |
Цилиндр высокого давления питается от съемных баллонов сжатого воздуха через редукционный клапан, понижающий давление с (175-225)105 до 16 × 105 Па. Воздух проходит через воздухоподогреватель (расширяющийся воздух подогревается при движении локомотива встречным потоком рудничного воздуха). Выхлоп цилиндра высокого давления (давление воздуха около 6 × 105 Па) через воздухоподогреватель низкого давления направляется в цилиндр низкого давления, из которого, после совершения работы, выбрасывается в атмосферу.
Сцепные веса пневмовозов от 8 до 10 g кН, скорость их движения 3-4 км/ч, развиваемая ими сила тяги около 7,5 кН, а суммарная мощность, развиваемая двумя пневмоцилиндрами, 30-40 л.с.
Источником энергии гировоза является размещенный на вертикальной оси маховик, который через коробку передач связан с колесными парами локомотива. Параметры испытанного гировоза: диаметр маховика 940 мм, начальная частота его вращения после раскручивания 3000 об/мин, развиваемая мощность 30 л.с. при скорости движения локомотива от 3 до 12 км/ч. Сцепной вес гировоза около 57 кН. Время зарядки (раскручивания маховика) 12 мин при давлении сжатого воздуха в сети (4,9-5,9)105 Па (5-6 атм).
Кроме рассмотренных типов локомотивов, существуют разработки в области создания альтернативных локомотивов на электрической тяге. К ним можно отнести рудничные электровозы с гидроприводом – сочетание нерегулируемого электродвигателя и регулируемой гидропередачи объемного типа с гидродвигателями. По такой схеме выполняются как контактные, так и аккумуляторные электровозы.
Известны результаты испытания конденсаторного электровоза. Тяговый двигатель – однофазная электрическая машина с двумя обмотками статора и короткозамкнутым ротором. Одна из обмоток присоединяется к сети непосредственно, а другая – через конденсатор, обеспечивающий необходимый сдвиг фаз для реализации крутящего момента на валу тягового двигателя.
Известно также техническое решение, обеспечивающее бесконтактную передачу энергии от питающего кабеля к электродвигателю (бесконтактный высокочастотный электровоз). Частота тока 3000 Гц. На электровозе имеются выпрямители, питающие двигатели постоянного тока.
3.5. Основы тягового расчета
3.5.1. Уравнение движения поезда
Движение поезда (локомотива с прицепленным к нему составом), как и всякого материального тела, может быть описано дифференциальным уравнением
где F – сила тяги, развиваемая локомотивом, Н; S W 0 – суммарные статические сопротивления движению поезда, Н; Р – вес (сцепной вес) локомотива, кН; Q – вес прицепной части поезда (состава), кН; K и – коэффициент, учитывающий инерцию вращающихся масс поезда; dv / dt – ускорение движения поезда, м/с2.
Коэффициент инерции
где K э, K в – коэффициенты, учитывающие инерцию вращающихся масс локомотива и вагонеток; обычно K Э = 0,036÷0,04; K В = 0,03÷0,04.
Для поезда K и = 1,06÷1,08.
Дифференциальное уравнение называется основным уравнением движения поезда, оно позволяет найти необходимую величину силы тяги при различных режимах работы локомотива как тягового агрегата.
Сила тяги при неустановившемся режиме работы в период пуска (трогания поезда с места)
где S W – статические сопротивления движению, S W 0 = S W; в этом режиме dv / dt > 0.
При равномерном движении dv / dt = 0, а уравнение движения поезда
т.е. потребная сила тяги численно равна суммарным статическим сопротивлениям движению.
При торможении поезда, когда тяговые двигатели выключены и F = 0, к силам естественного сопротивления движению S W добавляется искусственное сопротивление – тормозная сила В. Тогда S W 0 = = S W + B. В этом случае уравнение движения поезда примет вид
в котором dv / dt < 0.
При свободном выбеге, когда торможение поезда осуществляется только за счет естественных сопротивлений движению S W, т.е. В = 0 (S W 0 = S W), уравнение движения поезда
.
Режим свободного выбега может быть реализован, когда S W > 0, так как только в этом случае dv / dt < 0, т.е. поезд будет двигаться с замедлением и рано или поздно остановится без искусственного его подтормаживания. Если же S W < 0, то после выключения двигателей локомотива (F = 0) поезд начнет двигаться с ускорением, что совершенно недопустимо. В этом случае должно быть применено искусственное торможение (3-й режим).
