ПОДГОТОВКА ОГАРКА, ВОЗГОНОВ И ПЫЛЕЙ К ВЫЩЕЛАЧИВАНИЮ
Обожженный цинковый концентрат (огарок) по выходе из печи КС представляет собой порошкообразный довольно абразивный материал с температурой выше 900° С. Этот материал неоднороден но крупности и содержит около 40% зерен крупнее 0,174 мм. Другой продукт обжига - циклонная пыль, которая объединяется в последующем с огарком, имеет более низкую температуру (менее 500° С) и практически однородный гранулометрический состав, так как содержание основной фракции –0.1мм достигает 98%. Пыль электрофильтров также перерабатывается вместе с огарком.
Различная величина зерен продуктов обжига требует различной продолжительности выщелачивания для полного извлечения из обожженного концентрата цинка и других полезных компонентов. Тонкие фракции будут выщелачиваться быстрее, крупные - медленнее. При Данной продолжительности выщелачивания, которая определяется временем, необходимым для растворения преобладающей фракции материала, и ограничивается емкостью оборудования для этой операции цинк может быть полностью извлечен только из этой и из более тонких фракций. Из крупных фракций извлечение металла будет неполным.
|
|
В крупных фракциях материала содержится больше сульфидного цинка, который должен быть возвращен на обжиг, если в этом есть необходимость, или направлен на вельцевание. Высокая температура огарка также осложняет дальнейшую работу с ним обслуживающего персонала.
Кроме того, в процессе гидрометаллургической переработки огарок приходится транспортировать в смеси с раствором по желобам и трубам, перекачивать в виде пульпы насосами, перемешивать и перемещать в аппаратуре воздухом или механически. Наличие в огарке крупной, так называемой песковой, фракции чрезвычайно затрудняет процесс выщелачивания. Пески забивают аппаратуру и трубопроводы, оседают в желобах, вызывают поломки перегребающих механизмов. Поэтому подготовка огарка к выщелачиванию является обязательной и весьма существенной стадией производственного процесса, оказывающей большое влияние на технико-экономические показатели последующего передела выщелачивания.
В комплекс подготовительных операций входят охлаждение, классификация и измельчение крупных фракций огарка. Во многих случаях транспортирование огарка совмещают с дополнительным охлаждением.
Охлаждение и транспортирование огарка
Охлаждение огарка
Охлаждение огарка необходимо для удобства последующего транспортирования, проведения сухой классификации материала, взвешивания, дозирования и удаления из него остатков сернистого газа, затрудняющего окислительные операции при выщелачивании. Для этого, как правило, используют аэроводохолодильники, составляющие одно целое с печами кипящего слоя, а также водоохлаждаемые транспортные средства; шнеки, скребковые и трубчатые транспортеры.
|
|
В аэроводохолодильниках раскаленный огарок продувают сжатым воздухом, который затем поступает в обжиговую печь, и охлаждают с помощью кессонов водой. При этом температура огарка снижается с 950-1000 до 200-250° С. На рис. 23 показана конструкция промышленного аэроводохолодильника, разработанного Гипроцветметом и широко применяемого на отечественных заводах. За время прохождения огарком водоохлаждаемых транспортных механизмов его температура снижается до 100-120° С. На заводах, применяющих гидравлический транспорт и мокрую классификацию, Предварительного охлаждения огарка не требуется.
Транспортирование огарка
Полученный в печах кипящего слоя обожженный концентрат может быть доставлен в цех выщелачивания тремя видами транспорта: механическим, пневматическим и гидравлическим. При использовании первых двух видов транспорта материал может быть предварительно хорошо подготовлен и доставлен в цех выщелачивания в виде, удобном для взвешивания, учета, дозировки и организации как периодического, так и непрерывного выщелачивания. Пневматический транспорт, однако, предпочтительнее механического из-за меньшего пылеобразования.
При гидравлическом транспорте в качестве несущей среды используют оборотный кислый раствор, Использование нейтрального раствора не практикуется ввиду сильного зарастания трубопроводов сульфатами. Система гидравлического транспорта по существу исключает возможность предварительной подготовки огарка до контакта его с кислым раствором и не позволяет осуществить точный весовой учет и порционную дозировку материала при периодическом выщелачивании. Эта система более или менее удачно сочетается только с непрерывным способом выщелачивания. Преимуществом гидравлического транспорта является возможность использования физического тепла огарка для создания необходимой температуры растворов при выщелачивании.
