Процесс десульфурации можно представить уравнением реакции:
[S] + (CaO) = (CaS) + [O]
Константа равновесия реакции равна: kp = (74)
В результате можно записать:
[S] = (75)
Выразим значение XCaS - мольную долю сульфида кальция в шлаке через концентрацию серы, тогда XCaS = (76)
где - сумма молей компонентов шлака - CaO, CaS, SiO2, Ai2O3 и др. в 100 г. шлака. Подставляя выражение (3) в ур-ние (2) получим:
(77)
В результате логарифмирования ур-ния (4) получаем:
lg LS = lg (78)
В этом ур-нии первое слагаемое является величиной постоянной при неизменной температуре, второе слагаемое определяется основностью шлака, а третье - активностью кислорода и коэффициентом активности серы в расплаве.
При рафинировании простых, не легированных сталей можно принять значение fS = 1 и ур-ние (78) запишется в виде:
(79)
При экспериментальном изучении распределения серы между жидким металлом и шлаками системы CaO - MgO - Al2O3 - SiO2 для коэффициента распределения серы LS получили эмпирическое уравнение, имеющее ту же структуру, что и уравнение (6)
|
|
(80)
Эффективность процесса десульфурации обычно оценивают степенью десульфурации - (в долях)
. Выведем соотношение между LS и
. Для этого запишем два уравнения:
где: mме и mшл массы металла и шлака при обработке стали в ковше.
Из ур-ния (82) получаем:
mме×([S]H - [S]K) = mшл×(S)K = mшл×LS×[S]K. (84)
Поделив выражение в уравнении (84) на [S]H получим:
mме = mшл×LS
(85)
Введем в ур-ние (85) величину кратности шлака (в долях) тогда получаем из ур-ния (85):
Принимая , имеем:
; и тогда:
; или
Таким образом соотношение между и LS имеет вид:
(в долях или в процентах при умножении на 100).
Из анализа ур-ния (80):
следует, что величина LS - коэффициента распределения серы между рафинировочным шлаком и металлом определяется в основном двумя факторами:
а) основностью шлака
б) активностью кислорода в металле в процессе рафинирования шлаком в ковше.
Существенное влияние на величину LS должна оказывать величина aO. Учитывая, что одновременно с рафинированием стали шлаком происходит процесс ее раскисления ферромарганцем, ферросилицием и алюминием, необходимо предварительно рассчитать значение aO в раскисленном металле. При получении конструкционного металла элементом, определяющим величину aO в стали является алюминий, содержание которого для этого класса сталей составляет в среднем 0,05 %. По величине KAl=[Al%]2×[aO]3 можно рассчитать равновесную с алюминием активность кислорода - aO. Однако, при этом необходимо иметь в виду, что используемое для расчета aO значение KAl будет различным при обработке в ковшах с различной огнеупорной футеровкой; что было установлено экспериментально с использованием кислородных зондов для измерения активности кислорода [1]. Результаты этих исследований представлены в таблице № 1.
|
|
Таблица 1
Значения KAl=[Al]2×[aO]3
Кислая, шамотная футеровка | Высокоглиноземистая, смолодоломитовая | |||
без SiCa | с добавкой SiCa | без SiCa | с добавкой SiCa | |
Величина KAl | 10-12 | 10-12,5 | 10-13 | 10-13,5 |
Ниже представлены расчеты коэффициента распределения серы при обработке стали в сталеразливочных ковшах синтетическими шлаками и ТШС.
3.1. Обработка стали синтетическими шлаками.
Попробуем рассчитать значения LS и при обработке стали синтетическим шлаком в сталеразливочном ковше с различной огнеупорной футеровкой.
