Виділяють наступні типи дефектів (рис. 7.17):
· лінійна дислокація, що проросла в епітаксиальний шар (1);
· дефекти, що зароджуються на домішкових преципітатах, розташованих на поверхні підкладки (2);
· домішкові преципітати, що виникли під час росту епітаксиального шару (3);
· горбки на поверхні, що виникають через незадовільні умови процесу або поганого вихідного стану поверхні (4);
· дефекти впакування, що проросли в епітаксиальний шар (5).
![]() |
Рис. 7.17. Типи дефектів епітаксіальних плівок |
Причина появи технології виготовлення епітаксіальних плівок і їхні переваги. Причиною появи епітаксіальної технології послужила необхідність удосконалювання процесу виготовлення біполярних транзисторів. Ці прилади звичайно формуються в обсязі напівпровідникової підкладки з більшим питомим опором r, який визначається високою напругою пробою база-колектор Uб-к.
З іншого боку, високі значення r приводять до збільшення потужності, що розсіюється в напівпровідниковій підкладці, і зменшенню коефіцієнта підсилення транзистора на високих частотах. З метою розв’язання цього протиріччя була розроблена технологія одержання напівпровідникових шарів з високим опором на підкладці з низьким опором.
|
|
У цей час при виготовленні інтегральних схем використовуються епітаксіальні шари з низьким опором із протилежним щодо підкладки типом провідності. Утворений при цьому p-n перехід служить для електричної ізоляції сусідніх транзисторів, а високолегований n+ дифузійний шар використовується як колекторний контакт.
Шари, синтезовані по епітаксіальній технології, мають наступні переваги:
· широка область зміни рівня й профілю легування;
· зміна типу провідності вирощуваних епітаксіальних плівок;
· фізичні властивості епітаксіального шару відрізняються від властивостей матеріалу підкладки в кращу сторону, наприклад, у них менше концентрація кисню й вуглецю, менше число дефектів;
· процес може відбуватися при температурах менших, чим температура нарощування злитка монокристалу;
· можна нанести епітаксіальний шар на підкладку великої площі;
· епітаксіальний шар може бути нанесений локально.
Молекулярно-променева епітаксія. Молекулярно-променева епітаксія (МЛЕ) проводиться у вакуумі й заснована на взаємодії декількох молекулярних пучків з нагрітою монокристалічною підкладкою.
Переваги методу:
· Низька температура процесу. Зниження температури процесу зменшує дифузію домішки з підкладки й автолегування. Це дозволяє одержувати якісні тонкі шари.
· Висока точність керування рівнем легування. Легування при використанні даного методу є безінерційним (у відмінність епітаксії з газової фази), що дозволяє одержувати складні профілі легування.
|
|
Опис процесу МЛЕ.
МЛЕ полягає в осадженні випаруваних елементарних компонентів на підігріту монокристалічну підкладку. Цей процес ілюструється за допомогою рис. 7.18, на якому наведені основні елементи для одержання сполуки (GaAs).
![]() | ||||||||||
Рис. 7.18. Основні елементи для одержання сполуки AlxGa1-xAs |
Кожний нагрівач містить тигель, що є джерелом одного зі складених елементів плівки. Температура нагрівачів підбирається таким чином, щоб тиск парів матеріалів, що випаровуються, був достатнім для формування відповідних молекулярних пучків. Речовина, що випаровується, з відносно високою швидкістю переноситься на підкладку в умовах вакууму. Нагрівачі розташовуються так, щоб максимуми розподілів інтенсивності пучків перетиналися на підкладці.
Підбором температури нагрівачів і підкладки одержують плівки зі складним хімічним складом. Додаткове керування процесом нарощування здійснюється за допомогою заслінок, розташованих між нагрівачем і підкладкою. Використання цих заслінок дозволяє різко переривати або відновляти влучення кожного з молекулярних пучків на підкладку.
Аналогічним образом здійснюється МЛЕ кремнію (рис. 7.19).
Сутність процесу складається у випарі кремнію й однієї або декількох легуючих домішок. Низький тиск парів кремнію й легуючих домішок гарантує їхню конденсацію на відносно холодній підкладці.
![]() |
Рис. 7.19. Установка для МЛЕ кремнію: 1- термопара; 2- кварцовий кристал; 3- тепловий екран; 4- нагрівач; 5- підкладка; 6- тримач; 7- вікно для візуального спостереження; 8- мас-спектрометр; 9- іонізаційний вакуумметр; 10- механічний затвор; 11- джерело сурми; 12- електронна гармата; 13- титановий і гетерний насос; 14- турбомолекулярний насос |
Звичайно МЛЕ проводять у надвисокому вакуумі при тиску 6-10-8 Па. Температурний діапазон становить 400 - 800°С. Технічно можливе застосування й більш високих температур, але це приводить до збільшення автолегування й дифузії домішки з підкладки.