На большинстве отечественных и зарубежных заводов полученный огарок доставляют в цех выщелачивания в сухом виде. В качестве транспортных механизмов применяют водоохлаждаемые шнеки, скребковые, трубчатые, а также ленточные транспортеры. На отдельных зарубежных заводах с непрерывной схемой выщелачивания охлажденный и классифицированный огарок смешивают в обжиговом цехе с кислым оборотным раствором и в виде пульпы откачивают в цех выщелачивания.
На ряде отечественных цинковых заводов («Электроцинк», Челябинский, первый Усть-Каменогорский) для передачи огарка в цех выщелачивания используют гидравлический транспорт.
Рис. 23. Аэроводохолодильник:
1 – воздухораспределительная подина с соплами; 2 – стеновые кессоны; 3 – погруженные охлаждающие элементы; 4 – фланец примыкания холодильника к печи; 5 – воздушная камера; 6 – сливные воронки; 7 – разгрузочный бункер; 8 – рабочий люк; 9 – съемные секции для регулирования уровня кипящего слоя; 10 – люк донной загрузки
При этом горячий материал непосредственно из печей разгружают в желоб с циркулирующим оборотным раствором, в котором часть цинка и других компонентов быстро растворяется в серной кислоте. Таким образом, огарок предварительно не подготавливают, а классификации подвергают пульпу, содержащую в значительной мере уже выщелоченный материал.
Построенные в последние два десятилетия второй Усть-Каменогорский, Лениногорский и Алмалыкский цинковые заводы, а также заводы «Укрцинк» оснащены механическим и пневматическим транспортом для транспортирования сухого огарка. В частности, на втором Усть-Каменогорском заводе хорошо зарекомендовали себя в работе трубчатые транспортеры. Эти механизмы или, как их называют, шнек - трубы, просты по конструкции, имеют продолжительный срок службы, обеспечивают дополнительное охлаждение огарка и нормальные санитарно-гигиенические условия для обслуживающего персонала. Этим способом огарок перемещают внутри цеха. Далее его передают в цех выщелачивания ленточными транспортерами. На Лениногорском цинковом заводе успешно эксплуатируют пневматический транспорт огарка.
|
|
Классификация огарка
Необходимость классификации и выделения перед выщелачиванием тонких фракций огарка вызывается тем, что последние обладают большей реакционной способностью.
|
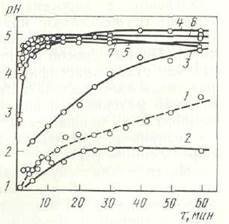
Так, с уменьшением размера частиц ускоряется растворение огарка в серной кислоте, быстрее и при меньшем избытке его (4-6% вместо обычных 15-20%) протекают процессы нейтрализации и гидролитической очистки растворов от примесей. На рис. 24 показан влияние крупности огарка на продолжительность растворения и скорость нейтрализации пульпы. Кроме то го, как указывалось выше, при выщелачивании крупных фракций образуется большое количество «песков», затрудняющих эксплуатацию оборудования и магистралей. В связи с этим в мировой практике наметилась вполне определенная тенденция к снижению крупности огарка направляемого на выщелачивание.
Для условий Усть-Каменогорского свинцово-цинкового комбината установлена оптимальная крупность огарка 0,15 мм. При этой крупности в остатке от выщелачивания огарка содержится наименьшее количество «песков», а максимальный размер их частиц ниже, чем при выщелачивании более крупных фракций. Это наглядно видно из приведенных ниже данных:
|
|
Крупность огарка до выщелачива -ния, мм | -5+1 | -1+0,25 | -0,25+0,15 | -0,15 |
Содержание песков в остатке, % | 59,3 | 49,6 | 69,2 | 40,0 |
Максимальный размер частиц песков, мм | 5 | 1 | 0,25 | 0,15 |
В гидрометаллургии цинка применяют два способа классификации огарка - сухой и гидравлический. При сухой классификации огарок просеивают на вибрационных грохотах через металлические сита или подвергают разделению в аэросепараторах. При гидравлическом способе осуществляют классификацию пульпы (смесь огарка с кислым раствором) в различных классификаторах. Первый способ имеет несомненные преимущества, так как сухая классификация, особенно в аэросепараторах, позволяет выделить более тонкие фракции обожженного материала и направить в те стадии выщелачивания, где их ценные свойства лучше всего используются (например, для нейтрализации и доводки пульпы до определенного рН).
