Производство труб на пилигримовом стане. В отличие от агрегатов с автоматическим и непрерывным станами на агрегат с пилигримовым станом, являющимся станом периодической прокатки, трубы производят не из катаной заготовки, а непосредственно из горячего слитка. Это является основным преимуществом пилигримового способа прокатки.
В зависимости от размеров прокатываемых труб пилигримовые агрегаты (пильгерстаны) делят на три группы: малые агрегаты для труб диаметром 22…120 мм, средние агрегаты для труб диаметром 102…325 мм и большие агрегаты для труб диаметром 178…665 мм. Трубы изготавливают с толщиной стенки от 5 до 60 мм, длиной 24…36 м. Производительность больших агрегатов достигает 300000 т/год.
Пилигримовой cтан состоит из двухвалковой рабочей клети, желоба для гильз, подающего аппарата, стержня оправки. Периодическое обжатие гильзы осуществляют валками, калибр которых имеет переменный радиус и вращаются валки в сторону, противоположную движению прокатанной трубы.
Толстостенную гильзу, полученную на прошивном стане, раскатывают на цилиндрической оправке, называемой дорном. Сечение калибра валков изменяется от максимального, называемого зевом, до минимального, соответствующего профилю готовой трубы. За каждый оборот валков обжимают небольшой участок длины трубы, после чего происходит подача трубы с помощью подающего аппарата с одновременным поворотом ее на 90°.
Профиль пилигримового валка (рисунок 13.1) состоит из переднего конуса, или гребня (примерно 1/6 часть окружности валка), с переменным радиусом калибра для основной деформации гильзы по диаметру и толщине стенки; калибрующего участка (примерно 1/4…1/3 часть окружности валка) с постоянным радиусом, производящего раскатку смещенного гребнем металла и формирование трубы по диаметру и толщине стенки; участка продольного выпуска для плавного отвода поверхности валка от поверхности трубы (составляет 10…20° окружности), холостого участка – плавного сопряжения кривых участков выпуска и гребня, обеспечивающего свободное прохождение гильзы при очередной подаче ее вперед.
Рисунок 13.1 – Валок пилигримового стана
Прокатка на пилигримовом стане состоит из трех периодов: первого, когда валки начальной точкой рабочего участка начинают обжимать гильзу и выталкивают ее в направлении, противоположном прокатке; второго, когда валки калибрующей частью раскатывают гильзу, уменьшая ее диаметр и толщину стенки; третьего, когда валки выходят из соприкосновения с трубой и ее вместе с дорном подающим аппаратом поворачивают на 90° и подают вперед. При каждом повороте валка труба получает движение на небольшое расстояние назад, а затем на большее расстояние вперед (поэтому процесс назван пилигримовым).
Агрегаты с пилигримовым станом могут иметь в своем составе две – четыре пилигримовых клети. Так как скорость периодической прокатки относительно невысока, то при одном прошивном стане обычно устанавливают две пилигримовые клети. На рисунке 13.2 представлена схема расположения оборудования агрегата с двумя пилигримовыми клетями.
1 – кантовательная машина; 2 – методические печи; 3 – прошивные станы;
4 – гильзовая тележка; 5 – подающий аппрат; 6 – полигримовые клети; 7 – шестеренные клети; 8 – маховик; 9 – двигатель; 10 – пила горячей резки труб; 11 – охладительный стол; 12 – подогревательная печь; 13 – калибровочный стан; 14 – правильная машина
Рисунок 13.2 – Схема расположения оборудования агрегата с пилигримовым станом
Две нагревательные методические печи установлены на оси, перпендикулярной к оси прокатных станов. С помощью кантовальных машин слитки перемещают в печи к окнам выдачи и по рольгангу передают к прошивному стану донным концом вперед. Прошивной стан, аналогичный по конструкции применяемым на агрегатах с автоматическим станом, прокатывает гильзы длиной до 4,5 м. Радиальная гильзовая тележка поочередно транспортирует гильзы от прошивного стана к пилигримовым станам. Температура гильзы перед прокаткой в трубу равна 1150…1180 °С.
На приемном столе пилигримового стана гильзу с помощью гидравлического устройства устанавливают по оси прокатки и вводят цилиндрический дорн, предварительно смазанный мазутно-графитовой смесью. Дорн вместе с гильзой подающим аппаратом задают в валки стана. Как только конец гильзы достигает валков, происходит захват и начинается обжатие гильзы между валками и дорном. Прокатку заканчивают, когда длина участка гильзы между валками и упором толкателя будет 300…400 мм. Из трубы извлекают дорн, поднимают верхний валок и подают ее на резку. Дисковой пилой или плазменной горелкой отрезают передний конец и после этого режут на мерные длины (6…12 м), отрезают недокатанный конец гильзы (пилигримовую головку).
Трубы, подвергающиеся последующему калиброванию, поступают в подогревательную печь и далее на калибровочный стан. Трубы, не требующие калибрования, передают на правильную машину и на отделку.
