Рисунок 32. Схема готовой к заливке формы
Таблица 5.1 - Зависимость поверхностной твердости пеномодели от плотности
Таблица 4.3. Прочность ХТС из различных смол
Таблица 4.2. - Количество катализатора в смеси в зависимости от температуры окружающей среды.
Рисунок 26. Изготовление оболочковой формы для чугунной отливки цилиндра
Рисунок 25. Последовательность изготовления отливки
Рисунок 9. Литейная форма со стержнем
Стержни подразделяются на пять классов по размерам, сложности, условиям работы в литейной форме и требованиям к качеству литой поверхности.
Первый класс - стержни тонкие, ажурные, сложной конфигурации с малыми знаками. Образуют в отливках необрабатываемые поверхности, к которым предъявляют высокие требования, оформляют протяженные отверстия, узкие полости корпусов двигателей внутреннего сгорания. Смеси приготавливают из 100% кварцевых песков с глинистой составляющей до 0.5%, связующие - 1-2% растительных масел или олифы
Второй класс - стержни сложной конфигурации, имеющие наряду с массивными частицами тонкие выступы, перемычки, знаки более крупные, чем поверхности полностью или частично обрабатываемые. Смеси приготавливают из 100% кварцевых песков с глинистой составляющей до 1%, связующие - заменители масел, смолы - 2-3%; для повышения сырой прочности вводят 1-2% сульфитной барды.
Третий класс - это стержни мелкие и средние для отливок массового производства, (картеров, ступиц, рычагов, втулок и др.). Не имеющих особо тонких деталей, опирающиеся на массивные знаки, оформляющие отверстия и полости, к чистоте которых предъявляются повышенные требоваРисунок 10. Не всплывающий стержень
со знаком внизу а и стержень 'С нижним
и верхним знаками б.
ния. Смеси приготавливаются из 100% кварцевых песков, связующие, заменители масел, смолы 2-3.5%, для обеспечения
требуемой сырой прочности вводят 2-3% сульфитной барды.
Четвертый класс - стрежни средние и крупные, преимущественно для отливок мелкосерийного производства, образующие обрабатываемые и необрабатываемые отверстия, к чистоте которых особых требований не предъявляется. Смесь изготавливается из 60-93% кварцевого песка и до 40% отработанной смеси, связующее - глина 1-7%, которая обеспечивает требуемую сырую прочность.
Для обеспечения сухой прочности вводят 2-3% сульфитной барды, она повышает и сырую прочность, С целью улучшения податливости и выбиваемости в смесь добавляют до 2% по массе древесных опилок.
Пятый класс - массивные стержни простой конфигурации, образующие большие внутренние полости в крупных отливках или внешние неответственные места. Смесь изготавливается из ДО-70% кварцевого песка, 20-60% отработанной смеси, связующее -глина 2-8%. Для обеспечения сухой прочности вводят 2-3% сульфитной барды, а для улучшения податливости и выбиваемости в смесь добавляют до 3% по массе древесных опилок.
|
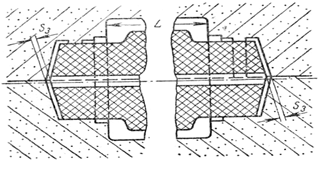
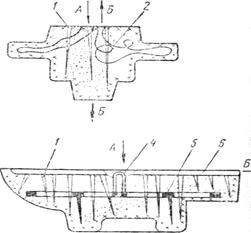
Рисунок 14. Способы вентиляции стержней:
А - сторона набивки стержня, Б - направление выхода газов;
1-вентиляционные каналы, Г -восковые фитили, 3 -слой шлака,
4- веска (подъемник), 5 - каркас,
в - прорезной вентиляционный канал
2. ИЗГОТОВЛЕНИЕ ЛИТЕЙНЫХ ФОРМ И СТЕРЖНЕЙ
Песчаные формы чаще всего для каждой отливки изготавливаются заново и называются разовыми. В многократных (полупостоянных) формах для каждой отливки возобновляется только облицовочный слой, а остальная часть служит 100-160 раз. Разовые формы пригодны для отливок любой массы, размеров и сложности и наиболее широко применяются в массовом, серийном и единичном производстве.
Приготовленная и разрыхленная пластичная формовочная смесь, смоченная той или иной жидкостью (чаще всего вязкой), имеет невысокую текучесть. Формы из нее приготавливаются теми или иными механическими способами уплотнения, которые решают одновременно два вопроса;
- смесь, увеличивая текучесть, лучше воспроизводит контуры модели;
- смесь получает необходимую технологическую прочность, чтобы противостоять тепловым и механическим нагрузкам, которым она подвергается при заливке, затвердевании и охлаждении отливки.
Это уплотнение смеси может выполняться вручную или на машинах трамбованием, прессованием, встряхиванием пескометным, пескодувным, пескострельным и комбинированными способами.
Насыпная масса разрыхленной смеси составляет от 600 до 1300 кг/м3 и зависит от ее состава, вида связующего, влажности, степени разрыхления. Объемная удельная масса уплотненной смеси составляет
примерно 1600-1700 кг/м3 и изменяется незначительно от количества и типа связующего, влажности. Коэффициент уплотнения
|
Рисунок16. Схема формовки по модели с подрезкой:
а- плотнение нижней опоки; б выполнние подрезки;
в - уплотнение верхней опоки; г- собранная форма; д – фальшивая опока.
|
Рисунок 18. Схема формовки по модели с перекидным
«болваном»:а - формовка нижней полуформы / и «болвана»
2; б –формовка верхней полуформы; в - съем верхней полуформы
и верхней части моделей; г - сборка полуформ
и кантовка их на 180°; д - съем нижней полуформы
и нижней части модели; е - сборка полуформ
|
где Рv1 - плотность разрыхления смеси до уплотнения; Руа - плотность смеси после уплотнения; коэффициент а всегда больше 1 и колеблется от 1,3 до 2,4.
2.1. Уплотнение трамбованием.
|
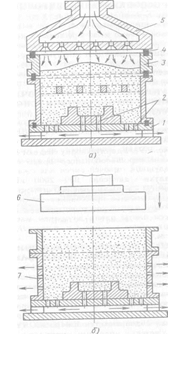
|
![]() |
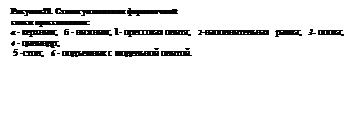
2.2. Уплотнение прессованием
Способ применяется для изготовления форм особенно в массовом производстве на автоматических линиях. Возможно применение нижнего и верхнего прессования.
При нижнем прессовании обеспечивается благоприятный характер распределения плотности по высоте опоки – максимальная плотность у поверхности модели со снижением по мере удаления от модели и минимальная у поверхности опоки,
Удельное давление прессования обычно составляет 0,6-0,7 МПа
Прессование при повышенном удельном давлении выше 1 МПа в исключительных случаях - 2,0 МПа. Более высокое удельное давление применяется редко, так как приводит к повышенному расходу электроэнергии, увеличению массы машин, не давая технических и технологических преимуществ.
