Легированные стали и сплавы с особыми физическими и химическими свойствами можно разделить на пять классов: коррозионно-стойкие (нержавеющие); жаростойкие (окалиностойкие, термостойкие) и жаропрочные; износоустойчивые; магнитные; с особыми тепловыми свойствами.
Стали, устойчивые против коррозии. Коррозия – это поверхностное разрушение металла под воздействием окружающей среды. При этом некоторые металлы (железо, стали) покрываются продуктами коррозии – ржавчиной. Различают химическую (воздействие на металл газов и неэлектролитов – нефть) и электрохимическую (присутствие электролитов – растворов кислот, щелочей, солей) коррозию. Существуют различные способы защиты металлов против коррозии:
– пассивирование – создание на поверхности металла прочной оксидной пленки, непроницаемой для кислорода воздуха;
– применение однофазных сплавов. Разные фазы сплава обладают различными электрохимическими потенциалами. Это приводит к тому, что в агрессивной среде эти фазы образуют электролитическую пару, в результате чего происходит разрушение металла;
|
|
– уменьшение поверхности взаимодействия с агрессивной средой, для чего проводят шлифование и полирование поверхности изделия. Чем меньше шероховатость поверхности изделия, тем больше устойчивость против коррозии на воздухе.
Наиболее распространенные стали – стали общетехнического назначения не обладают коррозионной стойкостью. Под воздействием кислорода атмосферы на поверхности стальных деталей образуются оксиды железа (Fe2O3). Оксиды железа представляют собой рыхлую пленку, не препятствующую проникновению кислорода воздуха, поэтому коррозия распространяется вглубь металла.
Коррозионная стойкость сталей достигается легированием элементами (хром, никель), создающими защитные оксидные пленки и (или) повышающими электрохимический потенциал. В промышленности используют коррозионно-стойкие хромистые и хромоникелевые стали.
Хромистые стали. Хром в воздушной среде имеет малый электрохимический потенциал, однако обладает высокой коррозионной стойкостью за счет возникновения на поверхности пленки оксида хрома Cr2O3, которая препятствует проникновению кислорода в глубь металла, в результате чего процесс коррозии в атмосфере прекращается. Коррозионная стойкость сталей, легированных хромом, возрастает за счет повышения их электрохимического потенциала. Однако это достигается при определенных количествах хрома в стали. Конструкционные хромистые стали (40Х, 40ХФА, 40ХН и др.), в которых массовая доля хрома менее 12 %, коррозионной стойкостью не обладают. Стали 30Х, 40Х, 50Х используются для изготовления небольших средненагруженных деталей. Эти стали склонны к отпускной хрупкости, поэтому после высокого отпуска охлаждение должно быть быстрым.
|
|
В промышленности используют коррозионно-стойкие хромистые стали с массовой долей хрома более 12 и 25 %.
Стали 12Х13, 20Х13, 30Х13, 40Х13 – это стали, имеющие структуру перлита (легирование смещает точку S диаграммы состояния системы Fe−Fe3C в область меньших значений углерода), т.е в сталях эвтектоидных углерода меньше 0,8 %, причем тем меньше, чем более легирована сталь. Следовательно, стали 12Х13, 20Х13 являются доэвтектоидными (это в отожженном состоянии структуры феррита и перлита), сталь 30Х13 – эвтектоидной (структура перлит), сталь 40Х13 – заэвтектоидной (структура перлит, цементит и карбиды хрома). Эти стали устойчивы против коррозии в атмосфере, воде, ряде слабых растворов кислот и щелочей.
Стали, легированные (сталь 12Х28) с 25…30 % Cr, обладающие более высоким электрохимическим потенциалом, обладают и большей коррозионной стойкостью. Они устойчивы против коррозии в азотной кислоте, слабых растворах соляной кислоты и др. кислот, их используют в химической промышленности.
Хром не является дефицитным материалом, поэтому хромистые стали – это конструкционные стали, они нашли широкое применение в промышленности.
Стали 30Х, 40Х, 50Х используются для изготовления небольших средненагруженных деталей. Эти стали склонны к отпускной хрупкости, поэтому после высокого отпуска охлаждение должно быть быстрым. Повышение прокаливаемости достигается микролегированием бором (35ХР). Введение в сталь ванадия значительно увеличивает вязкость (40ХФА).
Хромокремнистые (33ХС) и хромокремниймарганцевые (хромансил25ХГСА) стали обладают высокой прочностью и умеренной вязкостью. Стали хромансилы обладают высокой свариваемостью, из них изготавливают стыковочные сварные узлы, кронштейны, крепежные и другие детали. Широко применяются в автомобилестроении и авиации.
Никель – очень полезный, но дефицитный легирующий элемент, его следует применять лишь там, где другие легирующие элементы не могут обеспечивать требуемых параметров.
Хромоникелевые аустенитные стали легированы 12 % хрома и 10 % никеля, при меньшей доле никеля коррозионная стойкость не достигается. Стали с таким содержанием являются аустенитными. Широко используются хромоникелевые стали марок 12Х18Н9 и 12Х18Н9Т (0,12 % С, 18 % Cr, 9 % Ni и около 0,1 % Ti в стали 12Х18Н9Т). Структура этих сталей – аустенит, они не претерпевают полиморфного превращения, их упрочнить термической обработкой невозможно. Однако изделия из этих сталей подвергают термической обработке для повышения коррозионной стойкости за счет обогащения хромом твердого раствора. При наличии углерода в структуре отожженной стали присутствуют карбиды хрома. Закалка от температуры 1000 оС с охлаждением в воде позволяет растворить карбиды хрома в аустените и предотвратить их выделение при быстром охлаждении.