Рабочая клеть пилигримового стана (рисунок 13.3) имеет две станины, установленные на мощном фундаменте и скрепленные вверху хомутами. В окнах станин установлены подушки с подшипниками верхнего и нижнего валка. Подушки нижнего валка закреплены неподвижно, а верхнего валка перемещаются в вертикальном направлении с помощью нажимного винта. Верхний валок с подшипниками и подушками уравновешивают гидравлическим цилиндром и пружиной.
|
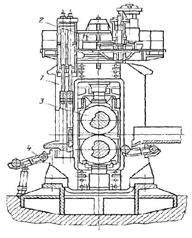
Наибольший объем труб производят на средних пилигримовых станах, предназначенных для диаметров 168…325 мм. Толщина стенки труб от 8 до 15 мм, длина до 36 м. Можно прокатывать трубы и с толщиной стенки до 40 мм.
Для уменьшения разностенности труб и расхода металла в новых цехах пилигримовой прокатки в качестве заготовки используют обработанные многогранные слитки с волнистой поверхностью. У нагретых слитков на специальных установках ломают окалину и сбивают ее водой высокого давления или вибрационными машинами. Слитки калибруют на вертикальном прессе и затем на прошивном прессе прошивают со стороны донной части. Этим достигают закрытия усадочной раковины. С прошивного пресса стаканы подают в печь для подогрева.
Стакан, нагретый до 1200 °С, задают на стан-удлинитель (элонгатор). Рабочие валки удлинителя расположены наклонно к оси прокатки, поэтому стакан, вращаясь и продвигаясь по оси стана, деформируется между валками и короткой оправкой, одновременно происходит прошивка донышка стакана. Прокаткой на стане-удлинителе достигают уменьшение поперечной разностенности гильзы, поступающей на пилигримовый стан.
Применение прошивных прессов и элонгаторов, вместо прошивных станов, улучшило качество гильзы-заготовки для пилигримовой прокатки, в результате повысилось качество поверхности готовых труб, уменьшилась их разностенность. Пилигримовые агрегаты используют в основном для прокатки легированных сталей, так как качество труб возросло настолько, что стала экономичной прокатка труб из легированных сталей. Производительность пилигримового стана и качество прокатываемых труб во многом зависят от работы подающего аппарата.
Прошитую гильзу прокатывают на пилигримовом стане с недокатом длиной не более 300..350 мм (рисунок 13.4, пол. I). Прекращают подачу охлаждающей воды на верхний валок, который поднимают. Извлекают из трубы дорн и заменяют новым, при этом пильгерголовка прокатываемой трубы во избежание выброса трубы из клети не должна касаться валков (рисунок 13.4, пол. II). На приемный стол пильгерстана подают следующую гильзу (рисунок 13.4, пол. III). Вводят дорн в поданную гильзу и прокатанную трубу до стыковки переднего конца гильзы с недокатом первой трубы (рисунок 13.4, пол. IV). Опускают и устанавливают по метке верхний валок, открывают охлаждающую воду и ведут прокатку с перекрытием операции – раскаткой пильгерголовки первой трубы и затравкой второй гильзы. После прокатки пильгерголовки первая труба свободно сходит с дорна и ее отводят по рольгангу.
Управление работой агрегата автоматическое. Имеется возможность ручного управления. Величина отреза со стороны затравочного конца 200…500 мм. Длина пильгерной головки 400…450 мм.
При выходе из пильгерстана трубу по сигналу фотоэлемента останавливают на выходном рольганге стана и передают на рольганг агрегата огневой резки. Резаки и тормозные колодки опускают на трубу. В таком положении начинают подогрев места начала резки. Время подогрева 2…15 с. После подогрева электромагнитные клапаны с замедлением 2,5 с открывают режущий кислород на работающих резаках, одновременно начинают вращение трубы. По окончании реза пильгерголовка падает в специальный проем, фотоэлемент подает сигнал в электрическую цепь агрегата, по которому закрывается режущий газ и резаки с тормозными колодками поднимают в исходное положение. Разрезанные трубы транспортным рольгангом подают к упору и выбрасывают на промежуточный стеллаж. Передвижение тележек, опускание и подъем резаков осуществляют с пульта управления.
Агрегат огневой резки состоит из трассы, по которой движется пять тележек с газовыми резаками, работающими на природном газе, и рольганга, вращающего трубу во время резки (резаки укреплены на тележках неподвижно).
|
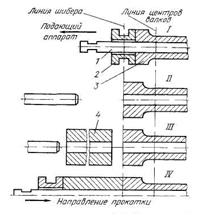
Трехвалковый раскатной стан. Рассмотренные выше агрегаты для производства горячекатаных труб не обеспечивают допуска по диаметру ±5 %. Для изготовления труб повышенной точности применяют агрегаты с трехвалковым раскатным станом. На этих агрегатах изготавливают бесшовные толстостенные трубы диаметром от 34 до 200 мм с толщиной стенки 10…50 мм.
