Обтачивание плоскостей. Необходимость выделять обтачивание плоскости в отдельную операцию встречается редко (например, при изготовлении тонких дисков). Обтачивание плоскости выполняется как один из переходов операции, в которой обрабатывается примыкающая к плоскости поверхность вращения. При таком построении операции (обработка в одну установку) соблюдается (без участия приспособления) перпендикулярность плоскости к оси поверхности вращения.
Значимость обтачивания плоскости как перехода операции зависит от размеров и формы детали. Для одних деталей (рис. 5.18, а) этот переход может быть в операции основным, а для других (рис. 5.18, б) — второстепенным. Часто плоскость образуется в том же переходе, что и цилиндрическая поверхность (вытачивание канавки, обтачивание ступени валика резцом с углом в плане j = 90° и т. п.).
а б
Рис. 5.18. Типы плоских поверхностей
а б
Рис. 5.19. Обтачивание с прямой (а) и обратной (б) подачей
Для обтачивания плоскости применяют проходной или подрезной резец. Выбрав резец, пригодный не только для обтачивания плоскости, но и для других переходов, уменьшают разнообразие резцов, необходимых для операции. Обтачивание выполняют с прямой или обратной подачей (рис. 5.19). Второй метод дает несколько лучшую точность, но менее удобен для контроля координаты плоскости, если нужны пробные проходы и промеры.
|
|
С позиций точности обработки плоская поверхность не имеет собственного размера (подобного, например, диаметру у цилиндрической поверхности). Поэтому требования к ней состоят из требований к точности формы и шероховатости поверхности.
Точность формы зависит от точности станка. Характерным дефектом формы является неплоскостность типа показанной на рис. 5.20. Такой дефект не обнаруживается при контроле торцового биения, поэтому в необходимых случаях предусматривают контроль плоскостности с помощью лекалькой линейки, по краске и т. п., в зависимости от местоположения плоскости и требуемой точности формы. Точность плоскости по чистоте обработки получается такой же, как при обтачивании цилиндрических поверхностей.
Рис 5.20. Дефекты плоской поверхности
Строгание и фрезерование плоскостей. Строгание плоскостей на продольно-строгальных станках почти совершенно вытеснено более производительным фрезерованием. Оно сохраняется, главным образом, в условиях единичного производства благодаря тому, что строгальные станки выгодно отличаются от фрезерных простотой необходимого инструмента (резцы) и наладки.
Операция фрезерования требует надежного закрепления детали и по возможности ближе к месту обработки во избежание вибраций. В зависимости от размеров и формы деталь закрепляют непосредственно на столе станка, в тисках, в патроне, но чаще всего (исключая единичное производство) в специальном приспособлении.
|
|
По величине допустимого припуска на обработку фрезерование относится к самым универсальным процессам обработки. Наибольшую величину припуска, который возможно снять в один проход, ограничивает лишь надежность закрепления детали, прочность детали и мощность станка.
Различают фрезерование цилиндрическое (осевое) и торцовое.
Для цилиндрического фрезерования желательно (а при большой ширине обработки — обязательно) горизонтальное положение плоскости с тем, чтобы использовать для операции горизонтально-фрезерный станок, допускающий двустороннее закрепление инструмента. Горизонтальное положение плоскости благоприятно также для приспособления, несущего деталь (благоприятное направление действующих сил).
Торцовое фрезерование в большинстве случаев оказывается производительнее и несколько точнее; область его применения значительно шире.
Для фрезерования широких плоскостей применяют крупные торцовые фрезы со вставными ножами или резцами—фрезерные головки (стандартные головки изготовляют с диаметрами до 600 мм). Для деталей из цветных сплавов часто пользуются однозубыми торцовыми фрезами, работающими на режимах, близких к тонкому точению. Такая обработка заменяет трудно выполнимое шлифование (t до 0,02 мм при шероховатости до Ra 1.25).
Операции фрезерования плоскости характеризуется возможностью значительно повышать производительность путем одновременной обработки деталей. Для небольших деталей эта возможность обусловлена сравнительно большой площадью стола станка и большим ходом стола, позволяющими применять крупные многоместные приспособления.
Для деталей более крупных одновременная обработка возможна на карусельно-фрезерном станке, причем станок двухшпиндельный позволяет в одной операции сделать и черновую, и чистовую обработку.
Станки продольно-фрезерные рассчитаны на обработку плоскостей с двух или трех (в зависимости от количества шпинделей) сторон детали. Высокопроизводительная непрерывная двусторонняя обработка деталей является основным назначением барабанно-фрезерных станков.
Рис. 5.21. Схемы шлифования плоских поверхностей:
а — на станке для наружного шлифования цилиндрических поверхностей; б—на внутришлифовальном станке
Шлифование плоскостей. Предшествующей обработкой для операций плоского шлифования служит чистовое обтачивание или фрезерование плоскости.
Плоскость и примыкающую к ней цилиндрическую поверхность, обточенные в одной операции, шлифуют также в одной операции на станке, требующемся для цилиндрической поверхности (рис. 5.21). В других случаях плоскость шлифуют на плоскошлифовальном станке.
Чистовым шлифованием обеспечивают величину плоскостности от 0,02 мм и больше (в зависимости от протяженности плоскости) и шероховатость до Ra 0.63.
Протягивание плоскостей. Как и протягивание отверстий, протягивание плоскостей отличается, прежде всего, высокой производительностью при снятии значительного припуска на обработку и большой точностью обработки. В большинстве случаев протягивание производят без какой-либо подготовительной обработки плоскости, снимая припуск в 2—6 мм.
Для наружного протягивания выпускают протяжные станки вертикального типа одинарного или двойного действия. Вторые имеют две плиты с протяжками, работающими попеременно, с целью перекрытия вспомогательного времени на установку и закрепление детали машинным временем.
Обрабатываемую деталь устанавливают и закрепляют в приспособлении, рассчитанном на получение заданной координаты плоскости. Погрешность, вносимая в координату (в исходный размер) методом обработки, колеблется в пределах 0,02— 0,06 мм, при шероховатости поверхности до Ra 1.25. Таким образом, одна операция протягивания в состоянии заменить не только черновое и чистовое фрезерование, но и шлифование плоскости, вместе взятые.
|
|
Протягиванием обрабатывают как открытые плоскости, так и сочетания плоскостей. Длину цельных протяжек допускают до 400—500 мм, а более длинные делают составными.
При протягивании широких плоскостей зубья протяжки получаются соответственно широкими, и для уменьшения нагрузки на протяжку (а также на деталь) подача на зуб должна быть малой. Встречаясь с грубой поверхностью заготовки, зубья протяжки быстро тупятся и легко выкрашиваются. В связи с этим применяют прогрессивное протягивание. Особенностью этого метода является то, что зубья протяжки снимают не тонкие стружки в направлении припуска на обработку, а толстые стружки в направлении ширины плоскости, подобно тому, как это делал бы резец на строгальном станке (рис. 5.22,а). Вариантов этого способа существует много. Например, для уменьшения длины протяжки (и уравновешивания боковых нагрузок) предусматривают не один, а два ряда режущих зубьев (рис. 5.22, б).
|
|
|
|
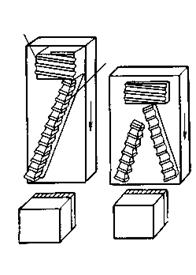
Рис. 5.22. Схемы прогрессивного протягивания