Способ получения стыковых сварных соединений поперечным выдавливанием:
1,2- соединяемые детали; 3 – пуансон; 4 – контейнер.
Образование стыковых соединений осадкой:
![]() | |||||||
![]() | |||||||
![]() | |||||||
![]() | |||||||
Для реализации этого способа создана гамма машин усилием от 6 до 1200 кН, на которых можно производить соединения прутков диаметром от 0,8 до 35 мм из меди и до 43 мм из алюминия. Основными деформационными технологическими параметрами при стыковой холодной сварке, определяющим прочностные свойства получаемых изделий, является отношение высоты деформируемой части прутка к его диаметру (1,0…1,4).
Схема образования тавровых соединений прутка с пластинкой:
1 – пруток; 2- зажимные губки; 3 – пластины; 4 - пуансон; 5 – опора.
Наиболее высокий уровень технологических свойств обеспечивается при соединении изделий из цветных сплавов обеспечивается при:
hо/ dо = 1,0…1,6; ε = 0,7…0,8.
Наибольшее технологическое усилие Р при изготовлении тавровых соединений прутка с пластиной возникает на последней стадии процесса:
|
|
Р= σs[13,1do(doh2o)0,33 + 0,15dп3 / (Н -hп)],
где σs – напряжение текучести металла соединяемых деталей с учетом упрочнения.
Способ соединения металла со стеклопластиком.
1- стержень; 2- наконечник; 3 – матрица.
По этому способу соединения получают в результате пластического деформирования металлического наконечника со вставленным в него стержнем через матрицу усилием, направленным вдоль продольной оси наконечника и упруго деформированного стержня. Величина деформации наконечника из низкоуглеродистой стали при отношении толщины стенки наконечника к диаметру стержня от 0,2 до 0,6 не превышает 15…20%.Способ обеспечивает равномерный натяг по периметру поперечного сечения соединяемых деталей.Получаемые таким методом изделия используются в качестве полимерных изоляторов линий высоковольтных передач.
Рекомендуемое значение угла наклона конусной части матрицы α = 7…12 град.
Для обеспечения стабильности прочностных свойств получаемых соединений рекомендуются следующие значения точности выполнения размеров соединения: для диаметра стержня do – h11; для диаметра отверстия наконечника do- H12;
для наружного диаметра наконечника D-h10.
Данные процессы реализуются на специальных технологических машинах с гидравлическим приводом или универсальных прессах, снабженных специальными приставками.
Гидродорнование.
Сущность этого метода состоит в том, что непрерывно поддерживается высокое давление рабочей жидкости в замкнутых зонах между зубъями дорна и обрабатываемой поверхностью заготовки, обеспечивая эффект гидродинамической смазки. Создаваемое давление не только способствует удержанию смазывающего слоя рабочей жидкости, но и совершает часть деформационной работы, так как направлено в сторону деформирования металла заготовки.
|
|
В настоящее время в ряде европейских стран ведутся интенсивные работы по внедрению метода гидродорнования в производство.При этом достигнут значительный экономический эффект.
Однако широкому внедрению этого метода в реальное производство препятствует сложность его практической реализации, обусловленная трудностью поддержания эффекта гидродинамической смазки. Поэтому на деталях зачастую возникают такие явления, как налипания металла на деформирующий инструмент, задиры и частичные разрушения поверхности детали, которые не допустимы при финишной обработке. Кардинальным решением этой проблемы является построение математических моделей процесса на основе выявления зависимостей между его основными технологическими параметрами, и их оптимизация расчетным или экспериментальным путем.
Причем с развитием средств вычислительной техники первое направление становится все более эффективным. Но для его реализации должна быть построена адекватная математическая модель процесса.