Задание № 1: Рассчитать величины LS и при обработке стали в ковше синтетическим шлаком состава: CaO = 55 %, Al2O3 = 35 %, SiO2 = 5 %, MgO = 5 %, FeO = 1 %. Расход синтетического шлака равен 40 кг/т. Концентрация алюминия в стали Al = 0,05 %. Расчеты провести для двух вариантов: а) обработка металла в ковше с шамотной футеровкой, KAl = 10-12
б) обработка металла в ковше с высокоглиноземистой футеровкой, KAl = 10-13. Температура металла в обоих случаях равна 1600OC
Вариант а). Рассчитаем активность кислорода в расплаве KAl=[Al]2×[aO]3=10-12, при этом = 0,00075 %. В этом случае: lg LS =
; LS=160
.
Вариант б). Рассчитаем активность кислорода в расплаве KAl=[Al]2×[aO]3=10-13, при этом = 0,00034 %. В этом случае имеем: lg LS = -2,78 + 1,65 + 3,79 = + 2,56.
LS=330, т. е. еще более высокие степени десульфурации, практически недостижимые на практике.
В обоих случаях расчетов получили очень высокие значения LS, однако недостигаемые на практике.
Причиной столь значительного расхождения значений LS и , рассчитанных по ур-нию (80) и наблюдаемых на практике, по нашему мнению, заключается в том, что в проведенных расчетах не учитывается процесс заметного разбавления состава рафинировочного шлака за счет попадания в него продуктов реакции раскисления стали, разрушения футеровки ковша, а в ряде случаев и попадания печного шлака при выпуске металла. Полный баланс шлака при рафинировании металла в сталеразливочном ковше можно записать так:
= Mсил. шл. + Моксиды + Мпечной шлак + Мфутеровка
Ниже сделана попытка показать влияние разбавления рафинировочного шлака на коэффициенты LS и .
Задание № 2: Рассчитать значения LS и при обработке стали в сталеразливочном ковше синтетическим шлаком предыдущего состава в количестве 40 кг/т. Условно задаемся, что в ковш попадает 5 кг/т печного шлака состава CaO = 45 %, SiO2 = 15 %, MnO = 25 %, Al2O3 = 5 % и из футеровки ковша состава SiO2 = 50 % и Al2O3 = 30 % переходит в процессе обработки 2 кг/т материала футеровки в рафинировочный шлак. Расчет количества оксидов, переходящих в рафинировочный шлак в результате процесса раскисления металла ведем исходя из следующих условий проведения процесса: раскисление марганцем проводим исходя из условий получения в стали 0,4 % Mn, угар Mn принимаем равным 15 %; содержание кремния в стали задаем равным 0,45 % Si, угар кремния задаем 20 %, алюминия = Al = 0,05 %, угар алюминия задаем 80 %. Результаты расчетов представлены в таблице № 2.
Таблица № 2
Количество оксидов, образующихся при раскислении
(расчет на 1 т. стали)
Элемент | Концентрация в стали, % | Вводится в металл с учетом угара, % | Угар элемента, % | Образуется оксидов, кг |
Марганец, Mn | 0,40 | 0,47 | 0,07 | 0,90 |
Кремний, Si | 0,45 | 0,562 | 0,112 | 2,40 |
Алюминий, Al | 0,05 | 0,250 | 0,20 | 3,70 |
Итого | 7,00 кг |
Изменение состава рафинировочного шлака к концу обработки представлено в табл. 3.
Таблица № 3
Изменение состава рафинировочного шлака.
