Формирование поверхностей деталей со снятием и без снятия стружки. Классификация методов формообразования поверхности деталей. Механическая обработка деталей резанием. Кинематические и геометрические параметры процесса резания. Физико-химические основы резания. Обработка поверхностей лезвийным, абразивным инструментом. Основы электрофизических и электрохимических способов обработки. Средства технологического оснащения при разных методах обработки. Вопросы автоматизации процессов получения заготовок, изготовления деталей и сборки изделия. Особенности обработки деталей на станках с ЧПУ. Термическая обработка в технологическом процессе изготовления изделий. Износостойкие, антикоррозионные и декоративные покрытия
Все многообразия технологических методов обработки заготовок удалением излишков металла и получение деталей представлена на схеме.
Наиболее широко представлены методы механической обработки, а среди них методы обработки металла резанием.
8.1. Обработка резанием
|
|
Обработка резанием - это технологический процесс обработки металлов снятием стружки для придания изделию заданной формы, размеров и шероховатости поверхности.
Обработка резанием включает в себя: точение, строгание, сверление, протягивание, фрезерование, шлифование и отделочную обработку.
Чтобы срезать с заготовки слой металла, необходимо режущему инструменту и заготовке сообщить относительное движение. Инструмент и заготовку устанавливают и закрепляют в рабочих органах станка, обеспечивающих эти относительные движения.
Движения рабочих органов станка подразделяют на движение резания, установочные и вспомогательные. Движения, которые обеспечивают срезание слоя металла с заготовки называют движением резания. К ним относят главное движение и движение подачи.
Главное движение - это движение, позволяющее осуществить процесс резания и определяющее скорость резания, обозначают буквой "V".
Движение подачи - это движение, обеспечивающее врезание режущей кромки инструмента в заготовку, обозначают буквой "S".
Движение, обеспечивающее взаимное, положение инструмента и заготовки перед срезанием с неё слоя материала, называют установочным.
Вспомогательные движения - это перемещения инструмента и заготовки при подготовке к процессу резания и после окончание его.
К элементам процесса резания относят скорость резания, подача, глубина резания.
Скорость резания - это скорость перемещения обрабатываемой поверхности заготовки относительно режущего инструмента. Если главное движение является вращательным (точение), то скорость резания вычисляют по формуле:
|
|
где Д— диаметр заготовки или инструмента, мм; n- частота вращения шпинделя, об/мин.
Подачей называют путь инструмента относительно заготовки при поступательном движении подач, измеряют в мм/об или мм/мин.
Глубина резания - это толщина слоя заготовки снимаемого за один рабочий ход, измеряют в мм. При точении цилиндрической заготовки глубину резания вычисляют по формуле:
где Д— диаметр обрабатываемой поверхности (заготовки); d - диаметр обработанной поверхности. Резание металлов - это сложный процесс взаимодействие режущего инструмента и заготовки. При движение инструмента упругие деформации переходят в пластические, которые при продолжение взаимодействия приводят к сдвиговым деформациям. Происходит процесс движения частей металла друг относительно друга вплоть до скалывания и образование стружки, когда напряжение превышает предел прочности металла (рис. 81).
Рис. 81. Схема процесса образования стружки
Срезанный слой металла дополнительно деформируется вследствие трения стружки о переднюю поверхность инструмента. В зависимости от свойств металла, режима резания и геометрии инструмента образуются 3 вида стружки (рис. 82):
- сливная стружка - представляет собой сплошную гладкую металлическую ленту. Образуется при резании пластичных металлов и сплавов с малой подачей и большой скоростью резания.
- стружка скалывания - металлическая лента с одной гладкой стороной (прирезцовой) и другой стороной с зазубриными. Образуется при резании металлов средней твердостью с большой подачей и малой скоростью резания.
- стружка надлома состоит из отдельных частей разной формы, не связанных между собой. Образуется при обработке хрупких материалов.
