Скорость химических и диффузионных процессов, протекающих с участием твердой фазы, повышается при увеличении ее поверхности. Увеличить поверхность обрабатываемого твердого материала можно, уменьшая размеры его кусков, т. е. путем измельчения.
Процессы измельчения условно подразделяют на дробление (крупное, среднее и мелкое) и измельчение (тонкое и сверхтонкое). Измельчение материалов осуществляют путем раздавливания, раскалывания, истирания и удара (рис.7.6). В большинстве случаев эти виды воздействия на материал используют комбинированно; при этом обычно основное значение имеет один из них, что обусловлено конструкцией машины, применяемой для измельчения.
В зависимости от физико-механических свойств и размеров кусков (крупности) измельчаемого материала выбирают тот или иной вид воздействия. Так, дробление твердых и
|
хрупких материалов производят раздавливанием, раскалыванием и ударом, твердых и вязких - раздавливанием и истиранием.
|
|
Дробление материалов обычно осуществляется сухим способом без применения воды, тонкое измельчение часто проводят мокрым способом (с использованием воды). При мокром измельчении пылеобразования не наблюдается и облегчается транспортирование измельченных продуктов.
Результат измельчения характеризуется степенью измельчения, равной отношению среднего характерного размера D куска материала до измельчения к среднему характерному размеру d куска после измельчения.
Характерным линейным размером куска шарообразной формы является диаметр, куска кубической формы — длина ребра.
Способы дробления крупнокусковых материалов и размеры дробильного оборудования зависят от размеров самых крупных кусков исходного и дробленого материала. Поэтому степень дробления часто определяется отношением характерного размера наиболее крупных кусков до измельчения к характерному размеру наиболее крупных кусков после измельчения.
В промышленности в большинстве случаев требуются высокие степени измельчения. Часто размеры кусков исходного материала достигают 1500 мм, тогда как в технологических процессах иногда используется материал, размеры частиц которого составляют доли микрона. Такие степени измельчения достигаются при измельчении в несколько стадий, поскольку за один прием (на одной машине) не удается получить продукт заданной конечной крупности.
По своему назначению измельчающие машины условно делятся на дробилки крупного, среднего и мелкого дробления и мельницы тонкого и сверхтонкого измельчения.
|
|
По основному способу механического воздействия на материал измельчающие машины можно разделить на следующие основные группы: раскалывающего действия, раздавливающего действия, истирающе-раздавливающего действия, ударного действия, ударно-истирающего действия, коллоидные измельчители. Рассмотрим некоторые из них.
Валковые дробилки (рис.7.7). Исходный материал поступает в валковую дробилку, затягивается парой вращающихся навстречу друг другу гладких цилиндрических валков 1, 2 в зазор между ними и дробится в основном путем раздавливания. Валки размещены на подшипниках в корпусе 3, причем валок 1 вращается в неподвижно установленных подшипниках, а валок 2 - в скользящих подшипниках, которые удерживаются в
|
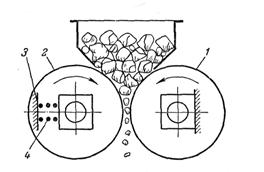
.
заданном положении (в зависимости от требуемой ширины зазора) с помощью пружины 4. При попадании в дробилку постороннего предмета чрезмерной твердости подвижный валок отходит от неподвижного и предмет выпадает из дробилки (при этом устраняется возможность ее поломки).
В промышленности используются валковые дробилки, отличающиеся по числу валков (одно-, двух- и четырехвалковые), форме и скорости вращения валков, виду привода. Валковые дробилки компактны и надежны в работе; вследствие однократного сжатия материал не переизмельчается и содержит мало мелочи.
В барабанных и кольцевых мельницах, широко применяемых для тонкого измельчения (рис.7.8), материал с кусками размером 10 - 2 мм измельчается до размера наибольших его частиц 2 - 0,075 мм под одновременным действием раздавливающих, ударных и истирающих усилий.
Барабанные мельницы - это машины, в которых материал измельчается внутри вращающегося корпуса (барабана) под воздействием мелющих тел или самоизмельчением. Мелющими телами служат металлические шары или стержни, окатанная галька. В зависимости от вида этих тел различают шаровые, стержневые, галечные мельницы, и мельницы самоизмельчения. При вращении барабана мелющие тела увлекаются под действием центробежной силы и силы трения вместе с поверхностью стенок на определенную высоту, а затем свободно падают и измельчают материал ударом,
раздавливанием и истиранием.
|
Измельчение проводится как мокрым (широко применяющимся в барабанных мельницах), так и сухим способом.
Благодаря этому удары мелющих тел (меньше смягчаются пульпой и эффективность измельчения повышается. Недостатками таких мельниц являются: уменьшение рабочего объема I и увеличение веса машины (за счет диафрагмы и лифтеров), возможность (забивания отверстий решетки изношенными мелющими телами.
Шаровые мельницы. В шаровой кольцевой мельнице (рис.7.9) материал измельчается между шарами 1 и вращающимся кольцом 2, к рабочей дорожке которого шары прижимаются при помощи кольца 3 нажатием пружин 4.
Мельницы для сверхтонкого измельчения. Вибрационная мельница, принципиальная схема которой приведена на рис.7.10, представляет собой цилиндрический или корытообразный корпус 1, примерно на 80% своего объема загруженный шарами (иногда стержнями) 2. Корпус приводится в колебательное движение валом 3, снабженным дисбалансом (в мельницах инерционного типа) или эксцентриковым валом вибрационных мельницах.
При вращении неуравновешенной массы вала (вибратора) 3 со скоростью от 1000 до 3000 мин-1 корпус 1 с загруженными в него шарами и измельчаемым материалом совершает качательное движение по эллиптической траектории в плоскости, перпендикулярной оси вибратора. Мелющие тела при этом вращаются вокруг собственных осей, а все содержимое корпуса приводится в планетарное движение в сторону, обратную направлению вращения вибратора. Материал интенсивно измельчается под действием частых соударений мелющих тел и истиранием. Корпус устанавливается на пружинящие опоры (рессоры или цилиндрические пружины) 4 и деревянные подкладки, предотвращающие передачу вибраций основанию мельницы.
|
|
Вибрационные мельницы используют для сухого и мокрого измельчения периодическим и непрерывным способами. Применение вибрационных мельниц наиболее эффективно для сверхтонкого измельчения материалов небольшой твердости с размерами зерен от 1—2 мм до 60 мк и менее. Вибрационные мельницы можно использовать и для тонкого измельчения, но при этом их эффективность не превышает эффективности обычных шаровых мельниц.
|
Измельчение в вибрационных мельницах имеет ряд существенных достоинств. Вследствие интенсивного ударно-истирающего воздействия на материал весьма быстро достигается высокая дисперсность продукта измельчения. Частицы материала в мельнице вибрируют во взвешенном состоянии, не слипаются и не спрессовываются. Этим обеспечивается большая однородность размеров частиц измельченного материала.
Относительно низкая производительность (корпус примерно на 80% заполнен мелющими телами), быстрый износ мелющих тел, тяжелые условия работы (вибрация) подшипников невыгодно отличают вибрационные мельницы от мельниц других типов для сверхтонкого измельчения.