Рис. 38 ЛАЧХ дроссельного ГП
Величина kПР выбирается исходя из заданных запасов устойчивости по фазе не менее Df=500 и по амплитуде DL=6дБ.
После замыкания привода обратной связью получим частотную характеристику замкнутого привода, которую на основании приведённой характеристики можно приближённо представить в виде:
![]() |
где: постоянная времени ТПР определяется по частоте, на которой сдвиг по фазе замкнутого привода равен 900. При наличии большой разницы сопряжённых частот 1/ТПР и 1/ТГП вторым колебательным звеном можно пренебречь и приближённое представление замкнутого привода в частотной области будет иметь вид:
![]() |
О переходном процессе привода.
При отработке приводом входных сигналов параметры привода выходят за область линейности характеристик. Для корректного описания его частотных характеристик необходимо в структурную схему включить нелинейное звено, как это показано на рисунке.
![]() |
В данном случае нелинейным звеном является ограничение по перемещению золотника. Для ЭГП это ограничение начинает работать при входных сигналах превышающих уже 2о…3о. С учётом ограничения по перемещению золотника характер переходного процесса привода будет иметь вид, представленный на графике:
|
|
![]() |
|
|

Рис. 39 Переходной процесс перемещения органа управления
После выхода золотника на упор (t=t1) выходной вал привода движется с постоянной скоростью до t=t2. Для определения реальных частотных характеристик привода в этом случае целесообразно использовать метод гармонической линеаризации нелинейности. Можно также провести численное решение нелинейных дифференциальных уравнений привода.
2.4.6. Описание работы газогидравлического привода общей системой дифференциальных уравнений с учётом источника энергии.
1. Дифференциальное уравнение работы ТТГГ – уравнение расходов:
![]() |
где:
массовый расход газа через торцовый зазор между блоком цилиндров и распределителем газа:
массовый расход газа через кольцевой зазор в плунжерной паре:
2. Уравнение нагрузки на валу ГМ:
![]() |
3.
Уравнение расходов жидкости в гидроприводе:
![]() |
где:
![]() |
4. Баланс сил на клапане:
![]() |
5.Уравнение расходов в РМ:
![]() |
6. Уравнение сил на поршне
![]() |
7.Уравнение действия отрицательной обратной связи:
Структурная схема газогидравлического привода представлена на рис. 40.
Рис. 40 Структурная схема газогидравлического привода с первичным источником питания и преобразователем энергии
|
|
3. ЭЛЕКТРОПНЕВМАТИЧЕСКИЙ ПРИВОД.
Схема. Принцип действия.
В поршневом приводе в качестве пневматического двигателя (ПД) используется силовой цилиндр. Входной газовый поток распределяется между полостями двигателя при помощи дроссельного распределительного устройства, например, струйной трубки, которая в зависимости от расположения по отношению к приёмным окнам обеспечивает перепад давления на поршне ПД.
Функциональная схема ПД имеет вид (рис. 41):
![]() |
На схеме обозначено: ИСГ – источник сжатого газа, АПМ – агрегаты пневмомагистрали, ПСУ – преобразующее и суммирующее устройство, УМ – усилитель мощности, ЭМП – электромеханический преобразователь, ПРУ – пневматическое распределительное устройство, ПД – пневматический двигатель, МП – механическая передача, НАГ – нагрузка, ПОС – потенциометр обратной связи, КОС – корректирующая обратная связь.
Каждый из обозначенных элементов привода является функционально завершённым. Приведённая функциональная схема соответствует автономному приводу, т.е. приводу с источником энергии.
Задача привода – преобразование входного сигнала Uвх в перемещение выходного вала d. На схеме обозначены промежуточные координаты: DU – сигнал ошибки контура привода, Iу – ток управления обмоток ЭМП, a - угол отклонения якоря ЭМП, Gi – расходы в полости пнематического двигателя, Y - перемещение штока поршня, Uос – напряжение обратной связи. Энергетический канал характеризуется двумя параметрами: Рz – давлением на входе в привод и Рб – давлением в баллоне.