Передепітаксіальна обробка підкладки. Передепітаксіальна обробка підкладки при використанні методу МЛЕ здійснюється двома способами.
1. Високотемпературний відпал при температурі 1000 - 1250 °С тривалістю до 10 хвилин. При цьому за рахунок випару або дифузії усередину підкладки віддаляється природний окисел і адсорбовані домішки.
2. Очищення поверхні за допомогою пучка низькоенергетичних іонів інертного газу. Цей спосіб дає кращі результати. Для усунення радіаційних дефектів проводиться короткочасний відпал при температурі 800 - 900 °С.
Особливості легування при МЛЕ. Однією з відмінних рис МЛЕ є низька швидкість росту плівки: приблизно 1 моношар/с або 1 мкм/годину, що дозволяє легко модулювати молекулярні пучки, що попадають на підкладку, якщо час керування рухом заслінки менш 1 секунди.
Легування при МЛЕ має кілька особливостей. У порівнянні з епітаксією з газової фази розширений вибір легуючих сполук, можливе керування профілем легування. Легуюча домішка може бути як p-, так і n-типу. Можливі два способи легування.
1. Після випару домішкові атоми досягають поверхні й вбудовуються в кристалічні ґрати. Найбільш часто застосовувані домішки (As, H, B) випаровуються або занадто швидко або занадто повільно для ефективного керування. У результаті частіше прибігають до вживання Sb, Ga або Al.
2. В іншому способі легування використовується іонна імплантація. У цьому випадку застосовуються слабкострумові (1 мкА) іонні пучки з малою енергією. Низька енергія цього процесу дозволяє впроваджувати домішки на невелику глибину під поверхню зростаючого шару, де вона вбудовується в кристалічні ґрати. Цей спосіб дозволяє використовувати такі домішки як B, P і As.
|
|
Система, використовувана для МЛЕ. Система, використовувана для МЛЕ кремнію, зображена на рис. 7.20. Основою установки є вакуумна система. Тому що в процесі МЛЕ потрібно підтримувати високий вакуум, установки забезпечуються вакуумними шлюзами для зміни зразків, що забезпечує високу пропускну здатність при зміні пластин і виключає можливість проникнення атмосферного повітря. Для десорбції атмосферних газів зі стінок системи потрібний тривалий відпал у вакуумі. Для забезпечення високої якості й чистоти зростаючого шару необхідний низький тиск. Цього домагаються, використовуючи безмасляні засоби відкачки (наприклад, титановий гетерний насос).
Метод МЛЕ дозволяє проводити всебічний аналіз деяких параметрів безпосередньо під час процесу вирощування плівки. Більшість промислових установок МЛЕ містять устаткування для аналізу дифракції відбитих електронів, мас-спектрометр, оже-спектрометр із можливістю дослідження оже-спектрів іонів, що розпилюються.
![]() |
Рис. 7.20. Схеми реакційних камер установок для епітаксіального нарощування: а- горизонтальна; б- ковпакова; в- «бочонок»: 1- високочастотний індуктор; 2- підкладкотримач; 3- потік парогазової суміші |
Випар кремнію здійснюється не шляхом нагрівання тигля, як для легуючих елементів, а за рахунок нагрівання електронним променем, тому що температура плавлення кременя відносно висока. Постійна інтенсивність потоку атомів забезпечується строгим контролем температури. Для контролю температури застосовуються термопари, ИК-датчики й оптичний пірометр. Керування потоками атомів легуючої домішки здійснюється за допомогою заслінок. Це дозволяє досягти гарної відтворюваності процесу й високої однорідності швидкості росту й рівня легування.
Перспективи розвитку. Прилади, одержувані з використанням МЛЕ.
МЛЕ використовується для виготовлення плівок і шаруватих структур при створенні приладів на (GaAs) і (AlxGa 1-xAs). До таких приладів відносяться лавинопролітні діоди, що перемикають Свч-Діоди, польові транзистори з бар'єром Шотткі, інтегральні оптичні структури.
|
|
Метод молекулярно-променевої епітаксії перспективний для твердотільної електроніки створення Свч-Приладів і оптичних твердотільних приладів і схем, у яких істотну роль грають шаруваті структури субмікронних розмірів. При цьому особливе значення надається можливості вирощування шарів з різним хімічним складом.
Успіхи напівпровідникової електроніки в останні роки зв'язані головним чином з розвитком напівпровідникової технології, зокрема з успіхами в техніці очищення поверхні, напилювання металевих і напівпровідникових плівок у високому вакуумі й розробці епітаксіальної технології, що дозволило одержувати контакти із заданими високими виробленими характеристиками.