Материал | Кол-во, кг | Состав материала, кг | ||||
CaO | Al2O3 | SiO2 | MgO | MnO | ||
1. Синтетический шлак | 22,0 | 14,0 | 2,00 | 2,0 | - | |
2. Оксиды - продукты раскисления | 7,0 | - | 3,70 | 2,40 | - | 0,90 |
3. Печной шлак | 5,0 | 2,25 | 0,25 | 0,75 | - | 1,25 |
4. Футеровка ковша | 2,0 | - | 0,60 | 1,00 | - | - |
Итого: | 54,0 | 24,25 | 18,55 | 6,15 | 2,0 | 2,15 |
Состав конечного рафинировочного шлака, % | 45,0 | 35,0 | 12,0 | 4,0 | 4,0 |
Рассчитаем значения LS и после разбавления синтетического шлака продуктами раскисления, попадания ковшевого шлака и футеровки ковша для двух вариантов футеровки
|
|
а) шамотной KAl=10-12
б) высокоглиноземистой KAl=10-13. *
Вариант а). Принимаем состав конечного рафинировочного шлака из табл. 3, aO = 0,00075 % (футеровка шамотная)
, LS=32,7
Вариант б). Состав конечного рафинировочного шлака принимаем так же, aO = 0,00016 % (футеровка высокогл.)
,LS=151
Усредненные значения коэффициента LS при обработке синтетическим шлаком составили . Следовательно, величины, характеризующие десульфурирующую способность синтетического шлака - LS и
существенно снижаются к концу обработки за счет заметного обогащения шлака кислыми (SiO2) и полукислыми (Al2O3) компонентами и значения LS и
приближаются к практическим данным, что и является подтверждением необходимости расчета значений LS и
по ур-нию (80) с учетом протекания процессов разбавления исходного синтетического шлака оксидами - продуктами раскисления металла, печным шлаком и продуктами эрозии футеровки. Влияние процесса разбавления исходного рафинировочного шлака за счет указанных выше источников должно еще более сильно проявиться при использовании ТШС - твердошлаковых смесей для десульфурации стали. Связано это с тем обстоятельством, что расход ТШС обычно составляет в пределах 8 - 17 кг/т. стали, что примерно в 3 - 5 раз меньше, чем расход синтетического шлака из-за сильного охлаждающего эффекта.
3.2. Обработка стали ТШС.
В последнее время для внепечной обработки стали с целью десульфурации вместо синтетического шлака все чаще используют так называемые ТШС - твердо - шлаковые смеси.
Основным требованием к выбираемому составу ТШС является обеспечение таких составов шлаковой рафинировочной смеси, чтобы после присадки ТШС в ковш она как можно быстрее переходила в жидкое состояние т. е. чтобы Tпл образующейся шлаковой смеси была ниже температуры металла в сталеразливочном ковше, что повышает кинетические возможности развития процесса десульфурации, что особенно важно при обработке ТШС.
|
|
Составы и способы ввода ТШС на различных металлургических заводах сильно различаются в зависимости от конкретных условий работы.
Так на Руставском металлургическом комбинате комплексная технология обработки стали в ковше включает продувку металла инертным газом и одновременно подачу ТШС.
Шихтовые материалы ТШС включали известь (45 - 65 %), отходы ПВА (производство вторичного алюминия) (20 - 45 %), вулканический шлак (10 - 20 %), доломит (10 - 20 %). В результате расплавления получали усредненный состав рафинировочного шлака: CaO = 50 %, SiO2= 10 %, Al2O3 = 36 %, MgO = 3 %, FeO = 1 %. Температура плавления этого шлака составляла 1350O С. Время плавления навески массой 1 % от массы металла составляла 5 мин. [2]
На комбинате «Азовсталь» сравнивали различные режимы раскисления трубного металла алюминием при обработке ТШС и синтетическими шлаками. В результате экспериментов установили, что с точки зрения экономии расхода алюминия наиболее оптимальными являются технологии с раскислением металла алюминием не в сталеразливочном ковше, а на УДМ. Однако, степень десульфурации металла в ковше при обработке ТШС при этом уменьшается, т. е. еще раз подтвердился тезис о лучшей десульфурации глубоко раскисленной стали. [3]
Задание: Рассчитать значения LS и при обработке стали смесями Руставского металлургического комбината т. е. CaO = 50 %, Al2O3 = 36 %, SiO2 = 10 % и MgO = 3 %. Обработку стали проводили в ковше с шамотной футеровкой т. е. принимали KAl=10-12, расход ТШС принимали равным 10 кг/т.