Трехвалковые раскатные станы прокатывают гильзу в трубу, т. е. выполняют функции автоматических или непрерывных станов. В отличие от этих станов в трехвалковом стане допускается большая степень обжатия гильзы по толщине стенки, при этом достигают меньшей разностенности трубы. Наиболее эффективно использование агрегатов с трехвалковым раскатным станом для прокатки труб с отношением диаметра к толщине стенки в пределах 10…12. Одним из важных достоинств трехвалковых раскатных станов является быстрая перестройка при переходе на прокатку труб другого сортамента.
На этих агрегатах прокатывают трубы из углеродистых, низколегированных и высоколегированных сталей. Последовательность технологических операций на агрегате с трехвалковым раскатным станом видна на рисунке 13.5.
1 – загрузочная машина; 2 – кольцевая печь; 3 – выгрузочная машина; 4 – пневматический зацентровщик; 5 – прошивной стан; 6 – трехвалковый раскатной стан; 7 – калибровочный стан; 8 – пила
Рисунок 13.5 – Схема агрегата с трехвалковым раскатным станом
Круглую катаную заготовку мерной длины подают загрузочной машиной в кольцевую печь. Нагретую до температуры 1150…1200 °С заготовку выгрузочной машиной подают на наклонный стеллаж и затем на рольганг, по которому она поступает к пневматическому зацентровщику ударного типа, после чего сбрасывают в приемный желоб прошивного стана. Прошивные станы подобны используемым на агрегатах с автоматическим станом. При прошивке коэффициент вытяжки достигает величины 1,3…2.
После прошивки гильзу по наклонной решетке перекатывают в приемный желоб трехвалкового раскатного стана. Одновременно с гильзой в желоб этого стана сбрасывают и задают в гильзу длинную оправку. Тележкой-толкателем гильзу с оправкой задают в раскатной стан. Валки стана расположены под углом 120° по отношению друг к другу.
Положение каждого валка относительно оси прокатки определяет наружный диаметр готовой трубы. Перемещение валков относительно оси прокатки регулируют тремя индивидуальными электродвигателями. Синхронная работа двигателя обеспечивает строго одинаковое расстояние оси каждого валка от оси гильзы. Валки вращают в одну сторону. Угол наклона оси верхнего валка к вертикальной плоскости, проходящей вдоль оси прокатки, называют углом подачи α, а угол наклона оси валка к горизонтальной плоскости – углом раскатки β.
Схема очага деформации металла на трехвалковом раскатном стане представлена на рисунке 13.6.
Валки раскатного стана имеют четыре участка: I – конус захвата, где происходит захват гильзы и подача ее в зону деформации, II – гребень, участок, где происходит наибольшее обжатие гильзы, III – раскатной и IV – калибрующий конусы. Благодаря такому профилю валков уменьшается диаметр гильзы и утоняется ее стенка. Коэффициент вытяжки на раскатном стане достигает величины 3,5.
Прокатанные на трехвалковом стане трубы подают на цепной или реечный оправкоизвлекатель.
После извлечения оправки труба по рольгангам поступает в подогревательную печь. Освобожденную оправку перемещают для охлаждения и смазки в автоматическую линию циркуляции оправок. Подогретую трубу калибруют на трехвалковом калибровочном стане. При калибровании происходит дальнейшее уменьшение диаметра трубы (на 1…3 мм). Это обеспечивает получение труб с высоким допуском.
|
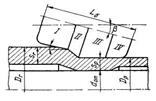
В линии современных агрегатов с трехвалковым раскатным станом имеются редукционные станы, которые позволяют расширить сортамент труб, получаемых с раскатного стана. Такие агрегаты полностью автоматизированы. Пневматические исполнительные механизмы почти полностью заменены электрическими. Агрегаты с трехвалковым раскатным станом различают по способу использования оправок при прокатке. Толстостенные трубы (с отношением диаметра к толщине стенки 7,5…12,0) прокатывают на свободно перемещающейся оправке, которую извлекают после окончания прокатки. Трубы с отношением диаметра к толщине стенки, равным 4,5…7,5, прокатывают на вытягиваемой оправке, извлечение которой начинают с началом прокатки и заканчивают в конце ее. При прокатке с полуперемещающейся оправкой, когда гильза и оправка движутся в одном направлении, но с разными скоростями, оправку, как и во втором случае, извлекают в конце прокатки. Наиболее производительным является процесс со свободно перемещающейся оправкой, поэтому он получил большое применение в промышленности.
Трехвалковый раскатной стан состоит из рабочей клети, главного привода, вталкивателя гильзы с оправкой в стан и оправко-извлекателя.
Конструкция клетей трехвалковых раскатных станов принципиально отличается от конструкции ранее рассмотренных трубопрокатных станов. Валки раскатного стана монтируют в поворотной кассете или планшайбе, что позволяет изменять угол подачи. Кассета поворачивается в траверсе, устанавливаемой в направляющих станины рабочей клети. Угол подачи можно изменять. Рабочая клеть имеет нажимные устройства, действующие на каждый валок. В первых конструкциях трехвалковых раскатных станов угол подачи не регулировался. Его можно было изменить при замене подушек с измененными расточками для рабочих валков.
