ТЕМА 1: Классификация металлорежущих станков.
|
Классификация станков по технологическому назначению.
Группа токарных станков предназначены для обработки поверхностей вращения. Объединяющим признаком станков является движение резанием - вращательное движение заготовки и движение подачи - продольное или поперечное движение инструмента.
Группа сверлильных станков включает также, и расточные станки выполняют обработку круглых отверстий. Движением резания – вращательное движение инструмента, которому обычно сообщается движение подачи. В горизонтально-расточных станках подача может осуществляться перемещением стола с обрабатываемой деталью.
|
|
Группа фрезерных станков применяются для обработки плоскостей и фасонных поверхностей, в качестве режущего инструмента используется многолезвийные инструменты — фрезы.
Группа строгальных станков состоит из станков, у которых общим признаком является использование в качестве движения резания прямолинейного возвратно-поступательного движения резца или обрабатываемой детали.
Группа разрезных станков включает все типы станков, предназначенных для разрезки и распиловки катаных материалов (прутки, уголки, швеллеры и т. п.).
Группа резьбонарезных станков включает все станки (кроме станков токарной группы), предназначенные специально для изготовления резьбы.
Группа зубообрабатывающих станков служат для обработки зубьев колес, в том числе и шлифовкой.
Группа протяжных станков имеет один общий признак: использование в качестве режущего инструмента специальных многолезвийных инструментов — протяжек.
Группа шлифовальных станков объединяется по признаку использования в качестве режущего инструмента абразивных шлифовальных кругов.
Группа полировальных и доводочных станков объединяется по признаку использования в качестве режущего инструмента абразивных брусков, лент, порошков и паст.
Классификация станков по степени универсальности.
- Специализированные станки предназначены для выполнения одной операции на однотипных деталях широкого диапазона размеров;
- Специальные станки предназначены для обработки конкретной детали или однотипных деталей небольшого диапазона размеров.
- Универсальные станки могут выполнять более трех операций, в том числе и с применением приспособлений на большой номенклатуре деталей большого диапазона размеров;
- Станки широкого назначения могут выполнять до трех операций на деталях широкой номенклатуры;
|
|
|
- легкие – весом до 1 тонны;
- средние – весом до10 тонн;
- крупные – весом до 30 тонн;
- тяжёлые – весом до 100 тонн;
- уникальные – весом свыше 100 тонн.
Классификация станков по точности.
- нормальной точности, обозначаются буквой Н (обычно не обозначаются);
- повышенной точности – П;
- высокой точности – В;
- особо высокой точности – А;
- особо точные – С (мастер – станки).
Правила обозначения моделей станков.
Первая цифра обозначает принадлежность станка к технологической группе.
Вторая цифра обозначает принадлежность станка к определенному тип.
Третья или третья и четвертая цифры обозначают основной размер станка.
Буква стоящая между первой и второй цифрой или второй и третьей обозначает модернизацию. Модификация станка сопровождается изменением конструкции отдельных узлов станка без изменения основных характеристик Буквы Н, П, В, А,С обозначают класс точности, буква М обозначает наличие у станка магазина инструментов и, или заготовок. Буква Ф обозначает наличие системы числового программного управления станком. Цифра стоящая сразу за буквой Ф обозначает тип системы числового программного управления. 1 – система цифровой индикации, 2 – позиционная система управления, 3 – контурная система управления, 4- комбинированная система управления.
Примеры:
16К20П
1-токарный (группа станка),
6- токарно-винторезный (тип станка),
К- завод-изготовитель,
20- основной размер(максимальный диаметр обрабатываемой заготовки),
П- повышенный класс точности.
6Р13Ф3
6-фрезерный (группа станка),
Р- завод изготовитель,
1- вертикально-фрезерный консольный (тип станка),
3- основной размер (максимальный размер рабочей поверхности стола),
Ф3- контурная система ЧПУ.
|
и их назначение.
Станина установлена на тумбах и служит для монтажа всех основных узлов станка и является его основанием. На станине монтируются передняя и задняя бабки, суппорт и коробка подач.
Передняя (шпиндельная) бабка крепится на левом конце станины. В ней размещена коробка скоростей и шпиндель, которые сообщают заготовке главное движение, а инструменту – движение подачи при выбранной глубине резания.
Шпиндель служит для крепления заготовки с помощью приспособлений и сообщения ей вращательного движения. Вал шпинделя делается полым для размещения в нем обрабатываемого прутка. Передний конец шпинделя имеет конусное отверстие, в которое при необходимости устанавливается центр. К торцу шпинделя крепится на резьбе или болтами кулачковый или поводковый патрон для закрепления обрабатываемых заготовок.
Коробка скоростей обеспечивает различных числа оборотов шпинделя в минуту. На передней панели коробки скоростей расположены рукоятки для установки числа оборотов шпинделя, рукоятка установки числа заходов резьбы и рукоятка установки правой и левой резьбы.
Коробка подач расположена на передней стороне станины под передней бабкой. Она обеспечивает получение необходимой величины подачи инструмента или шага нарезаемой резьбы с помощью рукояток. Передача к коробке подач осуществляется от шпинделя через гитару со сменными зубчатыми колесами. Далее движение через ходовой вал (при точении) или ходовой винт (при нарезании резьбы) передается на суппорт.
|
|
Суппорт служит для сообщения резцу движения подачи. Нижняя часть суппорта, называемая продольными салазками или кареткой, движется по направляющим станины при продольной подаче.
На Каретке Суппорта установлены Продольная и Поперечная салазки. На поперечных салазках расположен верхний поворотный суппорт с резцедержателем. Верхний суппорт используется при обтачивании конических поверхностей. Для этого его поворачивают на необходимый угол. Подачу суппорта осуществляют рукояткой.