Однако на степень уплотнения формы оказывает влияние модель. Чем выше модель, тем пространство над моделью будет уплотнено больше, чем между опокой и моделью.
Применение вибрации при прессовании повышает текучесть смеси, происходит разрушение арок в смеси, уменьшается внутреннее трение между песчинками и трение об оснастку.
2.3. Уплотнение встряхиванием
При встряхивании для уплотнения используется кинетическая энергия падающей формовочной смеси. Модельная плита с моделью, опокой и смесью подвижным столом 1 с помощью сжатого воздуха поднимается на 50-80 мм, а затем падает на станину2 машины.
|
Энергия встряхивания Е, где m-масса смеси; V- скорость падения стола; Z-высота падения стола;
g-ускорение свободного падения.
Е = m*V 2 /2 = m*2g*Z = m*g*Z
Под действием этой энергия наибольшее уплотнение у модельной плиты, так как здесь наибольшая масса, в вышерасположенных слоях смеси уплотнение меньше. На периферии опоки смесь слабо уплотняется, так как ее масса очень мала. Характер распределения плотности смеси благоприятный. Максимальная, у поверхности модели. Постепенно снижающаяся к периферии опоки, что обеспечивает хорошую газопроницаемость формы и удаление газов из нее. Вся работа уплотнения будет равна:
А = h*m*q*Z*n
где А-работа, Дж; h-коэффициент использования энергии, зависит от конструкции машины, износа ее, смазки и др., равен 0,3-0.7; m- масса смеси, кг; z - высота подъема стола, м; n -число ударов.
Низкие опоки (менее 150 мм) формовать встряхиванием не рационально, гак как верхние слои очень слабо уплотняются; применяется встряхивание с подпрессовкой. Подпрессовку используют для опок размером в свету до 1800-1200 мм; для более крупных - уплотнение верхних слоев смеси пневмотрамбовками, так как подпрессовочный механизм получается громоздким.
Подпрессовка особенно необходима при уплотнении встряхиванием опок с моделями, имеющими высокие вертикальные стенки, так как поток смеси, подобно жидкости, при движении огибает верхние острые кромки модели, образуя слабо уплотненные места.
2.4. Пескометный способ уплотнения
Основан на том, что порция формовочной смеси, разгоняется в
пескометной головке лопаткой, находящейся на центробежном
колесе, сидящем на валу, На лопатку смесь подается транспортером. Под действием центробежной силы
порция смеси получает ускорение и на конце лопатки разгоняется до радиальной скорости, окружной скорости, которые складываются и дают результирующую скорость. Смесь из головки выбрасывается со скоростью 30-40 м/с перпендикулярно модельной плите. Для заполнения объема формы необходимо порций, а работа уплотнения составит:
А =h*V2*mi/2, где m- порция смеси, V- скорость, h-коэф, уплотнения Так как масса смеси формы, то с учетом коэффициента потерь смеси при уплотнении h=1,1-1,5 (нижний предел для крупных форм, верхний для малых) работа уплотнения будет: А=h*V2*m/2
Уплотнение имеет тот же вид, что и для уплотнения встряхиванием. Разница в том, что при встряхивании масса смеси велика, а скорость мала, а при пескометном способе наоборот, скорость велика, а масса порции мала,
Характер распределения плотности смеси по высоте опоки практически равномерный, Способ применяется в основном для уплотнения средних и крупных форм в единичном и мелкосерийном производстве
2.5. Пескодувный способ уплотнения
Метод основан на том, что смеси придается скорость потоком сжатого воздуха, а кинетическая энергия смеси используется для ее уплотнения. На рис.11 представлена схема работы пескодувной машины. Сжатый воздух под давлением 0,5-0,7 МПа (5-7 атм), попадая в резервуар 1 со смесью через отверстия 2 надувной плиты, выбрасывает ее в опеку (стержневой ящик) 3 и уплотняет. Формовочная смесь может переноситься потоком воздуха непрямолинейно и заполнять полости сложной конфигурации. Отработанный воздух уходит через щели (венты) 4. Условиями для качественного заполнения формы является высокая разность давлений РГР2 в машине и оснастке, хорошая текучесть и газопроницаемость смеси. Смеси применяются с органическими связующими главным образом масляными. Вязкие смеси на основе глин непригодны, жидкостекольные смеси применяют ограниченно, так как они налипают на рабочие органы машины. Длительность заполнении стержневых ящиков в зависимости от их объема достигает 15с.
Размер и число вдувных отверстий и вент зависит от свойств смеси и конфигурации стержня, Чем сложнее конфигурация стержня, тем больше вент, особенно в зонах, удаленных от вдуваемого потока смеси.
Если прочность смеси на сжатие во влажном состоянии менее 0,01 МПа; то диаметр вдувных отверстий 10-12 мм, если более 0,01 МПа - то 15-25 мм; общая площадь вент принимается равной 0,3-0:7 площади вдувных отверстий. Каждое вдувное отверстие обслуживает 60-80 см поверхности стержня.
2.6. Пескострельный способ уплотнения
|
3. ЖИДКИЕ САМОТВЕРДЕЮЩИЕ СМЕСИ ДЛЯ ИЗГОТОВЛЕНИЯ ФОРМ И СТЕРЖНЕЙ
Почти все известные способы изготовления песчаных форм и стержней основаны на применении принципа уплотнения смесей и чаще всего в единичном и мелкосерийном производстве базируются на использовании встряхивающих машин и пескометов.
Развитие этого процесса за последние годы шло по пути увеличения мощности встряхивающих машин, применения новых методов уплотнения смеси прессованием, вибропрессованием и др. Однако объем ручных работ при этом остается большим и особенно велика доля ручного труда при почвенной и кессонной формовке крупных отливок.
Совершенно новые перспективы для решения задачи коренной механизации процессов изготовления форм и стержней в единичном и мелкосерийном производстве открываются при применении жидких самотвердеющих смесей.
Жидкие самотвердеющие смеси, как следует из их на звания, имеют свойства жидкости, представляют собой тестообразную массу» позволяющую получать формы и стержни свободной заливкой ее, и способны самозатвердевать на воздухе в заданное время.
Иногда эти смести называют наливными, псевдожидкими, жидкоподвижными.
При использовании ЖСС исключается трудоемкое ручное или машинное уплотнение смеси, а процесс изготовления форм и стержней сводится к простой операции заливки жидкой смеси в опоку на модель или в стержневой ящик.
а – чертёж отливки; б – деревянная модель; в – модель отливки, заформованная в
нижнюю полу-опоку (установлена модель литниковой системы); г – разъёмный
стержневой ящик; д – изготовленный стержень; е – две полуформы с извлечёнными
полу-моделями и установленным стержнем; ж – собранная форма; з – отливка.
