К этой группе относят стали которые обладают высокой стойкостью против коррозии в атмосферных условиях, в морской и речной воде, в растворах солей, кислот и щелочей. Основным легирующим элементом всех марок нержавеющих сталей является хром. От коррозии стали предохраняет тонкая, но плотная пленка окислов Cr2O3, которая образуется на поверхности тщательно обработанных деталей, однако хрома должно быть не менее 12%, в противном случае пленка не будет сплошной.
Антикоррозионные свойства хромистых сталей повышаются введением в их состав никеля. В связи с этим различают хромистые и хромоникелевые стали.
Из стали 12Х13 изготавливают клапаны гидравлических прессов, лопаток гидравлических и паровых турбин.
Из сталей марок 20Х13, 30Х13, 40Х13 – режущий, мерительный и хирургический инструмент, пружины, предметы домашнего обихода.
Хромоникелевые стали 12Х18Н9, 17Х18Н9Т, 12Х18Н10Т применяют для изготовления деталей сваркой, работающих в особо агрессивных средах.
Вопросы для повторения раздела.
1. Как классифицируются легированные стали?
2. Укажите марки и назначение цементуемых сталей.
3. Каково назначение улучшаемых сталей?
4. Укажите эксплуатационное назначение высокомарганцовистой стали.
5. Назовите основные требования, предъявляемые к рессорно-пружинным сталям и их маркировку.
6. Какие требования предъявляют к стали для изготовления подшипников?
7. Укажите маркировку и назначение коррозионостойких сталей.
К инструментальным сталям относят стали, предназначенные для изготовления режущего, измерительного, штампового и других инструментов. Основными свойствами этих сталей является твердость, вязкость, износостойкость, теплопроводность (красностойкость), прокаливаемость.
Стали для режущего инструмента должны обладать высокой твёрдостью, превышающей твердость обрабатываемого материала. Режущая кромка инструмента всё время находится в соприкосновении со снимаемой стружкой, т.е. происходит непрерывное трение и износ поверхности режущей кромки инструмента. Поэтому сталь для режущего инструмента, кроме высокой твёрдости, должна иметь высокую износостойкость. В процессе резания механическая энергия превращается в тепловую и вследствие этого нагревается инструмент, обрабатываемая деталь и стружка.
Инструментальные стали по назначению делятся на три группы: углеродистые и легированные стали для режущих инструментов; быстрорежущие стали; штамповые стали и отдельная группа – твердые сплавы.
10.1. Углеродистые инструментальные стали.
Углеродистые инструментальные стали производят качественными: У7, У8, У9, У10, У11, У12, У13 и высококачественными: У7А, У8А, У9А, У10А, У11А, У12А, У13А.
Высокая твердость (HRC 62-65) инструментальных сталей достигается в результате закалки. Стали У7, У8 подвергаются полной закалке, стали У9-У13 – неполной закалке. Закалку углеродистой стали проводят в воде или водных растворах солей и щелочей, так как она имеет малую устойчивость переохлаждённого аустенита. После закалки структура углеродистых сталейУ7, У8 состоит мартенсита и избыточного карбида (цементита). Избыточные карбиды повышают износостойкость стали. В структуре закаленных углеродистых сталей имеется также небольшое (до5-8%) количество остаточного аустенита, но так как его мало, твёрдость стали не снижается.
Критический диаметр изделий из углеродистых сталей не превышает 15мм. Поэтому эти стали применяют для изготовления мелких инструментов с поперечным сечением до 25мм с незакалённой сердцевиной. При несквозной прокаливаемости меньше деформация инструмента при закалке. Инструмент с незакалённой вязкой сердцевиной обладает большей устойчивостью к ударам и вибрациям.
После закалки инструмент из углеродистой стали подвергают низкотемпературному отпуску. В зависимости от назначения инструмента и требуемой твердости температура отпуска может изменяться в определенных пределах.
Для уменьшения внутренних напряжений при сохранении высокой
твердости достаточен отпуск при 150...180° С в течение 1-2 часов. Такой
отпуск проводят для инструментов, работающих с небольшими ударными
нагрузками. Для инструментов, для которых требуется достаточно высокая
твердость и повышенная вязкость, применяют отпуск при температурах до
220...240°С. Инструменты, работающие с ударными нагрузками, отпускают
при 250...320°С.
Так как инструмент из углеродистой стали теряет твердость при нагреве выше 200°C условия работы его должны быть такими, чтобы режущая кромка в процессе работы не нагревалась выше 200°С, т.е. резание следует проводить при небольших скоростях.
Из качественных углеродистых инструментальных сталей изготавливают несложные по конфигурации режущие и измерительные инструменты. Более сложные инструменты изготавливают из высококачественных инструментальных сталей.
Для режущего инструмента (фрезы, зенкеры, сверла, спиральные пилы, шаберы, ножовки ручные, напильники, бритвы, острый хирургический инструмент и т.д.) обычно применяют заэвтектоидные стали (У10, У11, У12 и У13). Деревообрабатывающий инструмент, зубила, кернеры, бородки, отвертки, топоры, молотки изготовляют из сталей У7, У8.
10.2. Легированные инструментальные стали.
Легированные инструментальные стали получают на базе углеродистых
инструментальных сталей путем легирования их хромом, вольфрамом,
ванадием, марганцем, кремнием и другими элементами. Легирование
приводит к большей устойчивости переохлажденного аустенита и большей
прокаливаемости, чем у углеродистых инструментальных сталей. Эти стали
отличаются также повышенной вязкостью, меньшей склонностью к
деформациям и трещинообразованию при закалке. Из легированных
инструментальных сталей марок 9ХС, ХВГ, Bl, XB5 и других
изготавливают различные режущие инструменты, имеющие сложную
конфигурацию.
