РАСЧЕТ ТЕХНОЛОГИЧЕСКИХ РЕЖИМОВ сварки под флюсом и электродуговой наплавки самозащитной
порошковой проволокой
Цель работы: Закрепление теоретических знаний по восстановлению деталей различными методами электродуговой сварки и наплавки.
Задание: Изучить технологию и оборудование для автоматической дуговой сварки под флюсом и электродуговой наплавки самозащитной порошковой проволокой и рассчитать режимы (сварки) наплавки.
Автоматическая дуговая сварка под флюсом
Основные положения
При дуговой сварке под флюсом (рис. 1) дуга горит между сварочной проволокой 1 и свариваемым изделием 5 под слоем гранулированного флюса 4. Ролики 2 специального механизма подают электродную проволоку в зону горения дуги 6. Сварочный ток переменный или постоянный (прямой или обратной полярности) подводится к проволоке с помощью скользящего контакта 3, а к изделию – постоянным контактом.
![]() | Сварочная дуга горит в газовом пузыре, который образуется в результате плавления флюса и металла. Кроме того, расплавленный металл защищен от внешней среды слоем расплавленного флюса 8. По мере удаления дуги от зоны сварки расплавленный флюс застывает и образует шлаковую корку 10, которая впоследствии легко отделяется от поверхности шва. Оболочка шлака наряду с надежным изолированием расплавленного металла от вредного воздействия воздуха, также препятствует разбрызгиванию жидкого металла и нарушению формирования шва. При сварке (наплавке) флюс засыпается впереди дуги из бункера слоем толщиной 40–80 мм и шириной 40–100 мм. Нерасплавленный флюс после сварки (наплавки) используется повторно. |
Расплавленные электродный и основной металлы 7 в сварочной ванне перемешиваются и при кристаллизации образуют сварной шов 9.
Сварочные флюсы – это гранулированные порошки с размером зерен 0,2–4,0 мм, которые делятся по способу получения на плавленные и керамические (неплавленные), а по химическому составу – на оксидные, солеоксидные (смешанные) и солевые. Оксидные флюсы состоят из оксидов металлов (SiO2, MnO, СаО и др.) и могут содержать до 10 % фторных соединений (CaF2, NaF, BaF2 и др.). Они предназначены для сварки низколегированных сталей. Солеоксидные флюсы, используемые для сварки легированных сталей, по сравнению с оксидными флюсами содержат меньшее количество оксидов и большее (12–30 %) количество солей. Солевые флюсы не содержат оксидов, целиком состоят из фторидов (CaF2, NaF, BaF2 и др.) и предназначены для сварки активных металлов.
Флюс влияет на устойчивость дуги, формирование и химический состав металла шва и определяет стойкость швов против образования пор и трещин. Оксиды щелочных и щелочно-земельных металлов увеличивают электрическую проводимость и длину дугового промежутка, что повышает устойчивость процесса сварки, соединения фтора, напротив, снижают эти показатели. Насыпная масса флюса и гранулометрический состав влияют на форму шва. Швы, сваренные под стекловидными плавлеными флюсами (насыпная масса 1,4–1,7 г/см3), имеют меньшую ширину, чем швы, сваренные под пемзовидным флюсом (насыпная масса 0,7–0,9 г/см3). Гранулометрический состав флюса (размер его зерен) также влияет на форму шва. Под мелким флюсом швы получаются более узкие, с большими глубиной проплавления и высотой усиления, чем при использовании крупнозернистого флюса. Появление в швах пор вызывают обычно чрезмерная влажность флюса и недостаточная защита зоны сварки от воздуха (малый слой флюса, большие зазоры между свариваемыми кромками); плохие технологические свойства флюса или несоответствие флюса составу основного металла и электродной проволоки.
Для сварки (наплавки) под слоем флюса наибольшее применение находят флюсы марок АН-348А, АН-348В, АНЦ-1 и др. Такие флюсы рекомендуются для сварки низко- и среднеуглеродистых сталей. Для сварки и наплавки низко- и среднелегированных сталей используются флюсы АН-60, АН-22 и другие в сочетании с проволоками Св-08А, Св-08ГА и проволоками, легированными хромом, молибденом, никелем. В табл. 1 приведено назначение некоторых марок флюсов и проволок.
