Механизм образования поверхностных соединений, их адгезия к металлу и свойства влияют на процесс коррозии. В свою очередь, эти показатели во многом определяются структурой и составом металла. Металлы имеют кристаллическую структуру, в узлах которой расположены положительно заряженные ионы, а электроны свободно перемещаются в металле. Наименьшая часть пространственной решетки называется элементарной ячейкой. Если эта ячейка является кубом, то и соответствующая ей решетка будет кубической. Простой кубической решеткой называется такая решетка, у которой атомами или ионами заняты лишь вершины ее элементарных ячеек. Такой тип решетки имеют, например, кристаллы поваренной соли NaCl.
Решетка, у которой кроме вершин атомом или ионом занят центр, называется объемно-центрированной. Такое кристаллическое строение имеют литий, натрий, калий, ванадий, хром, α–железо (при температурах до 900 °С).
Гранецентрированной называется такая решетка, у которой материальными частицами заняты центры граней. Такой тип кристаллической решетки имеют алюминий, никель, медь, свинец, серебро, золото, платина, γ–железо (в интервале температур 900-1400 °С)
|
|
Гексагональная ячейка имеет в основании шестиугольник. По такому принципу кристаллизуются бериллий, марганец, кадмий, титан и др.
Различают также плотноупакованные кристаллографические плоскости и решетки.
В ряде случаев кристаллографическая структура определяет коррозионную устойчивость металлов и их сплавов. Реальные металлические материалы, как правило, являются поликристаллическими, то есть состоят из множества отдельных кристаллов, которые в общем случае имеют неправильную форму и называются кристаллитами, или зернами. В отличие от идеальных кристаллов, в которых атомы кристаллической решетки расположены строго периодично, реальные кристаллы всегда имеют нарушения регулярности структуры (разупорядоченность), которые называются дефектами. Основными причинами отсутствия у реальных конструкционных металлических материалов идеального кристаллического состояния являются неравновесные условия кристаллизации металла, присутствие в его составе легирующих и примесных элементов, деформация кристаллической решетки вследствие воздействия на нее в процессе изготовления изделий механических, термических, радиационных и других факторов [1-4, 24]. Дефекты кристаллических решеток изменяют заданные свойства металлов, влияют на его химические и электрохимические характеристики [1]. Дефекты структуры, выходящие на поверхность металла, обладают повышенной реакционной способностью, и они являются первыми очагами коррозии. Посторонние примеси концентрируются у линейных дислокаций и дырок по границам зерен. Эти сегрегации могут увеличивать окисление металла, облегчать образование питтингов. Любой вид неоднородности усиливает как химическую, так и электрохимическую коррозию.
|
|
Наличие примесей, очагов остаточного напряжения приводит к увеличению скорости коррозии. Для того чтобы уменьшить или устранить эти явления, проводят технологические операции: закалку, отжиг и т.д.
Известны четыре типа точечных дефектов: вакансии, примесные атомы замещения и внедрения, дислоцированные атомы и дефекты Френкеля (рис. 1.1).
Вакансии (рис. 1.1, а) – наиболее часто встречающиеся точечные дефекты, которые представляют собой свободные узлы в кристаллической решетке. Вакансии возникают за счет тепловых колебаний атомов, при воздействии на металл механических напряжений, радиоактивного излучения и других факторов. При образовании вакансий кристаллическая решетка искажается, а ближайшие атомы смещаются от своего равновесного состояния.
Рис. 1.1. Точечные дефекты в кристаллах:
а – вакансия; б – дислоцированный атом; в – дефект Френкеля;
г – примесные атомы внедрения
(стрелками указаны направления смещения атомов в кристаллической решетке)
Дислоцированные атомы (рис. 1.1, б) – атомы основного металла, смещенные из своих равновесных положений в межузельные пространства; местами их расположения являются пустоты наибольшего объема. Если вакансии и дислоцированные атомы образуются одновременно, то возникают парные дефекты, называемые дефектами Френкеля (рис. 1.1, в), концентрация которых в металлических материалах ниже, чем остальных точечных дефектов. Точечные дефекты существенно влияют на процессы диффузии ионов металла при образовании поверхностных оксидных пленок. Дислокации являются линейными дефектами кристаллической решетки металла. Они возникают в процессе затвердевания охлаждающегося металла и при механических воздействиях на металл. В реальных металлических материалах дислокации образуют сплошную трехмерную сетку с узлами. В узлах происходит пересечение отдельных дислокаций, расстояние между которыми оценивается как ≈ 10-6 м [24]. К плоскостным и поверхностным дефектам кристаллической решетки (рис. 1.2 и 1.3) относят границы, разделяющие различно ориентированные области. Например, границы зерен (рис. 1.2, а, в, г), блоков (рис. 1.3, б), двойников (рис. 1.2, б). Типы границ различаются углом разориентировки Ω (рис. 1.3, а). Чем больше величина угла разориентировки, тем выше энергия кристаллической решетки, но всегда энергия решетки, содержащей поверхностные дефекты, выше, чем содержащей линейные [1, 24].