Для получения массивного инструмента и инструмента сложной формы предназначена сталь 9ХС (0,95-1,25% С; 1,2-1,6% Is).
Стали марок ХВГ (0,9% С; 0,9-1,2% Сr; 1,2-1,6% W; 0,8-1,1% Мn) и ХГ относятся к малодеформирующимся. Их используют для изготовления калибров, длинных метчиков, бритвенных ножей и лезвий и другого инструмента, для которого весьма важно сохранение размеров в процессе термической обработки, а также для изготовления деталей точных приборов.
Сталь ХВ5 (1,25-1,50% С) называется алмазной, обладает исключительно высокой твердостью в закаленном состоянии (HRC 67-69). Применяется для изготовления фильер холодного волочения, отделочного инструмента, снимающего стружку с твердых материалов (белый чугун, стекло, камень).
10.3. Быстрорежущие стали.
Быстрорежущие стали широко используют для изготовления режущего инструмента, обладающего большой твердостью и работающего при высоких скоростях резания. При обработке с большими скоростями резания твердых материалов и при снятии стружки большого сечения режущая кромка инструмента нагревается до высокой температуры. Поэтому режущий инструмент, работающий в тяжелых тепловых условиях, следует изготовлять из стали, обладающей красностойкостью, т.е. способностью сохранять высокую твердость при нагреве до высокой температуры (600...650° С). Для обеспечения красностойкости сталь легируют большим количеством вольфрама в сочетании с молибденом и ванадием. Кроме этих элементов все быстрорежущие стали легированы хромом (примерно 4%), а некоторые - кобальтом.
Быстрорежущие стали выпускают следующих марок: Р6, Р9, Р12, Р18 (цифра в марке стали означает процент вольфрама).
Вольфрам - дефицитный и дорогой элемент, поэтому его содержание в быстрорежущей стали стремятся уменьшить. Частично вольфрам заменяют молибденом из расчета, что 1% молибдена оказывает такое же влияние на свойства быстрорежущей стали, как 1,5-1,6% вольфрама. Содержание молибдена в быстрорежущих сталях обычно не превышает 5%. Такое сочетание вольфрама и молибдена имеется в широко применяемой стали Р6М5.
Быстрорежущие стали условно разделяют на стали умеренной красностойкости и стали повышенной красностойкости. В первую группу входят стали, легированные вольфрамом и молибденом и с небольшим содержанием ванадия (1-2%): Р18, Р12, Р9, Р6М5. Эти стали сохраняют высокую твердость (не ниже HRC 60) при нагреве до 620°С.
В настоящее время основной маркой быстрорежущих сталей (80% от общего объема производства) является Р6М5. Для повышения эксплуатационных свойств сталь дополнительно легируют азотом (Р6АМ5).
В группу сталей повышенной теплостойкости входят стали с высоким (> 2%) содержанием ванадия, а также стали, дополнительно легированные кобальтом (Р9К5, Р12ФЗ, Р18К5Ф2 и др.). Стали этой группы сохраняют высокую твердость при нагреве до 630...650°С.
Быстрорежущие стали по структуре в отожженном состоянии относятся к карбидному (ледебуритному) классу сталей. В их структуре имеется эвтектика (ледебурит), в состав которой входят карбидообразующие элементы - хром, вольфрам, ванадий, кобальт, молибден.
Эвтектика, которая располагается в виде сетки по границам зерен, снижает вязкость стали, поэтому литая быстрорежущая сталь отличается повышенной хрупкостью. При горячей обработке давлением (ковке) сетка эвтектики дробится и первичные (эвтектические) карбиды распределяются в структуре более равномерно.
Горячедеформированную быстрорежущую сталь подвергают отжигу при 840...860° С для снижения твердости, облегчения обрабатываемости резанием и подготовке структуры к закалке. Структура после отжига мелкозернистый сорбитообразный перлит, состоящий из феррита и мелких карбидов, и избыточные карбиды - вторичные и первичные. Твердость стали после отжига должна быть не более НВ 255-285.
В настоящее время все шире применяют быстрорежущие стали, полученные методом порошковой металлургии. В этих сталях карбидная фаза очень мелкая, что способствует более полному растворению карбидов в аустените и повышению теплостойкости. Основные порошковые стали, предложенные для замены сталей Р18 и Р6М5 – Р0М2ФЗ-МП, М6Ф1-МП, М6ФЗ-МП мало содержат дефицитного вольфрама. Несмотря на высокое содержание ванадия, стали хорошо шлифуются. Применяются и другие порошковые стали, например, Р6М5К5-МП и Р12МЗК8. Стойкость режущего инструмента из порошковых сталей по сравнению со стойкостью инструмента из аналогичных сталей обычного производства в 1,2-2 раза выше.
Инструмент, изготовленный из быстрорежущей стали, подвергают закалке и трехкратному отпуску (рис. 50. а).
Быстрорежущие стали обладают пониженной теплопроводностью, медленный или ступенчатый нагрев позволяет выровнять температуру по сечению инструмента и предупредить образование больших внутренних напряжений. При ступенчатом нагреве инструмент подогревают при 800...850°С. Для сложной формы инструмента применяют два подогрева: при 500°С и 800...850° С. Быстрый окончательный нагрев позволяет предупредить окисление и обезуглероживание стали. Выдержку при высокой температуре в интервале температур 1210...1290°С дают очень непродолжительную (10-12 с на каждый миллиметр диаметра или наименьшей толщины инструмента при нагреве в расплавленной соли).
Закаливают инструмент из быстрорежущей стали в масле. Для инструмента сложной формы применяют ступенчатую закалку с выдержкой при 450...500°С в течение 2-5 мин в соляной ванне для выравнивания температуры по сечению инструмента и дальнейшим охлаждением на воздухе.