Решение: Рассчитываем значение LS - коэф. распределения серы при обработке ТШС в сталеразливочном ковше:
LS = - 2,78 + 0,86 - lg aO = - 2,78 + 1,36 + 3,125 = 1,68; Величина
= 48,5 и
= 32 %.
Полученные расчетные значения и достаточно хорошо совпадают с практическими результатами, полученными на Руставском металлургическом заводе. Технология операции внепечной обработки при этом была следующей: продувку металла инертным газом через дно начинали сразу с момента появления металла на желобе. После наполнения металлом 1/5 - 1/4 высоты ковша производили присадку ферросплавов, а затем вводили ТШС в кол-ве 10 кг/т. Величины на отдельных плавках при этом изменялись от 29,4 до 40,2 % при среднем значении, равном
= 34,8 %. Если бы обработка стали ТШС указанного состава проводилась бы в высокоглиноземистых ковшах или в ковшах со смолодоломитовой футеровкой, расчетная величина LS составила бы:
LS = - 2,78 + 1,36 + 3,79 = + 2,37; LS = 234 и = 0,7 (70%).
Однако, при обработке стали ТШС, также как и при обработке синтетическим шлаком, одновременно проходит процесс разбавления рафинировочного шлака продуктами раскисления, что также должно приводить к снижению LS, причем более резкому, чем при обработке синтетическим шлаком, так как расход ТШС примерно в 4 раза меньше чем синтетического шлака.
Задание: Рассчитать изменение величины LS при обработке ТШС заданного состава и при условии, что раскисление стали проводится теми же раскислителями и с такими же угарами, как и в случае обработки металла синтетическим шлаком.
Решение: Полный баланс разбавленного рафинировочного шлака представлен в табл. 4.
Таблица № 4
Материал | Количество, кг | Количество оксидов, кг | ||||
CaO | Al2O3 | SiO2 | MgO | MnO | ||
1. ТШС | 10 кг | 3,6 | 1,0 | 0,3 | - | |
2. Оксиды - продукты раскисления | 7 кг | - | 3,7 | 2,40 | - | 0,90 |
3. Печной шлак (CaO = 45%, SiO2 = 15%, MnO = 25%, Al2O3 = 5%) | 5 кг | 2,25 | 0,25 | 0,75 | - | 1,25 |
4. Футеровка ковша (SiO2 = 50%, Al2O3 = 30%) | 2 кг | - | 0,60 | 1,00 | - | - |
Итого: | 24 кг | 7,25 | 8,15 | 5,15 | 0,3 | 2,15 |
Конечный состав рафинировочного шлака. | 100 % | 31,0 | 35,0 | 22,0 | 3,0 | 9,0 |
Рассчитаем значения LS и для периода окончания обработки металла ТШС с разбавлением рафинировочного шлака при аO = 7,5×10-4 (шамотная футеровка)
Вариант 1. (шамотная футеровка)
Вариант 2. - высокоглиноземистая футеровка
Для варианта обработки стали ТШС в высокоглиноземистом ковше имеем следующие значения при аO = 0,00016 %
Усредненные значения коэффициентов распределения LS при обработке металла ТШС (10 кг/т) в шамотном ковше составят
При обработке металла в высокоглиноземистом ковше ТШС (10 кг/т) величина
Полученные расчетные результаты можно сравнить с данными, полученными О. К. Токовым с соавторами [4] при обработке конвертерной стали ТШС состава (CaO: CaF2 = 3: 1) с расходом ТШС от 8 до 19 кг/т стали.
