Транспортная служба по назначению бывает:
1. Межцеховая (грузовые автомобили, электрокары, железнодорожные платформы, вилочные авто- и электропогрузчики).
2. Внутрицеховая (электрокары, вилочные электропогрузчики, кран-балки, тележки ручные, мостовые краны, железнодорожные платформы).
3. Межоперационная (конвейеры, склизы, приемопередаточные столы, рольганги, тележки ручные, электрокары, вилочные электропогрузчики, поворотные краны, кран-балки, мостовые краны).
По способу загрузки – в таре и без тары. Без тары транспортируются тяжелые и крупногабаритные детали (весом более 100 кг), хотя и они могут складываться в большой контейнер. Предпочтение отдается загрузке в тару. Если детали мелкие, то вес контейнера с деталями должен быть не более 16 кг (в крайнем случае не более 25 кг), т. к. такая тара достаточно удобна для подъема вручную: она не слишком громоздка, из нее легко можно достать деталь. Если детали достаточно крупные и тяжелые, то размеры тары определяются, исходя из легкости доставания деталей (глубина тары не более 600 мм, ширина не более 1000 мм), а вес будет определяться грузоподъемностью подъемного устройства, т. к. вручную такой контейнер подниматься не будет. Иногда на производстве применяются очень большие контейнеры (глубиной более 1500 мм), в которые детали просто кидаются, но доставать их оттуда довольно трудно, к тому же при ударе детали могут получить повреждения.
|
|
В таре детали лучше располагать ориентированно, а не навалом, т. к. меньше вероятность повреждения. Для шлифованных и полированных деталей может применяться тара с деревянными ложементами, покрытыми бархатом или другой плотной тканью. Крупногабаритные детали также могут транспортироваться на поддонах с деревянными ложементами. Сложные корпусные детали могут транспортироваться прямо со спутниками, позволяющими сохранить постоянство баз при обработке.
По схеме движения транспортные системы подразделяются на линейные (склизы, приемопередаточные столы и т. п.) и замкнутые (конвейеры), а также ветвящиеся и неветвящиеся.
По уровню расположения рабочей ветви транспортные системы подразделяются на напольные (электрокары, тележки ручные, напольные конвейеры для тяжелых и крупногабаритных деталей и изделий), эстакадные (на уровне пояса) и подвесные (транспортная ветвь конвейера располагается выше роста человека, а к ней подвешивается заготовка на уровне головы). Эстакадные более удобны для снятия заготовки, но затрудняют перемещение по цеху. Подвесные меньше загромождают помещение, но имеют повышенную шумность из-за цепной передачи.
Конвейеры применяются при поточном производстве и подразделяются на шаговые, прерывистые и постоянные.
|
|
По возможности необходимо сокращать объем грузопотока. Для этого:
1) механообрабатывающие участки должны примыкать к сборочному цеху в порядке востребования деталей по номенклатуре;
2) склады заготовок и полуфабрикатов должны быть расположены в механообрабатывающих корпусах;
3) необходимо перемещать грузы в таре, оптимальной по вместительности;
4) необходимо сокращать число перевалок (например, пустые контейнеры стоят на ручной тележке и после их заполнения тележка перевозится в нужное место без дополнительной перегрузки);
5) размещать оборудование по ходу техпроцесса;
6) при возможности использовать короткие цепи: приемопередаточные столы, склизы (наклонные лотки), рольганги (конвейер с валиками, уменьшающими сопротивление движению);
7) использовать механизацию разгрузочно-погрузочных работ (поворотные краны, шарнирно-балансирные механизмы, погрузчики, электрокары с подъемным краном (см. рис. 16.4), тележки с механизированным подъемом, мостовые краны и т. п.);
8) сокращать вертикальное перемещение грузов (использовать перемещаемые тележки с контейнерами, загрузку с пандуса, расположенного на уровне платформы транспортного средства и т. п.);
9) уменьшать число разветвлений и пересечений транспортной системы.
Автоматические монорельсовые системы применяют в цехах и на участках механосборочного производства для транспортирования изделий в потоке, для «обгонных» транспортных операций, для подачи изделий с поточных линий на склады и т. д.
В настоящее время все большее применение находят подвесные толкающие конвейеры, которые позволяют транспортировать изделия, имеющие различные такты выпуска. Кроме того, толкающие конвейеры применяют, если в технологическом процессе имеются лимитирующие операции, время выполнения которых значительно больше времени выполнения всех остальных операций. Они обеспечивают автоматическое адресование кареток с грузом к месту назначения, а также возможность подачи кареток на ответвления монорельсов, на которых они могут быть либо автоматически остановлены (и тогда из этих кареток с грузом может быть создан накопитель), либо переданы далее на трассу другого толкающего конвейера. Это дает возможность связывать всю сеть подвесных толкающих конвейеров в цехах в общую систему конвейеров с автоматической передачей, складированием и автоматической подачей грузов к месту назначения. Управление перемещением деталей может производиться от компьютера.
