Для определения механических свойств материалов используют структурные и физические методы исследования металлов.
Материалы обладают разнообразными свойствами. Используя один метод их исследования, невозможно получить информацию о всех свойствах. Используют несколько методов анализа:
1. Определение химического состава.
Используются методы количественного анализа.
1.1. Если не требуется большой точности, то используют спектральный анализ.
Спектральный анализ основан на разложении и исследовании спектра электрической дуги или искры, искусственно возбуждаемой между медным электродом и исследуемым металлом.
Зажигается дуга, луч света через призмы попадает в окуляр для анализа спектра. Цвет и концентрация линий спектра позволяют определить содержание химических элементов.
Используются стационарные и переносные стилоскопы.
1.2. Более точные сведения о составе дает рентгеноспектральный анализ.
Проводится на микроанализаторах. Позволяет определить состав фаз сплава, характеристики диффузионной подвижности атомов.
2. Изучение структуры.
Различают макроструктуру, микроструктуру и тонкую структуру.
2.1. Макроструктурный анализ – изучение строения металлов и сплавов невооруженным глазом или, при небольшом увеличении, с помощью лупы.
Осуществляется после предварительной подготовки исследуемой поверхности (шлифование и травление специальными реактивами).
Позволяет выявить и определить дефекты, возникшие на различных этапах производства литых, кованных, штампованных и катанных заготовок, а также причины разрушения деталей.
Устанавливают: вид излома (вязкий, хрупкий); величину, форму и расположение зерен и дендритов литого металла; дефекты, нарушающие сплошность металла (усадочную пористость, газовые пузыри, раковины, трещины); химическую неоднородность металла, вызванную процессами кристаллизации или созданную термической и химико-термической обработкой; волокна в деформированном металле.
2.2. Микроструктурный анализ – изучение поверхности при помощи световых микроскопов. Увеличение – 50…2000 раз. Позволяет обнаружить элементы структуры размером до 0,2 мкм.
Образцы – микрошлифы с блестящей полированной поверхностью, так как структура рассматривается в отраженном свете. Наблюдаются микротрещины и неметаллические включения.
Для выявления микроструктуры поверхность травят реактивами, зависящими от состава сплава. Различные фазы протравливаются неодинаково и окрашиваются по-разному. Можно выявить форму, размеры и ориентировку зерен, отдельные фазы и структурные составляющие.
Кроме световых микроскопов используют электронные микроскопы с большой разрешающей способностью.
Изображение формируется при помощи потока быстро летящих электронов. Электронные лучи с длиной волны (0,04…0,12)·10-8 см дают возможность различать детали объекта, по своим размерам соответствующие межатомным расстояниям.
Просвечивающие микроскопы. Поток электронов проходит через изучаемый объект. Изображение является результатом неодинакового рассеяния электронов на объекте. Различают косвенные и прямые методы исследования.
При косвенном методе изучают не сам объект, а его отпечаток – кварцевый или угольный слепок (реплику), отображающий рельеф микрошлифа, для предупреждения вторичного излучения, искажающего картину.
При прямом методе изучают на просвет тонкие металлические фольги, толщиной до 300 нм. Фольги получают непосредственно из изучаемого металла.
Растровые микроскопы. Изображение создается за счет вторичной эмиссии электронов, излучаемых поверхностью, на которую падает непрерывно перемещающийся по этой поверхности поток первичных электронов. Изучается непосредственно поверхность металла. Разрешающая способность несколько ниже, чем у просвечивающих микроскопов.
2.3. Для изучения атомно-кристаллического строения твердых тел (тонкое строение) используются рентгенографические методы, позволяющие устанавливать связь между химическим составом, структурой и свойствами тела, тип твердых растворов, микронапряжения, концентрацию дефектов, плотность дислокаций.
3.Физические методы исследования.
3.1.Термический анализ основан на явлении теплового эффекта. Фазовые превращения в сплавах сопровождаются тепловым эффектом, в результате на кривых охлаждения сплавов при температурах фазовых превращений наблюдаются точки перегиба или температурные остановки. Данный метод позволяет определить критические точки.
3.2. Дилатометрический метод. При нагреве металлов и сплавов происходит изменение объема и линейных размеров – тепловое расширение. Если изменения обусловлены только увеличением энергии колебаний атомов, то при охлаждении размеры восстанавливаются. При фазовых превращениях изменения размеров необратимы.
Метод позволяет определить критические точки сплавов, температурные интервалы существования фаз, а также изучать процессы распада твердых растворов.