У зв'язку з розвитком ептаксіальної технології у виробництві напівпровідникових матеріалів і приладів вимоги до чистоти об'ємних монокристалів зменшилися, оскільки їх використовують в основному для виготовлення підкладок, на яких методами газофазної (германій, кремній і напівпровідникові сполуки) або рідкофазної (напівпровідникові сполуки) епітаксії виготовляють робочий шар майбутнього напівпровідникового приладу або інтегральної схеми. Епітаксіальна технологія дозволяє одержувати шар напівпровідників дуже високого ступеня чистоти.
Під епітаксіальною плівкою розуміють кристалічну плівку, структура якої близька до структури підкладки, а орієнтація відповідає орієнтації останньої. Епітаксіальна технологія важлива в сучасній мікроелектроніці.
Цілком реальними для широкого практичного освоєння в найближчому майбутньому є процеси одержання високоякісних монокристалічних шарів кремнію, арсеніду галію й інших напівпровідникових матеріалів на ізолюючих (у тому числі некристалічних) підкладках великої площі, а також процеси епітаксіального вирощування багатошарових гетерокомпозицій типу метал-діелектрик-напівпровідник. В останньому випадку, крімтрадиційних епітаксіальних технологій, доцільно використовувати інтенсивно розроблювальні в останні роки процеси створення схованих провідних і діелектричних шарів, шляхом високодозової іонної імплантації (іонного синтезу) і наступного термічного відпалу. Успішна реалізація останніх вимагає детального дослідження закономірностей дефектоутворення й механізму процесів, що протікають на різних етапах іонного синтезу й наступної твердотільної епітаксії. Поки такого роду дослідження проводяться в основному в застосуванні до кремнію.
Реактори звичайно виготовляють із кварцу, рідше застосовують хромонікелеві сплави й монель-метал, а для ущільнень використовують фторопласт-4. Підкладкотримачі 2, щовиконують роль підставок, служать також для поглинання й передачі теплової енергії підкладкам. За формою вони можуть бути у вигляді бруска, піраміди, диска або циліндра й виготовляють їх з хімічно- і термостійкого матеріалу (графіту й склографіту) (рис.7.20).
Нагрівають підкладки струмами високої частоти за допомогою індуктора.
7.3. Вплив щільності пари на формування структури тонких плівок
Щільність пари залежить від тиску в системі (див. рис. 7.21).
При високих значеннях тиску пари Р молекули мають хаотичний характер руху й осадження.
У результаті плівки здобувають надлишкову пористість. Для одержання плівок задовільної пористості необхідно, щоб виконувалася наступна умова:
(7.5)
Графік залежності щільності пари від тиску показаний на рисунку 7.22.
Щільність пари впливає на тип осадження речовини, як видно з діаграми стану. При цьому більш низька щільність пари викликає процес конденсації, більш висока – процес сублімації.
Від щільності пари залежить і концентрація речовини в одиниці об’єму, що позначається на процесах структуроутворення при осадженні атомів пари на підкладку (рис. 7.23).
Вплив концентрації пари на процеси структуроутворення описується наступними умовами:
1) С1 < С2 < С3 р пари > р сублім.
2) Ств. > С2
3) Ств. ≈ С3
Зобразити таку залежність можна у вигляді графіка, показаного на рис. 7.24.
Таким чином, зі збільшенням щільності пари при сублімації речовини спостерігається послідовний перехід від дендритної до ніздрюватої й плоскої границі розділу між твердою й газоподібною фазами.
Тонкі плівки, отримані при низькій концентрації пари, тобто з дендритною структурою, мають пористість значно більшу ніж плівки з комірчастою структурою. Тому їх використовують як фільтри електродів хімічних джерел струму, адсорбційних систем та для інших цілей, де потрібна висока питома поверхня розділу.
Плівки одержувані при середніх значеннях концентрації пари, тобто з комірчастою структурою, використовуються в тих випадках, коли потрібно одержати досить високу щільність матеріалу й одночасно сформувати на його поверхні мікрорельєф, необхідний для гарної адгезії наступного напиляного шару, тобто цей режим використовується для одержання багатошарових тонких плівок (рис. 7.24).
А плівки отримані при високій щільності пари мають й високу щільність, таким чином ми отримаємо епітаксіальну плівку однорідну за будовою та не пористу. Тому напилювання при високій щільності пари використовується для одержання плоских і щільних тонких плівок. Звичайно ці плівки використовуються в електронній промисловості для створення елементів інтегральних схем. Але занадто висока щільність пари може привести до прискорення процесу напилювання, що у свою чергу, простимулює утворення аморфної структури плівки, тобто, так званих металевих стекол.
Ріст кристалічної фази спостерігається зі зростанням температури підкладки в інтервалі температур 250-280°С. Збільшення кількості та розмірів кристалічної складової спостерігається при підвищенні температури підкладки. Загальна тенденція у цьому випадку наступна: чим вище температура підкладки, тим більше кристалічної складової.
