Если неизвестны величины жесткостей J 1 и J 2, то в вышеприведенных формулах для расчета сил закрепления можно брать:
= 0,3–0,4 и
= 0,6–0,7.
Меньшие значения в первом соотношении и большие во втором берутся для зажимных устройств пониженной жесткости.
При контакте обработанных поверхностей заготовки с установочными поверхностями коэффициент трения f = 0,16 и мало зависит от шероховатости, давления и смазки. Если установочные элементы имеют сферическую форму, то при уменьшении радиуса сферы и увеличении давления коэффициент трения увеличивается с 0,18 до 0,3. При обычных нагрузках f = 0,20–0,25. При рифленых установочных элементах f = 0,7–0,9.
Зависимость между коэффициентом трения и нормальной силой можно представить для серого чугуна и стали в виде
f = ,
где N – нормальная сила в Н на 1 см2 площади установочного элемента. Коэффициент запаса в формулах нужно подбирать дифференцированно как произведение коэффициентов k 0 k 1 k 2…, отражающих поправки на этапах расчета:
k 0 – коэффициент, учитывающий неточность расчетов;
|
|
k 0 = k` 0 k`` 0 k``` 0;
k` 0 = 1,1–1,3 – меньшие значения для однолезвийных, а большие – для многолезвийных;
k`` 0 = 1,1–1,2 – большие значения для сложных многозвенных зажимных систем, а также многоместных приспособлений, где нужно обеспечить равномерное закрепление заготовки;
k`` 0 = 1,2-1,3 учитывает внезапные факторы (выкрашивание режущей кромки инструмента и др.).
Практически k 0 = 1,5–2.
Коэффициент k 1 учитывает наличие случайных неровностей на поверхности заготовки.
При черновой обработке k 1 = 1,2, а при чистовой и отделочной обработке k 1 = 1,0.
Коэффициент k 2учитывает увеличение сил резания от износа режущего инструмента k 2= 1,0–1,7 (табл. 30).
Коэффициент k 3 учитывает увеличение силы резания при прерывистом резании. При точении и торцевом фрезеровании k 3 достигает значения 1,2.
Коэффициент k 4зависит от постоянства зажимных сил. При ручных устройствах силы зажима непостоянны, и k 4 = 1,3. При наличии пневматических, гидравлических устройств прямого действия k 4 = 1,0. Если допуск на размер заготовки влияет на силу закрепления, что имеет место при использовании пневмокамер, мембранных патронов и др. устройств, то k 4 = 1,2.
Коэффициент k 5 учитывает расположение рукояток в ручных зажимных устройствах. При удобном расположении рукоятки и малом угле поворота (до 90°) k 5 = 1. Более 90° - k 5 = 1,2.
Коэффициент k 6учитывается при наличии моментов, стремящихся повернуть заготовку. Если заготовка установлена на опоры с ограниченной поверхностью, k 6 = 1,0. При установке на планке устойчивость заготовки хуже, и k 6 = 1,5. Выбирая значения
коэффициентов k 1, k 2, …, k 6 для заданных условий выполнения операций, можно получить расчетные значения k = k 0, k 1, k 2, k 3, …, k 6 (табл. 30).
|
|
Таблица 30
Значение коэффициента k 2
Метод обработки | Силовые компоненты резания | Коэффициент k 2 | Материал обрабатываемой заготовки |
Сверление | М кр Р о | 0,15 1,0 | Чугун |
Зенкерование | М кр Р о | 1,3 1,2 | Чугун |
Предварительное точение (в скобках – для чистовой обработки) | Рz Ру Рx | 1,0 1,0 1,4(1,1) 1,2(1,4) 1,6(1,0) 1,25(1,3) | Сталь Чугун Сталь Чугун Сталь Чугун |
Цилиндрическое и торцевое фрезерование | Рz | 1,7 1,3 | Сталь Чугун |
Шлифование | Рz | 1,20 | – |
Протягивание | Рz | 1,5 | – |
7. Конструкции зажимных устройств
и приводы в приспособлениях
Для создания силы зажима детали в приспособлениях используют простые и комбинированные зажимные устройства. К простым относятся винтовые, клиновые, эксцентриковые, рычажные и др., а к комбинированным – комбинацию из нескольких простых. Например: винто-клиновые, винто-рычажные и др. Расчет и конструкцию таких зажимных устройств можно взять из технической литературы [1, 2, 3].
