Станочные приспособления состоят из: установочных (опорных) элементов, зажимных устройств, корпусов, вспомогательных деталей и делительных устройств, силовых приводов, элементов для направления режущего инструмента, крепежных деталей.
|
|
|
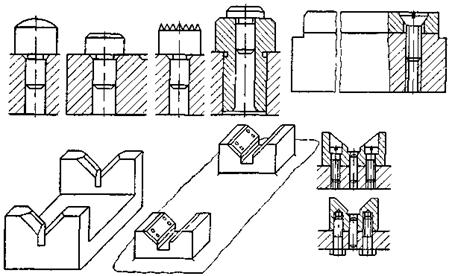
Рис. 6.12. Виды установочных неподвижных опор:
а – штыри; б – пластины; в – призмы
Установочные (опорные) элементы. Установочные элементы служат для установки на них обрабатываемых деталей и правильного размещения в приспособлении обрабатываемой детали.
Основными установочными элементами являются неподвижные опоры, жестко связанные с корпусом приспособления. Неподвижные установочные опоры (рис. 6.12) выполняются в виде опорных штырей (рис. 6.12, а), пластин (рис. 6.12, б) и призм (рис. 6.12, в). Опорные штыри со сферической и насеченной головками используются при установке деталей в приспособлении необработанными поверхностями. Эго делает контакт опоры с установочной поверхностью детали близким к точечному, создает устойчивость установки детали. При установке обрабатываемой детали в приспособлении обработанными поверхностями применяют опорные штыри с плоской головкой. В этом случае использование опорных штырей со сферической головкой не рекомендуется, так как точечный контакт опоры с поверхностью детали приводит к быстрому износу головки штыря, что снижает точность установки, а, кроме того, в результате точечного контакта может остаться вмятина на установочной поверхности детали.
В некоторых случаях штыри устанавливают в закаленные втулки, запрессованные в корпус приспособления, что обеспечивает смену только износившегося штыря (корпус приспособления остается).
Опорные пластины применяют при установке относительно крупных и тяжелых деталей или при обработке со значительными усилиями резания. Детали устанавливаются на пластины чисто обработанными поверхностями.
Рис. 6.13. Регулируемые винтовые опоры
Крепятся пластины к корпусу приспособления винтами с утопленной головкой. Опорные призмы используют для установки деталей в приспособление по их наружным цилиндрическим поверхностям. При установке деталей в приспособлении по необработанным поверхностям применяются также регулируемые винтовые опоры 1 (рис. 6.13) в качестве основных.
Для придания большей жесткости и устойчивости обрабатываемой детали в приспособлении вместе с основными размещают дополнительные (вспомогательные) самоустанавливающиеся и подводимые опоры (рис. 6.14). На рис. 6.14апоказана самоустанавливающаяся опора. Установочная поверхность обрабатываемой детали 1 контактирует с опорой 2 плунжера 3 под действием пружины 4. Плунжер 3 закрепляется винтом 6 при помощи пальца 5. Вырез на плунжере 3 ограничивает его подъем. На рис. 6.14бпоказана подводимая опора. При нажатии на рукоятку 6 клин 4 перемещается влево, поднимая плунжер 2 с регулируемой по высоте опорой 1. Плунжер с опорой закрепляется клином 4 при помощи винта 5 вращением рукоятки 6. Перемещаясь влево, винт 5 конусным концом раздвигает шпонки 3, стопоря клин 4.