При использовании стали 12Х18Н9 возникает опасность появления межкристаллитной коррозии. Нагрев закаленной стали может привести к выделению карбидов хрома (Cr23C6) по границам зерен аустенита, к обеднению хромом (ниже 12 %) областей аустенита, и к образованию микрогальванических пар (образуются две фазы с разным электрохимическим потенциалом – аустенит и карбид), в результате чего возникает множество очагов локальной коррозии. Склонность к этому виду коррозии можно устранить или заметно снизить легированием – введением в сталь сильных карбидообразующих элементов, например титана (сталь12Х18Н9Т). Титан связывает весь углерод в своем карбиде TiC, на образование карбидов хрома углерода не остается, поэтому весь хром растворяется в аустените.
|
|
Хромоникелевые аустенитные стали превосходят хромистые в сопротивлении коррозии, они устойчивы против коррозии в морской воде, лаках, органичеких и азотной кислотах, слабых щелочах.
Жаростойкие стали (окалиностойкие) – это сплавы, которые в течение длительного времени при значениях температуры выше 550 °С не разрушаются с поверхности под действием газовой среды.
Жаростойкие стали и сплавы применяют для изготовления деталей, подвергающихся воздействию высоких температур, но не испытывающих большой нагрузки (печное оборудование, сопловые аппараты, детали газотурбинных установок). В некоторых случаях такие стали используют для нагревательных элементов печей. Железо при значениях температуры выше 570 оС образует оксиды FeO, Fe3O4, Fe2O3, не защищающие поверхность металла от взаимодействия с кислородом.
Окалиностойкость сталей достигается легированием хромом, алюминием или кремнием. Эти элементы образуют на поверхности стали плотные оксиды Cr2O3, Al2O3, SiO2, затрудняющие окисление. Для работы при значениях температуры до 800 оС применяют хромистые стали. Влияние хрома наиболее заметно при его массовой доле 15 – 20 % (стали 12Х17, 15Х25Т). При более высоких температурах используют хромоникелевые стали (20Х23Н13) и сплавы на основе никеля (ХН45Ю с составом 44 – 46 % Ni, 15 – 17 % Cr, 2,9 – 3,9 % Al).
Жаропрочные сплавы и стали должны иметь не только достаточную окалиностойкость, но и сохранять механические свойства. Жаропрочность – это сопротивление металла ползучести и разрушению в области высоких значений температуры при длительной нагрузке. Повышение температуры ведет к ослаблению силы межатомных связей, и металлы разрушаются при напряжениях более низких, чем при комнатной температуре. Разрушение происходит в результате ползучести. Ползучесть развивается при значении рабочей температуры, превышающем значение температуры рекристализации, и напряжении выше предела текучести. Жаропрочность тем выше, чем выше температура рекристаллизации Т рек, которая в свою очередь зависит от температуры плавления металла Т пл :
|
|
Т рек = α Т пл ,
где α – коэффициент жаропрочности: для технически чистых металлов α = 0,3…0,4, для сплавовα = 0,6…0,8.
Повышение жаропрочности достигается применением металлов с высокой температурой плавления (тугоплавких), а также сплавов – за счет увеличения коэффициента α. Высокие значения α (0,6 – 0,8) характерны для твердых растворов. При этом аустенитные стали и сплавы обладают большей жаропрочностью, чем ферритные, так как температура рекристаллизации выше у сплавов с ГЦК, а не с ОЦК-решеткой.
В качестве жаропрочных материалов используют:
– стали на основе Feα для работы при температурах до 600 оС; низкоуглеродистые стали, легированные хромом до 1 %, молибденом и ванадием (12ХМ, 15ХМ, 12ХМФ), а также стали с массовой долей углерода около 0,4 % и легированные хромом и кремнием – сильхромы (40Х9С2, 40Х10С3М);
– аустенитные стали на основе Feγ, легированные никелем (около18 %), для работы при температуре до 850 оС (12Х18Н9Т, 08Х18Н10Т);
– сложнолегированные стали мартенситного класса 12Х2МФСР, 12Х2МФБ, 15Х12ВНМФ.
Увеличение массовой доли хрома повышает жаростойкость сталей. Хром, вольфрам, молибден и ванадий повышают температуру рекристаллизации, образуются карбиды, повышающие прочность после термической обработки. Термическая обработка состоит из закалки при значениях температуры выше 1000 oС в масле или на воздухе и высокого отпуска при значениях температуры выше температуры эксплуатации;
– сплавы на основе никеля (ХН77ТЮР – 20 % Cr, 2,7 % Ti, до 1,0 % Fe, до 0,4 % Mn, Ni – в основе) или железоникелевые сплавы (ХН35ВТ, в составе которого в среднем 15 % Cr, 35 % Ni, 3,0 % W, 1,3 % Ti) для работы при значении температуры до 950 оС;
– в технике находят применение тугоплавкие металлы с температурой плавления выше, чем у железа (1539 оС). К ним относятся Nb, Mo, Ta, Cr и W. Чистые металлы имеют сравнительно низкую жаропрочность (малое значение α), то для повышения жаропрочности их легируют элементами, образующими твердые растворы.
Характерной особенностью твердых сплавов является очень высокая твердость HRC87 – 92 при достаточно высокой прочнос-ти. Твердость и прочность зависят от доли связующей фазы (кобальта) и размера зерен карбидов. Чем крупнее зерна карбидов, тем выше прочность. Твердые сплавы отличаются большой износостойкостью и теплостойкостью. Основными твердыми сплавами являются группы ВК (WC + Co), TK (WC + TiC + Co), TTK (WC + TiC + TaC + Co). Наиболее распространенными сплава-ми группы ВК являются сплавы марок ВК3, ВК6, ВК8, ВК20, где число показывает массовую долю кобальта, остальное – карбиды вольфрамаWC. Сплавы группы ТК марок Т30К6, Т14К8: первое число показывает массовую долю карбидов титана, второе – массовую долю кобальта. Сплавы этой группы лучше противостоят изнашиванию, обладают большей твердостью, тепло- и жаростойкостью, стойкостью к коррозии, но меньшей теплопроводностью и большей хрупкостью. Используются на средних и высоких скоростях резания. Сплавы с малой массовой долей кобальта обладают повышенной твердостью и износостойкостью, но минимальной прочностью, Поэтому их используют для чистового точения (ВК3, Т30К4).