Структура быстрорежущей стали после закалки состоит из высоколегированного мартенсита, содержащего 0,3-0,4% С, нерастворенных избыточных карбидов и остаточного аустенита.
Сохранение в структуре закаленной стали большого количества остаточного аустенита объясняется тем, что аустенит высоколегированный и для него температура начала мартенситного превращения Мн выше комнатной температуры, а температура конца мартенситного превращения Мн - ниже 0°С.
Отпуск при 500...560°С приводит снова к повышению твердости до HRC 63-65. Такое повышение твердости обменяется выделением из мартенсита дисперсных специальных карбидов. К этому превращению добавляется также превращение остаточного аустенита. Высоколегированный остаточный аустенит достаточно устойчив при температурах отпуска до 500°С. В процессе выдержки при отпуске с температурой 550...570° С из аустенита выделяются в дисперсном виде специальные карбиды. Аустенит обедняется углеродом и легирующими элементами и становится менее устойчивым. В процессе охлаждения от температуры отпуска остаточный аустенит превращается в мартенсит (вторичная закалка). Превращение не заканчивается полностью при однократном отпуске. Для того, чтобы достигнуть почти полного превращения остаточного аустенита в мартенсит, необходимо двух-трехкратное повторение отпуска при 550...570° С с выдержкой при каждом отпуске 45-60 мин (рис. 50. а). Следует отметить, что аустенит превращается в мартенсит не при нагревании и не в процессе выдержки, а во время охлаждения.
Цикл термической обработки быстрорежущей стали может быть сокращен, если сразу после закалки сталь обработать холодом при -75° С...-80° С. В этом случае вместо трехкратного отпуска назначают однократный отпуск (рис. 50. б).
Микроструктура стали после закалки и отпуска состоит из мартенсита и карбидов. Если температура отпуска или во время выдержки недостаточны (сталь недоотпущена), то в структуре сохраняется некоторое количество остаточного аустенита. При отпуске выше 600°С твердость быстрорежущей стали снижается в связи с распадом мартенсита и коагуляцией выделившихся карбидов.
10.4. Штамповые стали.
Штампами называют инструменты, изменяющие форму материала без снятия стружки. Стали, используемые для изготовления штампового инструмента, должны обладать высоким сопротивлением пластической деформации и износостойкостью, а в некоторых случаях (при разогреве) и повышенной теплостойкостью. При больших размерах штампов стали должны иметь высокую прокаливаемость и незначительно изменять свой объем при закалке.
Штамповые стали, применяемые при изготовлении инструментов для обработки металлов давлением, делятся на два класса в зависимости от условий деформирования металла: в холодном или горячем состоянии.
10.4.1. Стали для штампов холодного деформирования.
К инструменту, деформирующему металл в холодном состоянии, относятся вытяжные, вырезные, гибочные, формовочные, высадочные штампы, дыропробивные пуансоны, обрезные матрицы, ножи для резания материалов, волочильные доски, ролики для накатывания резьбы и др.
Рис. 50. Режимы термической обработки инструмента из быстрорежущей стали:
а - с трехкратным отпуском; б - с обработкой холодом
Все штамповые стали для холодного деформирования являются высокоуглеродистыми, заэвтектоидными, а количество легирующих элементов определяется необходимой износостойкостью и прокаливаемостью стали.
Для обработки малопрочных материалов используют стали У10, У11, У12.
Более крупные и сложные по форме штампы, предназначенные для работы в более тяжелых условиях, изготавливают из легированных сталей повышенной прокаливаемости (X, ХВГ, 7ХГ2ВМ и др.). Штампы из легированных сталей закаливают в масле, что предохраняет их от образования трещин и значительного изменения размеров.
Для изготовления инструмента, который должен иметь высокую твердость и повышенную износостойкость, а также малую деформируемость при закалке (дыропрошивные матрицы и пуансоны, матрицы глубокой высадки листового металла, матрицы и пуансоны глубокой высадки вырубных и просечных штампов сложной конфигурации и др.), применяют стали высокой прокаливаемости и износостойкости Х12М, Х12Ф1,Х6ВФ.
Для инструментов, работающих с большими ударными нагрузками (пневматические зубила, ножи для холодной резки металла, обжимные матрицы и др.), применяют стали повышенной вязкости. В эту группу входят хромокремнистые стали (4ХС, 6ХС) и стали, дополнительно легированные вольфрамом: 4ХВ2С, 5ХВ2С, 6ХВ2С. Повышения вязкости достигается снижением содержания в сталях углерода (0,4-0,6%) и повышением температуры отпуска (температура закалки 840...900°С).
Для изготовления рабочих частей штампов широко используют металлокерамические твердые сплавы с более высокой твердостью, чем инструментальные стали (твердые сплавы группы ВК с содержанием кобальта не менее 15%).
10.4.2. Стали для штампов горячего деформирования.
К инструменту, деформирующему металл в горячем состоянии, относятся штампы для кузнечного производства, которые деформируют металл, предварительно нагретый до высоких температур (1000º...1150°С). В процессе работы штампы подвергаются воздействию сложных напряжений (сжатию, растяжению, изгибу) и истирающему действию горячего металла. Кроме того, при пластической деформации рабочая часть штампа значительно нагревается. Поэтому сталь для изготовления кузнечных штампов должна иметь высокие механические свойства (прочность, вязкость, износостойкость), не только при обычных, но и при повышенных температурах, т.е. быть теплостойкой.
Теплостойкие стали применяют для изготовления тяжелонагруженного прессового инструмента, а также штампов для горизонтально-ковочных машин. Из них также изготовляют детали пресс-форм для литья под давлением магниевых, алюминиевых и медных сплавов.
При кратковременном воздействии горячего металла на штамп используют стали 5ХГМ, 5ХНМ, 5ХНВ, 5ХНВС и др. Все стали содержат одинаковое количество углерода 0,5-0,6%, что дает возможность получить требуемую твердость и прочность при достаточной вязкости.
