Наиболее полно принципы логистики воплощены в производственных системах тянущего типа.
Она представляет собой систему организации производства, в которой детали и полуфабрикаты подаются на последующую технологическую операцию с предыдущей по мере необходимости.
При работе по тянущей системе на каждом производственном участке создается строго определенный запас готовых деталей и узлов. Здесь центральная система управления не вмешивается в обмен материальными потоками между различными подразделениями предприятия, а ставит задачу лишь перед конечным звеном производственной цепи (рис. 4.4).
|
|
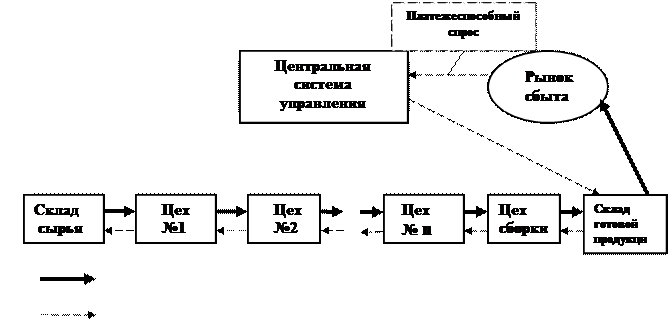
Рис. 4.4. Тянущая система организации производства
Последующий участок заказывает и вытягивает с предыдущего участка изделия строго в соответствии с нормой и временем потребления.
Тянущая система позволяет избегать колебаний спроса или объема производства, сводить к минимуму колебания запасов на производственных участках, децентрализовать управление производственными запасами.
|
|
Для данной системы не нужна компьютеризация. Однако для нее характерна высокая дисциплина поставок как по времени, так и по качеству и количеству изделий. В ней широко применяется метод поставок «точно в срок».
К преимуществам тянущей системы можно отнести:
- отказ от избыточных запасов;
- замена политики продажи произведенных товаров политикой производства продаваемых товаров;
- задача полной загрузки мощностей заменяется минимизацией сроков нахождения продукции в производстве
- снижение оптимальной партии, уменьшение партии обработки;
- выполнение заказов с высоким качеством;
- сокращение всех видов простоев и нерациональных внутризаводских перевозок.
Из систем тянущего типа наиболее известна японская система «Канбан», позволяющая реализовать принцип «точно в срок». Она основывается на управлении материальными потоками в зависимости от фактической загрузки производственных участков.
«Канбан» - комплексная система организации производства в соответствии с которой предприятие характеризуется как единое. В этом смысле система «Канбан» противоречит традиционной научной организации труда («тейлоризму»), принципом которой является максимальное разделение труда и узкая специализация работников.
Отличительной особенностью этой системы является сокращение производственного цикла. Материально-техническое обеспечение производства и отгрузка готовых изделий осуществляются по принципу «точно в срок». Фирмы не имеют складов сырья, материалов, комплектующих изделий, готовой продукции, а межоперационные запасы сокращены до минимума. В системе «Канбан» следует выделить три основные подсистемы:
|
|
- социальную (подбор и подготовка кадров, использование работников в соответствии с производственными потребностями, их стимулирование и продвижение по службе);
- техническую (оптимальное использование производственных мощностей, высокое качество продукции);
- производственную (рационализация материальных потоков, управление хо- дом производственного процесса).
В этой системе планирование производства осуществляется детально, графики разрабатываются с точностью до нескольких минут. При этом главным приоритетом является выполнение плана текущих заданий, трудовой день заканчивается только после выполнения этого плана.
Внедрение системы «Канбан» существенно повышает эффективность производства и конкурентоспособность фирмы. Этовыражается в снижении затрат на погрузочно-разгузочные, транспортные и складские работы, а также в повышении качества изделий, росте их конкурентоспособности, стабилизации кадров.
Сравнение аналогичных японских и американских фирм показывает, что, во-первых, материальные запасы ниже более чем на 50%, а производительность труда в целом на 20% выше. К примеру, фирма «Тойота», давно внедрившая систему «Канбан», в расчете на одного работающего производит за день 9 автомобильных двигателей, а фирма «Форд» при традиционной организации - два.
Время складирования готовых изделий не превышает в Японии шести часов, в то время как в Западной Европе составляет от двух до шести дней. В отношении межоперационных запасов эта разница еще больше. Так, в некоторых цехах фирмы «Мазда» производство осуществляется при материальных запасах, рассчитанных на 0,5 часа, а в фирме «Форд» до внедрения системы «Канбан» эти запасы были рассчитаны на срок до трех недель, но после ее внедрения были снижены до 11 дней. Однако, система «Канбан» приносит высокую эффективность только при условии ее комплексного внедрения.
Производство «методом «Точно в срок» позволяет выявить проблемы, которые не видны из-за избыточных запасов и лишнего персонала. Таким образом, идея системы - производить и поставлять готовые изделия как раз к моменту их реализации, отдельные детали - к моменту сборки узлов, а узлы и комплектующие - к моменту сборки изделия в целом.