Успешное решение поставленных целей позволит решить такую важную научно-техническую задачу, стоящую перед отечественным машиностроением, как замена сложных и дорогостоящих технологических операций растачивания, шлифования, хонингования и поверхностной обкатки роликом поверхностей отверстий на более производительные и дешевые процессы, такие как гидродорнование. В качестве объекта для исследования рассматривался класс деталей типа «втулка»(втулки гидро и пневмоамортизаторов, сменные втулки цилиндров двигателей внутреннего сгорания и др). Данный класс деталей требует обеспечения равномерности толщины стенки детали и качества ее поверхности по всей ее длине, что наиболее легко достигается именно с помощью гидродорнования.
1 2 4
3
β
![]() | |||||||||||||
![]() | |||||||||||||
![]() | |||||||||||||
![]() | |||||||||||||
![]() | |||||||||||||
![]() | |||||||||||||
![]() | |||||||||||||



































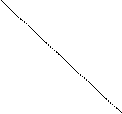

































Принципиальная схема гидродорнования деталей типа «втулка»:
1- гидродорн; 2- радиальный канал подвода рабочей жидкости высокого давления от гидромультипликатора; 3- центральный канал подвода рабочей жидкости высокого давления от гидромультипликатора; 4- рабочая жидкость высокого давления; 5 – деформируемая заготовка.
Сущность этого метода состоит в том, что непрерывно поддерживается высокое давление в замкнутых зонах между зубьями дорна. При этом оказывается дополнительное воздействие на смазывающий клин рабочей жидкостью подаваемой под высоким давлением. Кроме того рабочая жидкость совершает и часть деформационной работы, так как ее давление направлено в сторону деформирования материала заготовки.
Таблица 1
Технико-экономические показатели попыток использования процесса гидродорнования детали «втулка» с внутренним диаметром 60 мм, длиной – 230 мм и толщиной стенки 3мм из малоуглеродистой конструкционной стали [по данным Болгарской Академии Наук ].
№ п/п | Операция | Мощность оборудо- вания,квт | Время обра- ботки, мин. | КИМ, В % | ||
Черновая обто- чка | 7,5 | 1,8 | Существующая | |||
Чистовая обто- чка | 7,5 | 2,85 | Технология | |||
Шлифование | 8,3 | 4,6 | ||||
Хонингование | 12,6 | 2,65 | ||||
Черновая обто- чка | 7,5 | 1,85 | Новая | |||
Фосфатирова- ние | 6,3 | 0,48 | Технология | |||
Гидродорно- вание | 20,5 | 0,26 |
Для определения расхода рабочей жидкости в течении одного цикла деформирования предлагается воспользоваться следующей зависимостью:
|
|
V = 2pa2 c2 /(4a L) S (h0n-1-1 -h-1)tn-1 +p [ d12 hc2/(4a L1) + d2 2 hc 2/(4aL2)] ·
· (h0 -1 -h -1)t; (2)
где а,с,L - геометрические параметры дросселя установки; d 1, d2, L1, L2 – геометрические параметры гидродорна; n – количество зубъев гидродорна, t – время гидродорнования заготовки, tn-1 – время входа (выхода) в заготовку n-го элемента гидродорна. Анализ полученного выражения позволил сделать вывод о том, что расход рабочей жидкости за время рабочего цикла в первую очередь определяется толщиной смазочного слоя между инструментом и заготовкой.
Для определения осевого усилия гидродорнования получена следующая зависимость:
P = 0,25 w p sв d s [(d/d3 + 1)(1+ m^ ctgb) + 2(s3 /d3)0,5 sin b] [1 +(d3/d)0,5]
(3-2cosb);
(3)
где w = 1,1…1,2; d, s –внутренний диаметр и толщина стенки изделия; d3, s3 – внутренний диаметр и толщина исходной трубной заготовки; sв – предел выносливости материала заготовки; m^ - коэффициент жидкостного трения.
Полное усилие выпрессовки полученной детали из матрицы получили на основании решения задачи Ляме в предположении о достижении на ее внутренней поверхности напряжения текучести материала заготовки.