Из этих сталей изготавливают молотовые штампы, для которых характерны большие размеры и работающие со значительными ударными нагрузками при умеренном разогреве рабочих поверхностей (примерно до 400°С).
Долговременное воздействие ударных нагрузок выдерживают стали 4Х2В5ФМ, 4ХЗВФ2М2, ЗХ2В8Ф и др.
10.5. Твердые сплавы.
Для изготовления твердых сплавов используют метод порошковой металлургии. Для этого порошки карбидов вольфрама (WC), титана (ТС) и тантала (ТаС) смешивают с кобальтом (Со), прессуют в формы и затем запекают при 1500...2000°С.
Применение твердых сплавов позволяет не только увеличить скорость обработки, но и значительно повысить износостойкость обрабатывающего и штампового инструмента. Износостойкость твердых металлокерамических сплавов увеличивается с ростом твердости и в 10 - 15 раз превышает значения, характерные для быстрорежущей стали. Сохраняется она до 800...1000°С.
Твердые сплавы делятся на три группы: одно-, двух- и трехкарбидные.
Однокарбидные твердые сплавы, которые содержат карбиды вольфрама, называют вольфрамокобальтовыми (группа ВК). В марках ВК2, ВК4, ВК6, ВК10 цифра показывает процентное содержание кобальта, остальное - карбид вольфрама. Сплавы этой группы наиболее прочные, с увеличением содержания кобальта сплавы повышают сопротивление ударным нагрузкам, одновременно снижается износостойкость.
Сплавы ВК4, ВК6 рекомендуются для чернового точения, фрезерования, рассверливания, зенкерования при обработке чугуна, жаропрочных сплавов, цветных металлов и неметаллических материалов.
Сплав ВК8 применяют для чернового точения и других видов черновой обработки, а также для волочения и калибровки труб, прутков и проволоки.
Сплав ВК10 предназначается для изготовления быстроизнашивающихся деталей. Этот сплав характеризуется высокой эксплуатационной прочностью, но сравнительно низкой износостойкостью.
Таблица 7
Сплав | WC | TiC | ТаС | Со | Твердость HRA, не менее | |
Вольфрамокобальтовая группа (ВК) | ||||||
ВК3 | - | - | 89,5 | |||
ВК4 | - | - | 89,5 | |||
ВК6 | - | - | 88,5 | |||
ВК8 | - | - | 87,5 | |||
ВК10 | - | - | 87,0 | |||
Титановольфрамокобальтовая группа (ТВК) | ||||||
Т30К4 | - | 92.0 | ||||
Т15К6 | - | 90,0 | ||||
Т5К10 | - | 88,5 | ||||
Титанотанталовольфрамокобальтовая группа (ТТК) | ||||||
ТТ7К12 | ||||||
ТТ8К6 | 90,5 | |||||
ТТ20К9 | 89,0 |
Двухкарбидные твердые сплавы помимо группы ВК содержат еще карбиды титана, поэтому их называют титановольфрамокобальтовыми (группа ТВК). В марках Т5К10, Т15К6, Т30К4 цифры после буквы Т показывают процентное содержание карбидов титана, после К – содержание металлического кобальта, остальное - карбиды вольфрама. Эти сплавы менее прочны и более износостойки, чем сплавы первой группы.
Титановольфрамовые сплавы применяют для чистового (Т30К4) и чернового (Т15К6, Т5К10) точения, фрезерования и строгания стали.
Трехкарбидные твердые сплавы содержат еще и карбиды тантала и поэтому называются титанотанталовольфрамокобальтовыми (группа ТТК). В марках ТТ7К12, ТТ8К6, ТТ20К9 цифра перед К показывает суммарное процентное содержание карбидов титана и тантала, после К - содержание металлического кобальта, остальное - карбиды вольфрама. Сплавы обладают повышенной прочностью, износостойкостью и вязкостью.
Состав (массовая доля основных компонентов, %) и твердость HRA некоторых твердых сплавов даны в таблице 7.
Титанотанталовольфрамокобальтовые сплавы применяют при черновой и чистовой обработке труднообрабатываемых материалов, в том числе жаропрочных сплавов и сталей.
Разработаны твёрдые сплавы, не содержащиеся дефицитного вольфрама. Безвольфрамовые твердые сплавы на основе Ti + Ni + Mo – сплав ТН-20 (цифра показывает суммарное содержание Ni и Mo) и на основе карбонитрида титана Ti(NC) + Ni + Mo – KHT- 16. Никель и молибден образуют связывающую матрицу, применяются при получистовом и чистовом точении и фрезеровании сталей и цветных металлов.
Вопросы для повторения раздела.
1. Каковы достоинства и недостатки углеродистых инструментальных сталей?
2. Назовите преимущества легированных сталей для режущего инструмента по сравнению с углеродистыми.
3. Укажите марки быстрорежущих сталей.
4. Каким образом достигается упрочнение быстрорежущих сталей?
5. Каким требованиям должна отвечать сталь для штампов деформирования в холодном состоянии? Приведите примеры марок сталей.
6. Укажите стали для штампов горячего деформирования.
7. Что собой представляют твердые сплавы?
8. Назовите классификацию и назначение твердых сплавов.
9. Какие Вы знаете безвольфрамовые твердые сплавы?
11. Термическая обработка деталей машин.
11.1. Коленчатые валы.
Коленчатые валы работают в условиях высоких нагрузок, а шейки вала подвергаются интенсивному износу. Термическая обработка коленчатых валов преследует две цели: повысить их прочность и износостойкость. Изготовляют коленчатые валы из стали и из высокопрочного чугуна. Коленчатые валы автомобильных и тракторных двигателей, компрессоров изготовляют из сталей 45, 50Г, 30ХГ2, 47ГТ, 40ХН и др. (горячей штамповкой). Благодаря штамповке получается хорошая макроструктура - волокна металла не перерезаются, а соответствуют конфигурации вала (рис. 51).