Различие в типах пневматических приводов определяется конструктивным исполнением ПД и свойствами ПРУ. Ниже будем рассматривать только привод с ПРУ типа струйная трубка. Однако, приведённые модели, последовательность проектирования и основные рекомендации могут быть применены для поршневых приводов с произвольными дроссельными распределительными устройствами (сопло-заслонка, золотник) при соответствующих доработках модели.
Принципиальная схема пневматического привода со струйной трубкой приводится на рис. 42.
|

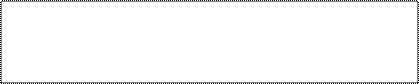

|
|
|
|

|
|
|
|
|
|
|
![]() |
Дроссельное ПРУ – это пневматический мост, состоящий из четырёх пневматических дросселей (сопротивлений), определяемых своими проходными сечениями Aij. В одну диагональ моста включено давление питания Рz, а в другую – полости ПД. Входной поток сжатого газа Gz проходит по дросселям ПРУ как показано на схеме, создавая различные давления Р1 и Р2 в полостях ПД. Управление давлениями в полостях ПД осуществляется путём изменения величин проходных сечений ПРУ.
Примечание: в дальнейшем в тексте лекций будут использоваться обозначения площадей и потоков втекания с индексами «1» (А1, G1), а площадей и потоков вытекания с индексами “2” (А2, G2).
Конструктивные особенности привода определяются конструктивными особенностями ПРУ и ПД. Преобразующее и суммирующее устройство (ПСУ) и УМ обычно выполняются в виде отдельных блоков из серийных элементов. Датчик обратной связи для приводов кратковременного действия выполняется в виде потенциометра, для приводов с длительным временем работы применяются бесконтактные, например, индукционные датчики. Механическая передача для поршневых ПД выполняется, как правило, рычажной. Если ПД достаточно разнообразны по способам преобразования энергии сжатого газа, то применение ПРУ в пневматических приводах ограничивается ПРУ дроссельного типа. Объёмного типа приводы не применяются из-за сложности реализации компрессоров переменной производительности.
Основные конструктивные параметры системы – это перечень параметров, необходимых для определения основных характеристик, которые нужны для выбора привода или оценки альтернативных вариантов приводов при техническом решении задачи. Для различных технических устройств и приводов, в том числе, перечень основных конструктивных параметров может быть различным.
|
|
Рассмотрим агрегат, состоящий из ПД, ПРУ и ЭМП. Такая совокупность является конструктивно и функционально завершённым устройством и часто называется рулевой машиной. Данному агрегату присущи основные технические характеристики, которые связаны с его конструктивными параметрами и параметрами рабочего тела и определяют пригодность РМ для выполнения той или иной технической задачи.
Основными конструктивными параметрами являются для:
ПД:
- АП – эффективная площадь поршня, площадь на которую действует давление,
- Ymax – максимальный ход поршня,
- rкп – радиус кинематической передачи.
|
- - максималь- максимальная площадь втекания,
-
|
- - максимальная площадь вытекания,
-
- где dCB – внутренний диаметр струйной трубки, dП – диаметр приёмного окна.
УМ:
- kU – коэффициент усиления по напряжению.
Приведённый перечень параметров значительно уже полного перечня параметров, определяемого математической моделью привода и его рабочим чертежом, но он является достаточным в смысле поставленной задачи выбора привода.
Кроме указанных выше параметров, при проектировании всегда имеется набор параметров, которые в меньшей степени зависят от проектировщика. К ним относятся:
- параметры рабочего тела:
отношение теплоёмкостей k,
газовая постоянная R,
температура газа Tz,
давление газа на выходе привода Ра,
максимальный ход штока Ymax (обычно выбирается в диапазоне 3…35 мм),
коэффициенты расхода сечений ПРУ - m =0,6…0,8,
коэффициенты восстановления давлений kP =0,8,
отношение площадей вытекания и втекания kA = A2m/A1m.
Основными техническими характеристиками (ОТХ) привода являются:
- максимальный момент на валу привода - Mmax,
- максимальная скорость выходного вала - Wmax,
|
|
- максимальный расход газа - Gz,
- максимальная мощность привода - Nmax.