При обработке корпусных деталей, деталей типа рычагов и др. часто устанавливают их в приспособлении плоскостью и двумя базовыми отверстиями на два установочных пальца его. Если устанавливают тяжелые детали, то пальцы делают выдвижными. Их вводят в базовые отверстия обрабатываемой детали после установки ее на плоскость (например, при установке в приспособление-спутник балансира об. 219).
|
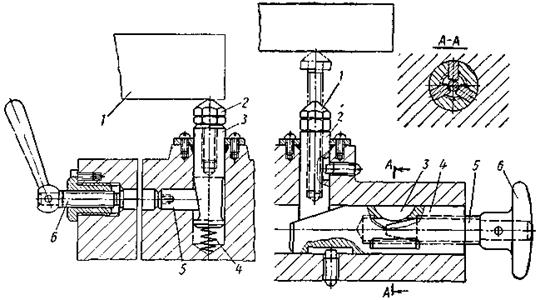
а б
Рис. 6.14. Вспомогательные опоры:
а – самоустанавливающаяся; б – подводимая
Два установочных пальца, один из которых делают цилиндрическим, а другой – ромбическим (срезанным), и плоскость достаточны для придания обрабатываемой детали нужного положения в приспособлении. Таким образом, срезанный палец уменьшает влияние колебаний в расстоянии между осями отверстий обрабатываемых деталей на точность их установки в приспособлении.
3ажимные устройства приспособлений служат для зажима и разжима деталей. Эти устройства должны обеспечивать при зажиме заданное положение детали, приданное ей при установке в приспособлении, и не должны допускать ее сдвига, поворота или вибрации при резании.
Определение сил зажима и их направления производится по усилиям резания и их моментам, действующим на обрабатываемую деталь. Точки приложения сил зажима должны исключать возможность появления опрокидывающих сил и изгибающих моментов.
Силы зажима детали в приспособлении определяются из условий равновесия свободного твердого тела.
Зажимные устройства бывают простые и сложные. Простые зажимные устройства, называемые обычно зажимами, состоят из одного элементарного механизма. К этим зажимам относят винтовые, клиновые, эксцентриковые и др. Сложные (комбинированные) зажимные устройства состоят из нескольких простых устройств, соединенных вместе.
Корпусы, вспомогательные детали и делительные устройства. На корпусе монтируются все остальные элементы приспособления, поэтому он является основной базовой деталью любого приспособления. Расположение этих элементов в корпусе и их конструкция предопределяются формой и габаритными размерами обрабатываемых деталей и выполняемой обработкой. Как и другие элементы приспособления, корпус должен быть простым и дешевым в изготовлении. Кроме того, корпус приспособления должен быть жестким, прочным и устойчивым. Силы зажима и резания через обрабатываемую деталь передаются корпусу, и он не должен деформироваться и вибрировать при ее обработке. Он должен обеспечивать быструю установку и снятие обрабатываемых деталей, иметь хороший доступ для очистки от стружки, должен быть удобным для установки на станке и обслуживания.
Заготовки для корпусов приспособлений могут быть: литыми из серого чугуна; сварными из стальных плит, листов и сортовых профильных материалов (угольников, швеллеров и др.); коваными из стали; сварно-литыми и сборными из отдельных стандартизованных или нормализованных деталей, собранных при помощи винтов.
Корпусы приспособлений средних и крупных размеров изготовляют обычно литыми или сварными. Литьем можно получить сложные корпусы с большей жесткостью. К сварным корпусам для повышения жесткости приваривают ребра жесткости.
В приспособлениях для обработки небольших деталей простой формы используют стальные кованые корпусы.
Рис. 6.15. Приспособление с литым корпусом
На рис. 6.15 показано приспособление, в котором заготовка для корпуса приспособления отлита из серого чугуна в форме неравнобокого угольника.
Наиболее распространенными вспомогательными деталями приспособлений являются ручки, опорные ножки корпусов, шпонки для, ускорения установки приспособления на станке, выталкиватели обработанных деталей, установы (упоры) применяемые при наладке станка. На эти вспомогательные детали имеются стандарты и нормали, согласно которым они должны конструироваться.
Рис. 6.16. Вытяжной конусный фиксатор
Для фиксации в определенном положении поворотной части приспособления, в которой закреплена обрабатываемая деталь, используются делительные устройства, состоящие из делительного диска, закрепленного на поворотной части приспособления, и фиксатора.