Рис. 51. Схема макроструктуры коленчатого вала:
а – штампованного; б – вырезанного из заготовки.
После штамповки валы подвергают нормализации – нагреву до температуры выше точки АС3 на 40–50° С и последующему равномерному охлаждению на воздухе. Применяют также нормализацию штампованных заготовок коленчатых валов с использованием тепла после горячей штамповки. Например, штампованные заготовки валов из стали 45 подвергают нормализации в специальной щелевой нормализационной печи с подвесным конвейером. Перед поступлением в рабочую камеру печи, нагретую до 850° С, штампованные заготовки валов проходят через специальный коридор, где охлаждаются с 1050–1100° С до 600–650° С. После нормализации штампованные заготовки проходят через камеру предварительного охлаждения и выдаются на воздух.
После нормализации штампованные заготовки для обработки поступают на металлорежущие станки, а затем шатунные и коренные шейки валов подвергают поверхностной закалке при индукционном нагреве, для чего применяют автоматизированные установки, на которых производят последовательный нагрев и охлаждение каждой шейки. Время нагрева и охлаждения шеек регулирует реле времени. За счет сокращения длительности охлаждения проводится самоотпуск шеек (температура самоотпуска 240–250° С). Для закалки коленчатых валов в поточной линии устанавливают специальные станки. Получают закаленный слой толщиной 3–5 мм, а твердость поверхности шеек HRC 56–62, микроструктура слоя – мелкоигольчатый мартенсит. Если закаленный слой не доходит до переходной поверхности (рис. 52, а), то вредные напряжения растяжения, выходящие на поверхность в месте обрыва закаленного слоя, располагаются вблизи переходной поверхности.
Литые коленчатые валы из высокопрочного магниевого чугуна по сравнению со стальными штампованными валами имеют преимущества, а поэтому находят широкое применение в двигателях, например автомобилей, тепловозов и т. п. Наиболее благоприятной структурой высокопрочного чугуна является структура зернистого перлита с шаровидным графитом. Структура зернистого перлита может быть получена только при определенном химическом составе и термической обработке высокопрочного чугуна.
Рис. 52. Расположение закаленного слоя на шейке вала
Рекомендуется следующий химический состав высокопрочного магниевого чугуна для коленчатых валов автомобильных двигателей: 3,4–3,6% С; 2–2,2% Si; 1,15–1,3% Мn; 0,15–0,25% Сr; 0,03–0,06% Мg; менее 0,005% 5; менее 0,12% Р. Повышенное содержание марганца в чугуне необходимо для повышения стойкости эвтектоидного цементита, чтобы при термической обработке происходила сфероидизация, а не графитизация эвтектоидного цементита.
Термическая обработка коленчатых валов проводится по следующему режиму: нормализация – нагрев до 950–960° С, выдержка 8 ч, охлаждение со скоростью 30–60° С/мин до 600° С; отпуск – нагрев до 725–740° С, выдержка 8 ч, охлаждение на воздухе. Получаемая структура – зернистый перлит и шаровидный графит, твердость НВ 207–241.
Термическую обработку коленчатых валов целесообразно проводить в печах с защитной атмосферой, и для уменьшения коробления нагревать коленчатые валы на специальных поддонах.
11.2. Зубчатые колеса.
Зубчатые колеса из цементуемых сталей. Зубчатые колеса широко применяют в машинах, механизмах и приборах различных отраслей машиностроения. Наилучшая макроструктура зубчатых колес получается при штамповке, когда расположение волокон соответствует конфигурации колеса, так как в этом случае прочность на изгиб повышается.
При выборе стали для изготовления зубчатых колес необходимо учитывать ее стоимость, обрабатываемость, прокаливаемость и деформацию колеса при термической обработке. Так как основным элементом зубчатого колеса является зуб, применяемые стали и методы упрочнения должны обеспечивать высокую контактную и усталостную прочность, прочность при изгибе, ударе и износостойкость зуба.
Цементуемые зубчатые колеса изготовляют из сталей 20Х, 12ХНЗА, 12Х2Н4А, 20Х2Н4А, 25ХГМ, 20ХН2М, 18ХГТ, 25ХГТ, 30ХГТ, 20ХГР, 18Х2Н4ВА и др.
Для подготовки структуры к обработке колес на металлорежущих станках и для улучшения механических свойств готовых зубчатых колес штампованные заготовки перед обработкой на металлорежущих станках подвергают термической обработке — отжигу (полному, изотермическому) или нормализации, или нормализации с высоким отпуском.
Наилучшей для резания (получение наименее шероховатой поверхности металла) является структура после изотермического отжига по режиму: нагрев до температуры в точке АС3 + 50° С, выдержка, кратковременное переохлаждение до 480—500° С и изотермическая выдержка при 580—600° С.
Зубчатые колеса из хромомарганцетитановых сталей (18ХГТ, 25ХГТ, 30ХГТ) подвергают газовой цементации (при температуре 920–950° С) с непосредственной закалкой из цементационной печи после предварительного подстуживания до 840–860° С. После закалки зубчатые колеса подвергают отпуску при 180–200° С. На поверхности достигается твердость HRC 56–62, а в сердцевине HRC 30–45 (нижний предел для стали 18ХГТ, верхний – для стали 30ХГТ). Микроструктура цементованного слоя – мелкоигольчатый мартенсит с мелкими включениями карбидов и небольшим количеством остаточного аустенита; сердцевины – сорбит (для стали 18ХГТ) и троостосорбит (для стали 30ХГТ).