Кристалічна структура представлена кристалами збиткової фази голчастої морфології різного розміру, в залежності від товщини напиляного шару та швидкості тепловідводу.
Кристали представляють собою гілки, що ростуть від підкладки вертикально або розгалужуються у направленні тепловідводу.
Нижче показана торцева поверхня тонких плівок складу МоО3, що ілюструє описані вище теоретичні положення (рис. 7.25).
![]() | ![]() |
Рис. 7.25. Мікроструктура шарів зразка багатошарової тонкої плівки складу МоО3, а – зона стовбчастих кристалів; б- зона дендритних кристалів; РЭМ, х1000 |
7.4. Вплив температурного градієнта в напрямку від випарника до підкладки на формування структури тонких плівок
Для отримання якісної тонкої плівки необхідно, щоб процес нанесення відповідав наступним умовам:
1) , (7.6)
де - різниця температур підкладки та випарника;
- відстань від випарника до підкладки.
У цьому випадку повинно бути максимальненаближення підкладки до випарника й найбільша температурна різниця між температурою підкладки Тпідкл та температурою випарника Твип.
, (7.7)
д е ,
Е – ефективність процесу напилювання;
К – постійна величина;
Т – температура підкладки,
l – відстань від випарника до підкладки.
Вплив температури (температурного градієнта) підкладки на щільність пари та, відповідно, на ефективність процесу нанесення показаний на рисунку 7.26. Із графіка також слідує, що важливим фактором є також тиск, що утворює пара в робочій камері.
![]() |
Рис. 7.26. Схема (а) і графік впливу (б) температурного градієнта на формування структури плівок |
З умови високого температурного градієнта слідує, що величина температури Т має велике значення й, одночасно із цим, високим повинен бути сам тиск, тобто осадження буде відбуватися при енергії атомів порядку 1,5 ÷ 2 еВ.
-енергія атомів;
-довжина вільного пробігу.
Такий режим забезпечує гарну адгезію підкладки. Мала довжина вільного пробігу забезпечує, з іншого боку, більшу конкуренцію атомів при осадженні на підкладку. Тому процес відбувається з великою швидкістю, однак тонкі плівки мають пухку структуру.
При високій швидкості витікання речовини, що напилюється, можливе утворення аморфних структур у відносно товстих плівках.
Максимізація температурного градієнта є перспективним способом одержання товстих аморфних плівок з матеріалів, що відрізняються великою кількістю компонентів, та мають високу енергію міжатомної взаємодії.
2)
Цьому випадку відповідає велика відстань між підкладкою і випарником і мала різниця температур між ними.
В умовах мінімального градієнта формуються тонкі плівки, що мають високу щільність, але низьку адгезію до підкладки. Плівки, як правило, мають тендітну структуру й, зазвичай, цей спосіб застосовується для неадгезійних процесів.
Таким методом одержують монохроматори рентгенівського випромінювання, які знаходять своє застосування як у рентгенівських аналізаторах так і в рентгенівських лазерах з ядерним накачуванням.
Вплив умов охолодження на структуроутворення в тонких плівках.
У сучасних пристроях для напилювання швидкість охолодження підкладки може варіюватися в такий спосіб (рис. 7.27).
1. За рахунок зниження температури або повного відключення нагрівача підкладки з її неробочої сторони.
2. За рахунок застосування температури випарника на заключній стадії одержання плівки.
3. За рахунок примусової подачі холодного газу, як з робочої, так і неробочої сторони підкладки.
Вплив умов охолодження підкладки ефективно позначається на структурі тонких плівок при їх товщині понад 20 ÷ 30 мкм. У плівках меншої товщини більш важливе значення має температура підкладки. Це пов’язане з тим, що температурний градієнт по перетині плівки має невелику величину й тверда фаза буде утворюватися приблизно в тих самих умовах (при однакових переохолодженнях) у повному об’ємі одержуваної плівки (рис. 7.28).
Способи одержання тонкоплівкових матеріалів залежно від характеру охолодження підкладки розрізняють наступні.
1. Прискорене охолодження з неробочої сторони підкладки й уповільнене з робочої сторони. У цьому випадку через розходження коефіцієнтів термічного розширення (КТР) матеріалів підкладки й форми виходять неадгезійні плівки, структура яких визначається умовами охолодження з боку випарника.
2. Уповільнене охолодження з неробочої сторони підкладки й прискорене з боку випарника. У цьому випадку виходять плівки з гарною адгезією до підкладки.
3. Швидке охолодження, як з боку підкладки, так і з боку випарника. При використанні цього методу вибирають тонкі підкладки, товщина яких порівнянна з товщиною одержуваних плівок. У цьому випадку утворення плівки відбувається по однаковому механізмі, як із зовнішньої, так і внутрішньої сторони при незначному температурному градієнті по її перетині. Таким способом одержують аморфні й нанокристалічні тонкі плівки.
