Ковка – это процесс обработки металлов давлением, при котором необходимое изменение форм и размеров заготовок достигается путем ударов или нажимов бойками, не ограничивающих течение металла в плоскости перпендикулярной оси приложения давления. К достоинствам ковки относится возможность обрабатывать давлением крупные слитки, масса которых достигает нескольких сотен тонн, улучшая структуру и механические свойства обрабатываемого металла и исправляя дефекты литого металла.
В качестве исходного материала для ковки применяют стали всех марок, алюминиевые, магниевые, титановые сплавы, а также сплавы на основе меди и никеля.
Ковка слитков протяжкой из цветных сплавов в одном направлении при достаточных степенях обжима приводит к измельчению зерна с образованием волокнистой структуры. При этом повышаются показатели механических свойств, однако одновременно возникает их анизотропия в продольном и поперечном направлениях, которую устраняют ковкой в трех взаимно перпендикулярных направлениях по схеме осадка – протяжка – осадка.
Для ковки поковок небольшой массы используется различный прокат, такой как блюмы, катанка круглого и квадратного сечения (сортовой прокат), периодические и сортовые профили. Кроме того, кузница перерабатывает прутки, полученные волочением и прессованием.
К достоинству ковки относят возможность с помощью простого и дешевого инструмента изготовлять поковки разнообразной формы и размеров любой массы (от гаек и болтов до коленчатых валов современных кораблей). Главным преимуществом процесса ковки является возможность обрабатывать крупные слитки и заготовки. В тяжелом машиностроении количество кованых поковок достигает 90 %, а в автомобилестроении (серийное и массовое производство) до 98 % их изготовляются объемной штамповкой. Поэтому потребность, а также вид и объем продукции обусловливает применение ковки. Ковку используют в единичном и мелкосерийном производстве. К ее недостаткам можно отнести значительный расход металла (коэффициент использования металла составляет 37 %) и низкую производительность по сравнению с объемной штамповкой.
Нагрев заготовок перед ковкой сопровождается изменением структуры и механических свойств исходного материала. С превышением температуры металла свыше величины, составляющей диапазон 0,3–0,4 от температуры плавления, начинают протекать процессы возврата и рекристаллизации. Ковочные температуры находятся между температурами плавления и интенсивной рекристаллизацией сплава. Более низкие температуры относятся к холодному деформированию. При нагреве заготовок в случае несоблюдения технологических требований могут иметь место явления перегрева и пережога. Первое ведет к росту зерен и резкому снижению механических свойств, а второе сопровождается окислением поверхности зерен и полной потерей пластических свойств. Поэтому выбор температур нагрева заготовок является важной технологической задачей.
Температурный интервал ковки – это максимальная температура нагрева металла в печи (верхний предел) и температура окончания процесса деформации поковок (нижний предел). Различают допустимый и рациональный температурные интервалы ковки. Допустимый является более широким и не зависит от размеров и формы поковок, а рациональный назначается с учетом опыта освоения технологического процесса для конкретных заводских условий.
В качестве основного оборудования для ковки применяют прессы и молоты. Выбор оборудования зависит от технологии получения поковок, заданной программы выпуска и особенностей деформации обрабатываемого сплава. В качестве инструмента для ковки применяют плоские, вырезные или плоско-вырезные бойки.
Выделяют основные (осадка, протяжка и прошивка) и вспомогательные (рубка, кузнечная гибка, передача, скручивание и др.) операции ковки.
Технологический процесс ковки обычно начинается с разделки слитка. Обычные стальные кузнечные (рисунок 7.1) слитки отливают сверху в изложницы с полостью, имеющей форму усеченной пирамиды и поперечное сечение шести-, восьми-, двенадцатиугольника. Форма слитка учитывает условия кристаллизации металла и требования к поковке. Прибыльная 1 и донная 3 части слитка 2 удаляются в кузнечном цехе. Масса слитка колеблется в пределах M сл = 0,2 – 350 т.
|
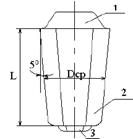
Отношение наибольшей длины L, используемой для изготовления поковок, к среднему диаметру D ср слитка обычно изменяется в пределах L ср/ D ср = 1,9 – 2,3.
