1 Сутність процесів і основні способи обробки металів тиском.
2 Вплив обробки тиском на структуру і властивості металів.
3 Прокатка.
4 Холодна прокатка кольорових металів.
5 Сутність процесу волочіння.
6 Пресування.
7 Кування, штампування.
1 Обробка металів тиском грунтується на використовуванні пластичності металу, тобто здатності змінювати первинну форму під дією зовнішніх сил або внутрішніх напруг без руйнування і зберігати знов отриману форму після зняття навантаження.
Унаслідок сприятливих структурних змін, що відбуваються при обробці тиском, метал одержує більш високий комплекс міцнісних і пластичних властивостей у порівнянні з литими. При гарячій обробці тиском, коли метал володіє великою пластичністю при малій міцності, його зерна витягуються і трансформуються у волокна.
Волоконна будова металу забезпечує важливі переваги в порівнянні із звичайною зернистою структурою, оскільки міцність деформованого металу на розрив уздовж волокон виявляється значно вище, ніж у поперечному напрямі.
|
|
Знаючи характер навантаження окремих елементів деталей в експлуатаційних умовах, можна ще при виготовленні заготовок додавати волокнам найвигідніше орієнтування, що відповідає характеру навантаження відповідних елементів деталей, і цим забезпечити великий запас міцності. Наприклад, показаний на рисунку 2.2,б болт, виготовлений з дотриманням даного принципу, міцніше ніж на рисунку 2.2,а, де головка легко зрізається.
Заготовки для деталей, отримані обробкою тиском, прийнято називати поковками. Початковими заготовками для крупних поковок, як правило, служать сталеві зливки. Заготовки для дрібних поковок одержують шляхом розрізання на мірні шматки-болванки так званих профілів – металевих балок або прутків різної форми поперечного перетину, одержуваних прокаткою.
У сучасному виробництві застосовують такі види обробки металів тиском: прокатка, волочіння, пресування, вільне кування і штампування.
2 Обробка металів тиском викликає зміну механічних і фізико-хімічних властивостей. Процес деформації металу починається з поверхні і з певною швидкістю розповсюджується в глибінь тіла, що деформується. При додаванні зусиль, невеликих за величиною і короткочасних за дією (удари молота), деформація відбувається тільки на поверхні. В цьому випадку спостерігається поверхневе зміцнення металу, зване нагартовкою.
Волоконна структура і деформована гратка, отримані в результаті холодної обробки, нестійкі і з часом можуть перейти в стійкий стан. Проте у більшості металів відновлення граток і структури при кімнатній температурі відбувається дуже повільно внаслідок малорухливості атомів при цих температурах. Для прискорення цього процесу метал необхідно нагрівати. При невеликому нагріві (для заліза до 200-300оС) холоднодеформованого металу відновлюються тільки кристалічні гратки, мікроструктура майже не змінюється, але зміцнення знижується на 20-30%. Цей процес називається поверненням або відпочинком.
|
|
Якщо холоднодеформований метал піддати термічній обробці – відпалу, то наклеп усувається і метал знову починає набувати пластичність та інші притаманні йому властивості.
У холодному стані обробці тиском піддаються тонкі листи, штаби з м'якої сталі, кольорові метали і сплави.
Обробку сталі тиском звичайно проводять у нагрітому стані, оскільки з підвищенням температури оброблюваний метал набуває найбільшу пластичність. При гарячій обробці тиском метал одержує рекристалізовану структуру без слідів зміцнення (наклепу).
Для нагріву металу при обробці тиском користуються різними нагрівальними пристроями, що працюють на твердому, рідкому і газоподібному паливі, а також за допомогою електричної енергії. За розподілом температури нагрівальні печі діляться на камерні і методичні. В камерних печах температура однакова у всьому робочому просторі, в методичних – температура змінюється по її довжині.