4. Повільне охолодження як з боку підкладки, так і з боку випарника. В цьому випадку плівка буде мати крупнокристалічну структуру. У товстих плівках при градієнтному охолодженні діють ті ж принципи структуроутворення, що й при затвердінні злитка (рис. 7.29).
Зниження щільності до зовнішнього краю плівки пояснюється усадочною розосередженою пористістю. Це явище й такий спосіб одержання плівок використовується для тонкоплівкових матеріалів, що контактують із рідкими середовищами (катодні електроди акумуляторних батарей, підкладки рідкокристальних модулів і т.п.).
![]() |
Рис. 7.29. Формування структури тонкої плівки залежно від швидкості тепловідводу |
7.5. Вплив енергії дисоціації матеріалів на характеристику їхнього осадження
Залежно від енергії, що підводиться до випарника, ступінь дисоціації матеріалу при переході в пароподібну фазу, розділяється на три рівні:
1. Молекулярна дисоціація – Е1;
2. Часткова (дипольна) дисоціація (часткове руйнування зв’язків молекул або комплексів стехіометричного складу) – Е2;
3. Повна дисоціація, якій відповідає руйнування всіх зв’язків між компонентами вихідного матеріалу – Е3 (рис. 7.30).
Оскільки температура підкладки нижче температури випарника, то в її околиці можуть відбуватися процеси повернення до більш низького ступеня дисоціації. Присутність комплексів з різним ступенем дисоціації призводить до утворення на підкладці різних структур.
Найчастіше наявність частково дисоційованих і не дисоційованих комплексів призводить до утворення пухких структур, що відрізняються по своїй стехіометрії від вихідного матеріалу.
Залежно від механізму взаємодії комплексів поблизу підкладки можуть бути отримані аморфні або нанокристалічні структури при великій енергії взаємодії атомів компонентів або полікристалічні й монокристалічні структури при малій енергії взаємодії компонентів. У цьому випадку енергія взаємодії компонентів збігається з енергією їхньої дисоціації.
Для керування процесами дисоціації біля підкладки часто встановлюють додатковий нагрівальний елемент. З підвищенням температури в області, що прилягає до підкладки, ступінь дисоціації матеріалу буде підвищуватися.
7.6. Вплив температури підкладки на охолодження матеріалу
Температура підкладки впливає головним чином на два параметри:
1. Адгезія плівки до підкладки. Зі збільшенням температури підкладки цей показник збільшується. Як було показано вище, підкладку нагрівають до температури не більше 100°С, це сприяє отриманню тонких плівок оптимальної щільності та адгезійності. При високому ступені перегріву у атомів підкладки буде спостерігатися значне температурне коливання, що визвано підвищеною температурою речовини. Це явище буде сприяти відштовхуванню атомів, які наближаються до підкладки, тому плівка не буде мати епітаксіальної та щильної структури.
З іншого боку, переохолодження підкладки викликає зовсім інший ефект, а саме, атоми речовини, що наноситься на підкладку, будуть зщеплюватися з поверхнею підкладки з високою інтенсивністю, що призведе до утворення пластівчастих за формою та великих за розміром часток речовини, що напилюється. У результаті такого явища ми отримаємо плівку з низькою щільністю та, ймовірно, з висококомірчастою, пористою структурою.
Таким чином, за допомогою температури підкладки можна контролювати такий показник тонкоплівкових матеріалів, як їх пористість, щільність та адгезія до матеріалу підкладки.
2. Ефективність осадження. Чим вище температура підкладки, тим менша кількість речовини буде осаджена на підкладку в одиницю часу. Це положення також можна пояснити ефектом відштовхування атомів або іонів речовини, що наноситься, від атомів підкладки в наслідок їх високого температурного коливання.
Вплив температури підкладки на структуру тонких плівок аналогічний впливу температурного градієнта поблизу підкладки.
8. СТРУКТУРОУТВОРЕННЯ В МЕТАЛОКЕРАМІЧНИХ ТОНКИХ ПЛІВКАХ, ОТРИМАНИХ ЗА ДОПОМОГОЮ HDS ТЕХНОЛОГІЇ
Суть даного методу полягає в наступному: частки активної речовини (порошок монооксиду кремнію) розганяються потоком газу високого тиску і прямують на металеву підкладку (мідна фольга товщиною 50 нм(рис. 8.1, 8.2).
![]() ![]() |
а
![]() |
Рисунок 8.1. Елементарна схема процесу структуроутворення металокерамічного покриття на мідній підкладці: а- торцевий зріз; б- вид зверху |
При попаданні наночасток на підкладку відбувається її часткове оплавлення в місцях контакту і закипання металевої підкладки, таким чином утворюється металевий аерозоль з матеріалу самої підкладки. Відбувається змочування наночасток, і рідкий метал встигає створити контакт, утворюючи мідні містки між частками монооксиду кремнію.