1;5 – стержневые знаки; 2 – литник; 3,4 – полу-опоки; 6 – стержень
Важное свойство жидкой смеси – самозатвердевание на воздухе – в свою очередь дает возможность отказаться от тепловой сушки форм и стержней (при применении самовысыхающих красок) или ограничиться кратковременной подсушкой водных красок. Все это вместе взятое позволяет в несколько раз повысить производительность труда. Существенно упростить средства механизации, открывает возможность для широкой комплексной механизации и автоматизации процессов изготовления формы и стержней в цехах с единичным и мелкосерийным характером производства отливок из чугуна, стали, цветных сплавов массой от нескольких десятков килограмм до нескольких десятков тонн.
3.1. Общие представления о механизме формирования
текучести жидких смесей
Сухой кварцевый песок обладает высокой текучестью, или сыпучестью, что определяется силами трения между отдельными зернами песка, иди коэффициентом внутреннего трения. При неоднородном зерновом составе и неправильной форме зерен на сыпучесть сухой песчаной смеси существенное влияние оказывает шероховатость и угловатость зерен, так называемое зубообразное зацепление отдельных частиц смеси при контакте друг с другом.
Чистый кварц SiO2 легко смачивается водой. Но при небольшом количестве влаги толщина образующейся водной пленки по сравнению с размерами зерен очень мала, и составляет около 5-10 см. Водная пленка такой толщины не может сгладить влияние шероховатости зерен на текучесть смеси. Из-за действия сил поверхностного натяжения образовавшиеся пленки увеличивают силы сцепления между твердыми частицами в точках их контакта, что приводит к ухудшению текучести. И лишь при значительном обводнении смеси по мере ее приближения к двухфазной системе песок - вода текучесть начинает повышаться, но этот путь не приемлем для литейных форм.
Введение в трехфазную систему «песок - водный раствор связующего -воздух» поверхностно-активных веществ (ПАВ) существенным образом изменяет ее физические свойства. Молекулы ПАВ адсорбируются на поверхности раздела раствор-воздух, сильно снижая поверхностное натяжение раствора. Наряду с этим ПАВ адсорбируются также на твердых поверхностях раздела, придавая им гидрофобизующие свойства.
Одновременно резкое снижение поверхностного натяжения жидкой фазы приводит к частичному образований пены и воздухововлечению в смесь при ее приготовлении. Поэтому для пенообразующих ПАВ текучесть будет улучшаться также за счет дополнительного воздухововлечения. Возникшие при перемешивании смеси пузырьки пены, располагаясь между зернами песка разобщают их, снижая тем самым трение между песчинками, сводя до минимума влияние шероховатости и "зубообразного" зацепления и облегчая скольжение песчинок относительно друг друга. Для перевода формовочных смесей в жидкое состояние необходимо применять ПАВ с высокой пенообразующей способностью, вызывающей в процессе перемешивания смеси интенсивное воздухововлечение.
3.2. Исходные материалы и их характеристика
Для приготовления ЖСС в принципе необходимы:
· наполнитель - огнеупорный формовочный песок (кварцевый, магнезитовый, хромомагнезитовый, оливиновый, цирконовый и др);
· отвердитель (феррохромовый шпак, нефелиновый шлам и др.);
· связующее (жидкое стекло, лигносульфонаты сульфитно-дрожжевой бражки (СДБ), смолы и др.);
· пенообразователь (контакт Петрова, ДС-РАС, мылонафт и др.);
· добавки для обеспечения необходимых технологических и физико-механических свойств смеси.
В настоящее время в России и за рубежом разработано большое количество составов ВСС, из которых наиболее широко применяемые можно свести к следующим:
· самотвердеющие композиции на основе жидкого стекла;
· самотвердеющие композиции на основе лигносульфонатов СДБ;
· ЖСС с синтетическими смолами;
· жидкие цементные смеси.
ЖСС применяются широко для изготовления средних и крупных отливок в единичном и мелкосерийном производстве. Часто при изготовлении крупных отливок ЖСС попользуется в качестве облицовочной смеси при изготовлении форм, а наполнительная смесь песчано-глинистая с уплотнением пескометами. Предел прочности затвердевшей смеси при сжатии для стержней и форм средней сложности перед заливкой металлом должен быть не ниже 0,6-0,7 МПа (6-7 кгс/см2), при извлечении модели из форм - не ниже 0,08-0,1 МПа (0,8-1,0 кгс/см2, при извлечении стержня из ящика - не менее 0,10-0,15 МПа (1,3-1,5 кгс/см2). Время затвердевания смеси до раскрытия ящика или извлечения модели из форм не должны превышать 40-60 мин.
Минимально допустимая живучесть смеси (условно характеризуемая устойчивостью пены), необходимая для разливки смеси в ящики или формы, установки каркасов, должна составлять 2-3 мин.Вполне понятно, что приведены лишь минимально допустимые показатели прочности, без ограничения верхнего предела. Вместе с тем для смесей
Технология получения форм рис 27 из химически затвердевающих оболочек заключается в том, что изготовляют только одну полумодель, смонтированную на модельной плите 4. Для продувки облицовочного слоя углекислым газом в стенках модели предусмотрены штуцер 1 и отверстия 5.
На модельную плиту 4 устанавливают рамку 3 и металлический каркас оболочки, модель обкладывают облицовочной смесью на жидком стекле, которую затем продувают через штуцер 1 углекислым газом. После затвердевания нижней оболочки 2 рамку снимают, а на модельную плиту ставят нижнюю опоку, которую набивают наполнительной смесью при помощи пескомета. При этом устанавливают на плиту керамику для выполнения литниковой системы 8. Нижнюю полуформу 7 с оболочкой снимают и переворачивают, а на модельную плиту вновь кладут рамку, формуют и продувают верхнюю оболочку. Затем верхнюю оболочку снимают (за каркас) с модели и устанавливают на нижнюю полуформу, уложив в полуформу перед этим стержень 6. На нижнюю опоку ставят верхнюю и набивают при помощи пескомета. Точность установки оболочек обеспечивается штырями, для которых выполняют отверстия 9 в выступах оболочки. Внутреннюю поверхность оболочек до сборки окрашивают и подсушивают горелками. Далее форму скрепляют и поворачивают для вертикальной заливки.
-
на основе неорганических связующих, таких, как жидкое стекло, верхний предел прочности требует уточнения, так как чрезмерная прочность смеси ухудшает, выбивку и податливость. Поэтому максимальную прочность ЖСС на жидком стекле следует ограничить величиной 1,2-1,3 МПа (12-13 кгс/см2).
|
Наполнители. Для приготовления ЖСС рекомендуются кварцевые пески класса 1К и 2К групп 016, 02, 0315 и 04. Большинство заводов в составах ЖСС применяют песок марки 02. Содержащаяся в песке глина ухудшает текучесть смесей и требует повышенного расхода жидкой композиции. Поэтому предельно допустимым содержанием глинистой составляющей в песке следует считать 2%. Если позволяют возможности, то предпочтение следует отдать обогащенным кварцевым пескам с содержанием глины до 1%.