3 Прокатка є процесом деформації зливка або іншої довгастої металевої заготовки між двома валками, що обертаються, відстань між робочими поверхнями яких менше висоти заготовки (рисунок 2.3)
|
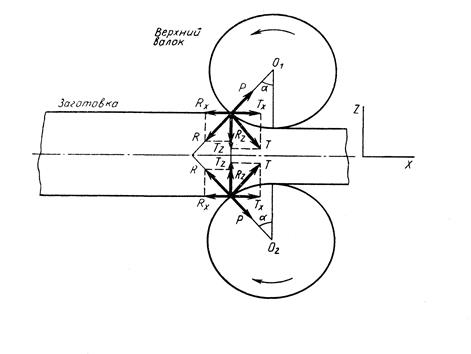
Метою прокатки є отримання різноманітної продукції, що розрізняється профілями і розмірами поперечного перетину, а також довжинами балок, прутків і складає так званий сортамент прокату (рисунок 2.4)
Рисунок 2.4 – Сортамент стального прокату.
Сортамент прокату включає такі п'ять основних груп:
- сортовий прокат простого і фасонного профілю. Простий профіль використовується для порізки на заготовки, які йдуть або на подальшу обробку тиском – кування або штампування, або на механічну обробку для виготовлення різних деталей. Профіль фасонний головним чином використовується для різних будівельних конструкцій, включаючи залізничні колії;
- листовий прокат ділиться на товстолистову сталь товщиною понад 4 мм і тонколистову 0,2-3,75 мм;
- труби безшовні різного діаметра з різною товщиною стінок, різноманітного призначення;
- спеціальний прокат включає вагонні колеса, шпунтові палі, автоободи і т.д;
- періодичний прокат – прокат з періодично змінним по довжині профілем. Він використовується як заготовки для штампування (наприклад, заготовок шатунів автомобільних двигунів) або безпосередньо для механічної обробки.
Існують також спеціально розроблені сортаменти для випуску прокату з кольорових металів і сплавів – міді, алюмінію, латуні, дюраля у вигляді листів, стрічки, труб, прутків і інших виробів.
Найважливішою особливістю деформації при прокатці є отримання волоконної структури металу з орієнтуванням волокон уздовж напряму прокатки, тобто перпендикулярно осям обертання валків. Це пояснюється тим, що при здавленні перетину заготовки між валками витяжка металу в основному відбувається у напрямі якнайменшого опору, тобто в зовнішню сторону. Деформації і витяжці у поперечному напрямі перешкоджають тертя об поверхню валків. Оскільки загальна витяжка металу заготовки складається з витяжки окремих зерен, то останні повинні перетворитися на волокна. Заготовка захоплюється в робочий простір між валками і переміщається силами тертя, що виникають між нею і валками. Умовою захоплення заготовки валками і здійснення процесу прокатки є перевищення коефіцієнта тертя над тангенсом кута захоплення. При цьому обтискаючими або крутячими заготовку силами є реактивна сила R і сила тертя Т.
|
|
Прокатка металів здійснюється на прокатних станах. Основними робочими елементами прокатних станів є валки, що мають циліндричну форму. Валки розміщуються в основній частині прокатного стана – робочій кліті. Робоча частина валка називається бочкою. Бочки можуть бути гладкими або рівчаковими. Перші застосовують для прокатки листів і стрічок, а другі – для сортового металу. Рівчак є кільцевими вирізами на поверхні валка. Рівчаки верхнього і нижнього валка, що збігаються, утворюють калібри, за допомогою яких сортовому прокату поступово додаються необхідні профілі.
Прокатні стани класифікують за рядом ознак, основним з яких є рід продукції, що випускається. У зв'язку з цим можна виділити такі види станів: сортопрокатні для випуску сортового прокату; листові і штабові стани гарячого прокату; трубопрокатні стани, стани холодного прокату сталі і кольорових металів (тонколистові, стрічкопрокатні, фольгопрокатні і т.д.); деталепрокатні стани для випуску спеціального або періодичного прокату.
4 Холодна прокатка кольорових металів і сплавів має свої особливості. Технологія отримання прокату з кольорових металів приблизно така ж, що і при прокатці сталі, але залежно від властивостей металу, розмірів і призначення готового прокату одні операції можуть повторюватися, а інші бути відсутніми. Наприклад, листи і штаби з олов'янисто-свинцевої бронзи прокочують у холодному стані. В цьому випадку нагрівання зливків не здійснюється.