3.1. Общие технические характеристики
ОТХ определяются следующими соотношениями:
![]() |
Из приведённой схемы ясно выражение для Mmax и Wmax. Усилие F на штоке создаётся перепадом давления (Р1 - Р2) – F = AП (Р1 - Р2), а момент относительно точки «О» будет M=FrKП=kPPzAПrKП.
Максимальный массовый расход газа определяется соотношением для сверхкритического истечения через сопло:
![]() |
Или объёмный расход, приведённый к нормальным условиям (в нормальных метрах):
![]() |
Рассматривая совместно выражения для расхода Gz, максимального момента Mmax и скорости Wmax, несложно получить зависимость мощности привода в форме:
![]() |
Полученная зависимость достаточно хорошо показывает влияние основных параметров на максимальную мощность пневматического поршневого привода с дроссельным распределителем.
По ОТХ проводится сравнение привода с альтернативными вариантами и принимается решение о возможности применения рассматриваемого привода в САУ. При положительном решении производится детальное уточнение характеристик привода.
3.2. Сжатый газ как рабочее тело газового привода.
При описании процессов в газовом приводе принято считать газ идеальным, т. е. подчиняющимся закону Бойля-Мариотта.
Сжатый газ характеризуется следующими параметрами:
- давлением, как отношение силы F ударов молекул к площади А
- объёмом V, который занимает сжатый газ,
- температурой Т,
- массой m.
Указанные параметры газа взаимоувязаны уравнением состояния для идеального газа:
где R – удельная газовая постоянная.
Из уравнения состояния следует соотношение для плотности газа
![]() |
Из уравнения состояния также следует связь массового секундного расхода газа с объёмным расходом:
А величины давления и температуры обычно принимаются нормальными, т. е. Р0=0,1 МПа и Т0=293оК.
Энергетическое состояние газа описывается первым законом термодинамики:
где:
![]() |
Q – теплота, подведённая к газу, U – внутренняя энергия, L – работа, совершаемая газом. С некоторыми допущениями уравнение первого закона термодинамики можно использовать в дифференциальной форме:
![]() |
При определении расходов газа для описания работы пневматических устройств используют зависимости массового секундного расхода газа. Особенностью газовых систем является то, что при изменении режима течения газа со сверхкритического на докритический изменяется форма зависимости массового расхода от давлений до и после дросселя. Если Р1 – давление перед дросселем, а Р2 – давление за дросселем, то критическое соотношение давлений определяется выражением:
![]() |
Из приведённого соотношения видно, что при отличии в давлениях до и после дросселя в два раза происходит изменение режимов течения газа.
При сверхкритическом режиме течения, т. е. при расход через дроссель сечением А определяется по формуле:
|
|
При докритическом режиме течения, т.е. когда расход
через дроссель сечением А определяется по формуле:
![]() |
В этих уравнениях:
![]() |
![]() |
3.3. Пневматические распределительные устройства.
Выше уже говорилось, что ПРУ является в приводе конечным каскадом усилителя мощности, а также указывалось, что в пневматическом приводе, как правило, применяются дроссельные распределительные устройства.
Дроссельное ПРУ – это пневматический мост, состоящий их 4-х пневматических дросселей (сопротивлений) Aij, в одну диагональ которого подключено давление питания Рz, а в другую – полости пневматического двигателя (ПД). Входной поток сжатого газа Gz проходит по дросселям ПРУ, как показано в схеме, создавая различные давления Р1 и Р2 в полостях ПД.
| |||||||||||
![]() | ![]() | ||||||||||
![]() | |||||||||||
![]() | ![]() | ||||||||||
|
|
|
|

|
|
|
|
|
|
|











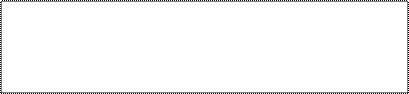



На схеме обозначено: Р1 и Р2 – давления в полостях ПД, А11 и А12 – дроссели втекания, А21 и А22 – дроссели вытекания, G11 и G12 – расходы втекания, G21 и G22 – расходы вытекания, G1 и G2 – расходы газа в полости ПД.
