Сборочная еди- ница | Номер ступени | Кромка лопатки | Повреждения, допустимые без зачистки | Повреждения, допустимые для зачистки | ||||||||||||||||
Расположение от торца пера L, мм | Глубина повреждения не более hмм | Расположение от торца пера L, мм | Глубина повреждения не более hмм | |||||||||||||||||
I | Входная | 0…18 18…89 10мм от хвостовика | 1,5 0,3 0,1 | 0…18 18…89 | 3,0 1,5 | |||||||||||||||
Выходная | 0…25 25…77 10мм от хвостовика | 1,5 0,3 0,1 | 0…25 25…77 | 3,0 1,0 | ||||||||||||||||
II | Входная | 0…13 13…43 10мм от хвостовика | 0,3 0,1 0,3 0,1 | 0…13 13…70 | 3,0 1,5 | |||||||||||||||
Выходная | 0…20 20…45 10мм от хвостовика | 0,3 0,1 0,3 0,1 | 0…62 | 1,0 | ||||||||||||||||
III | Входная | 0…10 10…30 30…60 6мм от хвостовика | 1,5 0,3 0,1 0,1 | 0…18 18…89 | 3,0 1,5 | |||||||||||||||
Выходная | 0…10 10…32 32…54 6мм от хвостовика | 1,5 0,3 0,1 0,1 | 0…10 10…54 | 2,0 1,0 | ||||||||||||||||
IV | Входная | 0…15 15…45 6мм от хвостовика | 0,3 0,1 0,1 | 0…20 20…45 | 2,0 1,0 | |||||||||||||||
Выходная | 0…10 10…42 6мм от хвостовика | 0,3 0,1 0,1 | 0…10 10…42 | 1,5 1,0 | ||||||||||||||||
Ротор КВД | V | Входная | 0…10 15…35 5мм от хвостовика | 1,5 0,3 0,1 | 10…15 15…35 | 1,5 1,0 | ||||||||||||||
Ротор КВД | V | Выходная | 0…10 15…35 5мм от хвостовика | 1,5 0,3 0,1 | 10…35 | 1,0 | ||||||||||||||
VI | Входная | 0…20 20…32 5мм от хвостовика | 1,0 0,5 0,1 | 0…20 20…32 | 1,5 1,0 | |||||||||||||||
Выходная | 0…12 12…30 5мм от хвостовика | 1,0 0,5 0,1 | 0…12 12…30 | 1,5 1,0 | ||||||||||||||||
VII | Входная | 0…7 7…17 5мм от хвостовика | 1,5 0,3 0,1 0,1 | 7…20 20…27 | 1,5 1,0 | |||||||||||||||
Выходная | 0…5 5…25 5мм от хвостовика | 1,5 0,3 0,1 | 5…25 | 1,0 | ||||||||||||||||
VIII | Входная | 0…10 10…24 5мм от хвостовика | 1,5 0,3 0,1 | 10…24 | 1,0 | |||||||||||||||
Выходная | 0…22 5мм от хвостовика | 0,3 0,1 | 0…5 5…22 | 1,5 1,0 | ||||||||||||||||
IX | Входная | 0…10 10…23 5мм от хвостовика | 1,5 0,3 0,1 | 10…23 | 1,0 | |||||||||||||||
Выходная | 0…5 5…21 5мм от хвостовика | 1,5 0,3 0,1 | 5…21 | 1,0 | ||||||||||||||||
ВНА | Входная | 7мм от полки цапфы | 0,1 | |||||||||||||||||
Выходная | 7…85 5мм от хвостовика | 1,5 0,1 | ||||||||||||||||||
Статор КВД | НА I | Входная | 0…68 68…81 7мм от хвостовика | 1,5 0,3 0,1 | 68…81 | 0,6 | ||||||||||||||
Выходная | 0…60 60…73 7мм от хвостовика | 1,5 0,3 0,1 | 60…73 | 0,6 | ||||||||||||||||
Статор КВД | НА II | Входная | 0…47 47…67 5мм от хвостовика | 1,5 0,3 0,1 | 47…67 | 0,6 | ||||||||||||||
Выходная | 0…39 39…59 5мм от хвостовика | 1,5 0,3 0,1 | 39…59 | 0,6 | ||||||||||||||||
НА III | Входная | 0…43 43…53 5мм от хвостовика | 1,5 0,3 0,1 | 43…53 | 0,6 | |||||||||||||||
Выходная | 0…35 35…45 5мм от хвостовика | 1,5 0,3 0,1 | 35…45 | 0,6 | ||||||||||||||||
НА IV | Входная | 0…10 10…40 5мм от хвостовика | 1,5 0,3 0,1 | 0…14 14…40 | 1,5 0,6 | |||||||||||||||
