Сущность обработки металла давлением состоит в целенаправленной пластической деформации, придающей ему определенные форму и размеры без разрушения или с разрушением, в ходе которой измельчается грубозернистая литая структура, устраняются пористость и рыхлость, улучшается металлургическое качество и создается благоприятная ориентировка вновь образовавшихся структурных составляющих металла.
Вследствие благоприятных структурных изменений, происходящих при обработке давлением, металл получает более высокий комплекс прочностных и пластических свойств по сравнению с литым. При горячей обработке давлением, когда металл обладает большой пластичностью при малой прочности, его зерна вытягиваются итрансформируются в волокна.
Волокнистое строение металла обеспечивает важные преимущества по сравнению с обычной зернистой структурой, поскольку прочность деформированного металла на разрыв вдоль волокон оказывается значительно выше, чем в поперечном направлении.
|
|
То же можно сказать и о сопротивлении срезающим нагрузкам: прочность на срез поперек волокон значительно выше, чем вдоль них. Зная характер нагружения отдельных элементов деталей в эксплуатационных условиях, можно еще при изготовлении заготовок придавать волокнам наивыгоднейшую ориентировку, отвечающую характеру нагружения соответствующих элементов деталей, и этим обеспечивать большой запас прочности деталей. Например, показанное на рис. 4.25, а изготовление зубчатого колеса из прутка где растягивающие напряжения, возникающие при изгибу зуба направлены поперек волокон, а следовательно прочность зубьев будет пониженной. Изготовленное зубчатое колесо осадкой рис. 4.25, б из отрезка прутка круглого сечения волокна получаются радиального направления. В этом случае все зубья будут равнопрочны, а растягивающие напряжения, возникающие в зубьях при изгибе направлены вдоль волокон. При этом возрастает не только прочность зубьев, но и увеличивается износостойкость.
Рис 4.25. Схемы макроструктуры зубчатых колес, изготовленных различными способами. |
4.3.1. Прокатка. Прокатка представляет собой процесс пластической деформации слитка или иной продолговатой металлической заготовки между двумя вращающимися валками, расстояние между рабочими поверхностями которых меньше высоты заготовки. Целью прокатки является получение разнообразной продукции, различающейся профилями и размерами поперечного сечения, а также балок, прутков и составляющей, так называемый сортамент проката. Сортамент стального проката включает (рис. 4.26):
|
|
Рис. 4.26. Профили сортового проката (а) и периодического профиля (б). |
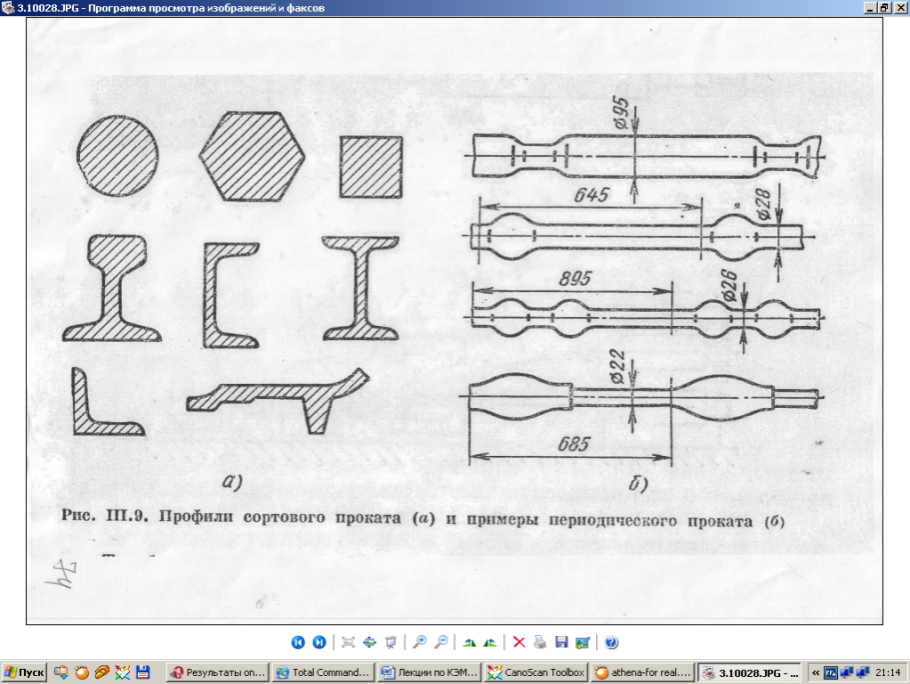
периодический прокат (рис. 4.26, б) – прокат с периодически изменяющимся по длине профилем. Он используется в качестве заготовок для штамповки (например, заготовок шатунов автомобильных двигателей) или непосредственно для механической обработки.