3.3. Магнитный анализ. Он используется для исследования процессов, связанных с переходом из паромагнитного состояния в ферромагнитное (или наоборот), причем возможна количественная оценка этих процессов.
Деформацией называется изменение формы и размеров тела под действием напряжений.
Напряжение – сила, действующая на единицу площади сечения детали.
Напряжения и вызываемые ими деформации могут возникать при действии на тело внешних сил растяжения, сжатия и т.д., а также в результате фазовых (структурных) превращений, усадки и других физико-химических процессов, протекающих в металлах, и связанных с изменением объема.
Металл, находящийся в напряженном состоянии, при любом виде нагружения всегда испытывает напряжения нормальные и касательные (рис.1.).
Рис. 1. Схема возникновения нормальных и касательных напряжений в металле при его нагружении
Рост нормальных и касательных напряжений приводит к разным последствиям. Рост нормальных напряжений приводит к хрупкому разрушению. Пластическую деформацию вызывают касательные напряжения.
Деформация металла под действием напряжений может быть упругой и пластической.
Упругой называется деформация, полностью исчезающая после снятия вызывающих ее напряжений.
При упругом деформировании изменяются расстояния между атомами металла в кристаллической решетке. Снятие нагрузки устраняет причину, вызвавшую изменение межатомного расстояния, атомы становятся на прежние места, и деформация исчезает.
Упругая деформация на диаграмме деформации характеризуется линией ОА (рис.2).
Рис. 2. Диаграмма зависимости деформации металла εот действующих напряжений σ
Если нормальные напряжения достигают значения сил межатомных связей, то наблюдается хрупкое разрушение путем отрыва (рис.3).
Рис. 3. Схема упругой деформации и хрупкого разрушения под действием упругих напряжений: а – ненапряженная решетка металла; б – упругая деформация; в, г – хрупкое разрушение в результате отрыва
Зависимость между упругой деформацией ε и напряжением σ выражается законом Гука
σ=Е ε,
где Е - модуль упругости.
Модуль упругости является важнейшей характеристикой упругих свойств металла. По физической природе величина модуля упругости рассматривается как мера прочности связей между атомами в твердом теле.
Эта механическая характеристика структурно нечувствительна, т. е. термическая обработка или другие способы изменения структуры не изменяют модуля упругости, а повышение температуры, изменяющее межатомные расстояния, снижает модуль упругости.
Пластической или остаточной называется деформация после прекращения действия вызвавших ее напряжений.
При пластическом деформировании одна часть кристалла перемещается по отношению к другой под действием касательных напряжений. При снятии нагрузок сдвиг остается, т.е. происходит пластическая деформация (рис.4).
В результате развития пластической деформации может произойти вязкое разрушение путем сдвига.
Рис. 4. Схема пластической деформации и вязкого разрушения под действием касательных напряжений: а – ненапряженная решетка; б – упругая деформация; в – упругая и пластическая деформация; г – пластическая деформация; д, е – пластичное (вязкое) разрушение в результате среза
Природа пластической деформации
Металлы и сплавы в твердом состоянии имеют кристаллическое строение, и характер их деформации зависит от типа кристаллической структуры и от наличия несовершенств в этой структуре.
Рассмотрим пластическую деформацию в монокристалле.
Пластическая деформация может протекать под действием касательных напряжений и может осуществляться двумя способами.
1. Трансляционное скольжение по плоскостям (рис. 5 а). Одни слои атомов кристалла скользят по другим слоям, причем они перемещаются на дискретную величину, равную целому числу межатомных расстояний.
В промежутках между полосами скольжения деформация не происходит. Твердое тело не изменяет своего кристаллического строения во время пластической деформации и расположение атомов в элементарных ячейках сохраняется.
Плоскостями скольжения является кристаллографические плоскости с наиболее плотной упаковкой атомов.
Это наиболее характерный вид деформации при обработке давлением.
2. Двойникование – поворот одной части кристалла в положение симметричное другой его части. Плоскостью симметрии является плоскость двойникования (рис. 5 б).
Двойникование чаще возникает при пластической деформации кристаллов с объемно-центрированной и гексагональной решеткой, причем с повышением скорости деформации и понижением температуры склонность к двойникованию возрастает.
![]() | ![]() |
а | б |
Рис. 5. Схемы пластической деформации различными способами:
а – скольжением; б – двойникованием
Двойникование может возникать не только в результате действия внешних сил, но и в результате отжига пластически деформированного тела. Это характерно для металлов с гранецентрированной кубической решеткой (медь, латунь). Двойникованием можно достичь незначительной степени деформации.