Выходная | 0…5 5…35 5мм от хвостовика | 1,5 0,3 0,1 | 5…35 | 0,6 | ||||||||||||||||
НА V | Входная | 0…19 19…34 5мм от хвостовика | 1,5 0,3 0,1 | 19…24 24…34 | 1,5 0,6 | |||||||||||||||
Выходная | 0…19 19…29 5мм от хвостовика | 1,5 0,3 0,1 | 19…29 | 0,6 | ||||||||||||||||
НА VI | Входная | 0…10 10…29 4мм от хвостовика | 0,3 0,1 0,1 | 0…8 8…29 | 0,6 0,2 | |||||||||||||||
Выходная | 0…17 17…24 4мм от хвостовика | 0,3 0,1 0,1 | 0…13 13…24 | 0,6 0,2 | ||||||||||||||||
НА VII | Входная | 0…12 12…28 4мм от хвостовика | 0,3 0,1 0,1 | 0…11 11…24 | 0,6 0,2 | |||||||||||||||
Выходная | 0…12 12…28 4мм от хвостовика | 0,3 0,1 0,1 | 0…9 9…22 | 0,6 0,2 | ||||||||||||||||
Статор КВД | НА VIII | Входная | 0…6 6…20 4мм от хвостовика | 1,5 0,3 0,1 | 6…20 | 0,6 | ||||||||||||||
Выходная | 0…6 6…20 4мм от хвостовика | 1,5 0,3 0,1 | 6…20 | 0,6 | ||||||||||||||||
НА IX | Входная | 0…15 15…20 4мм от хвостовика | 1,5 0,3 0,1 | 15…20 | 0,6 | |||||||||||||||
Выходная | 0…15 15…20 4мм от хвостовика | 1,5 0,3 0,1 | 15…20 | 0,6 | ||||||||||||||||
Спрямля-ющий аппарат IX ст. | Входная | 0…15 15…20 4мм от хвостовика | 1,5 0,3 0,1 | 15…20 | 0,6 | |||||||||||||||
Выходная | 0…15 15…20 4мм от хвостовика | 1,5 0,3 0,1 | 15…20 | 0,6 | ||||||||||||||||
![]() |
Если обнаружите повреждения - произведите осмотр всех ступеней КНД и
КВД.
2.6.1.5.3 При обнаружении повреждении на лопатках КНД или КВД, превышающих нормы, произведите осмотр всех ступеней КНД и КВД. Если обнаружите повреждения, превышающие нормы на зачистку (графа 6 и 7 табл.), то лопатка подлежит замене.
2.6.2 Нормы повреждений рабочих лопаток и СА ТВД.
2.6.2.1 На лопатках СА ТВД допускаются:
- поверхностное растрескивание алюмосилицированного слоя:
на корыте площадью 40х40 мм (рисунок 2.6.3,А);
на спинке площадью 30х30мм (рисунок 2.6.3, Б);
на радиусе входной кромки (рисунок 2.6.3, В);
- трещины по перу с выходом на выходную кромку:
на спинке (длиной не более 18мм) (рисунок 2.6.3, Г);
на корыте (длиной не более 18мм) (рисунок 2.6.3, Г);
на 5-ти блоках не более одной поврежденной лопатки и блоке;
- трещины длиной до 10мм на наружных и внутренних полках в канале между лопатками (рисунок 2.6.3,Д);
- трещины длиной до 5мм в радиусах перехода пера лопаток в наружную и внутреннюю полки (рис.2.6.3,Е);
- трещины в радиусе перехода выходной кромки пера в наружную и внутреннюю полки длиной не более 5мм (рисунок 2.6.3,Ж);
- трещины на малой полке со стороны входной кромки к отверстиям перфорации длиной не более 20мм (рисунок 2.6.3,И);
- трещины от отверстий компенсационных прорезей на нижней полке длиной не более 8мм (рисунок 2.6.3, К);
- трещины по «козырьку» малой полки длиной до 10мм не более 2-х трещин на блоке (при условии, что расстояние от трещины до прорези не менее 10мм и трещина не имеет тенденции к замыканию с компенсационной прорезью) (рисунок 2.6.3,Л).