Для того, чтобы использовать полученные уравнения при практических расчетах локомотивной откатки, должны быть выявлены механизмы реализации силы тяги F и тормозной силы В, а также найдена зависимость, определяющая величину статических сопротивлений движению поезда S W.
3.5.2. Механизмы реализации силы тяги и тормозной силы
При движении поезда с включенными двигателями локомотива сила тяги F может быть получена только за счет работы тяговых двигателей. При этом внутренние силы тяги реализуются во внешнюю (по отношению к поезду) силу тяги F через взаимодействие с рельсами колесных пар локомотива.
Внутренней по отношению к поезду силой тяги является крутящий момент М (в ньютон-метрах), развиваемый двигателем (через редуктор) на ведущих колесных парах, и который может быть реализован (рис.24) только в виде пары сил (в ньютонах)
,
где D к – диаметр колеса, м.
![]()
|
Силы F приложены в двух точках: к колесу (приведенному) в месте его контакта с рельсом и к подшипникам колесной пары.
Первая сила F уравновешена силой сцепления F сц колеса с рельсом, являющейся реактивной силой, возникающей поскольку действует сила F. Вторая сила F (приложенная к подшипнику) остается неуравновешенной, а потому вызывает качение колеса (колесной пары) по рельсам и, следовательно, поступательное движение локомотива и соединенного с ним состава. Эта сила F и является силой тяги.
Таким образом, реализация внутреннего крутящего момента М во внешнюю силу тяги F возможна лишь при наличии внешней силы F сц сцепления колес с рельсами, если F = F сц.
Но с другой стороны, F сц не может быть беспредельной, а ограничена коэффициентом сцепления ведущих колес локомотива с рельсами m и усилием Р прижатия ведущих колес локомотива к рельсам, т.е.
.
Отсюда и максимально возможная сила тяги F max также ограничена F сц, так как F = F сц. Тогда из условия сцепления колес локомотива с рельсами
.
С другой стороны, сила тяги F ограничена мощностью тяговых двигателей N (в киловаттах), поэтому из условия использования полной мощности тяговых двигателей максимально возможная сила тяги
где v – скорость движения поезда, км/ч; ηт.п – КПД тяговой передачи.
Если сила тяги при использовании полной мощности тяговых двигателей меньше силы тяги из условия сцепления, т.е. то локомотив называют недомоторенным, если
то локомотив называют перемоторенным.
Современные локомотивы обычно перемоторены. Это вызвано стремлением увеличить среднеходовые скорости движения поездов (за счет быстрого разгона) и обеспечить работу тяговых двигателей без перегрева. Однако при использовании перемоторенных локомотивов не исключено буксование колесных пар, сопровождаемое износом бандажей колес и рельсов.
При торможении поезда к его тормозным колесным парам (они же – ведущие) прикладывается тормозной момент М т (рис.25) за счет тяговых двигателей при электрическом или электродинамическом торможении противотоком и использования тормозных колодок при механическом торможении.
Внутренний (по отношению к поезду) тормозной момент М т также реализуется в виде пары сил В, одна из которых приложена к рельсам, а вторая – к подшипникам колесных пар, а значит, и к раме локомотива и ко всему поезду.
Как и сила тяги F, тормозная сила В ограничена максимально возможным значением силы сцепления F сц max колес локомотива с рельсами, т.е. всегда
а максимально возможное значение тормозной силы по условию сцепления
.
Для условий рудника расчетное значение коэффициента сцепления колес с рельсами m = 0,10÷0,28.
Рис.25. Расчетная схема к определению тормозной силы |
Попытка превышения силы тяги, определяемой сцеплением колес с рельсами, приводит к буксованию колес, при котором коэффициент сцепления μ снижается примерно на 30 %, а поэтому снижается и реализуемая сила тяги F. С точки зрения кинематики условие буксования можно представить в виде неравенства
,
где v о, v п – окружная и поступательная скорости движения колеса.
Характер износов бандажа и рельса при буксовании показан на рис.26, а.
Попытка превышения тормозной силы, определяемой также сцеплением колес с рельсами, приводит к так называемому юзу – движению невращающихся колес по рельсам скольжением. При этом предельное значение тормозной силы снижается. Кроме того, интенсивно и, самое главное, неравномерно изнашиваются бандажи колес, а также рельсы (рис.26, б.). В общем случае условие возникновения юза
Рис.26. Режимы буксования (а) и юза (б) колес локомотива с харак- терными картинами износа головок рельсов (1) и бандажей колес (2) |
Пути повышения силы тяги по сцеплению и тормозной силы следующие.
