Стеклообразное состояние является основной разновидностью аморфного состояния вещества. Стеклами называют аморфные тела, получаемые путем переохлаждения расплава независимо от их химического состава и температурной области затвердевания, приобретающие в результате постепенного увеличения вязкости механические свойства твердых тел, причем процесс перехода из жидкого состояния в твердое является обратимым.
В настоящее время в составы стекол введена большая часть элементов Периодической системы Д. И. Менделеева. По химическому составу имеющие практическое значение стекла делятся на три основных типа: оксидные – на основе оксидов (SiО2, GeО2, В2О3, Р2О5, А12О3), галогенидные – на основе галогенидов (BeF2, фторберилатные стекла), халькогенидные – на основе сульфидов, селенидов и теллуридов.
Наиболее широко применяются оксидные стекла, которые в зависимости от состава делятся на ряд классов и групп:
- по виду оксида-стеклообразователя – силикатные, боратные. фосфатные, германатные, алюмосиликатные и т.д;
- по содержанию щелочных оксидов – бесщелочные (могут содержать щелочно-земельные оксиды MgO, СаО, ВаО), малощелочные, многощелочные.
Получение стекол производится путем «варки» исходных компонентов стекла в стекловаренных печах и при быстром охлаждении расплавленного материала. При расплавлении шихты в результате реакции составляющих оксидов и удалении летучих составных частей (Н2О, СО2, SO3) получается однородная стекломасса, которая и идет на выработку стеклянных изделий. Изготовленные стеклянные изделия подвергаются отжигу при достаточно высокой температуре с последующим медленным охлаждением для устранения механических напряжений.
Физико-химические свойства стекла. Наиболее высокие показатели механических свойств имеют кварцевые и бесщелочные стекла, а наиболее низкие – стекла с повышенным содержанием оксидов PbO, Na20, К2О
Плотность стекол обычно находится в пределах 220-6500кг/м3. Теплопроводность стекла по сравнению с другими телами исключительно низкая (наибольшую теплопроводность имеют кварцевое и боросиликатное стекла). Термическая стойкость стекла прямо пропорциональна его прочности при разрыве и обратно пропорциональна его упругости и коэффициенту линейного расширения.
Химическая устойчивость стекла зависит от сопротивляемости его разрушающему воздействию различных реагентов — воды, кислот, щелочей. Для электротехнических стекол химическая устойчивость имеет в ряде случаев существенное значение. Наибольшей стойкостью к воздействию влаги обладает кварцевое стекло. Гидролитическая стойкость стекол сильно уменьшается при введении в состав стекла щелочных оксидов.
Электрические свойства стекла. Они в сильной степени зависят от состава стекла. Большинство стекол характеризуется ионной проводимостью. Некоторые специальные виды стекол – халькогенидные, ванадиевые (полупроводниковые) – имеют электронную или смешанную проводимость. Наиболее сильно понижают электропроводность стекол SiО2 и В2О3. Наименьшую электропроводность имеет кварцевое стекло, а наибольшую – высокощелочные. Обычно более химически устойчивые стекла имеют меньшую электропроводность. Электропроводность стекол очень быстро возрастает при увеличении температуры из-за увеличения подвижности ионов. Удельное объемное сопротивление промышленных стекол при невысоких температурах колеблется в пределах 108-1015Ом∙м. Заметный вклад в электропроводность стекол вносит поверхностная проводимость, сильно зависящая от адсорбированной водяной пленки.
Диэлектрические потери в стеклах складываются из потерь проводимости и потерь релаксационных и структурных; tgδ стекол увеличивается с ростом содержания щелочных оксидов при малом содержании оксидов тяжелых металлов. Стекла с большим содержанием оксидов РЬО и ВаО имеют низкий tgδ.
Самую низкую диэлектрическую проницаемость имеет кварцевое стекло (εr=3,7-3,8) и стеклообразный борный ангидрид (εr=3,1-3,2) у которых наблюдается преимущественно электронная поляризация. При наличии в составе стекол оксидов металлов свинца и бария, обладающих высокой поляризуемостью, εrстекол увеличивается и становится высокой (около 20).
Пробой стекол вызывается электрическими и тепловыми процессами. При постоянном напряжении электрическая прочность стекла весьма велика и достигает 500МВ/м, а при увеличении температуры резко снижается. В переменном электрическом поле электрическая прочность стекол составляет 17-80МВ/м.