Таблица 1. Флюсы и проволока для автоматической сварки
|
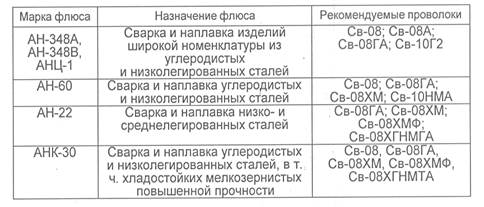
Исходя из класса свариваемой стали по табл. 1 выбираются марки флюса и электродной проволоки.
Сварку под сдоем флюса выполняют с применением специальных полуавтоматов или автоматов. Технические характеристики аппаратов для автоматической сварки и наплавки под флюсом приведены в табл. 2.
Таблица 2. Технические характеристики аппаратов для автоматической сварки и наплавки открытой дугой и под флюсом
Аппарат | Исполнение | Защита зоны сварки или наплавки | Диаметр проволоки (ширина ленты), мм | Ток сварки Iсв при | Скорость подачи электродной проволоки vпр, м/ч | Регулирование скорости подачи проволоки | Скорость сварки (наплавки) vсв, м/ч | Источник питания | |||||||||||||
1 | 2 | 3 | 4 | 5 | 6 | 7 | 8 | 9 | |||||||||||||
Аппараты общего применения для автоматической сварки | |||||||||||||||||||||
АБСК | Самоходный | Флюс | 2,0–6,0 | 300–1200 | 28–220 | Ступенчатое | 14–110 | ТДФ-1001 | |||||||||||||
А1401 | » | » | 2,0–5,0 | 1000 | 53–532 | Плавное | 12–120 | ТДФ-1001 | |||||||||||||
А1410 | » | » | 2,0–6,0 | 2000 | 53–532 | » | 24–240 | ТДФ-1601 | |||||||||||||
А1412 | » | » | 2,0–5,0 | 2х1600 | 53–532 | » | 24–240 | ТДФ-1601 | |||||||||||||
А1416 | » | » | 2,0–5,0 | 1000 | 47–508 | Ступенчатое | 12–120 | ВДУ-1001 | |||||||||||||
А1419 | » | » | 2,0–6,0 | 2000 | 47–508 | » | 24–240 | ТДФ-1601 | |||||||||||||
УДФ1001У4 | » | » | 2,5–3,0 | 400–1000 | 200–600 | Плавное | 18–50 | ТШС-1000-3 | |||||||||||||
Аппараты специализированные для автоматической сварки | |||||||||||||||||||||
А1423 | Подвесной | Флюс | 1,6–3,0 | 100–500 | 45–450 | плавное | 10–25 | ВДУ-504, ВС-600 | |||||||||||||
А1403 | Самоходный | » | 2,0–5,0 | 2х1600 | 53–530 | » | 24–240 | ТДФ-1601 (2 шт.) | |||||||||||||
А1425 | » | » | 4,0–5,0 | 1000 | 50–500 | » | 12–120 | ТДФ-1601 | |||||||||||||
А1208С | подвесной | Без внешней защиты или углекислый газ | 1,6 (сплошная) 2,0–2,5 (порошковая) | 200 | 102–196 | ступенчатое | 10–25 | ПСГ-500 | |||||||||||||
Аппарат общего применения для автоматической наплавки | |||||||||||||||||||||
А384МК | подвесной | Флюс | 3,0–5,0 | 1000 | 28,5–225 | Ступенчатое | 10–120 | ПСО-500 | |||||||||||||
А580М | » | » | 1,0–3,0 | 400 | 48–408 | » | 10–120 | ПСО-500 | |||||||||||||
А874Н | самоходный | флюс или | 2,0–7,0 | 1000 | 5–90 | плавное | 5–116 | ВДУ-1001 | |||||||||||||
Аппараты специализированные для автоматической наплавки | |||||||||||||||||||||
А1406 | подвесной | без внешней защиты, флюс или углекислый газ | 2,0–7,0 (сплошная, порошковая) | 1000
| 50–500
| плавное
| 12–120
| ВДУ-1001 | |||||||||||||
А1408 | » | без внешней защиты или углекислый газ
| 1,6 (сплошная) 1,6–2,0 (порошковая) | 500
| 50–500 | » | 5–120
| ВДУ-504 | |||||||||||||
А1409 | » | без внешней защиты или флюс | 1,6–3,0 сплошная, порошковая) | 300 | 50–500 | » | 10–120 | ВДУ-504 | |||||||||||||
1 | 2 | 3 | 4 | 5 | 6 | 7 | 8 | 9 | |||||||||||||
Тракторы общего применения для автоматической сварки однодуговые | |||||||||||||||||||||
ТС-17М-1 | Флюс | 1,6–5,0 | 200–1000 | 52–403 | ступенчатое | 16–126 | ТДФ-1001 | ||||||||||||||
ТС-42 | – | » | 2,0–5,0 | до 1000 | 60–1000 | » | 12–120 | ТДФ-1001 | |||||||||||||
АДС-1000-4 | – | » | 2,0–5,0 | 400–1200 | 60–360 | плавное | 12–120 | ТДФ-1001 | |||||||||||||
