информационного сигнала о качестве поверхностного слоя деталей
ственными дефектами, сформированными лазерным излучением. Формирование стохастических оценок периодических неоднородностей осуществляется на основании результатов контроля деталей, обработанных на станке с повышенным дисбалансом шлифовального круга.
Схема применения АСВК в ИИК системы мониторинга приведена на рис.4.4, при этом она отражает роль данного канала как элемента обратной связи при управлении качеством деталей, так как позволяет получить количественную оценку состояния поверхностного слоя шлифованных деталей.
На первом этапе при проверке производственной партии внутренних колец подшипника 256907 в количестве 1200 шт. из стали ШХ-15 было установлено, что приборреагирует на дефекты поверхностного слоя, не выявляемые однократным и многократным травлением, предположительно это внутренние напряжения, которые могу устраняться низкотемпературным отпуском; при проверке специально отобранных колец с прижогами установлено, что максимальная амплитуда сигнала от прижога более чем в три раза превышает сигнал от поверхности без дефекта, при этом выявляются мелкие дефекты глубиной менее 20 мкм (после оформления результатов приборного контроля образцы разрезались по местам расположения дефектов и исследовались металлографическими методами с оформлением протоколов исследований; результаты металлографических исследований этих деталей количественно характеризуют чувствительность прибора).
На втором этапе выявлено следующее:
1) в сигнале, снятом со всей сканируемой поверхности дорожек качения колец шариковых подшипников (рис.4.6), наблюдается плавное изменение сигнала по образующей тороидальной поверхности от краев к середине дорожки качения, причиной которого является то, что вследствие относительного увеличения к краям дорожек качения длительности контакта тороидальных поверхностей круга и обрабатываемой детали, происходит изменение структуры металла, увеличивающееся к краям дорожек качения. Условия обработки на краях хуже, тепловыделение больше, а нагрев детали приводит к вторичному отпуску поверхностного слоя. Экспериментально изменение микротвердости по образующей проверялось с помощью прибора Microdur-2 (Германия) на кольцах шариковых и роликовых подшипников. На всех кольцах выявлено существенное (на 2 – 3 HRС), снижение микротвердости по краям дорожек качения. В работе [94] получены аналогичные результаты. Отмечено понижение микротвердости и уменьшение содержания углерода на краях дорожек качения роликовых подшипников. Для сравнения на рис.4.7 приведены результаты контроля дорожки качения кольца роликового подшипника;
2) для определения зависимости чувствительности датчика от расстояния до дефекта на цилиндрической поверхности наружного кольца подшипника 256907 лазером нанесен искусственный дефект, выраженный трооститом вторичного отпуска шириной 0,1 мм, глубиной 0,02 мм. Ширина сигнала на уровне 0,5 амплитуды составляет 3 мм (рис.4.8а). Форма сигнала в первом приближении характеризует распределение чувствительности датчика по расстоянию от дефекта до оси датчика.
3) для выявления зависимости чувствительности датчика от размера дефектов проведены следующие замеры. На цилиндрической поверхности наружного кольца подшипника 256907 лазером на тех же режимах излучения нанесена прерывистая полоса искусственных дефектов длиной 1,5 мм (4.8б). Амплитуда сигнала от прерывистого дефекта существенно меньше (в полтора-два раза) амплитуды сигналов от протяженного дефекта при одинаковой интенсивности изменений физико-механических свойств, что свидетельствует о зависимости чувствительности вихретокового датчика от размеров дефектов. Этот наиболее серьезный недостаток вихретокового метода, который не позволяет обнаруживать мелкие дефекты типа штрихов и точек, выявляемые, например, травлением. Недостаток характерен всем известным приборам и связан с техническим ограничением минимальных размеров датчиков.
3) сравнение возможностей по выявлению прижогов вихретоковым методом и травлением проведено с помощью специально изготовленного образца с полосой термических изменений, вызванных лазером. С половины длины полосы образец прошлифован на конус так, что глубина дефекта постепенно снижается до нуля (косой шлиф). Травлением на образце выявлена постепенно сужающаяся полоса темного цвета, отмечающая область вторичного отпуска. На рисунке 4.9. показаны результаты контроля этого образца. Результаты травления и вихретокового контроля полностью совпадают.
