1) Шаровая мельница
Наиболее распространенными агрегатами для помола отощающих материалов являются шаровые мельницы.
В промышленности применяются шаровые мельницы периодические и непрерывно‒действующие, мокрого и сухого помола. Непрерывнодействующие мельницы не получили еще широкого распространения, несмотря на их бесспорное преимущество. Мельницы периодического действия более удобны в эксплуатации, хотя значительно энергоемки, позволяют изменять рецептуру массы и процесс ее приготовления в случае необходимости.
Шаровая мельница ‒ один из самых энергоемких агрегатов на керамических предприятиях. Поэтому большое значение имеет их правильная эксплуатация. Производительность шаровой мельницы и качество измельчаемого материала зависят от крупности и соотношения веса загружаемого материала, шаров, воды, скорости вращения мельницы, степени заполнения мельницы материалом и шарами. На продолжительность помола также влияет влажность суспензии. При повышенной влажности, равно как и при пониженной, время помола возрастает. Наиболее оптимальная влажность ‒ 37‒39%. Для ускорения помола отощающих материалов добавляют в массу поверхностно‒активные вещества (ПАВ), которые понижают твердость каменистых материалов, снижают вязкость суспензии [7].
Загрузка шаровых мельниц отощающими материалами производится со специальной площадки через загрузочный люк, после предварительного взвешивания всех компонентов на электровесовой тележке. Не менее важным является качество футеровки мельницы кремневой клепкой. Клепку рекомендуется класть на портландцементе М400 или 500 раствором 1:1 (цемент‒песок). Для ускорения процесса схватывания цемента после каждого периода обновления футеровки рекомендуется пропаривать мельницу острым паром в течение 2‒3 дней.
Не менее важным для процесса помола является количество мелющих тел, загружаемых в мельницу, их размеры и материалы, из которых они изготовлены. Наиболее распространенными являются кремневые (естественные), фарфоровые и уралитовые шары, специально изготовленные из фарфоровой и высокоглиноземистой массы. Размеры, количество применяемых шаров и их качество существенно сказываются на скорости и степени помола. Так, чем больше шаров, тем больше ударов произойдет за один оборот мельницы при одинаковой затрате энергии. Практически установлено оптимальное соотношение шаров, сырья, воды как 1,3:1,0:1,0.
2) Литейно‒подвялочный конвейер
Формование умывальников на литейно‒подвялочном конвейере включает следующие операции: подготовка гипсовых форм, заливка шликера, набор и закрепление черепка, слив шликера, разборка форм, оправка, подвялка изделий и сушка форм.
Литейно‒подвялочный конвейер для производства умывальников СМ‒462А работает по комбинированному способу. Этот конвейер имеет дне самостоятельные параллельные двухъярусные ветви, между которыми расположены подвялочный люлечный конвейер и возврата воронок и подвесная дорога для уборки отходов. Формы укреплены на каретках, перемещаемых по рельсам толкателями. На нижнем ярусе рабочие очищают гипсовые формы и обдувают их сжатым воздухом. Затем формы автоматически закрываются и в них вставляют воронки и сливные пробки. Механизмом в формы заливается шликер, после чего формы поступают в камеру набора черепка. По окончании набора черепка из формы вынимают сливную пробку и сливают избыточный шликер из бортов умывальника, которые отливаются полыми. Здесь же вынимают воронки, очищают их, укладывают на конвейер возврата к местам заливки форм. После слива шликера каретку гидроподъемником передают в верхний ярус в камеру закрепления черепка, пройдя которую, она снижателем передастся в нижний ярус на позиции съема изделий. Отлитый умывальник вынимают из формы, предварительно оправляют и пневмосъемнйком 6 устанавливают на люльку подвялочного конвейера по окончании подвялки влажность изделия снижается до 12—14%. После этого изделие окончательно оправляют и направляют в сушилку.
Стендовый способ отливки изделий. При стендовом способе гипсовую форму очищают от прилипших остатков массы, собирают, скрепляют металлическими стяжками и устанавливают' на литейном столе. Если необходимо, формы закрепляют на столе или скрепляют в батареи по 15—16 шт. После этого промазывают все швы формы массой, вставляют воронку и резиновым шлангом равномерной струей заливают шликер. Залитую форму выдерживают до образования черепка необходимой толщины (при сливном методе) или до образования черепка необходимой влажности (21—22%).