Специфика толкающего конвейера заключается в том, что в его системе имеется не один монорельсовый путь с каретками, а два: один путь (верхний) несет движущие элементы, а второй (нижний) — установленные грузы.
Система автоматизированных толкающих конвейеров хотя и является весьма сложной, однако, ее применение резко увеличивает производительность транспортирования при выполнении подъемно-транспортных работ. В качестве магистральных конвейеров, а также для транспортирования внутри участка изделий типа тел вращения (маховиков, фланцев, шестерен и т. д.) в поточном производстве находят использование лотковые транспортирующие устройства, по которым изделия перемещаются качением под действием силы тяжести, реже — скольжением.
Открытые лотки применяют там, где транспортируются легкие изделия на незначительной высоте, а закрытые лотки — при транспортировании тяжелых изделий над рабочим местом для соблюдения правил техники безопасности.
На рис. 16.5 представлена лотковая транспортная система автоматического цеха № 2 (АЦ-2) 1-го ГПЗ.
|
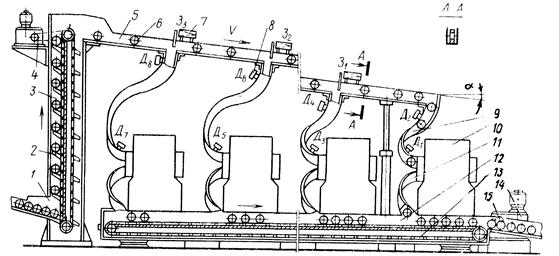
Рис. 16.5. Схема транспортной системы токарного участка автоматического цеха № 2 (АЦ-2) 1-й ГПЗ: 1 - приемный лоток; 2 - захваты конвейера-подъемника элеваторного типа; 3 - подъемник; 4 - привод конвейера-подъемника; 5 - распределительный трассовый лоток; 6 - заготовки; 7 - заслонки; 8 - датчики переполнения подводящих лотков; 9 - подводящие лотки станков; 10 - станки; 11 - отводящие лотки станков; 12 - отводящий конвейер; 13 – ролико-втулочная цепь конвейера; 14 - привод отводящего транспортера; 15 - отводящий лоток к следующему участку
|
|
Транспортная система на рис. 16.5 состоит из подъемника 3 с приводом 4, распределительного трассового лотка 5, подводящих 9 и отводящих 11 лотков, отводящего конвейера 12 с приводом 14 и электроавтоматики управления системой.
Работает конвейер следующим образом. Заготовки, поступая в цепной подъемник 3, направляются в распределительный трассовый лоток 5; скатываясь по этому лотку к подводящим лоткам 9, заготовки поступают в станки 10. После обработки кольца по отводящим лоткам 11 и конвейеру 12 заготовки перемещаются на следующий участок.
Электроавтоматика транспортной системы служит для согласования работы центрального подъемника с работой станков, а также сигнализации и предохранения механизмов от возможных поломок при переполнении кольцами лотков-накопителей.
В поточном производстве при изготовлении изделий средних размеров (автомобилей, тракторов, универсальных металлорежущих станков и т. п.) электрические мостовые краны, как правило, не применяют, за исключением отдельных случаев изготовления особо тяжелых изделий. Это объясняется тем, что требуется дополнительный штат крановщиков, а также тем, что точная установка изделий мостовым краном требует значительно больше времени, чем поворотным краном. При необходимости одновременной установки заготовок, деталей или изделий на несколько единиц оборудования приходится затрачивать дополнительное время на ожидание крана. Кроме того, для крановых пролетов требуется здание большой высоты, и поэтому их строительство обходится дороже, чем строительство бескрановых пролетов.
|
|
Примерное время установки и съема изделий массой до 150 кг составляет, при использовании мостового электрического крана (включая время на вызов его к месту работы), 3…5 мин; подвесного крана – 0,5 мин.
Подвесные краны особенно целесообразно применять при обслуживании определенной производственной площади, а не линии.
Для повышения безопасности передвижения на полу цеха наносятся сплошные полосы желтого цвета, обозначающие участки с активным транспортным движением. На оживленных участках устанавливаются барьеры, препятствующие неожиданному выходу людей на проезд, вывешиваются предупреждающие таблички, обозначаются переходы и даже устанавливаются светофоры. Скорость напольного транспорта должна быть меньше 80 м/мин, а подвесного – меньше 50 м/мин из-за инерционности.
При проектировании и расчете транспортной системы на компоновку цеха наносятся стрелки, ширина которых пропорциональна объему грузопотоков (рис.16.6.), и указывается их объем (штук в смену, т/сутки или т/год).
При проектировании необходимо согласование по времени, поэтому составляется график доставки, производится расчет размера доставляемых партий деталей. При непоточном производстве гораздо сложнее прогнозировать трудоемкость транспортных операций и в среднем она определяется по формуле
, (16.1)
где Т – трудоемкость транспортных операций, ч.; Q – грузопоток, т/г.; – средняя длительность транспортного цикла, мин; q – размер средней транспортной партии, т.