Выявление с помощью АСВК различных дефектов демонстрируются рисунками 4.10 и 4.11, на которых показаны примеры выявления трещин, периодических и локальных шлифовальных прижогов.
Исследование метрологических характеристик АСВК. Работа по определению метрологических характеристик системы проводилась в помещении измерительной лаборатории цеха № 26 ОАО «СПЗ». Метод определения – контроль специально изготовленных и аттестованных стандартных образцов с искусственными дефектами. Из результатов измерений, следует, что порог чувствительности прибора составляет D = 4.8 мкм глубины дефекта стандартного образца; чувствительность составила S = 0.07 ед. шкалы на 1 мкм глубины дефекта стандартного образца (например, размах сигналов в половину шкалы соответствует глубине дефекта 0.5 / 0.07 = 7.15 мкм); прибор позволяет выявлять дефекты размером от 0,005 х 0,2 х 2 мм (связан с диаметром датчика: в нашем случае он составляет 1,5 мм).
|
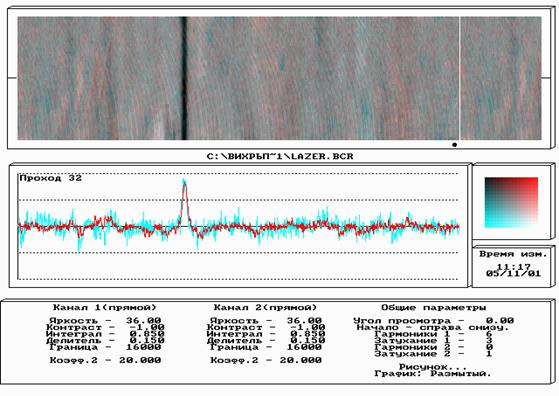
|
|
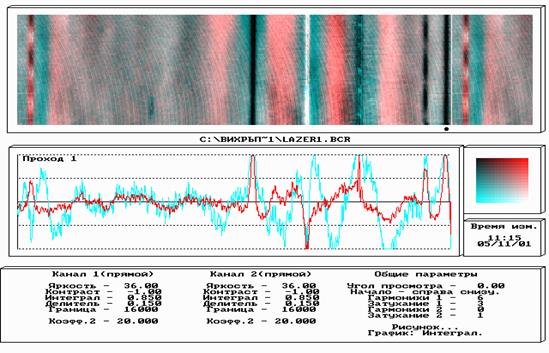
Рис. 4.9. Результаты контроля детали с косым шлифом полосы,
образованной лазерным излучением
Рис.4.10. Пример выявления продольных и поперечных трещин
Рис.4.11. Пример выявления периодических и локальных
шлифовочных прижогов
По результатам метрологической аттестации прибор ПВК-К2М внесен в Госреестр средств измерений.
4.3. Автоматизированный вихретоковый контроль
других технологических операций
4.3.1. Контроль роликов
Одним из важнейших и затратных этапов ТП изготовления роликов железнодорожных подшипников является шлифовальная обработка. Ее особенностью является сочетание напряженных режимов резания, малых припусков и требований обеспечения высокой точности и стабильности свойств.
Для шлифования роликов на ОАО «СПЗ» применяются бесцентровые шлифовальные станки модели Sasl 200x500. Шлифование осуществляется методом на проход, который применяется для цилиндрических изделий без буртов и ступенек, что дает возможность непрерывного шлифования, при котором изделие перемещается между кругами вдоль своей оси. Шлифовальная щель при этом остается неизменной по своей ширине и изменяется только за счет износа шлифовального круга. Припуск шлифуется за несколько проходов, число которых зависит от начальной формы заготовки и припуска на шлифование, материала и требуемой точности и качества поверхности.