Характеристики литейно‒подвялочного конвейера для производства умывальников СМ‒462А:
Годовая производительность в тыс. шт......... 200‒240
Количество обслуживающего персонала...... 8
Производительность в смену в шт................ 198‒208
Занимаемая площадь в м2........................... 422
Металлоемкость конвейера в т.................... 59,6
3. Туннельная печь
Современные туннельные печи обеспечивают непрерывность загрузки, процесса обжига и выгрузки изделий, соблюдение постоянства температурной кривой обжига, ‒ возможность автоматического регулирования режима обжига, охлаждения, гидравлического режима, возможность использования отходящего из зоны охлаждения тепла для сушки изделий.
По характеру ведения огня туннельные печи бывают прямого действия и муфельные.
В туннельных печах для обжига используются природный газ, жидкое топливо (мазут). В печах прямого действия топочные газы в процессе обжига омывают изделия. В муфельных туннельных печах нагрев изделий производится за счет радиации стенок муфеля и за счет циркулирующего подогретого воздуха в канале печи.
Туннельная печь состоит из печного канала, устройства для нагрева и охлаждения изделий и циркуляции печных газов, агрегата для передвижения в печном канале печных вагонеток с изделиями, приборов для регулирования и поддержания заданной температуры и аэродинамического режима в печи.
Туннельные печи работают по принципу противопотока, т. е. вагонетки с изделиями движутся навстречу обогреваемым, а затем охлаждающим печным газам. В зависимости от высоты канала печи садка изделий может быть одно-, двух- и трехъярусной. Изделия устанавливаются на плиты вагонетки с канализированным подом. В туннельной печи предусмотрены три зоны ‒ подогрева, обжига и охлаждения. Количество позиций этих зон обусловлено длиной печи, температурными режимами.
Для сокращения температурных перепадов по сечению печи в зоне подогрева предусмотрено рециркуляционное устройство, обеспечивающее интенсивное перемешивание тепловых потоков воздуха. Теплый воздух забирается из подовой части и подается в развитый под вагонетки.
У входа печь оборудована входной камерой, имеющей два подъемных шибера и гидравлический толкатель. На выходном конце печи имеется подъемный шибер. Печи оборудованы автоматическими приборами теплового контроля, регулирования максимальной температуры обжига, аэродинамического режима, соотношения давлений в рабочем и подвагонеточном пространстве [6, c.34].
Недостатком работы туннельных печей являются большие перепады температур по сечению канала печи, особенно при двух- и трехъярусной садке изделий. В зоне подогрева эти перепады увеличиваются за счет подсоса холодного воздуха через, неплотности в стыках вагонеток и песочных затворов. Так как в зоне подогрева в канале печи предусмотрено разрежение, этот перепад температур не удается устранить из-за поступления воздуха из подвагонеточного пространства в канал печи; иногда этот перепад температур достигает существенной разницы ‒ до 200‒350°.
Таблица 2.9 ‒ Технологические параметры туннельной печи
Показатели | Печи с количеством ярусов | |||
Размеры канала печи, м: длина ширина высота | 59-68 1,1-1.2 1,04 1,21 | 92,5 1,1-1,5 1,04 | 1,4 1,09 | 88-96 1,6 0,9-1,11 |
Объем обжигового канала, м3 | 68-85 | 150-165 | ||
Количество вагонеток в печи, шт. | 32-36 | |||
Загрузка на вагонетки,кг | 120-160 | 145-195 | 170-180 | 220-240 |
Продолжительность обжига, ч | 18-25,5 | 22,5 | 21-25 | 18-25 |
2.5 Технологический процесс производства санитарно‒строительных изделий
В данной курсовой работе рассмотрим способ производства сантехнических изделий методом литья под давлением.
Преимущества данного метода заключаются в:
1. строгой симметричности изделия и отсутствие различных дефектов поверхности;
2. равномерности толщины черепка по всему сечению, что препятствует деформации;
3. высокой плотности черепка, что определяет прочность и долговечность;
4. ускоренном процессе формирования черепка, что сокращает весь процесс производства в целом примерно на одни сутки.