АДС-1000-5 | – | » | 2,0–5,0 | 400–1200 | 60–360 | » | 12–120 | ВДУ-1001 | |||||||||||||
АДФ-1001 | – | » | 3,0–5,0 | 400–1200 | 60–360 | » | 12–120 | ТДФ-1001 | |||||||||||||
АДФ-1004 | – | » | 3,0–5,0 | 1000–1200 | 60–360 | » | 12–120 | ВДУ-1001 | |||||||||||||
АДФ-1602 | – | » | 3,0–6,0 | 600–1800 | 60–360 | » | 12–120 | ВДУ-1601 | |||||||||||||
Тракторы специализированные для автоматической сварки | |||||||||||||||||||||
ТС-32 | – | Флюс | 2,0–5,0 | до 900 | 137–284 | ступенчатое | 4–50 | ТДФ-1001 | |||||||||||||
ТС-44 | – | » | 3,0–6,0 | 1600 | 60–360 | плавное | 8–45 | ВДУ-1601 | |||||||||||||
ДТС–38 | – | » | 2,0–5,0 | 2х1600 | 58–580 | ступенчатое | 16–160 | ТДФ-1601 (2 шт.) | |||||||||||||
Режимы сварки под флюсом имеют основные и дополнительные параметры. К основным параметрам режима относятся: сварочный ток, его род и полярность, напряжение дуги, диаметр электродной проволоки, скорость сварки; к дополнительным – вылет электродной проволоки, состав и строение флюса (плотность, размеры частиц), положение изделия и электрода при сварке. Параметры режима сварки зависят от толщины и свойств свариваемого металла. При глубине проплавления менее 5 мм рекомендуется постоянный ток обратной полярности, при большей – постоянный ток прямой полярности. Основным условием для успешного ведения процесса сварки является поддержание стабильного горения дуги. Для этого определенной силе сварочного тока должна соответствовать своя скорость подачи электродной проволоки. Скорость подачи должна повышаться с увеличением вылета электрода. При его постоянном вылете увеличение скорости подачи уменьшает напряжение дуги. При использовании легированных проволок, имеющих повышенное электросопротивление, скорость подачи должна возрастать.
В промышленности находит применение способ сварки под флюсом сварочной проволокой, однако в некоторых случаях сварку и особенно наплавку выполняют ленточными электродами. Лента, используемая для этих электродов, имеет толщину до 2 и ширину до 40 мм. Сварку стыковых швов с разделкой кромок и угловых швов, где требуется большое количество наплавленного металла, выполняют с порошковым присадочным металлом или при увеличенном вылете электрода (до 100 мм).
Преимущества процесса сварки (наплавки) под слоем флюса состоят в: возможности вести процесс при повышенных сварочных токах (до 3000–4000 А, в то время как без флюса до 500–600 А из-за высокого разбрызгивания); низком расходе сварочных материалов за счет сокращения потерь металла на угар, разбрызгивание и огарки (≤3 %, в то время как при ручной сварке до 15 %); лучшем использовании теплоты дуги (расход электроэнергии на 30–40% меньше, чем при ручной дуговой сварке); снижении трудоемкости работ по разделке кромок под сварку, зачистке шва от шлака и брызг. Недостатки способа – трудности ориентировки положения электрода относительно шва, дополнительные стоимостные затраты на флюс, большой объем сварочной ванны и повышенная жидкотекучесть флюса и расплавленного металла, что ограничивает возможность применения сварки в различных пространственных положениях. Дуговая сварка (наплавка) под флюсом наиболее целесообразна в нижнем положении при отклонении плоскости шва от горизонтальной не более чем на 10–15о. Наплавка под слоем флюса цилиндрических поверхностей возможна только для деталей диаметром более 45–60 мм.