До якості поверхні листів і стрічок з кольорових металів пред`являються підвищені вимоги, тому механічну обробку поверхні зливків і заготовок проводять кілька разів. При холодній прокатці зливка в готовий виріб застосовується проміжний відпал для зняття наклепу і підвищення його пластичності.
Холодна прокатка стрічки з алюмінієвих сплавів АМц, Д1, Д16 проводиться з гарячекатаних листів товщиною близько 6 мм. Стрічку товщиною до 0,5-0,6 мм катають без проміжного зм'якшуючого відпалу.
|
|
Заготовками для холодної прокатки з міді і латуні Л62 служать згорнуті в рулони штаби завтовшки 5 –6 мм, отримані гарячою прокаткою із зливків. Відпалені і протравлені рулони прокочуються на спеціальних станах до товщини до 0,01 – 0,2 мм протягом чотирьох-п'яти операцій холодної прокатки, що чергують зм'якшуючими відпалами і травленнями для видалення окалини. Для холодної прокатки переважають однофазні латуні із вмістом цинку менше 30%, так як володіють великим запасом пластичності. Для запобігання налипання міді і латуні на сталеві валки застосовують рідке мастило (трансформаторне масло, гас, веретенне масло і т.д.).
5 Процес волочіння (рис. 2.3) полягає у протягуванні оброблюваного металу через отвір, розміри якого менше розмірів початкової заготовки, і який поступово звужується. При волочінні поперечний перетин заготовки зменшується, а її довжина збільшується. Волочінням обробляються тільки пластичні матеріали. Вихідним матеріалом для волочіння є гарячекатаний сортовий прокат різного профілю (круглого, квадратного, шестигранного), дріт, труби із сталі, кольорових металів.
Волочіння здійснюється без нагріву металу, тому за одне протягування не можна досягти значного зменшення поперечного перетину, оскільки при великих обтисканнях у металі можуть виникнути великі напруги, які приведуть його до розриву.
Рисунок 2.5 – Схема процесу волочіння.
Величину обтискання визначають коефіцієнтом К (К = d/D, де D – діаметр заготовки, d – діаметр отриманого дроту), який повинен дорівнювати 0,8-0,95, щоб не відбувалося руйнування металу.
Волочінням одержують дріт діаметром від 6 мм до сотих часток міліметра, труби малого діаметра й інші профілі. Волочіння труб проводять без зміни товщини стінки (рис. 2.3,б) і зі зменшенням діаметра труби і товщини стінки при протяжці на пробці 3 (рис. 2.3,в).
Волочіння здійснюють на волочильних станах, що складаються з волочильного очка або волочильної дошки з очком і пристрою, що тягне. Волочильне очко є звичайним подвійним конусом (усіченим), від розмірів якого залежать величина зусилля при волочінні, термін служби очка і якість виробу. Довжина циліндричної частини очка приймається рівною половині його діаметра. Волочильні очки виготовляються з легованої сталі, твердого сплаву або алмазу.
Тяговий пристрій виконується у вигляді барабана, що обертається, для протяжки дроту або у вигляді нескінченного ланцюга і каретки із захопленням для протяжки прутків дроту. Для волочіння дроту застосовують волочильні стани однократного і багатократного волочіння. У станах однократного волочіння протягують дріт через очко тільки один раз; у станах багатократного волочіння метал проходить послідовно 7 разів через очки з поступовим зменшенням поперечного перетину.
Дріт, що піддається протяжці, заздалегідь очищають від окалини, виконують травлення в розчинах кислот, а потім мастять яким-небудь мастилом (жир, масло, емульсія) для зменшення тертя при волочінні. Кінець прутка обмотують, заправляють в очко, закріплюють на барабані і лише після цього здійснюють волочіння. При багатократному волочінні на поверхні прутка створюється наклеп, що знижує пластичність металу. Для зняття напруги і відновлення пластичності застосовують проміжний світлий відпал. Після волочіння виходять профілі точних розмірів з високою якістю поверхні.
6 Процес пресування полягає у видавлюванні металу, що містять в замкнуту порожнину, через отвір меншого перетину, ніж початковий. Пресування може бути прямим і зворотним.
При прямому пресуванні (рис. 2.4,а) заготовку 1 видавлюють з контейнера 2 пуансоном 3 через отвір матриці. В цьому випадку метал видавлюється по напряму руху пуансона.
