Толкающая системапредставляет собой систему организации производства, в которой материалы, поступающие в цех, у предыдущего цеха не заказываются. Материальный поток «выталкивается» получателю по команде из центральной системы управления производством (рис.4.1).
|
|
|
|

Рис. 4.1. Толкающая система организации производства
Эти системы управления характерны для традиционных методов организации производства.
Данная система требует использования ЭВМ, что позволяет согласовывать и оперативно корректировать планы и действия всех подразделений предприятия, тем самым связывая их в единое целое. Эффективность работы таких систем определяется системой факторов, которые влияют на деятельность, как отдельных подразделений, так и предприятия в целом, а также качеством принимаемых решений и оперативностью их внедрения в производство. Первой системой, оставшейся по своей сути толкающей, но уже использовавшей принципы логистики, была система планирования потребности в материалах MRP (Material Requirements Planning) которая возникла в начале 60-х годов, в связи с ростом популярности вычислительных машин, появилась возможность использовать их для планирования деятельности структурных подразделений предприятия и предприятия в целом.
|
|
Рис. 4.2.Программный комплекс МRР -I
Программа производства — это оптимизированный график производственного процесса на планируемый период. Вначале формируется пробная программа производства, которую тестируют на выполнимость, чтобы определить, достаточно ли производственных мощностей для осуществления плана. Если производственная программа признана выполнимой, то она автоматически формируется в основную программу производства и становится входным элементом МRР I.
Перечень составляющих конечного продукта — это список, в котором перечислены материалы и указано их количество, необходимое для производства конечного продукта. Потребность в материалах рассчитывается исходя из норм расхода. Таким образом, каждый конечный продукт имеет свой перечень составляющих, содержащий описание структуры конечного продукта, т.е. полную информацию по технологии его сборки.
Описание состояния материалов — базовый элемент, обеспечивающий работу МRР-программы, поскольку в нем отражается информация обо всех комплектующих, необходимых для производства конечного продукта: статус каждого материала (имеется ли на руках, или находится на складе, или включен в текущий заказ, или его заказ только планируется), объем запасов, местоположение, цена, возможные задержки поставок, реквизиты поставщиков.
|
|
Основными результатами МRР-системы являются:
• план заказов, который определяет, какое количество каждого материала должно быть заказано в каждый период времени в течение срока планирования. Он является руководством к дальнейшей работе с поставщиками;
• изменения к плану заказов, которые являются модификациями к ранее спланированным заказам. Отдельные заказы могут быть отменены, изменены,
задержаны или перенесены на другой период.
Возможны и некоторые второстепенные результаты в виде отчетов, цель которых — обнаружение «узких мест» в ходе планируемого периода, т.е. промежутков времени, в которые требуется дополнительный контроль текущих заказов или которые необходимы, чтобы вовремя известить о системных ошибках, возникших при работе программы.
МRР-система формирует следующие дополнительные результаты-отчеты:
• отчет об «узких местах» планирования, предназначенный для информирования пользователя о времени в течение которого может возникнуть необходимость управленческого вмешательства (непредвиденно запоздавшие заказы на комплектующие, избытки комплектующих на складах и т.п.);
• исполнительный отчет — основной индикатор правильности работы МRР-системы, оповещающий пользователя о критических ситуациях, возникших в процессе планирования (полное израсходование страховых запасов по отдельным комплектующим, системные ошибки в процессе работы МRР-программы);
• отчет о прогнозах — документ, включающий информацию о возможном изменении объемов и характеристик выпускаемой продукции, полученную в результате анализа текущего хода производственного процесса и отчетов о продажах.
Таким образом, применение МКР 1-системы в планировании производственных потребностей позволяет оптимизировать время поступления каждого материала, тем самым способствуя значительному снижению складских издержек и облегчая ведение производственного учета.
Главными задачами системы МRР I являются:
• гарантия поставки необходимого количества требуемых материалов и комплектующих в соответствии с плановым графиком;
• поддержание возможно низкого уровня запасов материальных ресурсов, незавершенного производства, готовой продукции;
• планирование производства, времени доставки и закупки необходимых материалов.