Дислокационный механизм пластической деформации. Пластическая деформация происходит в результате скольжения или двойникования. Ранее предполагали, что при скольжении одна часть кристалла сдвигается относительно другой части на целое число периодов как единое целое. Необходимое для этого напряжение получается на несколько порядков выше действительного сдвигового напряжения.
Для железа теоретическое значение сдвигового напряжения τтеор=13300 МПа, τреал=20 МПа.
В основу современной теории пластической деформации взяты следующие положения:
· скольжение распространяется по плоскости сдвига последовательно, а не одновременно;
· скольжение начинается от мест нарушений кристаллической решетки, которые возникают в кристалле при его нагружении.
Схема механизма деформации представлена на рис. 6 а.
В равновесном состоянии дислокация неподвижна. Под действием напряжения экстраплоскость смещается справа налево при незначительном перемещении атомов. Нижняя часть плоскости Р/S (SR) сместится вправо и совместится с нижним краем экстра- плоскости РQ.
QR - остаточная деформация.
При дальнейшем движении дислокация пройдет всю плоскость скольжения и выйдет на поверхность зерна. При этом верхняя часть зерна сдвинута относительно нижней на один межатомный период решетки (рис. 6, б).
При каждом перемещении дислокации на один шаг необходимо разорвать связь только между двумя рядами атомов в плоскости Р/S, а не между всеми атомами, расположенными выше и ниже плоскости скольжения. Необходимое сдвиговое напряжение при этом мало, равно практически действительному.
а б
Рис. 6. Схема дислокационного механизма пластической деформации а – перемещение атомов при двихении краевой дислокации на одно межатомное расстояние; б – перемещение дислокации через весь кристалл
Разрушение металлов. Процесс деформации при достижении высоких напряжений завершается разрушением. Тела разрушаются по сечению не одновременно, а вследствие развития трещин. Разрушение включает три стадии: зарождение трещины, ее распространение через сечение, окончательное разрушение.
Различают хрупкое разрушение – отрыв одних слоев атомов от других под действием нормальных растягивающих напряжений. Отрыв не сопровождается предварительной деформацией. Механизм зарождения трещины одинаков - благодаря скоплению движущихся дислокаций перед препятствием (границы субзерен, фазовые границы), что приводит к концентрации напряжений, достаточной для образования трещины. Когда напряжения достигают определенного значения, размер трещины становится критическим и дальнейший рост осуществляется произвольно.
Для хрупкого разрушения характерна острая, часто ветвящаяся трещина. Величина зоны пластической деформации в устье трещины мала. Скорость распространения хрупкой трещины велика - близка к скорости звука (внезапное, катастрофическое разрушение). Энергоемкость хрупкого разрушения мала, а работа распространения трещины близка к нулю.
Различают транскристаллитное разрушение – трещина распространяется по телу зерна, интеркристаллитное – по границам зерен (всегда хрупкое).
Результатом хрупкого разрушения является блестящий светлый кристаллический излом с ручьистым строением. Хрупкая трещина распространяется по нескольким параллельным плоскостям. Плоскость излома перпендикулярна нормальным напряжениям.
Вязкое разрушение – это разрушение путем среза под действием касательных напряжений. Ему всегда предшествует значительная пластическая деформация.
Трещина тупая раскрывающаяся. Величина пластической зоны впереди трещины велика. Малая скорость распространения трещины. Энергоемкость значительная, энергия расходуется на образование поверхностей раздела и на пластическую деформацию. Большая работа затрачивается на распространение трещины. Поверхность излома негладкая, рассеивает световые лучи, матовая (волокнистый) излом. Плоскость излома располагается под углом.
По излому можно определить характер разрушения.
Механические свойства и способы определения их количественных характеристик.
Основными механическими свойствами являются прочность, упругость, вязкость, твердость. Зная механические свойства, конструктор обоснованно выбирает соответствующий материал, обеспечивающий надежность и долговечность конструкций при их минимальной массе.
Механические свойства определяют поведение материала при деформации и разрушении от действия внешних нагрузок.
В зависимости от условий нагружения механические свойства могут определяться при:
1) статическом нагружении – нагрузка на образец возрастает медленно и плавно;
2) динамическом нагружении – нагрузка возрастает с большой скоростью, имеет ударный характер;
3) повторном, переменном или циклическом нагружениях – нагрузка в процессе испытания многократно изменяется по величине или по величине и направлению.