Степень десульфурации стали на плавках без продувки аргоном изменяется в пределах 21 - 30 %, с продувкой аргоном 41 - 50 %, что совпадает с результатами расчетов в ковшах с шамотной футеровкой. С увеличением расхода ТШС с 7 до 18 кг/т, величина возрастала с 30 до 45 %. Содержание алюминия в стали оказывало заметное влияние на
при обработке ТШС. Так увеличение Al в стали с 0,004 до 0,012 % приводило к росту
с 35 % до 48 - 50 %. При обработке низкоуглеродистых («передутых») плавок степень десульфурации заметно падала:
[C%] | < 0,04 | 0,04 - 0,06 | 0,07 - 0,09 | > 0,09 |
![]() | 24,3 | 38,6 | 41,3 | 42,8 |
В работе Токового О. К. [4] было установлено заметное изменение состава рафинировочного шлака в процессе слива металла. (табл. 5)
Таблица № 5.
Время отбора пробы | MnO | SiO2 | S | CaO |
Середина | 0,45 | 9,14 | 0,54 | 52,9 |
слива | 0,24-0,85 | 4,90-13,90 | 0,43-0,70 | 48,3-58,5 |
Окончание | 3,31 | 17,5 | 0,39 | 50,75 |
слива | 0,94-5,4 | 15,2-18,5 | 0,32-0,56 | 48,5-54,2 |
Время отбора пробы | å FeO | CaF2 | Al2O3 |
Середина | 1,19 | 13,2 | 16,2 |
слива | 0,85-1,15 | 3,6-20,1 | 8,9-37,9 |
Окончание | 6,56 | 5,97 | 10,67 |
слива | 1,91-15,1 | 2,28-10,45 | 5,68-16,00 |
Эффективность десульфурации стали ТШС уменьшалась с понижением исходного содержания серы в металле, так при [S]нач = 0,030 %, = 40 %; при [S]нач = 0,020 %,
= 35 %; и при [S]нач = 0,10 %,
= 30 %.
4. Перемешивание и дегазация стали в ковше при продувке нейтральным газом.
Перемешивание в ковше необходимо для усреднения состава и температуры металла, в том числе при вводе различных реагентов, при необходимости охлаждения и нагрева металла, а также рафинирования покровным шлаком. Лишь после перемешивания отобранная проба металла и измеренная температура характеризуют состояние металла в целом.
С целью перемешивания нейтральный газ (аргон или азот) подают сверху или снизу. Сверху газы вдувают через погружную фурму, снизу - через пористые огнеупорные пробки в днище ковша.
Важнейшей характеристикой процесса является время полного перемешивания, характеризующее 95% гомогенизации расплава.
Время полного перемешивания можно оценить по уравнению:
t=k·e-n (86)
где k=600±100
k - константа, составляющая по данным различных исследований 600¸800
n - показатель степени, колеблющийся в пределах -0,25 ¸ -0,40.
Для нахождения времени полного перемешивания необходимо определить удельную мощность перемешивания e (кВт/т):
(87)
где V - расход газа, м3/мин
Т - температура металла, К
Gст - масса стали, т
r - плотность металла, кГ/м3
g - гравитационное ускорение, м/с2
Н - глубина погружения фурмы, м
Р - давление поступающего газа, Па
Для жидкой стали r=7000 кГ/м3 и тогда:
(88)
Следует учитывать, что глубина погружения фурмы должна быть не менее, чем на 0,5 м меньше, чем высота металла в ковше. Расход газа зависит от емкости ковша и составляет в среднем для ковшей 80 т 0,6 м3/мин; 160т - 1,0 м3/мин; 330т - 1,4 м3/мин.
При продувке нейтральным газом в ковше образуется газометаллическая эмульсия. В связи с ограниченностью объема ковша расход нейтрального газа ограничен. Если принять запас вместимости ковша 5-10% (это соответствует 0,007-0,012 м3/т стали), то в каждый момент времени в объеме ковша может быть не более Gст (0,007-0,012): м3 аргона при температуре стали, что соответствует 0,001-0,002 м3 при комнатной температуре.