Рисунок 27 Изготовление тормозного стального шкива нефтебуровой установки с продувкой углекислым газом через модель
На рис. 28 показано изготовление формы стального тормозного шкива нефтебуровой установки с продувкой углекислым газом через модель Форму изготавливают по модели, размещаемой в нижней опоке. При выполнении нижней полуформы применяют химически затвердевающую смесь с продувкой формы углекислым газом через модель 3 до ее извлечения. Для этой цели модельный комплект снабжен газопроводящими каналами. По трубе / углекислый газ поступает через металлическую модельную плиту 2 в нижний 4 и верхний 6 коллекторы модели. Из нижнего коллектора газ по отверстиям 5 (сечением 3x3 мм), расположенным в модели по окружности с шагом 100 мм, поступает к облицовочному слою нижней части формы. Из верхнего коллектора через полость в отъемной части 7 по каналам 8 я 9 газ поступает к облицовочному слою верхней части формы. Расплав подводится в нижнюю часть отливки под стержень.
Жидкие смеси могут быть приготовлены не только на основе кварцевого песка, но и на других огнеупорных материалах: магнезите, хромомагнезите, оливине и др. При этом важно, чтобы применяемый огнеупорный наполнитель по гранулометрии приближался к кварцевому песку.
Отвердители. Для получения жидкий смесей с необходимыми прочностными и технологическими свойствами феррохромовый шлак должен удовлетворять следующим требованиям: содержание СаО - не менее 48%; влажность шлака не более 1,5 %, удельная поверхность не ниже 1800-2000 см2/г. Шлак не должен содержать посторонних примесей - корольков металла, кусков неразложившегося шлака и др.; на заводе-поставщике или потребителе шлак должен быть просеян через сито с ячейкой менее 0,5 мм. Транспортировка и хранение шлака должны исключать возможность его увлажнения, с повышением влажности активность шлака снижается.
Основой феррохромового шлака является двухкальциевый силикат 2СаО×SiО2 (70%), наличие которого способствует саморассыпанию шлака, не требует дополнительного размола перед употреблением. Активность шлака тем больше, чем выше удельная поверхность.
Большое количество двухкальциевого силиката содержится в саморассыпающихся шлаках феррохромового производства, электропечных, мартеновских и доменных шлаках. Степень рассыпаемости электропечных, мартеновских, доменных шлаков и, соответственно, их активность различны, что осложняет получение ЖСС со стабильными свойствами. Так, саморассыпающиеся доменные шлаки в исходном состоянии имеют удельную поверхность 600-1000 см2/г и твердеют с жидким стеклом очень медленное (2,5-3.5 ч.) После помола шлака до удельной поверхности 4000-5500 см2/г активность его существенно возрастает и время твердения сокращается до 45-60 мин. Поэтому предварительная подготовка шлаков позволяет применять их в качестве отвердителей для ЖСС.
Нефелиновый шлам представляет собой побочный продукт производства Глинозема из нефелиновых руд. По минералогическому составу нефелиновый шлам содержит 80-85% b-2СаО×SiO2. Содержание СаО в нефелиновом шламе - не менее 53%. Поставляется шлам глиноземными заводами в тонкоразмолотом виде с удельной поверхностью 7500-8500 см2/г. Сырьевые ресурсы нефелинового шлама практически не ограничены.
Требования к влажности, транспортировке и хранению шлама такие же, как и требования к феррохромовому шлаку.
Пенообразователи. Для перевода смесей в жидкое состояние в наливных самотвердеющих смесях (НСС) применяют пенообразующие добавки, представляющие собой органические кислоты, сульфокислоты или соли этих кислот, при взаимодействии которых с жидким стеклом образуются натриевые соли - мыла, обеспечивающие равномерное и быстрое смачивание зерен песка и образование пены.
Наиболее широкое применение получили следующие пенообразователи: контакт черный нейтрализованный рафинированный (КЧНР), детергент советский рафинированный алкиларилсульфонат (ДС-РАС или паста РАС), контакт Петрова, нефтяное ростовое вещество (НРВ), сульфонол НП-1, КБЖ и другие, которые применяются в самостоятельном виде или в сочетании с мылонафтом (табл. 1.1).
КЧНР (ТУ38-3022-74) - маловязкая жидкость от темно-коричневого до черного цвета, представляет собой водный раствор кислого гудрона, нейтрализованного и рафинированного от масел, смол и сульфата натрия, обеспечивает устойчивость пены в смесях в течение 6-8 мин.
ДС-РАС (ТУ38-10764-75) - жидкость от желтого до коричневого цвета, получают при сульфонировании керосинового или газойлевого дистиллята нефти. Реакция нейтральная или слабощелочная. Содержание сульфокислот не менее 45%, сульфата натрия - не более 5%. Плотность при 20°С Ц20-П50 кг/м3, температура застывания 15-30°С. Перед использованием жидкость нужно хорошо перемешать.
Таблица 3.1 –Физико-химическая характеристика мылонафта
Характеристика | Показатели | |
1-го сорта | 2-го сорта | |
Внешний вид | Мазеобразное вещество от соломенно-желтого до светло-коричневого цвета | Мазеобразное вещество от соломенно-желтого до черного цвета |
Содержание нефтяных сульфокислот, %, не менее | ||
Содержание не омыляемых веществ в расчете на органическую часть, %, не более | ||
Кислотное число в миллиграммах на I г нефтяных кислот не менее | ||
Содержание минеральных солей, %, не более | ||
В том числе содержание хлоридов, %, не более |
Контакт Петрова (ОСТ36.01116-76) - маловязкая жидкость от коричневого до черного цвета плотностью 900-1110 кг/м3. Содержание сульфокислот в керосиновом контакте Петрова 55%, в газойлевом – 50%. Растворяется в воде в неограниченных количествах, не горюч, на взрывоопасен, слабо токсичен. Контакт Петрова имеет кислую реакцию и перед употреблением его необходимо нейтрализовать водным раствором едкого натра. Бели же контакт Петрова предварительно подвергается обезмасливанию, его можно вводить в смесь без нейтрализации.
НРВ - водный раствор натриевых солей нафтеновых кислот» Содержание нафтеновых кислот в продукте 39-42%, содержание не омыляемых (керосин, дизельное топливо) - не более 101, кислотное число 200-300 мг КОН/г, реакция НРВ - слабощелочная. Применяют в качестве ПАВ при изготовлении НСС.
