Дайте сравнительную характеристику лекарственной форме — таблетки.
· Обоснуйте необходимость проведения стадии грануляции в технологии производства таблеток с точки зрения ее влияния на качество продукта. Назовите возможные виды грануляции и используемого оборудования (грануляторы, сушилки).
· Обоснуйте оценку качества гранулята исходя из его технологических характеристик? Укажите методы их определения.
Таблетки – это твёрдая дозированная лекарственная форма, получаемая прессованием лекарственных веществ, смеси лекарственных и вспомогательных веществ или формирование специальных масс и предназначенная для внутреннего сублингвального или парантерального применения.
По способу получения таблетки подразделяются на два типа:
1. прессованные.
2. тритурационные, получаемые методом формирования масс.
По применению:
Пероральные
Сублингвальные
Имплантационные
Таблетки для экстемпорального применения инъекционных растворов
Таблетки для приготовления полосканий, спринцеваний
|
|
Таблетки специального назначения:ректальные,вагинальные, уретральные.
Преимущества таблеток перед другими лекарственными формами:
1. Преимущества биофармацевтического характера.
а) возможность регулирования всасывания лекарственных веществ из таблеток по месту локализации и во времени.
б) возможность сочетать несовместимые по физико-химическим свойствам и фармакологическому действию лекарственные вещества.
в) точность дозировки.
г) комфортность приёма.
2. Технолого-экономические и эксплуатационные преимущества.
а) производительность и экономичность по сравнению с другими лекарственными формами.
б) возможность полной механизации и автоматизации.
в) массовость и гигиеничность производства.
г) компактность, портативность, устойчивость к воздействию неблагоприятных факторов.
д) удобство транспортировки, хранения, отпуска.
Гранулирование — это процесс превращения порошкообразного материала в частицы (зерна) определенной величины. Оно позволяет предотвратить расслаивание многокомпонентных таблетируемых масс, улучшит сыпучесть (текучесть) порошков и их смесей, обеспечить равномерную скорость поступления их в матрицу таблеточной машины и большую точность дозирования и равномерное распределение активного компонента, а следовательно, большую гарантию лечебных свойств каждой таблетки. Задача гранулирования состоит в обеспечении тесного сближения частиц порошкообразного материала и формирования из них однородных и прочных гранул определенного размера.
Различают:
1) влажное гранулирование — (продавливанием) влажных масс, во взвешенном слое с последующим распылительным высушиванием;.
|
|
2) сухое гранулирование.
Формование гранул осуществляется протиранием (продавливание) увлажненных масс через прочные, сделанные, как правило, из специальных сортов стали сита с определенным размером отверстий. Данный процесс называется гранулированием. Механизмы, с помощью которых осуществляется гранулирование, называются грануляторами или протирочными машинами.
Гранулятор (рис. 1) содержит рабочую камеру (1), в которой через загрузочную воронку подается влажный материал, подлежащий гранулированию. В камере на двух параллельных валах (2) установлены шнеки (3), снабженные продольными стержнями (4) и лопастными колесами (5), смонтированными на противоположных концах валов. Шнеки перемещают и протирают материал через перфорированную пластину, образующую дно рабочей камеры.
Рисунок 1. |
Рисунок 2. |
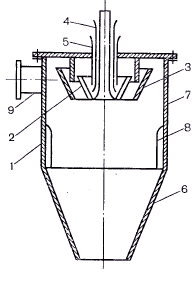
Рисунок 3. |
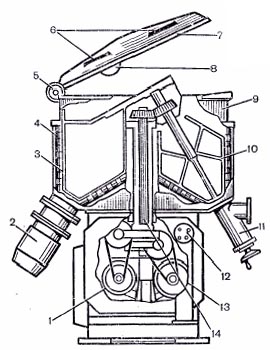
При влажном гранулировании к предварительно смешиваемому порошку в смеситель (9) подается гранулирующая жидкость и в зависимости от состава смесь перемешивается еще 3—10 мин. Подбирая скорость вращения мешалок, добиваются получения гранулята необходимой дисперсности.
После завершения процесса гранулирования открывают разгрузочный клапан (11) и при медленном вращении скребка (3) готовый продукт высыпается из емкости в течение 30—90 с для сушки в кипящем (псевдоожиженном) слое.