Из группы износостойких сталей упомянем марганцовистую сталь (0,9 − 1 % С и около 12 – 14 % Mn), которая после закалки в воде при 1000 – 1500 оС имеет чисто аустенитную структуру. Износостойкость зависит от условий, в которых работают пары трения. Аустенитные стали, склонные к наклепу, эффективны при работе в условиях высоких давлений и динамических нагрузок. Сталь 110Г13Л плохо обрабатывается резанием. Изделия из нее получают методами литья или реже – горячей пластической деформацией. Износостойкость сильно зависит от условий, в которых работают пары трения. Для конкретных условий следует подбирать соответствующие стали.
Магнитные стали в зависимости от конфигурации их петли магнитного гистерезиса разделяют на магнитомягкие и магнитотвердые.
Из магнитомягких сплавов изготавливают электромагниты, магнитопроводы электрических машин, трансформаторов, электрических приборов и аппаратов. Основные требования, предъявляемые к магнитомягким материалам, – низкая коэрцитивная сила Нс (узкая петля гистерезиса), высокая магнитная проницаемость, высокая индукция насыщения, малые потери на вихревые токи и перемагничивание. Магнитомягким материалом является, например, техническое железо.
Наиболее широкое распространение в качестве магнитомягких материалов, работающих в полях промышленной частоты (низкочастотные поля), получили кремнийсодержащие (электротехнические – с массовой долей углерода 0,05 – 0,005 % и кремния 1,0 – 4,8 %) стали. Основное назначение кремния – увеличение удельного электросопротивления стали, и, следовательно, сокращение потерь при перемагничивании. Дальнейшее уменьшение тепловых потерь достигается изготовлением магнитопроводов (роторов и статоров двигателей, сердечников трансформаторов и т.д.) из набора тонколистовых деталей с прослойкой изоляции (полимеров, оксидов).
Стали маркируются буквой Э и четырьмя цифрами: первая цифра означает вид проката и структурное состояние (1 – горячекатаная, 2 – холоднокатаная изотропная, 3 – холоднокатаная анизотропная); вторая цифра показывает массовую долю кремния: 0 – 0,4 %; 1 – от 0,4 до 0,8%; 2 – от 0,8 до 1,8 %; 3 – от 1,8 до 2,8 %; 4 – от 2,8 до 3,8 %; 5 – от 3,8 до 4,8 %;
– третья и четвертая цифры – магнитные характеристики и их уровень (потери при перемагничивании при разных частотах тока, магнитную индукцию и магнитную проницаемость при разной напряженности магнитного поля).
Магнитотвердые сплавы используют для изготовления постоянных магнитов, которые устанавливают в ряде измерительных приборов, радиоаппаратуре и т.д. Они обладают высокой коэрцитивной (размагничивающей) силой Н с > 4 кА/м и значительной магнитной энергией, пропорциональной значениям Н си остаточной магнитной индукции Вr.
Увеличение коэрцитивной силы магнитотвердых сталей достигается получением неоднородной напряженной структуры, представленной высокоуглеродистым мартенситом с высокой плотностью дефектов строения. Постоянные магниты изготовляют из сложных сталей, легированных Co, W, Cr, Bi, Cu, Al.
Высокие магнитные свойства и их стабильность в магнитотвердых сталях достигаются не только путем введения определенных количеств легирующих элементов, но и при соблюдении специальных режимов термической обработки. Для этого сначала проводят нормализацию при значениях температуры 1100 – 1250 оС, а затем нагрев под закалку до 830 – 860 оС с охлаждением в масле и, наконец, отпуск при 100 оС (охлаждение на воздухе).
Стали с большой массовой долей никеля (35 – 44 %) и малой долей углерода (до 0,35 %) имеют аустенитную структуру, что обеспечивает низкий коэффициент их теплового расширения при нагреве. Известны стали марок с особыми тепловыми свойствами: инвар (36 % Ni) и суперинвар (36 % Ni, 50 % Со), платинит (42 % Ni) и элинвар (Х8Н36). Коэффициент линейного расширения инвара от –50 до +100 оС близок к нулю. Однако при температуре выше 100 оС этот коэффициент повышается и при 275 оС становится больше коэффициента линейного расширения обыкновенных сталей. Инвар применяют в точном приборостроении (оптические и геодезические приборы).
Платинит имеет коэффициент линейного расширения, близкий к коэффициенту линейного расширения стекла, хорошо припаивается к нему (заменяет дорогую платину).
Элинвар отличается постоянным модулем упругости, практи-чески не изменяющимся в пределах температур от +50 до +100 оС. Из него изготовляют часовые пружины, камертоны и детали многих физических приборов.
К группе высокопрочных сталей, имеющих предел прочности более 1800 – 2000 МПа, относятся: стали комплексно-легированные, мартенситно-стареющие и трипстали.
Среднеуглеродистые комплексно-легированные стали с 0,45 – 0,50 % С (40ХГСН3ВА) получают прочность (до 2000 МПа) после закалки и отпуска при температуре 250 – 300 оС. Высокая прочность может быть получена и за счет термомеханической обработки.
Стали 30ХГСА, 38ХН3МА после низкотемпературной термомеханической обработки имеют предел прочности 2800 МПа, относительное удлинение и ударная вязкость увеличиваются в два раза по сравнению с обычной термической обработкой. Это связано с тем, что частичное выделение углерода из аустенита при деформации облегчает подвижность дислокаций внутри кристаллов мартенсита, что способствует увеличению пластичности.
По конструкционной прочности и технологичности мартенситно-стареющие стали (03Н18К9М5Т, 04Х11Н9М2Д2ТЮ) превосходят среднеуглеродистые легированные стали. Они обладают малой чувствительностью к надрезам, высоким сопротивлением хрупкому разрушению и низким порогом хладоломкости при прочности до 2000 МПа.