Рис. 1.2. Строение границ в простой кубической решетке:
а – граница скручивания; б – двойник с когерентной границей; в, г – границы зерен, разориентированные под большим углом; г – общий вид
Рис. 1.3. Образование малоугловой границы:
а – расположение двух кристаллов с углом разориентировки;
б – малоугловая граница
Пленки на металлах
В большинстве случаев продукты газовой коррозии образуются и остаются на металле в виде пленки. Пленки продуктов коррозии определяют кинетику процесса и в случае наличия защитных свойств могут привести к замедлению коррозионного процесса. Чтобы пленка продуктов коррозии обладала защитными свойствами, она должна быть сплошной, не разрушаться в агрессивной среде, прочно сцепляться с основным металлом и обладать близким к нему коэффициентом теплового расширения. Если пленка пористая, рыхлая и характеризуется плохим сцеплением с основным металлом, то даже при условии инертности в данной агрессивной среде, она не будет обладать защитными свойствами.
|
|
Пленки по толщине делятся на три группы:
- тонкие (невидимые), δ < 4000 нм;
- средние (дающие цвета побежалости), δ = от 4000 до 50000 нм;
- толстые (видимые), δ > 50000 нм.
Толщина пленок, образовавшихся при взаимодействии металла с сухим воздухом, различна и зависит от рода металла, температуры и других факторов. Толщина пленок на меде и железе при комнатной температуре составляет 100 – 300 нм, а на алюминии 1000– 1500 нм. При повышении температуры толщина пленки увеличивается и дает цвета побежалости. Так, при нагреве железа до 4000C в течение 1 ч на нем образуется желтая пленка толщиной 4600 нм, через 2 ч – красная пленка толщиной 5800 нм, а через 3 ч – синяя пленка толщиной 7200 нм. Примером толстой видимой пленки является окалина на железе или пленка, полученная на алюминии анодированием, имеющая толщину 10 – 15мкм, а в некоторых случаях – до 200 – 500 мкм. Наличие тонких, невидимых пленок было доказано различными способами:
- если сломать стальной образец (иглу, лезвие) под ртутью, то произойдет амальгамирование поверхности; если излом произвести на воздухе, а затем погрузить образец в ртуть, то амальгамирования не произойдет. Это объясняется образованием тончайшей окисной пленки, препятствующей амальгамированию;
- если железную полированную пластину нагреть с одного конца, то вследствие неравномерности толщины пленки, на поверхности пластины появятся цвета побежалости (желтый, красный, пурпурный, фиолетовый, синий).
При нанесении на различные участки поверхности железа капли азотно-кислой меди, можно определить защитные свойства пленки. В местах, где пленка не обладает защитными свойствами, протекает реакция
Fe + Cu(NO3)2 = Fe(NO3)2 + Cu,
и под каплей будет происходить выделение меди.
Наибольшими защитными свойствами пленка обладает не у нагретого конца, т.е. где пленка толще, а в преджелтой зоне, где пленка невидима;
Изоляция пленок от поверхности металла является самым наглядным доказательством их существования. Благодаря оптическим эффектам отражения света эти пленки, невидимые на поверхности металла, становятся видимыми. Если поместить металл в среду, которая хорошо растворяет металл, но не растворяет пленку, и нарушить целостность пленки, то металл растворяется, а пленка остается в изолированном виде.
|
|
Условия сплошности пленок
Защитными свойствами могут обладать только сплошные, т.е. покрывающие сплошным слоем всю поверхность металла, пленки. Условие сплошности определяется соотношением объемов образованного окисла и исходного металла.
Если объем продуктов коррозии Vок меньше, чем объем металла Vме, образующего это соединение, пленка будет пористой и обладает слабыми защитными свойствами. Наоборот, если объем продуктов коррозии больше, чем объем окислившегося металла, то можно ожидать образования сплошных пленок с повышенной способностью защищать от коррозии.