Технологический процесс производства сантехники состоит из 6 стадий:
1. Подготовка шликерной суспензии
Шликерная суспензия представляет собой определенным образом подготовленную массу из сырьевых материалов, которые по выполняемым функциям разделяются на:
![]() | ![]() | ![]() | ![]() | ![]() |
| |||||||
![]() | ![]() | ||||||||||
![]() | ![]() | ![]() | ![]() | ||||||||
|
|
|
|
|
|
|
|
|
|
|
|
|



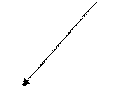
вода,
электролиты
![]() |
|
![]() |
![]() |
|

![]() |
![]() | |||
![]() | |||
|
Рис. 6 ‒ Технологический процесс производства санитарно‒строительных изделий
‒ пластичные (глина, каолин) – являются основой формирования структуры черепка в процессе литья, сушки и обжига;
‒ отощающие (кварцевый песок, пегматит, бой изделий)‒ стабилизируют форму (препятствуют деформациям).
Шликерная суспензия представляет собой определенным образом подготовленную массу из сырьевых материалов, которые по выполняемым функциям разделяются на:
‒ пластичные (глина, каолин) – являются основой формирования структуры черепка в процессе литья, сушки и обжига;
‒ отощающие (кварцевый песок, пегматит, бой изделий)‒ стабилизируют форму (препятствуют деформациям).
В зависимости от оборудования, с помощью которого происходит процесс получения полуфабриката, используются различные соотношения сырьевых материалов. В частности, для изделий производимых по технологии литья под давлением, наряду с украинской, используется менее пластичная немецкая глина. В производстве применяется в основном импортное сырьё и материалы из Украины, России, Германии, Италии.
Шликер готовят раздельным помолом сырьевых материалов в шаровой мельнице мокрого помола. Взвешенные кюбеля загружаются сырьевыми материалами, в соответствие с рецептом, и подаются краном электрическим подвесным в шаровую мельницу. Глина Веско‒Гранитик подается в два приема. Через водомер вода заливается в мельницу в соответствии с рецептом. Электролиты взвешиваются на весах и загружаются в мельницу. Помол отощающих в шаровых мельницах производится до остатка на контрольном сите с сеткой №0063 – не более 5%. Параметры шликера в шаровых мельницах: плотность 1,67–1,72 г/см3, влажность 30‒35 %. После 3,5–5,5 часов помола смолотые отощающие насосом (7,7а) подаются в емкость с турбораспускателем.
Глина Веско‒Гранитик краном подвесным электрическим загружается в ёмкости с турбораспускателем, распускается в течение 1,5‒2 часа, затем загружается глина Santon‒L и распускается в течение 1,5‒2 часов, добавляется необходимое количество воды и электролитов и загружается каолин в два приема с перерывом 0,5 часа. Перемешивание производится до полного роспуска глинистых компонентов в течение 2,5–3 часов. Для усреднения шликер в течение 1 часа выстаивается, затем проверяется однородность приготовленной суспензии (в случае необходимости время роспуска глины и каолина увеличить). Готовый шликер из ёмкости с турбораспускателем по шликеропроводу насосом через вибросито подается в промежуточный бассейн. Затем насосом по шликеропроводу через вибросито с сеткой № 02 и №018 иэлектромагнитом перекачивается в рабочие ёмкости. Сливной шликер подается в сливные бассейны, а затем насосом подаётся по шликеропроводу через вибросито в рабочие емкости в соотношении 1:1–1:2 со свежеприготовленным шликером. Усредненный шликер после выстаивания в течение не менее двух суток подается насосом по шликеропроводу в заливочные емкости для подачи настенды.Шликер насосом по шликеропроводу подается в ёмкость для подогрева. Температура шликера 40–42°С.