На этих агрегатах прокатывают котельные и подшипниковые трубы, которые являются заготовкой для производства колец подшипников.
Для изготовления котельных труб применяют кованые, ободранные, сверленые заготовки из сталей 20, 12Х1МФ, 15Х1М1Ф. Температура металла перед выдачей из печи должна быть 1180…1220 °С.
Настройку станов производят на трех – пяти контрольных заготовках из углеродистой стали того же диаметра, что и заготовки для котельных и шарикоподшипниковых труб.
Исходными заготовками для подшипниковых труб служат штанги, которые перед ломкой на гидропрессе на заготовки определенной длины размечают и подрезают в размеченных местах автогеном на глубину 15…20 мм.
После выдачи из печи заготовку подают к пневматическому центрователю, который настраивают так, чтобы ось бойка совпала с осью заготовки.
Задачу гильзы с оправкой в валки стана проводят толкателем. Свободный задний конец оправки при задаче гильзы должен быть минимальным. Массовую прокатку труб начинают после проверки настройки стана на первых трех трубах. В процессе работы периодически проверяют правильность настройки стана.
После раскатки гильзы трубу с оправкой передают на оправкоизвлекатель. Для облегчения извлечения оправки в гильзу перед вводом оправки засыпают поваренную соль. В люнет оправкоизвлекателя вставляют вкладыш, диаметр которого должен быть на 4…8 мм больше диаметра оправки.
После трехвалкового раскатного стана трубы подвергают подогреву и передают на калибровочный стан, на котором им придают окончательный размер по диаметру.
Все трубы после калибровочного стана передают на охладительный стол. Трубы из стали ШХ15 охлаждают под вентилятором, а с толщиной стенки 30 мм и котельные трубы охлаждают на спреерной установке. Для предотвращения коробления и значительного изгиба труб подача воды в спреерной установке должна быть равномерной на всю поверхность. Поэтому давление воды в системе спреера должно быть постоянным и не ниже 10 Па. По выходе из спреерной установки трубы должны иметь температуру 650…750 °С.
Литература 1 осн. [136-262], 4 доп [168-226].
Контрольные вопросы
1. Пилигримовоый стан состоит из чего?
2. Профиль пилигримового валка состоит из чего?
3. Какие основные оборудования включает трубопрокатный агрегат с раскатным станом?
4. Заготовками для агрегатов с раскатным станом что является?
5. Рабочая клеть раскатного стана иметь какие валки?
Лекция 14. Совмещенные процессы производства металлоизделий. Общие сведения о совмещенных процессах обработки металлов и сплавов. Перспективы развития. Классификация совмещенных процессов. Комбинирование операций обработки металлов давлением. Способы и устройства для совмещенной прокатки и прессования цветных металлов и сплавов
В области производства изделий из цветных металлов и сплавов можно выделить простые и сложные (интегральные) процессы обработки. Под простыми процессами понимают такие, которые включают один цикл обработки металла в одном очаге деформации (литья) без смены направления течения металла или приложения нагрузки. Интегральные процессы включают несколько воздействий (операций) в одном очаге деформации либо комбинацию их со сменой направления перемещения металла. Для классификации многообразия операций обработки цветных металлов и сплавов следует рассмотреть, каким образом при взаимодействии простых процессов образуется новый интегральный процесс, обладающий уже новым комплексом свойств и, как правило, исключающий недостатки совмещаемых (комбинируемых).
Базовым процессом назовем такой, при котором во время приложения нагрузки внешнее распределение силы и ее направление на поверхности очага пластической деформации (кристаллизации) не изменяется. Основными базовыми процессами для обработки металлов являются литье, прокатка, прессование, волочение, осадка, кручение, а также компактирование и термообработка.
Тогда комбинированным процессом обработки будем считать комбинацию двух и более базовых процессов, при котором происходит интегральное наложение нагрузок в одном очаге деформации, иногда и со сменой направления течения металла. Типовым примером такого комбинированного процесса можно считать, например, прокатку-волочение, когда прокатка ведется с натяжением конца полосы. При этом в зависимости от величины натяжения прокатка-волочение (рисунок 14.1, а) может в предельном случае превращаться в волочение-прокатку (рисунок 14.1, б), когда удельный вес процесса вытягивания превалирует над процессом обжатия в валках.
Совмещенный процесс является более сложным и характеризуется разделением базовых процессов во времени или пространстве. Такими типовыми процессами считаются литье и прокатка (рисунок 14.1, в), когда заготовку получают с помощью кристаллизатора, а затем прокатывают на непрерывном стане, или литье и прессование, когда ее подвергают непрерывному экструдированию. Возможна также схема бесслитковой обработки металла. В данном случае процессы обработки металла выстраиваются последовательно и только после окончания одного из них начинается следующий. В качестве таких процессов выделяют, например, совмещенный процесс литья, прокатки, фрезеровки и отжига ленты и считают, что именно с применением таких процессов можно добиться радикального повышения экономичности производства и качества продукции.
