Прессованием называют выдавливание металла из замкнутого объема через отверстие. Широко используют прессование для получения прутков, труб и профилей из алюминиевых и медных сплавов, сталей, титана и других тугоплавких металлов. В качестве разновидностей прессования можно выделить дискретное (прерывное), полунепрерывное и непрерывное прессование.
Сортамент пресс-изделий следующий: прутки диаметром 50–400 мм, трубы диаметром 20–400 мм с толщиной стенки более 1 мм, фасонные профили с площадью поперечного сечения до 500 см2, которые невозможно получить другими способами обработки давлением. Из плоского контейнера прессуют ребристые панели шириной до 1 м, из круглого – до 2,5 м. Изделия могут иметь утолщения на концах («законцовки») или плавно изменяющиеся размеры поперечного сечения. Наиболее разнообразны пресс-изделия из алюминия и его сплавов. Промышленный сортамент прессованных профилей из алюминиевых сплавов в настоящее время включает десятки тысяч типоразмеров. Однако, несмотря на столь широкий сортамент, профили по геометрической форме могут быть подразделены на четыре группы: профили сплошного сечения; профили переменного сечения; пустотелые (полые) профили; проволока; панели.
Наибольшее применение в производстве при этом нашли прутки, профили сплошного сечения, проволока и катанка.
Наиболее распространенной является схема прямого дискретного прессования на горизонтальных гидравлических прессах, которая протекает циклически. Данная схема характеризуется тем, что направление течения металла совпадает с направлением перемещения пресс-штемпеля пресса. При обратном прессовании истечение металла происходит в направлении, противоположном движению пресс-штемпеля. Часто при прессовании алюминиевых профилей используется многоканальное прессование.
При реализации процесса прессования (рисунок 4.1) на прутково-профильном прессе с подвижным контейнером заготовку 3 с пресс-шайбой 2 подают на ось контейнера 4 и движением вперед пресс-штемпеля 1 заготовку вводят в контейнер с передней стороны. Выходная сторона контейнера замкнута матрицедержателем 6 с матрицей 5 (рисунок 4.1, а, позиция I). После ввода слитка в контейнер до упора осуществляют его распрессовку, непосредственным продолжением которой является прессование (выдавливание) изделия 7 (рисунок 4.1, а, позиция II). По окончании выдавливания контейнер отводят назад. При этом пресс-остаток 9 с пресс-шайбой 2 остаются висеть у матрицы 5. Движением ножа 8 вниз изделие отделяют от пресс-пакета (т.е. от пресс-остатка с пресс-шайбой), который падает на желоб и передается к механизму разделки пакета (рисунок 4.1, а, позиция III). Изделия тянущим устройством выдергивают из матрицы, и контейнер возвращают в исходное состояние.
Рисунок 4.1 – Последовательность процесса прессования
При прямом прессовании труб после загрузки слитка 3 и пресс-шайбы 2 в контейнер 4 (рисунок 4.1, б, позиция I) осуществляют его распрессовку. При этом иглу 10, находящуюся внутри полого пресс-штемпеля 1, немного выдвигают вперед и запирают отверстие пресс-шайбы 2 (рисунок 4.1, б, позиция II). После распрессовки снимают давление с пресс-штемпеля и прошивают слиток (позиция III). Затем подают рабочее давление к пресс-штемпелю и слиток выдавливают в кольцевой зазор между иглой 10 и матрицей 5 (рисунок 4.1, б, позиция IV). Пресс-пакет отрезается ножницами 11 (рисунок 4.1, б, позиция V).
В качестве основной характеристики технологического процесса прессования выделяют также, как и при прокатке, вытяжку λ = F0/F1, характеризующую в данном случае отношение площади распрессованной заготовки к площади поперечного сечения прессуемого профиля.
Сравним прессование с процессами прокатки сорта и труб. Преимуществами прессования являются следующие. Пластичность металла при прессовании выше, так как металл в контейнере находится в условиях всестороннего сжатия. Это играет большую роль при производстве изделий из труднодеформируемых сплавов и необходимости получения большой вытяжки (до 50–100, а для алюминия и латуни до 1000). При прокатке за проход вытяжка составляет обычно менее 2. Перестроить пресс на изделие нового профиля гораздо легче, быстрее и дешевле, чем прокатный стан. Точность размеров при прессовании, как правило, выше. Прессование проще автоматизировать, чем сортовую прокатку.