При значениях L ср/ D ср = 2,3 наблюдается искривление слитка при ковке. Для изготовления длиноосных поковок используются удлиненные слитки с соотношением L ср/ D ср = 3 – 5. Эти слитки не подвергаются осадке бойками либо предусматривается их разрубка на части. Преимущества этих слитков заключаются в более однородном химическом составе металла.
Полые слитки получают методом центробежного литья в изложницы с холодильниками. Размеры полого слитка несколько меньше по сравнению с обычными слитками, так, L ср/ D ср = 1,25. Важным условием кристаллизации является отношение L / δ ≈4, (δ – толщина стенки полого слитка). Применяют полые слитки для поковок с отверстиями (устраняется операция прошивки). Преимуществами их являются меньшая продолжительность нагрева перед ковкой и то, что слитки не имеют осевой рыхлости и внецентренной ликвации.
Кроме того, получают малоприбыльные слитки, бесприбыльные, слитки с повышенной конусностью (до 12о).
Слитки из алюминиевых сплавов отливают непрерывным способом, D max ≈ 800 мм.
Круглые слитки из магниевых сплавов диаметром до 540 мм также получают непрерывным способом. Таким же способом получают плоские слитки размерами до 165×540×6000 мм.
Слитки из медных сплавов отливают в водоохлаждаемые изложницы (D max = 300 мм). Возможно непрерывное получение слитков.
Слитки из титановых сплавов получают дуговой вакуумной плавкой с расходуемым электродом в медном водоохлаждаемом кристаллизаторе (D max = 700 мм).
Существуют следующие дефекты слитков: Усадочная раковина и усадочная рыхлость; плены, появляющиеся в результате брызг жидкого металла при заливке; возникновение прямой ликвации легирующих компонентов и примесей в сплаве; трещины, пузыри и т.д.
Если на поверхности отливок сортового проката имеются дефекты (коррозия, плены, трещины), то они удаляются при помощи операций зачистки. Различают газопламенную зачистку, обработку пневмомолотками, зубилами, зачистку полировальными кругами.
Обычно слитки перед ковкой характеризуются структурной неоднородностью металла по сечению. Основным требованием к заготовке служит получение мелкозернистой структуры и однородного химического состава.
Степень уменьшения сечения при деформировании может служить показателем проработанности структуры. Оценивают эту степень показателем укова:
У = F нач/ F кон = L кон/ L нач.
Анизотропия свойств связана с различием свойств металла в поперечном и продольном направлениях. В этом смысле можно выделить 3 диапазона:
1. У = 2 – 3 – волокнистая структура (только средняя часть заготовки);
2. У = 3 – 6 – одинаковые свойства в продольном и поперечном направлениях (рабочий диапазон ковки);
3. У = 10 и более – анизотропия свойств.
Разделка слитков является операцией ковки и осуществляется с помощью прессов, при этом производится биллетировка слитка (сбивка граней и устранение конуса), удаляется донная и прибыльная части слитка (рисунок 7.2).
Прокатанный или прессованный металл разделывают на мерные длины в заготовительных отделениях кузнечно-штамповочного цеха. При этом используются резка на пилах, пресс-ножницах, хладноломах, с помощью газовых резаков, токарно-отрезных и горизонтально-фрезерных станках, электроискровая резка.
Резка кривошипными пресс-ножницами (рисунок 7.3) наиболее производительный способ разделки пруткового металла на заготовки. Пруток 1 подается по рольгангу до упора 2 в зону реза между верхним 3 и нижним 4 ножами пресс-ножниц. С целью избежания опрокидывания в процессе резки пресс-ножницы снабжены прижимным устройством 5.