Сварка под флюсом используется при изготовлении и ремонте конструкций и деталей ответственного назначения, которые должны надежно эксплуатироваться в условиях низких и высоких температур. Сварку под флюсом применяют для изготовления строительных конструкций, крупногабаритных резервуаров, труб и т.д. из сталей, никелевых сплавов, алюминия, меди, титана и их сплавов.
Режимы сварки под флюсом
Плотность сварочного тока. При сварке под флюсом для более глубокого проплавления рекомендуется использовать высокие значения плотности тока в электродной проволоке (j ≥ 40–50 А/мм2), а при наплавке для снижения глубины проплавления принимается j ≤ 30–40 А/мм2.
Диаметр электродной проволоки. При сварке под флюсом используют электродную проволоку диаметром в пределах dэ = 1,0–4,0 мм, при этом наиболее широко применяется проволока диаметром dэ = 2,4–3,0 мм.
Диаметр dэ и плотность тока j выбирают такими, чтобы они обеспечивали требуемую глубину проплавления hпр при максимальной производительности сварки (наплавки), а производительность сварки (наплавки) возрастает с увеличением диаметра dэ. Взаимосвязь диаметра электродной проволоки dэ и плотности сварочного тока j с глубиной проплавления hпр приведена в табл. 3
Таблица 3. Влияние плотности сварочного тока на глубину проплавления при автоматической сварке под флюсом
Диаметр электродной проволоки dэ, мм | Глубина проплавления hпр, мм | |||||
3 | 4 | 5 | 6 | 8 | 10 | |
Плотность тока j, А/мм2 | ||||||
1,0 | 65 | 104 | 127 | 143 | 157 | 200 |
2,0 | 43 | 50 | 57 | 71 | 89 | 107 |
3,0 | 29 | 36 | 40 | 44 | 53 | 64 |
4,0 | 23 | 26 | 28 | 31 | 37 | 42 |
Расчет сварочного тока Iсв (А) производится по формуле (1)
, (1)
где dэ – диаметр электродной проволоки, мм; j – плотность тока, А/мм2.
Напряжение дуги. Зависимость напряжения дуги Uд от силы сварочного тока Iсв приведена в табл. 4.
Таблица 4. Зависимость напряжения дуги от силы сварочного тока
Сварочный ток Iсв, А | 150–250 | 250–350 | 350–500 | 500–650 | 650–800 | 800–1000 | 1000–1200 |
Напряжение дуги Uд, В | 32–34 | 34–36 | 36–40 | 38–40 | 40–42 | 41–43 | 42–44 |
Наплавку рекомендуется вести на постоянном токе прямой полярности.
Длина вылета электродной проволоки принимается lв э = 30–60 мм, при этом более высокие его значения соответствуют большему диаметру проволоки и силе тока.
Скорость подачи электродной проволоки vпр (м/ч) определяется по формуле
, (2)
где dэ – диаметр проволоки, мм; αр – коэффициент расплавления, г/А·ч; γ – плотность металла электродной проволоки, г/см3 (для стали γ = 7,86 г/см3).
Коэффициент расплавления αр (г/А·ч) проволоки сплошного сечения при сварке под флюсом определяется по следующим формулам:
для переменного тока
; (3)
для постоянного тока прямой полярности
; (4)
для постоянного тока обратной полярности
. (5)
Скорость сварки vсв (м/ч), определяется по формуле
, (6)
где αн – коэффициент наплавки, г/А·ч; Fв – площадь поперечного сечения одного валика при многопроходной наплавке (сварке) или площадь поперечного сечения сварочного шва при однопроходной (Fш), см2; γ – плотность металла сварочной проволоки, г/см3.
Коэффициент наплавки αн находится из выражения
αн = αр (1– ψ), (7)
где ψ – коэффициент потерь металла на угар и разбрызгивание (при сварке (наплавке) под флюсом принимается ψ = 0,02–0,03).