2.6.2.2 НЕ ДОПУСКАЮТСЯ на лопатках СА ТВД:
- прогары лопаток СА в любом месте на пере, на наружной или внутренней полках;
- трещины на пере лопаток и на полках лопаток с тенденцией к замыканию между собой (рисунок 2.6.3,М);
2.6.2.3 На внутреннем и наружном кольцах на входе в СА ТВД ДОПУСКАЮТСЯ:
- поперечные трещины (количество не более 5);
- плавное коробление выходной кромки;
- обгар выходной кромки колец (величина обгара не более 20мм по окружности и не более 5мм в осевом направлении).
2.6.2.3.1 НЕ ДОПУСКАЮТСЯ:
- кольцевые трещины;
- трещины с тенденцией к замыканию между собой или с компенсационными
прорезями.
2.6.2.4 При осмотре рабочих лопаток ТВД:
2.6.2.4.1 ДОПУСКАЮТСЯ к дальнейшей эксплуатации:
- трещины на торце пера длиной не более 2мм;
- трещины на ножке замка длиной не более 2мм.
2.6.2.4.2 НЕ ДОПУСКАЮТСЯ к дальнейшей эксплуатации:
- трещины и прогары на пере лопаток.
Рисунок 2.6.3
Рисунок 2.6.4.
Рисунок 2.6.6
2.6.3 Нормы повреждений жаровой трубы КС.
2.6.3.1 Допускаются обгары, оплавления кромок козырьков секций жаровой трубы не более 10мм по окружности и не более 2мм по длине козырька (рисунок 2.6.5). На одной обечайке допускается не более трех мест.
2.6.3.2 Обгары кромок пистонов головочных отверстий допускаются на величину до 1/4 по окружности и до 1/2 по высоте выступающей части пистона.
2.6.3.3 На одном козырьке жаровой трубы (рисунок 2.6.5) допускается не более четырех трещин длиной по образующей до 7мм с расстоянием между трещинами не менее 20мм.
ВНИМАНИЕ! Разветвления трещин с тенденцией к замыканию
НЕ ДОПУСКАЮТСЯ!
2.6.3.4 Коробления козырьков секций жаровой трубы:
- допускаются плавные коробления кромок козырьков, при этом допускается уменьшение высоты щели пояса охлаждения до 1/2 номинального размера (т.е. размера в искоробленном месте);
- количество мест коробления - не более четырех на каждом поясе.
2.6.3.5 Коробление обечаек жаровой трубы:
- допускаются плавные коробления кромок обечаек жаровой трубы длиной 12мм, высотой до 3мм;
- количество мест коробления - не более четырех на каждой обечайке.
2.6.3.6 Оплавление одной выкружки на каждой обечайке до 10мм по окружности и 1 мм по глубине.
2.6.3.7 Трещины от отверстий компенсационных прорезей длиной не более 5мм на каждой обечайке.
ВНИМАНИЕ! НЕ ДОПУСКАЮТСЯ:
- на обечайках жаровой трубы разветвленные трещины с тенденцией к замыканию независимо от длины;
- коробления, расположенные «след в след» на трех и более обечайках;
- обгары, расположенные «след в след» на двух и более смежных обечайках жаровой трубы;
- сквозные прогары стенок жаровой трубы.