3.3. ЖСС с жидким стеклом
ЖСС с жидким стеклом являются одним из самых распространенных и широко применяемых. В качестве огнеупорного наполнители широко применяется кварцевый песок с содержанием глины до 1%, а также приготавливаются смеси на основе других огнеупорных материалов: хромомагнезите, оливине, цирконе и др. Температура песка £ 30°С. Жидкое стекло применяется содовое с модулем 2,6-2,9, плотностью 1,47-1,50 г/см3.
Магнитная обработка жидкого стекла полем промышленной частоты увеличивает прочность смесей на сжатие на 20-25% /2/.
В качестве пенообразователя чаще всего применяется ДС-РАС или контакт Петрова, а в качестве отвердителя - феррохромовый шлак, нефелиновый голам, кремнефтористоводородная кислота (8%-ный раствор H2SiF6).
Приведем примерные составы и свойства ЖСС на жидком стекле (табл.3.1.)
Таблица 3.2 – Состав смесей
Смесь 1, масс. ч. | Смесь 2, масс. ч. | |||
Кварцевый песок | 95-97 | 95-97 | ||
Феррохромовый шлак, Sуд=2000-2500 см/г | 3-5 | - | ||
Нефелиновый шлам, Sуд=7000-8000 см/г | - | - | ||
Пак древесный | 0,6-0,7 | 0,6-0,7 | ||
ИТОГО | ||||
Жидкое стекло М=2,6-2,9; r=1,47-1,5 г/см3 | 6-7 | 3,5-4,5 | ||
Вода | 1,5-2,0 | 1,5-2,0 | ||
Пенообразователь: Контакт Петрова Мылонафт ДС-РАС | 0,5 0-0,15 - | - - 0,1-0,15 | 0,5 0-0,15 - | - - 0,1-0,15 |
Таблица 3.3 – Свойства смесей
Прочность при сжатии, МПа, через - | ||||
1 час | 0,25-0,55 | 0,2-0,35 | ||
3 часа | 0,5-0,85 | 0,5-0,65 | ||
24 часа | 0,8-1,3 | 0,7-1,25 | ||
Газопроницаемость через: | ||||
1 час | 200-250 | 70-80 | 200-250 | 70-80 |
24 часа | 400-500 | 300-500 | 400-500 | 400-500 |
Устойчивость пены, мин | 3-20 | 3-5 |
Особенность приготовления смесей состоит в том, что вначале отдельно готовятся сухие и жидкие композиции. Подвижность ЖСС определяется процессом пенообразования при ее перемешивании, по этому смесители должны обеспечивать не только хорошее перемешивание, но и достаточно интенсивное вовлечение в смесь воздуха. Обычные смесеприготовительные бегуны практически не пригодны для получения жидких смесей. В этом случае использует лопастные смесители Периодического и непрерывного действия с горизонтальной осью вращения, конструкция которого создает благоприятные условия для вовлечения в смесь воздуха и перевода ее в подвижное состояние.
Установка для приготовления жидко! композиции может быть лопастной или с насосом.
Порядок загрузки составляющих при приготовлении жидкой композиции предпочтительно следующий:
жидкое стекло;
пенообразователь (например ДС-РАС);
керосин;
вода;
мылонафт.
Время перемешивания > 20 мин.
Керосин вводится при завышенной устойчивости пены или пенообразующей способности ДС-РАС.
Мылонафт вводится при заниженной устойчивости пены и пенообразующей способности, а также при пониженной плотности ДС-РАС.
При приготовлении смеси в смеситель вначале загружаются сухие составляющие в следующей последовательности:
кварцевый песок;
феррохромовый шлак;
древесный пек и другие технологические добавки.
Сухие составляющие перемешиваются 90-100 с (или 140-150 с после начала цикла).
Вводится жидкая композиция и перемешивается с сухими составляющими 140-150 с.
Общий цикл изготовления смеси 5-6 мин.
Отличительной особенностью ЖСС с нефелиновым шламом является большая дисперсность шлама и его высокая активность. Поэтому содержание нефелинового шлама в смеси можно ограничить 3%, а количество жидкого стекла 3.5-4,5%.
Преимущество этой смеси по сравнению со смесью на феррохромовом шлаке - низкое содержание жидкого стекла, что резко улучшает выбивку смесей из отливок. Недостаток смеси - ограниченная живучесть (устойчивость пены не более 3-5 мин), в то время как в жидких смесях с феррохромовым шлаком это свойство можно регулировать в большом диапазоне, изменяя, например, соотношение между контактом Петрова и мылонафтом.
3.4. ЖСС на основе лигносульфонатов СДБ
Лигносульфонаты СДБ - одни из самых дешевых и не дефицитных связующих материалов в литейном производстве. Главной составной частью СДБ являются соли лигносульфоновых кислот.
Широко известен способ получения твердеющих структур на основе лигносульфонатов за счет применения солей высоковалентных металлов, являющихся сильными окислителями, в частности соединений шестивалентного хрома. При взаимодействии таких соединений с лигносульфонатами происходит образование водонерастворимого геля. На основе этого взаимодействия разработаны ЖСС с лигносулъфонатами СДБ, отверждаемые хромовым ангидридом или бихроматом натрия.
Эти смеси имеют два недостатка. Во-первых, хромовый ангидрид и другие соединения шестивалентного хрома токсичны, и при работе о ними необходимо принимать специальные меры предосторожности. Кроме того, этот отвердитель слишком дорог, а надсернокислый аммоний очень дефицитен.
Во-вторых, жидкие смеси после затвердевания почти не имеют газопроницаемости. Она восстанавливается только после тепловой сушки. Удалось получить газопроницаемые смеси при использовании пенообразователя КЧНР или введением в смесь специальных добавок.
Одним из решений проблемы является уменьшение содержания в смесях хромового ангидрида путем частичной замены его медным купоросом в составе комплексного отвердителя с применением поверхностно-активного вещества КЧНР. Газопроницаемость смеси восстанавливается в течение 2 ч. устраняется сушка форм и стержней. Примерный состав смеси приводится ниже (табл.):
Таблица 3.3 – Состав смеси
Смесь 1, масс. ч. | Смесь 2, масс. ч. | |
Кварцевый песок КО315-КО2А | ||
Терморегенерат | - | |
Жидкая композиция (сверх 100%) | ||
Комплексный отвердитель (сверх 100%) | 1,1 | 1,1 |
Таблица 3.4 – Состав жидкой композиции, %
Смесь 1, масс. ч. | Смесь 2, масс. ч. | |
СДБ, разведенная водой до плотности 1190 кг/м3 (для форм) или 1195 кг/м3 (для стержней) | 92-90 | 84-82 |
КЧНР | 8-10 | 16-18 |
Таблица 3.5 – Состав комплексного отвердителя, %
Смесь 1, масс. ч. | Смесь 2, масс. ч. | |
Хромовый ангидрид | ||
Медный купорос | ||
Вода | ||
Плотность комплексного отвердителя, кг/м3 |
Таблица 3.6 – Свойства смеси
Смесь 1, масс. ч. | Смесь 2, масс. ч. | |
Влажность смеси, % | 3,5-4 | 4-5 |
Прочность на сжатие через 4 ч., МПа | 0,5-0,7 | 0,4-0,6 |
Текучесть по пластомеру, мм | 45-65 | 50-70 |
Газопроницаемость через 4 ч, ед. | ||
Общая продолжительность изготовления смеси, мин | 4-5 | 4-5 |
Физико-механические свойства в сочетании с хорошей податливостью смеси позволяют получать глубокие формы сложной конфигурации. Выбиваемость смеси на техническом лигносульфонате превосходит аналогичный показатель смоляных и жидко-стекольных смесей.