а – оттяжка цапфы под патрон; б – протяжка; в – отделение донной части; г – разметка и отделение прибыльной части
Рисунок 7.2 – Биллетировка слитка
Резка металла происходит в 3 стадии (упругой, пластической и скола). В элемент надавливания ножей в прутке возникают упругие деформации. Под действием пары сил с моментом M = Pa пруток изгибается, причем в зоне соприкосновения ножей с металлом наблюдается смятие последнего. Повороту прутка препятствует сила прижима. В момент, когда напряжения от действия ножей становятся больше сопротивления пластической деформации металла, происходит их внедрение в пруток. По достижении максимально возможной величины внедрения для данного материала образуются встречные трещины, называемые опережающими. При нормальной величине зазора Z между ножами противоположные трещины сходятся, образуя сплошную криволинейную поверхность.
|
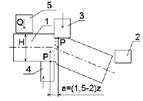
Максимальное усилие, необходимое для резки металла между параллельными ножами, определяют по формуле P = kF ср σср, МН, где k – коэффициент, учитывающий условия резки (состояние ножей, скорость резания), k = 1,0–1,7; σср – сопротивление срезу, принимаемое равным 0,7– 0,8 от предела прочности материала; F ср – площадь среза.
Резку высокоуглеродистой и легированной сталей ведут с подогревом до t = 450–650 oC.
Различают 3 вида пил: зубчатые, гладкие (пилы трения) и электромеханические. Заготовки, получаемые с помощью пил характеризуются точностью размеров, хорошим качеством реза и перпендикулярностью торца к оси заготовки. Но производительность при резке пилами значительно ниже, чем на кривошипных ножницах.
Зубчатыми пилами режут как сталь, так и цветные металлы. Различают ленточные и дисковые пилы.
Пилы трения получили небольшое распространение. Принцип их действия заключается в выделении большого количества тепла при трении о металл гладкого диска или диска с тупыми П-образными зубьями.
При использовании электромеханических пил в месте контакта создается электродуга, которая способствует расплавлению. Они сходны с пилами трения, но производительность их выше и производят они меньше шума.
Ломка хладноломами (рисунок 7.4) применяется для разделки прутков на заготовки из стали средней твердости. Пруток 1, предварительно надрезанный, укладывается на ломатель 2 до упора 3. При надавливании опор 4 на пруток в месте надреза происходит ломка.
Усилие ломки круглых прутков P = (0,4 β D 3σв)(1/ l о).
Усилие ломки квадратных прутков P = (0,5 β Н 3σв)(1/ l о), где β – коэффициент поправки, β = 0,4 − 0,9.
Газопламенная резка заключается в местном нагреве металла в струе кислорода. С ее помощью можно получить контуры реза сложной формы. Большие потери металла происходят по месту резки в шлак (слой 4 – 6 мм). В качестве горючего используют ацетилен, бензин, керосин. Нельзя обрабатывать легированные стали, так как в зоне реза наблюдаются структурные изменения металла (рост зерна, выгорание легированных элементов и т. д.). Кроме того, недостатком этого способа резки является недостаточно высокая производительность. К другим видам резки относятся: плазменная (аргоно-водородные, азотно-водородные смеси); лазерная; электроискровая резка; анодно-механическая; резка взрывом.
Рисунок 7.4 – Схема ломки с помощью хладнолома
Потери металла можно разделить на прямые и косвенные. К прямым (зависят от способа резки) относятся: пилы – отходы на пропил; электрическая и газовая резка – потери на сгорание и расплавление; хладноломы – потери при последующей штамповке в облой;
К косвенным относятся: неточность резки, потери на концы, некратность.
Расход металла можно определить по формуле: Q = Q 3 k, где Q З – масса заготовки; k – коэффициент, k = L /(L - l н); L – длина прутка; l н– длина заготовки.
Литература 1 осн. [16-25], 2 осн. [28-61], 8 доп [51-251].
Контрольные вопросы
1. Чем определяется экономическая и технологическая целесообразность применения операций ковки?
2. Каковы допустимые температурные интервалы ковки для сталей?
3. Какие виды оборудования применяются для ковки?
4. Какие операции ковки можно отнести к основным?
5. Каковы дефекты стальных кузнечных слитков?
6. Как производится биллетировка слитков?