Зубчатые колеса из хромоникелевых сталей 12Х2Н4А, 20Х2Н4А и других непосредственной закалке не подвергают – получается большое количество остаточного аустенита, что снижает твердость поверхности зуба. Поэтому зубчатые колеса из этих сталей после цементации охлаждают на воздухе, подвергают высокому отпуску при 600–650° С (для подготовки структуры цементованного слоя под закалку; во время отпуска происходит распад остаточного аустенита и мартенсита и выделяются карбиды), закаливают в масле от 800–820° С и подвергают низкому отпуску при 180–200° С.
Для уменьшения деформации зубчатых колес применяют следующие способы: 1) ступенчатую закалку; нагретые зубчатые колеса охлаждают в ванне с маслом или расплавленной солью с температурой 150–180° С и после выдержки в ванне для выравнивания температуры по сечению зубчатого колеса до температуры ванны охлаждают на воздухе до температуры 20° С; 2) закалку на специальных фиксирующих оправках, которые устанавливают в отверстии зубчатого колеса; 3) ступенчатую закалку в сочетании с фиксирующими оправками; зубчатое колесо помещают на оправку после выдержки его в горячей среде и затем охлаждают до температуры 20° С вместе с оправкой.
Зубчатые колеса из улучшаемых сталей. Зубчатые колеса изготовляют из улучшаемых сталей, например 45, 40Х, 40ХН и др., а также из стали 55ПП пониженной прокаливаемости. В зависимости от условий работы зубчатые колеса подвергают различной термической обработке: нормализации, улучшению, закалке и низкому отпуску, цианированию (нитроцементации) с последующей закалкой и отпуском.
Зубчатые колеса, работающие при низких скоростях и малых давлениях, изготовляют из стали 45 и подвергают нормализации при 850–870° С (твердость НВ 170–217) или улучшению – закалке в воде от 820–840° С и отпуску при 520–550° С (НВ 220–250). Зубчатые колеса, работающие при значительных изгибающих нагрузках и небольших скоростях, изготовляют из легированных среднеуглеродистых сталей и подвергают улучшению–закалке в масле и отпуску при 600–650° С (НВ 230–260). Зубчатые колеса, работающие при средних скоростях, средних давлениях и небольших ударных нагрузках, изготовляют из легированных среднеуглеродистых сталей. Режимы термической обработки зубчатых колес из этих сталей следующие: а) закалка в масле и отпуск при 180–200° С (НRС 50–55); б) цианирование (нитроцементация) при 830–850° С, закалка в масле и отпуск при 180–200° С (HRC 55–60); толщина слоя должна быть в пределах 0,2–0,3 мм, для чего необходима выдержка 30–50 мин при цианировании и 1–2 ч при нитроцементации.
Большое распространение в заводской практике получила поверхностная закалка зубчатых колес при индукционном нагреве. Закалка в этом случае проводится двумя методами: 1) со сквозным нагревом зубьев; 2) с нагревом только контактных поверхностей зуба (закалка «по зубу») или с одновременным нагревом контактных поверхностей и впадины (закалка «по впадине»).
11.3. Полуоси.
Полуоси являются тяжело нагруженными деталями, к которым предъявляются требования высокой статической и усталостной прочности, а также достаточно высокой твердости и износостойкости. Полуоси изготовляют ковкой-штамповкой, в результате чего направление волокон весьма точно повторяет внешние очертания детали, придавая ей наибольшую прочность. Поковки полуосей, изготовленных из легированных сталей (например, из стали 40ХГТР), подвергают нормализации (880° С) с последующим отпуском при 680–700° С. После обработки на металлорежущих станках полуоси подвергают объемной термической обработке по режиму: нагрев 860–880° С, закалка в масле, отпуск при 220°С с получением твердости HRC 50–52 или отпуск при 450–500° С с охлаждением в горячей (50° С) воде в связи с отпускной хрупкостью с получением твердости HRC 42–45. Полуоси из среднеуглеродистых сталей и подвергают поверхностной индукционной закалке с низким отпуском.
Рис. 53. Индуктор для нагрева под закалку полуоси автомобиля
Наиболее прогрессивной является технология поверхностной закалки при глубинном нагреве полуосей из стали регламентированной прокаливаемости марки 47ГТ (0,44–0,50% С; 0,9–1,2% Мn; £0,17% Si, 0,06–0,12% Тi). Для поверхностной закалки при глубинном нагреве полуосей применяют специальный станок-автомат. Нагрев полуоси 1 (рис. 53) осуществляется в индукторе, состоящем из одновитковой секции 2 для нагрева переходной поверхности фланца и многовитковой секции 3 для нагрева стержня (зазор 13 мм) и шлицевого конца (зазор 15 мм). Температура нагрева 890° С, общая выдержка 78 с.
11.4. Клапаны двигателей внутреннего сгорания.
Клапаны имеют грибовидную форму. Обычно их штампуют, в результате чего волокна располагаются соответственно конфигурации клапана. По условиям работы на двигателе клапаны разделяют на выпускные и впускные.
Условия работы головки и стержня выпускного клапана различны. Головка клапана в процессе работы сильно нагревается (до 600° С и выше), стержень изнашивается, а конец стержня изнашивается и сминается. Поэтому материал выпускного клапана должен сохранять свои механические свойства при высоких температурах (обладать жаропрочностью), не подвергаться местной закалке при остывании, не давать остаточных
Рис. 54. Схема установки для алитирования клапанов
деформаций, не подвергаться коррозии при высоких температурах, обладать высоким сопротивлением износу и смятию. Указанным требованиям удовлетворяют окалиностойкие и жаропрочные стали 40Х9С2 и 40Х10С2М, из которых в основном и изготовляют выпускные клапаны.