2.7 Сведения, необходимые при проверке цепей электрооборудования на двигателе:
2.7.1 При работах руководствуйтесь следующей документацией:
- 29.02.01 САУ - Альбом инструментальных схем, в том числе Перечень параметров работы двигателя и аварийно-предупредительных сигналов, совместно с 29.02-06П2;
- Перечень агрегатов двигателя;
- 29.10.00.000 Э3.9 - Схема электрическая принципиальная.
2.7.2 Проверяемые цепи электросхемы двигателя должны быть отключены от системы управления двигателем.
2.8 Щелевой сигнализатор стружки. Демонтаж, осмотр, промывка, проверка и монтаж чувствительного элемента.
- Инструмент и приспособления: плоскогубцы, ключи, переходник, съемник, заглушка, кисть – из комплектов по ведомостям 29.10ВД и 29.12ВД.
- Приборы: мегаомметр, универсальный вольтомметр.
- Расходуемые материалы: чувствительный элемент 29.09.07.010 (при замене) - 1 шт.; кольцо 039-042-19-2-043 - 1 шт.; проволока 0,8-ТС-12Х18Н10Т - 0,3 м; проволока 0,6-ТС-12Х18Н10Т - 0.3 м; смазка ЦИАТИМ-201 или ЦИАТИМ-221 - 10 г; НЕФРАС - 0,3 л.
2.8.1 Демонтаж.
2.8.1.1 Расконтрите и отстыкуйте розетку электрожгута от вилки чувствительного элемента.
2.8.1.2 Расконтрите и отвинтите гайку 1 (рисунок 2.8.1) крепления чувствительного элемента 3 в корпусе 5.
2.8.1.3 Извлеките чувствительный элемент 3 из корпуса 5 съемником.
2.8.1.4 Снимите с чувствительного элемента 3 кольцо 4.
2.8.1.5 Закройте отверстие в корпусе заглушкой.
2.8.2 Осмотр и промывка чувствительного элемента.
2.8.2.1 Снимите кожух 8, для чего расконтрите и отвинтите гайку 10; извлеките Г-образный замок 11, снимите крышку 9, а затем кожух 8. Установите крышку 9 и рукой завинтите гайку 10,
ВНИМАНИЕ! 1 КРЫШКУ 9 И КОЖУХ 8 СНИМАЙТЕ ПРИ ВЕРТИКАЛЬНОМ ПОЛОЖЕНИИ ЧУВСТВИТЕЛЬНОГО ЭЛЕМЕНТА ЭЛЕКТРИЧЕСКИМ СОЕДИНИТЕЛЕМ ВНИЗ!
2 НЕ ДОПУСКАЙТЕ СНЯТИЯ НАБОРА ТОКОПРОВОДЯЩИХ ШАЙБ 6 С НАПРАВЛЯЮЩИХ СТЕРЖНЕЙ!
2.8.2.2 Осмотрите чувствительный элемент - повреждения не допускаются.
2.8.2.3 Промойте чувствительный элемент НЕФРАСом, применяя кисть 880/520. Продуйте сжатым (Р = 1,5...2,0 кгс/см 2) воздухом.
2.8.2.4 Отвинтите гайку 10, снимите крышку 9; установите кожух 8, наденьте крышку 9, установите Г-образный замок, завинтите гайку 10 ключом с переходником моментом М кр = 0,04…0,06 кгс.м. Законтрите гайку 10.
1 - гайка
2 - вилка соединителя
3 - чувствительный элемент
4 - уплотнительное кольцо
5 - корпус
6 - токопроводящие шайбы
7 - электроизоляционные прокладки
8 - кожух
9 - крышка с изолятором
10 - гайка
11 - замок Г-образный
12 - кольцо токосъемника
А - окна
Б - выступ
Рисунок 2.8.1 - Сигнализатор стружки в масле
ВНИМАНИЕ! ПРИ УСТАНОВКЕ КОЖУХА 8 ОСЕВАЯ ЛИНИЯ ОКНА «А» КОЖУХА ДОЛЖНА СОВПАДАТЬ С ОСЕВОЙ ЛИНИЕЙ ВЫСТУПА «Б» НА СЕРДЕЧНИКЕ.