Рисунок 14.1 – Схемы комбинированных (а, б), совмещенных (в, г) и совмещено-комбинированных (д) процессов обработки металлов
В последние годы имеется тенденция в создании совмещенно-комбинированных процессов, когда на каждом последовательном этапе обработки может применяться комбинированный процесс. Примером реализации такого процесса может быть процесс, когда на одной установке осуществляются одновременно операции литья-кристаллизации, прокатки-прессования, охлаждения и смотки готовых пресс-изделий в бухту с калибровкой готового изделия на заданный диаметр (рисунок 14.1, д).
Таким образом, с использованием предлагаемого представления можно достаточно просто и точно классифицировать интегральные процессы по обработке цветных металлов и сплавов, которые в настоящее время все более усложняются, становясь многофункциональными и непрерывными. При этом на привычные сочетания операций обработки металлов могут накладываться особые виды обработки, например, такие как магнито-импульсная, вибрационная, термо-механическая и др.
Схема классификации таких процессов обработки цветных металлов и сплавов показана на рисунке 14.2. Она позволяет учитывать особенности реализации конкретных технологических схем. Следует отметить, что в данной схеме приведены лишь некоторые виды обработки, которые в настоящее время находят практическое применение и являются, на наш взгляд, наиболее перспективными. При этом она может быть дополнена и усовершенствована при появлении новых разновидностей таких процессов.
Таким образом, одной из основных тенденций развития процессов обработки цветных металлов и сплавов является совмещение операций литья и обработки металлов давлением, а также комбинирование в одном очаге деформации нескольких схем нагружения металла.
Наибольший интерес представляют конструкции устройств на базе процессов совмещения прокатки и прессования, характеризующиеся небольшими энергозатратами, простотой конструкции деформирующего узла и разнообразием сортамента получаемой продукции. Предложенные новые технические решения позволяют сделать процесс прокатки-прессования более устойчивым и сохранить все его вышеуказанные преимущества.
Рисунок 14.2 – Классификация интегральных процессов обработки металлов
Предложенные конструкции по сортаменту производимой продукции и назначению можно разделить на три основные группы: устройства для производства профилей и проволоки; устройства для получения труб; универсальные устройства, позволяющие изготавливать профили, трубы, прутки и проволоку.
Устройства, показанные на рисунке 14.3, а, относятся к первой группе и позволяют получать пресс-изделия преимущественно из алюминиевых и медных сплавов. Основным техническим решением, характерным для первого устройства, является значительное увеличение активных сил трения за счет применения закрытого балочного калибра с глубоким врезом закрытого ручья в валок. Это значительно повышает устойчивость процесса, однако сложная форма калибра требует точного изготовления матрицы и контролируемого усилия прижима последней к валкам.
С целью усовершенствования данного устройства предложена схема, показанная на рисунке 14.3, б, с применением ящичного калибра прямоугольного сечения с заданным отношением диаметров по гребню и выступу валков фиксированной величиной удаления матрицы от общей вертикальной оси валков и возможностью установки матрицы под определенным углом к этой оси.
а – из порошковых материалов; б – из литой заготовки
Рисунок 14.3 – Устройства для получения профилей и проволоки из цветных металлов и сплавов
Для получения труб с помощью совмещенной прокатки-прессования разработаны две основные схемы, показанные на рисунке 14.4. По первому варианту устройство для получения сварных труб (рисунок 14.4, а) преимущественно из алюминиевых сплавов включает два валка, образующих закрытый калибр с отношением диаметров по дну ручья и гребню выступа в диапазоне 0,6 – 1,0 и перекрытых на выходе из калибра матрицей, установленной на определенном расстоянии от плоскости, проходящей через оси валков.
Для получения пресс-изделий со сваркой применяют комбинированную матрицу. С целью повышения качества изделий на донной поверхности ручья и наружной поверхности гребня валков выполнены кольцевые канавки с параллельными стенками, причем эти поверхности выполнены с образующими, наклоненными к осям вращения соответствующих валков по острым углам, встречно обращенным для каждого из валков своими вершинами.
На матрице перед питающими каналами выполнены выступы, размещенные в образованном наружными и боковыми поверхностями выступающего гребня и ручья упомянутых валков пространстве, при этом наружные поверхности выступающего гребня валка и дна ручья в зоне их сопряжения с боковыми поверхностями выступающего гребня и ручья расположены с возможностью контакта.
В процессе работы устройства заготовка поступает в кольцевые канавки валков, а затем подается в очаг деформации, рассекается на два потока и перед упорами затекает через питающие каналы в камеру сварки. В последней потоки металла свариваются и деформируются, выдавливаясь через матрицу с иглой в виде трубы.