На гидравлическую классификацию поступает пульпа, в которой наиболее топкие фракции огарка уже выщелочены во время контакта горячего материала с кислым раствором и, естественно, использованы уже быть не могут.
|
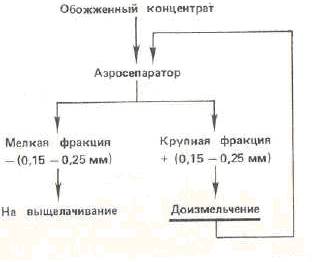
Гидравлическая классификация сложилась исторически на старых отечественных заводах, где она была связана с гидравлическим транспортированием огарка и непрерывным способом выщелачивания.
Сухая классификация удобна еще и тем, что дает надежную гарантию качества готового огарка по крупности зерна и не связана с определенным способом выщелачивания - периодическим или непрерывным, Она обеспечивает возможность точного весового учета огарка.
Сухая классификация.
С переходом на обжиг в кипящем слое разрыв в содержании сульфидного цинка в различных фракциях огарка значительно уменьшился. Поэтому выделяемую в процессе сухой классификации крупную фракцию на повторный обжиг не направляют, а доизмельчают в шаровых мельницах и передают вместе с основным продуктом на выщелачивание. За рубежом распространен способ сухой классификации на виброситах, а также в аэросепараторах. Вибросита применяли до 1960 г. и на втором Усть-Каменогорском заводе. Однако ввиду быстрого износа топких сеток с малым размером ячейки и большого пылеобразования этот метод был заменен аэросепарацией.
Схема сухой классификации огарка на аэросепараторах приведена на рис. 25. В качестве основного агрегата используют аэросепаратор с наружным диаметром 2,5 м (рис. 26), который состоит из внешнего и внутреннего концентрически расположенных конусов. По оси бонуса проходит пустотелый вал с приемным диском и закрепленным в верхней части лопастным вентиляторным ротором. При вращении ротора со скоростью 280-320 об/мин создается восходящий воздушный поток, циркулирующий в пространстве между наружным и внутренним конусами.
Рис. 26. Аэросепаратор:
1 – полый вал; 2 – регулировочные задвижки; 3 - диск
Материал, подлежащий классификации, попадает по пустотелому валу на приемный диск и рассеивается центробежной силой в зоне воздушного потока. Мелкая фракция выносится воздушным потоком во внешний конус сепаратора, откуда ее выгружают через шлюзовой затвор и направляют в цех выщелачивания. Крупная фракция остается во внутреннем конусе и поступает из него в шаровую мельницу сухого помола. После измельчения в мельнице огарок вновь направляют на аэросепарацию вместе с исходным материалом. Таким образом, мельница работает в замкнутом цикле с классификатором.
В зависимости от характера классифицируемого материала аэросепараторы регулируют на разделение по граничному зерну крупностью 0,15-0,25 мм. Метод аэросепарации позволяет получать в готовом продукте 90-95% фракций огарка требуемой крупности, т.е. -0,15 или -0,25 мм. Он также практически исключает пылеобразование и улучшает условия труда рабочих классификационного отделения, так как выделяющаяся при этом пыль отсасывается и улавливается в рукавных фильтрах. Весь выходящий из печи огарок в обязательном порядке подвергают аэросепарации. Циклонную пыль в некоторых случаях (при отсутствии комков) направляют непосредственно на выщелачивание.
Гидравлическая классификация.
Как следует из схемы, приведенной на рис. 27, гидравлическая классификация продуктов обжига сочетается с их частичным выщелачиванием. Горячий огарок из печи КС без предварительного охлаждения выгружают в желоб с циркулирующим кислым раствором. Образующаяся при этом пульпа подается на деревянные или из кислотостойкой стали сита с шириной щели 3-5 мм. На ситах проводится первая грубая классификация пульпы с целью выделения комков огарка величиной 3-5 мм. Для разрушения комков последние обрабатывают одним из двух способов: измельчением (Челябинский завод) или выщелачиванием в отработанном электролите с кислотностью 120-150 г/л (первый Усть-Каменогорский завод). В обоих случаях измельченные комки возвращают на сита.