Сушка гранулята. Сушка увлажненных гранулятов является одним из самых энергоемких процессов.
|
|
Сушилки типа СП (рис. 4) имеют идентичную конструкцию и работают следующим образом. Поток воздуха, необходимый для псевдоожижения гранулированного или порошкообразного материала, создается вентилятором, смонтированным в верхней части аппарата (1), который приводится в действие электродвигателем (2). Воздух, засасываемый из атмосферы или из рабочего помещения, нагревается в калорифере (3) до заданной температуры, очищается в фильтре (4) и попадает в сушильную камеру, где проходит через резервуар (5) снизу вверх, псевдоожижая продукт.
Резервуар снабжен перфорированным днищем, внутренняя поверхность которого покрыта мелкоячеистой сеткой из нержавеющей стали. В нем размещены специальные ворошители (7) для обеспечения равномерности слоя, а также дополнительного перемешивания и разрушения комкующихся материалов. Размещенный над продуктовым резервуаром рукавный фильтр (6) предотвращает унос потоком воздуха высушиваемого продукта. Фильтр встряхивается после окончания сушки или в процессе ее. Это делается вручную или автоматически для отделения налипших частиц и их возврата в резервуар. Аппаратура для пуска, контроля и регулирования размещена на отдельном пульте. Температура осушающего воздуха, длительность сушки задаются механизму предварительно и поддерживаются автоматически в ходе всего процесса. Использовать сушилки типа СП не целесообразно, так как возможно совместить две технологические операции в аппарате «сушилка-гранулятор»
Методы анализа гранулята.
Гранулированные порошки обычно имеют комковатый вид с относительно равноосной формой. Графическое распределение частиц по размерам является асимметричным со смещением в область более крупных частиц (2,5—1,0 мм), средний размер гранул составляет около 600—650 мкм. Гранулированные препараты, как правило, содержат и большой процент самых мелких частиц (менее 50 мкм). Объясняется это технологией гранулирования влажного материала, которая предусматривает повторное смешивание и опудривание. При смешивании и опудривании в смесь не только вносится большое количество мелких частиц, но она к тому же еще и измельчается.
|
|
Негранулированные порошки характеризуются полифракционным составом и сложной формой. Распределение частиц по размерам подчиняется закону нормального распределения: количество больших и самых мелких частиц мало, а основная их масса имеет приблизительно одинаковые размеры. Средний размер частиц негранулированных порошков составляет около 30—120 мкм.
Наиболее простым и распространенным методом определения фракционного состава является анализ при помощи сит, при котором исследуемый материал разделяют на фракции просеиванием через стандартный набор сит в течение 5 мин, а затем находят массу каждой фракции и ее процентное содержание.
Насыпная масса (плотность) - это масса единицы объема свободно насыпанного материала. Она зависит от гранулометрического состава, влажности, плотности укладки частиц в слое, их средней плотности и др. Определяют насыпную массу путем свободной засыпки порошка в определенный объем (например, мерный стакан) с последующим взвешиванием с точностью до 0,01 г.
Лекарственные порошки, как правило, легкие и сыпучие, погрешность измерения их насыпной массы выше, чем у более тяжелых сыпучих материалов. Поэтому представляет интерес измерение не минимальной, а максимальной насыпной массы. Ее определяют на приборе модели 545Р-АК-3. Взвешивают 5 г исследуемого порошка с точностью до 1 мг и засыпают его в измерительный цилиндр вместимостью 25 мл. Устанавливают амплитуду колебаний цилиндра посредством регулировочного винта и после отметки на шкале фиксируют положение контргайкой. Далее включают прибор тумблером и следят за отметкой уровня порошка в цилиндре. После того как уровень порошка устанавливается постоянным (обычно через 5-10 мин), прибор выключают.
Максимальную насыпную плотность рассчитывают по формуле:
Насыпная масса легко и точно определяется. Считают, что она влияет на текучесть и может ее характеризовать.
Текучесть (сыпучесть) является комплексным параметром, характеризующим способность материала высыпаться из емкости под силой собственной тяжести, образуя непрерывный устойчивый поток. На текучесть неуплотненных порошков влияют многочисленные факторы, характеризующие сыпучий материал: размер, форма и насыпная плотность частиц, коэффициенты межчастичного и внешнего трения, влажность.