Рисунок 14.4 – Устройства для получения сварных труб (а) и длинномерных полых изделий (б)
Конструкция устройства по второму варианту, предназначенного для получения длинномерных изделий из алюминия (рисунок 14.4, б), содержит два валка с каналами, матрицу, иглу, запирающий и упорный блоки. Матрица может быть выполнена в виде приводного валкового узла, а игла – телескопической, что позволяет получать трубы с изменяющейся толщиной стенки. Основным отличием от первого варианта является то, что прокатку ведут с использованием двух заготовок, задаваемых в калибр одновременно, а игла и матрица конструктивно разделены на отдельные узлы. Это дает возможность более гибкого построения технологического процесса и увеличения стойкости инструмента. В процессе работы две заготовка прямоугольного сечения одновременно задаются в калибр валков, где происходит их обжатие, продвижение до упоров, распрессовка с полным заполнением каналов и последующее поступление в камеру сварки. По мере поступления металла создается давление, необходимое для экструдирования изделия.
Устройство, относящееся к третьей группе (рисунок 14.5), предусматривает прокатку-прессование двух исходных заготовок, продавливаемых активными силами трения до упоров в полость камеры сварки большего сечения, расположенной между валками, и дальнейшее экструдирование профиля через матрицу.
|
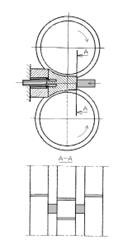
Устройство выполнено с закрытым калибром и матрицей, установленной на выходе из калибра, причем на дне ручья и обращенной к нему поверхности выступа выполнены кольцевые канавки, а в матрицедержателе перед матрицей расположена камера сварки. Устройство снабжено иглой, ее держателем, установленным в кольцевых канавках, образующим со стенками калибра два канала для подачи заготовок, сообщающиеся с камерой сварки, и выполненным с поверхностями, концентричными одна дну ручья и другая – поверхности выступа, обращенными к ним соответственно и расположенными с возможностью контактирования с ними. Кроме того, предусмотрены упоры, расположенные перед входом в камеру сварки и частично перекрывающие каналы для подачи заготовок. Данная конструкция позволяет получать профили сравнительно большого поперечного сечения, а также трубы после переналадки инструментального узла с установкой иглы.
Литература 1 осн. [36-41], 3 осн. [8-178], 6 осн. [6-241], 9 доп. [8-178].
Контрольные вопросы
1. Какие операции ОМД можно считать базовыми для создания комбинированных методов обработки металлов и сплавов?
2. К каким преимуществам ведет совмещение операций литья и обработки металлов давлением?
3. Какие вы знаете совмещенные процессы обработки металлов и сплавов?
4. В чем заключаются преимущества совмещения процессов прокатки и прессования?
5. Каким образом можно получать сплошные пресс-изделия с помощью метода совмещенной прокатки-прессования?
Лекция 15. Совмещение процессов литья и обработки металлов давлением. Производство изделий методом совмещенного литья и прокатки, литейно-прокатные агрегаты. Методы непрерывного литья и прессования. Способы совмещенного литья, прокатки и прессования (СЛИПП).
Процессы непрерывного литья появились в середине девятнадцатого века, при этом начали формироваться наиболее общие, традиционные способы непрерывных процессов, совмещающих плавку, литьё и дальнейшую обработку металлов давлением. Одним из первых совмещенных способов считается процесс введения непрерывно отлитой заготовки в нагретом состоянии в прокатный стан, где значительно уменьшалось её поперечное сечение, и сама заготовка соответствующим образом профилировалась.
На основе традиционных способов ведения непрерывных процессов были созданы мощные технологические линии, совмещающие плавку, литьё и прокатку, а оборудование для реализации совмещенного процесса названо литейно-прокатными агрегатами (ЛПА). Начиная с середины двадцатого века для осуществления совмещённых процессов плавки, литья, прокатки и других операций при производстве полуфабрикатов и готовых изделий из цветных металлов и их сплавов создаются мощные, высокосовершенные и автоматизированные агрегаты на базе горизонтальных графитовых и металлических кристаллизаторов скольжения, роторных, ленточных и валковых кристаллизаторов.
Все промышленные линии независимо от типа применяемого в них кристаллизатора имеют общую структуру, а их конструкционные различия определяются видом получаемого изделия, типом применяемых литейных машин, производительностью агрегатов в целом. Наиболее просты по конструкции горизонтальные кристаллизаторы скольжения и агрегаты на их основе. Особенностью непрерывного литья через такой кристаллизатор с графитовыми вставками является сравнительно низкая скорость движения отлитой заготовки.
Одним из методов решения проблемы совмещения процессов литья и прокатки является использование станов периодической прокатки, дающих возможность вводить в зону деформации заготовки с пониженной скоростью и обеспечивающих высокую степень обжатия за один проход. Однако при прокатке на таких станах не обеспечивается оптимального распределения деформаций, что в ряде случаев приводит к возникновению дефектов прокатываемого материала.