Для увеличения силы тяги пока найден только один способ – подмагничивание ведущих колес путем установки намагничивающей катушки внутри колеса. В результате возникновения магнитного поля в системе колесо – рельс колесо дополнительно прижимается к рельсу, поэтому к сцепному весу Р добавляется еще сила магнитного прижатия Р м. В этом случае
.
Для увеличения тормозной силы могут применяться специальные тормозные вагонетки, оборудованные колодочными тормозами, и электромагнитные рельсовые тормоза, устанавливаемые на локомотиве (электровозе).
В первом случае
,
где Σ G т – общая масса тормозных вагонеток, т.
Во втором случае
,
где Р м– сила нажатия одного башмака с электромагнитным приводом на рельс, Н; n – число одновременно включенных башмаков; f – коэффициент трения между башмаком и рельсом, f = 0,09÷0,15.
Р м |
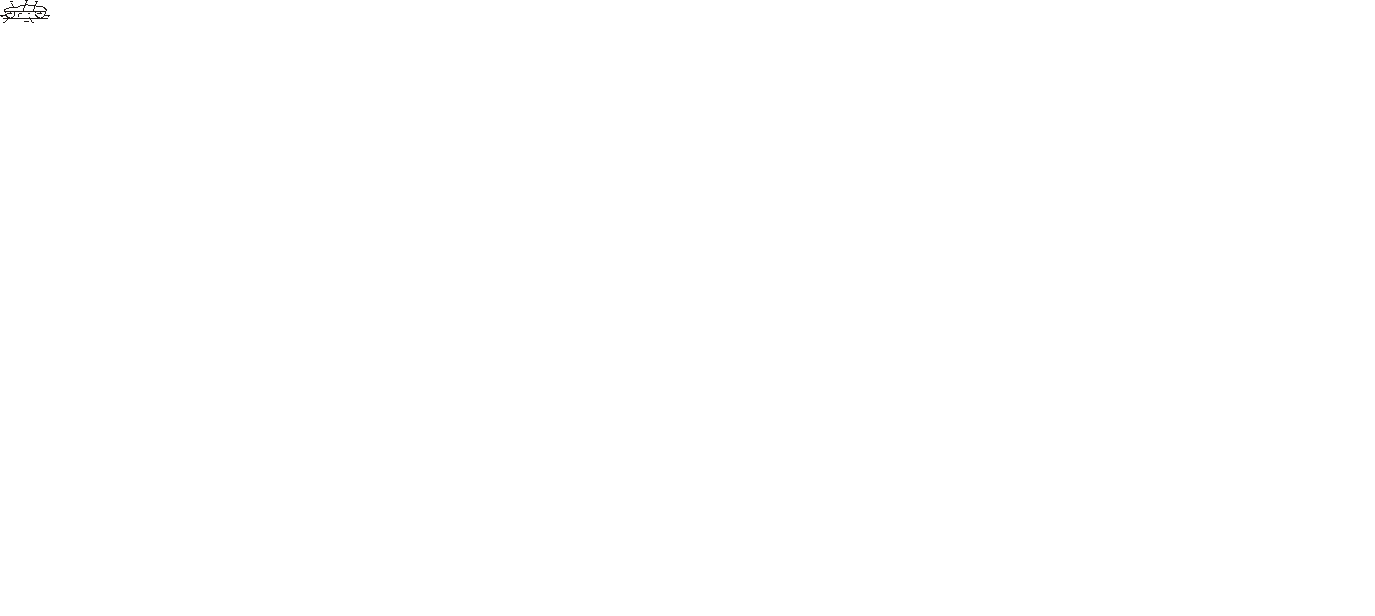
Рис.27. Увеличение тормозной силы с помощью подвесного
электромагнитного башмака
1 – рельс; 2, 6 – колесные пары; 3 – рама; 4 – пружинная подвеска
башмака 7; 5 – направляющие
Электромагнитный рельсовый тормоз (рис.27) состоит из двух башмаков, кинематически связанных поперечинами и подвешенных на пружинах между колесными парами электровоза. При включении электромагнитов башмаки, преодолевая сопротивление пружин, прижимаются к рельсам и обеспечивают дополнительную тормозную силу.