Основными преимуществами использования системы в производстве являются:
• гарантия наличия требуемых комплектующих и сокращение времени их доставки;
• уменьшение брака в процессе сборки готовой продукции, возникающего из-за использования нестандартных комплектующих;
• установление контроля за движением каждого материала начиная от заказа до изготовления изделия.
Основная цель MRP-системы контролировать и, при необходимости, изменять время поступления заказов таким образом, чтобы все материалы для производства поступали одновременно.
По сути МRР I позволяет оптимально загружать производственные мощности и при этом закупать столько материалов и сырья, сколько необходимо для выполнения текущего плана заказов. Тем самым планирование текущей потребности в материалах позволяет разгрузить как склады сырья (сырье и комплектующие закуплены точно в том объеме, который можно обработать за один производственный цикл, и поступают прямо в производственные цехи), так и склады готовой продукции (производство идет в строгом соответствии с принятым планом заказов, и продукция будет произведена к сроку его отгрузки.
С целью повышения эффективности планирования в конце 70 годов в США была предложена идея замкнутого цикла в MRP-системах. Смысл идеи заключался во введении большего количества факторов при планировании производства.
|
|
Если прежде действовал принцип «что-то произвести, а затем постараться продать», то теперь задача иная — «стараться производить то, что продается». Маркетинг и планирование продаж непосредственно включаются в процесс планирования производства.
В дальнейшем усовершенствование системы привело к преобразованию системы MRP с замкнутым циклом в расширенную модификацию, которую впоследствии назвали MRP-II.
Эта система была создана для эффективного планирования всех ресурсов предприятия, в том числе финансовых и кадровых. Кроме того, система класса MRP-II способна адаптироваться к изменениям внешней среды, что и обеспечивает ей гибкость. Именно это свойство является важным для планирования. Таким образом, появляется необходимость в автоматизированной системе, которая позволяет оптимизировать объемы и характеристики выпускаемой продукции, анализируя текущий спрос и положение на рынке в целом.
Принцип организации работы системы МКР II представлен на рис. 4.3.
|

|
|
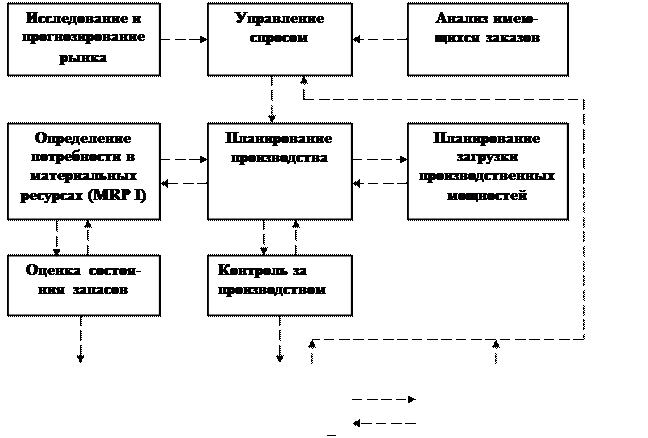
Рис. 4.3.Логическая схема функционирования систем класса МRР II
MRP-II включает в себя функции системы MRP I. Система МНР I является составной частью МRР II.
В настоящее время системы класса МRР II считаются эффективным инструментом планирования для реализации стратегических целей фирмы в области производства, маркетинга, финансов и логистики.
Преимуществами МRР II в сравнении с МRР I:
♦ сокращение производственного цикла;
♦ уменьшение запасов;
♦ улучшение организации поставок;
♦ ускорение реагирования на изменение спроса.
Особое значение в МRР II - системе приобретают функции обратной связи. Например, поставщик, не успевающий поставить материалы в оговоренные сроки, обязан безотлагательно послать информацию о задержке, узнав о возникновении этой проблемы.
|
|
Современная вычислительная техника позволяют системе МRР II функциониро- вать в режиме реального времени, что значительно повышает эффективность управле- ния материальными потоками. Кроме того, данная система более, чем МЕR I, приспо- соблена к мелкосерийному производству.