Максимально возможный расход аргона составляет:
(89)
где rст - плотность стали, кг/м3
Н - глубина погружения фурмы, м
W - скорость всплывания пузырей, принимаемая равной 0,3 м/сек
Размеры ковшей приведены в приложении 2.
За время выпуска и продувки происходит падение температуры металла связанное с потерей тепла, связанной с прогревом футеровки ковша и теплопередачей в атмосферу (при продувке интенсивность прогрева футеровки и теплопередача в атмосферу увеличиваются) и с теплом, уносимым нейтральным газом.
При отсутствии продувки во время выпуска в ковш падение температуры металла составляет 25-40°С (меньшие падения температуры относятся к предварительно хорошо прогретым ковшам). При продувке нейтральным газом падение температуры металла составляет: в первые 3-4 мин продувки от 2 до 4°/мин, в последующие - около 1°/мин.
Охлаждение металла за счет нагрева нейтрального газа можно рассчитать из уравнения теплового баланса:
(90)
или
VгСгDТг=МстСстDТст (91)
где Vг - расход газа, м3/кг
Сг - теплоемкость газа, кДж/м3
DТг - температура нагрева газа, К
Мст - масса стали, кг
Сст - теплоемкость стали, кДж/кг
DТст - изменение температуры стали, К
Теплоемкость аргона СAr=0,93 кДж/м3, азота СN2=0,78, стали 0,87 кДж/кг. Температуру инертного газа, удаляемого из стали, можно принять равной температуре стали.
В процессе продувки пузырьки нейтрального газа экстрагируют из жидкой стали растворенные в ней газы (водород и азот). Снижение содержания растворенных газов описывается уравнением Геллера, в упрощенной форме имеющего вид:
(92)
где Vг - расход нейтрального газа, м3/т;
Мг - молекулярная масса удаляемого газа;
- константа растворения газа (реакция 1/2Г2=[Г];
);
Р - давление над расплавом, МПа;
[Г]н и [Г]к - начальное и конечное содержание растворенного в стали газа.
Константы равновесия растворения газов равны:
(93)
(94)
На основании полученных результатов делается вывод о том, возможно ли на практике достигнуть требуемого содержания газов при продувке нейтральным газом.
На следующем этапе необходимо определить время продувки для получения требуемого содержания растворенных газов при максимальном расходе нейтрального газа (уравнение 84). Полученные результаты относятся к случаю, когда достигается состояние равновесия. В реальных условиях такое состояние не достигается. Степень приближения к равновесию составляет a=0,7-0,8. Тогда фактическое время, необходимое для требуемого снижения содержания газов, составляет:
(95)
5. Изменение температуры стали в ходе внепечной обработки.
Важной задачей является определение оптимальной температуры выпуска металла из конвертера. Исходной точкой при этом является необходимая температура разливки. Затем учитывают изменение температуры металла при выпуске, раскислении и легировании стали, продувке нейтральным газом, вакуумировании и во время разливки стали. Ход изменения температуры во время внепечной обработки позволяет принять решение о том, необходимо ли для конкретных условий использование установки ковш-печь. Принятие решения основывается на графике изменения температуры в ходе внепечной обработки, рис. 2
t°C
|
|
|
|
|
|
|
|
|
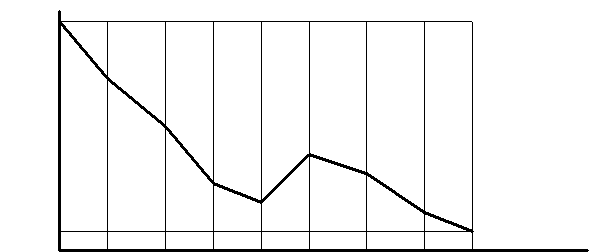
в кристаллизаторе
в промковше
в ковше на разливке
в ковше печи
в ковше после вакуумирования
в ковше перед вакуумированием
в ковше после продувки
в ковше после выпуска
выпуск стали
Рис. 2
На первом этапе построения графика определяются величины Dt°1, Dt°2, Dt°3, Dt°4. Затем последовательно оцениваются перепады температур Dt°8, Dt°7, Dt°6. Все определенные величины наносятся на график и определяется необходимая степень нагрева металла на установке ковш-печь Dt°5.