![]() |
Рис. 8.2. Мікроструктура металокерамічного покриття, нанесеного на мідну підкладку, РЕМ, х 50500 |
В одержаних за допомогою HDS-процесу зразках анодного металокерамічного матеріалу була отримана пориста структура, так звані «пористі глобулі», між якими спостерігається множинний контакт часток монооксиду кремнію з підкладкою та їх висока адгезія. Очевидно, що процес екологічно чистий, тому що система фільтрації надлишкових матеріалів виключає можливість потрапляння оксидних матеріалів в атмосферу. Більш того, газ-носій є інертним та ніяк не впливає на оточуюче середовище (рис.8.3).
В результаті, як сказано вище, на підкладці формується металокерамічне пористе покриття. Структура вихідного порошку представлена на рисунку 8.3,а, структура металокерамічного покриття - на рисунках 8.3б-г при збільшеннях х1000, х10000, х50000 відповідно. Фотографії для дослідження були отримані за допомогою растрового електронного мікроскопа JSM фірми Jeol (Японія).
З рисунку 8.3,б видно, що отримана структура не має видимих дефектів, але при даному збільшенні неможливо розрізнити структурні складові. Основними структурними складовими даного покриття є частки оксиду кремнію і, так звані, демпферні «містки» з міді.
![]() | ![]() |
![]() | ![]() |
Рис. 8.3. Мікроструктура, РЕМ: а- морфологія вихідного порошку монооксида кремнія, х 10000; б - г - металокерамічного покриття: б – х 1000; в – х 10000; г – х 50000 |
Для якісної і кількісної оцінки структурних складових були проведені металографічні дослідження при збільшеннях х10000 – х50000 за допомогою методик растрової електронної мікроскопії (рис. 8.3.б-г).
При збільшеннях х10000 та х50000 видно (рисунок 8.3,б і г), що частки покриття SіO достатньо рівномірно розподілені по поверхні покриття. Крім того, очевидно, що частки в результаті нанесення змінили свою форму і розміри. Якщо початковим порошком був грубий конгломерат з частками осколкової морфології, то після нанесення вони придбали форму, близьку до глобулярної і рівновісної.
9. ВИКОРИСТАННЯ ДІАГРАМ СТАНУ ДЛЯ РОЗРОБКИ РЕЖИМІВ ОДЕРЖАННЯ тонкоПЛІВКОВИХ МАТЕРІАЛІВ
Діаграми стану – це креслення, кожна крапка яких показує температуру й фазовий склад (співвідношення компонентів) для багатокомпонентних систем, температуру, тиск та поліморфний стан (для однокомпонентних діаграм), а також кількість компонентів у системі.
Визначення режиму залежить від способу, за допомогою якого буде отримана дана плівка. У свою чергу, способи одержання тонких плівок бувають:
1 – низькотемпературні або холодні;
2 – високотемпературні або гарячі.
1. Низькотемпературні (холодні) – засновані на утворенні плазми в розрядному проміжку й русі іонів напиляної речовини в напрямку до підкладки. До холодних можна віднести: електронно-променевий, іонно-плазмовий, магнетронний на постійному та змінному струмі, іонний, іонно-дифузійний та плазмовий низькотемпературний методи.
2. Високотемпературні (гарячі) – засновані на плавленні й випарі вихідної речовини способом її нагрівання й осадження пари на підкладку. До гарячих методів можна віднести: вакуум-термічний, у тому числі й VDS-процес; плазмово-дуговий та плазмовий високотемпературний методи.
Перше, що треба визначити, яким способом можна здійснити напилювання даного матеріалу: холодним або гарячим, це залежить від фізико–хімічних властивостей речовини, а саме, від температури плавлення й, особливо, від температури випару матеріалу.
Способи холодного напилювання використовуються для легкоплавких речовин. А для металів з високою температурою плавлення – «гарячі» способи.
Найвищі температури (найбільш високотемпературний спосіб) і найвищу теплову енергію дозволяє досягти іонно–променевий спосіб, тому що тут немає теплопередачі, а температура генерується в самій речовині. Обмеження для іонно–променевого методу бувають у випадках, коли в системі присутні два елементи, які будуть дифундувати друг у друга в рідкому стані. В останньому випадку найбільш ефективними будуть холодні методи.
Вибір способу напилювання заснований на аналізі діаграми стану вихідної речовини.
Речовини з надвисокою температурою плавлення або високою питомою теплотою випару випаровуються холодним способом, а саме способом нагрівання речовини без теплопередачі, тобто методом електронно–променевого випару або лазерним випаром.