В качестве недостатков можно отметить следующие. Технологические отходы при прессовании состоят из малодеформированного переднего конца профиля и пресс-остатка, достигая 10–15 % (при прокатке 1–3 %). Из-за неравномерного истечения центральных и наружных слоев прессуемой заготовки неравномерность структуры и свойств металла этих слоев выше, чем у проката. Из-за больших контактных напряжений и значительной скорости скольжения по инструменту пресса стойкость прессового инструмента значительно ниже стойкости валков сортовых станов и его приходится изготовлять из дорогостоящих сталей и сплавов. Производительность пресса существенно ниже производительности стана, а себестоимость пресс-изделий выше себестоимости проката.
Полунепрерывное прессование в настоящее время является одной из основных схем по производству пресс-изделий из алюминиевых сплавов, характерной чертой которого является использование специального форкамерного инструмента, обеспечивающего прессование со стыковой сваркой и натяжением. Характерным для такого процесса является снижение высокой степени деформации за счет ее дробления при последовательном выдавливании объема металла сначала из основного контейнера в промежуточный инструментальный блок, а затем из промежуточного блока в матрицу (рисунок 4.2). При реализации процесса прямого прессования на гидравлических прессах в большинстве случаев роль промежуточного инструментального блока выполняет специальный инструмент, называемый форкамерой.
Рисунок 4.2 – Схема очага деформации при полунепрерывном прессовании
с использованием форкамеры
Основным преимуществом такого процесса является предварительное перераспределение потоков металла заготовки таким образом, чтобы уже перед входом металла в канал матрицы неравномерность деформации была уменьшена. Кроме того, значительно снижаются нагрузки на прессовый инструмент, что приводит к повышению точности размеров прессуемого профиля. В зависимости от размеров и типа профиля конструкция форкамер может быть различной: в виде углублений в теле матрицы со стороны зеркала или отъемной шайбы, в которой изготовлены соответствующие емкости для прессуемого металла. Расширяющаяся форкамера позволяет прессовать профили, габаритный размер которых превышает размеры внутренней втулки контейнера. После окончания прессования через матрицу с форкамерами и отделения пресс-остатка последующая заготовка выталкивает оставшийся металл. Это требует несколько большего усилия, так как дополнительно приходится срезать сечение металла, остающегося в форкамерах. Кроме указанных преимуществ данного способа следует отметить возможность осуществления схемы полунепрерывного прессования с натяжением, при котором происходит стыковая сварка профилей.
В настоящее время большинство передовых заводов используют эту технологию при производстве алюминиевых профилей из мягких деформируемых сплавов. Однако вопросы исследования прочности сварного шва, его протяженности требуют научно-обоснованных методик проектирования и современных технологий изготовления прессового инструмента. Поэтому данный технологический процесс не позволяет получать длинномерные изделия, так как сварной шов в большинстве случаев приходится вырезать, что к тому же снижает выход годного при прессовании.
В качестве основного оборудования для реализации таких технологий применяются горизонтальные прессы номинальным усилием от 5 до 50 МН с размерами контейнеров, определяемыми сортаментом, длиной и маркой сплава пресс-изделий, коэффициентом вытяжки, способом прессования и др. Основными параметрами этих прессов являются номинальное усилие, размеры контейнера, ход и скорость движения прессующей траверсы. Тенденцией развития гидропрессового оборудования является применение автоматизированных линий, оснащенных тянущими устройствами, новыми системами передачи продукции и ее адьюстажной обработки.
Существующие способы прессования на гидравлических прессах позволяют получать как сплошные, так и полые изделия различного типоразмера, однако после каждого цикла прессования остаются отходы металла в виде пресс-остатка, а последующая закладка заготовки в контейнер сказывается на снижении производительности процесса. Получившие в последнее время развитие технологии и оборудование непрерывного прессования позволяют решать указанные проблемы путем концентрации деформации в необходимой степени в одном узле – узле непрерывного деформирования. При этом, наряду с основным видом обработки – прессованием, в очаге деформации в зависимости от вида непрерывного прессования могут совмещаться такие операции, как прокатка, волочение, осадка, раздача и др.
Основными способами непрерывного прессования являются Конформ, Лайнекс и Экстроллинг.