Мартенситно-стареющие стали представляют собой безуглеродистые сплавы железа с никелем (8 – 25 %), дополнительно легированные кобальтом, молибденом, титаном, алюминием, хромом и другими элементами. Благодаря высокой массовой доле никеля, кобальта и малой углерода в результате закалки в воде или на воздухе фиксируется высокопластичный, но низкопрочный железоникелевый мартенсит, пересыщенный легирующими элементами. Основное упрочнение происходит в процессе старения при значениях температуры 450 – 550 °С за счет выделения из мартенситной матрицы когерентно с ней связанных мелкодисперсных фаз.
Мартенситно-стареющие стали обладают высокой конструкционной прочностью в интервале значений температуры от криогенных до 500 °С и рекомендуются для изготовления корпусов ракетных двигателей, стволов артиллерийского и стрелкового оружия, корпусов подводных лодок, батискафов, высоконагруженных дисков турбомашин, зубчатых колес, шпинделей, червяков и т.д.
Трипстали – это сравнительно новый класс сталей. Типичный состав: 0,3 % С, 9 % Cr; 8 % Ni; 4 % Mo; 2 % Si. Наличие никеля и марганца обеспечивает получение после закалки при температурах ~1100 °С аустенитной структуры, имеющей низкую прочность. Прочность стали возрастает после деформации при комнатной температуре, происходит превращение аустенита в мартенсит деформации.
Трипстали обладают высокой прочностью, сохраняя высокую пластичность (σв = 1800 МПа, δ = 20 %). Отличительной особенностью этих сталей является высокое сопротивление развитию трещины.
Тестовые задания
148. Основными легирующими элементами для стали являются:
а) Cr, Ni, Mn, Si; б) P, S, O, N; в) Ti, Co, P,S; г) Al, V, O, N; д) Cu, W, S, P.
149. Твердый раствор легирующего элемента в α-железе называется легированным:
а) аустенитом; б) ферритом; в) цементитом; г) перлитом. д) ледебуритом.
150. Твердый раствор легирующего элемента в γ-железе называется легированным:
а) аустенитом; б) ферритом; в) цементитом; г) перлитом; д) ледебуритом.
151. Твердый раствор легирующего элемента в цементите называется легированным:
а) аустенитом; б) ферритом; в) цементитом; г) перлитом; д) ледебуритом.
152. Укажите легирующий элемент, который не уменьшает вязкость стали при увеличении ее твердости:
а) сера; б) фосфор; в) марганец; г) кремний; д) никель.
153. Укажите, какое влияние оказывают легирующие элементы на точки S и Е диаграммы состояния Fe –C:
а) не оказывает влияния; б) сдвигают вправо; в) сдвигают влево; г) сдвигают вверх; д) сдвигают вниз.
154. Установите соответствие между названиями стали (1 – 3) и содержанием в ней легирующих элементов (а – д):
1) низколегированная; 2) среднелегированная; 3) высоколегированная;
а) 0,01 – 0,05 %; б) 0,1 – 0,5 %; в) 1,0 – 2, 5%. г) 2,5 – 10,0 %; д) более 10,0%.
155. Установите соответствие обозначения легирующего элемента в марке стали (1 – 6) его названию (а – ж):
1) Х; 2) Н; 3) В; 4) М; 5) Г; 6)Ф;
а) молибден; б) марганец; в) медь; г) ванадий; д) вольфрам; е) хром; ж) никель.
156. Буква А в конце марки низколегированных стали означает:
а) массовую долю азота (сотые доли процента); б) массовую долю азота (десятые доли процента); в) массовую долю азота (проценты); г) сталь высококачественную; д) сталь экспериментальную.
157. В марках конструкционных сталей первые две цифры (например, 30ХГСА) означают:
а) предел прочности при растяжении σв, МПа; б) предел прочности при изгибе σи, МПа; в) массовую долю углерода (сотые доли процента); г) ударную вязкость KCU, МДж/м2.; д) относительное удлинение при разрыве δ, %.
158. Цифра в начале марки инструментальных сталей (например, 5ХНМ) означает:
а) предел прочности при растяжении σв, МПа; б) предел прочности при изгибе σи, МПА; в) массовые доли углерода (десятые доли процента); г) ударную вязкость KCU, МДж/м2; д) относительное удлинение при разрыве δ, %.
159. Стали марок 15Г, 20Г, …, 40Г2 относятся к сталям:
а) углеродистым; б) кремнистым; в) марганцовистым; г) износостойким; д) коррозионно-стойким.
160. Стали марок 50С2, 55С2, 60С2, 70С3А относятся к сталям:
а) инструментальным; б) специальным; в) шарикоподшипниковым; г) кремнистым; д) высокопрочным.
161. Особо ответственные пружины изготавливают из стали марки:
а) Ст3; б) 30; в) У7; г) 10Х18Н9Т; д) 50ХФА.
162. Стали марок Р9, Р18 относятся к сталям:
а) конструкционным; б) коррозионно-стойким; в) рессорно-пружинным; г) быстрорежущим; д) специальным.
ЧУГУНЫ
Общие сведения
Чугун отличается от стали: по составу – более высокой долей углерода (более 2,14 %) и примесей; по технологическим свойствам – более высокими литейными свойствами, малой способностью к пластической деформации; почти не используется в сварных конструкциях.
В зависимости от состояния углерода в чугуне различают:
– белый чугун – весь углерод в связанном состоянии в виде цементита, в изломе имеет матово-белый цвет и металлический блеск;
– чугун с графитом – весь углерод или большая часть находится в свободном состоянии в виде графита в металлической основе (матрице), а в связанном состоянии находится не более 0,8 % углерода. Из-за большой доли графита его излом имеет серый цвет;
– половинчатый чугун – часть углерода находится в свободном состоянии в форме графита, но не менее 2 % углерода находится в форме цементита. Мало используется в технике.
В чугунах содержатся те же постоянные примеси, что и в стали.
Сера и фосфор понижают вязкость и пластичность чугунов, так же как и в сталях. Но вредное влияние их на данные свойства не так ощутимо, потому что чугуны являются хрупким материалом. Поэтому в чугунах допускается более высокая доля серы – от 0,1 до 0,12 % и фосфора – от 0,4 до 0,6 %.
Чугуны являются литейными сплавами, поэтому производится оценка вредного влияния примесей на технологические свойства чугунов – жидкотекучесть и усадку.