Таким чином, висока температура плавлення не є єдиним чинником, що визначає режим напилювання речовини. Наприклад, для такого металу, як алюміній, у якого tплавл. = 630…660оС, але питома теплота плавлення й випару дуже високі – більше 2486оС. У цьому випадку треба орієнтуватися саме на питому теплоту плавлення й випару металу й вибирати холодний метод.
9.1. Однокомпонентні системи
У цьому випадку використовують діаграми для чистих металів – умовні діаграми (рис. 9.1) у системі координат тиск – температура.
Залежно від термодинамічних умов у даній системі відбуваються наступні перетворення: при низьких температурах
– возгонка, тобто перехід із твердого стану речовини в газоподібний. Цей же процес, що відбувається у зворотному напрямку, називається сублімацією.
При більш високих температурах:
- випар, перехід Р → Г, і зворотний процес –
- конденсація, тобто Г → Р.
Схильність речовини до сублімації або випару при нагріванні визначається його особливостями кристалічної будови й типом міжатомних зв’язків. Метали, що характеризуються сильним ковалентним зв’язком, схильні до випару більшою мірою, чим до возгонці.
|
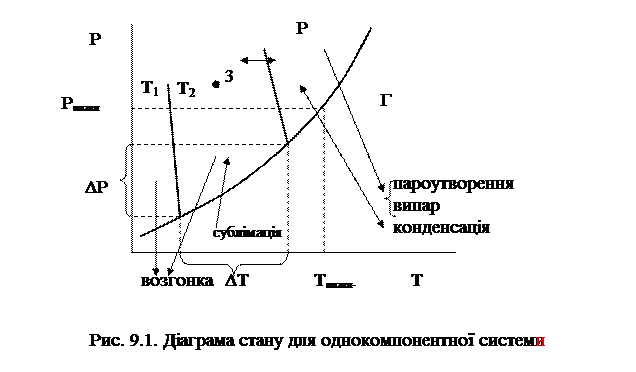
Температури плавлення й кипіння (випару) речовин можуть значно розрізнятися. Для деяких речовин, наприклад, для оксидів вісмуту й кадмію, температура випару нижче температури плавлення.
Процес осадження речовини на підкладку при підвищених температурах і тиску відбувається за механізмом конденсація → затвердіння.
При низьких температурах і тисках тверда фаза утворюється з газоподібної, тобто в процесі сублімації.
При конденсації матеріалу на підкладці формуються адгезійно міцні тонкі плівки. Крім цього, якщо рідка плівка добре змочує підкладку, то цим методом можна одержувати гладкі плівки на нерівних поверхнях (рис. 9.2).
За допомогою конденсації одержують плівки товщиною 10–2 мкм. Більш тонкі плівки одержати неможливо через властивості рідини: сили зв’язку й сили поверхневого натягу недостатні.
Для одержання тонких плівок використовується процес сублімації речовини, що випаровується, тобто Г → Р → Тв.
Сублімовані плівки можуть мати товщину в кілька десятків або сотень Å. Це можуть бути плівки з оксидів, наприклад SiО2.
Застосування перерахованих вище положень на практиці. При низьких тиску й температурі система перебуває в газоподібному стані, при більш високих значеннях тиску та температури – у твердому, у нашому випадку це дві поліморфні модифікації Т1 і Т2 (рис. 9.1). При найвищих значеннях температури й тиску система перебуває в рідкому стані.
При низьких Р и Т треба використовувати процеси:
– возгонки, тобто перевести метал із твердого відразу в газоподібний стан;
– розплавлювання, тобто перехід із твердого в рідкий стан.
Приклад. Матеріал має 2 поліморфні модифікації у твердому стані.
1. Визначити умови возгонки високотемпературної поліморфної модифікації (точка 3, рис. 9.1).
Шукаємо на діаграмі лінію сублімації для цієї точки, опускаємо лінії на осі Р и Т і знаходимо інтервали температур і тисків.
2. Знайти умови паротворення.
Для цього треба спочатку розплавити метал, а потім випарувати. Чим вище тиск, тим більше буде температура плавлення.
При низьких показниках тиску процес возгонки речовини буде проходити раніше плавлення. До таких речовин відносяться оксиди, наприклад, Mo2O3, який переходить у пару, не плавлячись, при низьких значеннях тиску.
9.2. Багатокомпонентні системи
У разі багатокомпонентної системи варто враховувати наступні фактори:
1) взаємну розчинність компонентів, на діаграмі стану це лінії обмеженої розчинності (ЛОР).
2) наявність нонваріантних перетворень;
3) поліморфні перетворення.
Розглянемо нижче деякі діаграми стану з їхнім використанням для розробки режимів нанесення тонких плівок. Розглянемо це на прикладі діаграми стану з евтектичним перетворенням.
Евтектичне перетворення (рис. 9.3).