Управление такого рода ТП на современном уровне требует системного подхода, который может формироваться на основе большого объема измерительной информации, накапливаемой в СМТП. Одним из информационных каналов СМТП, который применяется в ОАО «СПЗ» для контроля качества железнодорожных подшипников, является вихретоковый контроль поверхностного слоя роликов, структурные изменения в котором можно соотнести с динамическим состоянием технологического оборудования. Первые вихретоковые дефектоскопы использовались в ТП как пассивные устройства, фиксирующие качество готовых деталей, причем отбраковка производилась по амплитуде всплеска сигнала вне зависимости от формы и природы дефекта. Это вполне устраивало потребителя, которому важно не допустить установки детали ненадлежащего качества в узлы машин и агрегатов. Однако, с точки зрения производителя, информация о природе дефекта открывает большие возможности для управления ТП. Автоматизированный неразрушающий контроль роликов на различных стадиях обработки и статистическая обработка этой информации в рамках СМТП позволяют определить, в какой момент возникают те или иные дефекты, а, следовательно, выявлять и устранять причины появления некачественной продукции. При таком подходе контроль становиться активным методом корректировки ТП.
Практика применения универсальных вихретоковых приборов для межоперационного контроля роликов буксовых подшипников на ОАО «СПЗ» показала достаточную эффективность мониторинга. Однако значительные затраты времени на контроль одной детали и невозможность принятия решения в автоматическом режиме привели к необходимости разработки прибора для автоматического контроля и сортировки деталей – автомата контроля роликов АВК-Р (рис.4.15).
Автомат предназначен для вихретокового контроля однородности физико-механических свойств поверхностного слоя цилиндрической поверхности и торцов тел качения буксовых подшипников – роликов 32х52 мм после шлифовальной обработки. Автомат выявляет локальные и периодические неоднородности поверхностного слоя шлифованных деталей и может применяться для выявления несоответствия деталей требованиям качества поверхностного слоя, вызванных шлифовальной либо термической обработкой, а также дефектами металла.
Рис.4.15. Автомат контроля роликов АВК-Р
Конструктивно автомат состоит из сканирующего механизма с устройством перемещения и раскладки роликов и стойки управления. Автомат содержит три вихретоковых преобразователя, датчики которого одновременно сканируют цилиндрическую поверхность и торцы роликов. Система управления прибора - двухуровневая. На первом уровне (промышленный компьютер ПК) реализованы: графический интерфейс, компилятор управляющей программы и математическая обработка результатов. На втором уровне (контроллер HERCULES) в режиме реального времени происходят все остальные процессы: управление перемещениями вихретоковых датчиков, сбор и буферизация результатов измерений.
Перемещение датчиков, вращение устройства подачи роликов и смена положения выходного лотка производится шаговыми двигателями. Вращение роликов при сканировании осуществляется асинхронным двигателем. Начальное положение шаговых двигателей и скорость вращения асинхронного привода определяется датчиками исходного положения. Деталь сканируется датчиками, информационные сигналы в блоке управления затем оцифровываются с помощью АЦП на плате контроллера HERCULES. Контроллер собирает данные и пакетами передаёт их в персональный компьютер (ПК) для обработки. Обмен информацией между контроллером и ПК ведётся по шине Ethernet с помощью сетевой платы в ПК и встроенного Ethernet-адаптера в контроллере.
Процедура контроля производится автоматически, без участия оператора. Сканирование образующей и торцов ролика происходит одновременно. Результаты сканирования отображаются в виде трех панелей на дисплее.
Под панелью графика расположены 5 цветных квадратов (фонарей), которые показывают результат анализа дефектов по каждому из каналов анализа. Зеленый цвет означает, что на данном датчике при данных настройках деталь признается годной; желтый цвет – деталь условно годная; красный цвет – деталь бракованная. Серый цвет означает, что анализ дефектов по данному датчику отключен.
По результатам контроля производиться разделение роликов на годные и бракованные (дефектные). Предусмотрен режим сортировки бракованных роликов по задаваемым оператором критериям. По результатам контроля ведется статистика общего количества годных и отбракованных роликов.