Сера понижает жидкотекучесть, увеличивает усадку и повышает склонность к образованию трещин.
Фосфор улучшает жидкотекучесть благодаря снижению температуры плавления. Чугуны с увеличенной долей фосфора используют для художественного литья.
Марганец и кремний – полезные примеси, как и в сталях, представляют собой технологические добавки, необходимые для раскисления чугунов. Кремний, являясь графитизатором, способствует образованию свободного углерода, а марганец, будучи карбидообразующим элементом, затрудняет его. Вместе с тем марганец несколько улучшает механические свойства чугунов, особенно в тонкостенных отливках.
Белые чугуны
В белом чугуне весь углерод находится в связанном состоянии – в цементите. Структура белых чугунов описывается диаграммой состояния системы Fe−Fe3C. В структуре белых чугунов присутствует большая доля цементита, химического соединения с высокой твердостью (HV 800 – 1000), поэтому белые чугуны, имеющие высокую твердость (до НВ450 – 550), обладают большой хрупкостью. Они плохо поддаются обработке резанием, преимущественно в промышленности изготавливают из них литые детали простой формы и небольшой массы. Основное назначение белого чугуна – это переработка на ковкий чугун.
Ограниченное применение находят отбеленные чугуны. В поверхностном слое такие отливки имеют структуру белого чугуна, а в сердцевине – чугуна с графитом. Отбеливание – это следствие быстрого охлаждения поверхности отливки. Отбеленный чугун имеет высокую твердость на поверхности. Применяют для валков листовых деталей, практически не подвергаемых обработке резанием и предназначенных для работы в условиях, требующих высокой износостойкости.
Чугуны с графитом
Графит – это полиморфная модификация углерода. Так как графит состоит из 100 %углерода, а цементит включает 6,67 %, то жидкая фаза и аустенит по составу более близки к цементиту, чем к графиту. Следовательно, образование цементита из жидкой фазы и аустенита должно протекать легче, чем образование графита. С другой стороны, при нагреве цементит разлагается на железо и углерод. Следовательно, графит является более стабильной фазой, чем цементит.
Возможны два пути образования графита в чугуне.
1. При благоприятных условиях (наличие в жидкой фазе готовых центров кристаллизации графита и очень медленное охлаждение) происходит непосредственное образование графита из жидкой фазы.
2. При разложении ранее образовавшегося цементита при значении температуры выше 738 oС цементит разлагается на смесь аустенита и графита по схеме
Fе3С→ 3Fеg(С)+ С (графит).
При значениях температуры ниже 738 oС разложение цементита осуществляется по схеме
Fе3С→ 3Fеa(С)+ С (графит).
При малых скоростях охлаждения степень разложения цементита больше.
Графитизацию из жидкой фазы, а также от распада цементита первичного и цементита, входящего в состав эвтектики, называют первичной стадией графитизации.
Выделение вторичного графита из аустенита называют промежуточной стадией графитизации. Образование эвтектоидного графита, а также графита, образовавшегося в результате цементита, входящего в состав перлита, называют вторичной стадией графитизации.
Рис. 7.1. Схема образования структур при графитизации |
Из рассмотрения структур чугунов можно заключить, что их металлическая основа похожа на структуру эвтектоидной или доэвтектоидной стали или технического железа. Чугуны отличаются от стали только наличием графитовых включений, определяющих специальные свойства чугунов.
Рис. 7.2. Зависимость схем микроструктур чугуна от металлической основы и формы графитовых включений |
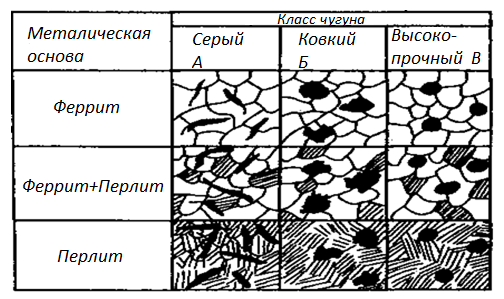
Таким образом, по структурным признакам различают девять видов чугунов: три по форме графита (серый, ковкий, высокопрочный), каждый из которых может иметь ферритную, ферритно-перлитную или перлитную матрицу как видно на рис. 7.1. Твердость и прочность перлита выше, чем у феррита. Поэтому наибольшей прочностью и износостойкостью обладают чугуны с одинаковой формой графита на перлитной основе, наименьшей – на ферритной основе.
Различные неметаллические включения, присутствующие в жидком чугуне (Al2O3, SiO3 и т.д.), являются центрами кристаллизации и облегчают процесс графитизации. В зависимости от массовой доли углерода, связанного в цементите (Ссвяз), меняется структура металлической основы (матрицы) чугуна (табл. 7.1).
Таблица 7.1
Структура чугуна
Массовая доля углерода, % | Структура матрицы | Структура чугуна |
не более 0,02 | Феррит | Феррит+графит |
0,02…0,8 | Феррит+перлит | Феррит+перлит+графит |
0,8 | Перлит | Перлит+графит |
Наиболее широкое распространение получили чугуны с массовой долей углерода 2,4 – 3,8 %. Чем выше массовая доля углерода, тем больше образуется графита и тем ниже его механические свойства, следовательно, доля углерода не должна превышать 3,8 %. В то же время для обеспечения высоких литейных свойств (хорошей жидкотекучести) доля углерода должна быть не менее 2,4 %.
Наименьшей прочностью обладают серые чугуны. Пластинки графита в сером чугуне можно рассматривать как трещины, нарушающие целостность металла и являющиеся концентратами напряжений. Пластинки уменьшают прочность чугуна при растяжении. Чем крупнее пластинки графита и менее равномерно они распределены по объему, тем ниже прочность чугуна. Минимальной прочностью обладает серый чугун на ферритной основе.