3.5. Свойства ЖСС
Наиболее характерные свойства ЖСС: текучесть, живучесть, прочность, продолжительность твердения, гидравлические свойства и выбиваемость.
Свойства смесей условно можно разделить на две группы:
свойства при нормальных температурах;
свойства при высоких температурах.
К первой группе свойств относятся текучесть, живучесть, газопроницаемость и взаимосвязь основных свойств между собой.
Вторая группа свойств включает газовый режим, прочность смесей
при нагревании и после охлаждения, в том числе свойства, определяющие выбиваемость смеси, ее податливость и деформацию.
Рассмотрим основные свойства смеси.
Текучесть. Под текучестью формовочных смесей в общепринятом понимании подразумевают их способность перемещаться под действием внешних сил или собственного веса и воспроизводить конфигурацию стержневого ящика или модели.
Применительно к ЖСС термин текучесть приобретает более точный физический смысл. Здесь текучесть проявляется как самостоятельный фактор формирования стержня и формы, когда смесь действительно может течь под воздействием собственного веса, свободно заполняя полость стержневого ящика или воспроизводя конфигурацию модели без каких-либо механических усилий. Высокая текучесть ЖСС позволяет полностью отказаться от уплотнения смеси при формовке.
Для не жидкой формовочной смеси, представляющая собой пористую систему, в соответствии с законом Кулона сопротивление сдвигу (tсв, МПа) обусловлено действием сил трения и сцепления между частицами смеси:
tед= Рн ×tgj+С’ (1)
где Рн - нормальное напряжение, МПа (кгс/см2); j - угол внутреннего трения; tgj- коэффициент внутреннего трения; С’ - сцепление на единицу площади, МПа (кгс/см2).
Для сухого песка силы сцепления практически равны нулю (С’=0) и уравнение (I) принимает вид
tед= Рн ×tgj (2)
В жидких смесях вследствие разобщения твердых частиц смеси пузырьками пены силы внутреннего трения и сцепления снижаются до минимума. В этом случае коэффициент внутреннего трения смеси может характеризоваться ее вязкостью h, а силы сцепления - предельным напряжением сдвига q и уравнение (I) превращается в уравнение Шведова-Бингама
tед= Рн ×h+q
![]() |
ЖСС является типичной вязкопластичной системой, для которой характерно наличие предельного напряжения сдвига. С увеличением интенсивности и продолжительности перемешивания текучесть смеси повышается (предельное напряжение сдвига падает), а объем воздухововлечения возрастает, причем эти две характеристики между собой тесно связаны: чем больше воздухововлечение, тем выше текучесть (рис.29).
Предельно возможная продолжительность перемешивания смеси в смесителях после ввода жидкой композиции определяется активностью отвердителя. Для шлаков средней активности она не должна превышать 5-6 мин.
Текучесть смеси с увеличением расхода жидкой композиции непрерывно возрастает; предельное напряжение сдвига снижается.
Текучесть смесей после приготовления непрерывно снижается, что связано с непрерывным разрушением пены.
Живучесть. Под живучестью формовочной смеси понимают время сохранения смесью свойств формуемости.
Для ЖСС живучесть характеризуется временем, в течение которого смесь сохраняет свойство подвижности или текучести и с ней можно
осуществлять различные технологические операции – транспортировку, разлив, установку каркасов и др.
Живучесть ЖСС определяется двумя важными характеристиками - устойчивостью пены и индукционным периодом твердения. Если индукционный период больше периода устойчивости пены, регулировать живучесть можно, изменяя устойчивость пены. Если же индукционный период меньше устойчивости пены, живучесть может быть увеличена за счет замедления твердости смеси.
Газопроницаемость. Газопроницаемость ЖСС отличается от известных формовочных смесей тем, что изменяется во времени (сразу после заливки в форму или стержневой ящик равна нулю и увеличивается со временем) и даже для одной и той же смеси может колебаться в широких пределах. Она зависит от следующих факторов:
режима перемешивания и, соответственно, от объема воздухо-вовлечения;
вида и состава пенообразователя;
устойчивости пены и скорости твердения;
структуры наполнителя;
температуры воздуха.
Из перечисленных факторов наиболее сильное влияние на газопроницаемость оказывают вид и состав пенообразователя, а также температура окружающей среды. При температуре 5-100С она близка к нулю, и лишь при 30-35°С достаточно высока. При нагреве смеси быстрое восстановление газопроницаемости начинается при температуре 60-800С и более полное восстановление наступает при 100%, а для смесей с низкой начальной газопроницаемостью - при нагреве до 140-150°С. Это важно учитывать при выборе режима подсушки стержней или красок при низкой исходной газопроницаемости смеси. Для восстановления газопроницаемости центральная зона стержня должна прогреться до 80-100°С.
Газопроницаемость ЖСС при пониженных и средних температурах можно значительно повысить при дополнительном введении в смесь пеногасителей: НЧК, минерального масла, керосина.
В настоящее время содержание масел и в ДС-РАС и в контакте Петрова колеблется в значительных пределах, из-за чего пенообразующая способность их также сильно колеблется, что затрудняет получение ЖСС со стабильными технологическими характеристиками.
Газопроницаемость ЖСС с СДБ ниже, чем с жидким стеклом и с трудом поддается регулированию, что объясняется высокой вязкостью СДБ и большой эластичностью затвердевших пленок связующего, затрудняющих разрушение пены и восстановление газопроницаемости.
Выбиваемость. ЖСС на жидком стекле выбиваются значительно легче жидкостекольных смесей, отверждаемых СО2, но все же она затруднительна, особенно при изготовлении стальных отливок. На выбиваемость смеси оказывает влияние содержание в ней жидкого стекла и величина его модуля. Снижение количества жидкого стекла в смеси на 1% уменьшает работу выбивки в области температур 1000-1200°С почти в 2 раза /3/. Поэтому содержание жидкого стекла в смеси необходимо снижать до минимально возможного уровня, исходя из требуемых прочностных и технологических характеристик.