При зворотному пресуванні метал 1 видавлюється з контейнера 2 через отвір матриці 4 назустріч руху пуансона 3 (рис.2.4,б)
Рисунок 2.4 – Схема пресування
Пресування є високопродуктивним процесом і здійснюється переважно на гідравлічних пресах великої потужності. Пресуванням одержують прутки діаметром 3-250 мм, труби діаметром до 800 мм і товщиною стінки 1,5 мм і більш, а також багато інших виробів, які не можна отримати іншими способами обробки тиском.
7 Кування – це процес отримання деталей шляхом пластичної деформації металу під дією послідовних ударів молота або під тиском преса. Кування ділиться на вільне кування і кування в штампах (ручне і машинне). Ручне вільне кування ведеться на ковадлі за допомогою кувалди, ручника та іншого ковальського інструменту. Ручним куванням виготовляють дрібні поковки різної форми масою до 10 кг з прокатних профілів в умовах індивідуального виробництва або при ремонтних роботах.
Машинне або механічне кування здійснюють на кувальних молотах і пресах для середніх і крупних поковок в умовах серійного виробництва.
Куванням виготовляють поковки і заготовки різної форми шляхом послідовного виконання основних ковальських операцій. Основними операціями вільного кування є: рубка, витяжка, осідання, висадка, гнуття, прошивка отворів і вибілювання.
Рубання – це операція розділення початкової заготовки на мірні заготівки. Рубка проводиться за допомогою зубил і сокир.
Витяжкою називається операція кування, при якій довжина заготовки збільшується за рахунок зменшення поперечного перетину. Витяжку ведуть на вузькому бойке молотка з поворотом заготовки на 90о. Удари наносять упоперек заготовки, що забезпечує хід металу в подовжньому напрямі.
Осідання – операція кування, при якій відбувається збільшення перетину заготовки за рахунок зменшення висоти (рис. 2.5,а). Для того, щоб при осіданні не виходив вигин заготовки, відношення висоти заготовки до її діаметра повинне складати не більше ніж 3:1. Осіданням виготовляють заготовки для шестерень, фланців і дисків, оскільки при цьому виходить найсприятливіший напрям волокон.
Висадкою називається операція, що полягає у збільшенні перетину заготовки за рахунок зменшення її висоти. При висадці проводять місцевий нагрів заготовки (рис. 2.5,б). Висадкою виготовляють болти, заклепки і тому подібні кріпильні вироби.
Гнуттям називають операцію кування, за допомогою якої заготовці або її частині надається зігнута форма. Гнуття проводять також з місцевим нагрівом заготовки. Для того, щоб не змінився перетин у місці вигину, необхідно в цьому місці провести висадку. Для отримання точної форми виробів гнуття дуже часто здійснюють за допомогою підкладних штампів.
Прошивка – це операція для отримання в заготовці отвору або поглиблення за допомогою пробійників різної форми або прошивкою. Пробійником одержують отвори в тонких заготовках, а прошивкою – в товстих. Прошивку здійснюють у декілька переходів. Спочатку прошивнем 1 (рис. 2.5,в) намічають отвір (положення І) і заглиблюють його за допомогою підставки 2 і 3 майже на всю висоту заготовки (положення ІІ), потім заготовку перевертають на 1800 і прошивнем виштовхують залишок металу (положення ІІІ). При прошивці особливо товстих заготовок застосовуються трубчасті пустотілі пробійники. Обробку проводять гладилками і обтисканнями для отримання точного профілю і гладкої поверхні.
Рисунок 2.5 – Операції вільної ковки
Технологічний процес вільного кування є сукупністю описаних вище елементарних ковальських операцій, виконуваних у певній послідовності, пов'язаних із зміною форми початкової заготовки.
Як матеріал для вільного кування використовують зливки, блюм, прокат.
При штампуванн і хід металу обмежений стінками робочої порожнини штампу і відбувається по заданих напрямах до визначеної межі. Форма і розміри робочих порожнин (рівчаків) штампу повністю визначаються конфігурацією майбутньої поковки.