Управление ПД осуществляется путём изменения проходных сечений дросселей ПРУ. Проходные сечения образуются между торцом струйной трубки и приёмными окнами.
|
|







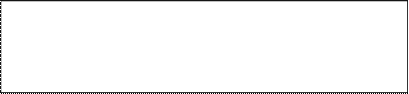
Исходной схемой для определения характеристик ПРУ дроссельная схема, представленная выше.
Входным сигналом ПРУ является х – перемещение торца трубки, в соответствии с чем изменяются все проходные сечения Аij. Выходным сигналом ПРУ являются расходы G1 и G2 или их разность DG = G1 - G2. Вывод зависимости F (x, DG)=0 даст обобщённую характеристику ПРУ.
Для вывода уравнения задано: параметры газа k, R,Tz, Pz, Pa, зависимость Аij=f(x), схема ПРУ.
Необходимо определить зависимость: DG = f(x).
Исходным уравнением является уравнение неразрывности газового потока, составленное для узловых точек схемы:
![]() |
Принятые допущения:
1.
![]() |
Режим течения через все дроссели сверхкритический, т.е.
2. Температуры газа постоянны и равны входной температуре:
![]() |
3. Проходные сечения дросселей линейно зависят от входного сигнала:
![]() |
4. Давление Р1 и Р2 меняются линейно:
Параметры с индексом «0» называются равновесными параметрами распределителя и являются координатами точки, в окрестности которой проводится линеаризация полученных уравнений. Равновесные параметры определяются при среднем положении струйной трубки по отношению к приёмным окнам (a=0).
Раскроем с учётом приведённых допущений уравнения неразрывности расходов:
![]() |
![]() |
В последние уравнения подставим выражения для давлений и площадей:
![]() |
Вычтя из первого уравнения второе после преобразований, получим:
В компактной форме уравнение ПРУ можно записать его механическую характеристику:
![]() |
3.4. Уравнение движения поршневого пневматического двигателя (ПД).
![]() |
ПД преобразует энергию сжатого газа в механическую энергию. ПД работает на принципе попеременного наполнения и опорожнения своих полостей сжатым газом. Расчётная схема ПД представлена на рисунке выше.
Входным сигналом ПД являются расходы
| |||
| |||
Входной величиной является F – усилие и скорость штока -
Под уравнением ПД понимается зависимость
![]() |
Для вывода уравнения заданы:
- параметры сжатого газа k, R, T, PZ, Pa;
- кинематические параметры ПД АП – площадь поршня, уm – максимальный ход штока, rKH – радиус звена между штоком и органом управления.
Принятые допущения:
1.
![]() |
Температуры газа в полостях ПД и равны входной температуре
2. Давления в полостях Р1 и Р2 меняются линейно
![]() |
Параметры с индексом «0» называются равновесными параметрами ПД и являются координатами точки механической характеристики, в окрестности которой проводится линеаризация полученных уравнений.
![]() |
Усилие на штоке ПД можно определить на основании уравнения состояния газа для каждой из полостей ПД:
Для связи выходных параметров ПД с расходами газа следует при принятых допущениях использовать уравнение состояние газа, действующее в каждой полости:
Из уравнения состояния для расхода после дифференцирования, получим:
Связь расходов с выходными параметрами после дифференцирования по переменным Рi, Vi для каждой полости имеет вид:
Для поршневого ПД зависимость объёмов Vi от перемещения описывается простым соотношением:
![]() |
|
Подставляя в уравнения для расходов выражения для давлений Рi и объёмов Vi и вычитая из первого уравнения второе, после преобразований, получим уравнение ПД:
![]() |
Полученное уравнение является искомым, так как усилие на штоке есть F=AПРД. Из уравнения следует, что подведённый в полости ПД газ расходуется на заполнение (опорожнение) полости при движении поршня с постоянной скоростью и на изменение давления в полости.
Используя радиус кинематической передачи rKH, можно характеристики ПД привести к выходному валу привода на основании простейших кинематических соотношений.
3.5. Элементы контура пневматического привода(ПП).