Повышение модуля стекла также заметно улучшает выбиваемость смесей, так, увеличение модуля с 2,7 до 3,0 снижает работу выбивки при 1200°С более чем в 2 раза. Кроме того, высокомодульное стекло позволяет получать более высокие прочностные характеристики. Поэтому, применяя высокомодульное стекло, можно дополнительно снизить его содержание в смеси и тем самым улучшить выбиваемость.
Тем не менее основные рекомендации по облегчению выбиваемости сводятся к введению в смесь самых разнообразных добавок органического и неорганического происхождения.
Из органических добавок для улучшения выбивки рекомендуются: черный и серебристый графит, кокс, древесный пек, каменный уголь, мазут, древесные опилки, гидрол (побочный продукт крахмалопаточного производства), фенольные смолы и др. Так как органические вещества выгорают при температуре ниже 800°С, то и эффективное влияние на выбиваемость оказывают при прогреве смеси до температуру не превышающих 800°С (главным образом при изготовлении отливок из чугуна и цветных сплавов).
При изготовлении стальных отливок углеродосодержащие добавки применять нежелательно, так как это приведет к науглероживанию поверхности отливок; для улучшения выбивки рекомендуется применять неорганические вещества, содержащие окислы Аl, Сa, Mg, Ba и др.
Можно применять до 3% глины, но при этом несколько снижается текучесть и прочность смеси; лучше из глиноземистых добавок применять Al(ОН)3, который не влияет на физико-механические свойства, существенно улучшает выбиваемость. Аналогично влияет на выбиваемость СаО, СаСО3, боксит, размолотый до 0,5-1,0 мм. Особенно благотворное влияние на выбиваемость оказывает гипс в количестве 1-2%, который вводят взамен соответствующего количества шлака или шлама. Гипс несколько снижает огнеупорность смесей, что может сказаться на чистоте поверхности отливок.
Широко распространен в последнее время способ изменения свойств жидкого стекла модифицированием поверхностно-активными веществами (ПАВ). Наибольший эффект наблюдается, когда модификаторы вводят в жидкое стекло в процессе его получения /5, 6/, что повышает прочность пленки, уменьшает поверхностное натяжение последовательно, улучшает смачивание. Это в конечном счете улучшает физико-механические свойства смеси, а значит, создает предпосылки для снижения дозы жидкого стекла в смесях, и, следовательно, сказывается на выбиваемости.
3.6. Технология изготовления форм
и стержней из ЖСС
Требования к оснастке. Модели и стержневые ящики могут быть изготовлены из различных материалов - дерева, метала, пластмасс. ЖСС на жидком стекле имеет повышенную прилипаемость и хрупкость, поэтому при изготовлении оснастки необходимо предусматривать повышенные уклоны, тщательно выполнять галтели и отъемные части, уделять особое внимание качеству отделки поверхности.
При работе с жидкими смесями предпочтение следует отдавать вытряхным ящикам, отдельные элементы которых собираются в неразъемной деревянной коробке, что позволяет избежать поломок стержней при раскрытии ящиков.
Разделительные покрытия. Для устранения прилипаемости смеси к оснастке необходимо применять разовые или постоянные разделительные покрытия.
Из разовых разделительных покрытий рекомендуется применять водный раствор эмульсола в соотношении 1:1, раствор сулъфитно-дрожжевой бражки плотностью 1,15-1,20 г/см3, мазут с керосином (1:1) или мазут с керосином и серебристым графитом (1:1:0,5), машинное масло, водный раствор хлористого кальция, ДС-РАС и др.
Из полупостоянных покрытий лучшими являются химически стойкий лак ХСЛ на основе перхлорвиниловой смолы и полеуретановый лак УР-24.
После нанесения на оснастку лаков ХОД и полиуретанового требуется выдержка на воздухе для высыхания в течение пяти суток. При нагреве окрашенной оснастки до 80-100°С продолжительность сушки может быть сокращена до 5 ч. Число съемов без возобновления покрытий Можно подучить до 50-60.
Изготовление форм и стержней из ЖСС сводится к простой операции заливки смеси на модель, находящуюся в опоке, или в стержневой ящик. Смесь наливают с избытком для компенсации возможной небольшой усадки; после начала твердения излишек смеси срезают и спустя 35-50 мин с момента заливки производят раскрытие стержневых ящиков или извлечение моделей. Каркасы проставляют в стержневые ящики до заливки смеси или погружают в смесь сразу после заполнения.
Положение формы или стержневого ящика при заливке его смесью необходимо стремиться иметь таким, каким оно будет при заливке готовой формы металлом, так как плотность затвердевшей смеси по высоте неодинакова - снизу она максимальна, а сверху минимальна.
Во всех случаях, когда это возможно, стержни следует делать пустотелыми, применяя различные вставки и вкладыши. При изготовлении форм целесообразно пользоваться профильными опоками или жакетами, позволяющими снизить расход смеси до минимума и получить тонкостенные формы из ЖСС для крупных отливок. При этом не только снижается расход жидкой смеси, но также улучшается газовый режим и облегчается выбивка смеси из отливок.
Средние и крупные формы могут изготавливаться двухслойными: жидкой смесью типового состава на свежем песке заполняют опоку до покрытия модели, остальную часть формы заливает жидкой наполнительной смесью на регенерате или с добавкой отработанной смеси при пониженном расходе жидкого стекла.
При изготовлении крупных стержней и форм допускается многократная периодическая заливка смеси с интервалом, не превышающим устойчивости пены. Для более качественного заполнения стержневых ящиков, особенно повышенной сложности, рекомендуется применять кратковременную вибрацию, пока смесь находится в жидком состоянии, до уплотнять верхние слои смеси в опоке ручными или пневматическими трамбовками.
Стержни и формы из ЕСС обычно не нуждаются в тепловой сушке. Если же в качестве противопригарных покрытий пользуются водными красками, то стержни подсушивают 30-60 мин, иногда до 2 ч в зависимости от их размера и типа сушил.
В качестве противопригарных покрытий используются водные и само-высыхающие краски.
Формы и стержни можно заливать металлом через несколько часов после изготовления.
При работе с жидкими смесями полностью устраняются такие неблагоприятные производственные факторы, как шум, вибрация, пыле-выделение. Газовыделение при заливке металлом форм из ХСС ниже, чем при заливке обычных форм.
4. САМОТВЕРДЕЮЩИЕ СМЕСИ НА ОСНОВЕ СИНТЕТИЧЕСКИХ СМ0Л
Процессы изготовления стержней и форм с отверждением в оснастке являются наиболее рациональным технологическим средством повышения точности и качества отливок, автоматизации процесса, снижения трудоемкости и увеличения производительности труда. Они основаны на применении смесей, характерных тем, что в качестве связующего материала в их состав вводят искусственные (синтетические) смолы: мочевиноформальдегидные (карбамидные), фенолформальдегидные фурановые и др.