специальный прокат включает в себя вагонные колеса, шпунтовые сваи, автоободья и т.д.;
трубы бесшовные различного диаметра с разной толщиной стенок, разнообразного назначения;
листовой прокат делится на толстолистовую сталь толщиной свыше 4 мм и тонколистовую 0,2-3,75 мм;
Существуют также специально разработанные сортаменты для выпуска проката из цветных металлов и сплавов – меди, алюминия, латуни, дюраля в виде листов, ленты, труб, прутков и других изделий. Важнейшей особенностью деформации металла при прокатке является получение волокнистой структуры металла с ориентировкой волокон вдоль направления прокатки, т. е. перпендикулярно осям вращения валков.
Это объясняется тем, что при сдавливании сечения заготовки между валками вытяжка металла в основном происходит в направлении наименьшего сопротивления, т. е. при выходе из валков. Деформации и вытяжке в поперечном направлении препятствуют трение о поверхности валков. Так как общая вытяжка металла заготовки складывается из вытяжек его отдельных зерен, то последние должны превратиться в волокна. Заготовка захватывается в рабочее пространство между валками и перемещается силами трения, возникающими между нею и валками (рис. 4.27).
Действительно, при подходе заготовки к валкам в точках первичного контакта возникают, с одной стороны, радиально ориентированные активные Р и равные им реактивные (действующие на заготовку) N силы, а с другой — силы трения Т, касательные к поверхности валков в точках упомянутого контакта. Каждая из сил трения равна произведению нормальной силы Nна коэффициент трения f, т. е. Т = Nf. Рассмотрим проекции сил N и Т на продольное (горизонтальное) направление X и вертикальное – Z. При этом заметим, что силы Nx выталкивают заготовку из рабочего пространства, а силы Тх – втягивают в него заготовку. Условием захвата заготовки валками и осуществления прокатки будет неравенство Тх > Nх. Но так как Тх· cos α=Nf · cosα, а Nx=N· sinα, то условием прокатки будет Nf cos α > N sinα. Разделив обе части неравенства на N cosα, получим f >tgα, где α – угол захвата.
Таким образом, условием захвата заготовки валками и осуществление процесса прокатки является превышение коэффициента трения над тангенсом угла захвата.
Прокатка металлов осуществляется на прокатных станах (рис. 4.28, г).
Основными рабочими элементами прокатных станов являются валки, имеющие цилиндрическую форму. Валки размещаются в основной части прокатного стана – рабочей клети 4. Рабочая часть валка (рис. 4.28, а) называется бочкой 1. Опорная часть валка шейка 2, соединительная – треф 3. Бочки могут быть гладкими или ручьевыми (рис. 4.28, а и 4.28, б). Первые применяются для прокатки листов и лент, а вторые – для сортового металла. Ручьи представляют собой кольцевые вырезы на поверхности валка. Совпадающие ручьи верхнего и нижнего валков образуют калибры, с помощью которых сортовому прокату постепенно придаются требуемые профили (рис. 4.26, а, б).
|
|
Рис. 4.28. Инструмент и оборудование прокатки: а) гладкий волок: 1 – бочка валка; 2 – шейка; 3 – треф; б) ручьевой валок; в) открытый и закрытый калибры; г) схема прокатного стана: 4 – рабочая клеть; 5 – шпиндель; 6 – шестерная клеть; 7 – редуктор; 8 – электродвигатель.
Прокатные станы классифицируются по ряду признаков, основным из которых является род выпускаемой продукции. В связи с этим можно выделить следующие наиболее распространенные виды станов: для получения полупродукта из слитков блюмов и слябов; заготовительные; сортопрокатные для выпуска из блюмов сортового проката; из слябом листовые и полосовые станы горячей прокатки; трубопрокатные станы; станы холодной прокатки стали и цветных металлов (тонколистовые, лентопрокатные, фольгопрокатные и т.д.); деталепрокатные станы для выпуска специального или периодического проката.
