К тонким относят пленки, толщина которых составляет десятые и сотые доли микрометра.
При изготовлении ИМС по тонкопленочной технологии для токопроводящих линий, с помощью которых соединяются пленочные элементы микросхемы, и контактных площадок дли подсоединения навесных элементов применяют различные металлы, имеющие высокую электропроводность: алюминий, медь, серебро, золото, никель, хром, олово, их соли и сплавы. Металлы должны быть устойчивы к химическим воздействиям и иметь хорошую адгезию к подложке. Для изготовления обкладок конденсаторов чаще всего применяют алюминий и медь; индуктивные элементы (рис. 21.6) изготовляют из никеля, серебра или хрома.
|
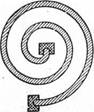
Для получения резистивных элементов используют тантал, титан, никель, хром и их сплавы, также углерод и кремний. Изолирующие диэлектрические пленки получают окислением внешних слоев металлических пленок и нанесением покрытий из диэлектрических материалов. Для нанесения тонких пленок на подложку применяют различные методы: вакуумное напыление, катодное распыление, химическое осаждение и электролитическое анодирование.
|
|
Метод вакуумного напыления иллюстрируется рис. 21.7. Материал для изготовления помещают в тугоплавкий тигель из пластины или вольфрама. Эту систему плотно закрывают колпаком, давление под которым понижают до 10-3 Па, затем тигель нагревают до температуры примерно 1000К. Материал начинает интенсивно испаряться, осаждаясь на более холодной подложке. Осажденная пленка должна быть однородной и плотно соединяться с подложкой, для чего ее поверхность должна быть хорошо очищена от посторонних примесей. Для этого подложку подогревают. Между испарителем и подложкой устанавливают экран, который поглощает молекулы, не попадающие на нее. Осаждающиеся на экране дорогостоящие металлы в дальнейшем смывают и используют вторично. Если в рассмотренной схеме нагрев испарителей осуществляется электрическим током, то для создания пленок из тугоплавких материалов, например вольфрама, титана, молибдена, нагрев производят электронным лучом, направленным непосредственно на испаряющуюся поверхность
Рис. 21.7. Схема вакуумного напыления: 1— колпак; 2 — подогреватель подложки; 3 — подложка; 4 — экран; 5 — испаряющий материал; 6— подогреватель |
Вакуумное напыление можно использовать во всех случаях, однако испарение материалов с высокой температурой кипения — достаточно трудная задача. Поэтому широкое применение находит также метод катодного распыления (рис. 21.8).
При катодном распылении рабочий объем камеры заполняют инертным газом при давлении около 1 Па, а к электродам подводят постоянное напряжение в несколько тысяч вольт. Газ в камере ионизируется, и положительные ионы газа, устремляясь к катоду, выбивают из распыляемого материала молекулы, которые осаждаются на подложке, образуя пленку. Так как разгон ионов осуществляется электрическим полем, процесс распыления может идти при относительно низких температурах распыляемого материала. Метод катодного распыления применяют для создания пленок из таких материалов, как тантал, титан, молибден, вольфрам, платина.
|
|
При химическом осаждении в камеру, где помещается подложка, по различным трубопроводам подают газообразные реагенты. В результате химической реакции выделяются молекулы металла или его солей, которые и осаждаются на подложке. Ненужные продукты реакции откачиваются.
Электролитическое анодирование производят в жидком электролите, куда помещают подложку и материал пленки, растворяющийся в электролите. Подложку (анод) подсоединяет к плюсу источника постоянного тока, а материал пленки (катод) — к минусу. Так как при изготовлении микросхемы нанесение пленок на подложку производят многократно, для получения определенной строго рассчитанной конфигурации каждого слоя применяют фотолитограф и ю.