Раскрой материала. Рациональный раскрой полосы (ленты)
(рис. 3.1) характеризуется коэффициентом использования материала h (%) и определяется по формуле [1,2]:
,
где F д – площадь штампуемой детали в мм; F 3 – площадь заготовки, необходимой для изготовления штампуемой детали F 3 = ТВ; Т – шаг между деталями в мм; В – ширина полосы.
Рис.3.1- Раскрой материала
Ширина перемычек между деталями (a 1 и b 1) и по краям полосы (a и b) зависит от толщины материала, формы и размеров детали. Рекомендуемые значения ширины перемычек при вырубке приведены в таблице 1.
Таблица 3.1
Ширина перемычек при вырубке
Толщина материала, мм и номер вариан- та задания | Ширина перемычек, мм | |||||||||
Круглых и овальных при D | Прямоугольных деталей при L | |||||||||
Обозначение | До 50 | Св. 50 до 100 | Св. 100 до 200 | Св. 200 | Обозначение | До 50 | Св. 50 до 100 | Св. 100 до 200 | Св. 200 | |
До 0,5 01 | a a 1 | 1,5 1,2 | 1,7 1,4 | 1,9 1,6 | 2,2 1,8 | b b 1 | 1,8 1,5 | 2,0 1,7 | 2,5 2,2 | 3,0 2,7 |
Св. 0,5 до 1 | a a 1 | 1,2 0,8 | 1,4 1,0 | 1,6 1,2 | 1,8 1,4 | b b 1 | 1,5 1,0 | 1,7 1,2 | 2,2 1,7 | 2,7 2,2 |
Св. 1 до 1,5 | a a 1 | 1,5 1,1 | 1,7 1,3 | 1,9 1,5 | 2,1 1,7 | b b 1 | 1,9 1,4 | 2,1 1,6 | 2,6 2,1 | 3,1 2,6 |
Св. 1,5 до 2 | a a 1 | 1,9 1,5 | 2,1 1,7 | 2,3 1,9 | 2,5 2,1 | b b 1 | 2,2 1,7 | 2,4 1,9 | 3,0 2,5 | 3,4 2,9 |
Св. 2 до 2,5 | a a 1 | 2,3 1,8 | 2,5 2,0 | 2,7 2,2 | 2,9 2,4 | b b 1 | 2,6 2,2 | 2,8 2,4 | 3,3 2,9 | 3,8 3,4 |
Св.2,5 до 3 | a a 1 | 2,6 2,1 | 2,8 2,3 | 3,0 2,5 | 3,2 2,7 | b b 1 | 3,0 2,5 | 3,2 2,7 | 3,7 3,2 | 4,2 3,7 |
Св. 3 до 3,5 | a a 1 | 3,0 2,5 | 3,2 2,7 | 3,4 2,9 | 3,6 3,1 | b b 1 | 3,4 2,9 | 3,6 3,1 | 4,1 3,6 | 4,6 4,1 |
Св. 3,5 до 4 | a a 1 | 3,3 2,8 | 3,5 3,0 | 3,7 3,2 | 3,9 3,4 | b b 1 | 3,7 3,2 | 3,9 3,4 | 4,4 3,9 | 4,9 4,4 |
Св. 4 до 4,5 | a a 1 | 3,6 3,1 | 3,8 3,3 | 4,0 3,5 | 4,2 3,7 | b b 1 | 4,0 3,6 | 4,2 3,8 | 4,7 4,3 | 5,2 4,8 |
Св. 4,5 до 5 | a a 1 | 4,0 3,4 | 4,2 3,6 | 4,4 3,8 | 4,6 4,0 | b b 1 | 4,5 4,0 | 4,7 4,2 | 5,2 4,7 | 5,7 5,2 |
Св. 5 до 6 | a a 1 | 4,2 3,5 | 4,5 3,9 | 4,8 4,2 | 5,0 4,5 | b b 1 | 4,5 4,0 | 5,5 4,5 | 5,5 4,5 | 6,0 5,0 |
Св. 6 до 7 | a a 1 | 4,5 3,6 | 5,0 4,0 | 5,5 4,2 | 6,0 4,5 | b b 1 | 4,8 4,3 | 6,0 5,0 | 6,0 5,0 | 6,5 5,5 |
Св. 7 до 8 | a a 1 | 5,0 4,2 | 5,5 4,5 | 5,8 4,8 | 6,0 5,0 | b b 1 | 5,3 4,8 | 6,5 5,5 | 7,0 6,0 | 7,8 6,8 |
Св. 8 до 9 | a a 1 | 5,5 4,5 | 6,0 5,0 | 6,3 5,2 | 6,5 5,5 | b b 1 | 5,8 5,3 | 7,0 6,0 | 7,5 6,5 | 8,0 7,0 |
Св. 9 до 10 | a a 1 | 6,0 5,0 | 7,0 6,0 | 7,5 6,5 | 8,0 7,0 | b b 1 | 6,3 5,8 | 7,0 6,0 | 7,5 6,5 | 8,0 7,0 |
При пользовании таблицей 1 необходимо учитывать следующее:
|
|