Литье производится на стенде под давлением ALS‒150(бачки, умывальники, пьедесталы). После подготовки стенда к работе производят запуск цикла. Внутрь пористой формы под давлением подаётся шликер. Набор черепка происходит следующим образом: под давлением воздуха, подаваемого в форму, вода, содержащаяся в шликере, уходит через поры формы, вызывая образование слоя керамической массы (черепка). По истечении времени, необходимого для набора черепка, происходит слив шликера. Сушка изделий осуществляется следующим образом: внутрь изделий под давлением подается воздух, что способствует закреплению черепка. Извлечению изделий из форм способствуют дренажные сети, имеющиеся внутри формы и позволяющие распределить сжатый воздух (или воду) по поверхности формы, контактирующей с изделием (а также создавать на поверхности некоторую степень вакуума). После извлечения изделий из форм производят оправку изделий. Затем выставляют изделия на конвейер. Для промывки полимерных форм вода по трубопроводу подается на установку очистки воды «Акватон», которая предназначена для удаления солей кальция и магния.
2. Получение полуфабриката
При производстве на стендах литья под давлением процесс получения полуфабриката существенно сокращается за счёт уменьшения времени на формирование черепка. Набор черепка происходит следующим образом: при увеличении давления воздуха, подаваемого в форму до 13 бар, вода, содержащаяся в шликере, уходит через поры полимерной формы, вызывая образование слоя керамической массы (черепка). В результате через 20 ‒ 30 минут из каждой формы получается полуфабрикат, который при этом имеет равную толщину по всему объему и исключает деформацию.
Требования, предъявляемые к полуфабрикату
Шликер для литья изделий под давлением должен соответствовать следующим требованиям:
– плотность 1,795-1,82 г/см3;
– массовая доля влаги 27-29%;
– массовая доля остатка на сите №0063 2,0-3,0%;
– воздушная усадка 2-2,5%;
– полная усадка 10-11%;
– механическая прочность не менее 1,97 Н/мм2;
– водородный показатель 8,0-9,2;
– потери при прокаливании 5,7-6,5%;
– массовая доля (свободного) 24-29,5%;
– массовая доля 24-27,5%.
3. Обработка полуфабриката. Сушка
Извлечённые из форм полуфабрикаты имеют значительную влажность, в то время как влажность изделий перед глазуровкой не должна превышать 1%. Поэтому после специальной обработки, извлечённые из форм полуфабрикаты, нуждаются в сушке. Сушка осуществляется в конвейерной сушилке производства Progetti (при температуре до 100° С). Показатель влажности изготовленной заготовки составляет 15‒17% после полимерных форм, поэтому продолжительность сушки для полуфабрикатов из полимерных форм составляет ‒ от 17‒18 часов.
Сушка всех видов полуфабрикатов санитарных керамических изделий осуществляется в сушилке непрерывного действия, которая обеспечивает быстрый режим сушки. Это обеспечивается наличием внутренних сопел, которые обдувают изделия воздухом. Полки люлек толкающего конвейера должны быть обиты ворсонитом или другими мягкими материалами. Продолжительность сушки составляет не мене 8 часов. Массовая доля влаги в изделиях после сушки не более 1%.
4. Глазурование
После сушки полуфабрикат подвергается глазурованию – операции, от которой в значительной степени зависит внешний вид и качество готового изделия. Глазурование осуществляется с помощью автоматической глазуровочной установки с роботом напыления GA 900 EV (производства SACMI). Данное оборудование позволяет равномерно наносить глазурь по всей поверхности и обеспечивает высокую белизну изделий.
После нанесения глазури, на умывальники и бачки всех коллекций наносится деколь «Керамин», что делает санитарную керамику еще более узнаваемой среди конкурентов.
Сырьевые материалы в кюбелях взвешиваются на весах в соответствии с рецептом, откорректированным лабораторией с учетом массовой доли влаги и химического состава сырьевых материалов. Взвешенные сырьевые материалы краном электрическим подвесным подаются в шаровую мельницу для совместного помола. Продолжительность помола глазури (10±2) часов.
После помола глазурь из мельницы сливается насосом через вибросито с сеткой №0125 в емкости сбора и хранения глазури. Из емкости глазурь пневмоприводным насосом через электромагнит подается в емкость с быстроходной мешалкой для приготовления глазури для нанесения на автоматической глазуровочной установке с роботом напыления.
В расходную емкость для стабилизации вязкости подается приготовленный раствор пептапона‒52.