Усилитель мощности в контуре ПП выполняет те же функции, что и в гидравлическом приводе. Передаточная функция УМ была рассмотрена в разделе элементов гидравлического привода. Следует отметить, что и в ПП УМ является практически основным элементом, который позволяет просто изменять коэффициент усиления контура привода, добиваясь заданные устойчивость и качество регулирования.
Электромеханический преобразователь (ЭМП) в ПП также служит для преобразования электрических сигналов системы управления в перемещение струйной трубки. Передаточная функция ЭМП рассматривалась ранее.
Математическая модель поршневого пневматического привода.
Для анализа частотных характеристик рассмотрим систему уравнений привода в операторной форме. Уравнения составлены для всех элементов функциональной схемы привода.
![]() |
В уравнениях часть параметров привода определяется при проектировании, а часть определяются для конкретных условий: kOC=Uпит/dm, Ry – определяется из паспортных данных ЭМП (для транзисторных усилителей постоянного тока Ry =100…500 Ом), Ту=0,01…0,008 с – определяется характеристиками УМ, сЭ/km=amax/Imax – определяется выбранным УМ и ЭМП, V0=Апуmax – равновесный объём полостей ПД, Р0=(0,3…0,4)РZ – равновесное давление в полостях ПД, kПР и kGP – определяются типом ПРУ, ku – коэффициент усиления усилителя по напряжению – выставляется при настройке привода по запасам устойчивости по амплитуде не менее 6 дб и по фазе не менее 50о, ТЭ – постоянная времени механической части ЭМП и ПРУ, которая имеет, как правило, значения (4…6)10-4с, xЭ =0,2…0,4 – показатель демпфирования в механической части ЭМП и ПРУ, lстр – длина струйной трубки.
При описании ПП необходимо учитывать трение в выходном звене. Трение определяется взаимодействием поршня и цилиндра, цилиндра и штока, трением в кинематике, трением в нагрузке. Трение существенно влияет на динамические характеристики ПП, позволяет в несколько раз увеличивать добротность привода при обеспечении заданных запасов устойчивости.
Ранее рассматривалось трение и приводилось уравнение
![]() |
где kBT – коэффициент вязкого трения, МТ – сухое трение в подвижной системе руля. В итоге уравнение нагрузки на валу привода примет вид:
Cледует отметить, что при описании работы гидропривода трение опускалось, так как жидкость при перетекании через дроссели имеет высокую степень демпфирования, значительно превышающее влияние трения. В случае пневматического привода трение следует учитывать. Для упрощения расчётов проводят гармоническую линеаризацию последнего уравнения нагрузки, которое принимает вид:
![]() |
которое является добавкой к вязкому демпфированию.
3.6. Структурная схема пневматического привода.
Как и в случае гидропривода, ограничимся рассмотрением структурной схемы исполнительной части привода.
Структурная схема исполнительной части привода может быть получена на основании уравнений ПРУ, ПД и нагрузки. Рассмотрим соответствующие уравнения:
На основании приведённых уравнений можно представить структурную схему участка прямой цепи привода. Точки суммирования обратных связей по перепаду давления и скорости штока можно поменять местами.
![]() |
Параметры структурной схемы определяются через конструктивные параметры и параметры сжатого газа по соотношениям, полученным на основании приведённой выше системы уравнений привода:
Постоянная времени ТП является основной постоянной времени, характеризующей инерционность ПП. Можно показать, что она приближённо определяется как отношение перемещения ymax к максимальной скорости штока поршня
После несложных преобразований получим структурную схему ПП в более компактной форме с учётом безинерционности УМ и ЭМП
![]() |
Полученная структурная схема достаточно хорошо отражает основные свойства ПП при очевидной простоте. Схема может быть принята за основу для анализа характеристик привода. В некоторых случаях необходимо учесть запаздывание сигнала в усилителе мощности, а также основные нелинейные свойства привода (трение, ограничение по перемещению струйной трубки).
Структурная схема ПП при kШ=0 и kBT=0.
Рассмотрим участок структурной схемы ПП при наличии только инерционной нагрузки (kШ=0 и kBT=0):
На основании приведённой схемы для замкнутого контура получаем:
![]() |
Полученное выражение передаточной функции привода показывает, что в рассматриваемом случае ПП описывается колебательным звеном с астатизмом первого порядка.