Во время выпуска стали из конвертера температура металла изменяется (Dt°1) по следующим причинам:
- за счет теплоизлучения струи металла в атмосферу и прогрев футеровки ковша
- за счет добавки легирующих
- за счет добавки раскислителей
- за счет прогрева и плавления теплоизолирущих и десульфурирующих добавок
Dt°1=Dt°1, фут+Dt°1, лег+Dt°1, раск+Dt°1, смеси (86)
За счет теплоизлучения и прогрева футеровки температура стали падает (Dt°1, фут) на 30-50° в зависимости от вместимости ковша и степени предварительного прогрева его футеровки (чем больше вместимость ковша и температура прогрева футеровки тем меньше теплопотери).
При легировании металла (10кг/т стали) температура металла падает (Dt°1, лег) следующим образом:
ферромарганец (75% Mn) | -14° |
феррохром (70% Cr) | -20° |
никель | -12° |
ферросилиций (75% Si) | +16° |
ферросилиций (45% Si) | 0° |
угольный порошок | -14° |
При раскислении алюминием температура стали возрастает (Dt°1, раск) на 10-20° в зависимости от содержания углерода в стали (меньшие значения для повышенных содержаний углерода).
Прогрев теплоизолирующих и десульфурирующих смесей снижает температуру (Dt°1, смесь) на 20-25° при добавках 10 кг/т стали.
При продувке нейтральным газом температура стали снижается в результате нагрева газа до температуры металла и ускорение теплопередачи от металла к футеровки и в атмосферу за счет интенсификации перемешивания. Теплопотери за счет нагрева нейтрального газа рассчитывают по уравнению (83), а за счет ускорения теплопередачи температура стали первые 2-3 мин падает со скоростью 2,5-5,0 °/мин и в дальнейшем 1,0-1,5 °/мин (меньшие значения относятся к ковшам большей вместимости).
На всех этапах выдержки металла в ковше и его транспортировки температура падает на 0,5-1,0 °/мин (меньшие значения относятся к ковшам большей вместимости). Исходя из этого рассчитывают величины Dt°3, Dt°6.
За время вакуумирования температура стали падает на 30-70° в зависимости от время вакуумирования (скорость снижения температуры составляет для 100 т ковша 2-3 °/мин, 300т ковша 0,7-1,3 °/мин.
Исходя из проведенных расчетов теплопотерь определяют необходимое время нагрева стали на установке ковш-печь. Скорость нагрева составляет 2-4 °/мин. При разработке температурного режима внепечной обработки стали (рис. 2) следует иметь ввиду возможность совмещения в одном агрегате ряда технологических операций: обработки шлаковыми смесями, раскисления, вакуумирования, подогрева.
Приложение1.
Состав различных материалов принимающих участие в шлакообразовании:
|
Материал | CaO | SiO2 | Al2O3 | MgO | S | CO2 | H2O |
Известь | 85,0 84,0 | 2,0 3,0 | 0,8 2,8 | 2,0 7,0 | - - | 9,0 3,1 | 1,1 - |
Миксерный шлак | 20-25 | 45-50 | 5-7 | 2-8 | 0,30-0,45 | - | - |
Шлак после внедоменной десульфурации | 20-30 | 35-55 | - | 5-20 | 1-4 | - | - |
Футеровка | 2,0 | 2,0 3,0 1,6 | 2,0 1,8 0,3 | - - - | - - - | - - - | |
Загрязнения металлолома | - | - | - | - | - |
Приложение 2.
|
Емкость, т | высота | средний диаметр |