Эти стали имеют высокие критические точки: для стали 40Х9С2, температура в точке АС1 900° С, а.в точке АС3 970° С; для стали 40Х10С2М температура в точке АС1 900° С, а в точке АС3 950° С. После штамповки клапаны подвергают отжигу при 850–900° С (НВ 197–241). Закалку клапанов проводят двойную – всего клапана и затем конца стержня. Первая закалка (всего клапана) от 1050–1100° С с охлаждением в масле, затем отпуск при 800–850° С с охлаждением в воде (для предотвращения отпускной хрупкости), HRC 30–36. Вторая закалка (конца стержня клапана на длине 4–7 мм) от 1050–1100° С с охлаждением в масле, затем отпуск при 720–750° С, HRC – 40. Нагрев конца стержня клапана для закалки проводится с помощью т. в. ч. или в установке для концевого нагрева в электролите.
Для повышения жаростойкости головку клапана целесообразно подвергать алитированию. На рис. 54 показана схема установки для алитирования клапанов методом погружения в расплавленный алюминий. Клапаны 1, предварительно обезжиренные паром, конвейером подаются к ванне 2 и погружаются головками в расплавленный флюс (40% NаС1, 40% КС1, 10% криолита А1F3·3NaFe, 10% фтористого алюминия А1F3), где выдерживаются 3 мин. В этой же ванне находится тигель 3 с расплавленным алюминием, который автоматически поднимается в тот момент, когда над ним проходит клапан и головка клапана погружается в расплавленный алюминий (температура 720–735° С) и выдерживается 5 с. Затем тигель 3 опускается, и клапан перемещается в камеру 4, где излишек алюминия сдувается горячим воздухом. В результате алитирования на поверхности головки клапана образуется слой общей толщиной 0,04–0,05 мм, состоящий из слоя чистого алюминия и диффузионного слоя химического соединения Fe2А15. В связи с тем, что условия работы головки и стержня клапана различны, а стержень в процессе работы не нагревается, для экономии жаропрочной стали клапаны иногда изготовляют сварными: головка из жаропрочной стали, а стержень из менее легированной стали (обычно из стали, применяемой для впускных клапанов).
Впускные клапаны изготовляют в основном из сталей 40Х и 40ХН. Клапаны из стали 40Х закаливают в масле от 850–870° С и отпускают при 600–630° С (HRC 30–36). Затем закаливают конец стержня клапана от 820° С с охлаждением в масле (HRC 40–45).
Термическую обработку впускных клапанов можно проводить с использованием тепла после штамповки. При таком способе осуществляют: 1) непосредственную закалку в масле после штамповки с предварительным подстуживанием до 800–850° С или без подстуживания и отпуск при 600–630° С; 2) изотермическую закалку по режиму: штамповка поковок, перенос их в изотермическую среду (щелочь или селитру) с температурой 390–500° С, выдержка 15 мин, охлаждение в воде, промывка в растворе
хромпика и окончательная промывка в проточной воде. Наиболее, целесообразным является первый вариант как более простой.
11.5. Пружины и рессоры.
Общие сведения. Пружины и рессоры испытывают в работе многократные знакопеременные нагрузки и после снятия нагрузки должны полностью восстанавливать свои первоначальные размеры. В связи с такими условиями работы металл, применяемый для изготовления пружин и рессор, должен обладать, кроме необходимой прочности в условиях статического, динамического или циклического нагружений, достаточно хорошей пластичности, высокими пределами упругости и выносливости и высокой релаксационной стойкостью, а при работе в агрессивных средах (атмосфере пара, морской воде и др.) должен быть также и коррозионно-стойким.
Высокие свойства (максимальные пределы упругости и выносливости) пружины и рессоры имеют при твердости HRC 40–45 (структура–троостит), которая достигается после закалки (с равномерным и полным мартенситным превращением по всему объему металла) и среднего отпуска при 400–500° С (в зависимости от стали).
Для изготовления пружин применяют углеродистые и легированные стали, а для приборов – сплавы цветных металлов, главным образом бериллиевую бронзу. Рессоры изготовляют только из легированных сталей.
Пружины и рессорные листы упрочняют следующими способами: 1) холодной пластической деформацией с последующим низкотемпературным нагревом (отпуском, старением); 2) закалкой с последующим отпуском (упрочнение в результате мартенситного превращения); 3) закалкой с последующим старением (упрочнение в результате дисперсионного твердения).
Упрочнение холодной пластической деформацией. Для изготовления средних и мелких витых пружин широко применяют патентированную проволоку (диаметром до 8 мм), изготовляемую из среднеуглеродистых сталей с содержанием марганца 0,3–0,6% и сталей 65Г и 70Г с содержанием марганца 0,7–1,0%, а также из углеродистых инструментальных сталей. После навивки в холодном состоянии пружины подвергают низкому отпуску (175–250° С, выдержка 15–20 мин в зависимости от диаметра проволоки) для снятия напряжений, повышения пределов упругости и выносливости, релаксационной стойкости и обеспечения стабильности размеров пружины.
Упрочнение закалкой с последующим отпуском. Для изготовления пружин, упрочняемых термической обработкой (закалкой и отпуском), применяют углеродистые (65, 75) и легированные (60С2А, 50ХФА, 60С2Н2А и др.) стали, для рессор – только легированные стали, для пружин, работающих в агрессивных средах–нержавеющие стали 30X13, 40X13, 12Х18Н10Т и др.
Углеродистые стали в связи с их малой прокаливаемостью применяют для изготовления пружин из проволоки диаметром до 6 мм. Преимущество кремнистой стали по сравнению с углеродистой – ее повышенная прокаливаемость и более высокие прочность и пластичность. Недостатком этой стали является повышенная склонность к образованию поверхностных дефектов при горячей обработке, обезуглероживанию и графитизации. В результате обезуглероживания наружной поверхности пружин или рессор резко снижается их сопротивляемость длительным нагрузкам. Поэтому нагрев пружин и рессор необходимо проводить с предохранением от обезуглероживания или (для устранения вредного влияния обезуглероженного слоя) подвергать их после термической обработки обдувке дробью.