Наиболее высокими свойствами обладает кварцевое стекло, выплавляемое из горного хрусталя или чистых кварцевых песков. Кварцевые стекла отличаются высокой оптической прозрачностью, механической прочностью при высоких температурах (свыше 1000°С), инертностью к действию многих химических реагентов, высокими электрическими характеристиками: при нормальной температуре tgδ=0,0002; εr=3,8; ρ v при 200°С около 1015Ом∙м.
Кварцевое стекло находит применение для изготовления различных изделий в электрорадиовакуумной промышленности: трубчатые, опорные и проходные изоляторы для электрических газоочистительных установок, высоковольтные изоляторы для высоковольтных линий, различные детали переменных конденсаторов, катушек самоиндукции, ламп, приборов, аппаратов и пр.
Рис. 8.5. Высоковольтный линейный подвесной стеклянный изолятор ПС-4-5: 1 – изоляционная деталь из закаленного стекла (а – тарелка, б - головка, в – шейка, г – ребра); 2 – шапка (ковкий чугун); 3 – стержень (сталь Ст3); 4 – замок (сталь); 5 – цементно-песчаная связка; 6 – прокладка (толь или кожа). |
Разнообразие и особенности свойств полупроводниковых стекол открывают широкие возможности для их применения в электронных приборах и устройствах, например в термосопротивлениях, в светофильтрах и фотосопротивлениях, сочетающих избирательное поглощение света с повышенной электропроводностью.
Электрическая керамика. Она представляет собой материал, получаемый в результате отжига формовочной массы заданного химического состава из минералов и оксидов металлов. При соответствующем выборе состава керамики из нее можно получить материалы, обладающие разнообразными свойствами. В электротехнической и радиоэлектронной промышленности керамическая технология применяется для изготовления диэлектрических, полупроводниковых, пьезоэлектрических, магнитных, металлокерамических и других изделий. Многие керамические материалы имеют высокую механическую прочность и нагревостойкость. высокие электрические характеристики, отсутствие механических деформаций при длительном приложении нагрузки, большую, чем у органических материалов, устойчивость к электрическому и тепловому старению. Керамику можно подвергать металлизации обычно методом выжигания серебра и осуществлять герметичные спаи с металлом.
Широкое применение в качестве электроизоляционного материала находит электротехнический фарфор, который является основным керамическим материалом, используемым в производстве широкого ассортимента низковольтных и высоковольтных изоляторов и других изоляционных элементов с рабочим напряжением до 1150кВ переменного и до 1500кВ постоянного тока. Электротехнический фарфор, как и любая керамика, состоит из кристаллической, аморфной и газовой фаз. Его свойства определяются химическим и фазовым составом, микро- и макроструктурой и технологией изготовления.
Рассмотрим основные особенности керамической технологии на примере электротехнического фарфора. Основными компонентами фарфора являются сырьевые материалы минерального происхождения – глинистые вещества (каолин и глина, кварц, полевой шпат, гипс, пегматит). Глинистые вещества в сыром виде при замешивании их с водой обладают свойствами пластичности и при достаточно высокой температуре способны спекаться. Пластичность глинистых веществ дает возможность формовать их них изделия различной формы, которая сохраняется после сушки и обжига при высоких температурах. Изделия, изготовленные из глинистых веществ, дают большую усадку при сушке и при обжиге, кроме того, они склонны к образованию трещин. Температура спекания таких веществ высока. Поэтому в состав фарфора вводят «отощающие» материалы, снижающие усадку и деформацию изделий при сушке. Такими материалами служат кварц и битые фарфоровые изделия. Полевой шпат и пегматит являются плавнями при образовании фарфора: они плавятся при более низких температурах, чем глинистые вещества и кварц. Главной составной частью каолина является гидроалюмосиликат, называемый глинистым веществом или каолинитом, его состав А12О3∙2SiO∙2Н2О – это высокосортная глина. В воде каолин образует суспензию. Пластичные огнеупорные глины в качестве составной части содержат каолинит. Кварц состоит из кремнезема SiО2 с ничтожными примесями. Полевые шпаты представляют собой безводные алюмосиликаты, содержащие ноны Na+, К+, Са2+. Пегматит состоит из полевого шпата и кварца. Твердые компоненты фарфоровой массы подвергаются грубому и тонкому помолу и после добавления небольшого количества воды взмучиваются, образуя суспензию, и подаются в сборники через вибросито и магнитные сепараторы. Затем на фильтр-прессах отжимается избыточная вода и масса после проминки в вакуумных прессах, проходя через мундштук определенной формы, превращается в заготовки требуемой длины, которые и подаются на формовку.