Совмещение литья и прокатки в одной технологической линии предполагалось как необходимый последующий шаг при разработке способа литья в роторные кристаллизаторы, позволяющие вести процесс с высокими скоростями. Начало современной эпохи этих машин связано с агрегатом для производства алюминиевой катанки, состоящей из роторной литейной машины и непрерывного прокатного стана.
На рисунке 15.1 показана схема ЛПА-АК8П, применяемого для получения алюминиевой катанки со среднечасовой производительностью 8 т. Агрегат имеет в своем составе роторную литейную машину для получения заготовки трапециевидного сечения площадью 3300 мм2 и прокатный стан с 12 чередующимися двухвалковыми рабочими клетями, расположенными в две группы. При прокатке используется калибровка овал-круг, а диаметр выпускаемой катанки колеблется от 9 до 19 мм. Суммарная установленная мощность электродвигателей составляет 1500 кВт.
1 – литейная машина; 2 – линия транспортировки заготовки; 3 – прокатный стан; 4 – участок охлаждения катанки; 5 – моталка
Рисунок 15.1 – Схема литейно-прокатного агрегата
Для получения тонких полос и фольги методом совмещённого литья и прокатки используется способ непосредственного литья в валки прокатного стана.
Разнообразие способов непрерывного литья и видов кристаллизаторов привело к созданию во многих странах множества различного типа технологических линий, включающих непрерывные процессы, совмещающие плавку, литьё, прокатку и другие операции обработки металлов. В наши дни на их основе созданы мощности, обеспечивающие выпуск продукции, превысивший потребности многих стран.
Процессы совмещения литья и прессования появились позже, в начале двадцатого века. Процессы совмещенного литья и прессования позволяет значительно снизить капитальные затраты на проектирование и изготовление промышленной линии, существенно сократить энергозатраты на изготовление продукции, получить широкую гамму изделий из цветных металлов и сплавов, получить изделия со стабильными свойствами и качеством по всей длине. Принципиальная схема реализации этого процесса, приведена на рисунке 15.2.
Машина такой конструкции оснащена системой подачи жидкого металла и башмаком большего размера. Расплав из миксера через литейную насадку попадает в канавку охлаждающегося колеса машины. Быстрое охлаждение металла позволяет получить литую заготовку с незначительной ликвацией и мелким зерном, что дает высокую пластичность. По мере вращения колеса происходит накопление металла перед матрицей и его прессование. Этот способ и позволяет получать пресс-изделия с производительностью до 6 тонн в час. Стабильность его реализации во многом зависит от эффективной работы системы непрерывной подачи расплавленного металла в ручей рабочего колеса.
Эта система должна отвечать следующим требованиям: расплавленный металл не затвердевает в начальной фазе процесса; скорость перемещения расплавленного металла постоянна и соответствует скорости его затвердевания, определяемой интенсивностью теплоотвода от рабочего колеса; в потоке расплавленного металла нет завихрений, иначе в его центральный слой могут попасть окислы, газовые пузыри и прочее, что приводит к дефектам пресс-изделий.
Учеными России предложена установка совмещенного литья и прессования для получения прутка диаметром 6 мм из алюминиевых сплавов, при этом базовым оборудованием является литейная машина карусельного типа. Данное оборудование предназначено для производства профилей мелких сечений из расплавленной заготовки путем ее непрерывной кристаллизации и прессования через калибрующее отверстие матрицы.
|
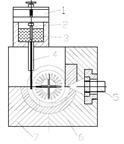
Установка (рисунок 15.3) состоит из приводного карусельного кристаллизатора 1, разливочного устройства 2, прямоугольной канавки 3, выполненной в кристаллизаторе и играющей роль изложницы, кольцевого сегмента 4, неподвижного относительно кристаллизатора, кольцевой вставки 5, выступа 6 и матрицы 7. Привод кристаллизатора осуществляется двигателем мощностью 90 кВт через червячный редуктор. Расплавленный металл через разливочное устройство, выполненное в виде прямоугольной емкости с отверстием в дне, подается в канавку движущегося колеса кристаллизатора.
|
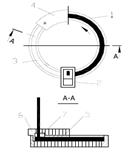
По мере продвижения жидкого металла вместе с колесом к матрице, закрепленной в кольцевом сегменте, происходит его кристаллизация и охлаждение до заданной температуры, при которой металл выдавливается из камеры, образованной тремя сторонами канавки кристаллизатора и поверхностью кольцевой вставки, сопрягающейся с этой канавкой. Для предотвращения выхода металла из камеры по направлению движения канавки в сегменте имеется выступ, который перекрывает поперечное сечение канавки в конце участка ее сопряжения с кольцевой вставкой. Затвердевший в канавке металл достигает выступа в сегменте, после чего распрессовывается по всему сечению камеры. При этом силы трения металла с поверхностью движущейся канавки возрастают до величины, достаточной для его выдавливания через калибрующее отверстие матрицы.