Система предусматривает уменьшение размера партий обрабатываемых деталей, сокращение задела. Сведение к минимуму объемов запасов практически невозможно без существенного сокращения времени на переналадку оборудования.
В Японии время на переналадку составляет 10-12 минут для 99% продукции. Условия применения системы - высокий уровень автоматизации, синхронизация производственных процессов, высокий уровень культуры производства, качества продукции, производительности, ликвидация складских помещений и сокращение длительности цикла.
Система «Точно в срок» минует промежуточное складирование (производство без запасов, работа с колес). Применение системы требует синхронизации материального потока и технических операций. Концепция ЛТ стимулирует потребителей к ограничению числа поставщиков, отбору наиболее надежных среди них с точки зрения качества продукции и соблюдения сроков поставки. О том, какую роль играет надежность поставщиков, говорит тот факт, что автомобилестроительные фирмы США смогли внедрить ее в производство спустя лишь 10—15 лет после японских компаний. Основной причиной длительного не внедрения метода как раз явилась низкая надежность поставщиков материалов по срокам поставок и качеству комплектующих.
Значительную роль в организации производства на основе ЛТ-технологий играет информационное обеспечение. Без надежных вычислительных и телекоммуникационных систем реализация метода ЛТ невозможна. Перспективы развития информационных технологий ученые связывают с созданием искусственного интеллекта, т. е., компьютера, способного принимать решения подобно тому, как это делает квалифицированный специалист на основе накопленных знаний и опыта.
|
|
Переход от традиционной организации производства к системам ЛТ требует от предприятий существенной перестройки не только самой системы управления, но и философии ведения бизнеса.
Система ОПТ (оптимизированная производственная технология) широко применяется в США и других странах с 1980-х годов. В этой системе на качественно новой основе получили дальнейшее развитие идеи, заложенные в таких системах, как «Канбан» и MRP. Основной принцип ОПТ состоит в выявлении «узких» мест или, критических ресурсов, в качестве которых могут выступать запасы сырья и материалов, машины и оборудование, работники предприятия.
В системе ОПТ в автоматизированном режиме решается ряд задач оперативного и краткосрочного управления производством, в том числе формирование графика производства на день, неделю и т.д. При формировании близкого к оптимальному графику производства используются критерии обеспеченности заказов сырьем и материалами, гибкости, эффективности использования ресурсов, минимум оборотных средств в запасах.
Вторая американская система управления и планирования распределения продукции (DRP) обеспечивает устойчивые связи снабжения, производства и сбыта, используя элементы MRP.
DRP позволяет оптимизировать логистические издержки за счет сокращения транспортных расходов и затрат на товародвижение. DRP позволяет планировать поставки и запасы.
Конечная функция системы DRP - планирование транспортных перевозок. В системе обрабатываются заявки на транспортное обслуживание, составляются и корректируются в реальном масштабе времени графики перевозок. Долгосрочные планы работы складов служат основой для расчета потребности в транспортных средствах, корректировка потребности осуществляется с учетом оперативной обстановки. Базой данных системы DRP является информация о перевозимой и складируемой продукции, получаемой с фирмы-изготовителя, и информация со складов.
|
|
Среди отечественных логистических систем следует отметить комплексную систему оптимального транспортного обслуживания (КСО-ТО). Необходимым условием для ее создания явилось наличие устойчивых транспортных связей.
Внедрением КСО-ТО были решены следующие задачи:
- создание оптимальных постоянно действующих маршру-
тов и построение модели внутризаводских перевозок;
- оптимизация количества транспортных средств, необходимых для обслуживания цехов;
- оптимизация межцеховых перевозок;
- изучение динамики грузопотоков предприятия.
- оптимизация структуры парка транспортных средств фирмы;
- оптимизация величины партии грузов, перевозимых в унифицированной таре;
- разработка методики определения удельных затрат на погрузочно-разгрузочные, транспортные и складские работы при межцеховых перевозках,
5.3 Законы организации производства
Законы проявляются во всех сферах жизни человека, в том числе и в производстве.
Знание действия законов, а главное - использование их на практике позволяет устранить традиционные потери рабочего времени рабочих и оборудования по организационно-техническим причинам, которые составляют не менее 40% всего рабочего времени. Это дает возможность повысить конкурентоспособность предприятия за счет минимизации затрат на производство, гарантийного времени доставки заказов.
Закон упорядоченности движения предметов труда в производстве. Традиционное отсутствие стандартизации и типизации индивидуальных технологических маршрутов изготовления разных деталей вызывает неупорядоченное их движение в производстве. Следовательно, без предварительной организации движения деталей по типовым межцеховым и внутрицеховым технологическим маршрутам невозможно планирование хода производства.
Упорядоченное движение деталей в производстве достигается двумя способами:
- стандартизацией и типизацией межцеховых и внутрицеховых технологических маршрутов;
- применением типовой схемы движения деталей в производстве, что позволяет до 10 и более раз сократить количество различных межцеховых технологических маршрутов.