Разновидностью серых чугунов с пластинчатой формой графита считается чугун с вермикулярной формой графита, в котором пластинки графита имеют меньший размер и более равномерно распределены в матрице. Он занимает промежуточное положение между чугунами с пластинчатым и шаровидным графитом и сочетает в себе хорошие литейные свойства с достаточно высокой прочностью, пластичностью, ударной вязкостью. Поэтому чугуны с вермикулярной формой графита часто применяют вместо остальных серых чугунов. ГОСТ 28394–89 устанавливает марки чугуна, имеющие в структуре графит вермикулярной формы с массовой долей шаровидного графита до 40 %.
Для изготовления отливок применяются чугуны марок ЧВГ30, ЧВГ35, ЧВГ40 и ЧВГ45. Условное обозначение марки включает: Ч – чугун; ВГ – формы графита (вермикулярный графит) и цифры – минимальное значение временного сопротивления при растяжении σв, МПа∙10-1, (кгс/мм²). Например: ЧВГ30 ГОСТ 28394–89.
Повышение прочности серых чугунов можно достигнуть модифицированием (например, 75%-м ферросилицием в количестве 0,3 – 0,8 %) и легированием (хромом, никелем, алюминием). Свободный графит заметно снижает модуль упругости.
Вместе с тем наличие в структуре свободного графита определяет ряд преимуществ чугуна перед сталью:
– графит улучшает обрабатываемость резанием, так как образуется ломкая стружка;
– чугун имеет лучшие антифрикционные свойства, по сравнению со сталью, так как наличие графита обеспечивает дополнительную смазку поверхностей трения;
– чугун хорошо гасит вибрации и имеет повышенную циклическую вязкость из-за микропустот, заполненных графитом;
– детали из чугуна нечувствительны к поверхностным дефектам (выточки, отверстия, переходы в сечениях, надрезы);
– чугун значительно дешевле стали;
– производство изделий из чугуна литьем дешевле изготовления изделий из стальных заготовок обработкой резанием, а также литьем и обработкой давлением с последующей механической обработкой.
ГОСТ 1412–85 устанавливает марки, химический состав, физические и механические свойства серого чугуна. Для изготовления отливок предусматриваются следующие марки чугуна: СЧ10, СЧ15, СЧ20, СЧ25, СЧ30, СЧ35. Для изготовления отливок по требованию потребителя допускаются марки СЧ18, СЧ21 и СЧ24.
В зависимости от прочности серый чугун подразделяют на 10 марок (ГОСТ 1412–85).
Серые чугуны при малом сопротивлении растяжению имеют достаточно высокое сопротивление сжатию. В составе серых чугунов массовая доля углерода – от 3,2 до 3,5 %; кремния – от 1,9 до 2,5 %; марганца – от 0,5 до 0,8 %; фосфора – от 0,1 до 0,3 %; серы менее 0,12 %. Обозначаются индексом СЧ (серый чугун) и числом, которое показывает значение предела прочности при растяжении, кгс/мм2 (1 кгс/мм2 = 10 МПа). Например: СЧ15 – серый чугун с пределом прочности при растяжении 150 МПа (15 кгс/мм2). Обладающие меньшей прочностью ферритные (СЧ10, СЧ15) и ферритно-перлитные (СЧ20, СЧ25) чугуны используют для менее нагруженных деталей; перлитные (СЧ30, СЧ35) – для более нагруженных. Обладающий хорошей жидкотекучестью серый чугун с повышенной массовой долей фосфора (до 1,6 %) используют в производстве художественного литья.
Высокопрочные чугуны (ГОСТ 7293–85) могут иметь ферритную (ВЧ35), ферритно-перлитную (ВЧ45) и перлитную (ВЧ 80) металлическую основу. Получают эти чугуны из серых в результате модифицирования магнием, редкоземельными металлами или церием (добавляется 0,03 – 0,07 % массы отливки). По сравнению с серыми чугунами механические свойства повышаются, это вызвано отсутствием неравномерности в распределении напряжений из-за шаровидной формы графита.
Чугуны с перлитной металлической основой имеют высокие показатели прочности при меньшем значении пластичности. Соотношение пластичности и прочности ферритных чугунов – обратное.
Высокопрочные чугуны обладают высоким пределом текучести: σт = 300…420 МПа, что выше предела текучести стальных отливок. Также характерна достаточно высокая ударная вязкость и усталостная прочность σ−1 = 230…250 МПа при перлитной основе.
В высокопрочных чугунах массовая доля углерода – от 3,2 до 3,8 %, кремния – от 1,9 до 2,6 %, марганца – от 0,6 до 0,8 %, фосфора – до 0,12 %, серы – до 0,3%. Эти чугуны обладают высокой жидкотекучестью, линейная усадка – около 1%. Литейные напряжения в отливках несколько выше, чем для серого чугуна. Из-за высокого модуля упругости достаточно высокая обрабатываемость резанием. Обладают удовлетворительной свариваемостью.
Для изготовления отливок предусматриваются следующие марки высокопрочного чугуна: ВЧ35, ВЧ40, ВЧ45, ВЧ50, ВЧ50, ВЧ60, ВЧ70, ВЧ80 и ВЧ100.
Из высокопрочного чугуна изготовляют тонкостенные отливки (поршневые кольца), шаботы ковочных молотов, станины и рамы прессов и прокатных станов, изложницы, резцедержатели, планшайбы.
Отливки коленчатых валов массой до 2 – 3 т, в отличие от кованых валов из стали, малочувствительны к внешним концентраторам напряжения, обладают более высокой циклической вязкостью, лучшими антифрикционными свойствами и значительно дешевле. Обозначаются индексом ВЧ (высокопрочный чугун) и числом, которое показывает значение предела прочности на растяжение, МПа (кгс/мм2). Например, ВЧ 60 – высокопрочный чугун с пределом прочности при растяжении 600 МПа (60 кгс/мм2).
Чугуны на перлитной основе (ВЧ 80, ВЧ 60) имеют наибольшую прочность, она снижается у высокопрочных чугунов с ферритно-перлитной основой (ВЧ50, ВЧ45) и минимальна у чугунов с ферритной основой (ВЧ35, ВЧ40).