Структурная схема силового ДПП в общем случае.
В общем случае нагружения, т.е. при kШ¹0, kВТ¹0 и IН¹0, частотные характеристики и передаточную функцию привода можно получить на основании анализа логарифмических частотных характеристик. Для проведения анализа частотных характеристик вновь рассмотрим структурную схему ПП, ограничившись исполнительной частью.
Рассмотренный контур имеет третий порядок, что делает неоднозначным анализ свойств контура в общем случае без конкретных значений постоянных времени и коэффициента передачи. Для случая применения пневмопривода в рулевых приводах ЛА диапазоны изменения параметров контура имеют определённые границы, что позволяет анализировать его характеристики. Для анализа используем построение логарифмических частотных характеристик, только амплитудных и асимптотических. Ниже приводятся построения для приведённой выше структурной схемы с учётом глубокой отрицательной обратной связи.
![]() | |||||||||
|
|
| |||||||
![]() |
![]() ![]() ![]() ![]() ![]() ![]() ![]() ![]() ![]() ![]() | |||||||||
![]()
| |||||||||
![]() | |||||||||
|
|
При глубокой обратной связи замкнутая частотная характеристика идёт по нижней из характеристик. Для построения необходимо строить прямую передаточную характеристику и 1/Woc, имея в виду, что числитель определяется соотношением
В результате построений мы как и в случае гидропривода можем заменить исходную структурную схему разомкнутого привода приближённым произведением двух звеньев
1.1.3. Приводы газогидравлические с вытеснительной системой подачи рабочей жидкости
Приводы газогидравлические с вытеснительной системой подачи рабочей жидкости в рулевые машины представляются весьма перспективными. В отличие от приводов, работающих по замкнутому циклу, жидкость из полости слива рулевой машины сбрасывается за борт летательного аппарата (рис. 1.4.). Достоинством такой схемы является простота конструкции, а следовательно, и высокая надежность.
Рис. 1.4. Принципиальная схема газогидравлического привода
Однократное использование рабочей жидкости требует увеличения ее запаса. Однако непрерывное уменьшение массы в процессе работы привода позволяет учитывать в суммарной массе рулевого только ее часть (30 - 60%). Вытеснители, служащие для преобразования энергии горячих газов в энергию потока жидкости, выполняются с раздельными корпусами и в едином корпусе[2]. Устройство для вытеснения может быть поршневым и с разделительной диафрагмой. В связи с большим разбросом параметров газа газогенератора применяются автоматические устройства для регулирования (стабилизации) давления, расхода. Определенный интерес представляют вытеснительные устройства, совмещающие функцию подачи рабочей жидкости в приводе с креновым устройством. Конструктивная схема газогидравлического источника питания представлена на рис. 1.5.
Рис. 1.5. Конструктивная схема газогидравлического источника питания
1. Газогенератор, 2. Пороховой заряд, 3. Теплозащитное покрытие, 4. Фильтр газовый, 5. Инициатор, 6. Клапан, 7. Мембрана, 8. Бак, 9. Рабочая жидкость, 10. Фильтр гидравлический, 11. Навеска
Как видно из рис. 1.5. основными элементамигазогидравлического источника питания являются газогенератор, вытеснитель и клапан.
Вытеснитель предназначен для преобразования давления газа в давление рабочей жидкости и для её хранения. На практике используются вытеснители двух типов: поршневые и диафрагменные. Более перспективными являются вытеснители сферического типа с эластичными диафрагмами. Основные их достоинства: компактность и простота конструкции.
Масса вытеснителя складывается из массы рабочей жидкости и массы конструкции:
Масса рабочей жидкости:
где – коэффициент использования рабочей жидкости;
- давление нагнетания рабочей жидкости;
- плотность рабочей жидкости.
Масса конструкции вытеснителя складывается из массы баллона, массы диафрагмы и массы прочих элементов конструкции (штуцеров, мест крепления и др.). В формуле масса конструкции вытеснителя, масса диафрагмы и других элементов учтены коэффициентом конструкции. Тогда формулу массы конструкции вытеснителя можно представить виде:
,
где - коэффициент конструкции вытеснителя;
- плотность металла корпуса;
- площадь поверхности вытеснителя;
- толщина стенки вытеснителя. Эти параметры определяются по формулам:
где ,
- объем и диаметр вытеснителя;
- предел прочности материала вытеснителя.