Конструкции фиксаторов различны, но наиболее распространенными являются быстродействующие фиксаторы, заскакивающие в гнездо под действием пружины. На рис. 6.16 дана конструкция вытяжного конусного фиксатора делительного устройства. При фиксировании детали поворотом головки 1 вводят штифт 2 в пазы направляющей втулки 3. Конический фиксатор 4 при этом под действием пружины 6 переместится влево во втулке 3, которая установлена в неподвижной части приспособления, и заскочит в одну из втулок 5 (гнездо) поворотной части приспособления.
При выводе фиксатора из втулки 5 штифт фиксатора перемещается вправо по направляющей втулке 3. При выходе из втулки 5 фиксатор поворачивается на 90° и удерживается штифтом 2 в натянутом положении.
Силовые приводы. В станочных приспособлениях ручные зажимы все более часто заменяются механизированными (силовыми), которые повышают производительность труда за счет сокращения времени установки и снятия детали, а также облегчают условия труда. Кроме того, применение силовых приводов устраняет ряд недостатков, присущих ручным зажимам: нестабильность величины силы зажима деталей; относительно небольшая величина силы зажима, развиваемая рукой рабочего; субъективность оценки необходимой величины силы зажима для надежного закрепления детали, приводящая к пережиму детали.
Наибольшее распространение получили пневмо-, гидро- и пневмогидроприводы.
Пневматические силовые приводы. Пневмоприводы широко применяются на машиностроительных предприятиях, так как в их составе имеются мощные компрессорные.
Эти приводы подразделяются на поршневые и диафрагменные. Они монтируются или в корпусе приспособления, составляя с ним одно целое, или прикрепляются к корпусу. При универсальной (агрегатированной) компоновке пневмопривод перемещает зажимные элементы различных станочных приспособлений.
Поршневые приводы бывают одно- или двустороннего действия. В первом случае воздух подается с одной стороны поршня, а возврат поршня в исходное положение происходит под действием пружины. Односторонние приводы используют в тех случаях, когда разжим обработанной детали не требует больших усилий. В пневмоприводах двустороннего действия сжатый воздух поочередно подается в две полости цилиндра. Такие пневмоприводы применяются в приспособлениях, вращающихся при обработке (например, токарные и револьверные станки); в стационарных приспособлениях, устанавливаемых на столах станков; в приспособлениях на вращающихся столах и т. д.
На рис. 6.17 показан поршневой пневмопривод с вращающимся цилиндром. В крышке 1 корпуса 2 пневмоцилиндра жестко установлена вращающаяся ось 12, на которой имеется невращающийся приемник 11 сжатого воздуха. В приемник ввернуты штуцеры 9 и 8. Поршень 4 закреплен на штоке 5. На поршне имеются уплотнители 3 из маслостойкой резины, прижатые к нему кольцом 7. В корпусе предусмотрены уплотнитель 6 из резины и прокладки между корпусом и крышкой, препятствующие утечке воздуха из пневмоцилиндра в атмосферу. Утечке воздуха из приемника 11 препятствуют уплотнение 10 и воротник. Зажим детали происходит при поступлении сжатого воздуха в правую полость пневмоцилиндра. При разжиме детали сжатый воздух подается к штуцеру 8 и через нижнее отверстие в оси 12 поступает в левую полость пневмоцилиндра.
Рис. 6.17. Вращающийся поршневой пневмопривод двустороннего действия
Основные параметры вращающихся пневмоцилиндров нормализованы.
Сила на штоке пневмоцилиндра двустороннего действия
,
где р – давление воздуха на поршень (обычно давление в цеховой сети, равное 4 – 5 кГ/см2);
D – диаметр поршня;
η ≈ 0,85 – к. п. д.
Расход воздуха за один ход поршня
,
где р 1 – давление в цилиндре;
F – площадь поршня;
L – ход поршня;
р 2 – давление внешней среды.
Для пневмоцилиндров одностороннего (толкающего) действия сила на штоке определится
,
где Рпр – сопротивление возвратной пружины при крайнем рабочем положении поршня.
Для увеличения силы на штоке применяют пневмоцилиндры с несколькими поршнями (2–3), закрепленными на одном штоке. Они используются и для стационарных и для вращающихся приспособлений.