1) при вырубке с поворотом полосы надо величины перемычек увеличивать на 50% по сравнению с приведенными данными;
2) ширину кромки, обрезаемой шаговым ножом, принимать равной величине перемычки b 1;
3) при вырубке неметаллических материалов ширину перемычек увеличивать на 50% по сравнению с табличными данными;
4) при вырубке на пластинчатых штампах ширину перемычек принимать в 1,5–2 раза больше рекомендуемых в таблице значений;
5) при многорядной вырубке перемычек между деталями a 1 и b 1 рассчитывать, исходя из размера детали, а по краям полосы величины a и b определять по ширине полосы;
|
|
6) при вырубке магниевых сплавов табличные значения увеличивать в два раза;
7) при штамповке титановых сплавов ВТ1 без подогрева и ВТ5 с подогревом табличные значения увеличивать на 25–30%, а при штамповке сплава ВТ5 без подогрева – в два раза.
Ширину полосы В определяют для круглых и прямоугольных деталей соответственно по формулам:
B = D + 2 a + Δ n;
B = L + 2 b + Δ n,
где В – округляется до целого числа в большую сторону; Δ n – допуск на ширину B в мм, принимаемый при разрезке листа на гильотинных ножницах по таблице 3.2, а при разрезке широких лент на узкие на многодисковых ножницах – по таблице 3.2.
Таблица 3.2
Допуски на ширину полос Δ n в мм при резке на гильотинных ножницах
Ширина полосы, мм | Толщина материала, мм | ||||
До 1 | Св. 1 до 2 | Св. 2 до 3 | Св. 3 до 5 | Св. 5 до 10 | |
До 50 Св. 50 до 100 «100 «150 «150 «220 «220 «300 | 0,4 0,5 0,6 0,7 0,8 | 0,5 0,6 0,7 0,8 0,9 | 0,7 0,8 0,9 1,0 1,1 | 0,9 1,0 1,1 1,2 1,3 | 1,8 2,0 2,5 3,0 4,0 |
Примечания: 1. Допуски на ширину полос принимать со знаком минус. 2. Допуски даны для реза длиной не более 1000 мм.
При назначении ширины полосы необходимо учитывать стандартные размеры листов и лент. Располагать детали следует так, чтобы ширина полосы была кратной стандартным размерам листов.
Расчет усилия вырубки в штампах с прямыми и скошенными режущими кромками. Расчетное усилие Р определяют по формуле
,
где L – периметр вырубаемого (пробиваемого) контура, мм; S – толщина материала, мм; tср = 0,58σ s – сопротивление срезу (таблица 3.4).
Таблица 3.3
Допуски на ширину полос Δ n (мм) при резке
на многодисковых ножницах
Толщина материала, мм | Ширина ленты, мм | |||||
До 100 | Св. 100 до 300 | Св. 300 | До 100 | Св. 100 до 300 | Св. 300 | |
Нормальная точность | Повышенная точность | |||||
До 0,1 Св. 0,1 до 0,63 «0,63 «1,0 «1,0 «3,6 | 0,10 0,20 0,30 0,40 | 0,15 0,30 0,40 0,50 | 0,25 0,40 0,50 0,60 | 0,05 0,10 0,20 0,30 | 0,08 0,15 0,25 0,35 | 0,15 0,25 0,35 0,45 |
Необходимое усилие пресса Р д рассчитывают по формуле
,
где P д ном – номинальное усилие пресса.