2.8.3 Проверка чувствительного элемента.
2.8.3.1 Проверьте наличие цепи между контактами 1 и 4 вилки соединителя при замыкании металлическим проводником кольца 12 с металлической частью крышки 9.
2.8.3.2 Проверьте мегаомметром напряжением 500В сопротивление изоляции контактов 1 и 4 вилки соединителя между собой и относительно изоляционного материала крышки 9. Сопротивление изоляции должно быть не менее 20 мОм.
2.8.4 Монтаж.
2.8.4.1 Установите новое кольцо 4 на чувствительный элемент 3 и нанесите на него смазку.
2.8.4.2 Установите чувствительный элемент в корпус, совместив выступ «Б» с пазом в гнезде корпуса.
2.8.4.3 Завинтите гайку 1 ключом и законтрите проволокой 0,8.
2.8.4.4 Состыкуйте розетку электрожгута с вилкой 2 чувствительного элемента и законтрите ее проволокой 0,6.
2.8.4.5 При работе двигателя проконтролируйте герметичность места установки чувствительного элемента.
ПРИМЕЧАНИЕ: В случае замены чувствительного элемента на новый, снятый подготовьте к отправке.
2.9. Термостружкосигнализатор - демонтаж, промывка, проверка и монтаж:
- Инструмент и приспособления: плоскогубцы, ключ, заглушка, кисть – из комплектов по ведомостям 29.10ВД и 29.12ВД.
- Приборы: мегаомметр, универсальный вольтомметр.
- Расходуемые материалы: кольцо уплотнительное 021-024-19-2-043 - 1 шт.; проволока 0,8ТС12Х18Н10Т - 0,2 м; проволока 0,6ТС12Х18Н10Т - 0,2м; смазка ЦИАТИМ-201 или ЦИАТИМ-221-10г; НЕФРАС-0,3л; салфетка батистовая- 1 шт.
2.9.1Демонтаж.
2.9.1.1 Расконтрите и отсоедините розетку электрожгута от вилки 4 ТСС (рисунок 2.9.1).
2.9.1.2 Расконтрите и отвинтите винты (ключ S = 10) крепления ТСС в корпусе, извлеките ТСС из корпуса.
2.9.1.3 Закройте отверстие корпуса заглушкой.
2.9.1.4 Осмотрите магнит 1, целостность клеевой поверхности 5. Трещины и сколы не допускаются.
2.9.1.5 Осмотрите зазор между магнитом 1 и контактом 2. При наличии металлической стружки или загрязнения промойте ТСС.
2.9.2 Промывка ТСС.
2.9.2.1 Протрите магнит салфеткой.
2.9.2.2 Промойте магнит 1 и контакт 2 НЕФРАСом с использованием кисточки, затем продуйте сигнализатор воздухом (Р = 2 кгс/см 2). Промойте отверстие «А» НЕФРАСом; засорение отверстия не допускается.
2.9.3 Проверка ТСС.
2.9.3.1 Проверьте отсутствие цепи между штырями № 2 и № 3 вилки соединителя 4. При наличии цепи замените ТСС новым.
2.9.3.2 Проверьте наличие цепи между магнитом 1 и штырем № 3 соединителя 4, между контактом 2 и штырем № 2 соединителя 4.
2.9.3.3 Проверьте мегаомметром сопротивление изоляции между штырями
№ 2 и № 3 соединителя 4 последовательно между собой и каждого штыря с корпусом 3. Сопротивление изоляции при стандартных условиях должно быть не менее 2МОм.
2.9.4 Монтаж.
2.9.4.1 Наденьте новое уплотнительное кольцо 021-024-19-2-043.
2.9.4.2 Снимите заглушку с корпуса: вставьте ТСС в корпус.
2.9.4.3 Завинтите винты крепления ключом S = 10 и законтрите их проволокой 0,8.