Среди перечисленных способов особое место занимает способ Конформ, предложенный Д. Грином. Он имеет ряд технических и экономических преимуществ и широкую сферу применения, причем особенно перспективным он представляется в цветной металлургии.
Способ Конформ основан на применении неподвижного инструмента, называемого башмаком и подвижного вращающегося инструмента типа колеса с канавкой по периферии, причем в торце башмака установлена матрица, которая перекрывает канавку колеса. Схема процесса приведена на рисунок 4.3.
|
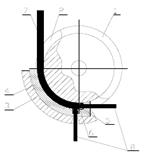
В качестве заготовки используется пруток 7, который задается в ручей 2, выполненный на рабочем колесе 1 в виде кольцевой канавки. Ручей 2 с внешней стороны закрыт прижимным башмаком 3, на внутренней поверхности которого выполнен ручей 4, охватывающий заготовку 7. В башмаке 3 закреплен блок инструмента с прессовой матрицей 5. При задаче прутковой заготовки в зазор между башмаком и колесом она продвигается в камеру прессования, образуемую поверхностями башмака и канавки, под действием сил трения по поверхности контакта с вращающимся колесом и, наконец, достигает матрицы.
В зоне непосредственно перед матрицей заготовка подвергается интенсивному пластическому деформированию («раздавливанию») и заполняет все сечение канавки (зона захвата при выдавливании); это способствует увеличению сил трения между поверхностью канавки и заготовкой. По мере поворота колеса силы сжатия, приложенные к заготовке, возрастают и достигают значений, необходимых для выдавливания материала заготовки через отверстие в матрице, т.е. начинается процесс прессования. Зона неполного контакта заготовки с поверхностью канавки (зона первичного захвата) служит для развития давления, необходимого для пластического деформирования материала и заполнения объема в зоне перед матрицей. В качестве заготовки можно использовать обычную проволоку, причем процесс ее деформирования – втягивание в камеру прессования по мере поворота колеса, предварительное профилирование и заполнение канавки в колесе, создание рабочего усилия и, наконец, прессование – идет непрерывно, т. е. реализуется технология непрерывного выдавливания. Данный способ позволяет выдавливать пресс-изделия не только в направлении вращения рабочего колеса, но и в направлениях, перпендикулярных оси рабочего колеса, в том числе и радиальном.
С целью оптимизации кинематики течения деформируемого металла, снижения усилия прессования и упрощения конструкции прессового инструмента для изготовления труб и полых профилей может применяться двухручьевая схема, а для изготовления тонкостенных труб, профилей, проволоки и плакированных изделий особенно действенна двухколесная схема реализации процесса Конформ. Прессовый инструмент отличается тем, что прессовая матрица и игла устанавливаются раздельно, снижается величина потребных давлений и температуры прессования, что способствует росту производительности процесса.
На основе вышеприведенных технических решений специалистами Springfilds laboratory и Advanced Metal Forming Group при Управлении атомной энергии «UKAEA» Великобритании была разработана линия непрерывного прессования, схема которой представлена на рисунке 4.4.
Преимуществами линии являются следующие: высокое качество пресс-изделий, сравнительно низкая себестоимость производства; низкие удельные капитальные затраты; незначительное количество технологических отходов (3–7 % вместо 25–45 % традиционных); большая технологическая гибкость. В настоящее время установки по методу Конформ, предназначенные для производства прессованной продукции, производятся английскими фирмами «Holton Machinery» и «Babcock Wire Equipment».
Мощность привода установки фирмы «Holton Machinery» с диаметром колеса 400 мм составляет 150 КВт, а габаритные размеры – 27250х6800х4380 мм. На этих установках изготавливают секторные провода для кабеля с поперечным сечением 16-300 мм2, электрошины различной формы и размеров, трубы всех типов охлаждающих систем диаметром от 4 до 8 мм с толщиной стенки до 0,6 мм и др. Однако отсутствие исследований формоизменения металла, учета граничных сил трения, изучение закономерностей деформации различных металлов и сплавов выявили ряд недостатков, которые существенно ограничивают возможности этого метода прессования.