Таблица 3.4
Механические характеристики различных материалов
Материал | Е, ГПа | r · 10–3, кг/м3 | s s, ГПа | n |
Алюминиевая бронза Алюминий отожженный Дюралюминий | 68,5 | 4,1 2,7 2,6 | 0,2–0,6 0,05–0,12 0,18–0,5 | 0,25 0,36–0,37 0,31 |
Латунь катанная Латунь холоднотянутая Медь катанная Медь холоднотянутая | 89–97 | 8,6 8,9 3,9 4,8 | 0,3–0,6 0,3–0,6 – – | 0,36 0,32–0,42 0,31–0,34 0,33 |
Сталь легированная Сталь углеродистая Чугун белый | 195–205 113–116 | 7,87 7,87 4,4 | 0,8 0,38–0,47 0,65–1,3 | 0,25–0,30 0,24–0,26 0,23–0,27 |
Титан | 4,5 | 0,56–0,88 | 0,32 |
При отсутствии пресса необходимого усилия можно осуществлять вырубку на прессе меньшего усилия, применяя скошенные режущие грани на пуансоне или матрице, а также ступенчатое расположение пуансонов. При вырубке наружного контура скос делают на матрице, а пуансон должен быть плоским (рис. 3.2,а). При пробивке отверстия скос выполняют на пуансоне, а матрица остается плоской (рис. 3.2,б). Соблюдение указанных условий обеспечивает получение плоских изделий при изогнутых отходах. Скосы делают симметричными. Высоту скоса и угол наклона режущих кромок принимают в пределах: Н = (1 – 3) S, j = 3 – 8° (рис. 3.2).
|
|
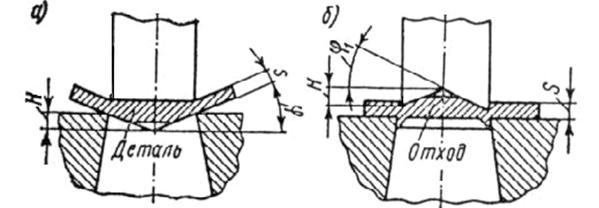
Рис.3.2- Вырубка наружного контура и пробивка отверстия
При вырезке скошенными режущими гранями усилие Р 1 ориентировочно определяют по формулам:
– при Н = S, Р 1 = 0,6 LS tср;
– при Н ≥ 2 S, Р 1 = 0,4 LS tср.
Ступенчатое расположение пуансонов в многопуансонных штампах (рис. 3.3) можно получить укорочением пуансонов с меньшими сечениями на величину, равную (0,5–1) S. В штампах последовательного действия наибольшую высоту имеют пуансоны с ловителями, а в пробивных штампах – пуансоны с наибольшими диаметрами.
|
|
Рис. 3.3- Ступенчатое расположение пуансонов
Усилие вырубки при ступенчатом расположении пуансонов подсчитывают по периметру вырубаемого (пробиваемого) контура, который является наибольшим.
Усилие снятия отхода или штампуемой детали с пуансона Р сн определяют по формуле
,
где К сн – коэффициент, зависящий от штампуемого материала (табли-
ца 3.5).
Таблица 3.5
Значения коэффициентов К пр и К сн
Металл | Среднее значение коэффициентов | |
К ср | К пр | |
Сталь Латунь Медь Алюминий Дюралюминий и магниевые сплавы | 0,03–0,05 0,02–0,04 0,015–0,03 0,0250–0,05 0,025–0,05 | 0,02–0,06 0,02–0,05 0,03–0,07 0,03–0.06 0,02–0,06 |
Усилие Р пр для проталкивания детали или отхода через матрицу вычисляют по формуле
,
где К пр – коэффициент, зависящий от штампуемого материала (табли-
ца 5).
Значения К сн относятся к снятию отхода с одного вырубного пуансона. При одновременной пробивке нескольких отверстий, расположенных друг от друга на расстоянии, большем двух-трех толщин материала, К сн = 0,08 – 0,1; а при перемычках, ширина которых близка к толщине материала, К сн = 0,15 – 0,2.
При работе без смазки приведенные в таблице 3.5 значения коэффициентов следует увеличивать на 20–25%.
При холодной вырубке и пробивке напряжение текучести увеличивается с увеличением степени деформации вследствие деформационного упрочнения металла.
Усилие вырубки равно
,
где L – периметр отдельного контура; S – толщина материала; x – координата (0 ≤ x ≤ S); σ s – предел временного сопротивления материала;
ψ – относительное равномерное сужение образца при растяжении: для материалов М2(т), БрБ2, Д16А-Т ψ = 0,02; ЛС59-1, БрОЦ4-3 ψ = 0,04; БрОЦ4 ψ = 0,05; Ст7 ψ = 0,07; БрА7, Л62, У9А, У12, У13А, 60С2, БрА7, 70Г ψ = 0,09; 65Г, Ст6, 85ХФ, Д16А-М ψ = 0,1; 60Г ψ = 0,12; Л68, Д16А, Ст5, 40Х13, 30Х13 ψ = 0,13; 15Х25Т ψ = 0,14; 25ХГСА, 12Г2А, 16ГС, 12Х17, 15ХСНД ψ = 0,15; Ст4, У8, Ст4 ψ = 0,16; Ст3, 12Х13 ψ = 0,17; 10Г2А ψ = 0,18; Ст2, Э1100, ЛМц58, ψ = 0,2; Э3100, Ст1 ψ = 0,22; М2(м), М1 ψ = 0,23; 17Х18Н9, 12Х18Н9 ψ = 0,26; 20Х13Н4Г9, 08Х18Н12Б, Л68, ЭА ψ = 0,28; ЭАА ψ = 0,3; 08Х18Н9 ψ = 0,31; 50Х, 18ХГ, 45 ψ = 0,4; АД ψ = 0,44;30Х, 30ХГС, 20ХГСА ψ = 0,45; 30ХМА ψ = 0,5; 10 кп ψ = 0,55; 08кп ψ=0,6.