В специальных приспособлениях в качестве механизированных приводов находят применение плавающие пневмоцилиндры. Конструктивная особенность их состоит в том, что на конце вертикального штока и в серьге нижней крышки цилиндра закреплены на осях шарнирно-рычажные механизмы, связанные с прихватами для зажима детали. При поступлении сжатого воздуха в нижнюю полость цилиндра деталь зажимается, а при поступлении воздуха в верхнюю полость – деталь разжимается.
Диафрагменные приводы с упругими диафрагмами также бывают одно- и двустороннего действия. Они разделяются на универсальные, встраиваемые и прикрепляемые и применяются при небольших зажимных усилиях.
Диафрагменный привод состоит из штампованного стального или литого чугунного корпуса, разделенного на две половины, между которыми размещены плоские, в форме тарелок, диафрагмы из прорезиненной ткани толщиной 2 мм.
По сравнению с пневмоцилиндрами пневмокамеры имеют ряд преимуществ: они проще и дешевле, не требуют такой точности и чистоты обработки поверхности, как пневмоцилиндры, исключают утечку сжатого воздуха до полного износа диафрагмы, выдерживают очень большое число включений (до 500 тыс.), тогда как манжеты пневмоцилиндров выдерживают не более 50 тыс. включений.
К недостаткам пневмокамер следует отнести небольшую величину хода штока и нестабильность усилия на штоке при перемещении штока.
Основные размеры пневмокамер нормализованы.
Рис. 6.18. Нормализованный диафрагменный пневмопривод
На рис. 6.18 показан нормализованный диафрагменный привод одностороннего действия. Резинотканевая диафрагма 1, закрепленная между двумя крышками 2, жестко связана со стальным опорным диском 3, установленным на штоке 4. Сжатый воздух поступает в бесштоковую полость пневмокамеры, диафрагма 1 при этом прогибается и перемещает диск 3 и связанный с ним шток 4. Когда сжатый воздух выпускается в атмосферу, система возвращается в исходное положение под действием пружин 5 и 6.
Работу пневмокамеры определяют сила Q на штоке и длина его рабочего хода. Сила Q зависит от отношения , где d – диаметр опорного диска; D – диаметр рабочей части диафрагмы (рис. 6.18), и от длины рабочего хода штока.
С увеличением отношения сила Q возрастает; по мере удаления штока от своего исходного положения сила Q уменьшается. Энергия сжатого воздуха в конце хода штока расходуется на упругую деформацию, и полезное усилие на штоке становится равным нулю.
По этой причине используют часть длины рабочего хода, чтобы сила Q на штоке была равна 80 – 85% силы при исходном положении штока.
На практике принимают отношение ≈ 0,7; длина хода штока для тарельчатых диафрагм равна (0,22 – 0,3) D, для плоских диафрагм (0,16 – 0,2) D.
Так как вследствие вогнутости диафрагмы сжатый воздух давит под некоторым углом к ее оси, то активная площадь диафрагмы
.
Сила Q на штоке в исходном положении для пневмокамеры одностороннего действия
,
где р – давление сжатого воздуха;
Q 1 – сопротивление возвратной пружины при крайнем рабочем положении штока с диафрагмой.
Для пневмокамеры двустороннего действия
.
Гидравлические силовые приводы. Преимущества гидравлических силовых приводов по сравнению с пневмоприводами: высокое давление рабочей жидкости, что создает большую силу зажима; обеспечение смазки трущихся деталей гидроцилиндра; меньший вес и габариты.
Из недостатков следует указать сложность установки и большую стоимость гидроприводов.
Гидравлический силовой привод является самостоятельной установкой, состоящей из электродвигателя, рабочего гидроцилиндра, насоса, бака, аппаратуры управления и регулирования и трубопроводов. Он может быть индивидуальным (для одного станка) или групповым (для нескольких станков). Гидравлические силовые приводы для индивидуального и группового обслуживания различаются только мощностью.