2.9.4.4 Соедините розетку электрожгута с вилкой соединителя ТСС, завинтите гайку розетки до упора рукой и законтрите ее проволокой 0,5.
|
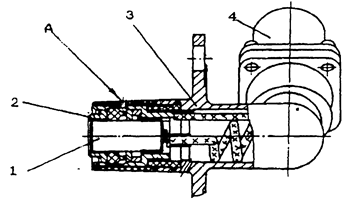
Рисунок 2.9.1 - Термостружкосигнализатор
2.10 Отбор проб масла на анализ.
2.10.1 Отбор проб для определения показателей физико-химических свойств масла выполняют на работающем агрегате из маслобака в сроки:
- на частичный – три раза в неделю;
- на контрольный – один раз в месяц;
- на полный – при выполнении регламентных работ, но не реже одного раза в квартал.
2.10.2 На рентгеноспектральный анализ пробы масла отбирают:
- после технологического запуска вновь установленного двигателя;
- через каждые 100…200 часов наработки;
- при выполнении регламентных работ.
2.10.3 Дополнительно на рентгеноспектральный анализ пробы масла отбирают при поиске неисправностей в случаях:
- срабатывания сигнализатора стружки;
- повышенных вибраций;
- уменьшения времени выбега роторов ниже ТУ;
- наличия стружки на фильтрах.
2.10.4 После технологического запуска, при выполнении регламентных работ и поиске неисправностей пробы масла отбирают (рисунок 16.1) из:
- верхнего редуктора (КПА-1) - КС - 1;
- передней опоры ГГ - КС - 2;
- сливного бачка ГГ - КС - 2;
- линии откачки передней опоры СТ - КС - 4;
- линии откачки задней опоры СТ - КС - 4;
- коробки приводов силовой турбины (КПА-2);
- блока откачивающих насосов - КС7.
2.10.5 Пробы масла из каждой точки отбирают в количестве:
- на частичный и контрольный анализ - не менее 250 мм 3;
- на полный анализ - не менее 500 мм 3;
- на рентгеноспектральный анализ не менее 50 мм 3.
2.10.6 Время между отбором проб масла и выключением двигателя не должно превышать 20 минут. При превышении этого времени необходимо выполнить запуск, выход на режим холостого хода и работу на нем не менее 5 минут.
Примечание - Если запуск невозможен ввиду неисправности, пробы масла отбирают без запуска. В сопроводительном документе делают запись: «Проба масла отобрана не по регламенту по причине...(указать конкретно)».
2.10.7 Последовательность отбора проб масла.
2.10.7.1 Средства отбора проб и сосуды должны быть тщательно вымыты и высушены. Сосуды под пробы должны быть пронумерованы.
Примечание - Запрещается протирать средства отбора и сосуды для проб салфетками.
2.10.7.2 Снимите заглушку и протрите кран слива чистой салфеткой, слегка смоченной нефрасом.
2.10.7.3 Подсоедините приспособление (трубопровод) для отбора пробы к крану слива.
2.10.7.4 Откроите кран слива и слейте 40...50 см 3 масла в отдельную емкость,
2.10.7.5 Не закрывая кран слива, отберите пробу масла в сосуд для анализа.
2.10.7.6 Закройте кран слива, отсоедините приспособление для слива масла, законтрите кран слива и установите заглушку.
Примечание - По конструкции все краны слива одинаковы. Их открытие осуществляется нажатием на головку крана и ее поворотом на 90 градусов.
2.10.8 Лицо, отобравшее пробу масла, заполняет сопроводительное свидетельство. При этом разборчиво указывает:
- наименование эксплуатирующей организации;
- номер сосуда и место отбора;
- номер двигателя;
- марку масла;
- дату отбора пробы масла;
- наработку двигателя (с начала эксплуатации и за установку) и масла (после последней замены);
- фамилию и подпись отобравшего пробу масла.
2.10.9 Пробы масла вместе с сопроводительными свидетельствами отправьте на анализ не позднее следующего дня после отбора проб масла.
2.10.10 Оценку технического состояния двигателя по результатам спектрального анализа масла выполняют путем сопоставления значений, полученных при анализе проб масла, с нормами предельно допустимого содержания химических элементов в масле (Приложение № 8).