Глазурование изделий осуществляют на автоматической глазуровочной установке с роботом напыления GA 900 EV и способом ручного напыления в камерах.
Перед глазурованием на автоматической глазуровочной установке с роботом напыления GA 900 EV полуфабрикат обдувается сжатым воздухом в камере обеспыливания и замывается рабочая и лицевая поверхность влажной губкой. Производится глазурование внутренних поверхностей сифонов и колец унитазов. Давление глазури на устройстве устанавливается от 1,5 до 1,75 бар. Изделия автоматически переставляются на каретку глазуровочной карусели, и производится глазурование изделий роботом, согласно заданной программе. В течение технологического процесса осуществляется визуальный контроль за выполнением требуемых операций. Заглазурованные изделия автоматически подаются к разгрузочному конвейеру и переставляются с каретки глазуровочной карусели на блок разгрузки и транспортируются к месту разгрузки. Изделия вручную снимаются с конвейера, и производится зачистка установочных поверхностей. После глазурования изделия вручную устанавливаются на полку подвесного люлечного конвейера для сушки. Массовая доля влаги в изделиях перед заталкиванием в печь не более 1,0 %.
Изделия перед глазурованием способом ручного напыления в камерах обдуваются сжатым воздухом, замывается рабочая и лицевая поверхность влажной губкой. Особое внимание обращается на чистоту сифона унитаза. На невидимой поверхности изделия керамической краской при помощи резинового штампа наносится товарный знак предприятия и номер смены, номер глазуровщика. Подготовленное изделие устанавливается на глазуровочный столик и подвергается глазурованию пистолетом для ручного напыления jGV–562/3. Заглазурованное изделие устанавливается на стеллаж, подвергается зачистке установочных поверхностей, а затем выставляется на конвейер, транспортирующий изделие на участок ставилки.
5. Обжиг
Заключительной операцией технологического процесса производства является обжиг полуфабриката в туннельной печи итальянской компании «Sacmi» на протяжении 19‒22 часов. Температура в печи вначале постепенно повышается до 1200° С, а затем также плавно происходит её снижение. Подобный температурный режим требуется для получения качественных изделий, как в отношении самого черепка, так и в отношении глазурованного покрытия. Использование современной печи для обжига позволило существенно уменьшить вероятность таких дефектов, как наколы, засорка, вскипание глазури. Установлена ремонтная печь, предназначенная для для однократного обжига и повторного обжига для исправления дефектов.
Обжиг изделий производится в туннельной печи открытого пламени с автоматическим регулированием на печных вагонетках с развитым подом. Вид топлива – природный газ. Печная вагонетка должна иметь развитой под в виде одноярусной этажерки, выполненный из огнеупорных плит. Рабочая поверхность вагонетки должна быть ровной и покрыта ангобом с массовой долей влаги (30±2) %. Температурная кривая приведена в прилож. 3.
Обожженные изделия снимаются с вагонетки и устанавливаются на предназначенные для готовых изделий площадки раздельно по ассортименту. При сортировке каждое изделие простукивается и осматривается на соответствие требованиям ГОСТ 15167–93, ГОСТ 30493- 96 и ГОСТ 21485-94. При этом зашлифовываются слипыши и следы от подставок, заделываются белым цементом допускаемые посечки. Изделия, имеющие дефекты, поддающиеся исправлению, отбираются контролером-приемщиком и оставляются в специально отведенном месте. Места дефектов отмечаются маркером. Годные изделия люлечным конвейером транспортируются на склад готовой продукции. Брак изделий направляется в цех №5 на переработку. После исправления дефектов (лечки) санитарных керамических изделий производится повторный их обжиг в печи периодического действия SSK 440/170-6. В этой же печи может производиться первичный обжиг полуфабриката.
6. Сортировка
Сортировка является заключительным этапом системы контроля качества за технологией производства на предприятии, который существует на всех основных операциях: осмотр изделий после процесса литья, сушки, нанесения глазури.
Следует отметить, что все изделия строго соответствуют стандартам качества по ГОСТ, а также, принятой на предприятии, технологической инструкции по установлению критериев качества для изделий санитарно‒керамических. Данная инструкция ужесточает требования и является основополагающим документом при сортировке изделий.