|
|
Определение центра давления штампа. Ось хвостовика необходимо располагать в центре давления штампа для предотвращения перекоса и несимметричности зазора. Координаты центра давления (х 0, у 0, рис. 3.4) следует определять для многопуансонных штампов, штампов последовательного действия и при несимметричном вырезаемом контуре:
,
где li, l 1, l 2, l 10 – периметры соответствующих участков контура вырубаемых (пробиваемых) деталей; xi, x 1, x 2, х 10 – расстояния от геометрического центра соответствующих участков до оси у; уi,. y 1, y 2, y 10 – расстояния от геометрического центра соответствующих участков до оси x.
Пересечение координат х 0 и у 0 дает искомый центр О давления штампа.
Определение исполнительных (рабочих) размеров пуансонов и матриц при вырубке и пробивке. Размеры изделия, получаемого вырубкой, соответствуют размерам рабочего отверстия матрицы. Изнашивание матрицы приводит к увеличению ее рабочего отверстия. Поэтому исполнительные размеры рабочего отверстия матрицы для вырубки должны быть наименьшими предельными.
Если штампуемое изделие имеет форму круга и допуски на его диаметр назначены в системе отверстия, то исполнительный диаметр рабочего отверстия матрицы определяется как разность между номинальным диаметром изделия и допуском на этот диаметр:
,
где D н – номинальный диаметр штампуемого изделия; Тd – допуск на диаметр изделия; Т м – допуск на размер матрицы.
Рис. 3.4- Схема определения центра давления штампа
Рабочий (исполнительный) диаметр пуансона для вырубки в данном случае будет меньше диаметра матрицы на значение зазора z (таблица 3.6) между ними: D п = D м – z,или
,
где Т п – допуск на размер пуансона.
Диаметр отверстия, получаемого пробивкой, соответствует диаметру пуансона. Изнашивание пуансона приводит к уменьшению его диаметра. Поэтому исполнительный диаметр пуансона должен быть наибольшим предельным.
Если допуски на штампуемое изделие назначены в системе отверстия, то диаметр пуансона определяется как сумма номинального диаметра отверстия и допуска на этот диаметр:
.
Таблица 3.6
Зазоры между пуансоном и матрицей
Толщина материала, мм | Низкоуглиродистые стали марок 10, 20; медь, латунь, алюминий | Среднеуглиродистые стали марок 25, 35, 45; дюралюминий, бронза | Высокоуглиродистая, трансформаторная и нержавеющая стали | |||
z | Δ | z | Δ | z | Тm | |
0,1 | 0,005 | – | 0,006 | – | 0,007 | – |
0,2 0,3 0,4 0,5 | 0,010 0,015 0,020 0,025 | + 0,010 | 0,012 0,018 0,024 0,030 | + 0,010 | 0,014 0,021 0,028 0,035 | + 0,010 |
0,6 0,7 0,8 0,9 1,0 | 0,030 0,035 0,040 0,045 0,050 | + 0,020 | 0,032 0,042 0,048 0, 054 0,060 | + 0,020 | 0,042 0,049 0,056 0,063 0,070 | + 0,020 |
1,2 1,5 | 0,070 0,090 | + 0,030 | 0,080 0,110 | + 0,030 | 0,100 0,120 | + 0,030 |
1,8 2,0 2,2 2,5 2,8 3,0 | 0,110 0,120 0,160 0,180 0,200 0,210 | + 0,050 | 0,130 0,140 0,180 0,200 0,220 0,240 | + 0,050 | 0,140 0,160 0,200 0,230 0,250 0,270 | + 0,050 |
3,5 4,0 4,5 5,0 | 0,280 0,320 0,360 0,400 | + 0,100 | 0,320 0,360 0,450 0,500 | + 0,100 | 0,350 0,400 0,540 0,600 | + 0,100 |
6,0 7,0 8,0 9,0 10,0 | 0,500 0,700 0,800 1,100 1,200 | + 0,200 | 0,600 0,900 1,000 1,300 1,400 | + 0,200 | 0,700 1,000 1,100 1,400 1,600 | + 0,200 |
11,0 12,0 13,0 14,0 | 1,600 1,700 2,100 2,300 | + 0,300 | 1,800 1,900 2,300 2,500 | + 0,300 | 2,000 2,200 2,600 2,800 | + 0,300 |
15,0 16,0 17,0 18,0 19,0 20,0 | 2,700 2,900 3,400 3,600 4,200 4,400 | + 0,500 | 3,000 3,200 3,800 4,000 4,600 4,800 | + 0,500 | 3,300 3,500 4,100 4,300 5,000 5,200 | + 0,500 |
Примечание: z – наименьший допустимый зазор; Δ – допускаемое отклонение в сторону увеличения зазора.