Синтетические смолы получают в результате конденсации фенола, анилина с формальдегидом и мочевины с формальдегидом.
Эти смолы по характеру твердения могут быть:
термопластичными, функциональные группы таких смол не способны к межмолекулярному взаимодействию, их твердение производят в присутствии катализаторов (отвердителей);
термореактивными, функциональные группы таких смол склонны к межмолекулярному взаимодействию, их твердение осуществляется без катализаторов, при этом ускорение процесса отверждения достигается тепловым воздействием.
Особенность термореактивных смол (например, ПК-104) в том, что при нагреве они сначала размягчаются (20-30 с), а затем вследствие химических процессов затвердевают необратимо (3-4 мин).
Преимущество синтетических смол как связующих по сравнению с маслами в том, что процесс твердения смесей протекает с большой скоростью, особенно при нагреве, с образованием прочной и эластичной пленки, что резко ускоряет процесс изготовления стержней и форм. Это позволяет легко автоматизировать процесс с отверждением в оснастке, что существенно повышает размерную точность, улучшает качество.
К числу недостатков песчано-смоляных смесей относят их токсичность - при заливке форм выделяются вредные вещества, такие как фурфурол, формальдегид, поэтому в помещении литейного цеха необходимо обеспечивать усиленную местную вентиляцию с очисткой выбрасываемых в атмосферу газов.
4.1. Классификация связующих
В результате целенаправленной комплексной научно-исследовательской работы в нашей стране в последние годы разработано большое количество современных связующих, отвердителей и смесей, организовано их производство для новых процессов изготовления форм и стержней в нагреваемой и холодной оснастке (например, ФКС, СФ-480), которые превосходят лучшие зарубежные аналоги или находятся на их уровне /7/.
Наиболее распространена в СССР следующая классификация синтетических смол (табл. 2.1), используемых в литейном производстве.
Таблица 4.1 – Классификация синтетических смол (по Ляссу А.М.)
Класс смол | Наименование класса смол | Термостойкость смол | ||
Группа А | Группа Б | Группа В | ||
Малая | Средняя | Высокая | ||
Мочевиноформаль- дегидные (карбамидные) | А-1 УКС-Л, М-19-62, МБС, КС-58, ВК-1, КС-11, МФ-17, М-70 | Б-1 | В-1 | |
Мочевиноформаль-дегиднофенольные (карбамиднофенольные) | А-2 | Б-2 ФМС, ФПР-24 | В-2 | |
Мочевиноформаль-дегиднофурановые (карбамиднофура-новые) | А-3 | Б-3 УКС-ЛФ, М-19-62Ф, БС-40, КФ-40, МФС-1, Фуритол-102М, КСФ-1 | В-3 КФ-90 | |
Фенолформаль-дегидные (фенольные) | А-4 | Б-4 Фенолоспирт, СФЫ-011, СФ-480, ВР-1, ПК-104 | В-4 ОФ-1 | |
Фенолформаль-дегиднофурановые (фенолфурановые) | А-5 | Б-5 | В-5 ФФ-1С, ФФ-1Ф, ФФ-1ФМ, КОФ-4 | |
Полиацетатные | А-6 Поливиниловый спирт, ПВАЗ | Б-6 | В-6 |
I класс. Карбамидные смолы - продукты конденсации мочевины с формальдегидом, хорошо растворяются в воде и применяются для приготовления быстросохнущих и самовысыхающих связующих М, МСБ, МФ-17 и др.
Смолы карбамидного класса доступны и относительно дешевы, так как выпускаются централизованно, используются без подготовки, но при длительном хранении загустевают, в этом случае допускается растворение холодной водой. Очень длительное хранение (более года) приводит к самопроизвольной полимеризации, связующее сильно густеет, не разбавляется водой и теряет свои связующие свойства.
Смолы этого класса обладают высокой адгезионной способностью, большой скоростью отверждения, обеспечивают хорошую прочность смеси в твердом состоянии, но так как они являются жидкостью, прочность смеси во влажном состоянии на сжатие невысока (0,04-0,05)×105 Па(кгс/см2). Добавка глины увеличивает прочность в сыром состоянии, несколько снижая ее в сухом состоянии, но все равно прочность остается достаточно высокой, более 1О105 Па(кгс/см)
Добавка сульфитно-дрожжевой бражки (СДБ) повышает не только прочность в сыром состоянии, но и в сухом, а также термостойкость/ при этом уменьшается запах формальдегида /8/.
Наиболее высокой связующей способностью, обеспечивающей высокую прочность, обладают смолы УКС (ГХТ 14231-78) и М-19-62 (ГОСТ14231-28), но они имеют и существенный недостаток - весьма широкие пределы физико-химических свойств, что не обеспечивает стабильности свойств смеси. Для устранения этого недостатка разработана модификация смолы УКС-1 (литейные) (ТУ 6-05-1336-76), представляющая собой вязкую жидкость плотностью 1,2-Ю3 кг/м3
Карбамидные смолы обладают малой термостойкостью, поэтому применяются для изготовления цветного и тонкостенного чугунного литья. В стержневую смесь дают 2,5-3,0% связующего, температура сушки 120-180°С. После сушки стержни не гигроскопичны и легко выбиваются из отливок. Отрицательной особенностью карбамидных смол является содержание N2, представляющего опасность с точки зрения образования ситовидной пористости в отливках.
Мочевиноформальдегидные (карбамидные) смолы могут иметь более широкое применение, если путем специальных добавок существенно повысить их термостойкость. Примером может служить карбамиднофенольная смола ФМС (ТУ 6-05-7367-70), относящаяся ко П классу, получаемая в результате двухфазной конденсации фенола, карбамида с формальдегидом в щелочной среде; представляет собой однородную жидкость красновато-коричневого цвета с условной вязкостью 70-280с (по В3-4),, содержанием сухого остатка не менее 68% и содержанием N2 не более 8%.
К этому классу, может 6ыть отнесена и смола ФПР-24 (ТУ 6-05-1507-76), представляющая собой смесь трех смол: карбамидноформальдегидной, фенолоформальдегидной и модифицированной небольшим количеством фурилевого спирта. Смола - подвижная вязкая жидкость красновато-коричневого цвета плотностью 1200-1300 кг/м3, вязкостью 35-65 с (по вискозиметру ВЗ-4), содержание N2 не более 8%.
Смолы ФМС и ФПР-24 применяются для изготовления стержней в горячих.ящиках для чугунного литья, в смесь дают 2-3% связующего, температура нагрева ящика ЗВО-220°С.
II класс. Мочевиноформальдегидно-фурановые (карбамиднофурановые смолы) обладают средней термостойкостью, применяются для чугунного литья, в том числе толстостенного, а смола КФ-90 обладает высокой термостойкостью и применима для стального лттья.
Фуриловый спир