Прошедшую через сито пульпу передают далее на первичную стадию классификации в гидроциклонах для выделения тонких фракций огарка крупностью не более 0,2-0,3 мм. Для этой цели используют гидроциклоны (рис. 28) марки ГЦ-500 с внутренним диаметром 500 и высотой 1700 мм, футерованные каменным литьем. В зависимости от отношения ж: т пульпы диаметр песковой насадки находится в пределах 22-34 мм.
Рис. 27. Схема гидравлической классификации огарка
|
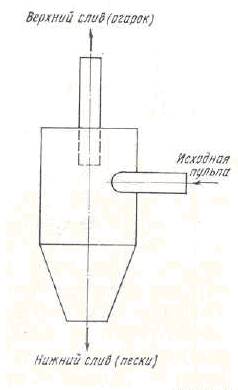
Гидроциклон работает следующим образом. В его верхнюю часть через входное отверстие тангенциально к окружности насосом подают пульпу. За счет вращения пульпы внутри аппарата под действием центробежных сил крупные частицы твердой части пульпы прижимаются к поверхности, теряют скорость и сползают к нижнему выпускному отверстию. Тонкие частицы выносятся потоком пульпы через верхнее сливное отверстие. Производительность гидроциклонов составляет 45-60 м3/ч.
Таким образом, в гидроциклонах осуществляют основную классификацию обожженного продукта с направлением верхнего слива, содержащего тонкие фракции огарка, в цех выщелачивания и выделением песковой части (нижний слив) для дальнейшей обработки кислыми растворами.
В первых установках гидравлической классификации гидроциклоны не применяли; пески после первой стадии классификации в нейтральных конусах перед выщелачиванием предварительно измельчали в галечных мельницах. Однако вскоре было обнаружено, что при этом зерна песков переизмельчались, а внутреннее ядро, состоящие в основном из необожженных сульфидов, разрушалось. Частицы сульфидного цинка при последующей классификации переходили в слив, снижая извлечение металла в основном цикле выщелачивания.
При обработке песков серной кислотой без предварительного их измельчения в мельницах растворение зерен огарка начинается с поверхности, внутреннее сульфидное ядро остается почти без изменений. Подбирая концентрацию кислоты и продолжительность перемешивания, можно так отрегулировать процесс, что в раствор будет переходить цинк в основном из обожженной наружной части зерен, а уменьшенные в размерах пески будут выведены из процесса при последующей класса фикации. Как показал многолетний опыт работы предприятий, такой способ обработки песков вполне себя оправдал.
Рис. 29. Конусный классификатор
Выщелачивание песковой фракции проводят в чанах с пневматическим перемешиванием (пачуках) отработанным электролитом при кислотности 10-25 г/л, после чего пульпу классифицируют. Классификатор (рис. 29) представляет собой конус, изготовленный из дерева и покрытый изнутри листовым свинцом или из нержавеющей стали. Вокруг бортов конуса имеется кольцевой желоб. Внутри конуса у разгрузочного отверстия установлена диафрагма для предупреждая образования воронки при выпуске песков. Разгрузочное отверстие снабжено дисковым затвором. Изменяя высоту слоя песков в конусе, можно в известных пределах получать желаемую степень классификации огарка.
Верхний слив конусов возвращают на смыв огарка у печей КС, а нижний (пески) вновь направляют на выщелачивание в пачуках, но при более высокой кислотности -25-30 г/л. Обработанные серной кислотой пески подвергают повторной классификации в конусах, из которых верхний слив также поступает на смыв огарка, а пески обезвоживают в дренажном ящике или спиральном классификаторе и направляют на вельцевание. Содержание общего цинка в конечных песках не должно превышать 14, а цинка, растворимого в слабой серной кислоте, 7%.
Сопоставляя практику и показатели работы сухой и гидравлической классификации, можно отметить, что первый способ дает возможность, применяя аэросепарацию, выделить для выщелачивания более тонкие фракции огарка крупностью не более 0,15 мм и фактически не иметь оборотного продукта. Кроме того, способ более прост в обслуживании. Гидравлическая классификация требует тщательного наблюдения за циркуляцией растворов, работой гидроциклонов и конусов и связана с получением оборотного продукта - песков, которые необходимо направлять на вельцевание.
На некоторых зарубежных предприятиях при хорошо налаженном процессе обжига и получении обожженного продукта с низким содержанием сульфидной серы предпочитают не проводить классификацию огарка, а весь материал, выходящий из печи, измельчают в шаровой мельнице сухого помола до нужной крупности и направляют непосредственно на выщелачивание.