Рабочий (исполнительный) диаметр матрицы для пробивки будет больше диаметра пуансона на значение зазора между ними: D м= D п + z, или
.
Приведенные формулы для определения исполнительных размеров пуансонов и матриц применимы в том случае, когда толщина штампуемого металла сравнительно невелика; (до 1–2 мм), т.к. при этом условии боковая поверхность отделенной части металла может считаться приблизительно перпендикулярной плоскости листа.
При штамповке более толстого металла (свыше 2 мм) необходимо принимать во внимание конусность боковой поверхности отделенной части металла, которая образуется вследствие того, что скалывающие трещины направлены под определенным углом к образующей. Поэтому для устранения возможности выхода размеров штампуемой детали за предельные поля допусков диаметр детали искусственно уменьшается. Уменьшенный допуск принимается равным 0,6–0,8 номинального допуска. В этом случае формулы для определения исполнительных размеров пуансонов и матриц имеют вид:
– для вырубки:
;
;
– для пробивки:
;
.
Допуск на рабочие размеры пуансонов и матриц T м и T п принимают равным 5–35% от допуска на соответствующий размер штампуемой детали. Допуски на размеры инструмента назначают по определенным классам точности: при толщине штампуемого металла до
3 мм – по 8-му квалитету и при толщине металла свыше 3 мм – по
10-му квалитету.
Пример.Требуется определить исполнительные размеры пуансонов и матриц для штамповки шайбы с наружным диаметром 40–0,34 мм, внутренним диаметром 20+0,28 мм в условиях массового производства. Материал шайбы – листовая сталь Ст20 толщиной 2,5 мм.
Определяем допуски на размеры пуансонов и матриц в зависимости от номинальных размеров шайбы и ее толщины:
По таблице 15.2 определяем минимальный зазор между пуансоном и матрицей, z min = 0,18 + 0,05 = 0,23 мм. Находим исполнительные размеры инструмента:
– для вырубки наружного контура диаметром 40 мм:
– для пробивки отверстия диаметром 20 мм:
Методика определения исполнительных размеров матриц и пуансонов для вырубки-пробивки некруглых деталей в основном та же, что и для круглых. Поскольку инструмент изнашивается «в тело», размеры отдельных элементов контура инструмента (выступы и впадины) в процессе штамповки изменяются по-разному: одни размеры увеличиваются, другие – уменьшаются. Участки контура инструмента с одинаковым направлением изнашивания (размер С)остаются приблизительно неизменными (рис. 3.5,а).Направление изнашивания инструмента обозначено стрелками. Экономически целесообразная точность изготовления инструмента для штамповки некруглых деталей (или заготовок) определяется допусками, равными одной четвертой части допуска на размеры детали:
.
При проектировании инструмента для вырубки исполнительные размеры с соответствующими допусками проставляются только на чертеже матрицы, а для пробивки – только на чертеже пуансона. На чертеже пуансона для вырубки и матрицы для пробивки в виде примечания дают указания о пригонке контуров с определенным
зазором z. На рисунке 3.5,бпоказаны контур детали и рабочий контур матрицы, размеры которой определены согласно изложенным правилам.
Если деталь или заготовка имеет особо сложную форму с криволинейным очертанием, контур инструмента изготовляют по специальному шаблону. При вырубке по шаблону делают матрицу, припробивке – пуансон. Затем сопрягающийся инструмент (пуансон – при вырубке, матрицу – при пробивке) подгоняют с требуемым зазором.
а) б)
Рис.3.5- Направления изнашивания инструмента при вырубке (а),
размеры детали и соответствующие размеры матрицы (б)