Для даної системи визначення режиму напилювання буде проходити у два етапи:
– як випарувати дану речовину;
– як потім провести його осадження на підкладку.
З діаграми стану ми бачимо, що система при охолодженні/нагріванні проходить через евтектичне перетворення:
Тобто, під час нагрівання даної речовини відбуваються наступні процеси:
а) першою буде плавитися евтектика складу по наступній реакції:
, тобто треба нагріти систему вище лінії солідус;
б) наступними будуть плавитися кристали α фази по реакції:
При підвищенні температури схильність до випару збільшується експоненціально.
Коли матеріал переходить у рідкий стан, випар проходить легко й при низькому тиску. У міру нагрівання α –твердого розчину плавлення буде здійснюватися уздовж лінії ліквідусу, при цьому зміст компонента В буде зменшуватися.
Якщо шари напиляної речовини будуть відрізнятися за складом, то плівка буде відшаровуватися від підкладки.
Щоб процес пройшов швидко, треба провести нагрівання дуже швидко, тобто з більшим ΔТ, тоді й плавлення й осадження теж пройдуть швидко, і отриманий матеріал буде мати однорідний склад. Пояснити даний факт також допоможе діаграма стану. Чим більше фазових перетворень випробує матеріал при нагріванні (повільне нагрівання), тим більш неоднорідним буде склад отриманої плівки. Тому нагрівати речовину треба з дуже великою швидкістю, це призведе до швидкого випару матеріалу й одержанню плівки однорідного складу.
Щоб одержати багатошарову плівку з матеріалу заданого складу, треба робити ізотермічні витримки при різних температурах, тобто при температурах завершення кожного фазового перетворення.
Монотектичне перетворення. У цьому випадку необхідно одержати однорідну плівку при обмеженій розчинності речовини в рідкому стані (рис. 9.4).
З діаграми стану видно, що при нагріванні сплаву 1 необхідно пройти область неоднорідного складу двох рідин, що не змішуються, Р1+Р2. При повільному нагріванні буде отриманий неоднорідний двокомпонентний склад, що відповідає даній області діаграми.
Щоб одержати однорідну плівку, треба одержати однорідну пару(газ) складу 1 за діаграмою. Для цього дану систему треба нагрівати з дуже високою швидкістю до області однорідного рідкого розчину Р.
Використання таких систем часто застосовується для одержання багатошарових композицій з одного джерела пари (рис. 9.4,б). Це найбільш ефективно, якщо температури плавлення й випару компонентів значно відрізняються.
Нагрівання здійснюється в три етапи:
I – плавлення в області розшарування рідин.
II – випар компонента А.
III – випар компонента Б.
Даний спосіб має широке застосування, оскільки важкі атоми металу роблять сильну каталітичну й модифікуючу дію. З їхньою допомогою можливе одержання нитковидних структур С, Si, і т.д.
9.3. Використання діаграм стану при напилюванні холодним методом
Основною характеристикою холодних методів є відсутність плавлення катода в процесі одержання тонкої плівки.
При призначенні режимів напилювання для холодних процесів необхідно проаналізувати перетворення вихідного матеріалу у твердому стані.
Розглянемо декілька випадків.
Доевтектичне перетворення (рис. 9.5)
Процес розплавлювання при нагріванні сплаву 1 проходить в 3 етапи:
1 – розплавлювання евтектики ;
2 – евтектичне перетворення
3 – розплавлювання залишкових кристалів α фази.
- При катодному розпиленні температура процесу лежить в інтервалі 200–300оС. Так само як і при магнетронному напилюванні.
Іонне напилювання від плазмового відрізняється наступним:
- При іонному напилюванні у якості атомів, що бомбардують мішень, тобто вихідну речовину, використовують аргон, який подається у вакуумний об’єм у невеликій кількості. Атоми аргону іонізуються, й іони аргону бомбардують вихідну речовину, вибивають із неї атоми, які й осаджуються на підкладці (див. рис. 4.16).
- При плазмово–дуговому методі аргон не використовують. Але тут є присутнім магнітне поле. В якості бомбардуючих атомів – іскра електричного пробиття. Сила індукції магнітного поля повинна бути більше сили індукції пробиття (розряду), тобто:
В цьому випадку при пробитті використовуються атоми не газу аргону, а тої ж вихідної речовини, яка іонізується в магнітному полі й вибивають атоми собі подібні з мішені, які й осаджуються на підкладці. Цей процес більш ефективний.
Обидва способи відносяться до холодного напилювання, тобто підкладка не гріється. Відмінність ще й у тім, що α–твердий розчин буде вибиватися легше, ніж евтектика, на відміну від гарячих методів, коли першою плавиться евтектика. Щоб випаровувалися обидва компоненти (α‑фаза й евтектика), напруги міняють циклічно, згідно з режимом, показаним на рис. 9.6.