Для получения сопоставимых результатов образцы и методика проведения механических испытаний регламентированы ГОСТами.
При статическом испытании на растяжение: ГОСТ 1497 получают характеристики прочности и пластичности.
Прочность – способность материала сопротивляться деформациям и разрушению.
Испытания проводятся на специальных машинах, которые записывают диаграмму растяжения, выражающую зависимость удлинения образца Δ l (мм) от действующей нагрузки Р, т.е. Δ l=f (P).
Для получения данных по механическим свойствам перестраивают зависимость относительного удлинения Δ l от напряжения σ
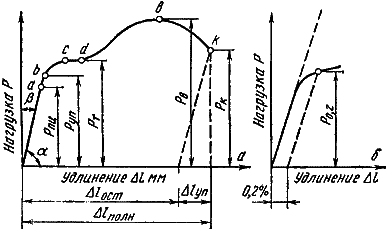
а б
Рис. 7. Диаграмма растяжения: а – абсолютная, б – относительная схема определения условного предела текучести
Проанализируем процессы, которые происходят в материале образца при увеличении нагрузки.
Участок оа на диаграмме соответствует упругой деформации материала, когда соблюдается закон Гука. Напряжение, соответствующее упругой предельной деформации в точке а называется пределом пропорциональности.
Предел пропорциональности (σпц) – максимальное напряжение, до которого сохраняется линейная зависимость между деформацией и напряжением
.
При напряжениях выше предела пропорциональности происходит равномерная пластическая деформация (удлинение или сужение сечения).
Каждому напряжению соответствует остаточное удлинение, которое получается путем проведения из соответствующей точки диаграммы растяжения линии параллельной оа. Так как практически невозможно установить точку перехода в неупругое состояние, то устанавливают условный предел упругости – максимальное напряжение, до которого образец получает только упругую деформацию. Считают напряжение, при котором остаточная деформация очень мала (0,005…0,05%).
В обозначении указывается значение остаточной деформации (σ0,05)
.
Предел текучести характеризует сопротивление материала небольшим пластическим деформациям. В зависимости от природы материала используют физический или условный предел текучести.
Физический предел текучести (σт)– это напряжение, при котором происходит увеличение деформации при постоянной нагрузке (наличие горизонтальной площадки на диаграмме растяжения). Используется для очень пластичных материалов
.
Но основная часть металлов и сплавов не имеет площадки текучести.
Условный предел текучести (σ0,2)– это напряжение, вызывающее остаточную деформацию δ=0,2%:
.
Физический или условный предел текучести являются важными расчетными характеристиками материала. Действующие в детали напряжения должны быть ниже предела текучести. Равномерная по всему объему пластичная деформация продолжается до значения предела прочности. В точке в в наиболее слабом месте начинает образовываться шейка – сильное местное утомление образца.
Предел прочности (σв)– напряжение, соответствующее максимальной нагрузке, которую выдерживает образец до разрушения (временное сопротивление разрыву)
.
Образование шейки характерно для пластичных материалов, которые имеют диаграмму растяжения с максимумом.
Предел прочности характеризует прочность как сопротивления значительной равномерной пластичной деформации. За точкой в, вследствие развития шейки, нагрузка падает, и в точке с происходит разрушение.
Истинное сопротивление разрушению – это максимальное напряжение, которое выдерживает материал в момент, предшествующий разрушению образца (рис. 8),
.
Истинное сопротивление разрушению значительно больше предела прочности, так как оно определяется относительно конечной площади поперечного сечения образца.
F к- конечная площадь поперечного сечения образца.
Истинные напряжения Si определяют как отношение нагрузки к площади поперечного сечения в данный момент времени
;
При испытании на растяжение определяются и характеристики пластичности.
Рис. 8. Истинная диаграмма растяжения
Пластичность – способность материала к пластической деформации, т.е. способность получать остаточное изменение формы и размеров без нарушения сплошности.
Это свойство используют при обработке металлов давлением.
Характеристики:
1) относительное удлинение
где и
– начальная и конечная длина образца;
– абсолютное удлинение образца, определяется измерением образца после разрыва;
2) относительное сужение
,
где - начальная площадь поперечного сечения,
-площадь поперечного сечения в шейке после разрыва.
Относительное сужение более точно характеризует пластичность и служит технологической характеристикой при листовой штамповке.
Пластичные материалы более надежны в работе, т.к. для них меньше вероятность опасного хрупкого разрушения.