Процесс непрерывного литья и прессования, осуществляемый на данной установке, имеет следующие преимущества перед традиционными способами прессования: реализуется совмещение непрерывных процессов литья и прессования металла; силы контактного трения между заготовкой и контейнером способствуют созданию усилия, необходимого на прессование заготовки; устраняется операция по производству слитка и его нагрева перед прессованием; повышается выход годного металла.
Основным недостатком развития совмещенного процесса является различная организация процесса, так как на большинстве заводов процесс прессования остался дискретным, а процесс литья – непрерывным. При реализации процесса непрерывной подачи заготовок в очаг деформации, что характерно для методов непрерывного прессования, задача становится разрешимой. При этом экономия энергозатрат, например для алюминия, составит около 600 кДж/кг.
По сравнению с затратами на прессование экономия энергозатрат при обработке алюминия составит до 350 %, причем чем меньше коэффициент вытяжки, тем больше эта экономия. Таким образом, способы непрерывного прессования должны совмещаться с методами непрерывной разливки металла, что существенно повышает экономические показатели предлагаемых технологий.
Применение ЛПА выгодно при больших объемах производства и небольшой номенклатуре выпускаемых изделий. При этом в значительной степени сокращаются нерациональные потери времени, энергии и металла, снижаются затраты на установку дополнительного оборудования (нагревательных печей), сокращается производственный цикл, уменьшается объем незавершенного производства и достигается высокая степень механизации и автоматизации.
Одним из новых решений для производства пресс-изделий небольшого сечения из алюминиевых сплавов является схема совмещенного литья и прокатки-прессования. В состав линии входят: установка непрерывного литья заготовок, правильно-задающее устройство, агрегат непрерывной обработки металла, инструментальный узел, поджимное устройство с гидроцилиндром поджима матрицы, охлаждающее устройство, накопитель, стол обрезки с ручными ножницами, моталка, механические ножницы (рисунок 15.4).
Рисунок 15.4 – Принципиальная схема линии непрерывной обработки алюминия и его сплавов
Ориентировочные габаритные размеры проектируемого оборудования, таким образом, составили 12700х5100х4000 мм. Последовательность работы линии следующая. Расплавленный металл из плавильной печи загружается в миксер, где поддерживается постоянная температура расплава, составляющая около 720 оС. Далее из миксера по летке расплавленный металл поступает на установку непрерывного литья заготовок. В состав последней могут входить, в зависимости от варианта технологической цепочки, устройство подачи металла в валки с разливочной коробкой, кристаллизатор, причем тип кристаллизатора зависит от формы, размеров и назначения получаемого изделия. Например, для получения прутков используется роторный кристаллизатор, где формируется заготовка трапецеидальной формы с площадью поперечного сечения около 1600 мм2. Затем при помощи правильно-задающего устройства литая заготовка поступает в валки прокатного стана, где подвергается прокатке и последующему экструдированию через матрицу с заданным диаметром калибрующего отверстия. Полученное пресс-изделие охлаждается и через накопитель поступает для смотки на моталку со сменной катушкой.
Для резки литой заготовки предусмотрены механические ножницы, а для резки изделий – ручные ножницы, установленные на столе. Для гарантированного поджима матрицы к валкам используется гидроцилиндр, имеющий привод от маслостанции. Ориентировочная часовая производительность установки, рассчитанная исходя из параметров кристаллизатора, должна составить от 300 до 500 кг. Возможен также вариант использования только узла совмещенной прокатки-прессования. При этом подогретая до температуры деформации заготовка обрабатывается только путем прокатки-прессования. В данном случае производительность при непрерывной подаче заготовки может быть увеличена в 2–5 раз.
Рисунок 15.5 – Устройство для бесслитковой прокатки-прессования сплошных (а) и полых (б) пресс-изделий
С целью снижения металлургических переделов и исключения из схемы обработки такой достаточно сложной машины, как кристаллизатор, предлагается вариант устройства для бесслитковой прокатки-прессования (рисунок 15.5). В этом случае расплав заливается непосредственно в валки-кристаллизаторы установки, кристаллизуется в виде заготовки прямоугольной формы, подвергается деформации при помощи тех же валков, а затем выдавливается через калибрующее отверстие матрицы. Отличительной чертой данного устройства является то, что оно снабжено установленной сосной матрице длинномерной иглой с механизмом ее отвода, жестко закрепленной фиксатором и расположенной в обойме с каналами для подачи смазки, размещенными по периметру иглы выступами для запирания каналов. При этом в валках выполнены водоохлаждаемые полости.
Литература 1 осн. [36-41], 3 осн. [8-178], 6 осн. [6-241], 9 доп. [8-178].
Контрольные вопросы
1. Для производства какой продукции целесообразно применять агрегаты совмещенного литья и прокатки?
2. Какое оборудование входит в состав ЛПА?
3. В чем заключается сущность процесса бесслитковой прокатки ленты?
4. В чем заключается особенность установок непрерывного литья и прессования металлов?
5. Какое оборудование входит в состав линии совмещенного литья и прокатки-прессования?