1 – размоточное устройство; 2 – заготовка; 3 – устройство правки заготовки; 4 – устройство очистки заготовки; 5 – гильотинные ножницы; 6 – машина «Conform»; 7 – устройство охлаждения и сушки пресс-изделия; 8 – устройство натяжения пресс-изделия; 9 – устройство контроля натяжения пресс-изделия при его смотке; 10 – пресс-изделие; 11 – намоточное устройство
Рисунок 4.4 – Схема компоновки оборудования линии непрерывного прессования по способу Конформ
Следует отметить, что для деформации даже мягких алюминиевых сплавов требуются большие энергозатраты, так как трение по инструментальному узлу достаточно велико. Кроме того, это приводит еще и к сильному разогреву деформирующего инструмента и, как следствие, к снижению его стойкости. Свойства пресс-изделий характеризуются неоднородностью из-за неравномерной деформации за счет создания реактивных сил трения на контакте металл – прессовый узел (башмак), что не вполне приемлемо, например, для продукции электротехнического назначения.
Особенностью способа Лайнекс (рисунок 4.5), предложенного специалистами фирмы Western Electrik Co (США), является то, что, давление, необходимое для реализации процесса, создается за счет использования активных сил трения, которые возникают между плоскими поверхностями звеньев бесконечных цепей и верхней, и нижней плоскостями заготовки, имеющей прямоугольное поперечное сечение.
|
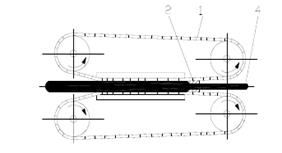
При этом величина давления прессования оказывается зависимой от соотношения (разности) сил трения на несмазанных и смазанных плоскостях заготовки. Этот способ применяют для производства алюминиевых шин и проволоки на заводах фирмы Venscuck (США). Максимальная величина коэффициента вытяжки не превышает 20, т.е. на порядок меньше, чем при производстве аналогичного пресс-изделия способом Конформ.
Процесс Экстроллинг был предложен в 1975 г, запатентован Б. Авитцуром в 1976 г и представляет собой способ совмещения процессов прокатки и прессования в одном очаге деформации. Он характеризуется тем, что за счет активных сил контактного трения между валками и заготовкой выдавливание осуществляют через прессовую матрицу. Схема процесса показана на рисунке 4.6.
Рисунок 4.6 – Схема устройства для процесса Экстроллинг
Для осуществления процесса исходная заготовка непрерывно задается в калибр, обжимается в нем, что полностью соответствует стадии прокатки и выдавливается в калибрующее отверстие матрицы, установленной на выходе из калибра.
Данный способ реализуется как в холодном состоянии, так и при повышенных температурах и имеет меньшие потери мощности на трение реактивного действия, а также более эффективное заполнение полости калибра металлом заготовки. Рассматриваемый процесс сочетает в себе низкие потери на трение и малую продолжительность обработки, характерные для прокатки, и большие степени деформации, возможные при прессовании. Недостатки прокатки (небольшое единичное обжатие) и прессования (ограниченная длина получаемого изделия) при такой реализации процесса могут быть устранены.
Однако способ не нашел должного применения в промышленности, так как предложенное техническое решение (использование открытого калибра, расположение матрицы на общей вертикальной оси валков и т. д.) не обеспечивало устойчивого протекания процесса и создания необходимых для экструдирования металла давлений.
Таким образом, из всех процессов непрерывного прессования цветных металлов и сплавов, которые начали активно внедряться в производство с 1974 г, наиболее применимым и доведенным до промышленного внедрения оказался способ Конформ, установки на базе которого изготавливаются и распространяются по всему миру фирмами Babcock Wire Equipment и Holton Machineri LTD. В странах СНГ, несмотря на имеющиеся многочисленные технические решения, защищенные авторскими свидетельствами и патентами, попытки создания таких установок не удались вследствие отсутствия автоматизированной системы отвода тепла от рабочего инструмента. Действительно, ряд особенностей этого метода, основной причиной которых является наличие контактных сил трения реактивного действия, приводит к сильному разогреву инструмента, контролировать и управлять которым в процессе деформации достаточно сложно.
Литература 1 осн. [9-15], 6 осн. [57-98], 7 доп [8-251], 9 доп [3-341].
Контрольные вопросы
1. Какой вид прессования является в настоящее время самым распространенным?
2. Какой основной сортамент прессовой продукции?
3. В чем отличие прямого метода прессования от обратного?
4. Как рассчитываются коэффициент вытяжки при прессовании?