Рис. 8.6. Изоляторы: а – опорный группы А и Б на 6кВ; б – проходной группы Б на 6кВ. |
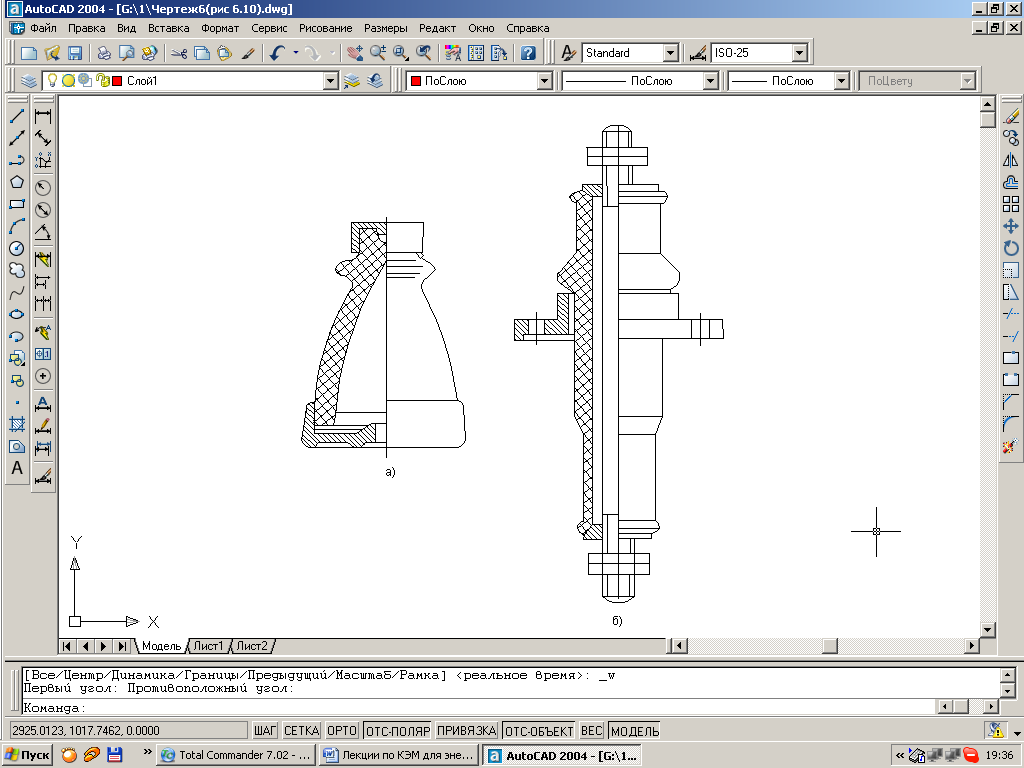
Наличие стекловидной фазы определяет довольно высокую механическую прочность фарфора. Фарфор имеет высокий предел прочности на сжатие (400-700МПа), значительное меньший предел прочности при растяжении (45-70МПа) и при изгибе (80-150МПа). Электроизоляционные свойства фарфора при нормальной температуре позволяют использовать его при низких частотах: εr≈6-7, tgδ ≈ 0,02. Однако tgδ электротехнического фарфора быстро растет при увеличении температуры, что затрудняет применение его при высоких температурах и на высоких частотах.
Электротехнический фарфор находит применение для изготовления высоковольтных и низковольтных изоляторов различного типа. К числу высоковольтных изоляторов относятся: 1) стационарные для оборудования распределительных устройств и аппаратуры – опорные, проходные, вводы, маслонаполненные покрышки разного назначения; 2) линейные для линий электропередачи – подвесные и штыревые. На рис. 8.6 показаны некоторые типы изоляторов, изготовляемые из электротехнического фарфора.