Применение двухуровневой схемы управления обеспечивает автомату высокую производительность контроля (менее 3 секунд на один ролик). За время перемещения ролика на позицию сканирования автомат собирает и анализирует количество информации о состоянии поверхностного слоя, достаточное для формирования и распознавание вихретоковых образов дефектов, например микротрещин или прижогов, и образов типичных помех – следов напряженно-деформированного состояния, связанного с механической и термической обработкой. В результате обеспечивается высокая чувствительность к дефектам и низкая чувствительность к помехам.
На рисунке 4.16 показан пример автоматического распознавания трещины на цилиндрической поверхности ролика.
Рис. 4.16. Результат автоматического распознавания мелкой трещины
в вихретоковом образе цилиндрической поверхности ролика
методом свертки функции
В настоящий время автоматы АВК-R2 включены в техпроцесс, заменив устаревшие детекторы трещин ДТ-407, и успешно используются для окончательного контроля качества роликов железнодорожных подшипников, а также выборочного контроля, направленного на выявление отклонений в ТП на всех этапах шлифовальной обработки.
Стопроцентный неразрушающий контроль в рамках СМТП и обработка информации в соответствии со специальным ПМО позволяют определить качество деталей, проверить эффективность совершенствования производственного процесса и дает возможность отобрать годную часть роликов для дальнейшего использования при сборке подшипников.
4.3.2. Контроль суперфинишной обработки колец подшипников
При изготовлении деталей подшипников (колец, роликов) в качестве финишной операции применяется суперфиниширование. Качество обработки поверхностей качения определяется параметрами: некруглость менее 1 мкм, волнистость менее 0,2 мкм, параметр шероховатости Rа = 0,04…0,16 мкм, отсутствие дефектного слоя металла (структурно-фазовых изменений, напряжений растяжения, микротрещин), исправление погрешностей предыдущей обработки, обеспечение формы микронеровностей для несущей опорной поверхности. Несущая часть поверхности при суперфинишировании достигает порядка 95%, что важно для изменения начальных зазоров и сил трения в трущихся парах, а также влияет на начальный этап износа и приработки деталей.
Повысить качество процесса суперфиниширования деталей подшипников можно на основе мониторинга ТП, одним из элементов которого является контроль качества поверхностного слоя вихретоковым методом. Он позволяет сравнить предварительный (шлифовальный) и окончательный (суперфинишный) этапы ТП между собой и оценить исправляющую способность суперфинишной обработки при совместном рассмотрении двух вихретоковых образов поверхностей качения деталей подшипников.
На рис.4.19 приведены образы наружного кольца 92705, обработанные на предварительной стадии на шлифовальном станке модели SIW-4 и на окончательной стадии на суперфинишном автомате ВДА-70Н.
В поверхностном слое шлифованной детали (рис.4.19а) видны остаточные периодические неоднородности (зона 1, 36-й оборот кольца). Причиной могут быть низкочастотные вибрации (10...400 Гц), вызываемые дисбалансом шлифовального круга или низким качеством шпинделей, которые приводят к периодическим изменениям физико-механических свойств поверхностного слоя. После суперфинишной обработки (рис.4.19б) видна слабая остаточная периодическая неоднородность (зона 2, 36-й оборот кольца), которая могла быть получена из-за недостаточного съема припуска на окончательной стадии.
Рис.4.19. Вихретоковые образы поверхностей качения наружного кольца 92705
после операций шлифования (а) и суперфиниширования (б)
Данное кольцо обрабатывается на станке за 6 с, после чего абразивный брусок переходит в стадию полирования; съем достигает за время цикла 7-8 мкм, которого, видимо, недостаточно для удаления дефектного слоя.
Таким образом, совместный анализ вихретоковых образов позволил выявить особенности ТП на финишной стадии обработки и рекомендовать внести изменения в режим суперфиниширования для увеличения съема припуска и снижения неоднородности поверхностного слоя дорожек качения колец.