Рис. 82. Виды стружек а - сливная;
б - скалывания; в - надлома
Токарная обработка
Токарная обработка характеризуется наличием движений: вращательное движение заготовки (главное движение, скорость резания) и поступательное движение режущего инструмента - резца (движение подачи).
Разновидностями точения является:
- обтачивание - обработка наружных поверхностей;
- растачивание - обработка внутренних поверхностей;
- подрезание - обработка плоских (торцовых) поверхностей;
- разрезание - резка заготовки на части;
Основным инструментом токарной обработки является резец. Резец состоит из головки - рабочая часть, и тело - стержень, который служит для закрепления резца в резцедержателе. Все многообразие резцов классифицируют по различным признакам (рис. 83).
|
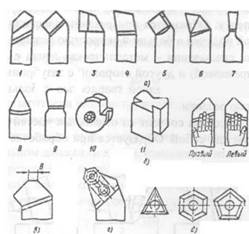
- проходные для обтачивания наружных цилиндрических и конических поверхностей (1-3);
- подрезные для обтачивания плоских торцевых поверхностей (4);
- расточные для растачивания сквозных и глухих отверстий (5-6);
- отрезные для разрезания заготовок (7);
- резьбовые для нарезания резьб (8);
- фасонные для обтачивания фасонных (криволинейных) поверхностей (10-11).
По характеру обработки различают резцы черновые, получистовые и чистовые (9). По направлению подачи резцы подразделяют на правые, работающие с подачей справа налево; левые - слева направо.
По способу изготовления резцы делят: на целые, с приваренной или припаянной рабочей частью; и со сменными многогранными не-перетачиваемыми твердосплавными пластинами. Форма пластин самая разнообразная (рис. 83, г-д).
Строгание
Строгание характеризуется наличием двух движений: поступательным резца или заготовки (скорость резания) и прерывистым поступательным подачи, направленного перпендикулярно вектору главного движения.
Процесс резания при строгании прерывистый и снятие стружки происходит только при рабочем (прямом) ходе инструмента, во время обратного (холостого) хода резец работу резания не производит.
|
|
Инструмент для строгания - резец. Резец, врезаясь в материал заготовки при каждом рабочем ходе, испытывает ударны; нагрузки. Поэтому строгание осуществляют на средних скоростях, а инструмент делают более массивным, по сравнению с резцами применяемых при обработке точением. Наличие холостого хода при строгании увеличивает время обработки и снижает производительность.
Строгание проводят на поперечно-строгальных и продольно-строгальных станках (рис. 84).
Рис. 84. Схемы обработки плоской поверхности на поперечно-строгальном (а), продольно-строгальном (б) и долбежном (в) станках
На поперечно-строгальных станках резец совершает возвратно-поступательное главное движение V, а заготовка движение поперечной подачи в горизонтальной плоскости S. При этой схеме обработки возможно строгание горизонтальной, вертикальной и наклонной плоскостей, а также получение рифленой поверхности.
На продольно-строгальных станках заготовка совершает возвратно-поступательное главное движение V, а режущий инструмент -движение подачи S. Поскольку двигается заготовка возможно использование несколько резцов одновременно:
- строгание горизонтальной и вертикальной плоскостей заготовки;
- строгание паза "ласточкин хвост" и призматического паза;
- строгание фасонных поверхностей по копиру.
Разновидностью строгания является долбление, которое проводят на долбёжных станках. Заготовку обрабатывают при возвратно-поступательном движении режущего инструмента, совершаемом в вертикальной плоскости, и движении подачи заготовки в горизонтальной плоскости.
На долбёжных станках обрабатывают вертикальные плоскости, вертикальные криволинейные поверхности и шпоночные пазы. На зу-бодолбёжных станках возможно изготовление зубчатых цилиндриче
ских колес внешнего и внутреннего зацепления с прямыми и косыми зубьями методом обкатки (рис. 85).
Рис. 85. Схема формоооразования зубьев 1 - долбяк; 2 - нарезаемое колесо
|
|
3. Сверление
Сверление - метод механической обработки для получения сквозных и несквозных (глухих) отверстий или обработка предварительно полученных отверстий для предания им требуемого размера, точности и шероховатости поверхности.