В итоге с учётом формул масса вытеснителя:
, (1)
где
Как видно из формулы (1) масса вытеснительного источника питания зависит от мощности, времени работы привода, плотности жидкости.
1.3.3. Построение областей минимальных масс приводов управления поворотным соплом
При проектировании приводов для новых разработчиков приводов возникает задача выбора схемы привода, имеющего минимальный вес при широком сочетании возможных мощностей и времен работы.
В данном разделе построена область минимальных масс приводов с вытеснительным источником питания и аксиально-поршневым моторнасосным агрегатом по методике, приведенной в [9].
Как следует из данных натурных испытаний ЛА, реальный интегральный ход штока рулевых машин не превышает 10—15% от максимально возможного хода привода за полное время работы двигательной установки. В связи с этим фактом вытеснительный источник питания может быть использован в мощных (> 0,5 кВт) рулевых приводах для достаточно длительного времени работы (30 — 100 с). При этом по своим энергомассовым показателям, а также простоте использования, вытеснительный источник питания становится конкурентоспособным другим типам источников питания, работающих по замкнутой схеме циркуляции жидкости. При наличии информации о реальном движении объекта управления, то есть о пути движения штока рулевой машины, выражение для определения значений коэффициента относительного интегрального хода штока рулевой машины можно записать в следующем виде:
![]() |
,
где - максимально возможный путь движения штока рулевой машины,
- максимальная скорость штока, t- текущее значение,
- время работы привода.
При этом следует отметить, что в отличие от замкнутых источников питания, вытеснители работают по разомкнутой схеме. В работе [2] показано, что при уменьшении , границы применимости рулевых приводов с газогидравлическим вытеснителем расширяются и приближаются к границам использования приводов с высокоэкономичными аксиально-поршневыми моторнасосными агрегатами. Для того чтобы пояснить вышесказанное графически, рассмотрим энегомассовые характеристики приводов.
Уравнение границы в плоскости параметров N-tп при использовании равенства:
(1.5)
![]() |
Рис. 1.11 Зависимость мощности от времени при различных значениях интегрального хода штока, где ВИП – вытеснительный источник питания, АПМНА - аксиально-поршневой моторнасосный агрегат, t - время работы, N - мощность привода.
Как следует из рис. 1. 11, с уменьшением KL происходит существенное расширение границ применимости рулевых приводов с вытеснительным источником питания и приближение к области применения привода с аксиально-поршневыми моторнасосными агрегатами. Таким образом, использование информации об интегральном ходе штока рулевой машины позволяет наряду с упрощением конструкции и повышением надежности работы рулевого привода улучшить его энергомассовые показатели.
2.2. Разработка методики расчета газогидравлического источника питания рулевого привода управления поворотным соплом путем построения эпюры сопряжения располагаемой и потребной мощностей, а также с учетом зависимости для непроизводительного расхода рулевых машин от вязкости жидкости
2.2.1 Анализ диаграммы нагрузки поворотного управляющего сопла беспилотного летательного аппарата
Для беспилотных летательных аппаратов наиболее перспективно для пространственного управления вектором тяги относительно центра масс применение поворотных сопел с использованием эластичного шарнира – конструктивного узла связи между соплом и корпусом двигателя [15]. В этом случае для рулевого привода упругий элемент поворотного управляющего сопла, состоящий из пакета чередующихся стальных и каучуковых конических пластин, представляет собой преимущественно позиционную нагрузку при угловом перемещении раструба поворотного управляющего сопла относительно центра вращения (рис.2.4).
Исследованиями показано [15], что упругий элемент поворотного управляющего сопла характеризуется значительным шарнирным моментом и для управления требует применение мощных рулевых приводов. При этом, алгоритм управления положением проекции вектора тяги в плоскости тангажа «x» и рыскания «y» относительно продольной оси беспилотного летательного аппарата при использовании по одной рулевой машине в канале управления построен системой управления таким образом, что координаты проекции вектора тяги не выходят за пределы окружности в соответствии с соотношением командных сигналов[2]:
где ,- сигнал по каналу тангажа,
- сигнал по каналу крена.