Резцедержатель служит для установки и крепления резцов. Он имеет четыре позиции, что позволяет установить одновременно четыре инструмента и менять их, поворачивая резцедержатель рукояткой.
Фартук крепится к каретке суппорта. В нем расположен механизм, при помощи которого вращательное движение ходового вала или ходового винта преобразуется в поступательное прямолинейное (продольное или поперечное) движение суппорта. Рукоятка служит для включения маточной гайки (при нарезании резьбы).
Задняя бабка служит для поддержания обрабатываемой заготовки при работе в центрах, а также для закрепления сверл и других инструментов при обработке осевых отверстий. Корпус задней бабки установлен на направляющих станины и может по ним перемещаться. В отверстии корпуса имеется пиноль, которая выдвигается с помощью маховика. Корпус задней бабки смещается относительно ее основания в поперечном направлении, что необходимо при обтачивании наружных конических поверхностей.
Гитара сменных колес служит для передачи вращения от передней бабки к коробке подач и для изменения передаточного отношения этой передачи в целях обеспечения нарезания всех типов резьбы.
|
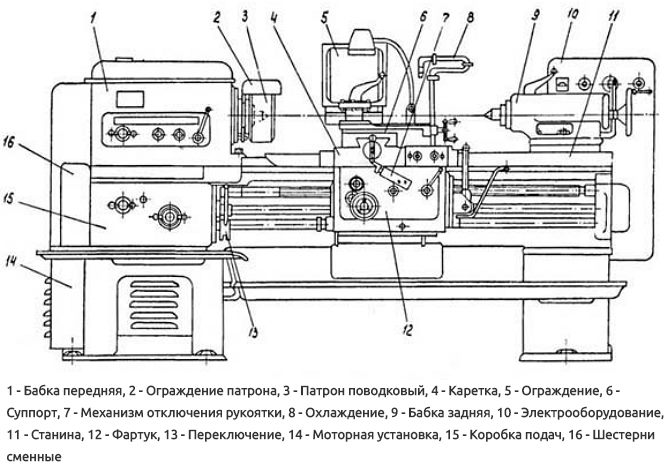
|
Материалы резцов.
Для токарной обработки применяют разнообразные резцы. В зависимости от направления движения подачи различают левые и правые резцы (рис. 1, а, б).
По форме и расположению головки относительно стержня резцы могут быть прямые, отогнутые и оттянутые. По назначению различают: проходные, упорные, подрезные (торцовые), прорезные, отрезные, фасонные, резьбовые и расточные резцы. Резцы подразделяются также на черновые, служащие для предварительной обработки, и чистовые, предназначенные для окончательной (чистовой) обработки.
Резцы могут быть цельные, выполненные из одного материала, и составные: державка из конструкционной стали, а режущая часть резца из специального инструментального материала. Составные резцы бывают сварные, с напаянной режущей пластинкой и с механическим креплением режущей пластинки.
Рабочая часть режущего инструмента, в том числе резца, должна обладать высокой твердостью, красностойкостью (способностью не терять твердости при высокой температуре), высокой износостойкостью (сопротивлением истиранию), а также высокой вязкостью (сопротивлением ударной нагрузке). Материалы, из которых изготовляются рабочие части режущих инструментов, должны отвечать указанным требованиям.
Первая группа — материалы дня инструментов, работающих на низких скоростях резания. К ним относятся высококачественные углеродистые инструментальные стали (У10А, У11А, У12А) твердостью ИКС 60—64 после закалки. Инструмент из этих сталей сохраняет режущие свойства при температуре нагрева только до 200—250°С, поэтому применяется редко. В эту группу входят также легированные инструментальные стали: хромокремнистая 9ХС, хромовольфрамовая ХВ5, хромомарганцовистая ХВГ и др., имеющие красностойкость 250—300°С.
Вторая группа — материалы для инструментов, работающих на повышенных скоростях резания, — быстрорежущие стали Р9, Р12, Р6М5, Р9К5Ф2 и др. После термической обработки эти стали приобретают высокую твердость (ИКС 62—65), высокую износостойкость и красностойкость до.650°С.
Третья группа — материалы для инструментов, работающих на высоких скоростях резания металлокерамические твердые сплавы, выпускаемые в виде пластинок различных размеров и форм. Красностойкость твердого сплава достигает 1000°С. Для обработки чугуна, а также цветных металлов и сплавов применяют твердые сплавы вольфрамокобальтовой группы (ВК): ВК8 — для обдирочной обработки, ВК6 – для получистовой и чистовой обработки. Для обработки сталей применяют твердые сплавы титановольфрамокобальтовой группы (ТК): Т5К10 — для черновой обработки и при прерывистом резании. Т15К6—для получистовой и чистовой обработки.
|
поверхностей.
Существуют несколько способов обработки цилиндрических поверхностей, используемых в зависимости от требуемой конфигурации детали - формы, диаметра, длины и степени её шероховатости.
Самым распространенным является обтачивание — черновое (обдирочное) и чистовое. Черновое обтачивание, применяемое при грубой и предварительной обработке заготовок, выполняется на более высокой скорости работы оборудования и отличается снятием стружки большего сечения.
Задача таких токарных работ состоит в том, чтобы изготовить деталь цилиндрической формы в точном соответствии с установленными параметрами. Тем не менее, допускается незначительное отклонение размеров в пределах погрешностей, прописанных в рабочих чертежах. Если они не указаны, их величина устанавливается в размере допуска на диаметр. Также делается припуск 0,3 – 0,6 мм на шлифование.