Вид соединения. Стыковые соединения в зависимости от толщины металла и применяемой техники сварки выполняются односторонними и двусторонними швами, с разделкой (скосом) и без разделки кромок (рис. 2).
|
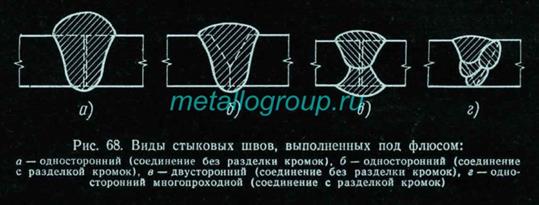
Чтобы предотвратить образование прожогов, односторонние стыковые соединения сваривают: в замок (рис. 3, а); на остающейся стальной подкладке (рис. 3, б); на медной или флюсо-медной подкладке (рис. 3, в), после ручной подварки с обратной стороны стыка (рис. 3, а), а также на флюсовой подушке.
|
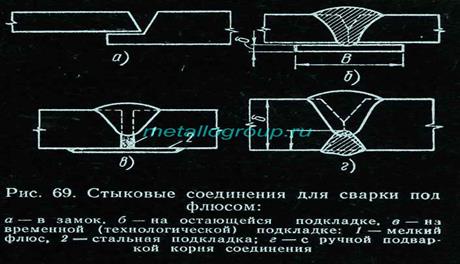
Как односторонние, так и двусторонние швы могут быть однопроходными (рис. 2, а, б) или многопроходными (рис. 2, в, г). Если свариваемая сталь не восприимчива к сварочному нагреву (перегреву) и швы не склонны к образованию горячих трещин, то стыковые соединения толщиной до 20 мм можно сваривать в один проход односторонним швом без разделки кромок (рис. 2, а). При этом для обеспечения полного провара и оптимального усиления шва (не превышающего установленных размеров) необходим зазор в стыке шириной bш = 5–6 мм. Одностороннюю сварку металла толщиной до 14 мм можно производить без разделки кромок.
При однопроходной сварке площадь поперечного сечения Fв равна площади поперечного сечения сварочного шва Fш, определяемой по формуле
Fш = 0,01 · Kp · hпр · bш, см2 (8)
где Kp – коэффициент, учитывающий усиление шва (Kp = 1,1–1,2); hпр – глубина проплавления, мм; bш – зазор в стыке, мм.
При наплавке площадь поперечного сечения валика, укладываемого за один проход, можно принять равной Fв = 0,3–0,6 см2.
Масса наплавленного металла Gн (г), определяется по формуле
, (9)
где Vн – объем наплавленного металла, см3; γ – плотность наплавленного металла, г/см3.
Объем наплавленного металла Vн (см3) определяется по формулам:
при сварке
, (10)
где Fш – площадь поперечного сечения шва, см2; lш – длина сварочного шва, см;
при наплавке
, (11)
где Fн – площадь наплавленной поверхности, см2; hсл – высота наплавленного слоя, мм (с учетом восстановления износа ∆ изн и припуска на обработку ∆мех.обр = =2–3 мм).
Расход сварочной проволоки Gпр (г) определяется по формуле
, (12)
где Gн – масса наплавленного металла, г; ψ – коэффициент потерь на угар и разбрызгивание (ψ = 0,02–0,03).
Расход флюса Gф (г) определяется по формуле
, (13)
где lш – длина сварочного шва, см; Gфl – удельный расход флюса на 1 пог.м сварочного шва (г/пог.м) рассчитывается по формуле
, г/пог.м (14)
где Uд – напряжение на дуге, В; vсв – скорость сварки, м/ч.
Толщина слоя флюса hф зависит от силы сварочного тока (табл. 5)
Таблица 5. Зависимость толщины слоя флюса от величины сварочного тока
Сварочный ток Iсв, А | 150–400 | 400–800 | 800–1200 |
Толщина слоя флюса hф, мм | 25–35 | 35–45 | 45–60 |
Время горения дуги to (ч) определяется по формуле
, (15)
Полное время сварки T (ч) определяется по формуле
, (16)
где tо – время горения дуги, ч; Кп – коэффициент использования сварочного поста (Кп = 0,6–0,7).
Расход электроэнергии А (кВт·ч) определяется по формуле
, (17)
где Uд – напряжение дуги, В; Iсв – сварочный ток, А; η – КПД источника питания (для источников постоянного тока η = 0,6–0,7, переменного – η = 0,8–0,9); Wo – мощность источника питания, расходуемая на холостом ходу, кВт (для источников постоянного тока W o = 2,0–3,0 кВт, для источников переменного тока – Wo = 0,2–0,4 кВт); T – полное время сварки, ч; to – время горения дуги, ч.
Оборудование для сварки (наплавки) под флюсом выбирается с учетом диаметра электродной проволоки dэ, тока сварки Iсв, скорости подачи электродной проволоки vпр, скорости сварки (наплавки) vсв. Технические характеристики аппаратов для автоматической сварки (наплавки) под флюсом приведены в табл. 2.