Штампи за конструкцією бувають однорівчаковими і багаторівчаковими. Однорівчакові штампи застосовують для отримання деталей простої форми, багаторівчакові – для складних деталей. Для виготовлення поковок методом гарячого штампування застосовуються штампувальні молоти, кривошипні, кувально-штампувальні преси, горизонтально-кувальні машини, ротаційно-кувальні машини, кувальні вальці. На вибір того або іншого устаткування для штампування впливають форма і розміри поковки, що виготовляється, її матеріал, необхідна точність і інші чинники.
Гаряче штампування в порівнянні з куванням має ряд переваг:
1. Висока продуктивність, що в десятки разів перевищує продуктивність вільного кування.
2. Однорідність, точність штампованих поковок.
3. Висока якість поверхні поковок, одержуваних гарячим штампуванням не вимагає механічної обробки (обробляти доводитися тільки в місцях сполучення деталей).
Недоліки:
1. Невелика маса поковок (звичайно до 200-300 кг).
2. Висока вартість штампів.
2.3 ОБРОБКА МЕТАЛІВ РІЗАННЯМ
1. Загальні відомості про обробку металів різанням.
2. Різальний інструмент.
3. Обробка на токарних верстатах.
4. Обробка на свердлильних верстатах.
5. Обробка на фрезерних верстатах.
6. Обробка шліфуванням.
7. Верстати з числовим програмним керуванням.
1 Процес різання металів полягає в тому, що зрізається з оброблюваної заготовки шар металу – припуск, спеціально залишений на обробку, з метою отримання деталі із заданими кресленням формою, розмірами і шорсткістю поверхонь.
Основними видами обробки різанням є точіння, стругання, свердління, фрезерування і шліфування. Обробка металів різанням здійснюється на металорізальних верстатах – токарних, строгальних, свердлильних, фрезерних і шліфувальних – з використанням основних різальних інструментів – різців, свердел, фрез, шліфувальних кругів.
Метал, що видаляється у процесі різання – припуск – перетворюється на стружку, при цьому наявність стружки є характерною ознакою всіх різновидів процесу різання металів.
Для здійснення процесу різання необхідно мати головний рух різання і рухи подачі. Головний рух різання (головний рух) має найбільшу швидкість і називається швидкістю різання. Рух подачі має швидкість меншу, ніж швидкість головного руху різання, і призначений для того, щоб зрізати припуск зі всієї поверхні, що підлягає обробці. Цей рух називається подачею. Головний рух і рух подачі залежно від виду обробки можуть бути обертальним або прямолінійно-поступальним і задаватися як заготовкою, так і різальним інструментом.
При точінні головний рух – обертальний рух заготовки, рух подачі – прямолінійно-поступальний рух різального інструменту - різця. Переміщенням різця щодо заготовки зрізається її початкова поверхня, яка називається оброблюваною поверхнею.
При струганні головний рух передається різцю, а рух подачі – заготовці або як головний рух, так і рух подачі передається тільки різцю.
При свердлінні (зенкеруванні і розгортанні) як головний рух, так і рух подачі звичайно передається різальному інструменту – свердлу (зенкеру, розгортці), проте є схеми свердління, згідно з якими головний рух передається заготовці.
При фрезеруванні головний рух передається різальному інструменту – фрезі, а рух подачі – заготовці, проте є схеми фрезерування, згідно з якими як головний рух, так і рух подачі передається фрезі.
При круглому і плоскому шліфуванні головний рух передається різальному інструменту – шліфувальному кругу, а рух подачі – заготовці.
2 Різальним інструментом називається інструмент для обробки металів різанням. Металорізальний інструмент може зрізати шар матеріалу з поверхні заготовки в тому випадку, якщо його різальна частина виготовлена або оснащена інструментальним матеріалом, що володіє високою твердістю, міцністю, температуростійкістю і стійкістю проти спрацювання.
Як інструментальні матеріали для лезвених інструментів використовують швидкорізальні сталі, тверді сплави (металокераміка), мінералокерамічні сплави (кермети), надтверді матеріали, синтетичні алмази.
Швидкорізальні інструментальні сталі є високолегованими сталями з добавками вольфраму, молібдену, ванадію, кобальту при вмісті приблизно 4% хрому і 1% вуглецю. Твердість сталей знаходиться в межах НRА 62-64, температуростійкість 620-640оС.