Для избежания появления дефектов на изделии в процессе гидродорнования предложено производить проверку выбранной заготовки по величине предельных коэффициентов раздачи, полученных из условия отсутствия трещин и потери продольной устойчивости:
Кр< exp (2n^/3) + { `s cosb/[2exp(n^/3)]}(1 + 2n^/3); (4)
Kp< { (2,2 jy ss) /[ sb (1 + m ctg)(3 –2cos b) + 1 }0,5; (5)
где Кр – коэффициент раздачи; `s - относительная толщина стенки заготовки; jу – коэффициент продольной устойчивости; m - коэффициент сухого трения гидродорна и заготовки; n^ - показатель деформационного материала заготовки.
Для определения предельных возможностей обработки детали типа «втулка» гидродорнованием без разрушения материала заготовки, воспользовались феноменологическим критерием деформируемости, который для случая многозубого дорна приобретает вид:
|
|
N ei (i j) m
Y = S { B А [ei (i j)А-1 ] / epА ei (i j)} - S (Dyl); (6)
i=1 0 l=1
где Y - остаточный ресурс пластичности полученной детали; ei (i j) - степень деформации на i- м этапе нагружения в j- й зоне детали, характеризующая типоразмер получаемый на i- зубе гидродорна внутреннего диаметра втулки; DY- восстановление ресурса пластичности при l - м рекристаллизационном отжиге; N- количество зубъев гидродорна; m- количество восстановительных отжигов.
Таблица
Рекомендуемые составы рабочей жидкости для гидродорнования.
Материал | Относительная толщина стенки заготовки S3 /d3 | |
1,05 Q 1,15 | > 1,15 | |
Малоуглеродистые стали | 1,7 | 2,5 |
Коррозионностойкие стали | 4,5 | 1,2,3 |
Аллюминиевые и медные сплавы | 3,6,8 | 4,6 |
В данной таблице:
1- сульфофрезол, 2- 5% эмульсия PЗСОЖ8 (ТУ 38-101-258-84), 3- 3 Q 15% эмульсия Укринол-1, 4- масло MP-1, 5- масло MP-1 при омеднении заготовок, 6- масло АМГ –10, 7- эмульсия АМГ-10 (10%) и талька (20%), 8- 10% раствор мыла в воде.
Статистическая обработка результатов экспериментального исследования позволила выявить оптимальную геометрию заходной части гидродорна обеспечивающую наименьшую шероховатость получаемой поверхности при минимальном потребном усилии деформирования.
bопт = 6,149 + 8,059b – 6,588b2 + 2,205b3 + 0,255b4 [град], (10)
где b- ширина калибрующего пояска гидродорна [ мм].
Таблица 3.
Определение числа зубьев гидродорна и процентное распределение натяга в зависимости от общего натяга при гидродорновании деталей типа «втулка».
Натяг I, мм | 0,1… 0,6 | 0,7… 2,5 | 2,6…5,4 | 5,5…7 | ||||
Число зубьев Гидродорна, N | ||||||||
Процентное Распределение Натяга (%) между зубьями | 50/50 | 50/30/20 | 40/25/20/15 | |||||
Также предложены выражения позволяющие еще на стадии проектирования технологического процесса гидродорнования деталей «втулка» оценить ожидаемую шероховатость получаемой поверхности.
Ra = - 2,563 I + 0,049b + 0,232b I [мкм ] (при N= 1…2) (11) и
Ra = 17,197 – 6,943 b – 1,793 b + 0,732 b b [мкм ] (при N= 3…4) (12).
Установленная экспериментально область рационального применения процесса гидродонования, в которой данный процесс обеспечивает устойчивое высокое качество обработанной внутренней поверхности (Ra 0,16…0,32 при точности Н7…Н8), составляет: по наружному диаметру детали – 40…90 мм; по длине – 80…250 мм; по относительной толщине стенки – 1,05…1,20).