Чаще всего текучесть определяют по скорости высыпания определенного количества материала (100 - 30 г) из металлической или стеклянной воронки со строго заданными геометрическими параметрами и по углу естественного откоса.
Для определения текучести используется коническая воронка с углом конуса 60° и укороченным стеблем. Конец стебля воронки срезается под прямым углом на расстоянии 3 мм от вершины конуса. Диаметр выпускного отверстия изменяется от 1 до 25 мм.
Текучесть может быть точно определена при минимальном влиянии зависания порошка в тех случаях, когда отношение диаметра стебля воронки к максимальному размеру частиц достаточно велико (более 10 - 15).
Текучесть характеризуют коэффициентом текучести, который определяют по формуле:
К = t·rn/m
где t — среднее время истечения порошка, с; r — радиус выпускного отверстия воронки, мм; т — масса навески сыпучего материала, г; n — показатель степени, равный 2,58.
Текучесть выражают как среднюю скорость истечения сыпучего материала и подсчитывают по формулам, см/с:
Vтек=4v/πd2t или Vтек=4m/πd2γt
Где V – объём навески, см3; t – время истечения всей навески, с; d – диаметр стебля воронки, см; m – масса навески, г; γ – насыпная масса, г/см3
Для сравнительных определений текучести сыпучих материалов созданы стандартные приборы (например, прибор модели ВП-12А).
При высыпании сыпучего материала из воронки на горизонтальную плоскость он рассыпается по плоскости, принимая вид конусообразной горки. Угол между образующей и основанием этой горки и называется углом естественного откоса (выражается в градусах). Его величину определяют с помощью углометра, вычисляют по высоте горки и радиусу её основания.
Таким образом, угол естественного откоса является показателем, определяющим потенциальную текучесть сыпучего материала.
Влагосодержание — содержание влаги в материале. Оно оказывает большое влияние на текучесть и прессуемость порошков и гранулятов. Повышенная влажность прессуемого материала снижает его текучесть за счет образования массивных адсорбционных слоев на частицах, повышает их адгезионные свойства как друг к другу, так и к соприкасающимся с ними поверхностям. Подсушивание материала в этом случае восстанавливает его текучесть. При недостаточном влагосодержании снижается сила сцепления между частицами прессуемого материала и уменьшается прочность таблеток. Поэтому таблетируемый материал должен иметь оптимальную влажность. Для большинства материалов влажность составляет 2 - 5 %.
Влагосодержание таблетируемого материала можно определить высушиванием исследуемого образца (точная навеска от 1,0 до 3,0 г) в сушильном шкафу (при температуре 100—105°) до постоянной массы. Метод достаточно точен, однако в условиях заводского производства он неудобен вследствие своей длительности.
Для определения остаточной влажности в порошках и гранулятах наиболее приемлем метод высушивания инфракрасными лучами.
Расчет влажности производят по формуле:
где х — содержание влаги в материале, %; (а — b) - потеря в массе, г; с — навеска, г.
Прессуемость порошков (гранулята) — это способность его частиц к взаимному притяжению и сцеплению под давлением. От степени проявления этой способности зависит прочность и устойчивость таблетки после снятия давления. Лекарственные вещества, входящие в состав таблеток, обладают различной индивидуальной прессуемостью. Знание этой величины позволяет прогнозировать типоразмеры таблеток (подбор соответствующих пресс-форм) и правильно выбирать величину давления прессования для их получения. Прессуемость может быть оценена по прочности таблеток на сжатие и выражена в абсолютных величинах в мПа или через коэффициент прессуемости, который выражается отношением массы таблетки к ее высоте. Для определения коэффициента прессуемости навеску материала, которая составляет 0,3 или 0,5 г, прессуют в матрице 9 или 11 мм соответственно на гидравлическом прессе при давлении 120 мПа. Полученную таблетку взвешивают на торсионных весах, высоту измеряют микрометром и коэффициент прессуемости вычисляют по формуле:
Кпр = m/h
где m — масса таблетки, г; h — высота таблетки, см.