Для изготовления высокочастотных высоковольтных изоляторов применяют стеатитовую керамику, так как фарфор имеет сильную зависимость электрических характеристик от температуры из-за наличия большого количества полевошпатового стекла с повышенной электропроводностью. Стеатитовая керамика изготовляется на основе тальковых минералов, основной кристаллической фазой которых является метасиликат магния MgO-SiО2. Стеатитовые материалы характеризуются высокими значениями ρ, в том числе при высокой температуре, малым tgδ, за исключением материала группы 210 ГОСТ20419-83, предназначенного для производства крупных высоковольтных изоляторов. Стеатитовая керамика характеризуется высокими механическими свойствами, стабильностью параметров при воздействии различных внешних факторов (влаги, температуры, высокого напряжения и др.). Благодаря высоким электромеханическим свойствам стеатит нашел применение для изготовления высокочастотных установочных деталей, высоковольтных и низковольтных конденсаторов, высоковольтных антенных внутриламповых пористых и других изоляторов. Пластичный высокочастотный высоковольтный стеатитовый материал СПК-2 применяется для изготовления крупногабаритных изоляторов, а непластичные СНЦ, СК-1, Б-17, С-55 и С-4 – для изготовления электроизоляционных деталей и высокочастотных конденсаторов.
Для применения в радиотехнической и электронной промышленности было разработано большое количество новых керамических материалов, обладающих повышенными свойствами по сравнению с фарфором. Отметим лишь некоторые из этих материалов.
Радиофарфор представляет собой фарфор, стекловидная фаза которого облагорожена введением в нее тяжелого оксида ВаО. Ультрафарфор различных марок характеризуется большим содержанием А12О3 и является дальнейшим усовершенствованием радиофарфора. Ультрафарфор имеет по сравнению с обычным фарфором повышенную механическую прочность и теплопроводность.
Высокоглиноземистая керамика (алюминооксид) в основном состоит из оксида алюминия (глинозема) А12О3. Это материал требует весьма высокой температуры обжига (до 1750°С), затрудняющей его изготовление. Он отличается высокими характеристиками: нагревостойкостью до 1600°С. высоким ρ и малым tgδ при повышенных температурах, чрезвычайно высокой теплопроводностью и механической прочностью. Поликор, имеющий особо плотную структуру (близкую к теоретической для А12О3), обладает оптической прозрачностью и применяется для изготовления колб некоторых специальных источников тока. Электрические характеристики некоторых высокочастотных керамических материалов приведены в табл. 8.5.
Таблица 8.5
Электрические характеристики некоторых высокочастотных керамических материалов.
Материал | tgδ·104 при 1МГц | Электрическая прочность при 20°С и 50Гц, МВ/м | |
При 20°С | При 100°С | ||
Радиофарфор Ультрафарфор Стеатит Ультрастеатит | 35-45 6-9 12-20 3-6 | 50-60 16-18 15-24 6-10 | 15-20 15-20 20-30 20-30 |
Конденсаторная керамика имеет повышенные (εr=10-230) и высокие (εr=900) значения диэлектрической проницаемости. В первом случае керамика относится к высокочастотным диэлектрикам и tgδна частоте 1МГц не должен превышать 0,0006, во втором случае керамика низкочастотная – на частоте 1000Гц tgδ=0,002-0,025. К конденсаторной керамике обычно предъявляется требование возможно меньшего значения температурного коэффициента диэлектрической проницаемости. Многие из конденсаторных материалов имеют в своем составе диоксид титана – рутил (TiO2). В принятом обозначении такие составы имеют букву Т («титановая керамика»); последующая цифра обычно обозначает номинальную диэлектрическую проницаемость. Эти материалы называют также тикондами. Среди них можно выделить керамику на основе титанатакальция и титаната стронция – СаТiO3 и SrTiO3. При высоких частотах у этих материалов температурная зависимость tgδ выражена слабо, однако эти виды материалов характеризуются пониженной электрической прочностью ( 8-12МВ/м). При длительной выдержке под постоянным напряжением тикондовая керамика подвергается электрохимическому старению. Из-за высокого отрицательного значения температурного коэффициента εr эти материалы применяются для конденсаторов, к которым не предъявляются требования температурной стабильности емкости. Для повышения температурной стабильности в керамику вводят компоненты с положительным значением температурного коэффициента εr. Такие материалы часто называют термокомпенсированными. К этой группе относятся титаноциркониевая керамика ТiO2–ZrO2 , CaTiO3–CaZrO3; лантановая керамика системы LаАlO3–СаТiO3, станнатная и другие керамические материалы. Преимуществом беститановой керамики является более высокая устойчивость к воздействию постоянногонапряжения.
В ряде случаев для изготовления конденсаторов применяют ультрафарфор, стеатит и другие виды установочной керамики.
Основу низкочастотной керамики составляют титанат бария ВаТiO3и твердые растворы на его основе. Эти материалы отличаются высокими значениями диэлектрической проницаемости и ее нелинейной зависимостью от напряженности электрического поля.