Для механизации закрепления деталей в приспособлениях используют пневматические, гидравлические, пневмогидравлические, магнитные, вакуумные и другие приводы.
В крупносерийном и массовом производствах широко используют сжатый воздух, жидкости под давлением, электроэнергию. По быстроте действия пневмоприводы значительно превосходят многие механизированные приводы. Выполняя компоновку зажимных устройств в приспособлении по требуемой силе зажима деталей, рассчитывают исходную силу для привода элементов приспособления. По исходной силе производят выбор конструкций привода и расчет. Например, для пневмоцилиндра или пневмокамеры по известной величине давления воздуха определяется диаметр пневмоцилиндра и другие конструктивные параметры.
Например, для многозвенной конструкции зажимного устройства, показанного на рис. 25, передача силы зажима происходит через прихват и кулачки.
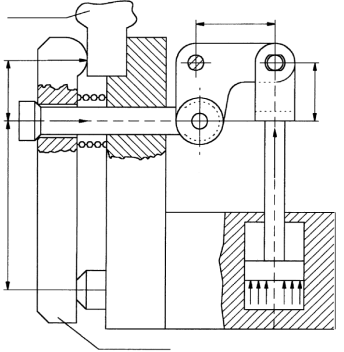
Рис. 25. Многозвенное зажимное устройство
Из уравнения равновесия и учитывая потери на трение в звеньях зажимного устройства коэффициентом f, зависимость исходной силы и силы зажима можно представить уравнением:
,
где q – сила пружины возврата прихвата.
По силе Р можно найти диаметр пневмоцилиндра из выражения:
где D – диаметр цилиндра;
р – давление сжатого воздуха (обычно 0,4–0,5 МПа);
h – КПД, учитывающий потери в цилиндре
(при D = 120–200 мм, h = 0,9–0,95).
8. Расчет точности обработки заготовок
в приспособлении
В технологии машиностроения под точностью изготовления деталей понимается степень приближения геометрических параметров детали к параметрам, заданным на чертеже. Различают три показателя точности: точность выполнения размеров, формы поверхностей и их взаимного расположения. Отклонения параметров реальной детали от заданных номинальных значений называются погрешностями. Общая (суммарная) погрешность является следствием влияния отдельных факторов, вызывающих первичные погрешности, которые делятся на систематические постоянные, систематические закономерно изменяющиеся и случайные. Точность выполнения размеров регламентируется допусками, в которые, как правило, входят допустимые отклонения формы поверхностей и их взаимного расположения. Поэтому при анализе точности обработки заготовок наиболее важным является анализ точности операционных размеров, выполняемых в приспособлениях. Этот анализ и рекомендуется выполнять в курсовом проекте.
В результате выполнения технологической операции суммарная погрешность рассматриваемого размера Δ не должна превышать заданного допуска, т.е. Δ
.
Приспособления для обработки заготовок и сама заготовка являются элементами системы СПИД. Поэтому в самом общем случае для анализа точности требуется построение и решение размерной цепи системы СПИД, которая показывает роль каждого звена в достижении точности операционного размера. Такой анализ сложен и трудоемок, поэтому на стадии проектирования приспособления его отделяют от остальных элементов системы СПИД. Далее все погрешности разбивают на две группы. Первая группа – это Dо – погрешность, связанная с методом обработки. Это есть суммарная погрешность обработки, вызываемая факторами, не связанными с приспособлением, а именно: упругими отжатиями системы СПИД под действием сил резания, погрешностью настройки станка, размерным износом инструмента, тепловыми деформациями системы, геометрическими погрешностями станка и деформацией заготовки при обработке. В литературе [3] Dо очень удачно рассматривается как сумма погрешностей статической и динамической настройки. Dо определяется как экономическая точность метода обработки [5,12,14,15,17]. По данным [14], она имеет следующие значения (табл. 31).
|
|
Таблица 31