Механические свойства и способы определения их количественных характеристик: твердость, вязкость, усталостная прочность.
Твердость – это сопротивление материала проникновению в его поверхность стандартного тела (индентора), не деформирующегося при испытании.
Широкое распространение объясняется тем, что не требуются специальные образцы.
Это неразрушающий метод контроля. Основной метод оценки качества термической обработке изделия. О твердости судят либо по глубине проникновения индентора (метод Роквелла), либо по величине отпечатка от вдавливания (методы Бринелля, Виккерса, микротвердости).
Во всех случаях происходит пластическая деформация материала. Чем больше сопротивление материала пластической деформации, тем выше твердость.
Наибольшее распространение получили методы Бринелля, Роквелла, Виккерса и микротвердости.
Схемы испытаний представлены на рис. 9.
Рис. 9. Схемы определения твердости: а – по Бринеллю; б – по Роквеллу; в – по Виккерсу
Твердость по Бринеллю. Испытание проводят на твердомере Бринелля (рис. 9 а).
В качестве индентора используется стальной закаленный шарик диаметром D 2,5; 5; 10 мм, в зависимости от толщины изделия.
Нагрузка Р, в зависимости от диаметра шарика и измеряемой твердости: для термически обработанной стали и чугуна – , литой бронзы и латуни –
, алюминия и других очень мягких металлов –
.
Продолжительность выдержки τ: для стали и чугуна – 10 с, для латуни и бронзы – 30 с.
Полученный отпечаток измеряется в двух направлениях при помощи лупы Бринелля.
Твердость определяется как отношение приложенной нагрузки Р к сферической поверхности отпечатка F:
.
Стандартными условиями являются D = 10 мм; Р = 3000 кгс; τ = 10 с. В этом случае твердость по Бринеллю обозначается НВ 250, в других случаях указываются условия: НВ D / P /τ, НВ 5/ 250 /30 – 80.
Метод Роквелла основан на вдавливании в поверхность наконечника под определенной нагрузкой (рис. 9 б).
Индентор для мягких материалов (до НВ 230) – стальной шарик диаметром 1,6 мм, для более твердых материалов – конус алмазный.
Нагружение осуществляется в два этапа. Сначала прикладывается предварительная нагрузка Р 0 (10 ктс) для плотного соприкосновения наконечника с образцом. Затем прикладывается основная нагрузка Р 1, в течение некоторого времени действует общая рабочая нагрузка Р. После снятия основной нагрузки определяют значение твердости по глубине остаточного вдавливания наконечника h под нагрузкой Р 0.
В зависимости от природы материала используют три шкалы твердости (табл. 1)
Таблица 1. Шкалы для определения твердости по Роквеллу
Шкала | Обозначение твердости | Форма наконечника | Нагрузка, кг | Пределы изм. в ед. твердости Бринелля |
В | HRB | шарик стальной | 60-230 | |
С | HRC | алмазный конус | 230-700 | |
А | HRA | алмазный конус | свыше 700 |
Твердость по Методу Виккерса определяется по величине отпечатка (рис.9 в).
Ее определяют путем вдавливания в испытуемую поверхность алмазной четырехгранной пирамиды с углом при вершине 136 градусов под нагрузкой 120 кг. Число твердости по Виккерсу (HV) представляет собой нагрузку, приходящуюся на единицу поверхности отпечатка и определяется по формуле
=
,
где Р - нагрузка на пирамиду в кг,
d - среднее арифметическое обеих диагоналей отпечатка после снятия нагрузки в мм,
α - угол между противоположными гранями пирамиды, α = 136°.
Числа твердости HV, вычисленные по указанной выше формуле, в зависимости от длины диагонали, величины приложенной нагрузки, приведены в таблицах. Следовательно, твердость по методу Виккерса практически определяют по величине диагонали отпечатка. Твердость по Виккерсу для стали, имеющей твердость НВ до 400, примерно соответствует значениям твердости по Бринеллю. При более высокой твердости ее значение становится больше, чем по Бринеллю. Способ микротвердости – для определения твердости отдельных структурных составляющих и фаз сплава, очень тонких поверхностных слоев (сотые доли миллиметра).
Аналогичен способу Виккерса. Индентор – пирамида меньших размеров, нагрузки при вдавливании Р составляют 5…500 гс
.
Метод царапания. Алмазным конусом, пирамидой или шариком наносится царапина, которая является мерой. При нанесении царапин на другие материалы и сравнении их с мерой судят о твердости материала.