Собственно гидравлический силовой привод, как и пневматический, представляет собой цилиндр и поршень со штоком, который перемещается под давлением, но не сжатого воздуха, а масла.
Сила Q на штоке гидроцилиндра предопределяется давлением масла и площадью поршня гидроцилиндра.
Рис. 6.19. Пневмогидравлический привод
Для гидроцилиндров одностороннего толкающего действия
.
Для гидроцилиндров двустороннего действия:
при давлении масла на поршень в бесштоковой полости гидроцилиндра
;
при давлении масла на поршень со стороны штока
,
где D – диаметр поршня гидроцилиндра;
р = 20 ÷ 75 кГ/см2 – давление масла на поршень;
η = 0,85 – к. п. д. гидроцилиндра;
Q 1 – сопротивление пружины при крайнем рабочем положении поршня;
d – диаметр штока.
Пневмогидравлические силовые приводы. Пневмогидравлические силовые приводы применяют в тех случаях, когда нужно развить большие усилия зажима, не создавая громоздких силовых устройств. Иногда их называют пневмоприводами с гидроусилителем.
Принцип действия пневмогидравлических силовых приводов следующий (рис. 6.19). Из воздушной сети цеха воздух выпускается в бесштоковую полость пневмоцилиндра 1, и поршень 2 со штоком-плунжером 3 перемещается влево. Шток-плунжер давит на масло в гидроцилиндре 4. Сувеличением давления масла в гидроцилиндре поршень 5 его соштоком 6 перемещается влево, и шток посредством промежуточных звеньев оказывает воздействие на зажимные устройства приспособления. Давление масла в гидроцилиндре во столько раз превышает давление воздуха в пневмоцилиндре, во сколько раз площадь поршня пневмоцилиндра больше площади штока-плунжера.
При условии равновесия давления между воздухом и маслом, которое выражается равенством
,
давление масла pм в гидроцилиндре
,
где рв – давление воздуха в пневмоцилиндре;
Dв – диаметр поршня пневмоцилиндра;
d – диаметр штока-плунжера.
Отношение является коэффициентом усиления и принимается равным 16 – 26.
Сила Q, создаваемая давлением масла на поршень гидроцилиндра и передаваемая зажимным устройствам приспособления,
.
Подставив выражение
в формулу для Q, получим
.
Приняв
,
получим
,
где Q 1 – сила на штоке пневмоцилиндра;
Dм – диаметр поршня гидроцилиндра;
η = 0,8 ÷ 0,85 – к. п. д. пневмогидропривода.
Пневмогидравлические силовые приводы применяются в стационарных и вращающихся приспособлениях.
Элементы для направления режущего инструмента. При обработке отверстий сверлами, развертками, зенкерами, а также при растачивании отверстий резцами, установленными в борштанге, или резцовыми головками применяют приспособления с направляющими, называемые кондукторами. Втулки кондукторов бывают постоянными, сменными, быстросменными и специальными.
Постоянные кондукторные втулки запрессовывают в корпус приспособления-кондуктора и применяют обычно для направления сверл и зенкеров.
Сменные втулки вставляются (посадка движения) в запрессованные в корпус приспособления постоянные втулки и закрепляются винтом.
При обработке одного и того же отверстия в детали при одном ее закреплении иногда применяют разные инструменты (например, зенкер и развертку). В этом случае используют быстросменные кондукторные втулки.
Допуски на диаметр отверстия втулок для сверления и зенкерования соответствуют полю F8, для развертывания – G7 системы вала. Если точность расположения оси отверстия 0,05 мми выше, допуск на диаметр отверстия для прохода сверл принимают по посадке G7, а для чистового развертывания – по посадке G6. Но при этом необходимо предупреждать чрезмерное нагревание инструмента.
Расстояние от нижнего торца втулок по поверхности обрабатываемой детали принимают равным 0,3 – 1,0 диаметра отверстия втулки. При обработке хрупких материалов принимается меньшее расстояние, при обработке вязких – большее.