Сверление характеризуется сочетанием двух движений, которые сообщают инструменту: первое - вращательное движение вокруг оси инструмента (главное движение) и второе - поступательное движение вдоль оси (движение подачи) (рис. 86).
Рис. 86. Схемы сверления (а) и рассверливания (б)
Режущим инструментом для обработки отверстий является сверла, зенкеры, развертки и метчики (рис. 87).
![]() | |||
|
Наиболее распространённым инструментом для сверления и рассверливание отверстий является спиральное сверло, которое имеет 2 главных режущих лезвия и состоит из 4 частей:
1 часть - рабочая (6), которая объединяет режущую (7) и направляющую (5) (калибрующую) части;
2 часть - шейка, соединяющая рабочую (б) и часть сверла с хвостовиком (4);
3 часть - хвостовик, служащий для установки сверла в шпинделе станка;
4 часть - лапка (3), которая является упором для выбивания сверла из станка.
Рассверливание - операция увеличения диаметра ранее просверленного отверстия сверлом большого диаметра. Обычно применяется для получения отверстий диаметром более 30 мм.
Зенкер - инструмент для придания предварительно полученным отверстиям более правильной формы. Зенкеры в отличие от сверл снабжены 3-4 главными режущими лезвиями.
По виду обрабатываемых отверстий зенкеры делятся на:
- цилиндрические, для обработки цилиндрических поверхностей, операцию называют зенкерование;
- конические, для получения углублений под головки винтов, болтов, заклёпок и других деталей, операцию называют зенкование;
- торцевые, для достижения перпендикулярности торцевой поверхности отверстия к его оси, операцию называют цекование;
Возможно изготовление комбинированных зенкеров для обработки двух поверхностей цилиндрической и конической - совмещение двух операций: зенкерование и зенкование.
Развертка - инструмент для окончательной обработки отверстий. Развертка имеет 6-12 главных режущих лезвий, обеспечивающих необходимую точность и шероховатость поверхности, используют обычно после зенкерования. По форме обрабатываемого отверстия развертки различают:
- цилиндрические, для обработки цилиндрических отверстий;
- конические, для обработки конических отверстий; Возможно изготовление сборных разверток с механическим
креплением режущих пластин.
Метчик - инструмент для нарезания внутренних резьб.
4. Протягивание
Протягивание характеризуется главным движением - поступательным движением инструмента относительно неподвижной заготовки.
Принцип протягивания заключается в том, что размер каждого последующего зуба инструмента больше предыдущего. Поскольку каждый зуб срезает с обрабатываемой поверхности заготовки небольшое количество металла, то есть стружку небольшой толщины, поэтому получаемая поверхность имеет малую шероховатость. Несмотря на сравнительно низкую скорость резания, протягивание является высокопроизводительным методом за счет большой суммарной длины инструмента.
Инструмент для протягивания называется протяжка. Протяжка состоит из следующих частей (рис. 88):
- замковая часть (хвостовик), служит для закрепления протяжки в патроне тянущего устройства l1;
- шейка, для соединения замковой и передней направляющей частей l2,
- передняя направляющая часть, для центрирования заготовки перед процессом резания l3;
- режущая часть, для срезания припуска, состоит из режущих зубьев, высота которых последовательно увеличивается на толщину срезаемого слоя l4;
- калибрующая часть, для предания обработанной поверхности окончательных размеров, точности и шероховатости l5,
- задняя направляющая часть, для поддержания протяжки от провисания l6.
5. Фрезерование
Фрезерование характеризуется главным вращательным движением инструмента и поступательным движением подачи заготовки.
Особенностью процесса фрезерования является прерывистость резания каждым зубом инструмента. Зуб находится в контакте с заготовкой и выполняет работу резания только на небольшой части оборота инструмента, а затем продолжает движение, не касаясь заготовки, до следующего врезания. Врезание зуба в заготовку сопровождается ударным воздействием, что приводит к неравномерности процесса резания, вибрации, повышенному износу инструмента и не дает возможности получать высокую точность и низкую шероховатость обрабатываемой поверхности.