Высокопрочные чугуны легируют хромом, никелем, молибденом, титаном и алюминием для получения следующих особых свойств: жаростойкости, антифрикционности, коррозионной стойкости и др.
Высокопрочные чугуны эффективно заменяют сталь. Ряд высокопрочных чугунов имеет высокую износостойкость, хорошие антифрикционные свойства и обладает хорошими демпфирующими свойствами. Следует отметить, что высокопрочный чугун унаследовал лучшие технологические, в том числе и литейные, свойства серого чугуна и сохраняет свои механические свойства до значения температуры нагрева 450 – 500 oС. Все это позволяет отнести высокопрочный чугун к числу материалов, обладающих уникальным комплексом физико-механический и служебных свойств, что обеспечивает использование его в различных отраслях современной техники (в частности, в тяжелом и энергетическом машиностроении – детали прокатных станков, дизелей, паро-, газо- и гидротурбин).
Высокопрочные чугуны используют в автомобильном, транспортном и сельскохозяйственном машиностроении. Из них изготовляют коленчатые валы, шестерни, зубчатые колеса.
Ковкий чугун получают путем графитизирующего отжига белого доэвтектического чугуна.
Хорошие свойства у отливок обеспечиваются, если в процессе кристаллизации и охлаждения отливок в форме не происходит процесс графитизации. Чтобы предотвратить графитизацию, чугуны должны иметь пониженную массовую долю углерода и кремния. В ковких чугунах массовая доля углерода – от 2,4 до 3,0 %, кремния – от 0,8 до 1,4 %, марганца – от 0,3 до 1,0 %, фосфора – до 0,2%, серы – до 0,1%.
Формирование окончательной структуры и свойств отливок происходит в процессе отжига по схеме (рис. 7.3).
Рис. 7.3. Отжиг ковкого чугуна |
Структура после выдержки состоит из аустенита и графита (углерод отжига). При медленном охлаждении (5 – 12 ч) в интервале 760 – 720 oС, происходит разложение цементита, входящего в состав перлита, и структура после отжига состоит из феррита и углерода отжига (получается ферритный ковкий чугун со светлым изломом).
При относительно быстром охлаждении (режим б, рис. 7.3) вторая стадия полностью устраняется, и получается перлитный ковкий чугун с бархатисто-черным изломом. Структура чугуна (отожженного по режиму в рис. 7.3) состоит из перлита, феррита и графита отжига (получается ферритно-перлитный ковкий чугун). Отжиг является длительной70 – 80 часов и дорогостоящей операцией. В результате усовершенствований длительность сократилась до 40 часов.
Различают марки ковкого чугуна: с ферритной (КЧ30-6, КЧ33-8; КЧ35-10; КЧ37-12) и с перлитной (КЧ65-3, КЧ50-5; КЧ55-4) основой (ГОСТ 1215–79).
Хлопьевидный графит ослабляет металлическую основу в меньшей степени, чем пластинчатый. Отсутствие литейных напряжений, которые полностью устраняются во время отжига, обусловливают высокие механические свойства ковких чугунов. Уступая высокопрочным чугунам, они существенно превосходят по прочности серые чугуны, а по пластичности – и высокопрочные. Именно из-за своей высокой для чугунов пластичности они получили название ковких. Однако это название условное, пластичность ковких недостаточна для проведения пластической деформации, поэтому ковкие чугуны не куют.
По механическим и технологическим свойствам ковкий чугун занимает промежуточное положение между серым чугуном и сталью. Недостатком ковкого чугуна по сравнению с высокопрочным является ограничение толщины стенок для отливки и необходимость отжига.
Отливки из ковкого чугуна применяют для деталей, работающих при ударных и вибрационных нагрузках.
Из ферритных чугунов изготавливают картеры редукторов, ступицы, крюки, скобы, хомутики, муфты, фланцы.
Из перлитных чугунов, характеризующихся высокой прочностью, достаточной пластичностью, изготавливают вилки карданных валов, звенья и ролики цепей конвейера, тормозные колодки.
Маркируют индексом КЧ (ковкий чугун) и цифрами. Первые – это предел прочности при растяжении, МПа (кгс/мм2), вторые – относительное удлинение, %. Например, КЧ45-6 означает: ковкий чугун с пределом прочности при растяжении, равным 450 МПа (45 кгс/мм2), и относительным удлинением при испытаниях на растяжение, равным 6 %.
В промышленности находят применение чугуны с особыми свойствами, в частности антифрикционными, которые обозначают буквами АЧ (ГОСТ 15485–85). Предусматривают следующие марки чугунов:
– серые чугуны АЧС-1 – перлитный серый чугун, легированный кремнием и медью;
– АЧС-2 – то же, дополнительно легированный с никелем и титаном;
– АЧС-3 – перлитоферритный серый чугун, легированный титаном и медью;
– АЧС-4 – перлитный серый чугун, легированный сурьмой;
– АЧС-5 – аустенитный серый чугун, легированный марганцем и алюминием;
– АЧС-6 – пористый серый чугун, легированныйсвинцом и фосфором.
Здесь АЧ – антифрикционный чугун, С – с пластинчатым графитом (серый чугун), цифры – порядковые номера чугуна. Чугуны АЧВ-1 и АЧВ-2 – антифрикционные чугуны с шаровидным графитом (высокопрочные чугуны), АЧК-1 − чугун, легированный медью, АЧК-2 − ковкий чугун с компактным графитом (с углеродом отжига).
Легированные чугуны. Наряду с обычными конструкционными чугунами в промышленности находят применение легированные конструкционные чугуны. По условиям эксплуатации чугунные отливки в ряде случаев должны обладать не только механическими, но и специальными свойствами – жаропрочностью, жаростойкостью, износостойкостью и т.д. В этом случае применяют специальные чугуны – чаще всего высоколегированные. Состав, свойства и назначение легированных чугунов регламентируются ГОСТ 7769–82.
Термическая обработка чугунов. Чугуны подвергают упрочняющей, разупрочняющей, стабилизирующей и графитизирующей обработке.