Соотношение объемов образованного оксида и исходного металла может быть легко подсчитано. Предположим, что окислится 1 грамм-атом металла. Его объем равен
(9)
где А – атомная масса металла;
d – плотность металла.
Объем полученного оксида будет равен
(10)
где М – молекулярная масса окcида;
D – плотность оксида;
n – число атомов металла в молекуле оксида.
Соотношение между объемом оксида и объемом металла
(11)
Щелочные и щелочноземельные металлы, указанное соотношение у которых меньше 1, образуют рыхлые пленки, со слабыми защитными свойствами и характеризуются высокими скоростями окисления. Металлы с соотношением образуют, как правило, пленки, значительно тормозящие дальнейшее протекание процесса окисления, т.е. обладающие хорошими защитными свойствами. Однако при соотношении
не следует ожидать высоких защитных свойств пленки. Ориентировочно
не должно быть более 2,5-3.
В табл. 2 приведены данные рассчитанного соотношения объемов для ряда металлов.
Эти данные подтверждают условия сплошности пленок. Так, натрий, кальций, барий, магний при окислении не могут образовать сплошных пленок, так как у этих металлов . Молибден и вольфрам тоже не образуют сплошных пленок, так как у них
.
Таблица 2
Отношение объемов оксида и металла для некоторых металлов
Металл | Оксид | ![]() |
натрий кальций барий магний кадмий алюминий свинец цинк никель хром железо молибден вольфрам | Na2O CaO BaO MgO CdO Al2O3 PbO ZnO NiO Cr2O3 Fe2O3 MoO3 WO3 | 0,57 0,64 0,74 0,79 1,21 1,24 1,29 1,57 1,60 2,03 2,16 3,45 3,36 |
Механизм окисления металлов
Для большинства случаев окисления основным направлением диффузии является движение металла через пленку наружу и в меньшей степени - диффузия кислорода в обратном направлении.
Так как оксидные и солевые пленки на металлах имеют ионную кристаллическую структуру, обладающую, как правило, ионной и в некоторой степени электронной проводимостью, то можно ожидать диффузию через пленку не непосредственно атомов металла, а ионов металла и самостоятельно электронов. Можно также предполагать возможность диффузии ионов кислорода в противоположном направлении. Ионизация кислорода при этом происходит на внешней поверхности прошедшими через пленку электронами. Естественно, что допущение ионного характера диффузии не исключает возможности параллельного протекания и атомной диффузии.
Ион металла имеет меньший радиус, чем атом. Наоборот, анионы имеют больший радиус, чем атомы соответствующего металлоида. Следовательно, в общем случае можно предполагать, что от металла сквозь пленку двигаются ионы металла, а с поверхности пленки вглубь - атомы кислорода, ионизация которых происходит уже в самой пленке. Из-за большей подвижности при диффузии металлических ионов преимущественный рост пленки происходит вблизи ее внешней поверхности (рис.3).
|
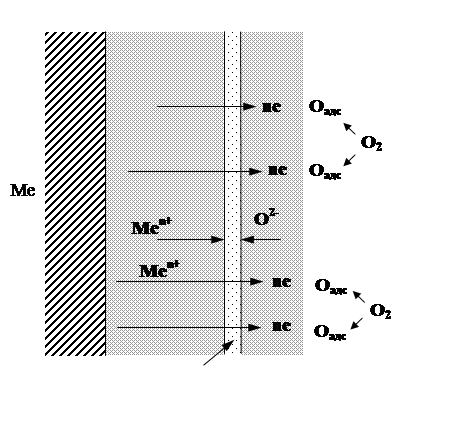
Законы роста пленок
Исходя из современной теории роста пленок, образование и их дальнейший рост осуществляется взаимной двусторонней диффузией как окислительного реагента к поверхности металла, так и металла к внешней поверхности пленки.
Скорость роста защитной пленки находится в зависимости от диффузии и скорости химического превращения и определяется уравнением, предложенным Эвансом:
(12)
где y – толщина пленки;
τ – время ее образования;
Кd – константа диффузии при данных условиях;
Кс – константа скорости химической реакции образования пленки;
Со – концентрация действующей среды на внешней поверхности пленки.
При достаточно толстой пленке величина y2/Kd значительно больше чем 2y/Kc. Принебрегая последней, получаем зависимость роста толщины пленки от процесса диффузии:
Заменяя величины 2КdCo через k1, получаем уравнение параболы
(13)