Можно нанести царапину шириной 10 мм под действием определенной нагрузки. Наблюдают за величиной нагрузки, которая дает эту ширину.
Динамический метод (по Шору). Шарик бросают на поверхность с заданной высоты, он отскакивает на определенную величину. Чем больше величина отскока, тем тверже материал.
В результате проведения динамических испытаний на ударный изгиб специальных образцов с надрезом оценивается вязкость материалов и устанавливается их склонность к переходу из вязкого состояния в хрупкое.
Вязкость – способность материала поглощать механическую энергию внешних сил за счет пластической деформации, является энергетической характеристикой материала, выражается в единицах работы. Вязкость металлов и сплавов определяется их химическим составом, термической обработкой и другими внутренними факторами.
Также вязкость зависит от условий, в которых работает металл (температуры, скорости нагружения, наличия концентраторов напряжения). С повышением температуры вязкость увеличивается (см. рис. 10).
Предел текучести S т существенно изменяется с изменением температуры, а сопротивление отрыву S от не зависит от температуры. При температуре выше Т в предел текучести меньше сопротивления отрыву. При нагружении сначала имеет место пластическое деформирование, а потом – разрушение. Металл находится в вязком состоянии.
При температуре ниже Т н сопротивление отрыву меньше предела текучести. В этом случае металл разрушается без предварительной деформации, то есть находится в хрупком состоянии. Переход из вязкого состояния в хрупкое осуществляется в интервале температур Т н - Т в.
Хладоломкостью называется склонность металла к переходу в хрупкое состояние с понижением температуры.
Хладоломкими являются железо, вольфрам, цинк и другие металлы, имеющие объемноцентрированную кубическую и гексагональную плотноупакованную кристаллическую решетку.
Рис. 10. Влияние температуры на пластичное и хрупкое состояние
Способы оценки вязкости. Ударная вязкость характеризует надежность материала, его способность сопротивляться хрупкому разрушению.
Испытание проводят на образцах с надрезами определенной формы и размеров. Образец устанавливают на опорах копра надрезом в сторону, противоположную удару ножа маятника, который поднимают на определенную высоту (рис. 11).
Рис.11. Схема испытания на ударную вязкость: а – схема маятникового копра; б – стандартный образец с надрезом; в – виды концентраторов напряжений; г – зависимость вязкости от температуры
На разрушение образца затрачивается работа:
,
где Р – вес маятника, Н – высота подъема маятника до удара, h – высота подъема маятника после удара.
Характеристикой вязкости является ударная вязкость (ан) - удельная работа разрушения.
.
где F 0 - площадь поперечного сечения в месте надреза.
ГОСТ 9454 – 78 ударную вязкость обозначает KCV, KCU, KCT.
KC – символ ударной вязкости, третий символ показывает вид надреза: острый (V), с радиусом закругления (U), трещина (Т) (рис. 11 в).
Серийные испытания для оценки склонности металла к хладоломкости и определения критических порогов хладоломкости.
Испытывают серию образцов при различных температурах и строят кривые «ударная вязкость – температура» (ан – Т) (рис. 11 г), определяя пороги хладоломкости.
Порог хладоломкости - температурный интервал изменения характера разрушения, является важным параметром конструкционной прочности. Чем ниже порог хладоломкости, тем менее чувствителен металл к концентраторам напряжений (резкие переходы, отверстия, риски), к скорости деформации.
Оценка вязкости по виду излома.
При вязком состоянии металла в изломе более 90 % волокон, за верхний порог хладоломкости Т в принимается температура, обеспечивающая такое состояние. При хрупком состоянии металла в изломе 10 % волокон, за нижний порог хладоломкости Т н принимается температура, обеспечивающая такое состояние. В технике за порог хладоломкости принимают температуру, при которой в изломе 50 % вязкой составляющей. Причем эта температура должна быть ниже температуры эксплуатации изделий не менее чем на 40oС.
Испытания на выностивость (ГОСТ 2860) дают характеристики усталостной прочности.
Усталость - разрушение материала при повторных знакопеременных напряжениях, величина которых не превышает предела текучести.
Усталостная прочность – способность материала сопротивляться усталости.
Процесс усталости состоит из трех этапов, соответствующие этим этапам зоны в изломе показаны на рис. 12.
Рис 12. Схема зарождения и развития трещины при переменном изгибе круглого образца:
1 – образование трещины в наиболее нагруженной части сечения, которая подвергалась микродеформациям и получила максимальное упрочнение;
2 – постепенное распространение трещины, гладкая притертая поверхность;