Упрочняющая обработка возможна для чугунов, в структуре которых присутствует цементит. Чугуны, так же как и стали, подвергают закалке и отпуску.
При закалке чугун нагревают до температуры 850 – 950 оС для растворения цементита в аустените. Время изотермической выдержки определяется исходя из массы садки. Охлаждение осуществляется в воде или масле. В результате закалки получается мартенсит, бейнит или троостит, помимо которых в структуре присутствует графит. Температуру отпуска (200 – 600 оС) назначают в зависимости от требований к свойствам детали. Охлаждение после отпуска проводят на воздухе.
Графитизирующая обработка – отжиг белого чугуна для получения ковкого.
К разупрочняющей обработке можно отнести смягчающий отжиг, графитизирующий низкотемпературный отжиг. Его проводят для улучшения резанием и повышения пластичности путем продолжительной выдержки при 680 – 700 оС (ниже точки А1) или медленном охлаждением отливок от 760 – 700 оС. Время выдержки должно быть достаточным для полного или требуемого частичного распада эвтектоидного цементита. В результате отжига в структуре чугунов увеличивается доля феррита, снижается твердость, но улучшается обрабатываемость резанием.
Стабилизирующая обработка выполняется для базовых деталей машин (станины, корпуса и т.п.), определяющих точность станка, агрегата. Для них важно сохранение формы и размеров во времени. Изменения размеров возможны из-за наличия остаточных напряжений, возникающих в процессе получения отливки вследствие неравномерного охлаждения отдельных элементов заготовки и/или черновой механической обработки, выполняемой для отливок с большими припусками. В процессе эксплуатации эти напряжения релаксируют (снижаются), вызывая деформацию детали.
Стабилизация размеров чугунных деталей может быть достигнута термической обработкой, вызывающей снижение уровня остаточных напряжений, или деформационного упрочнения чугуна.
Для снижения остаточных напряжений применяют низкотемпературный отжиг, при котором значения температуры ниже критической точки А 1 (520 – 620) оС. Время выдержки зависит от массы и конструкции отливки. Далее охлаждают на воздухе. Такой отжиг не вызывает фазовых превращений и снижает остаточные напряжения, исключая практически деформации в процессе эксплуатации.
Методы деформационного упрочнения основаны на том, что в результате приложенных нагрузок в материале отливки происходят микропластические деформации, которые вызывают наклеп (т.е. повышение прочностных характеристик), что предотвращает развитие деформации. На этом принципе основаны технологии естественного, искусственного и вибрационного старения, методы статической перегрузки.
Естественное старение заключается в длительном вылеживании предварительно грубо механически обработанных отливок на открытом воздухе. Естественное старение – самый универсальный и надежный метод стабилизации размеров и формы отливок.
Искусственное старение осуществляют при повышенных температурах в течение нескольких часов.
Вибрационное старение происходит за счет воздействия на отливку принудительных циклических напряжений – вибраций, во время которых в отливке возникают напряжения, вызывающие локальные пластические деформации чугуна и, таким образом, повышающие стойкость против последующего коробления.
Метод статической перегрузки отличается от вибрационного старения воздействием на деталь внешних статических напряжений (0,6 – 0,75) σв.
Метод термоудара – это деформационно-термическое старение. Он заключается в быстром нагреве и охлаждении детали. Стойкость против коробления повышается за счет локального наклепа вследствие пластических деформаций, вызываемых температурными напряжениями.
Тестовые задания
163. Чугунами называют железоуглеродистые сплавы:
а) с массовой долей углерода более 0,8 %; б) с массовой долей углерода более 4,3 %; в) с массовой долей углерода более 0,02 %; г) с массовой долей углерода более 2,14 %.
164. Белым называют чугун:
а) в котором весь углерод или часть его содержится в виде графита; б) в котором весь углерод находится в химически связанном состоянии; в)в котором металлическая основа состоит из феррита; г) в котором наряду с графитом содержится ледебурит.
165. Ф орма графита в белом чугуне:
а) хлопьевидная; б)вбелом чугуне графита нет; в) шаровидная; г) пластинчатая.
166. В доэвтектических белых чугунах при температуре ниже 727 °С присутствуют две фазовые составляющие: первая – цементит. Вторая фаза называется:
а) ферритом; б) аустенитом; в) ледебуритом; г) перлитом.
167. Ледебурит является одной из структурных составляющих:
а) доэвтектического белого чугуна; б) стали при температуре, выше температуры эвтектоидного превращения; в) ферритного серого чугуна; г) технического железа.
168. Вид чугуна (серый, ковкий, высокопрочный) определяют по микроструктуре:
а) по размеру графитных включений; б) по характеру металлической основы; в) по форме графитных включений; г) по числу графитных включений.
169. Вид чугуна (ферритный, ферритно-перлитный, перлитный) определяют по микроструктуре:
а) по размеру графитных включений; б) по количеству графитных включений; в) по форме графитных включений; г) по характеру металлической основы.
170. Ферритными чугунами называют железоуглеродистые:
а) сплавы, в которых весь углерод (более 2,14 %) находится в виде графита; б) чугуны, в структуре которых наряду с цементитом имеется феррит; в) сплавы с ферритной структурой; г) чугуны, в которых графит имеет пластинчатую форму.
171. Массовая доля связанного углерода в ферритном сером чугуне:
а) 4,3 %; б)0,0 %; в) 2,14 %; г) 0,8 %.
172. Массовая доля связанного углерода в перлитном сером чугуне
а) 2,14 %; б) 0,8 %; в) 4,3 %; г) 0 %.
173. Ч угуны с одинаковой металлической основой в порядке возрастания прочности при растяжении:
а) высокопрочный – ковкий – серый;
б) серый – высокопрочный – ковкий;
в) ковкий – высокопрочный – серый;
г) серый – ковкий – высокопрочный.
174. Путем длительного отжига белого чугуна получают чугун:
а) ковкий; б) отбеленный; в) серый; г) высокопрочный.
175. Путем модифицирования жидкого расплава магнием или церием получают чугун:
а) серый; б) белый; в) высокопрочный; г) ковкий.