Холодная прокатка ленты из алюминиевых сплавов АМц, Д, Д16 производится из горячекатаных листов толщиной около 6мм. Ленту толщиной до 0,5-0,6мм катают без промежуточного умягчающего отжига. Заготовками для холодной прокатки лент из меди и латуни Л62 служат свернутые в рулоны полосы толщиной 5-6мм, полученные горячей прокаткой из слитков. Отожженные и протравленные рулоны прокатываются на специальных станах до толщины 0,01-0,2мм в течение четырех-пяти операций холодной прокатки, чередующихся умягчающими отжигами и травлением для удаления окалины.
Тонкие листы и ленту из меди или латуни получают холодной прокатной из горячекатаных заготовок толщиной 10-15мм с предварительно удаленными фрезерованием поверхностными дефектами. Прокатку ведут до требуемой толщины в несколько обжатий, применяя промежуточные отжиги при 450-800°С для восстановления пластичности металла.
|
|
Для холодной прокатки предпочтительнее однофазные латуни с содержанием цинка менее 30%, как обладающие большим запасом пластичности. Для предотвращения налипания меди и латуни на стальные валки применяют жидкую смазку (трансформаторное масло, керосин, веретенное масло и т. д).
4.3.2. Ковка и штамповка. При ковке деформирование металла заготовки осуществляется путем целенаправленно наносимых ударов или нажатий. В зависимости от используемого оборудования ковка делится на свободную и ковку в штампах (штамповку).
Сущность свободной ковки заключается в том, что происходящая формообразующая пластическая деформация металла осуществляется специальным инструментом. Придание заготовке требуемых формы и размеров осуществляется за счет выполнения ряда ковочных операций.
Горячая объемная штамповка. При штамповке требуемые формы и размеры заготовки получаются в результате принудительной деформации металла в ручье специального приспособления - штампа (рис. 4.29). Различают объемную штамповку в открытых и закрытых штампах. В открытом штампе (рис. 4.29, а) по периферии ручьяна стыке нижней 1 и верхней 2 частей штампа выполняется заусенечная канавка 3 для выхода избыточного металла, образующего удаляемый после штамповки заусенец, а в закрытом штампе (рис. 4.29, б, в) нет заусенечной канавки для выхода металла.
Рис. 4.29. Схемы штамповки в открытых и закрытых штампах.
Несложные заготовки штампуются в одноручьевых штампах, а сложные - в многоручьевых, в которых при переходе от ручья к ручью поковка постепенно приобретает требуемые размеры и форму. Исходные заготовки для штамповки отрезаются от сортового проката. Ими могут служить изделия периодического проката. Перед штамповкой металл нагревается до определенной температуры, зависящей от рода металла с целью повышения, его пластичности и уменьшения усилий при обработке. Свободная ковка и штамповка производятся с помощью специальных ковочных или штамповочных молотов и прессов.
Вследствие интенсивной теплоотдачи в атмосферу и теплопередачи в стенки ручья штампа происходит быстрое охлаждение заготовки, что приводит к наклепу и охрупчиванию ее металла. Во избежание образования трещин это требует дополнительных промежуточных нагревов цветных заготовок. При штамповке латуни следует иметь в виду, что при температуре выше 680°С из нее интенсивно возгоняется цинк в виде порошка ZnO. Это влечет изменение се химического состава и прочностных характеристик. Следует также учитывать, что при горячей штамповке латуни более хрупкая при комнатной температуре β-фаза оказывается пластичнее α-фазы. Поэтому для горячей штамповки однофазных латуней следует выбирать марки с предельным для α-латуней содержанием цинка - до 39%. После нагрева в результате α→β -превращения их структура состоит из α+β - или только β -зерен и имеет более высокую пластичность, чем у латуней с меньшим содержанием пинка, не претерпевающих α→β -превращений.
Ковка и штамповка дюралюминия производится при температуре около 380°С со степенями деформации соответственно 3-5 и 2-3%.
С целью экономии металла при обработке давлением осваиваются и внедряются более рациональные ее виды.
Так, в прокатном производстве применяются так называемые облегченные, тонкостенные, сложные, фасонные и другие экономичные профили проката. Прокаткой получаются экономичные профильные заготовки и изделия: шары, валы, зубчатые колеса, сверла, винты, различные виды периодического проката (для экономии металла при штамповке). Для производства машиностроительных профилей применяют еще методы прессования, волочения, а из листового материала получают изделия вырубкой, вытяжкой, формовкой, а прокаткой – гнутые профили.