При производстве профилей, прутков и труб используется типовая технологическая схема. Такая схема применительно к процессу прессования алюминиевых профилей на горизонтальных гидравлических прессах показана на рисунке 5.1.
Характеризуя типовой технологический процесс, отметим, что заготовки используют чаще литые, реже деформированные. Для расчета размеров слитка используют рекомендации И.Л. Перлина, в соответствии с которыми общая вытяжка при прессовании должна быть не менее 10. Отношение длины слитка L сл к диаметру для полых профилей должно составлять 1,5–2, а для сплошных – 2–3. Массу слитка подбирают по усилию пресса. Перед прессованием производят обработку слитка.
Наиболее эффективный способ удаления поверхностных дефектов слитка – это горячее скальпирование, т. е. проталкивание слитков через матрицу с острой кромкой (на отдельном прессе усилием 2-3 МН, расположенном на выходной стороне нагревательной печи). При этом снимается слой толщиной 2-3 мм. Слитки подвергают гомогенизации (нагреву и выдержке при заданной температуре) с целью устранения дендритной ликвации и повышения пластичности литой заготовки.
|
|
Рисунок 5.1 – Типовая технологическая схема прессования
Оптимальная температура нагрева слитка зависит от пластичности и прочности металла, степени неравномерности деформации, окисления поверхности, схватывания (сваривания) металла с инструментом, скорости остывания металла в контейнере и т.д. Температурный интервал прессования шире у однофазных сплавов и чистых металлов. Перед прессованием латуни, магниевых, алюминиевых сплавов и других применяют подогрев контейнера, матрицы и пресс-шайбы до 200–250 оС, а иглы – до 350 оС.
При прессовании прутков алюминиевых сплавов контейнер подогревают до 330–430 °С. Технологическая смазка поверхности контейнера и пресс-шайбы уменьшает усилие прессования, остывание заготовки, неравномерность деформации, удлиняет срок службы инструмента. Обычно в качестве смазки применяют смесь графита с машинным маслом.
После прессования профили проходят термическую обработку, их режут на мерные длины, правят на правильно-растяжных машинах, устраняют поверхностные дефекты вырубкой, шабровкой, травлением и другими методами. Термическую обработку (закалку, старение) проводят, как правило, в электрических печах. Для защиты от коррозии изделия покрывают лаком, краской, оксидируют, анодируют, смазывают и т. п.
Основным видом оборудования для прессования профилей, прутков и труб является горизонтальные гидравлические прессы усилием от 8 до 35 МН. В настоящее время на ряде заводов имеются прессы и большего усилия 50 и 70 МН. На базе гидравлических прессов последнее время на многих заводах созданы установки полунепрерывного прессования, включающие устройства натяжения и охлаждения пресс-изделий.
|
|
Инструмент, применяемый для прессования на горизонтальных гидравлических прессах, включает контейнер, пресс-штемпель, матрицы, пресс-шайбы, иглы и др.
Контейнер пресса (рисунок 5.2) состоит из корпуса, внутренней и промежуточной втулок. Корпус имеет каналы для размещения нагревателей, а на быстроходных (50–70 прессовок/ч) прессах также каналы для охлаждения. Внутренняя втулка изготовляется из теплостойкой стали, часто с упрочняющей наплавкой.
Пресс-штемпель изготовляют из поковок легированной стали с пределом прочности, равным 1600–1700 МПа.
Пресс-шайба служит для предохранения пресс-штемпеля от разогретого слитка.
Матрицы – это наиболее ответственные и быстроизнашиваемые детали инструмента (рисунок 5.3). Матрица служит для формирования контура пресс-изделия и определяет точность его геометрических размеров и качество пресс-изделий. Матрица устанавливается в передней части втулки контейнера и замыкает ее полость с заготовкой. Изготовляют матрицы из высоколегированных сталей и жаропрочных сплавов.
|
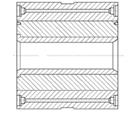
а – плоские; б – плоско-конические; в – конические; г – радиальные; д – с двойным конусом; е – со вставкой из жаропрочных или твердых сплавов
Рисунок 5.3 – Виды матриц
Из мягких материалов на основе алюминия прессуют фасонные профили (рисунок 5.4).
Для равномерного истечения «тонких» и «толстых» элементов профиля рекомендуется «тонкие» элементы размещать ближе к центру, увеличивать ширину пояска матрицы и применять тормозящий конус (рисунок 5.5) на «толстых» элементах профиля. Язычковую матрицу используют при прессовании полых профилей.
Одной из важнейших задач при разработке технологического процесса прессования является правильное изготовление прессового инструмента, в основе которого лежит проектирование прессового инструмента: матриц, форкамер, подкладок и спецподкладок и т. д.
Проектирование матрицы состоит из следующих основных этапов: подготовки чертежа нормали профиля; определения геометрических размеров канала матрицы с учетом припуска на температурную усадку; выбора способа прессования и оборудования; размещения канала или каналов на зеркале матрицы; расчета рабочего пояска; подготовки чертежа матрицы.
|
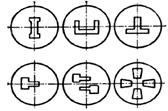
|
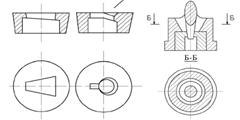
Для процесса проектирования матриц характерно высокое влияние субъективного фактора, который проявляется при размещении каналов на зеркале матрицы, поскольку не существует четкой методики их проектирования. Поэтому был выработан ряд рекомендаций по размещению каналов на зеркале матрицы. В большинстве случаев центр тяжести сечения канала располагают в центре зеркала матрицы. Этот же принцип использует и при проектировании многоканальных матриц, когда несколько каналов профилей образуют симметричную фигуру, центр тяжести которой расположен в центре зеркала матрицы. При проектировании матриц для прессования несимметричных профилей необходимо ориентировать разнотолщинные элементы тонкими полками к центру матрицы.
При выборе расположения профиля на зеркале матрицы (рисунок 5.6) каналы следует располагать на одной линии, что исключает соприкосновение профилей во время движения по выходному столу и обеспечивает возможность их захвата зажимным устройством движущейся каретки захватного органа (пулллера).
Рисунок 5.6 – Рациональное расположение каналов, обеспечивающее
качественную поверхность
Выполнение разновысоких рабочих поясков матриц необходимо для выравнивания скоростей истечения различных элементов профиля.
|
|
Для процесса полунепрерывного прессования также проектируются форкамеры, исходными данными для чего служат чертеж матрицы и технологические характеристики процесса прессования (например, величина вытяжки из форкамеры в матрицу). Проектирование форкамеры заключается в определении геометрических размеров эвкидистантной фигуры, описанной вокруг профиля и глубины форкамеры, на основании чего строится ее чертеж.
Литература 1 осн. [9-15], 6 осн. [57-98], 7 доп [8-251], 9 доп [3-341].
Контрольные вопросы
1. В чем заключаются преимущества непрерывного прессовании?
2. Какова последовательность технологического процесса при прессовании?
3. Какой инструмент применяется при прессовании труб?
4. Для чего служит контейнер пресса?
5. Какова последовательность этапов проектирования прессовых матриц?