Детали ремонтного фонда имеют износ рабочих поверхностей и отклонения от установленной геометрической формы, которые выявляют с помощью измерительных инструментов и приборов с необходимой для каждого случая точностью.
Для проверке размеров деталей при дефектации служат калибры и универсальный инструмент. Для контроля валов используются предельные калибры-скобы (ГОСТ 2216-84, ГОСТ 18355-73, ГОСТ 18356-73), для контроля отверстий – калибры-пробки (ГОСТ 14810-69,ГОСТ 14815-69).
Универсальный инструмент включает штангенциркули (ГОСТ 166-80) – для измерения наружных и внутренних размеров деталей; штангензубомеры – для измерения толщины зубьев цилиндрических зубчатых колёс; Штангенглубиномеры (ГОСТ 162-80) – для измерения глубины отверстий и высоты выемок; гладкие микрометры (ГОСТ 6507-78) – для измерения наружных размеров деталей; индикаторные нутромеры (ГОСТ 868-82, ГОСТ 9244-75) с комплектом сменных измерительных вставок – для измерения внутренних размеров; индикаторы часового типа (ГОСТ 577-68), которые крепятся или перемещаются в стойке или штативе (ГОСТ 10197-70) – для измерения линейных размеров и отклонения формы.
|
|
Отклонения от круглости измеряют кругломерами, от плоскостности – с помощью плит и щупов или по положению отдельных точек, от прямолинейности в плоскости – с помощью поверочных линеек, уровней и оптико-механических приборов.
Контроль отклонений расположения поверхностей и осей детали. Для оценки точности положения поверхностей, как правило, задаётся база, которой может являться поверхность (плоскость), её образующая или точка (вершина конуса, центр сферы), ось (цилиндрическая или коническая поверхность, резьба). За отклонение от параллейности плоскостей принимают разность V наибольшего и наименьшего расстояния между прилегающими плоскостями в пределах нормируемогоучастка. Измерение отклонения от параллейности плоскостей на практике осуществляют следующим образом. Деталь одной поверхностью (базовой) устанавливают на поверочную плиту. С помощью измерительной головки, закреплённой на стойке, определяют отклонение (рисунок 6.1.,а). Измерения отклонения от параллейности плоскости и оси отверстия или двух осей можно проводить с помощью специальных контрольных оправок. На рисунке 6.1, б показана схема измерения отклонения от параллейности установочной поверхности детали и оси отверстия. Деталь устанавливают базовой поверхностью на поверочную плиту. В отверстие детали вводят оправку и с помощью измерительной головки со стойкой определяют отклонение от параллейности как разность двух отсчётов. При такой схеме измерения необходимо учитывать, что в технической документации допустимое отклонение от параллейности задаётся для нормированной длины. Так, если на чертеже были заданы отклонения от параллейности на длине детали l, а измерения провели на другой длине L, то необходимо привести измеренное на длине L отклонение от параллейностиVL к нормированной длине измерений l, т.е V=VL(l/L), где V – отклонение от параллейности на длине l.
|
|
|
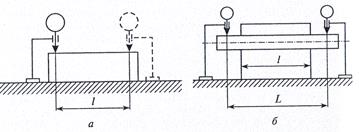
За отклонение от перпендикулярности принимают отклонение угла между плоскостями, осями или осью и плоскостью от прямо го угла 90°, выраженное в линейных единицах на длине нормируемого участка от прилегающих поверхностей или линий.
Измерение отклонения от перпендикулярности плоскостей или торцовых поверхностей деталей относительно осей отверстий или валов (рис. 6.2, а). Приспособление центрируют в отверстии детали, индикатор устанавливают на нуль. Затем его поворачивают вместе с приспособлением вокруг оси отверстия на 360 °. При контроле отклонения от перпендикулярности оси вала к какой-либо плоскости приспособление выполняют в виде кольца. На кольце параллельно его оси крепят индикатор. Кольцо надевают на вал до упора и поворачивают на 360°.
|
Отклонение от перпендикулярности осей двух отверстий можно осуществить с помощью оправки и специального приспособления мостикового типа (см. рис. 6.2, а). Приспособление с двумя индикаторами и оправкой устанавливают в одно из отверстий. Вторую оправку вставляют в другое отверстие. Индикаторы, размещаемые на нормируемом расстоянии друг от друга, вводят в контакт с поверхностью второй оправки и устанавливают на нуль. Поворачивают оправку с мостиком на 180°. Полуразность показаний двух индикаторов соответствует отклонению от перпендикулярности. Радиальное и торцовое биения относятся к погрешностям расположения поверхностей.
За радиальное биение принимают разность наибольшего и наименьшего расстояний от точек реальной поверхности до базовой оси вращения в сечении, перпендикулярном этой оси. Радиальное биение поверхности может задаваться относительно оси вращения детали или относительно других поверхностей. В этом случае последние используют как базовые и деталь устанавливают не в центрах, а призмы на эти поверхности (рисунок 6.3.,а). За биение измеряемой поверхности относительно установочных поверхностей принимают разность наибольшего и наименьшего показаний измерительного прибора за один оборот детали.
![]() | ||||
| ||||
![]() |
Радиальное биение измеряемой поверхности относительно другой может быть оценено при установке детали в центрах. Используют приспособление типа мостик, изображённое на рисунке 6.3, б. Приспособление подводят к измеряемой детали до контакта упора с базовой поверхностью. Измерительный наконечник головки касается измеряемой поверхности. За радиальное биение измеряемой поверхности относительно базовой принимают разность отклонений за один оборотдетали. За торцовое биение принимается разность наибольшего и наименьшего расстояний от точек торцовой поверхности до плоскости, перпендикулярной оси вращения. На рис. 6.3в изображена схема измерения торцового биения цилиндрической детали, которая установлена базовой поверхностью в призму. Упор расположен на оси детали. Торцовое биение определяют как разность предельных показаний измерительной головки. На чертежах торцовое биение задается в габаритах детали для размера D — наибольшего диаметра проверяемой детали, а измеряют биение на диаметре d. Следовательно, получаемый результат измерений необходимо умножить на величину D/d.
|
|
За отклонение от соосности относительно оси базовой поверхности принимается наибольшее расстояние между осью рассматриваемой поверхности вращения и осью базовой поверхности на длине нормируемого участка, определяемое измерением радиального биения проверяемой поверхности в заданном сечении и крайних сечениях при вращении детали вокруг оси базовой поверхности(рис.6.15). На рис. 6.15, а показано определение отклонений от соосности шеек вала с использованием двух измерительных приборов, а на рис. 6.15, б — двух отверстий, расточенных в корпусе, с помощью двух оправок и кольца с измерительной головкой.
|
|

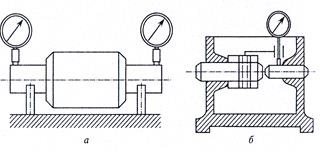
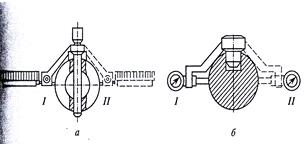
Отклонением от симметричности относительно базового элемента называется наибольшее расстояние между плоскостью симметрии (осью) рассматриваемого элемента (или элементов) и плоскостью симметрии базового элемента в пределах нормируемого участка.
Контроль отклонения от симметрии осуществляют универсальными измерительными средствами. На рисунке 6.16. а показано измерение отклонения от симметрии сквозного отверстия, а на рисунке 6.16 б, - шпоночного паза.
За отклонение от симметрии берётся полуразность показаний прибора в I и II положениях.