Тверді сплави поділяються на три групи: вольфрамокобальтову(ВК), вольфрамотитанокобальтову (ТК) і вольфрамотитанотанталокобальтову (ТТК). Твердість вказаних твердих сплавів складає НRА 87-91, температуростійкість 800-1250 оС. Покриття твердих сплавів тонким шаром (5-15 мкм) карбитів (титану, ніобію), боритів, нітридів дозволяє підвищити їх стійкість проти спрацювання у 5-6 разів.
Основою мінералокерамічних сплавів (керметов) є корунд-оксид алюмінію Аl2О3. Температуростійкість мінералокераміки і керметів складає 1500-1300 оС.
Надтверді матеріали є синтетичними матеріалами на основі гексагонального або кубічного нітриду бору, який за твердістю перевершує кермети і поступається тільки синтетичному алмазу. Температуростійкість композитів і нітриду бору досягає 1300-1800 оС.
Синтетичні алмази утворюються при спіканні вуглецю під високим тиском і при значній температурі. Температуростійкість алмазів невелика – приблизно 650оС.
У процесі різання при переміщенні різального інструменту щодо заготовки йому доводиться долати силу опору пластичної деформації оброблюваних матеріалів, силу опору пластично деформованих шарів металу руйнуванню в місцях виникнення нових (оброблених) поверхонь і сили тертя стружки по передній поверхні інструменту і обробленій поверхні об його задні поверхні. Результуюча цих сил називається силою різання.
3. Точіння проводиться на токарних верстатах і застосовується для обробки зовнішніх і внутрішніх тіл обертання: циліндрових, конічних, сферичних і фасонних.
При точінні заготовка закріплюється у встановленому на шпінделі верстата патроні і обертається, а закріплений у резцетримачі різець здіснює поступальний рух в подовжньому і поперечному напрямах.
Токарно-гвинторізний верстат загального призначення показаний на рисунку 2.6. На основі 1 закріплені станини 11 і корито 12 для збору стружки. На станині 11 розміщені передня бабка 3 з коробкою швидкостей для обертання заготовки з різною частотою і коробки подач 2 для переміщення різального інструменту з різними подачами. По направляючих станини 11 переміщається супорт 6 із закріпленим в різцетримачі різцем і фартухом, а також задня бабка 7, призначена для підтримки кінця довгої заготовки. Привод верстата – електродвигун – встановлений в основі 1 і закритий кожухом.
Рисунок 2.6 – Токарно-гвинторізний верстат
Рух від коробки швидкостей 2 передається механізмам фартуха 9 через ходовий вал 8 (при точінні) або через ходовий гвинт 10 (при нарізуванні різьблення різцем). На передніх стінках передньої бабки 3, коробки передач 2 і фартуха 9 розташовані рукоятки керування верстатом. Екран 4 і щиток 5 забезпечують безпеку роботи на верстаті. Електроустаткування верстата зосереджено в електрошафі 13.
4 Свердлильні верстати призначені для виготовлення отворів у деталях. Для підвищення точності і якості отворів після їх обробки свердлами, використовуються зенкери і розгортки. Основні частини і конструкції свердла, зенкера і розгортки приведені на рисунку 2.7.
Свердла, зенкери і розгортки застосовуються для виготовлення наскрізних, глухих, східчастих і глибоких отворів з відношенням глибини отвору до його діаметра більше п'яти.
Обробку отворів проводять на вертикально- і радіально-свердлильних верстатах з вертикальним розташуванням шпінделя.
На вертикально-свердлильному верстаті (рисунок 2.8) оброблювана деталь закріплюється на столі 2, який за допомогою гвинта 1 встановлюється на певну висоту залежно від висоти заготовки і закріплюється рукояткою 8 щодо станини 9. Різальний інструмент закріплюється в шпінделі 3, одержуючому обертальний рух від електродвигуна 7 через коробку швидкостей 6 і рух подачі від коробки подач 5. Вертикальне переміщення шпінделя 3 також може здійснюватися вручну за допомогою маховика 4.
Рисунок 2.7 – Основні частини і Рисунок 2.8 - Вертикально-свердлильний