Нержавеющие стали применяют для изготовления пружин, работающих в коррозионной среде и повышенных (до 400° С) температурах. Пружины из высокохромистых нержавеющих сталей мартенситного класса (30X13, 40X13 и др.) закаливают от температуры 1000–1050° С в масле (пружины из стали 40X13 можно охлаждать также и на воздухе); структура после закалки – мартенсит. Отпуск после закалки проводят в зависимости от условий работы пружин: при 550–500° С для пружин, работающих при повышенных температурах, и при 300–350° С – для пружин, работающих при температуре 20° С (при более высокой температуре отпуска понижается стойкость к коррозии под напряжением). Очень высокая прокаливаемость этих сталей позволяет изготовлять из них пружины больших сечений.
Цилиндрические пружины нагревают в горизонтальном положении. Для предупреждения коробления при нагреве на поду печи располагают швеллерные балки, на которые укладывают пружины. Для закалки пружин сжатия применяют приспособление, показанное на рис. 55, представляющее собой стальной стакан (внутренний диаметр которого на 0,3–0,4 мм больше наружного диаметра пружины, а высота на 10–12 мм больше высоты пружины) с отверстием в дне, равным среднему диаметру пружины. В приспособление помещают пружину и загружают его в печь. После нагрева до заданной температуры и выдержки приспособление вместе с пружиной вынимают из печи и охлаждают в масле (в горизонтальном положении при непрерывном покачивании). Закаленную пружину выталкивают из приспособления, нажимая на нее со стороны отверстия в стакане.
Коробление пружины, полученное при закалке (рис. 56, а), можно устранить при отпуске. Закаленную пружину надевают на оправку и зажимают клином (рис. 56, б). В таком состоянии осуществляют отпуск пружины. После отпуска на оправке коробление пружины, полученное при закалке, устраняется (рис. 56, в).
|
|
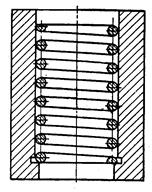
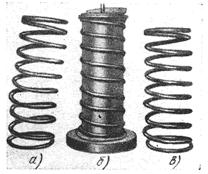
11.6. Детали подшипников.
Общие сведения. Наряду с высокими точностью обработки и качеством отделки рабочих поверхностей металл для деталей подшипников качения и термическая обработка их являются основными факторами, определяющими срок службы подшипников. При работе подшипников качения кольца, шарики и ролики подвергаются: а) воздействию высоких удельных нагрузок переменного характера, вследствие чего в металле возникают явления усталости, в частности развивается контактное выкрашивание; б) износу от трения; в) химическому износу вследствие контакта с атмосферой или смазкой, содержащей примеси; г) абразивному износу; д) напряжениям от раздавливающей нагрузки.
Для изготовления деталей подшипников применяют стали ШХ15 (0,95–1,05% С; 1,30–1,65% Сr; 0,2–0,4% Мn; 0,17– 0,37% Si) и ШХ15СГ (0,95–1,05% С; 1,30–1,65% Сr; 0,9–1,2% Мn; 0,40–0,65% Si); в обеих сталях содержится не более 0,02% 5 и 0,027% Р. После ковки структура стали – пластинчатый перлит и тонкая разорванная карбидная сетка, твердость НВ 255–340, обрабатываемость стали с такой структурой и твердостью затруднена.
Для снижения твердости до НВ 178–207 и получения структуры зернистого перлита, обеспечивающей хорошую обрабатываемость, заготовки подвергают отжигу при 780–800° С с последующим медленным охлаждением (15–25° С/ч) в интервале температур 650–760° С. Ускоренное охлаждение при отжиге (100–300° С/ч) вызывает образование мелкодисперсной структуры с повышенной твердостью. Очень медленное охлаждение (~5° С/ч) приводит к образованию крупнозернистого перлита; такая структура обладает низкой твердостью, но неблагоприятна для последующей закалки. Нормальной структурой после отжига является структура мелкозернистого перлита.
На процесс закалки подшипниковых деталей влияет хром. Хром увеличивает количество избыточных карбидов в структуре стали и уменьшает чувствительность к перегреву. Вследствие присадки хрома уменьшается критическая скорость закалки и увеличивается прокаливаемость. Небольшая критическая скорость закалки необходима для того, чтобы можно было детали закаливать в масле. При закалке в масле происходит частичный отпуск мартенсита, что снижает напряжения.
Температура закалки подшипниковых сталей колеблется в пределах 790–870°С в зависимости от массы деталей: чем крупнее деталь, тем выше температура закалки. Охлаждение проводится в масле (кольца, ролики) или в растворе соды, или поваренной соли в воде (шарики). После закалки и отпуска твердость HRC 62–65. Оптимальной структурой закаленной подшипниковой стали является скрытокристаллический мартенсит с равномерно распределенными мелкими избыточными карбидами.
Вопросы для повторения раздела.
1. Какова технология термообработки коленчатых валов?
2. Какие из чугунов используются для производства коленчатых валов? Укажите режим термообработки и структуру после нее.
3. Укажите факторы, которые необходимо учитывать при выборе стали для изготовления зубчатых колес.
4. Какие технологии используют для термообработки зубчатых колес?
5. Обоснуйте технологию изготовления полуосей.
6. Какие стали используют для производства клапанов двигателей внутреннего сгорания?
7. С какой целью производится алитирование головки клапана?
8. Назовите способы упрочнения пружин и рессор.
9. Как можно избежать коробление пружин?
10. Какие стали и почему используются для изготовления деталей подшипников качения?