В зависимости от направлений движений инструмента и заготовки возможно два способа фрезерования (рис. 89):
1. Встречное, когда направления движений инструмента и заготовки не совпадают, при этом нагрузка на зуб возрастает от нуля до максимума.
2. Попутное, когда направления движений инструмента и заготовки совпадают, при этом нагрузка на зуб при врезании максимальна.
![]() |
Инструмент для фрезерования - фреза. В зависимости от назначения и вида обрабатываемой поверхности различают следующие типы фрез (рис. 90):
-
![]() |
цилиндрические, для обработки горизонтальных плоскостей (а);
- торцевые, для обработки прямолинейных поверхностей: горизонтальных, вертикальных и наклонных при вращающемся шпинделе станка (б);
- дисковые, для обработки пазов: прямоугольных, Т-образных и шпоночных под сегментные шпонки (в);
- концевые, имеющие режущие лезвия на боковой и торцевой поверхностях, используют для обработки вертикальных и наклонных плоскостей, изготовления уступов и шпонок (г);
- угловые, для получение наклонных плоскостей и фасонных пазов (д);
- шпоночные, для изготовления шпоночных пазов (е);
- фасонные, для обработки криволинейных поверхностей (ж). Возможно изготовления фрез со сменными многогранными не-
перетачиваемыми твердосплавными пластинами (з).
На зубофрезерных станках по методу обкатки нарезают цилиндрические колеса внешнего зацепления с прямыми и косыми зубьями, червячные колеса.
6. Шлифование
Шлифование характеризуется вращательным движением инструмента и поступательным и вращательным движением заготовки.
Шлифование - это процесс обработки резанием при помощи абразивного инструмента. Абразивный инструмент состоит из зерен природных или искусственных материалов.
Природные материалы - наждак, кварцевый песок, кремень, корунд, алмаз.
![]() |
Искусственные материалы: электрокорунд, синтетические алмазы, карбид бора (ВС), карбид кремния (SiC).
Абразивные зерна расположены в инструменте беспорядочно и удерживаются связующим материалом. При вращательном движении инструмента (абразивного круга) при очень больших скоростях (более 30 м/с) в зоне контакта абразива с заготовкой срезается очень большое число тонких стружек. Процесс резания каждым зерном осуществляется почти мгновенно с выделением большого количества теплоты, мелкие частицы обрабатываемого материала сгорают, образуя пучок искр. Обрабатываемая поверхность представляет совокупность микроследов от абразивных зерен и имеет малую шероховатость.
Существуют следующие способы шлифования (рис. 91):
- плоское шлифование, которое характеризуется возвратно-поступательным движением заготовки (а);
- круглое шлифование, которое характеризуется совместным возвратно-поступательным и вращательным движением заготовки (б-в).
Таким способом возможна обработка как внутренних, так и наружных цилиндрических поверхностей. Разновидностью круглого шлифования является бесцентровое шлифование наружной цилиндрической поверхности.
7. Отделочная обработка
Интенсификация производства ведет к увеличению нагрузок на детали, повышению скорости движения их друг относительно друга, что предъявляет повышенные требования к состоянию и качеству поверхности деталей. Для повышения точности деталей и уменьшения шероховатости их поверхности проводят отделочную обработку.
Отделочная обработка характеризуется малой силой резания, небольшой толщиной срезаемых слоев и незначительным тепловыделением.
Отделочная обработка объединяет следующие методы:
- абразивно-жидкостная отделка;
- полировка;
- притирка (доводка);
- хонингование;
- суперфиниширование;
- шевингование.
7.1.Абразивно-жидкостная отделка
Шлифование объёмно-криволинейных и фасонных поверхностей затруднено, единственный метод, дающий возможность получения требуемой величины шероховатости, является абразивно-жидкостная отделка.