Таким образом, независимо от направления движения проекции вектора тяги суммарная максимальная нагрузка, действующая со стороны поворотного управляющего сопла на рулевую машину, не превышает нагрузки действующей на одну рулевую машину при отклонении поворотного управляющего сопла на максимальный угол по каналу «x» или «y» и в координатной плоскости представляет окружность радиусом F.
Рис. 2.4Поворотное сопло с использованием эластичного шарнира, где 1- днище, 2- упругий чехол, 3 – упругий элемент, 4 – подвижное сопло, 5 – пакет термоэрозионностойких элементов, 6 – несущая оболочка подвижного сопла, 7 – рулевая машина.
С учётом представляемых данных разработчиками системы управления по результатам моделирования возмущённого движения ЛА о 10…12% энергетической загрузке рулевого привода в течение полного времени работы (1…1.5 мин) двигательной установки [2], целесообразно в качестве источника энергии рулевых машин использовать газогидравлический источник питания, состоящий из твёрдотопливного газогенератора и вытеснительной системы подачи рабочей жидкости - вытеснительный пороховой аккумулятор давления. При работе с нагрузкой в виде поворотного управляющего сопла указанный привод имеет значительный резерв энергетических ресурсов, реализация которых позволит существенно улучшить энергомассовые показатели источника энергии и привода в целом.
Сущность отмеченных энергетических резервов заключается в том, что располагаемая мощность привода при одновременном движении двух рулевых машин превышает требуемую со стороны поворотного управляющего сопла мощность за счёт принятого в практике проектирования расчёта поверхности горения заряда газогенератора из условия потребления рабочей жидкости двумя рулевыми машинами под минимальным давлением Р0 в гидросистеме с обеспечением максимальных скорости движения V и располагаемого усилия F:
Избыточная мощность проявляется при движении проекции вектора тяги в плоскости управления в направлении отличном от базовых: «x» или «y». Избыток мощности рассеивается в газовом клапане – регуляторе давления в виде сброса газа через проходное сечение клапана и в гидроусилителе рулевой машины в виде нагрева дроссельных элементов протекающей через золотник жидкостью.
Анализ располагаемых сил и действующих нагрузок в плоскости управления показывает, что круговая диаграмма шарнирного момента поворотного управляющего сопла (позиционная нагрузка) оказывается вписанной в квадрат располагаемых сил при работе двух рулевых машин [2, 16] с точками касания, в которых рулевая машина крепится к раструбу поворотного сопла рис. 2.5
![]() |
Рис. 2.5 Круговая диаграмма шарнирного момента поворотного управляющего сопла,
где Fр,Vр - располагаемая сила и скорость рулевых машин соответственно, δ - угол поворотного управляющего сопла, Fтр,Vтр – требуемая сила и скорость рулевых машин соответственно
В этих точках касания располагаемая и действующая силы максимальны и равны друг другу при максимальном отклонения поворотного управляющего сопла. В остальных направлениях, когда перемещаются две рулевые машины одновременно, результирующая располагаемая сила, при наличии в гидросистеме постоянного давления питания, находящегося на минимальном уровне рабочей жидкости на входе в рулевые машины, превышают нагрузку со стороны поворотного управляющего сопла. Рассмотрим подробнее требуемые и располагаемые характеристики привода.
Требуемые характеристики:
- Требуемая характеристика скоростей для двух рулевых машин (круг см. рис. 2.5).
Проекция требуемой скорости на ось х и y соответственно:
Суммарная скорость рулевых машин:
- Требуемая характеристика сил для двух рулевых машин (круг см. рис 2.5):
- Требуемая характеристика мощностей для двух рулевых машин (круг см. рис 2.5):
Располагаемые характеристики:
- Располагаемая характеристика скоростей для двух рулевых машин (квадрат см. рис. 2.5).:
- в диапазоне a =0…45º
- в диапазоне a =45…90º
- Располагаемая характеристика сил для двух рулевых машин (квадрат см. рис. 2.5):