Сущность метода состоит в том, что на обрабатываемою поверхность подают под давлением с большой скоростью струи антикоррозионной жидкости со взвешенными частицами абразивного порошка. Частицы абразива ударяют о поверхность, сглаживают микронеровности. В качестве абразива применяют электрокорунд, в суспензии его содержится 30-35 % (по массе).
7.2.Полировка
Полированием уменьшают шероховатость поверхности. Для этого используют полировальные пасты или абразивные зерна, смешанные со смазочным материалом. В качестве абразива применяют порошки из электрокорунда, наждака, окисей железа и хрома. Порошки смешивают со смазочным материалом, который состоит из смеси воска, сала, парафина и керосина. Порошок со смазкой наносят на быстровращающиеся (до 50 м/с) эластичные круги или колеблющиеся щетки, которые изготавливают из войлока, фетра, кожи, спрессованной ткани и других материалов. Хорошие результаты дает полирование бесконечными лентами, плотно огибающими полируемую поверхность. Полировку проводят в автоматическом или полуавтоматическом режиме.
8.1.7.3.Притирка
Притиркой (доводкой) достигается наивысшая точность и наименьшая шероховатость поверхности деталей. Процесс осуществляют с помощью инструмента называемого притиром, повторяющим контур обрабатываемой детали. Материал притира должен быть мягче обрабатываемого материала (чугун, бронза, медь, дерево). На притир наносят притирочную пасту, состоящую из мелкого абразивного порошка (электрокорунд, карбид кремния и бора, оксиды хрома и железа) со связующей жидкостью (машинное масло, керосин, стеарин, вазелин). Абразив внедряется в поверхность притира и удерживается, снимая с обрабатываемой заготовки тонкую стружку. Притирку проводят вручную или на специальных доводочных станках.
7.4. Хонингование
Хонингование применяют для создания специфического профиля в виде сетки на поверхности детали с высокой точностью и малой шероховатостью. Профиль служит для удерживания смазочного материала на поверхности детали. Инструмент для хонингования называется хоном, состоит из головки, в которой закреплены мелкозернистые абразивные бруски (рис. 92). При хонинговании заготовка неподвижна, а головка с брусками вращается и одновременно совершает возвратно-поступательные движения вдоль оси обрабатываемой детали. Обработку проводят при обильном охлаждении зоны резания сма-зочно-охлаждающей жидкостью: керосином, смесью керосина (80-90%) и веретенного масла (20-10%), водно-мыльными эмульсиями.
Рис. 92. Схема хонингования отверстий
7.5. Суперфиниширование
Суперфинишированием уменьшают шероховатость поверхности, оставшуюся от предыдущей обработки. Этой обработкой изменяются глубина и вид микронеровностей, поверхность приобретает сетчатый рельеф. Поверхность обрабатывается абразивными брусками, устанавливаемыми в специальной головке (рис. 93). В качестве абразива используют электрокорунд или карбид кремния. Бруски совершают колебательные движения (амплитудой 1,5-6 мм, частотой 400-1200 колебаний в минуту) с одновременным вращательным движением заготовки. Процесс резания происходит в присутствии смазочного материала малой вязкости - смесь керосина (80-90%) с веретенным или турбинным маслом (20-10 %).
![]() |
8.1.7.6. Шевингование
Шевингование - это процесс уменьшающий или полностью ликвидирующий погрешности профиля и улучшающий качество поверхности зубчатых колес. Обработка состоит в соскабливании с поверхности зубьев незакаленных колес очень тонких волосообразных стружек. Отделку проводят специальным металлическим инструментом - шевером, представляющим собой режущее колесо с зубьями со специальными (режущими) канавками. Обработка идет при обильном охлаждении, которое обеспечивает удаление стружки, смазку и охлаждение режущих лезвий. После шевингования зубчатые колеса становятся более точными, что обеспечивает более качественную передачу движений, облегчает сборку машин, значительно сокращает шум при их работе.